proe模具设计上Word文档格式.docx
《proe模具设计上Word文档格式.docx》由会员分享,可在线阅读,更多相关《proe模具设计上Word文档格式.docx(34页珍藏版)》请在冰豆网上搜索。
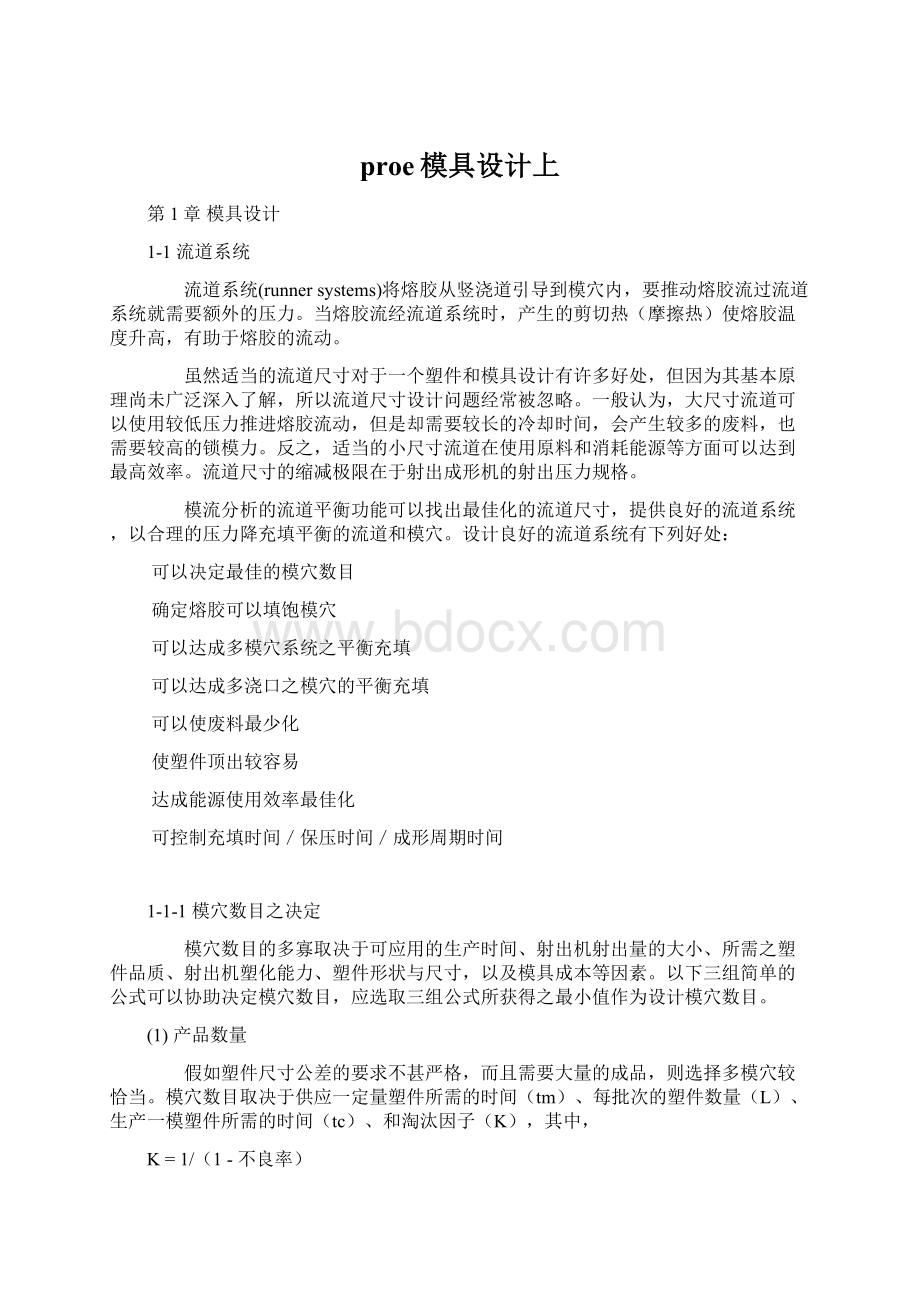
射出机的塑化能力是影响模穴数目的另一个重要因素。
将射出机的塑化能力(P)除以每分钟估计的射出次数(X)和塑件重量(W),即可计算出模穴数目。
模穴数目=P/(X×
W)
1-1-2流道配置
多模穴系统的基本流道配置方式如图1-1,包括:
标准流道系统(standard,或鱼骨形Herringbone)
H形流道系统(H-bridge,或分枝形branching)
辐射流道系统(radial,或星形star)
H形和幅射流道系统提供自然平衡,亦即从竖浇道到所有的模穴都有相同的流动距离和流道尺寸,所以各模穴都有相同的充填条件。
至于鱼骨形流道系统,虽然不是自然平衡,却比自然平衡系统可以在相同的模具内塞进更多模穴,造成最小的流道体和最低的模具加工成本。
除了采用自然平衡的流道系统之外,不平衡的流道系统也可用人工改变流道直径与长度,或是在各个子流道加装流量调节螺丝,以调整获得平衡的系统。
模流分析软件的流道平衡分析可以自动化完成流道平衡。
1-1-3竖浇道尺寸之决定
竖浇道尺寸主要决定于塑件尺寸,特别是塑件的肉厚。
竖浇道的设计必须能够方便可靠地让塑件脱模,于射出成形时,竖浇道不可以比塑件其它部分的截面更早凝固,如此才能够有效
图1-1基本的流道系统之配置
图1-2是建议的竖浇道设计规范。
不具有锐角的系统有助于塑料的流动,所以,应该将竖浇道根部设计成半径r2的圆角。
其它的设计规格如下列:
Dco≧tmax+1.5(mm)
Ds≧Dn+1.0(mm)
α≧1°
~2°
tan(α)=(Dco–D)/2L
图1-2竖浇道根部的圆角可以改善熔胶的流动
6-1-4流道截面之设计
常见的流道截面如图1-3,包括:
圆形流道
梯形流道
改良梯形流道(圆形与梯形之组合)
半圆形流道
长方形流道
通常建议采用前三种流道截面设计。
就最大的体积与表面积比值而言,圆形流道最佳,也具有最小的压力降和热损失,然而,却必须在两侧模板都进行加工,模具加工成本通常较高昂,而且合模时两侧的半圆也必须对齐。
相对地,梯形流道只在母模侧加工,其效能也很好,梯形流道通常应用于三板模,因为三板模如果采用圆形流道时,可能无法顺利脱模,而且模具可能在分模线造成圆形流道与模板滑动件之间的干涉。
图1-3常用的流道截面形状
对于不同形状的流道,可以使用做为流动阻力指标的水力直径(hydraulicdiameter)进行比较。
水力直径愈大,流动阻力愈低。
水力直径定义为:
其中,
Dh=水力直径
A=截面面积
P=周长
图1-3比较各种流道形状之等效水力直径,这些系数正好是C-mold软件之形状因子(shapefactor)的倒数。
图1-3各种流道形状的等效水力直径
1-1-5流道尺寸之决定
流道的直径和长度会影响流动阻力。
流动阻力愈大的流道,充填就会造成愈大的压力降。
加大流道直径可以降低流动阻力,但是会耗用较多的树脂材料,也需要更长的冷却时间,才能顶出塑件。
设计流道直径最初可以根据实验数据或是下列方程式进行,然后应用模流分析软件微调流道直径,最佳化熔胶传送系统。
最初估算的流道直径为:
D=流道直径(mm);
W=塑件重量(g);
L=流道长度(mm)。
范例说明:
图1-4和图1-5所提供实验数据可以用来计算流道尺寸,例如,一个300公克重的ABS塑件,其厚度为3mm,流道长度为200mm,则流道直径该是多少?
1.根据图1-4,在300公克重之水平线和3mm厚直线之交点处画一垂直线,与横轴交于5.8mm处,即为参考直径D’。
2.使用图1-5,在流道长度200mm处画水平线与曲线得到交点,再画垂直线与横轴交于1.29,即为长度系数fL。
3.将5.8mm乘上1.29,获得之流道直径为7.5mm。
图1-4材料的流道直径图,其中,G=塑件重量(g);
S=塑件厚度(mm);
D’=参考直径(mm)
图1-5流道长度与长度系数对于流动直径的影响
一般无法填充料之塑料的典型流道尺寸列于表1-1。
表1-1无填充料之塑料的典型流道尺寸
材料
直径
mm
inch
ABS,SAN
5.0-10.0
3/11-3/8
Polycarbonate
聚碳酸脂(PC)
Acetal
聚缩醛树脂
3.0-10.0
1/8-3/8
Thermoplasticpolyester
热塑性聚脂树脂
3.0-8.0
1/8-5/11
Acetate
5.0-110.
3/11-7/19
Thermoplasticpolyester(reinforced)
补强热塑性聚脂树脂
Acrylic压克力
8.0-10.0
5/11-3/8
Polyethylene
聚乙烯
2.0-10.0
1/11-3/8
Butyrate
Polyamide
聚丙烯酸脂
Fluorocarbon
聚氟碳树脂
Polyphenyleneoxide
1.0-10.0
1/4-3/8
Impactacrylic
耐冲击压克力
5/11-1/2
Polyphenylene
聚丙烯
Ionomers
3/32-3/8
Polystyrene
聚苯乙烯
Nylon耐隆
Polysulfone
聚氟乙烯
Phenylene
Polyvinyl(plasticized)
聚氯乙烯
Phenylenesulfide
1/4-1/2
PVCRigid
硬质聚氯乙烯
1.0-11.0
1/4-5/8
Polyallomer
异聚合物
Polyurethane
聚尿素树脂
1.0-8.0
1/4-5/11
1-1-1热流道系统
理想的射出成形系统可以生产密度均匀的塑件,而且不需要流道,不产生毛边和浇口废料。
使用热流道系统(hotrunnersystems)可以达成此一目标。
热流道内尚未射进模穴的塑料会维持在熔融状态,等充填下一个塑件时再进入模穴,所以不会变成浇口废料。
热流道系统也称作热歧管系统(hotmanifoldsystems)或无流道成形(runnerlessmolding)。
常用的热流道系统包括:
绝热式和加热式两种。
使用绝热式流道(insulatedrunners)的模具,其模板有足够大的通道,于射出成形时,接近流道壁面塑料的绝热效果加上每次射出熔胶之加热量,就足以维持熔胶流路的通畅,如图1-1(a)所示。
加热式流道(heatedrunners)系统有内部加热与外部加热两种设计。
内部加热式如图1-1(b),由内部的热探针或鱼雷管加热,提供了环形的流动通道。
藉由熔胶的隔热作用可以减少热量散失到模具。
外部加热式提供了内部的流动通道,并由隔热组件与模具隔离以降低热损失,如图1-1(c)。
表5-2列出三种热流道的优缺点。
表1-2各种流道系统之优缺点
热流道种类
优点
缺点
绝热式
设计较简单
成本较低
会在浇口处产生不必要的凝固层。
必须以短周期时间维持熔融状态。
需要较长的起动时间以到达稳定的熔胶温度。
有充填不均之问题。
内部加热式
改善热分布情形
成本较高,设计较复杂。
应注意流动平衡和复杂的温度控制。
应考虑模具的不同组件之间的热膨胀。
外部加热式
温度控制较佳
成本较高,设计较复杂。
应考虑不同的模具组件之间的热膨胀。
图1-1热流道系统之种类:
(a)绝热式、(b)内部加热式、和(c)外部加热式。
1-2流道平衡
如果可能的话,应使用自然平衡流道系统来平衡进入模穴的熔胶流动。
让熔胶平衡地流入模穴是高品质塑件之先决条件,藉由改变流道的尺寸与长度可以达成自然平衡的流道系统。
假如无法达成自然平衡之流道系统,可以改用人工平衡流道系统,经由改变浇口尺寸获得相似的平衡充填,但是会显著地影响浇口的冷凝时间,进一步影响塑件的均质。
应用模流分析软件的流道平衡工具,可以使人工平衡流道系统变得更节省时间和成本,并且获得平衡充填的塑件,参阅图1-7。
图1-7人工平衡流道系统之成形塑件
要平衡流道系统,促成熔胶流向距离竖浇道最遥远的模穴,可以缩减充填其它模穴的流道口径。
但必须注意到,太小的流道口径可能使流道内的熔胶提前凝固,造成短射;
另一方面,小口径流道会增加剪切热,使熔胶黏滞性降低,造成更快速的充填。
此外,应该牢记非标准规格的流道口径会增加模具的制作成本与维修成本。
人工平衡流道系统有可能因为塑料差异就射出不同品质的塑件,所以需要更严谨地控制成形条件。
只要成形件稍有变化,充填模式就可能改变,造成不平衡的充填。
在流道设计的最终阶段,模流分析软件可以协助确认流动速率对于流道系统设计的敏感度,并且决定适当的成形条件。
例如,使用鱼骨形流道系统时,不同的进浇速率会造成不同充填模式。
一般而言,低进浇速率将先充饱远离竖浇道的模穴;
高进浇速率则先充饱靠近竖浇道的模穴。
原因在于低进浇速率的熔胶流动到第一个浇口时,会因流动阻力而流向流道的其它部分,等到流道系统内充满熔胶之后,上游的第一个浇口因部分熔胶凝固而产生较大的流动阻力,于是,下游的模穴较先充饱,如图1-8所示。
图1-8使用不同射出速度之不平衡流道系统的流动模式
1-2-1流道设计规则
流道设计对于塑件品质与产能有绝对的影响,本节之流道设计规则提供了流道设计的基本规范。
(1)在流道尺寸方面,流道截面面积不应该小于竖浇道截面面积,以便熔胶可以快速流到浇口区域。
但是必须注意不要使用太大口径的流道,才能够降低废料量。
选择冷流道口径应考虑能够使用标准刀具加工者优先。
对于大部分的塑料,建议流道最小直径为1.5mm(0.01英吋)。
未加填充材料的塑料之典型流道尺寸可以参考表1-1。
梯形流道的高度与宽度大约相等,而且每边各有5°
~15°
的斜角。
(2)每当流道有分支,其分支流道的直径应该要小于主流道的直径,因为只有较少量的熔胶会流进分支。
而且,从经济观点而言,应减少流道内的的熔胶量,以减少废料。
当主流分流到N个分支流道时,主流道直径(dmain)和分支流道直径(dbranch)的关系为:
dmain=dbranch×
N1/3
(3)考虑熔胶温度,一般而言,小尺寸流道比大尺寸流道为佳,其可以产生较大量的黏滞热,有效地提升熔胶温度,而不必采用高温料管。
不当地应用高温料管可能会导致塑料裂解。
然而,小尺寸流道系统有可能提前凝固,造成短射。
(4)所有的流道必须在交接处设计一冷料井(coldslugwell),帮助熔胶流进流道系统和模穴。
图1-9显示冷料井的长度通常等于流道直径。
流道与另一分支流道相交处,通常在流道延伸处设置冷料井。
图1-9冷料井
(5)流道的设计必须顾及顶出和脱模的方便性,提供适当的剖面和脱模斜角。
对于大部份的塑料而言,必须将流道表面抛光,以方便熔胶流动和顶出塑件。
加长的流道系统应该采用多竖浇道拉杆(multiplespruepullers)和多重顶出位置。
(6)设计热浇道系统时,应咨询塑料供货商,以确定正确的歧管尺寸和进浇量。
1-3浇口设计
浇口是熔胶流进模穴处的小开口,一个塑件的浇口设计包括浇口种类、尺寸和位置。
浇口设计受到塑件设计、模具设计、塑件规格(例如外观、公差、同轴性)、成形塑料、填充材料、模板种类、和经济因素(模具加工成本、成形周期、允许之废料量等)的影响。
浇口设计对于塑件的品质和产量的影响甚巨。
除非熔胶的流动长度超过实用上的限制,而必须使用多浇口系统,否则最好采用单浇口。
多浇口系统通常会产生缝合线和熔合线的问题。
单浇口系统可以确保材料、温度的均匀分布和均匀的保压,以及较佳的分子链配向性。
虽然单浇口系统模具的最初加工成本较高,但是废料少,塑件品质佳等结果使其值回票价。
图1-10显示浇口尺寸的名词。
和塑件及流道比较,浇口截面通常很小,所以塑件可以很容易地去除浇口而不会留下浇口痕迹。
通常浇口厚度大约是塑件厚度的2/3。
由于浇口处的塑料凝固可以视为保压阶段的结束,大截面的浇口可以减少黏滞热热,大截面浇口容许使用较低进浇速度进浇,使用较高的保压压力进行较长时间的保压,以提高塑件的材料密度。
假如必须考虑塑件的外观、低残留应力和较佳尺寸稳定性等因素,就应该选用较大的浇口。
图1-10浇口各个尺寸之名称
浇口位置之选择,应该确保均匀快速地充填,而且将缝合线/熔合线和排气孔安排到最不影响塑件外观或强度的区域。
另外,熔胶流动的高压力和高流动速度使得浇口附近产生极高的残留应力,所以应将浇口设置在远离塑件承受外来高应力的区域。
浇口应远离塑件之薄截面区域或肉厚突然变化区域,以避免迟滞现象或产生凹痕与空洞。
1-3-1浇口种类
浇口有许多类型,根据去除浇口方式方类可以区分为人工去除式浇口(manuallytrimmedgates)和自动去除式浇口(automaticallytrimmedgates)。
(A)人工去除式浇口
人工去除式浇口需要作业员二次加工切除浇口,其使用的原因包括:
浇口太大,必须移到模具外面再予以剪除。
对于剪切应力很敏感的塑料(例如PVC),应避免采用自动去除式浇口。
来自不同方向的熔胶同时流过大的截面积,而且要求纤维的配向性时,应避免自动去除式浇口。
人工去除式浇口有下列形式:
直接浇口、凸片浇口、边缘浇口、重迭式浇口、扇形浇口、盘状浇口、环状浇口、辐状浇口、和薄膜浇口。
(1)直接浇口
直接浇口(directgate)又称为竖浇道浇口(spruegate)如图1-11,通常使用于单模穴模具,塑料以最小的压力降直接从竖浇道填入模穴。
此类浇口于剪除后容易在塑件表面留下浇口痕迹。
直接浇口的凝固受控制于塑件肉厚,而不是浇口厚度。
通常塑件在接近直接浇口区域的收缩不大,但在直接浇口处有大量的收缩,结果造成浇口处的大量拉伸应力。
直接浇口入口端的直径与射出机喷嘴直径有关系,此浇口入口直径必须比射出机喷嘴直径大1mm以上。
标准竖浇道衬套具有2.4°
锥度向塑件端开口,因此,直接浇口的长度控制着塑件端的浇口根部直径,此浇口根部直径至少要比塑件肉厚大1.5mm以上,或者大约取塑件浇口肉厚的2倍。
直接浇口锥角至少要1°
,太小的锥角可能在顶出时使竖浇道无法与竖浇道衬套分离;
太大的锥角则浪费塑料,并且加长冷却时间。
非标准锥角的竖浇道加工成本较高,却没有什么好处。
图1-11直接浇口
(2)凸片浇口
凸片浇口(tabgate)如图1-12,通常使用于扁平塑件或薄塑件,以减小模穴内的剪应力。
浇口周遭的高剪应力只发生在辅助凸片,并且将于成形后剪除。
凸片浇口经常应用于PC、压克力、SAN和ABS等树脂的成形。
凸片的最小宽度是1.4mm,最小厚度为模穴肉厚的75%。
(3)边缘浇口
侧边浇口(edgegate)又称为标准浇口(standardgate),如图1-13所示,通常位于模具的分模在线,而且从塑件的侧边、上方或下方充填。
典型边缘浇口尺寸为塑件厚度的1%~75%,或是0.4~1.4mm,宽度为1.1~12.7mm,浇口面长度不应超过1.0mm,最佳值为0.5mm。
图1-12凸片浇口图1-13边缘浇口
(4)重迭浇口
重迭浇口(overlapgate)与边缘浇口类似,如图1-14所示,但是重迭浇口与塑件侧壁或表面有重迭。
重迭浇口通常用来防止喷流效应。
典型重迭浇口尺寸为0.4~1.4mm厚,1.1~12.7mm宽。
(5)扇口浇口
扇形浇口(fangate)如图1-15,是厚度逐渐改变的宽边浇口,具有大充填面积,可以让熔胶迅速地充填大型塑件。
大型塑件非常在乎翘曲问题和尺寸的稳定性,使用扇形浇口可以让大型塑件的熔胶波前均匀地充填模穴。
扇形浇口的宽度和厚度具有锥度,并且要维持固定的熔胶波前面积,以确保固定的熔胶速度,让熔胶在整个浇口的宽边以相同压力进行充填。
如同其它的人工去除式浇口,扇形浇口的最大厚度不超过塑件的肉厚的75%。
典型的扇形浇口厚度为0.25~1.1mm,宽度从1.4mm到模穴侧边长度的25%。
(1)盘状浇口
盘状浇口(diskgate)又称为薄膜浇口(diaphragmgate),如图1-11所示,常用在内侧有开口的圆柱体或圆形,并且需要高度同轴性的塑件,或是不容许有缝合线的塑件。
基本上,盘状浇口是在塑件的内缘使用毛边状的浇口,熔胶从同轴的竖浇道充填进入模穴,很容易获得熔胶均匀流动的塑件。
盘状浇口厚度通常是0.25~1.27mm。
图1-14重迭浇口图1-15扇口浇口
(7)环状浇口
环状浇口(ringgate)如图1-17,也应用于圆柱体或圆形塑件,塑料先沿着模心环绕,然后再沿着圆管向下充填。
环状浇口并不适用在所有的塑件。
环状浇口的厚度通常为0.25~1.1mm。
图1-11盘状浇口图1-17环状浇口
(8)辐状浇口
辐状浇口(spokegate)如图1-18,也称为四点浇口(four-pointgate)或者十字浇口(crossgate),它适用于管状塑件,具有容易去除浇口和节省塑料的优点。
但是可能会造成缝合线,也无法获得完美的真圆度。
辐状浇口通常是0.8~4.8mm厚,1.1~1.4mm宽。
(9)薄膜浇口
薄膜浇口(filmgate)如图1-19,又称为毛边浇口(flashgate),薄膜浇口与环状浇口类似,但使用于边缘平直的塑件,它具有平直的浇口,浇口宽度可以跨接整个模穴边缘或是部份的模穴。
薄膜浇口适用于压克力塑件,而且常常用在又大又平整的塑件,以保持最小量的翘曲。
薄膜浇口尺寸很小,厚度大约是0.25~0.13mm,宽度大约为0.13mm。
图1-18辐状浇口图1-19薄膜浇口
(B)自动式去除式浇口
自动去除式浇口与模具动作配合,在顶出塑件时剪断浇口。
它们应用于:
避免去除浇口的二次加工。
维持均一的周期时间
使浇口痕迹最小化。
自动去除式浇口包括下列各类型:
针状浇口、潜式浇口、热流道浇口、和阀浇口。
(1)针状浇口
针状浇口(pingate)如图1-20,通常应用于三板模,其流道系统位于模板的一组分模在线,塑件模穴接在主要分模在线。
具有倒锥角的浇口在平行于模板运动方向穿透中间模板。
当打开模穴主分模线时,针状浇口的小直径端从塑件撕离,再打开流道分模线即可顶出流道废料。
此系统也可以先打开流道分模线,再使用辅具撕下流道废料。
针状浇口最常使用在单一塑件多点进浇,以确保对称的充填,或是缩短流道长度以确保整个塑件的保压操作。
典型的针状浇口的直径0.25~1.1mm。
(2)潜式浇口
潜式浇口(submarinegate)或称为隧道浇口(tunnelgate)、凿子浇口(chiselgate),如图1-21所示,使用于两板模,在分模线以下,流道末端与模穴之间加工一倾斜之锥状隧道。
于顶出塑件和流道时,浇口会与塑件分离。
典型的潜式浇口直径为0.25~2.0mm,浇口由粗变细,直到成为球状端点。
假如塑件的非功能区具有大直径的针状特征,可以将它与潜式浇口连接,以减低加工成本。
假如针状特征发生在隐藏面,亦可以不将他去除。
将多重潜式浇口设计在圆柱体的内面,可以取代盘状浇口,并且具备自动去除浇口的功能,其获得塑件的外围真圆度虽然比盘状浇口塑件的真圆度差,但通常也还可以接受。
图1-20针状浇口图1-21潜式浇口
(3)热流道浇口
热流道浇口(hot-runnergate)或称为热探针浇口(hot-probegate),如图1-22所示,通常从电热式竖浇道和加热流道直接传送熔胶进入模穴,以产生无流道的塑件。
其保压周期受控制于塑件浇口附近的凝固情形。
当模板打开时,相当高温的塑料将自模穴撕开。
(4)阀式浇口
阀式浇口(valvegate)如图1-23,在热流道浇口内增加一针杆,以便在浇口凝固之前关闭浇口。
它可以应用在较大的浇口而不会产生浇口痕迹。
因为保压周期受控于针杆,阀式浇口可以得到较佳的保压周期和较稳定的塑件品质。
图1-22热流道浇口图1-23阀式浇口
1-3-2浇口设计原则
设计恰当的浇口可以均匀迅速、单一方向地传送熔胶以充