刘姗的论文Word格式文档下载.docx
《刘姗的论文Word格式文档下载.docx》由会员分享,可在线阅读,更多相关《刘姗的论文Word格式文档下载.docx(47页珍藏版)》请在冰豆网上搜索。
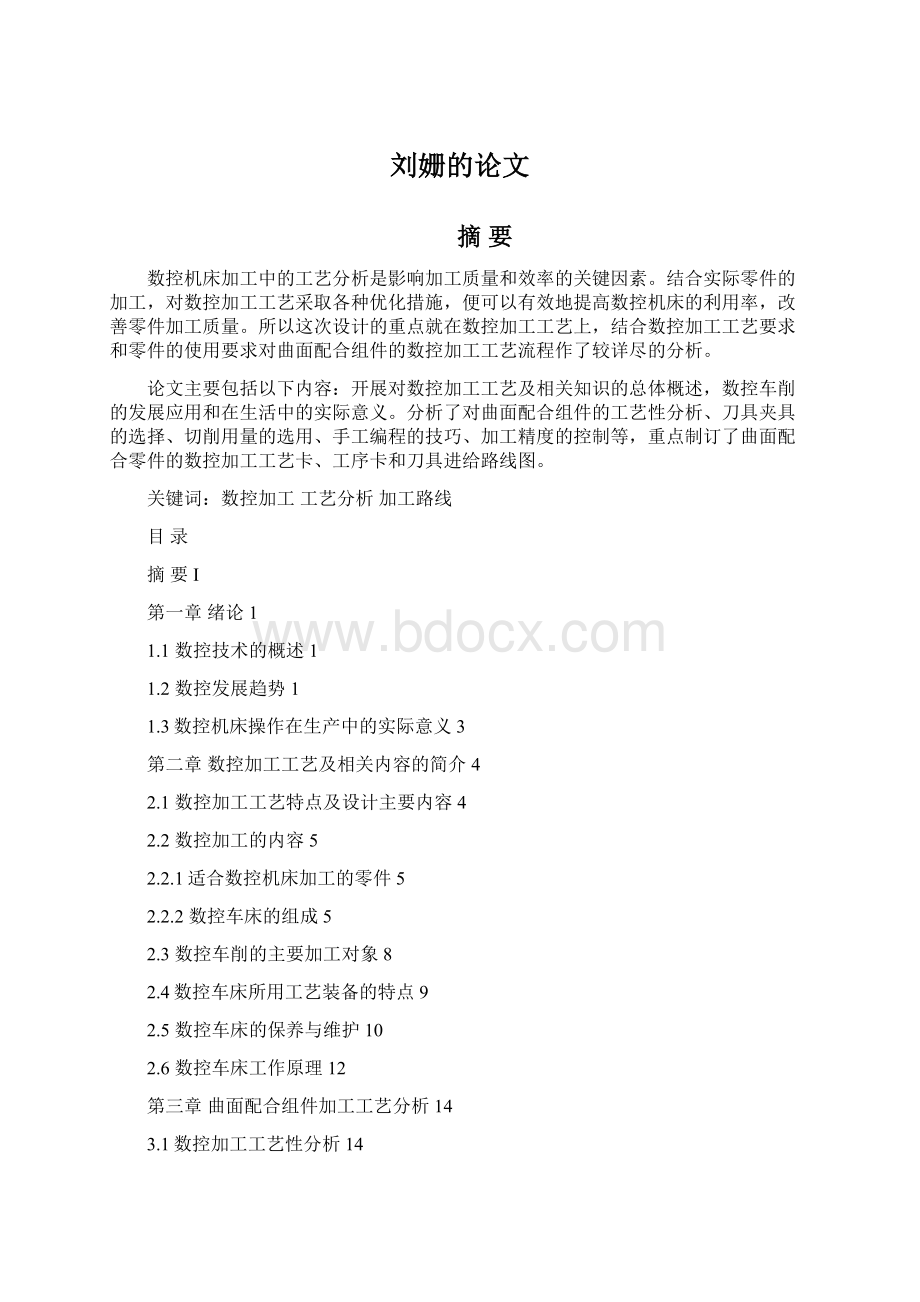
3.2数控车削用夹具16
3.2.1夹具的选择16
3.2.2夹具的类型17
3.3刀具的选择17
3.3.1常用车床用刀具18
3.3.2车削用量的选择18
3.4曲面配合组件实例分析21
3.4.1零件工艺分析内容24
3.4.2编程误差及其控制25
3.4.3加工精度的内容介绍26
3.4.4表面质量27
第四章数控加工程序编制30
4.1编程技巧30
4.2工序卡的制定及编程31
第五章总结与展望44
5.1总结44
5.2展望44
致谢45
参考文献46
第一章绪论
1.1数控技术的概述
数控技术就是指一种采用计算机对机械加工过程中的各种控制信息进行数字化运算、处理、并驱动单元对机械执行构件进行自动化控制的技术。
世界各工业发达国家通过发展数控技术、建立数控机床产业,促使制造业跨入一个新的发展阶段,给国民经济的结构带来了巨大的变化。
数控机床是世界第三次产业革命的重要内容,它不但是机电工业的重要基础装备,还是汽车、石化、电子和现代医疗装备等产业现代化的主要手段。
虽然数控机床产业本身的产值远不如汽车、化工等产业,但高效的数控机床给制造业带来了现代化的生产方式以及高倍率的效益增长,这是促进国民经济发展的巨大源动力。
特别是数控技术在制造业的扩展与延伸所产生的辐射作用和波及效果,足以给机械制造业的产业结构、产品结构、制造方式及管理模式等带来深刻的变化。
近年来,我国对数控加工和数控设备的应用呈突飞猛进之势,包括以组合机床为主的大量生产方式现在都向以数控设备为主的生产方式转变,社会上对掌握数控技术的人才需求越来越大,特别是对掌握数控加工技术的人才需求量更大。
我国数控技术起步于1958年,由清华大学研制出了最早的样机。
近50年的发展历程大致可分为3个阶段:
第一阶段从1958年到1979年,即封闭式发展阶段。
在此阶段,由于国外的技术封锁和我国的基础条件的限制,数控技术的发展较为缓慢。
第二阶段是在国家的“六五”、“七五”期间以及“八五”的前期,即引进技术,消化吸收,初步建立起国产化体系阶段。
在此阶段,由于改革开放和国家的重视,以及研究开发环境和国际环境的改善,我国数控技术的研究、开发以及在产品的国产化方面都取得了长足的进步。
第三阶段是在国家的“八五”的后期和“九五”期间,即实施产业化的研究,进入市场竞争阶段。
在此阶段,我国国产数控装备的产业化取得了实质性进步。
在“九五”末期,国产数控机床的国内市场占有率达50%,配国产数控系统(普及型)也达到了10%。
数控加工技术的应用和普通机床的数控化改造已成为传统机械制造业提高竞争力、摆脱困境的有效途径。
当今世界各国制造业广泛采用数控技术,以提高制造能力和水平,提高对动态多变市场的适应能力和竞争能力。
数控技术及装备是发展新兴高新技术产业和尖端工业的使用技术和最基本的装备,装备工业的技术和现代化程度,正决定着整个国民经济的水平和现代化程度。
1.2数控发展趋势
数控技术的应用不但给传统制造业带来了革命性的变化,使制造业成为工业化的象征,而且随着数控技术的不断发展和应用领域的扩大,他对国计民生的一些重要行业(IT、汽车、轻工、医疗等)的发展起着越来越重要的作用,因为这些行业所需装备的数字化已是现代发展的大趋势。
从目前世界上数控技术及其装备发展的趋势来看,其主要研究热点有以下几个方面:
1.高速、高精密化
效率、质量是先进制造技术的主体。
高速、高精加工技术可极大地提高效率,提高产品的质量和档次,缩短生产周期和提高市场竞争能力。
为此日本先端技术研究会将其列为5大现代制造技术之一,国际生产工程学会(CIRP)将其确定为21世纪的中心研究方向之一。
2.轴联动加工和复合加工机床快速发展
采用5轴联动对三维曲面零件的加工,可用刀具最佳几何形状进行切削,不仅光洁度高,而且效率也大幅度提高。
一般认为,1台5轴联动机床的效率可以等于2台3轴联动机床,特别是使用立方氮化硼等超硬材料铣刀进行高速铣削淬硬钢零件时,5轴联动加工可比3轴联动加工发挥更高的效益。
但过去因5轴联动数控系统、主机结构复杂等原因,其价格要比3轴联动数控机床高出数倍,加之编程技术难度较大,制约了5轴联动机床的发展。
当前由于电主轴的出现,使得实现5轴联动加工的复合主轴头结构大为简化,其制造难度和成本大幅度降低,数控系统的价格差距缩小。
因此促进了复合主轴头类型5轴联动机床和复合加工机床(含5面加工机床)的发展。
3.智能化、柔性化、网络化、集成化
数控系统引入了自适应控制、模糊系统和神经网络的控制机理,不但具有模糊控制、学习控制、自适应控制、三维刀具补偿、运动参数运动补偿等功能,而且具有故障诊断专家系统,使自诊断和故障监控功能更趋完善。
21世纪的数控装备将是具有一定智能化的系统,智能化的内容包括在数控系统中的各个方面:
为追求加工效率和加工质量方面的智能化,如加工过程的自适应控制,工艺参数自动生成;
为提高驱动性能及使用连接方便的智能化,如前馈控制、电机参数的自适应运算、自动识别负载自动选定模型、自整定等;
简化编程、简化操作方面的智能化,如智能化的自动编程、智能化的人机界面等;
还有智能诊断、智能监控方面的内容、方便系统的诊断及维修等。
4.重视新技术标准和规范的建立
数控标准是制造业信息化发展的一种趋势。
数控技术诞生后的50年间的信息交换都是基于ISO6983标准,即采用G,M代码描述如何(how)加工,其本质特征是面向加工过程,显然,他已越来越不能满足现代数控技术高速发展的需要。
为此,国际上正在研究和制定一种新的CNC系统标准ISO14649(STEP-NC),其目的是提供一种不依赖于具体系统的中性机制,能够描述产品整个生命周期内的统一数据模型,从而实现整个制造过程,乃至各个工业领域产品信息的标准化。
1.3数控机床操作在生产中的实际意义
数控机床是根据加工程序对工件进行自动加工的先进设备,工件的加工质量主要由机床的加工精度、工艺和加工程序的质量决定,基本上排除了机床操作人员手工操作技能的影响,但对操作者的综合素质提出了较高的要求。
尤其是在我国开始逐渐普及数控加工技术的初期,很多企业拥有先进的数控机床,但数控加工工艺及加工程序的质量却很低,数控机床操作人员的数量和素质不能满足数控加工快速发展的要求,导致产品质量差,加工效率低。
目前,符合数控加工实际需要的数控机床操作人员还存在较大的缺口。
数控机床是典型的机、电、液、气一体化的设备,对操作人员的要求较高,是国家劳动和社会保障部要求持职业资格证书上岗的技术复杂性工种。
数控机床的操作不同于普通机床操作者的经验和手工技巧的要求,需要操作人员具有较好的工艺基础知识和较高的综合素质,能够不断了解和掌握先进加工技术的实际应用。
数控机床要按照数控加工程序自动进行零件加工,必须由机床操作人员具体实施。
可以说,数控加工工艺方案是通过机床操作人员在数控机床上实现的,数控加工现场经验的积累又是提高数控加工工艺和数控加工程序质量的基础。
因此,数控机床的操作是企业生产过程中一个重要的环节,数控机床操作人员的素质和水平将直接影响企业的生产效率、产品质量以及生产成本,高素质的机床操作人员是保证数控加工工艺得以正确和顺利实施的重要条件之一。
第二章数控加工工艺及相关内容的简介
2.1数控加工工艺特点及设计主要内容
数控机床的加工工艺与通用机床的加工工艺有许多相同之处,但在数控机床上加工零件比通用机床加工零件的工艺规程要复杂得多。
在数控加工前,要将机床的运动过程、零件的工艺过程、刀具的形状、切削用量和走刀路线等都编入程序,这就要求程序设计人员具有多方面的知识基础。
合格的程序员首先是一个合格的工艺人员,否则就无法做到全面周到地考虑零件加工的全过程,以及正确、合理地编制零件的加工程序。
1.数控加工工艺内容要求更具体、详细
普通加工工艺上的许多具体的工艺问题,如工步的划分和安排、刀具的几何形状与尺寸、走刀路线、加工余量、切削用量等,在很大程度上由操作人员根据实际经验和习惯自行考虑和决定,工艺人员在设计工艺规程时不必进行过多的规定,零件的尺寸精度可由试切保证。
数控加工工艺的所有工艺问题必须事先设计和安排好,并编入加工程序中。
数控工艺不仅包括详细的切削加工步骤,还包括夹具型号、规格、切削用量和其他特殊要求,以及标有数控加工坐标位置的工序图等。
2.数控加工工艺要求更严密、精确
采用数控加工工艺加工时,自适应性较差,加工过程中可能遇到的所有问题必须事先精心考虑,否则将导致严重后果。
3.数控加工零件图形的数学处理和编程尺寸设定值的计算
编程尺寸并不是零件图上设计的尺寸的简单再现。
在对零件图进行数学处理和计算时,编程尺寸设定值要根据零件尺寸公差要求和零件的形状几何关系重新调整计算,才能确定合理的编程尺寸。
4.考虑进给速度对零件形状精度的影响
制定数控加工工艺时,选择切削用量要考虑进给速度对加工零件形状精度的影响。
在数控加工中,刀具的移动轨迹是插补运算完成的。
根据插补原理分析,在数控系统已定的条件下,进给速度越快,则插补精度越低,导致工件的轮廓形状精度越差。
尤其是高精度加工时,这种影响非常明显。
5.数控加工工艺的特殊要求
(1)由于数控机床比普通机床的刚度高,所配的刀具也较好,因此在同等情况下,数控机床切削用量比普通机床大,加工效率也较高。
(2)数控机床的功能复合化程度越来越高,因此现代数控加工工艺的特点是工序相对集中,表现为工序数目少,供需内容多,由于在数控机床上尽可能安排较复杂的工序,所以数控加工的工序内容比普通机床的加工工序内容复杂。
(3)由于数控机床加工的零件比较复杂,因此在确定装夹方式和夹具设计时,要特别注意刀具与夹具、工件的干涉问题。
2.2数控加工的内容
(1)通过数控加工的适应性分析选择并确定进行数控加工的零件的内容。
(2)结合加工表面的特点和数控设备的功能对零件进行数控加工的工艺分析。
(3)进行数控加工的工艺设计。
(4)根据编程的需要,对零件图形进行数学处理和计算。
(5)编写加工程序单。
(6)按照程序单制作控制介质。
(7)检验与修改加工程序。
(8)首件试加工以进一步修改程序,并对现场问题进行处理。
(9)编制数控加工工艺技术文件。
2.2.1适合数控机床加工的零件
(1)多品种中小批量零件最合适。
随着数控车床制造成本的逐步下降,现在不管是国内还是国外,加工大批量零件的情况也已经出现。
加工很小批量和单件生产时,如能缩短程序的调试时间(机外编程与调试)和工装(刀、量、夹具)的准备时间也是可以选用的。
(2)精度要求高的零件。
由于数控车床的刚性好,制造精度高,对刀精确,能方便的进行尺寸补偿,所以能加工尺寸精度要求高的工件。
(3)表面粗糙度值小的零件。
在工件和刀具的材料、精车余量及刀具角度一定的情况下,表面粗糙度取决于切削速度和进给速度。
普通车床是恒定转速,直径不同,切削速度(线速度)不同,而数控车床具有恒线速度切削功能,车端面、不同直径外圆时可以用同样的线速度,保证表面粗糙度值既小又一致;
在车削表面粗糙度不同的表面时,粗糙度小的表面选用小的进给速度,粗糙度大的表面选用大些的进给速度,可变性很好,这点在普通车床很难做到。
(4)轮廓形状复杂的零件。
任意平面曲线都可用直线或圆弧来逼近,数控车床具有圆弧插补功能,因此数控车床不仅可以加工素线为直线的回转体,也可以加工素线为曲线的回转体。
2.2.2数控车床的组成
组成一台完整的数控机床,主要由控制介质、数控装置、伺服系统和机床四部分及辅助装置组成,如图2-1所示:
图2-1数控车床的组成
1.数控车床的分类
数控车床的品种和规格繁多,一般可以用下面三种方法分类。
(1)按控制系统分
目前市面上占有率较大的有法拉克、华中、广数、西门子、三菱等。
(2)按运动方式分类
①点位控制数控车床
②点位/直线控制数控车床
③连续控制数控车床
(3)按控制方式分类
按控制方式分类可以分为开环控制数控车床、闭环控制数控车床和半闭环控制数控车床。
2.数控车床的性能指标
(1)主要规格尺寸:
数控车床主要有床身与刀架最大回转直径、最大车削长度、最大车削直径等。
(2)主轴系统:
数控车床主轴采用直流或交流电动机驱动,具有较宽调速范围和较高回转精度,主轴本身刚度与抗振性比较好。
现在数控车床主轴普遍达到5000~10000r/min甚至更高的转速,对提高加工质量和各种小孔加工极为有利;
主轴可以通过操作面板上的转速倍率开关调整转速;
在加工端面时主轴具有恒线切削速度(恒线速单位:
mm/min),是衡量车床的重要性能指标之一。
(3)进给系统:
该系统有进给速度范围、快速(空行程)速度范围、运动分辨率(最小移动增量)、定位精度和螺距范围等主要技术参数。
进给速度是影响加工质量、生产效率和刀具寿命的主要因素,直接受到数控装置运算速度、车床特性和工艺系统刚度限制。
数控车床的进给速度可达到10~30m/min其中最大进给速度为加工的最大速度,最大快进速度为不加工时移动的最快速度,进给速度可通过操作面板上的进给倍率开关调整。
脉冲当量(分辨率)是CNC重要的精度指标。
有其两个方面的内容,一是车床坐标轴可达到的控制精度(可以控制的最小位移增量),表示CNC每发出一个脉冲时坐标轴移动的距离,称为实际脉冲当量或外部脉冲当量;
二是内部运算的最小单位,称之为内部脉冲当量,一般内部脉冲当量比实际脉冲当量设置得要小,为的是在运算过程中不损失精度,数控系统在输出位移量之前,自动将内部脉冲当量转换成外部脉冲当量。
数控车床的加工精度和表面质量取决于脉冲当量数的大小。
普通数控车床的脉冲当量—,般为0.001mm,简易数控车床的脉冲当量一般为0.01mm,精密或超精密数控车床的脉冲当量一般为0.0001mm,脉冲当量越小,数控车床的加工精度和表面质量越高。
定位精度和重复定位精度:
定位精度是指数控车床各移动轴在确定的终点所能达到的实际位置精度,其误差称为定位误差。
定位误差包括伺服系统、检测系统、进给系统等的误差,还包括移动部件导轨的几何误差等。
它将直接影响零件加工的精度。
重复定位精度是指在数控车床上,反复运行同一程序代码,所得到的位置精度的一致程度。
重复定位精度受伺服系统特性、进给传动环节的间隙与刚性以及摩擦特性等因素的影响。
一般情况下,重复定位精度是呈正态分布的偶然性误差,
它影响一批零件加工的一致性,是一项非常重要的精度指标。
一般数控车床的定位精度为0.001mm,重复定位精度为±
0.005mm。
(4)刀具系统:
数控车床包括刀架工位数、工具孔直径、刀杆尺寸、换刀时间、重复定位精度各项内容。
加工中心刀库容量与换刀时间直接影响其生产率,换刀时间是指自动换刀系统,将主轴上的刀具与刀库刀具进行交换所需要的时间,换刀一般可在5~20s的时间内完成。
数控车床性能指标还有电机、冷却系统、车床外形尺寸、车床重量等。
3.数控车床的特点
与普通车床相比,数控车床具有以下几个特点:
(1)适应性强
由于数控车床能实现多个坐标的联动,所以数控车床能加工形状复杂的零件,特别是对于可用数学方程式和坐标点表示的零件,加工非常方便。
更换加工零件时,不需数控车床的机械部分和控制部分的硬件,只需更换零件加工的NC程序。
这一特点不仅满足了当前产品更新快的市场竞争需要,而且较好的解决了单件、中小批量和多变产品的加工问题。
(2)加工质量稳定
对于同一批零件,由于使用同一车床和刀具及同一加工程序,刀具的运动轨迹完全相同这就保证了零件加工的一致性好,且质量稳定。
(3)效率高
数控车床的主轴转速及进给范围比普通车床大。
目前数控车床最高进给速度可达到100m/min以上,最小分辨率达0.01um。
一般来说,数控车床的生产能力约为普通车床的三倍,甚至更高。
数控车床的时间利用率高达90%,而普通车床仅为30%~50%。
(4)精度高
数控车床有较高的加工精度,一般在0.005mm~0.1mm之间。
数控车床的加工精度不受零件复杂程度的影响,车床传动链的反向齿轮间隙和丝杠的螺距误差等都可以通过数控装置自动进行补偿。
因此,数控车床的定位精度比较高。
(5)减轻劳动强度
在输入程序并启动后,数控车床就自动地连续加工,直至完毕。
这样就简化了工人的操作,使劳动强度大大降低。
还有能实现复杂的运动、产生良好的经济效益、利于生产管理现代化等特点。
2.3数控车削的主要加工对象
对于一个零件来说,并非全部加工工艺过程都适合在数控车床上完成,而往往只是其中的一部分工艺内容适合数控加工。
这就需要对零件图样进行仔细的工艺分析,选择那些最适合、最需要进行数控加工的内容和工序。
在考虑选择内容时,应结合本企业设备的实际,立足于解决难题、攻克关键问题和提高生产效率,充分发挥数控加工的优势。
1.适于数控加工的内容
在选择时,一般可按下列顺序考虑:
(1)通用车床无法加工的内容应作为优先选择内容;
(2)通用车床难加工,质量也难以保证的内容应作为重点选择内容;
(3)通用车床加工效率低、工人手工操作劳动强度大的内容,可在数控车床尚存在富裕加工能力时选择。
2.不适于数控加工的内容
一般来说,上述这些加工内容采用数控加工后,在产品质量、生产效率与综合效益等方面都会得到明显提高。
相比之下,下列一些内容不宜选择采用数控加工:
(1)占机调整时间长。
如以毛坯的粗基准定位加工第一个精基准,需用专用工装协调的内容;
(2)加工部位分散,需要多次安装、设置原点。
这时,采用数控加工很麻烦,效果不明显,可安排通用车床补加工;
(3)按某些特定的制造依据(如样板等)加工的型面轮廓。
主要原因是获取数据困难,易于与检验依据发生矛盾,增加了程序编制的难度。
2.4数控车床所用工艺装备的特点
(1)刀架的特点
刀架是数控车床的重要部件,它安装各种切削加工刀具,其结构直接影响机床的切削性能和工作效率。
转塔式刀架是普遍采用的刀架形式,如图2-2所示。
它通过转塔头的旋转、分度、定位来实现机床的自动换刀工作。
两轴连续控制的数控车床,一般都采用6~12工位转塔式刀架。
排刀式刀架主要用于小型数控车床,适用于短轴或套类零件加工。
方刀架在中低档数控车床中也有使用。
图2-2转塔式刀架
(2)刀具的特点
数控机床刀具应满足以下要求:
①精度较高、寿命高、尺寸稳定、变化小。
数控车床能兼作粗精车削,为使粗车能大切深、大走刀,要求粗车刀具有强度高、耐用度好;
精车则保证加工精度,所以要求刀具锋利、精度高、耐用度好。
②快速换刀。
③刀柄应为标准系列。
④能很好地控制切屑的折断、卷曲和排出;
数控车床一般在封闭环境中进行,要求刀具具有良好的断屑性能,断屑范围要宽,一般采用三维断屑槽,其形式很多,选择时应根据零件的材料及精度要求来确定。
⑤具有很好的可冷却性能。
从结构上看:
车刀可分为整体式车刀、焊接式车刀和机械夹固式车刀三大类。
整体式车刀主要是整体式高速钢车刀,它具有抗弯强度、冲击韧性好,制造简单和刃磨方便、刃口锋利等优点;
焊接式车刀是将硬质合金刀片用焊接的方法固定在刀体上,经刃磨而成;
机械夹固式车刀可分为机械夹固式可重磨车刀和机械夹固式不可重磨车刀。
数控车床应尽可能使用机夹刀。
由于机夹刀在数控车床上安装时,一般不采用垫片调整刀尖高度,所以刀尖高的精度在制造时就得到保证。
对于长径比较大的内径刀杆,应具有良好的抗震结构。
从刀具的形状看,数控车削加工中常用的车刀如图2-3所示。
从刀具的材料看,由于在数控加工中,速度要远高于普通加工,为适合因高速
图2-3数控车削刀具
而带来的高切削温度及严重摩擦,而不致使刀具磨损过于迅速,数控加工刀具以硬质合金为主,一般采用YT、YW类硬质合金加工钢料,YG类硬质合金加工铸铁。
为不断提高刀具切削性能,数控刀具中,越来越多地采用涂层硬质合金,涂层材料及涂层技术的迅猛发展,为数控刀具的性能提高提供了良好的条件。
除此之外,数控刀具中,亦有采用CBN、金属复合陶瓷等特硬材料的。
(3)夹具的特点
高精度。
数控机床精度很高,一般用于高精度加工。
对数控机床夹具也提出较高的定位安装精度要求和转位、定位精度要求。
快速装夹工件。
为适应高效率、自动化加工的需要,夹具结够应适应快速装夹的需要,以尽量减少工件装夹辅助时间,提高机床切削运转利用率。
为适应快速装夹的需要,夹具常采用液动、气动等快速反应加紧动力。
夹具应具有良好的敞开性。
数控机床加工为刀具自动进给加工,夹具及工件应为刀具的快速移动和换刀等快速动作提供较宽敞的运行空间。
尤其对于需多次进出工件的多刀多工序加工,夹具的结构应尽量简单、开敞,使刀具容易进入,以防刀具运动中与夹具工件系统相碰撞。
夹具本身的机动性要好。
在数控机床加工追求一次装夹条件下,尽量干完所有机加工内容。
2.5数控车床的保养与维护
数控车床具有机、电、液集于一身的,技术密集和知识密集的特点,是一种自动化程度高、结构复杂且又昂贵的先进加工设备。
为了充分发挥其效益,减少故障的发生,必须做好日常维护工作,所以要求数控车床维护人员不仅要有机械、加工工艺以及液压气动方面的知识,也要具备电子计算机、自动控制、驱动及测量技术等知识,这样才能全面了解、掌握数控车床,及时搞好维护工作。
1.选择合适的使用环境:
数控车床的使用环境(如温度、湿度、振动、电源电压、频率及干扰等)会影响机床的正常运转,所以在安装机床时应严格要求做到符合机床说明书规定的安装条件和要求。
在经济条件许可的条件下,应将数控车床与普通机械加工设备隔离安装,以便于维修与保养。
2.应为数控车床配备数控系统编程、操作和维修的专门人员:
这些人员应熟悉所用机床的机械部分、数控系统、强电设备、液压、气压等部分及使用环境、加工条件等,并能按机床和系统使用说明书的要求正确使用数控车床。
3.长期不用数控车床的维护与保养:
在数控车床闲置不用时,应经常经数控系统通电,在机床锁住情况下,使其空运行。
在空气湿度较大的霉雨季节应该天天通电,利用电器元件本身发热驱走数控柜内的潮气,以保证电子部件的性能稳定可靠。
4.数控系统中硬件控制部分的维护与保养:
每年让有经验的维修电工检查一次。
检测有关的参考电压是否在规定范围内,如电源模块的各路输出电压、数控单元参考电压等,若不正常并清除灰尘;
检查系统内各电器元件联接是否松动;
检