二分部移动模架施工方案0501Word下载.docx
《二分部移动模架施工方案0501Word下载.docx》由会员分享,可在线阅读,更多相关《二分部移动模架施工方案0501Word下载.docx(60页珍藏版)》请在冰豆网上搜索。
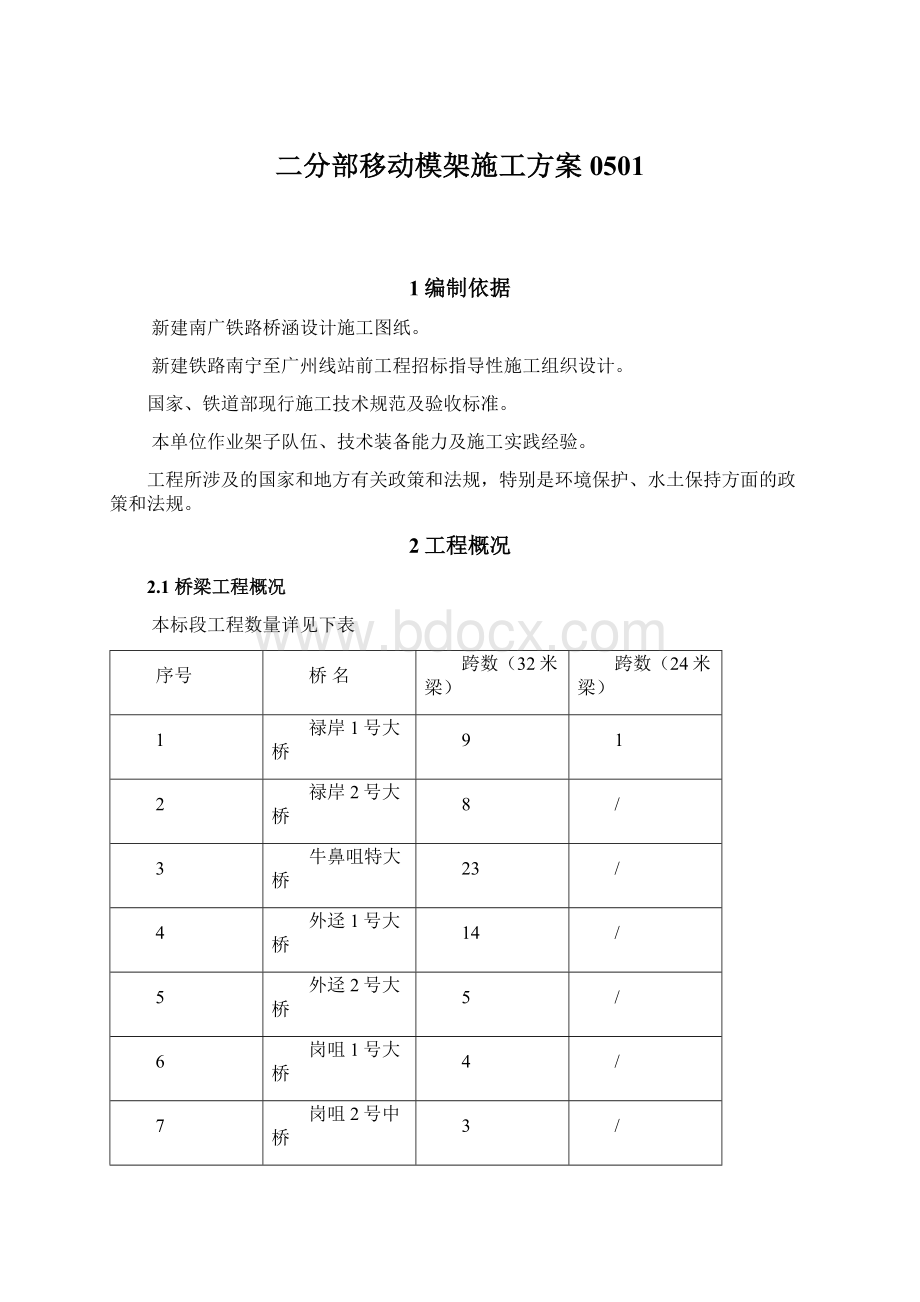
C50
310.6
1.957
54.357
0.011
3.363
0.622
标准型预应力筋钢绞线抗拉强度1860MPa
重量(t)
直线
曲线
11.725
11.975
24米箱梁主要参数表(线间距4.6米)
梁体(24米梁)
241.5
1.481
44.123
2.532
0.545
4.961
5.015
3总体施工布署及施工准备
3.1组织机构与作业队安排
3.1.1施工组织机构
成立南广铁路NGZQ-8标段项目经理部二分部。
项目二分部设六个管理部室,即工程管理部、安质环保部、设备物资部、财务部、实验室和综合办公室。
二分部下设六个工区,在一、三工区各设有桥梁队,用于桥涵施工。
组织机构设置见“工区组织机构图”。
在桥梁移动模架施工的主要技术和管理人员由公司选派,抽调具有丰富的客运专线施工经验、专业技术能力强、综合素质高人员,进行施工任务。
由于客运专线箱梁施工技术难度大,工艺复杂,施工组织采用专业作业队组成流水施工。
工区组织机构图
3.2人员、设备配置
3.2.1移动模架拼装作业人员、设备配置(每套模架)
(1)拼装设备及工具
机具名称
型号
单位
数量
汽车吊
50t
台
冲钉
把
手锤
8磅
5磅
螺栓套筒扳手
M24
M30
M56
倒链
5-10t
液压千斤顶
30-50t
梯子
6m
条
钢丝绳
M
100
枕木
根
水准仪
11
水平尺
12
钢尺
电焊机
氧焊设备
套
(2)拼装作业人员配置
人员分工
指挥员
人
技术员
安全员
电工
起重工
液压工
辅助工
15
合计
26
3.2.2钢筋、预埋件加工设备及人员配置(每套模架)
(1)钢筋及预埋件加工设备
设备名称
规格
闪光对焊机
UN-100w
弯曲机
40b
调直机
交流电焊机
BXI-500
切断机
GQ-40
卷扬机
IT
氧气乙炔
(2)人员配置
人数
备注
钢筋工
电焊工
普工
20
(3)钢筋绑扎人员配置(每套模架)
每班组钢筋工20人,普工10人,合计30人,两班组共60人。
3.2.3预应力施工设备及人员配置(每套模板)
(1)设备配置
电动砂轮切割机
内卡式千斤顶
300t
电动油泵
前卡式千斤顶
20t
真空压浆设备
水泥浆拌制设备
电动葫芦
3t
个
支撑架
负责钢绞线下料、穿束、张拉8人,压浆6人,合计14人。
3.2.4混凝土施工设备及人员配置(每套模架)
振入式振捣器
¢50
¢30
提浆整平机
汽车泵或地泵
振捣工10人,普工12人,合计22人。
3.3混凝土生产及供应
箱梁浇筑砼量大,施工速度要求快,为保证砼生产质量和供应速度,箱梁施工时,采用集中拌合,由混凝土车运至现场进行浇筑。
机械数量表
砼搅拌站
一、三工区各2套
运输车
16
一、三工区各8台
汽车砼输送泵
每台移动模架配2台
固定输送泵
一、三工区各1台
4.施工进度计划
4.1总工期目标
移动模架工法具有作业工序清晰、结构受力明确、模架强度高的特点,能不受地质的条件的限制满足施工作业工况的要求,同时便于开展平行流水作业。
经综合考虑,我们采用郑州大方桥梁机械有限公司针对客运专线设计的上行式移动模架,这种模架占用桥下空间少,对低矮桥墩具有很强的适应性,且首末跨施工方便,能满足通过高压线等障碍物的净空要求。
根据设计工期要求,现浇简支梁2010年12月31日必须完成50%,2011年12月31日前全部完成。
根据工地桥梁,分布广,地理位置复杂等特点加之工期紧,我部采用三套移动模架进行施工,确保在要求工期内完成现浇梁施工。
4.2每孔梁的施工周期
根据移动模架施工周期安排,模板拼装时间为30天,考虑施工场地影响因素,首片梁施工时间为17天,移动模架循环每孔周期为15~16天。
单片梁施工周期表
工序名称
持续(天)
脱、移外模,模架过孔
0.5
绑扎梁底、腹板钢筋
1.5
安装内模、端模
绑扎梁体顶板钢筋
浇筑混凝土
养生
顶张拉(砼强度达到60%)
不占循环时间
拆内模、端模(砼强度达到60%)
初张拉(脱外模)(砼强度达到80%,龄期≥5天)
终张拉、压浆、封锚(砼强度达到100%,龄期≥10天)
合计(天)
说明:
每天工作时间24小时计
5.移动模架施工
5.1移动模架结构及特点
结合本标段的实际情况,经过多方面的比较选择,全部采用郑州大方产的DSZ32/900上行式结构,能够自行倒装支腿。
我单位在其他客运专线项目上已经成功应用,且取得了很好的效果及丰富的施工经验。
DSZ32/900上行式移动模架主要由主框架、后行走结构、后支承、中主支腿、前支腿、起吊小车、吊挂外肋、外模及底模系统、端模系统、外肋横移机构、吊挂外肋横向锁定机构、拆装式内模系统、电气液压系统及辅助设施等部分组成。
上行式移动模架主要特点为:
承重的主梁系统位于桥面上方,外模系统吊挂在承重主梁上,主梁系统通过支腿支撑在梁端或墩顶上。
过孔时外模系统横向开启(或打开)以避开桥墩。
外模系统统一同纵移。
支腿可自行向前倒装。
上行式移动模架占用桥下净空小,对低矮桥墩具有很强的适应性,且施工首跨和末跨或连续梁施工更方便(不需拆除主梁),能够满足通过高压线等障碍物的净空要求。
5.1.1主要技术参数
项目
技术规格及特性
施工工法
逐跨原位现浇
施工梁跨
32m、24m
混凝土梁梁跨重
≤900t
适用纵坡
≤2.0%
适应曲线半径
≥2000m
适用最低墩高
1.65米
后支承最大反力
370t
后行走最大轮压
40t
前支腿托轮最大轮压
起吊小车走行速度
3m/min
5吨电动葫芦起升速度
8m/min,0.8m/min
总电容量
约80kw
最大件尺寸及重量
12m*1.6m*2.9m,重量小于22吨
风力条件
移动时风压小于150N/m2
主梁扰度比
小于L/700
17
移动模架速度
1.5m/min
前移过孔稳定系数
K>1.5
19
工作效率
13天/单孔(按每天工作24小时计)
液压系统压力
31.5MPa/16MPa
21
整机重量
约530t(不含墩顶散模)
22
动力条件
380V
自动化方式
竖向顶落用大吨位分离式千斤顶实现
纵向移位用电机驱动完成
模架横向开、合采用液压油缸完成
5.1.2结构
5.1.2.1主框架组成
主梁系统由并列的2组纵梁+连接梁、挑梁组成,总重225t。
主要吊挂外模板系统等设备重量及钢筋、混凝土等结构材料重量。
每组纵梁由3节承重钢箱梁(12.9m+12m+12m)+3节导梁(3*11m)组成,全长69.9m,相邻两组纵梁中心距为6米。
浇筑状态时,钢箱梁的设计刚度大于1/700。
钢箱梁高2.9米,翼缘板宽1.6米。
钢箱梁接头采用螺栓节点板连结。
每节钢箱梁重量不小于21.5t。
导梁采用空腹式箱梁结构,接头为螺栓节点连结。
钢箱梁盖板和腹板材质为Q345B,主梁接头螺栓GB5782-86,10.9级。
其它钢材质Q235B。
主梁连接系共9组,挑梁每侧8组。
挑梁与连接系位置对应,便于力的对称传递。
5.1.2吊挂外肋、横移机构及锁定机构
吊挂外肋共8组,吊挂安装在主梁的挑梁上,用以支撑外模系统;
吊挂外肋沿中部可以剖分,携带外模系统在横移机构的作用下可以横向打开和合拢;
合拢后由锁定机构锁定,可以避免外肋的横向滑动。
(1)吊挂外肋(DSZ32-08.00.00)
吊挂外肋分为中间标准吊挂外肋6组和边吊挂外肋2组。
边吊挂外肋用以适应首跨和末跨施工。
中间标准吊挂外肋分为4段,由2段上肋、2段下肋和限位装置组成,限位装置用于外肋在主梁挑梁上滑动时,起导向和防止侧翻的功能。
边吊挂外肋分为6段,由2段上肋、2段中肋、2段底肋和限位装置组成,限位装置用以外肋在主梁挑梁上滑动时,起导向和防止侧翻的功能。
1组吊挂约10t。
(2)横移机构(DSZ32-08.00.00):
横移机构由支承座、油缸和连结销轴组成,共16套。
其一端与外肋顶端连结,一端与主梁或挑梁连接,横移机构的油缸循环伸缩,可实现外肋沿挑梁开启和合拢。
(3)横向锁定机构(DSZ32-08A.00.00):
外肋横向合拢后,在外肋外侧的挑梁上安装横向锁定机构,由人工调整锁定机构上螺杆的长度,使其与外肋顶紧,以固定外肋的横向位置。
横向锁定机构工16套。
5.1.2.3外模系统
外模系统由底模、腹模、翼模、可调支撑系组成,模板通过可调支撑系支撑在吊外肋上。
底模由两部分组成,组合位置位于梁体中心线处,施工过程中便于随着吊挂外肋横向打开和合拢(见浇注状态、过孔状态示意图)。
墩身由面板及骨架组焊而成,其腹板及翼模面板厚6mm、底模板厚为8mm;
每块模板在横向和纵向都有螺栓连接。
墩柱处的底模板现场使用散模组立并固定牢靠。
外模板应起拱,起拱度的设置应按造桥机主梁承受的由实际混凝土荷载(包括钢筋)+内模自重产生的曲线特征值以及设计要求的预下拱度进行,以使成桥后桥梁曲线与设计值吻合。
模架就位后,应调整底模标高(侧模、翼模也应随底模一起起拱且必须是同一线型同一拱量),使其与所提供(或修正后)的预拱曲线特征值吻合。
外模及底模纵向标准按4米分段。
外侧模及底模的起拱通过可调支承系实现;
底模共设置32根可调支承杆,外侧模共设置48根可调支承杆。
外模的设计满足32米梁且兼顾24米高梁的预制施工:
将梁端处的腹模和翼模和底模向前移动8米即可实现24米跨高粱的预制施工。
翼模上安装有人行通道,便于人员操作和通过。
外模系统图(DSZ32-07.00.00)
5.1.2.4内模系统
内模系统采用拆装式内模结构,内模设计满足32米梁的制梁施工。
内模面板厚度为5mm。
内模的分块设计充分考虑最后一孔梁浇注完毕后内模出腔的施工要求,内模标准分块尺寸为2000mm*300mm*105mm。
最后一孔梁施工时,混凝土梁顶板应开洞,以适应内模的拆除。
内模系统图(DSZ32-09.00.00)
5.1.2.5后主支腿
后主支腿共1套,位于主梁系统的尾部,支撑于已浇注好的桥梁端部,主要由后走形机构2个、后支承机构(含400t液压支撑油缸,行程150mm)2个等组成。
后行走机构(DSZ32-02.00,00)为轮轨式,电机驱动(8*1.5KW),以实现主梁系统携外模系统纵移过孔。
走行速度1.5m/min。
后走行轮共8个,启动时最大轮压为39.5t,走行至跨中时最大轮压为30.5t。
后支承机构(DSZ32-02.00,00)的竖向支承油缸用于重载支撑,并有机械锁紧螺母,在打梁状态实现机械支撑。
5.1.2.6中主支腿
中主支腿共1套,由支撑立柱、下横联和400t竖向支撑油缸(行程400mm)等组成。
中主支腿固定于主梁系统的中部,直接支撑在墩顶上,纵向距离墩中心0.75m。
中主支腿上桥台或既有桥梁时,需先拆除支撑立柱,400t竖向支撑油缸直接支撑钢箱梁。
前辅助支腿共1套,由托辊机构、上横联合下立柱框架等组成。
前辅助支腿设置在导梁前端,为活动支腿,直接支撑在墩顶,与后走行一起实现模架的纵移过孔。
托辊机构共设8个从动轮,最大轮压为39.5t。
下立柱框架拆除,可以实现上桥台和既有桥梁作业。
5.1.2.7起吊小车
起吊小车共一套,可沿导梁顶部的轨道纵向运动,用于起吊前辅助支腿纵向移位过跨及作为辅助吊机的功能。
吊挂小车主要由四轮台车、2台5t固定式电动葫芦组成,用于吊挂中主支腿下横联和前辅助支腿。
5.1.2.8吊挂走道及5t电动葫芦
在承重跨主梁连接系上设置有两根32米长吊挂工钢,用于2台5t电葫芦的行走。
5.1.2.9液压系统
DSZ32/900上行式移动模架整机共配四套液压系统,每套液压系统由泵站、400t自锁支承油缸(1根)、横移油缸(4根)、液压管路和电气控制系统组成。
(1)液压泵站:
包括油箱、液压泵、电机、吸油滤油器、回油滤油器、电磁换向阀组、压力表、液位液温计等。
其主要参数为:
电机功率:
7.5kw;
工作压力:
29Mpa/16Mpa;
额定压力:
31.5Mpa;
流量:
14.4/Min。
(2)400t垂直支承油缸:
该油缸为特殊订货构件,配有机械锁定机构。
缸径/杆径:
420/300;
最大行程:
150mm/400mm;
最大推力:
400t。
400t垂直支承油缸共4台,安装在造桥机承重主梁前后端。
(3)横移水平油缸:
主要参数:
缸径/杆径:
100/55
820mm
最大推力/拉力:
12.5T/8.7T(16Mpa)
其伸缩速度可以通过截流阀进行调节。
横移水平油共16台,分别安装在模架的两侧。
5.1.2.10电气控制系统
电气系统采用380V三相五线制交流供电,零线与机体连接,电源进线电缆采用四芯3x25+1,容量不得小于250A,由主梁配电柜借入后,分别给4台泵站、后走行、起吊小车和2个5吨电葫芦供电。
整机设置相应的照明系统,满足夜间施工作业要求。
该设备电控部分需要控制的对象为起吊小车、四个液压泵站、后支腿行走、两个5t吊挂电动葫芦等四种。
5.2移动模架作业原理
移动模架造桥机利用侨梁端部和桥墩安装支腿,支腿支撑主梁系统,外模及模架吊挂在主梁系统上,行成一个可以纵向移动的桥梁制造平台,完成桥梁的施工。
移动模架下落脱模,横向开启使其能够通过桥墩,纵向前移过孔到达下一施工位,横向合拢再次形成施工平台,完成下一孔施工。
5.3各阶段施工步骤及工况
步骤1:
混凝土浇注完毕并达到张拉强度后,拆除内模撑杆,张拉,桥面铺设轨道:
拆除吊杆,拆除底模、外肋位于中缝处的对接螺栓。
中、后支腿垂直支承油缸回收使模架整体下落约10cm脱模,后主支腿作用在轨道上,前辅助支腿托辊与轨道接触(此时中、后支腿垂直支承油缸仍然支承);
操作泵站横移油缸顶推外肋,外模系统横移开启。
步骤2:
拆除中支腿连接系;
操作泵站使中、后支腿垂直支承油缸脱空;
驱动后支腿下走行机构使模架前移一跨;
此时前、中支腿位于同一桥墩上。
步骤3:
中、后支腿横向调整、垂直支承油缸支承、锁定;
起吊小车将前辅助支腿吊挂前移一孔,并在前方墩顶就位;
操作泵站使横移油缸循环回收,外模系统横向合拢就位。
步骤4:
各支腿系统竖向标高调整、锁定;
外模系统横向调整、锁定;
穿吊杆、钢筋绑扎。
步骤5:
立模,浇注混凝土。
5.4特殊工况
5.4.1首跨施工
5.4.1.1首跨施工时(首墩为桥台),需将桥台侧的边吊挂外肋的底肋部分向前移动1.4米安装并在底部将底肋临时支撑。
5.4.1.21-1面得底模支撑杆直接支撑在桥台上。
5.4.1.3桥台侧边吊挂无吊杆。
5.4.2末跨施工
5.4.2.1末跨施工时(末墩为桥台),需将桥台侧的边吊挂外肋的底肋部分向后移1.4米安装并在底部将底肋临时支撑。
5.4.2.21-1面得地模支撑杆直接支撑在桥台上
5.4.2.3桥台侧边吊挂无吊杆。
5.5移动模架拼装
5.5.1移动模架现场拼装与试验
(1)设备:
50t流动吊机一台及必须的吊索具;
电焊机2台;
脚手架若干;
缆绳;
钳工工具及其它专用工具,如冲钉φ24,50个;
扳手;
梯子等。
(2)场地:
在长70米、桥两侧各20米宽范围内平整,五障碍物。
(3)人员:
起重工、钳工、电工、技术人员其他辅助工作人员。
5.5.1.2基本要求
(1)拼装人员应熟读图纸,清楚该设备的主要功能及各种动作。
(2)整个装、试、拆的过程中应有足够得安全设施。
(3)备有水平仪、卷尺,靠尺、测量钢丝等检测器具。
5.5.1.3基础要求
(1)计划好在某墩台处安装此移动模架。
(2)承台顶荷载作用点应用砂浆找平。
(3)安装临时拼装支架,每个要求承压能力大于60t,高度根据实际确定。
5.5.1.4移动模架拼装步骤:
(1)在首跨墩台支架搭设4个临时支架。
(2)安装后、中主支腿。
(3)拼装两根主梁。
(4)安装主梁之间联系梁。
(5)安装外模支撑系。
(6)安装外模板。
(7)安装前辅助支腿。
(8)安装导梁。
(9)安装电气、液压系统。
(10)整机调试、预压,拆除临时支架。
5.5移动模架预压及预拱度设置
本标段桥梁为32米箱梁梁跨31.1m,梁高3m。
顶板宽12.2m。
跨中底板宽5.68m,跨中腹板厚0.443m,梁体混凝土为C50共计310.6m3,一孔梁钢筋约60t,钢绞线11.7t。
梁体总重量约为788t。
移动模架拼装后,在第一孔箱梁施工前要对移动模架进行预压,预压按1.2系数进行预压。
预压的目的是消除移动模架拼装的非弹性变形,测算出施工荷载时的弹性变形,根据箱梁张拉后的上拱度再计算出来移动模架底模的预拱度。
模拟梁体浇注顺序对造桥机实施预压,先底板、再腹板、后翼缘板,分四级对称加载(见分级预压控制表),即每级加载时先Ⅰ区域、再Ⅱ区域、最后Ⅲ区域对称加载(见移动模架分区域加载示意图)
一级加载:
60%腹板、顶板重+底板重+内模重=60%×
479+99+35+10=431.4t;
二级加载:
90%腹板、顶板重+底板重+60%翼板重+内模重=90%×
479+99+60%×
198.5+35+10=774.2t;
三级加载:
100%梁体自重+内模重=776.5+35+10+11.7=833.2t;
四级加载:
120%梁体自重+内模重=120%×
788.2+35+10=991t。
移动模架横断面分区域加载示意图
移动模架纵断面分区域加载示意图
综合考虑各种因素,确定基准荷载,用压重物(袋装砂子)模拟混凝土箱梁的重量分布,对移动模架分级荷载试验,测量各点的标高值,用预压前、预压期、稳定期、卸载后的标高观测值,算出支架总下沉值(预压前-稳定期),计算弹性变形量(卸载后-稳定期)和非弹性变形量(预压前-卸载后)(详见预压方案)。
荷载分布示意图如下:
5.6.1设备与物资
35吨汽车吊一台,991吨砂子及运输车辆,标高测量用仪器一套。
试验步骤:
调整四个支腿液压缸的行程,使主框架的四角处于同一标高位置,再调整底模撑杆的高低,使底模处于水平状态,底模中部处于水平状态。
在两侧主梁上沿纵向布置5个测点,位置分别为0L,1/4L,1/2L,3/4L,L;
8组吊挂外肋上共有16个竖向吊点,沿纵向布置六个测点,分别位于第1、4、7、10、13、16个吊点处,可布置在外肋的下表面,横向位置可选在与混凝土箱梁腹板对应处。
5.6.2测量各测点的原始标高
分级预压控制表
加载
砂袋(增加量)
方木
(10×
10cm)
数量(袋)
一级
7190
431.4
腹板处靠外模布置,间距3m,共计30根,重量不计。
二级
5713
342.8
三级
983
59.0
四级
2630
157.8
合计
16516
991
第一级按431.4吨加载,测量各测点的标高值。
第二级按774.2吨加载,测量各测点的标高值。
第三级按833.2吨加载,测量各测点的标高值。
第四级按991吨加载,测量各测点的标高值。
静置24小时后,再次测量各测点的标高值。
卸载后再次测量各测点的标高值。
5.6.3施工预拱度的设置
箱梁施工标高与线行控制的关键是预拱度的设置。
第一套模架采取预压测定系统变形值。
通过预压:
(1)检验系统各构件受力后的安全