冷氢化制备三氯氢硅Word文档下载推荐.docx
《冷氢化制备三氯氢硅Word文档下载推荐.docx》由会员分享,可在线阅读,更多相关《冷氢化制备三氯氢硅Word文档下载推荐.docx(18页珍藏版)》请在冰豆网上搜索。
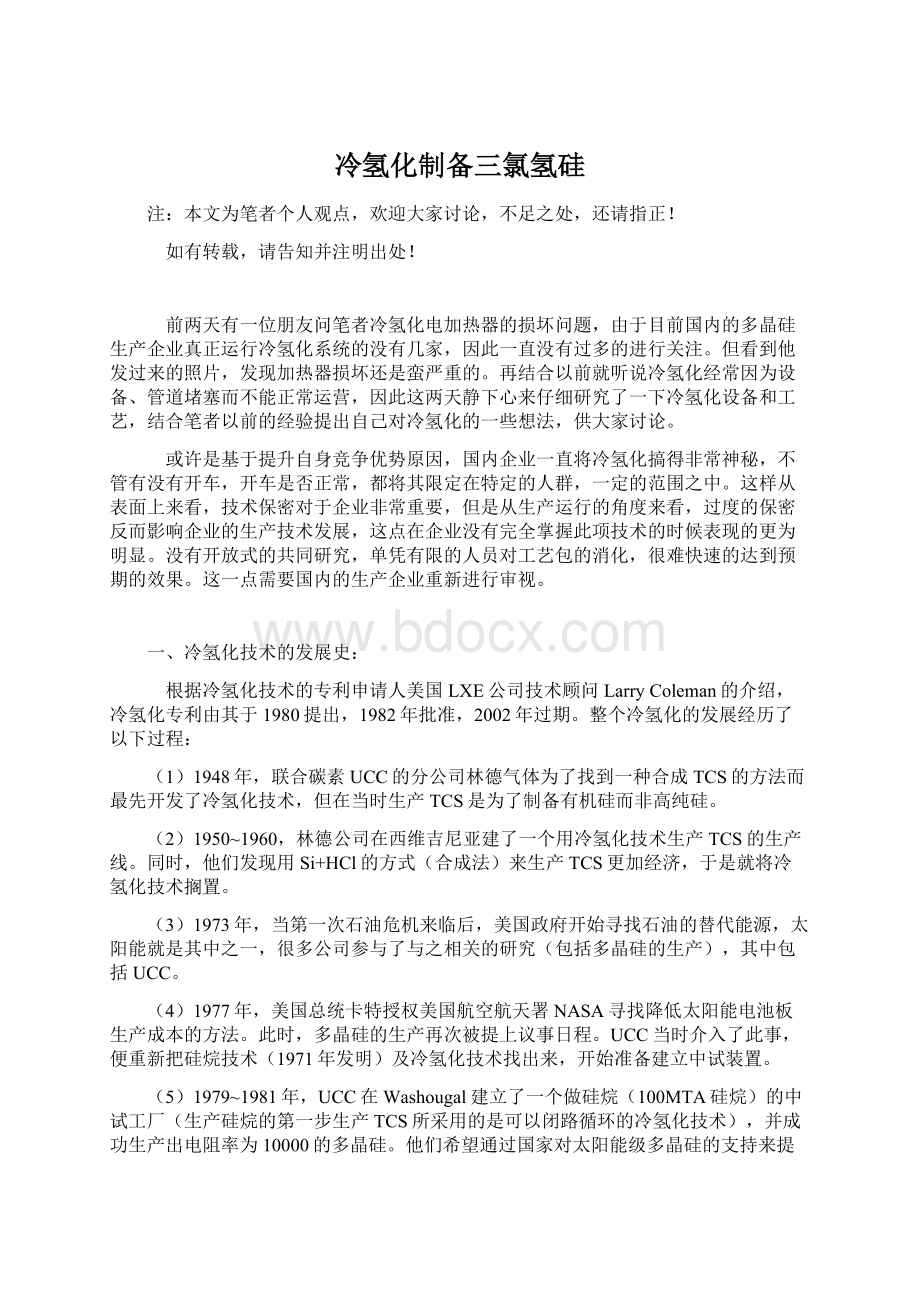
二、冷氢化工艺原理:
目前国内的冷氢化技术主要分为两种,一种就是传统意义上的由H2、硅粉、STC作为原料在催化剂的作用下及中温高压条件下生产TCS的冷氢化技术,其反应原理如下:
另一种是在传统冷氢化技术上引入回收HCl生产TCS的方法,即氯氢化技术。
其整合了三氯氢硅合成和冷氢化两者的特点,可看作是传统冷氢化工艺的衍生和优化,将回首HCl得到充分的利用。
其反应原理如下:
不论是传统的冷氢化生产技术还是改良后的氯氢化技术,其主要生产工艺流程和设备基本是相同的。
三、冷氢化生产工艺概述:
为了便于讨论,需要先充分了解一下冷氢化的生产工艺。
为了防止与相关企业产生不必要的知识产权纠纷,本文中的冷氢化工艺论述均来自笔者自己掌握的一些公开资料及个人的生产技术经验汇编而成的技术方案。
任何企业或个人如对本文中所阐述的工艺论述有知识产权疑议,请及时与笔者进行联系确认。
一般的冷氢化工艺可以分为四大部分,即物料供应系统(含STC、H2、硅粉、HCL等)、氢化反应器系统、冷凝分离系统和精馏系统。
详细工艺如下图所示:
从工艺流程图中可以看出,硅粉经过干燥后和催化剂在硅粉中间槽内进行H2活化,然后后通过给料仓进入氢化反应器。
一般硅粉进入氢化反应器主要有三个部位,反应器顶部、反应器中部和反应器底部,这三个部位进料各有优势,后续进行详细的分析。
STC和H2分别经过加压、汽化后按照一定的摩尔比从流化床底部进入,如同TCS合成炉一样,这样可以使氢化反应器内的物料进行充分沸腾反应。
反应尾气通过旋风分离器分离掉绝大部分的催化剂和未反应完全的硅粉,之后再进入洗涤塔通过氯硅烷喷淋洗涤进一步除去尾气中的固含物。
比较洁净的尾气通过STC加热器与液体STC进行充分换热,然后再通过两级冷凝器对尾气进行深冷,尾气中的氯硅烷变为液体,这样就可以将尾气中H2和HCL与氯硅烷通过气液分离器进行分离。
分离出来的气体H2和HCL根据企业工艺和设备情况回收至合成车间或是氢化反应器。
液体氯硅烷一部分被泵入尾气洗涤塔来洗涤尾气,剩下的均进入汽提塔进一步除去固体杂质。
除杂后的氯硅烷进入粗馏塔进行STC和TCS的分离,STC为液体从塔底排出,TCS成气体从塔顶排出进入下一级精馏塔分别进行除重、除轻处理。
精馏后的TCS进入TCS储槽,之后被泵入多晶硅还原工序。
如果从传统的改良西门子法工艺角度来看,冷氢化工艺其实是由三个工序构成的,即TCS合成工序、合成干法尾气回收的冷凝工序和合成精馏工序。
笔者之所以从传统的生产工艺角度来对冷氢化进行工序分割,主要是为了便于分析冷氢化经常存在的问题,并给予一些相应的解决方法。
未完,详见《冷氢化生产工艺讨论(中)》
四、冷氢化工艺分析:
(一)、物料供应系统:
1、硅粉和催化剂供应:
一般的工业硅粉都含有一定的水分,因此在使用前都必须进行烘干。
在传统的TCS合成工艺中,一般采用加热N2来进行烘干处理。
但考虑到冷氢化需要使用铜基或镍基的催化剂,为了确保催化剂活性,所以基本上采用加热H2来对硅粉进行干燥,并起到进一步活化的作用。
干燥后的硅粉与催化剂在硅粉中间仓内混合均匀,然后进入硅粉供应仓。
为了保证硅粉的安全、持续加料,一般硅粉供应仓设置为两个,其中一个供应仓先装满混合均匀的硅粉和催化剂,在使用过程中由H2加压均匀送入氢化反应器中。
另一个供应仓此时由硅粉中间仓补充硅粉和催化剂,等待下一步交替送料。
在这一生产步骤中由于物料均为干燥的粉料,因此除了需要计量配比准确外,并无大的问题。
2、H2供应:
这个生产步骤相对比较简单,回收的H2或是来自电解的H2经过氢压机加压至15~30kg后进入H2缓冲罐,然后再通过电加热器进行汽化。
在这里需要注意的是冷氢化系统回收H2的使用。
因为在冷氢化生产系统中一般没有专门的HCL吸附解析系统,因此其回收H2含有一定量的HCL。
如果将此回收H2与还原回收的H2或是电解的H2混合经过氢压机压缩,则压缩后的HCL会成为液体,需要与H2分离后单独由电加热器进行加热汽化。
如果企业已经有TCS合成系统,建议将此冷氢化回收H2压缩后与HCL进行简单的分离,然后将回收的HCL送入TCS合成炉内单独使用。
这样的好处是可以使氢化反应器内的物料种类相应减少,便于生产控制。
3、STC供应:
从STC储槽来的洁净STC经过屏蔽泵加压至15~30kg,然后进入STC换热器与反应尾气进行换热,起到初步的预热作用。
然后经过预热的STC通过STC加热器进行进一步加热,一般到这一步骤时STC已基本全部汽化。
加热的媒质通常为蒸汽或是导热油,由于导热油可以加热至300℃左右,所以一般使用导热油居多。
由于氢化反应器中的物料反应温度在500℃以上,因此进入反应器的物料温度需在500℃左右,此时需要再通过电加热器进行加热,以满足进料工艺温度要求。
汽化后的STC和H2按照一定的摩尔比例进行混合,通过氢化反应器底部进入氢化反应器中。
在这一步骤中需要关注的是STC的汽化程度和STC物料的干净程度。
如果STC汽化效果不理想,那么就很有可能出现气体夹液现象,这样直接导致的结果就是STC液体会与反应器中的硅粉和催化剂结块,从而堵塞旋风分离器、冷凝器和相应管线。
如果STC物料处理的不干净,也会堵塞冷凝器、加热器及氢化反应器底部的气体分布器等设备或部件。
(二)、氢化反应器系统:
主要包括氢化反应器和湿法洗涤两个部分。
1、氢化反应器:
一般的氢化反应器主要包括反应器本体、底部气体分布盘、旋风分离器、硅粉进料口及电加热器等部件。
A、反应器本体:
由于冷氢化反应器的工作条件要求非常高,既要耐高压,还要耐高温、耐腐蚀,因此对其设备材质要求非常苛刻。
为了满足这种工艺条件要求,目前业内普遍采用Incoloy800H作为氢化反应器的设备材料。
Incoloy800H材质的化学成份如下表所示:
铬
镍
锰
硅
铝
钛
铝+钛
碳
铜
磷
硫
铁
最小值
19.0
30.0
--
0.15
0.85
0.06
最大值
23.0
35.0
1.5
1.0
0.6
1.2
0.1
0.75
0.045
0.015
39.5
由于Incoloy800H大直径的管材市场上很少供应,且非常昂贵,而板材且在焊接和热处理方面难度比较大,所以通常情况下采用棒材掏心的方法来加工氢化反应器筒体。
这种方法在一定程度上解决了Incoloy800H的焊接难题,但是存在材料浪费比较大,且筒体壁厚无法保证均匀等问题。
为了解决这种加工缺陷,现在已经出现了一种采用特种铸造方式来加工氢化反应器筒体的加工工艺。
这种加工工艺可以根据设计要求加工出任意直径的Incoloy800H筒体,且保证筒体壁厚均匀,可实现同轴心的一体式筒体变径,对于原材料浪费极少。
这种加工工艺的出现在很大程度上降低了氢化反应器的制造成本。
B、底部气体分布盘:
氢化反应器底部分布盘的主要作用就是将STC和H2在反应器内分布均匀,以利于物料充分接触,使反应能够更加充分。
一般底部气体分布盘有两层,最低下一层相当于喷嘴,上一层相当于一个均布器。
C、旋风分离器:
又叫做旋风除尘器,主要是除去反应尾气中的硅粉和催化剂,其结构与化工行业的常用旋风分离器基本相同。
按照目前的常用设计,旋风分离器分为内旋风分离器、上旋风分离器和外旋风分离器三种,这三种形式各有特点。
内旋风分离器位于氢化反应器的内部上端,其好处在于其位于氢化反应器内,与氢化反应器成为一体,热损较小,硅粉和催化剂回收率高,回收的硅粉和催化剂可直接在反应器内继续参与反应,其缺点就是检修及部件更换操作不便,且受反应器空间影响,处理能力有限,因此对于处理量比较大的反应器而言不太适合。
上旋风分离器位于氢化反应器顶部,与反应器直接相连,也可看为一体。
其好处在于回收的硅粉和催化剂可直接在反应器内继续参与反应,检修及部件更换操作比较方便,同样其受反应器影响,处理能力受到现在,因此一般用于中型的氢化发反应器。
外旋风分离器与氢化反应器通过管道相连,基本是一个独立的处理设备。
其好处除了检修及部件更换方便以外,还可以不受氢化反应器限制,可以根据生产要求同时并联几套设备,因此无论是处理能力还是处理效果,都得到了有效的提升,因此对于大型的氢化反应器其比较适合。
但其缺点是收集的硅粉和催化剂需专门回收处理。
D、硅粉进料口:
按照通常的氢化反应器设计,硅粉有三个进料位置,即顶部,中部和底部,同样这三种进料方式各有特点。
顶部进料是在氢化反应器顶部设计有一根深入反应器内部的硅粉下料管道,硅粉和催化剂基本上是依据自身重量加入反应器内,这样在一定程度上就减少了对气体输送的依赖。
但是由于加料位置与反应器出口比较紧,因此,硅粉和催化剂损失比较大,在一定程度上增加了旋风分离器的处理负荷。
底部进料是指硅粉和催化剂从氢化反应器底部进入,依靠H2、STC、HCL的气体吹入反应区域。
这种进料方式有利于硅粉和催化剂的充分反应,单对气体输送要求比较高。
中部进料是一种比较常见的反应器进料方式,在氢化反应器中部硅粉和催化剂通过H2加压和自身重力作用进入反应器内。
其优缺点介于上述两种方式之间。
E、电加热器:
由于冷氢化的主要反应是STC转化为TCS,这是一个吸热反应。
因此,单纯依靠物料的预热来满足反应温度会存在一定的风险,因此,一些氢化反应器的设计在底部会增加一个电加热器,以满足工艺所需的反应条件。
(三)、湿法洗涤:
湿法洗涤相对比较简单,就是在洗涤塔内通过液体氯硅烷喷洒反应尾气,进一步除去尾气中的固体杂质,防止堵塞后续冷凝器等设备。
冷凝分离系统:
在本设计中包括热交换器、两级冷凝器和一个气液分离器。
A、
热交换器:
洗涤后的反应尾气在列管式热交换器中STC进行换热,这样就可以起到对STC进行预热的作用,同时降低反应尾气的温度。
B、
一级冷凝器:
依据反应温度的控制,使用冷却水或是冷冻盐水在此设备内对反应尾气进行进一步的冷却。
C、
二级冷凝器:
使用冷冻液在此设备内对反应尾气进行更深的冷却,以使反应尾气中的氯硅烷全部变成液体。
D、气液分离器:
在此设备内,液体氯硅烷与H2及HCL气体进行分离,氯硅烷从底部进入氯硅烷中间槽,H2和HCL从顶部进入回收系统。
(四)、精馏系统:
包括汽提、TCS粗馏和TCS精馏三个部分。
汽提:
液体氯硅烷在此通过再沸器加热变为气体,以便在此对液体中的固体杂质进行分离,从而获得更加干净的氯硅烷。
TCS粗馏:
TCS粗馏由一级精馏塔组成,包含精馏塔,再沸器和冷凝器,其作用主要是分离STC、TCS及DCS。
STC塔底排放至STC储槽,TCS和DCS从塔顶排出,经过冷凝器冷凝后TCS变为液体,一部分回流至塔内,剩余部分进入下一级精馏系统。
DCS此时大部分仍未气体,从冷凝器顶部排出,至废气储罐。
TCS精馏:
TCS精馏有两级精馏塔组成,主要是除去TCS总的金属氯化物,即经常所说的轻重组分杂质。
一般而言,TCS精馏一级塔是去除TCS中的重组分,重组分从塔底排出,二级塔是去除TCS中的轻组分,轻组分是从塔顶冷凝器排出。
经过两级精馏之后的TCS则为纯净的TCS,生产上一般称为精制三氯氢硅。
未完,详见《冷氢化生产工艺讨论(下)》
五、冷氢化生产探讨
(一)、冷氢化面临的生产问题:
在前面笔者已经提到从传统的改良西门子法生产工艺角度来看,冷氢化主要工艺其实是由TCS合成、干法尾气回收和合成精馏三个部分组成,分别对应如下:
1、
冷氢化反应器系统对应TCS合成中的TCS合成炉、旋风分离器和洗涤塔;
2、
冷凝分离系统对应的是合成干法尾气回收中的尾气冷凝部分,在常见的CDI系统中对应的就是四级冷凝系统,即常说的“短路”;
3、
精馏系统对应的就是合成精馏中的粗馏和精馏。
所以,从事过传统改良西门子法生产的人员都知道,合成干法尾气回收中的四级冷凝系统和合成精馏都是比较容易操作的,而TCS合成对于许多企业而言尚还是一个挑战。
因此,不难看出,冷氢化的操作挑战在于氢化反应器系统。
在日常的TCS合成生产中常见的问题就是TCS转换率、设备管道堵塞和设备管道损坏,而TCS转换率的高低取决于TCS合成炉的工艺控制水平,管道堵塞和设备管道损坏状况则取决于TCS合成炉的工艺控制水平和相应设备或备件的合理性即操作技巧。
因此,相对于冷氢化而言,最终也不能逃脱这三个问题点。
从目前一些公司的冷氢化系统实际运行情况来看,也正是这三个问题点一直困扰着企业的正常生产运行,尤其是设备管道堵塞和设备管道损坏直接导致冷氢化系统,影响冷氢化的生产运行周期。
针对以上问题,各企业需要根据自身设备和人员状况进行摸索,形成一套适合自己的生产工艺控制标准。
并借鉴一些TCS合成运行不错的企业生产经验,从TCS合成的运行角度来完善冷氢化反应器的不足。
(二)、冷氢化电耗到底是多少
从目前的行业舆论来看,大家都认为冷氢化耗电量非常低,大致的范围在0.8~1.5Kwh/kg.TCS。
前一段时间笔者有幸与一位国内有名的冷氢化工艺设计大师讨论目前的多晶硅技术问题,其中就涉及到目前冷氢化的耗电量。
大师说他们的冷氢化工艺包在国内是非常有竞争优势的,并已在几家公司成功运行,效果不错。
他们的工艺包中所有动设备的平均最大功率是0.6Kw/kg.TCS(所有动设备的铭牌功率之和与产能的平均值),即最大电耗是0.6Kwh/kg.TCS。
从设计院的这个数据可以看出,冷氢化的设计电耗还是非常低的。
但是,这些数据是基于达成设计产能的理论值,但实际如何,企业还需心中有数。
按照国家的设计标准,企业年生产操作时间应为7440h,即310天,对于一条年产50000t的TCS冷氢化生产线而言,则TCS产量应为6.72t/h。
暂且不考虑设备的实际运行功率,既有效功率如何,但从产能这方面来考虑,50000t的产能对应的电耗是0.6Kw/kg.TCS,如果企业的实际产能达不到50000t时,那么此时的电耗将会是多少呢?
对于此问题,或许只有每个企业自己知道。
所以,冷氢化电耗高低除了与技术、工艺、设备有关外,还与企业的生产运行水平和人员有很大关系,而且在一定程度上,后者往往会起到决定性作用。
因此,对于各企业而言,必须明白一个最基本的常理,技术和设备可以帮助企业,但真正能够帮助企业的还是企业自己。
(三)、冷、热氢化之争:
目前经常会出现冷氢化是未来的必然发展趋势,热氢化最终会被冷氢化所淘汰,即所谓的冷、热氢化之争。
综合所有言论,可以不难看出,认为冷氢化要优于热氢化的依据无非有五点:
1、冷氢化耗电量低;
2、冷氢化TCS转化率高;
3、冷氢化一次性投资成本低;
4、热氢化备品备件费用高;
5、第1和4点决定冷氢化的生产成本很低。
针对以上五点,笔者不妨进行逐条分析,以探求其实质的问题所在。
关于第一点冷氢化电耗低,这个是无需置疑的。
但是冷氢化到底会比热氢化低多少,真如大家所认为的会低至30%以下吗?
对于这一点,笔者不是很认同,这个主要取决于企业自身的生产运行水平的高低。
这点已经在上面进行了简单的分析,在此就不再重复。
需要说明的一点是目前所说的热氢化的耗电量在3Kwh/kg.TCS以上是基于热氢化工序而言的,如果将TCS合成、TCS尾气回收和TCS精馏三个工序也看作热氢化的一部分的话,那么热氢化的耗电量应在2.2Kwh/kg.TCS左右。
关于第二点冷氢化TCS转化率高,这个是存在问题的。
目前从已运行的企业的冷氢化来看,运行水平比较好的冷氢化的平均摩尔转化率在20~22%,并非大家所听到的25%以上(这个数据可能是瞬时值)。
而目前经过技术改造后的热氢化的平均摩尔转化率也在20~22%,瞬时值也会达到25%左右。
因此,对于TCS转化率,目前两种氢化工艺相差不是很大。
关于第三点冷氢化一次性投资成本低,这点也是无需置疑的,毕竟热氢化的设备要比冷氢化多很多。
关于第四点热氢化备品备件费用高,这点比较难以确定。
毕竟每家企业的采购渠道和采购成本都不一致,很难进行两者间的直接比较。
但是有一点必须说明的是,热氢化现在所有的备品备件均已实现国产化,很多关键的备品备件已经实现了更新换代,目前备品备件价格已经有了大幅度的降低。
关于第五点冷氢化可以使多晶硅生产成本有很大程度上的降低,甚至有人士说只要上马冷氢化多晶硅成本就会降至20美金以下。
对于这种观点,笔者是不敢苟同的。
冷氢化在一定程度上是可以降低多晶硅生产成本的,但是并非业内所期望的那么多,毕竟多晶硅生产系统是一个综合性的生产系统,需要一个整体运行来支撑,而多晶硅的成本降低不是依靠某一两个工段就能够决定的(包括冷热氢化在内),在运行正常的情况下,综合运行水平的高低决定企业生产成本的高低,过程控制不容忽视。
通过上面简单的分析,可以简单的看出冷、热氢化之间的关系及优劣势,借此给大家一个简单的参考。
(四)、CL离子的补充不容忽视:
在于许多行业人士谈论时,许多人认为冷氢化是一个真正的闭环系统,因此不存在需要额外补充STC。
关于这一点,大家是有一个误区的。
包括热氢化在内,所谓的闭环生产永远是相对,最简单的就是多晶硅生产过程中需要排出杂质和不冷凝气。
多晶硅生产中的杂质主要是依靠STC排出的,而不冷凝气基本上是DCS,这两个就在一定程度上决定硅和CL离子是有损耗的,关键在于损耗的多与少。
冷氢化的STC转化率在理论上要比热氢化高,这主要是热氢化对STC的纯度要求比较高,尤其是TCS合成产生的STC是不能够在热氢化炉中使用的。
所以,对于冷氢化而言是需要补充一定量的STC的,除非企业直接向氢化反应器中补充Cl2。
至于补充量是多少,这个需要看各企业的运行水平。
(五)、冷氢化的发展方向:
虽然目前市场上已经出现了18t/h处理量的热氢化炉的信息,但是冷氢化作为企业降低多晶硅生产成本的一个方向不能忽视。
冷氢化和热氢化各有其自身特点,不能轻易的下结论说是谁能替代掉谁。
如果要想生产高质量的多晶硅产品,热氢化就不能够缺少。
在市场上STC供应紧张时,热氢化的相应配套系统将会发挥出其更大的作用。
因此,笔者认为,未来的冷氢化发展方向除了扩大其自身单线生产规模和降低投资、运行成本以及提高TCS产品质量外,与热氢化生产系统相联合,将更是其应该发展的方向。
所以,对现在已经建成并投产的企业而言,冷氢化是一个选择方向,但并非需要以完全抛弃热氢化系统作为代价。
当然,企业如果是为了融资需要,为了给市场一个概念,到可以做做,否则,还是将现有的做好才是最好。
简单的做了一个以热氢化和冷氢化为基础生产多晶硅的主要物料关系图,感兴趣的话可以参考一下。
欢迎一起讨论。
冷氢化的图中理论STC缺口是依据理论数据计算得出,实际生产耗用量要大于此数据。
冷氢化技术综述(上)的表格显示不完整,重发一遍:
项目名称
高温低压热氢化
低温高压冷氢化
操作压力:
Bar
6
15~35
操作温度:
℃
1250
500~550
主要反应
SiCl4+H2=SiHCl3+HCl
Si+3HCl=SiHCl3+H2
3SiCl4+Si+2H2=4SiHCl3
优点
汽相反应;
不需催化剂;
连续运行;
装置单一、占地少;
易操作和控制,维修量小;
氢化反应不加硅粉,无硼磷及金属杂质带入,后续的精镏提纯工艺较简单,提纯工作量小;
STC转化率一般为(17%~24%)
流化床反应;
三氯氢硅合成与四氯化硅氢化可在同一装置内进行,可节省投资;
反应温度低、电耗低,单耗指标为≤1kWh/kg-TCS;
STC转化率为20%以上;
缺点
反应温度高、电耗高,单耗指标为≤2.2~3kWh/kg-TCS;
加热片为易耗材料,运行费用较高,有碳污染的可能性。
气固反应,操作压力较高,对设备的密封要求很高,维修工作量大;
操作系统较复杂,;
氢化反应加入硅粉,有硼磷及金属杂质带入,提纯工作量大,增加精馏提纯费用(如蒸汽、电力、冷却水等消耗);
需硅粉干燥及输送系统;
需加入催化剂。
冷氢化技术综述
(上)
朱骏业
岳菡
张永良
20世纪70年代美国喷气推进实验室(JPL)在美国能源部的支持下组织研究新硅烷法工艺过程中,采用多晶硅工厂的副产物四氯化硅(STC)作原料,将其转化为三氯氢硅(TCS),然后将三氯氢硅通过歧化反应生产硅烷。
80年代初,为得到低成本、高纯度的多晶硅,又进行了一系列的研究开发。
其中高压低温氢化工艺(以下简称冷氢化)就是一项能耗最低、成本最小的STC转化为TCS的工艺技术