板块类零件机械加工工艺规程设计Word格式文档下载.docx
《板块类零件机械加工工艺规程设计Word格式文档下载.docx》由会员分享,可在线阅读,更多相关《板块类零件机械加工工艺规程设计Word格式文档下载.docx(20页珍藏版)》请在冰豆网上搜索。
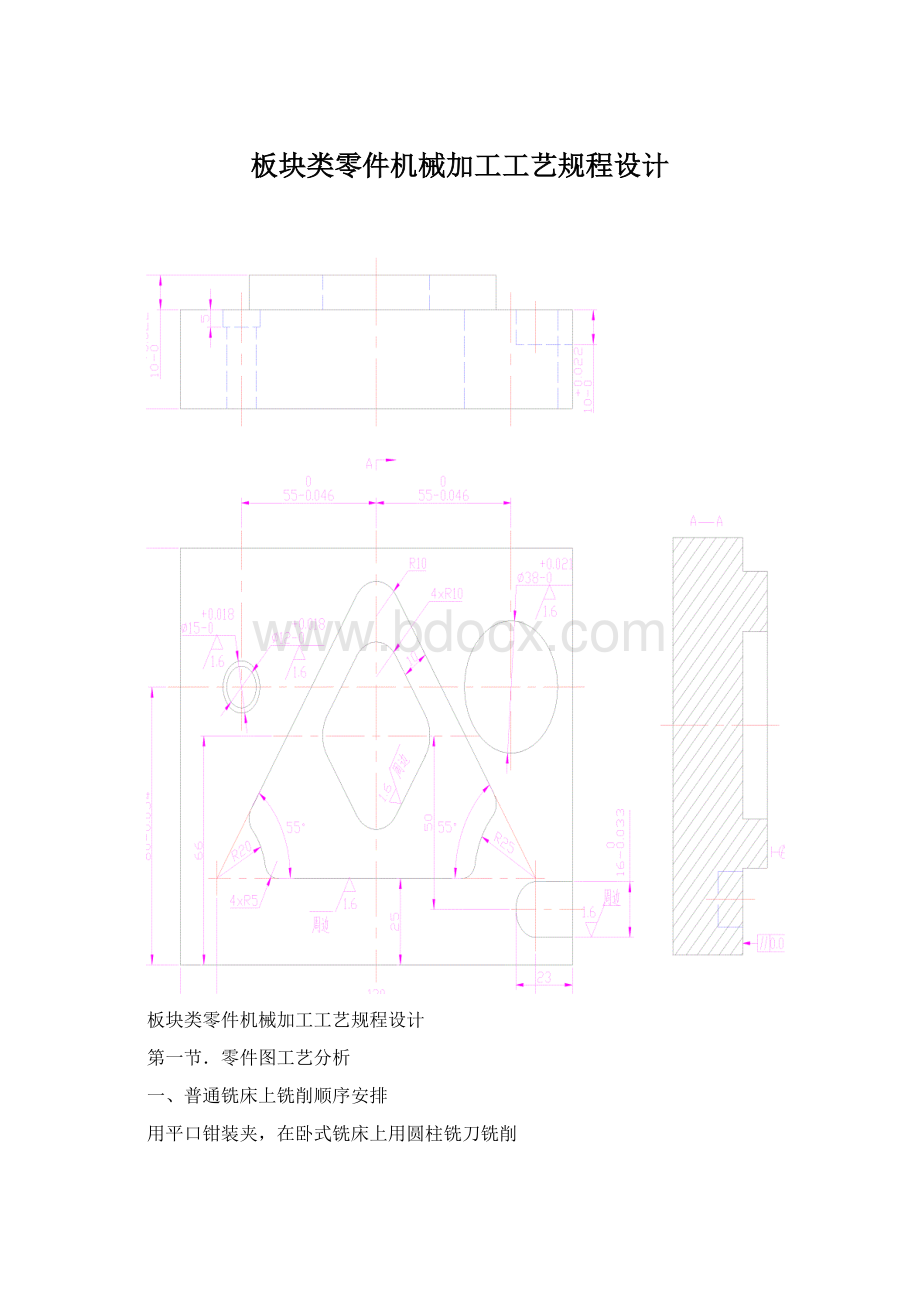
可在一次装夹中加工来保证。
表面粗糙度要求较高的为Ra1.6um,其余的为Ra3.2um。
1.选择加工机床
用立式三坐标数控铣床较合适。
第二节工件定位与装夹
一、工件定位
合理选择定位基准对保证加工精度,提高生产效率有着重要的作用。
确定零件的定位基准,应遵循以下原则:
(1)尽量使定位基准与设计基准重合。
(2)保证零件在一次装夹中完成尽可能多的加工内容。
(3)工件坐标原点的确定
工件坐标原点的确定主要应考虑编程和测量。
确定定位基准时,不必与其原点重合,但应考虑坐标原点能否通过定位基准得到准确的测量,即得到准确的集合关系,同时兼顾到测量方法。
设计课题2中的工件坐标系原点选在工件上表面的左下角,与编程原点重合,便于计算和编程。
二、工件的装夹与夹具
为了保证数控加工的精度,提高生产效率,一般要求夹具具有结构紧凑、简单,夹紧动作迅速、准确,操作方便、省力、安全,并有足够的刚性。
经分析,设计课题2中,以已加工过的底面和侧面作为定位基准,其中底面为主定位面,采用等高垫铁在平口虎钳上装夹定位或直接将工件毛坯放在工作台上,用等高垫铁将工件托起,再用百分表找正工件两侧面进行安装定位,在虎钳上夹紧前后两侧面。
虎钳用T形螺栓固定于铣床工作台上。
第三节加工工序与工步的划分
加工方法的选择原则:
保证加工表面的加工精度和表面粗糙度的要求,由于获得同一级精度和表面粗糙度的方法很多,因而在实际选择时,要结合零件的形状、尺寸、大小、热处理要求等全面考虑。
一般小尺寸的孔采用较孔,孔径较大时则应选择镗孔。
此外还应考虑生产效率和经济性要求。
由于加工设计课题零件时,仅需一次装夹即可完成所有加工内容,因此确定工序为一道,在按平面铣削、挖槽、钻孔等分粗、精加工来划分工步。
在安排加工顺序时应遵循:
先面后孔、先集基准后其他、先主后次、粗精分开等原则。
(1)粗铣顶面
(2)去周边余料粗加工
(3)粗铣凸台轮廓
(4)粗铣中心菱形封闭槽
(5)粗铣右下角半通槽
(6)用φ2mm中心钻打φ12mm、φ38mm的中心孔
(7)扩φ12mm、φ38mm的通孔至φ11mm
(8)铰φ12mm的通孔至11.8
(9)铣φ15mm的沉孔至φ14.8
(10)扩φ38mm的孔至φ36mm
(11)粗镗38mm的通孔至φ37.8mm
(12)精铣顶面
(13)去周边余料精加工
(14)精铣凸台轮廓
(15)精铣中心菱形封闭槽
(16)精铣右下角半通槽
(17)铰φ12mm的通孔至尺寸
(18)铣φ15mm的沉孔至尺寸
(19)精镗φ38mm的通孔至尺寸
(20)去毛刺
(21)检验
第四节刀具选择
铣刀的几何参数对铣削金属的变形、铣削力、切削温度和铣刀的磨损都有显著的影响。
并由此影响加工质量、铣刀的使用寿命和生产效率。
为了充分发挥铣刀的切削性能,除了正确选择铣刀的材料外,还应根据具体铣削条件,合理地选择铣刀的几何参教。
一、铣刀直径的选择原则
铣刀直径大,散热条件好,铣刀刚性好,所允许的铣削速度和切削量大,但铣刀直径大时,铣削时铣刀的切入长度增加,工作时间长,铣削力矩大,刀具材料消耗也大。
一般面铣刀的直径应比宽大20%——50%,立铣刀直径的选择主要应考虑工件加工尺寸的要求,并保证刀具所需功率在机车额定功率范围以内。
二、铣刀齿数的选择
铣刀有粗齿和细齿之分,粗齿铣刀的刀齿强度高,容屑空间大,到铣削时同时参与切削的齿数少,因而工作平稳性差,振动大,适宜用于粗铣;
细齿铣刀在铣削时同时参与切削的齿数多,每齿进给量f
z小,铣削平稳,适宜精车。
刀具准备:
1号刀φ150硬质合金面铣刀6齿
2号刀φ40硬质合金面铣刀6齿
3号刀φ30高速钢立铣刀6齿
4号刀φ18键槽铣刀
5号刀φ12键槽铣刀
6号刀φ2中心钻
7号刀φ11麻花钻
8号刀φ11.8铰刀
9号刀φ36麻花钻
10号刀φ37.8镗刀
11号刀φ12铰刀
12号刀φ38镗刀
第五节铣削用量的选择
一、选择铣削用量的原则
选择铣削用量的原则是在保证加工质量、降低加工成本和提高生产效率的前题下,使铣削宽度(或铣削深度)、进给量、铣削速度的乘积最大,这时的工时最少。
粗铣时按铣削铣削宽度(或铣削深度)、进给量、铣削速度的次序,选择和确定铣削用量。
精铣时为了保证加工精度和表面粗糙度要求,工件的切削层宽度应尽量在一次铣出;
切削层深度一般在0.5mm左右,再根据表面粗糙度要求选择合适的每齿进给量;
最后根据铣刀的耐用度确定铣削速度。
1.铣削层深度的选择
端铣时的铣削深度ap、圆周铣削时的铣削宽度ae即是被切金属层的深度。
当精度要求较高或加工表面的粗糙度Ra植小于6.3um时,应分粗、精加工。
粗铣时应留精铣余量0.5~2.0mm。
2.进给量的选择
进给量有三种表示和度量方式:
①每转进给量f(mm/r)②每齿进给量fz(mm/z)③进给速度vf(mm/min)。
三种进给量的关系为:
fz=fn=fzzn(其中n为主轴转速,z为铣刀齿数)
粗铣时,限制进给量提高的主要因素是铣削力。
精铣时,限制进给量提高的主要因素是加工表面粗糙度,进给量越大,表面粗糙度值也越大,为了减小工艺系统的弹性变形,减小已加工表面残留面积的高度,一般采用较小的进给量。
3.铣削速度的选择
在铣削深度ap、铣削宽度ae、进给量f确定后,最后选择铣削速度vc。
铣削速度vc是在保证加工质量和铣刀耐用度的前提下确定的。
粗铣时,由于金属切除量大,产生热量多,切削温度高,为了保证合理的铣刀耐用度,铣削速度要比精铣时低一些。
二、.切削用量的计算
公式:
n=1000vc/でd
vf=fzzn
1铣上顶面:
查表得铣削速度vc=100~180m/min,每齿进给量fz=0.05~0.2mm/z,铣削深度0.5~1.0mm。
(附表12数控铣削加工技术)
取n=1000×
150/3.14×
150≈320n/min
vf=280mm/min
②铣凸台轮廓:
查表得铣削速度vc=20m/min,每齿进给量fz=0.15mm/z。
粗:
n=1000×
20/3.14×
30≈210r/min
vf=6×
0.15×
210≈190mm/min
精:
vc=20×
(1+30%)=26m/min
n=1000×
26/3.14×
30≈270r/min
vf=6×
270≈240mm/min
粗加工每层最大切深5mm
③铣中心菱形封闭槽:
查表得铣削速度vc=20m/min,进给量f=0.2mm/r。
18≈210r/min
vf=0.2×
210≈42mm/min
18≈460r/min
vf=460×
0.2≈92mm/mi
④铣右下角半通槽:
查表得铣削速度vc=20m/min,进给量f=0.08mm/r。
18≈320r/min
vf=320×
0.08≈26mm/min
12≈700r/min
vf=700×
0.08≈56mm/min
⑤打φ12mm、φ38mm的中心孔:
取n=1000r/min
vf=100mm/min
⑥钻φ12mm、φ38mm的通孔至φ11mm:
查表得铣削速度vc=20m/min,进给量f=0.15mm/r。
(附表1数控铣削加工技术)
11≈600r/min
vf=600×
0.15≈90mm/min
⑦铰φ12mm的通孔:
查表得铣削速度vc=10~20m/min,进给量f=0.12~0.20mm/r。
(附表5数控铣削加工技术)
12≈530r/min
vf=530×
0.2≈106mm/min
⑧钻φ38mm的孔至φ36mm:
查表得铣削速度vc=10~20m/min,进给量f
=0.30~0.4mm/r。
36≈180r/min
vf=180×
0.4≈70mm/min
⑨粗镗φ38mm的通孔:
查表得铣削速度vc=30m/min,进给量f=0.4mm/r。
(表9数控铣削加工技术)
30/3.14×
37.8≈250r/min
vf=250×
0.4≈100mm/min
⑩精镗φ38mm的通孔:
查表得铣削速度vc=120m/min,进给量f=0.12m/min(表9数控铣削加工技术)
120/3.14×
38≈1000r/min
vf=1000×
0.12≈120mm/min
注:
本设计课题中,凸台轮廓、中心菱形封闭槽和右下角半通槽的粗精加工都是使用同一把刀,可以用同一程序,通过改变半径补偿来实现。
第六节数控加工工艺卡片
厂名
数控加工
工艺卡片
产品名称
材料
零件图号
45锻件
工序号
程序编号
夹具编号
使用设备
车间
FANUC立式加工中心
工步号
工步内容
刀具号
刀具规格(mm)
刀具长度补偿号
刀具半径补偿号
主轴转速(r/min)
进给速度(mm/min)
切深(mm)
1
粗铣顶面
T0101
φ150面铣刀
H01
S240
F300
2
去周边余料粗加工
T0202
φ40面铣刀
H02
D02
S200
F280
3
粗铣凸台轮廓
T0303
φ30立铣刀
H03
D03
S210
F190
4
粗铣中心菱形封闭槽
T0404
φ18键槽铣刀
H04
D04
F45
5
粗铣右下角半通槽
T0505
φ12键槽铣刀
H05
D05
S320
F30
6
用φ2mm中心钻打φ12mm、φ
T0606
φ2中心钻
H06
S1000
F100
2.5
38mm的中心孔
7
扩φ12mm、φ38mm的通孔至φ11mm
T0707
φ11麻花钻
H07
S550
F90
8
铰φ12mm的通孔至11.8
T0808
φ11.8铰刀
H08
S500
9
铣φ15mm的沉孔至φ14.8
F60
10
扩φ38mm的孔至φ36mm
T0909
φ36麻花钻
H09
S180
F70
1.8
11
粗镗38mm的通孔至φ37.8mm
T1010
φ37.8镗刀
H10
S250
12
精铣顶面
面铣刀
0.5
13
去周边余料精加工
S300
14
精铣凸台轮廓
D06
S270
F240
15
精铣中心菱形封闭槽
D07
S460
16
精铣右下角半通槽
D08
S700
17
铰φ12mm的通孔至尺寸
T1111
φ12铰刀
H11
S530
F110
0.2
18
铣φ15mm的沉孔至尺寸
19
精镗φ38mm的通孔至尺寸
T1212
φ38镗刀
H12
S900
F120
20
检测、校核
第七节加工程序
①去边角余料加工子程序
序号程序内容程序说明
O2002子程序名
N5G00G41X0Y98.03D01;
建立刀具半径补偿
N10G01G90Z-5;
Z向增量下刀,切深
5mm
N15X15.0Y120.0;
N20X51.33;
N25X0Y47.0;
N30Y0;
N35X160.0;
N40Y47.0;
N50X145.0;
N55X160.0Y98.03;
N60G00G40;
取消刀具半径补偿
N65M99;
子程序结束
②凸槽轮廓加工子程序
O2003子程序名
N5G91G01Z-5;
Z向增量下刀,切深5mm
N10G90X15Y25;
N15X71.81Y106.13;
N20G02X88.19Y106.13R10;
N25G01X130.95Y45.07;
N30G02X130.48Y38.76R5;
N35G03X125.40Y29.0R25.0;
N40G02X120.51Y25.0R5.0;
N45G01X39.49Y25.0;
N50GO2X34.6Y29.0R5.0;
N55G03X29.52Y38.76R20.0;
N60G02X29.05Y45.07R5.0;
N65G03X-3.72Y68R20.0;
圆弧切出至工件外
N70M99;
③菱形槽轮廓加工子程序
O2004子程序名
N10G90X91.876Y56;
N15G03X100.07Y71.74R10.0;
圆弧切入至工件轮廓上
N20G01X88.19Y88.7;
N25G03X71.81Y88.7R10.0;
N30G01X59.09Y71.74;
N35G03X59.09Y60.26R10.0;
N40G01X71.81Y43.3;
N45G03X88.19Y43.3R10;
N50G01X100.07Y60.26;
N55G03X91.876Y76R10;
N60G40G01X80Y66;
④铣半通槽加工子程序
O2005子程序名
N10G90X180.0Y24.0;
切线方向切入
N15X154.0;
N20G03X145.0Y8.0R8.0;
N25G01X180.0;
切线方向切出
N30M99;
⑤加工主程序
O2001主程序名
N5G17G90G40G80G49G21;
G代码初始状态
N10T01;
N15M06T02;
主轴换上T01号刀
N20G90G54G00X-80.0Y60.0;
工件坐标系设定
N25M03S240;
主轴正转
N30G43Z100.0H01;
刀具长度补偿,至安全高度
N35Z0.5;
切入下刀
N40G01X240.0F280;
切削
N45G00Z100.0M05;
退刀,主轴停止
N50G91G28Z0;
Z轴回参考点
N55G49;
取消刀具长度补偿去边角余料粗加工
N60M06T03;
主轴换上T02号刀
N65G90G54G00X0Y0;
N70M03S300;
N75G43Z100.0H02;
N80G00Z0F280;
Z向子程序调用点
N85M98P22002;
调用O2002号子程序
N90G00Z100.0M05;
N95G91G28Z0;
N100G49;
取消刀具长度补偿
N105M06T04;
主轴换上T03号刀
N110G90G54G00X0Y0;
N115M03S210;
N120G43Z100.0H03;
N125G00G41X15.0Y25.0D02F100;
N130G01Z0;
N135M98P22003;
调用2次O2002号子程序
N140G00G40X0Y0;
N145Z100.0M05;
N150G91G28Z0;
N155G49;
粗铣菱形槽
N160M06T05;
主轴换上T04号刀
N165G90G54G00X0Y0;
N170M03S210;
N175G43Z100.0H04;
N180G00G41X80.0Y66.0D04;
N185G01Z0F45;
N190M98P22004;
N195G00Z100.0M05;
N200G91G28Z0;
N205G49;
粗铣半通槽
N210M06T06;
主轴换上T05号刀
N215G90G54G00X0Y0;
N220M03S320;
N225G43Z100H05;
N230G00G41X180.0Y24.0D06;
N235G01Z0F30;
N240M98P22005;
N245G00Z100.0M05;
N250G91G28Z0;
N255G40G49;
钻中心孔
N260M06T07;
主轴换上T06号刀
N265G90G54G00X25.0Y80.0;
N270M03S1000;
N275G43Z100H06;
N280G99G81X25.0Y80.0Z-5.0R10.0F100;
钻孔循环,刀具返回R点
N285G98X135.0Y80.0;
钻孔循环,刀具返回起始点
N290G80G91G28Z0;
取消循环,Z轴回参考点
N295G49;
取消刀具长度钻φ12、φ38的孔至φ11.8
N300M06T08;
主轴换上T07号刀
N305G90G54G00X25.0Y80.0;
N310M03S550;
N315G43Z100H07;
N320G99G83X25.0Y80.0Z-38.5R10.0Q5F50深孔排屑循环,刀具返回R点
N325G98X135.0Y