球磨机操作工培训资料Word文档格式.docx
《球磨机操作工培训资料Word文档格式.docx》由会员分享,可在线阅读,更多相关《球磨机操作工培训资料Word文档格式.docx(14页珍藏版)》请在冰豆网上搜索。
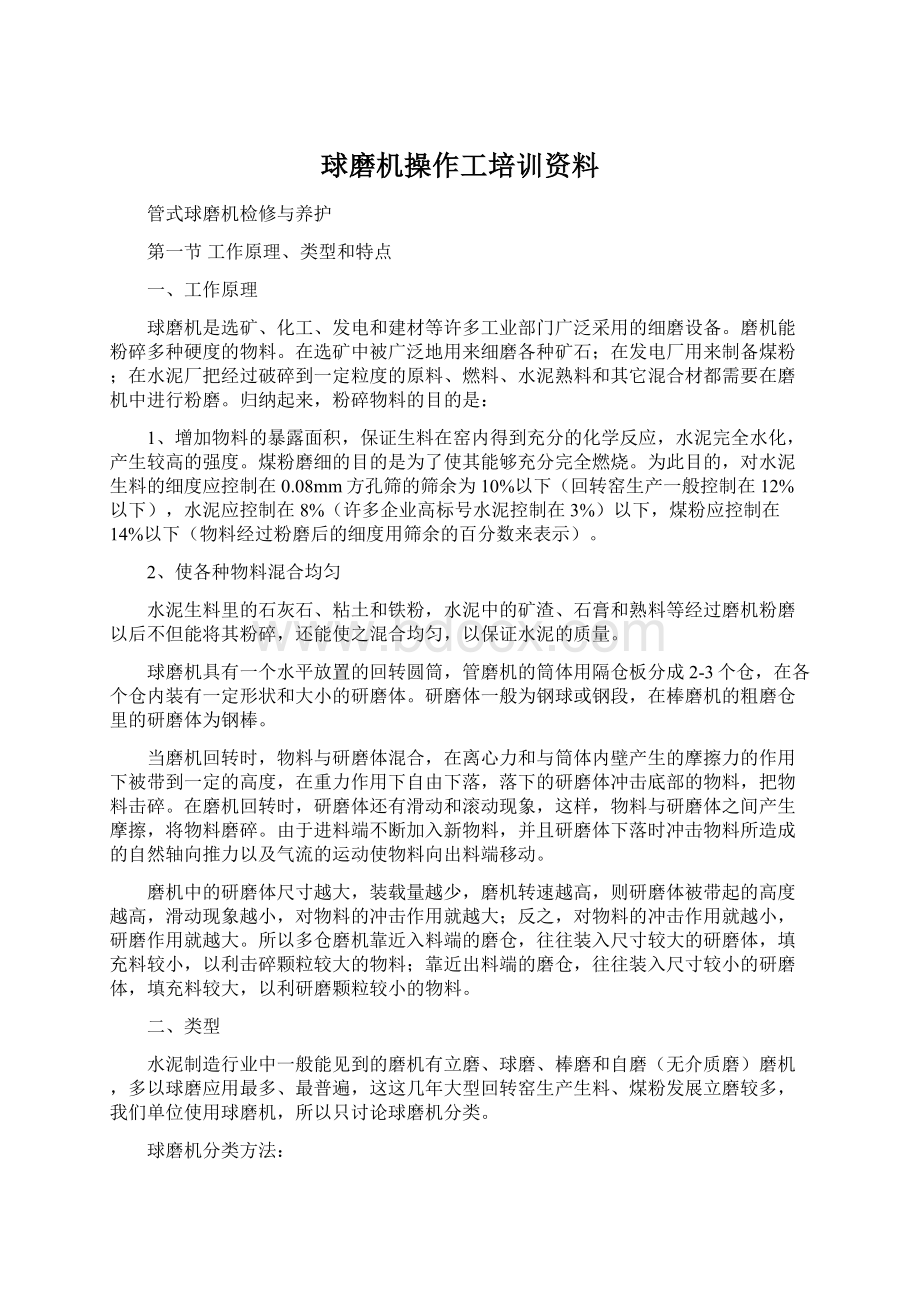
3、砾磨机
用砾石、瓷球为研磨介质,以花岗岩、瓷料作衬板,用以生产白色、彩色水泥及陶瓷工业使用。
二)按照筒体现状分类
1、短型磨机
筒体长度与直径之比L/D≤1-1.5,一般用以粗磨或一级磨。
2、长筒型磨机
筒体长度与直径之比L/D≥1.5,当L/D=3-5则称为管磨机,生料磨长径比较小,水泥磨长径比较大,管磨机内部常分隔为几个仓,称为多仓管磨机,这种磨机在水泥厂用得较多。
这几年出现了长径比很大的磨机,采用开流生产,称高细磨。
三)按照卸料方式分类
1、中心卸料
出料口在磨机中心轴孔,这种卸料最普遍,我厂煤磨、水泥磨都是这样。
2、周边卸料
在筒体端盖的圆周边开有卸料孔,物料从孔中卸出。
3、中间卸料
出料口在磨机筒体的中间,开有许多椭圆孔,物料从孔中卸出,这种磨机相当于两台周边卸料磨机的合成,设备紧凑,单位动力产量高,多用于有选粉机的圈流系统。
我厂生料磨就是这种卸料方式。
四)按传动方式分
1、中心传动
由卸料端径中空轴直接与减速机出轴联接,由电动机带动,传动轴的中心与筒体中心线一致,我厂生料及水泥磨都是中心传动。
2、边缘传动磨机
这种磨机的传动装置是将电动机的动力经过减速机后,传到与磨机筒体中心线相平行的传动轴上。
再经过这根轴上的小齿轮带动装在磨机筒体上的大齿轮,使磨机回转,我厂煤磨即此传动。
三、特点
管磨机的主要特点如下:
一)优点
1、对各种物料都能适应,能连续生产,生产能力大,可以满足工业上大规模生产的需要;
2、粉碎比大,可达到300以上,并易于调整产品的细度;
3、可以适应各种不同情况下作业,既能干法生产,也可湿法生产。
还可以把干燥和粉磨工序合并在一起同时进行生产;
4、设备本身操作可靠,能够长时间连续运转;
5、维护管理简单易行;
6、有很好的密封装置,可防止粉尘飞扬。
二)缺点
1、能耗大、效率低。
在生产水泥的过程中,用干粉碎作业的电量约占全厂用电量的2/3,据统计,每生产一吨水泥的磨机耗电量不低于70Kwh.,但这部分电能的有效利用率却很低。
据分析,磨机输入的功率用于粉碎物料(做有用功)的功率消耗只占约5-10%,而绝大部分电能消耗于其它方面、主要转化为热能和声能而消失掉,这是一项很大的浪费;
2、体型笨重;
3、由于磨机筒体转速很低,如甩普通电动机驱动,则需配置昂贵的减速装置。
大型减速机制造成本和加工精度都很高;
4、研磨体在冲击和研磨物料的同时,本身也受到磨削,筒体内的衬板,隔仓板等零件也被磨损,因此在整个水泥生产过程中,粉碎作业(生料制备,磨水泥)所消耗的钢铁量是很多的,据分析,大约每生产一吨水泥的钢铁消耗量为1Kg左右。
第二节主要参数的确定
一、转速
(一)临界转速
为了确定球磨机的适宜工作转速,首先研究球磨机的临界转速。
能使研磨体升举至脱离角,即研磨体上升至顶点这样一个临界状态,若转速再加快一点,理论上,研磨体将紧贴在筒壁上,随筒体转动不会落下,这个转速就叫临界转速,用nkp表示。
由于磨机在某一转速下进行工作时,筒体内各层研磨体运动的脱离角各不相同,在确定磨机筒体转速时,一般均以最外层研磨体为基准。
经理论推导,临界转速为nkp=
=
欲使研磨体能落下来将物料击碎,磨机的转速必须低于临界转速。
(二)球磨机的理论适宜转速
理论上,当脱离角00时,由于研磨体紧贴在筒壁上,不能起任何磨碎作用,因此对物料粉碎功为零。
当磨机筒体转速极低时,研磨体没有被筒壁带起,所产生的冲击粉碎功也为零。
由此可见,磨机中研磨体对物料的粉碎功是筒体转速的函数,而使研磨体产生最大的粉碎功的转速,称为磨机适宜转速。
欲产生最大粉碎功,研磨体必须有最大降落高度。
经计算得出研磨体最适宜脱离角为54040、,在此脱离角时,研磨体落下高度最大磨机转速应是临界转速的76%,在生产实际上可能略有出入,但都在76%上下波动。
(三)球磨机的工作转速
球磨机适宜转速
,是根据筒体内最外层研磨体,当磨机转动时具有最大降落高度的观点所确定的。
这个观点没有考虑到研磨体随筒体内壁上升的过程中,部分研磨体有向下滑动和滚动现象,这不仅影响研磨体的提升高度。
而且也使筒体衬板和研磨体造成附加磨损。
同时还应该考虑到球磨机对物料的粉碎作用是冲击和研磨的综合效应。
为了使磨机具有最好的粉碎效果,应该考虑冲击和研磨作用的平衡问题。
实际上,在确定磨机的工作转速时,应该考虑到磨机的规格,生产方式,衬板形式,研磨体种类,填充率,披磨物料的物理化学性质,入磨物料的粒度,要求产品的细度等因素。
具体说,衬板表面与研磨体摩擦系数较大者,如突棱衬板,转速可低些;
对平衬板转速可适当高些。
磨机内研磨体填充率越低,相对滑动越大,则转速应高些,反之则相反。
水泥厂运行的多仓管磨机的工作转速,实际工作转速都作适当调整修正,一般修正公式:
当D>2m时,转速=
-0.2D
当1.8m≤D≤2m时,转速=
当D<1.8m时,转速=
+(1-1.5)
二、磨机功率
物料粉磨是水泥生产中消耗电力最大的工序,用来拖动磨机的电动机功率主要消耗在以下两个方面:
一方面用来提升研磨体和粉磨物料,以及使研磨体具有一定的运动速度抛射出去;
另一方面是较小部分的功率消耗在主轴承和传动系统的机械摩擦上。
理论推导功率计算公式:
N=
,
G----研磨体总量;
R----磨机净空半径;
n-----转速;
----机械效率0.86-0.92
磨机实际配套功率比计算值增加10-15%余量,以免临时性超载。
三、研磨体的填充率
研磨体的填充率是指研磨体的堆积体积占磨机有效容积的百分比。
填充率所以成为重要的参数之一的原因在于它不但直接关系着粉磨过程的冲击次数及研磨面积,而且还影响着研磨体本身的提升高度,即对物料的冲击力。
对于多仓的管磨机,研磨体的填充率平均为25-35,%之间;
开流磨居低值,圈流磨居高值。
这样的填充率,能以最小的电耗而获得最大的生产率(指每吨研磨体的单位生产率)。
即这样的填充率比较经济。
另外,适当地增加磨机的填充率,又是提高磨机台时产量的一项措施。
但单位产品的电耗也要有所上升。
因此,确定磨机的填充率就是要妥善处理生产率和生产经济性的矛盾。
适宜的填充率又与磨机的长径比有关,随长径比减小填充率要加大。
以上谈的是一台多仓管磨机研磨体填充率的平均值,实际上研磨体在各仓的填充率是不一样的。
一般情况下应该是从入料到出料逐仓依次递减成阶梯状(棒球磨例外),装有钢段磨仓的填充率稍低有利,因钢段堆积紧密,不易滚动,从而产生较大的偏心力矩。
研磨体的装载量决定于磨机的规格和填充率,其计算式为:
G=
D2L
式中G———磨机内研磨体装载量;
D———磨机有效内径;
L———磨机有效长度;
———研磨体填充率;
———钢球堆积容量,一般取4.5t/m2。
四、磨机的产量
影响磨机产量的因素很多,从大的方面看,可分为物料的性质,磨机本身的结构,规格,转速和操作条件。
而要求磨机的生产能力是由要求的粉磨物料量来确定的。
如生产水泥的原料磨或水泥磨是以窑的煅烧能力来决定的,并要求有一定的富余能力。
在工艺设计上磨机的利用率比窑为低,当窑的利用率为90%时,磨机的利用率也就是75%-80%.
至于物料性质的影响,是指入磨物料的粒度,硬度,温度和湿度,要求磨细的程度和加料均匀程度。
磨机本身的结构指示长度和直径之比,仓数,隔仓板和衬板的形状以及研磨体的装填情况。
因此,准确地确定磨机的产量是比较困难的。
第三节磨机的构造及主要零部件
一、磨机的构造
管磨机是一种重要的细磨设备,这种设备在水泥工业和选矿工业中应用很广泛。
管磨机由于筒体较长,可使物料在磨内粉磨的时间较长,得到成品的细度也较高。
管磨机的规格是以筒体的内径和筒体长度的乘积来表示的,如∮3.5×
10m磨机。
磨机总体结构主要分三大部分:
即回转部分、支撑部分和传动部分。
回转部分包括筒体及其内部安装的衬板、隔仓板、出料篦板等各种衬板,筒体采用钢板焊接,两端设有端盖,端盖上固定中空轴颈,中空轴颈内固定有螺旋叶片或套筒,利于进料和出料。
支撑部分是指两端中空轴颈相配合的主轴承,它承受回转部分全部质量,安装于轴承底座上,并保持水平。
传动部分包括电机、减速机、大小齿轮及联轴器等,它提供设备动力和必要的转速。
二、磨机主要零部件
一)筒体
磨机的筒体是用钢板卷制焊接的薄壁壳体,内部装有各种衬板,筒体上开有人孔门,以便检修和装填研磨体;
人孔形状应具有较大圆角的矩形或椭圆形,以减少应力集中,人孔盖的结构形式,目前有以以下两种,一种是“内提式”的,另一种是“外盖式”的。
外盖式磨门在开启时,往往由于内衬四周缝隙中嵌有碎的物料块而不易打开,但装盖时较方便。
二)衬板
为了避免研磨体及物料对筒体的直接冲击机磨损,在磨机筒体内部铺设了一层衬板,同时也可以利用衬板的不同表面形状来调整各仓研磨体的运动状态。
筒体内物料粉磨过程是:
在第一仓(入料端)物料粒度大,主要以冲击破碎为主,研磨体应为抛落状态,后面仓物料粒度逐步变小,其破碎形式应以研磨为主,,研磨体呈倾泻状态,不要求研磨体提升很高;
但是,研磨体的运动状态取决于筒体转速,对于同一台磨机转速是相同的,要解决这个矛盾,就要利用衬板的不同表面形状具有不同的摩擦系数,来改变各仓研磨体的运动状态,以适应不同粒度物料的粉磨需求。
1、衬板的材料和尺寸
球磨机的衬板大多数是用金属材料制成,也有少数是用非金属材料制成的。
由于各仓研磨体的运动状态不同,为适应这种不同工作状态的要求,各仓衬板材质选择也有所区别。
在粉碎仓,衬板应具有良好的抗冲击性能,传统选用高锰钢(ZGMn13,改性高锰钢ZGMn13Cr2),它有较高的抗冲击韧性,而且在受冲击后表面能够冷作硬化,变得坚硬耐磨。
在细磨仓的衬板主要应具有良好的耐磨性能,经常采用的有耐磨白口铁、高铬铸铁,冷硬铸铁,中锰稀土球墨铸铁。
这几年出现许多中合金衬板,综合性能很好,可以用于各仓衬板。
衬板规格尺寸主要应考虑到能自由地进入磨门,同时便于检修更换衬板。
单块衬板的重量不宜过大,最好一个人能搬运,减轻检修时的劳动量。
一般衬板重量在25-60Kg.为宜。
还要考虑衬板尺寸不能过小,不然衬板数目就会增多,相应的筒体上螺拴孔数也增多,会削弱筒体的强度。
同一台磨、衬板的尺寸规格尽可能少,这样便于制造和配件管理。
2、衬板表面形状
衬板表面形状不同,对研磨体的牵制能力也不一样,根据磨机特性和粉磨物料粗细不同来选择衬板的表面形状。
衬板表面形状的一些基本类型有以下几种:
2.1、凸棱衬板
它是在平衬板上铸成断面为半圆或梯形的凸棱,这种衬板在牵制研磨体时,除去衬板与研磨体之间的静摩擦力外,还附加了凸棱侧面对研磨体的直接推力,这就大大加强了衬板对研磨体的牵制能力,使研磨体可提升得较高,给研磨体以强能量大的冲击。
所以凸棱衬板适用于多仓管磨机的第一仓,对于物料块度大,硬度高而需要较大破碎能力的场合更为合适。
它也是改造转速略低磨机的一种有效的衬板形式。
但是凸棱磨损后与其相连的尚未损坏的平板也要一起报废,这样造成材料利用不合理。
不然粉磨效率就要降低,所以现在使用的较少。
2.2、波形衬板
使凸棱衬板的凸棱平缓化就形成了波形衬板。
对于一个波节上升部分对提升研磨体是很有效的,而下降部分却有些不利的作用。
这种衬板带球的高度较凸棱衬板显著减少。
实际上会使研磨体产生一些滑动,但能避免某些研磨体抛起过高的不良现象出现。
2.3、波纹衬板
这是一种适合细磨仓铺设的衬板,可以用螺栓联结在筒体上,也可以不用螺栓而镶砌在筒体上。
为了适应细磨仓内研磨体尺寸较小及较低的提升高度的需要,而设计成较低的波峰和较小的节距。
2.4、阶梯衬板
由于平衬板存在比较大的弱点,就是摩擦力不足以防止研磨体沿其表面滑动。
若让衬板表面形成一个倾角与原有的摩擦角合成,加大衬板对研磨体的牵制能力,这也就是阶梯衬板极产生的理论基础。
至于阶梯衬板表面曲线的形式,经我国设计人员通过分析比较得出:
工作表面呈阿基米德螺线的衬板,由于它的各点厚度增加量与转角成正比,这样沿整个衬板表面的牵制系数必然相等。
这种衬板广泛使用于粗料仓。
2.5、分级衬板
衬板在轴向成斜面,错位安装,磨机回转时起到研磨体分级作用,尺寸大的研磨体推向物料粒度大的一侧,使破碎冲击作用与粒径吻合,是很好的一种衬板,这几年得到很好推广应用。
2.6、沟槽衬板
断面为沟槽,使钢球在衬板上以密排六方结构堆积,使球与物料充分接触,提高筒壁处能量利用率,提高粉磨效率,现在第一仓大多使用这种结构的衬板。
三)、隔仓板
磨机根据筒体长度与直径比值不同,在筒体内用隔仓板分隔成不同数目的仓室,一般长径比<2.0的为单仓;
长径比=2.0-3的为两仓,长径比>3的为三仓磨或四仓。
1、隔仓板的作用
3.1分隔研磨体,在粉磨过程中,物料的颗粒尺寸(粒度)向磨尾方向递减,也就要求研磨体开始以冲击作用为主、向磨尾方向逐渐过渡到以研磨作用为主。
这样就要求研磨体的尺寸也向磨尾方向递减,隔仓板可将研磨体加以分隔。
3.2防止大颗粒物料窜向出料端隔仓板的篦板对物料有筛析作用,可以防止过大的物料颗粒进入冲击力较弱的区域,不然,破碎不了的料块将堆积起来,严重影口向粉碎效果。
3.3控制物料的移动速度隔仓板的篦板孔决定了磨内物料的填充程度,同时也控制了物料在磨内经受粉磨的时间,相应地统一了产量和质量这一对矛盾。
2、隔仓板的类型及性能
隔仓板按结构可分为单层和双层两种类型:
小磨机为单层隔仓板,大磨机为双隔仓板,仓板主要受研磨体的挤压和磨剥,受冲击力不大。
在材料选择上宜采用塑性较好的高锰钢铸件。
四)磨机的进出料装置
1、进料装置:
常见两种,一种是圆锥漏斗形式的进料器;
另一种是螺旋叶片进料器。
2、卸料装置:
一种是中心传动,物料经过出料篦板直接从中间或筒体边缘卸料;
一种是边缘传动磨机,物料从出料篦板磨头装有径向螺旋,把物料旋入中空轴,物料从中心锥体或螺旋卸料。
五)主轴承
1、主轴承构造
主轴承是磨机的支撑部件,筒体、物料、研磨体的重量及运动离心力都全部由其支撑。
各类磨机主轴承结构有所差异,但基本构造大致相同,都由轴瓦、轴承箱、润滑及冷却系统组成。
由于磨机体重很大,磨机回转时各种作用力的合力方向近似垂直向下,所以主轴承只需要下轴瓦,小型磨机是中心夹角1200-1800轴瓦,大型磨机现在使用两块筒体夹角600的中心夹角300轴瓦(又称滑履轴承)。
磨机两主轴瓦安装间距很大,为了保证轴瓦同心,轴瓦底部制造成球面,利于自动调节对正。
为了防止球面瓦受力后从轴承座内滑出,用定位螺钉和压板来固定控制,在安装时定位压板与球面瓦间隙一般在2-4mm.
2、轴瓦的冷却润滑方式
磨机主轴承在工作时,由于摩擦产生的热和热物料通过空心轴时把热量不断地传给轴瓦。
如果不及时把热量排除,将使轴瓦温度升高,破坏润滑条件,甚至造成烧瓦事故。
因此主轴承必须具备有冷却润滑装置。
主轴承是通过铸在轴瓦内的却水
道,连续不断通过冷却水使轴瓦降温的,主轴瓦内部有铸孔式冷却水道或蛇形管过水冷却。
主轴承工作时,必须有可靠的润滑装置,以减少轴瓦发热,大型磨机多使用稀油站强制润滑,中小磨机多采用油圈及油勺带油润滑,依靠固定在中空轴上的油圈或油勺,油圈浸到主轴承座油池里,当磨机回转时,油圈源源不断地将油池中的油带到中空轴上方,再由刮油器刮下,流至空心轴。
油勺带油与之相似,只是不要刮油器。
它们的特点是供油量少,但比较安全可靠。
3、轴瓦材料
球面瓦必须用优质灰铸铁或铸钢制成,在球面瓦的工作表面铸有一层具有一定强度,跑合性能,减磨性能及耐磨性良好的轴承衬,这种轴承衬很容易和轴颈跑合妥贴。
这种轴承合金的弱点是机械强度低,并且与钢铁的贴附性差。
目前常用的轴承合金有两种:
锡基的有ZChSnSb11-6.,铅基的有ZChPbSb16-16-1.8。
六)传动装置
磨机传动的特点和发展过程,磨机是一种重载,低速,转速恒定的机械。
初期的磨机都是边缘传动,即动力最后经磨体上的大齿圈而转动磨体。
后来由于开式齿轮传动弱点的逐渐暴露,慢慢又出现了以减速机为重要环节的中心传动方式。
从根本上解决了大型磨机传动的经济性和合理性。
但在一定的条件下边缘传动仍保留它的应用价值。
随着磨机功率的增大,后来又出现了双传动磨机,它是由两个相同的电动机共同驱动。
双传动有边缘传动和中心传动。
双传动的出现,为设计和制造大型磨机的传动开辟了新的途径。
中心传动比较简单,由电机、减速机、电机及慢驱组成。
边缘传动相对复杂,故障也较多,由电机、减速机、大小齿轮、二轴组件及电机组成。
三、研磨体
一)种类
磨机用的研磨体从外形上可以分为球,段和棒。
钢球是磨机中最普遍采用的介质,
其规格是以球的直径大小来表示。
钢球的直径在30-120mm之间,分成许多级,每级球径相差10mm。
由于钢球工作时不断的冲击和研磨物料,本身磨损也较快。
钢段是一种短圆柱体,其特点是具有较大的研磨表面积,工作时段与段之间基本上是线接触,置于细磨仓。
钢段的规格是以“直径×
长度”来表示的。
钢棒是装于湿法生料磨粗磨仓内的一种研磨体,构成棒球磨机。
棒较钢球的质量大得多,对喂入磨内的大块物料作用力集中,容易得到粉碎,同时钢棒之间也是线接触,较钢球对物料点接触的冲击机会增多。
棒仓对喂入物料粒度有较大适应性,产品粒度均匀,粉碎效率也高。
二)材质
由于钢球工作时彼此之间不断地冲击和研磨物料,故要求选用的钢材要耐磨,坚硬不易碎裂,目前多采用高碳钢和高铬钢铸造而成。
细磨仓的段有的采用钢段,有的采用铁段,它们的长径比1-1.3。
三)级配
为提高磨机的粉磨效率,降低单位产品的耗电量,在满足研磨体装载量的前提下,研磨体的级配也是一个十分重要的问题。
根据物料的粉磨原理,大块物料主要依靠研磨体的冲击作用将其击碎,这就要求研磨体的质量大一些,而小块物料主要靠研磨体的研磨作用将其磨细,当然接触面积越大,研磨的效果越好。
为了适应各种粒径物料的冲击和研磨作用的需要,需将不同尺寸的研磨体、按照合适的比例配合在一起装入磨内。
称之为研磨体的“级配”。
一般在粗磨仓多为3-5种不同直径的钢球,在细磨仓采用两种不同尺寸的段配合在一起。
在同一仓里不同规格的研磨体的装填量是两头小,中间大。
磨机运转过程中,研磨体将逐渐磨损,质量变小,使磨内研磨体的数量与级配发生变化,影响粉磨效果,因此,磨机运转一定时间后必须添补研磨体,否则将会影响磨机的生产能力。
第四节管式球磨机的检修
一、检修周期
球磨机运转时间以每日24小时为计划检修依据,其计划检修分为大、中、小修三类,小修周期2-3月,中修周期20-24月,大修周期一般48月。
注:
检修时间按一天三班工作制。
二、管式球磨机的修理内容
1、小修项目
(1)各部固紧螺栓的松紧检查、拧紧。
(2)循环油路疏通检查,油勺检查,滤油槽清理。
(3)筒体衬板、进出料端料板、中间隔仓板、筛板、筛筒等检查或部分更换。
(4)进料口螺旋器疏通。
(5)减速机的油量补充。
(6)进出料漏斗检查修补。
(7)润滑装置的检查、修理,疏通油路。
(8)水冷却系统检查、修理,调整密封、疏通水路。
(9)大小齿轮啮合情况检查调整。
(10)各主传动部分检查、调整。
2、中修项目
(1)包括小修项目。
(2)筒体内部各种衬板的更换。
(3)主轴瓦磨损检查,刮研或更换。
(4)小齿轮轴衬套的磨损检查,刮研或更换。
(5)传动小齿轮组件检修或更换。
(6)减速机解体清洗,部件磨损检查,传动齿轮组件更换。
(7)高速和低速两级联轴节的径向位移,倾斜度的复位,联轴节的螺栓、胶圈的检查及更换。
(8)传动齿轮的啮合情况检查及间隙调整。
(9)大齿轮罩的整形、修复。
(10)修正筒体局部变形,补焊筒体裂纹。
(11)检测并调整筒体中心线的水平偏差。
(12)漏斗的修复及更换,出磨筛筒、筛筒罩及排气筒修理或更换。
3、大修项目
(1)包括中小修项目。
(2)筒体、中空轴端盖的更换。
(3)大齿圈的修正、翻面或更换。
(4)大小轴承衬的更换。
(5)大小轴承座及底盘的修整及更换。
(6)小齿轮组件更换,减速机整体更换。
(7)基础的修正,消除缺陷,提高强度。
(8)更换联轴器总成,调整并校正传动系统。
第五节、球磨机的操作要求
球磨机机旁操作规程
1主题内容和适用范围
1.1、本标准规范了球磨机安全操作维护要求,适用于设备机旁的安全操作的要求。
1.2、本标准适用于球磨机巡检工机旁操作,也适用于设备维修工、中控室操作员参考。
2、安全操作要求
2.1凡操作人员应掌握磨机的主要结构、设备性能及操作要点。
2.2开车前的准备与检查:
2.2.1清除机器周围有碍运转的杂物,开机信号铃是否良好,辅传是否与主机脱开;
2.2.2检查所有紧固件是否安全牢固;
2.2.3检查各润滑点情况是否良好。
有稀油站的要检查高低压泵是否正常,润滑系统的流量、油位是否达到规定范围;
冬季稀油站温度不小于25℃,否则应用电加热器加热,使油温达启动要求;
2.2.4检查冷却水管是否畅通,各处无泄露密封良好;
2.2.5所有有关仪表、照明、信号装置均应完整良好;
2.2.6电动机及控制系统均应完整良好;
2.7所有附属设备应运转正常;
2.2.8电源电压要在规定范围内;
2.3、开车注意事项:
2.