锅炉运行操作规程Word文件下载.docx
《锅炉运行操作规程Word文件下载.docx》由会员分享,可在线阅读,更多相关《锅炉运行操作规程Word文件下载.docx(31页珍藏版)》请在冰豆网上搜索。
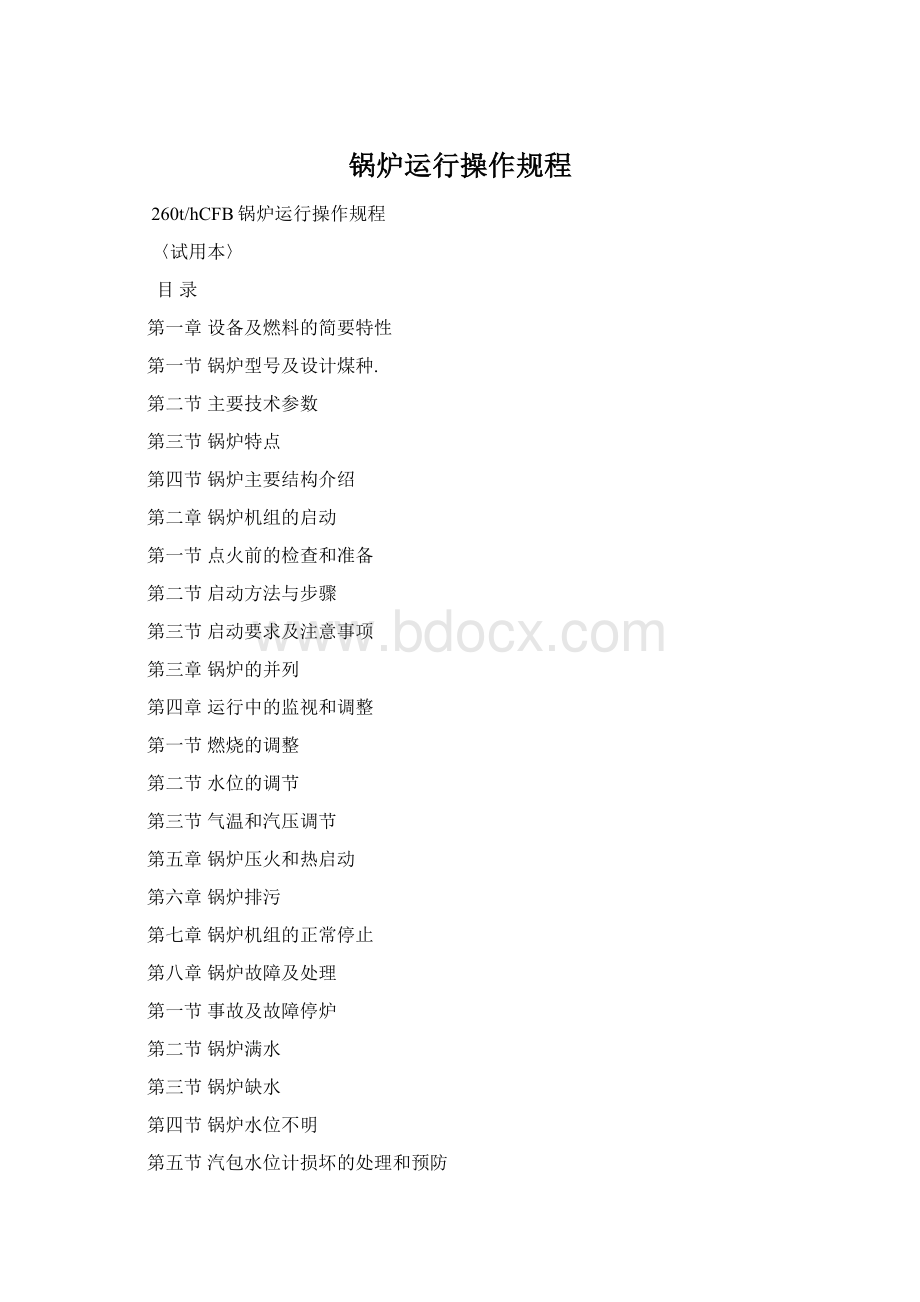
第一节锅炉型号及设计煤种
一、锅炉型号CG-260/5.30-MX
二、锅炉形式中温、次高压、单锅筒、自然循环流化床锅炉
三、制造厂家四川川锅锅炉有限责任公司
四、设计煤种
项目
设计煤种(混合煤种、元素分析)
应用基碳:
Cy
37.16
应用基氢:
Hy
2.1
应用基氧:
Oy
10.01
应用基氮:
Ny
0.33
应用基硫:
Sy
0.57
应用基灰:
Ay
12.61
应用基水分:
Wy
37.1
可燃基挥发分:
Vr
44.15
应用基低位发热量:
Qydw
14100
一、锅炉技术规范
额定蒸发量
260t/h
额定蒸汽压力
5.30MPa
额定蒸汽温度
450℃
给水温度
150℃
空预器进风温度
20℃
设计排烟温度
138℃
锅炉设计效率
90.2%
二、锅炉基本尺寸
锅筒中心标高
42830mm
锅炉高度(顶板标高)
47500mm
锅炉宽度(内、外柱中心线)
13940(23940)mm
锅炉深度(柱中心线)
23650mm
三、燃煤粒度及点火用油
锅炉按照燃烧褐煤设计。
锅炉点火启动和负荷低于30%额定负荷时投用轻柴油。
燃料入炉粒度:
0~10mm;
平均粒径d50约1.8mm,其中小于1mm占30-40%,小于0.10mm的不大于10%,大于5mm的不大于20%。
四、锅炉给水和蒸汽品质
符合GB/T12145-2008《火力发电机组及蒸汽动力设备水汽质量标准》要求。
第三节260t/hCFB循环床锅炉特点
260t/h高温水冷旋风分离器循环床锅炉主要特点如下:
一、采用全膜式壁结构
锅炉的炉膛(包括水冷布风板)、分离器均为膜式壁结构。
二、布置两个“高温水冷旋风分离器”
该分离器由膜式水冷壁加高温防磨内衬组成,锅炉启动不受耐火材料的限制,负荷调节快,冷启动时间时间短;
有水冷却,在燃用不易燃烬的燃料时,对于分离器里可能出现的二次燃烧起冷却作用,避免结焦。
三、过热器的布置
按成熟的中温次高压循环床锅炉布置:
包墙过热器,高低温过热器布置在分离器之后的锅炉尾部烟道内。
选取合适的烟气流速,并采用成熟可靠的防磨措施,满足运行等要求。
过热器面积布置适中,同时辅以给水喷水减温,能满足锅炉负荷大范围变动时蒸汽参数保持稳定。
高温过热器材质为12Cr1MoVG,低温过热器材质为20G。
包墙过热器材质为20G。
四、床下点火
由于采用了水冷风室及水冷布风板,为床下点火创造了条件。
该炉采用床下热烟气发生器点火。
点火用油在热烟气发生器内筒燃烧,产生高温烟气,与夹套内的冷却风充分混合成850℃左右热烟气,经过布风板,在沸腾状态下加热物料。
因此,该点火方式具有热量交换充分、点火升温快、油耗量低、点火劳动强度低、成功率高等特点。
点火采用一次风,结构简单。
五、特殊的回灰系统
本炉型采用高流率、小风量的自平衡J型回灰阀。
回灰系统由分离器灰斗、料腿、J型阀构成,高压风多点布置,保证可靠回料,回料量大,负荷适应范围广,回料系统没有任何运动部件,完全消除了高温条件下易发的机械故障,运行操作简单可靠。
回灰阀的松动风采用高压风(单独的萝茨风机配风),运行操作方便、安全可靠。
六、固定膨胀中心
本次设计借鉴大容量锅炉固定膨胀中心的方法,采用了刚性平台固定中心。
实践证明,锅炉按预定方向膨胀,利于密封。
七、有效的防磨措施
循环流化床锅炉的磨损是影响锅炉连续经济运行的重要因素之一,在炉膛燃烧室、“水冷旋风分离器”内等膜式壁部分采用焊密集销钉+特殊的高温耐磨浇注料进行防磨处理;
对流受热面采用合适的烟速、加防磨盖板等有效措施;
对穿墙等处和某些局部均采取特殊防磨措施。
八、非机械的风播煤结构
采用高速风播煤,解决了正压给煤的密封问题,同时又能将煤播散开,使给煤非常均匀。
第四节260t/hCFB锅炉主要结构介绍
一、总体布置
锅炉采用单锅筒横置式自然循环、“水冷旋风分离器”、膜式壁炉膛前吊后支、全钢架Π型结构。
循环床锅炉燃烧室内飞灰浓度较高,炉室要良好的密封和防磨,本炉采用膜式壁结构。
锅炉燃料所需空气分别由一、二次风机提供,一次风机送出来的风经过一次风空气预热器预热后,由左右两侧风道引入水冷风室中,通过安装在水冷布风板上的风帽,进入燃烧室;
二次风经过管式空预器预热后由二次风口进入炉膛,补充空气与之扰动混合,为保证二次风充分到达炉膛,本炉采用炉膛前后墙分别进风结构。
燃煤在炉膛内燃烧产生大量烟气和飞灰,烟气携带大量未燃烬碳粒子在炉膛上部进一步燃烧放热后,进入“水冷旋风分离器”中,烟气和物料分离,被分离出来的物料经过料斗、料腿、J型阀再返回炉膛,实现循环燃烧。
经分离器后的“洁净”烟气经转向室、包墙、高温过热器、低温过热器、高温省煤器、低温省煤器、一、二次风空气预热器后由尾部烟道排出。
燃煤经燃烧后所产生的大渣由炉底排渣管排出,进入冷渣器将渣冷却至200℃以下,干排渣。
锅炉给水经给水分配集箱,由省煤器加热后进入锅筒,锅筒内的饱和水由集中下降管、分配管分别进入炉膛水冷壁下集箱、水冷屏下集箱以及水冷旋风分离器下部环形集箱,被加热成汽水混合物,随后经各自的上部出口集箱,通过汽水引出管进入锅筒。
饱和水及饱和蒸汽混合物在锅筒内经汽水分离装置分离后,饱和蒸汽通过引入管进入位于尾部竖井内包墙过热器、低温过热器,喷水减温器后,进入高温过热器,加热到额定参数后进入集汽集箱,最后从主汽阀至主蒸汽管道。
二、锅筒及内部装置
锅筒内径为Φ1600mm,壁厚为55mm,材料为Q245R。
锅筒正常水位在锅筒中心线以下100mm,最高水位和最低水位离正常水位各75mm。
锅筒内布置有旋风分离器、梯形波形板分离器、钢丝网分离器和顶部多孔板等内部设备,它们的作用在于充分保证汽水分离,平衡锅筒蒸汽负荷,以保证蒸汽品质。
由于采用了大口径集中下降管,为防止下水管入口处产生旋涡,在下降管入口处有栅格板。
此外,为保证蒸汽品质良好,在锅筒内部还装有磷酸盐加药管、连续排污管和紧急放水管等。
三、炉膛
炉膛由膜式水冷壁构成,截面6130mm×
11650mm,管子为φ51×
5mm,材料20G,节距为80mm,净空高约34m。
前后墙在炉膛下部收缩形成锥形炉底,前墙水冷壁向后弯,与两侧水冷壁共同形成水冷布风板和风室。
布风板面积约35m2。
布风板上部流速设计值约5.05m/s,以保证较大颗粒亦能处于良好流化状态。
在布风板的鳍片上装有耐热铸钢件风帽,该风帽为钟罩型风帽,对布风均匀性、排渣通畅、减轻磨损、防止漏渣有很大好处。
炉膛的四周6.2m高度范围是本炉磨损最严重的部位之一,在此区域水冷壁焊有密排销钉,并涂敷有特殊高温耐磨浇注料。
主燃烧室工作温度850~950℃,由于烟气携带大量循环物料,其热容量很大,故整个炉膛温度较均匀。
四、分离器
本炉布置有两个“高温水冷旋风分离器”,分离器内径为φ5500mm(净空),膜式壁结构。
炉膛后墙一部分向后弯制形成分离器入口段,分离器入口处设有膨胀节,分离器出口和回料管上均设有膨胀节,回料管采用高温防耐磨浇注料做内衬。
五、过热器系统
锅炉采用对流过热器,并配以喷水减温系统。
由包墙管、低温过热器、高温过热器及喷水减温系统组成。
饱和蒸汽从锅筒至侧包墙上集箱,通过侧包墙管,进入低温过热器;
低温过热器布置在尾部竖井中,由两级构成,管子规格为Φ38×
4,材质为20G,光管错列布置。
为减少磨损,一方面控制烟速避免过高,另一方面加盖有材质为12Cr13的防磨盖、压板及防磨瓦,对局部也作了相应的处理。
过热蒸汽从低温过热器出来通过喷水减温器调节后进入高温过热器,高温过热器为三管圈顺列布置,管子规格为Φ42×
4,材质为12Cr1MoVG;
在前排加盖1Cr20Ni14Si2的防磨盖板。
蒸汽加热到额定参数后引入集汽集箱。
六、省煤器
尾部竖井烟道过热器后设有三级省煤器,均采用φ32×
4,材质为20G,省煤器为光管错列布置,并辅以成熟有效的防磨措施,以保证运行寿命。
两组省煤器之间留有~1000mm间隙,便于检修,省煤器进出口集箱位于尾部竖井两侧。
七、空气预热器
在省煤器后布置了卧式管式空气预热器用来加热一、二次风,一、二次风空气预热器采用四流程交叉布置。
一次热风温度约为192℃,二次热风温度约202℃。
空气预热器管子选用φ51×
2mm,迎风面前三排采用φ51×
3mm,材质均为Q235AF/空气进口侧低温段为10CrNiCuP(考登钢)。
每组流程之间留有一定间隙,便于检修和更换。
八、锅炉范围内管道
锅炉为单母管给水,给水母管首先引入给水操作台,通过操作台实现对锅炉给水的调节和控制。
给水操作台分别为三个管道:
DN200、DN100、DN50,分别为50-100%、30-50%额定负荷及上水等用。
给水通过给水操作台进入省煤器。
锅筒装有各种监督、控制装置,如各种水位表、水位自动控制装置、压力表、紧急放水管、加药管、连续排污管等。
所有水冷壁下集箱、集中下降管设有定期排污。
锅筒装有两套全量型弹簧安全阀,过热器集汽集箱也装有两套全量型弹簧安全阀。
集汽集箱上还装有升火排汽管路、反冲洗管路、疏水等管路。
减温器和集汽集箱上均设有读数用和自控用热电偶的插座(规格均为M33×
2),在锅炉各最高点装有排放空气的阀门,最低点有排污阀或疏水阀。
为了监督给水、炉水和蒸汽品质,装设了给水、炉水、饱和蒸汽和过热蒸汽取样装置及冷却装置。
在锅筒和省煤器进水管之间装有再循环管,供锅炉升火时保护省煤器之用。
九、燃烧设备
本炉燃烧设备主要由给煤装置、布风装置、二次风装置、飞灰循环装置、点火装置等组成。
在炉前布置有四套给煤装置,采用播煤风将煤吹入炉内,给煤管外有密封罩,保证良好的密封。
燃烧室一次风约占总风量的50%,由左右两侧风道引入炉前水冷壁室中。
风室与水冷壁直接相连,并随膜式壁一起胀缩,利于密封。
风帽安装在底部水冷布风板鳍片上,风帽采用种罩型风帽。
本炉设置有4根φ219排渣管。
两根作正常排渣用,两根作事故排渣用。
为保证燃烧始终在低过量空气系数下进行,以抑制NOx的生成,本炉采用分段送风。
播煤风、二次风占总风量的50%,通过播煤风口、二次风管分别送入燃烧室。
播煤风管连接在每个给煤机入口,并配有简易风门,以便根据给煤机的使用情况控制入口风量,二次风通过燃烧床前后墙分两层布置,共16根风管(标高7500mm、10100mm)进入炉膛,运行时可调节一、二次风比来适应煤种和负荷变化需要。
回灰系统是本炉的关键设备之一。
本炉设有两个回料器,分别由水冷灰斗、料腿、J型阀、布风床构成。
水冷灰斗由分离器水冷壁收缩而成。
回料腿为圆柱形,悬吊在水冷灰斗上,采用双层结构,保证密封。
J型阀为一高流率、小风量自平衡回灰阀,将循环物料由炉膛后墙送入燃烧室。
J型阀与料腿之间设有膨胀节。
本炉采用水冷布风板和水冷风室,为床下点火创造了条件。
设有两个热烟气发生室,作为点火热源。
由于整个加热启动过程均在流态化下进行,热量是从布风板下均匀送入料层,不会引起低温和高温结焦。
床下油点火方式具有耗油省、启动快、成功率高、环境卫生好、工人劳动强度低等优点。
一、检查所有阀门,并置于下列状态:
1、蒸汽系统:
主汽门经开关试验后关闭。
隔绝门及其旁路门关闭(指七十二小时试运前)。
2、给水系统:
给水门、给水旁路门及放水门关闭,给水调整门、给水中间门、省煤器入口门开启。
省煤器与锅筒再循环门开启(若锅炉无水,在上水前关闭,上水后开启),旁路给水门关闭。
3、减温水系统:
减温器入口门、出口门、调整门关闭,放水门关闭。
4、放水系统:
各联箱的排污门、连续排污门二次门、事故放水门关闭,定期排污总门、连续排污一次门开启。
5、疏水系统:
主汽门前所有的疏水门及主汽门后的疏水门开启。
6、蒸汽及炉水取样门、锅筒加药门关闭,加药泵出口门关闭。
7、锅筒水位计的汽门、水门开启,放水门关闭。
8、所有压力表一次门开启,所有流量表的一次门开启。
9、空气门开启(给水管空气门可关闭),对空排汽门开启。
二、检查所有的风门挡板,并转于下列位置:
1、引风机进口导流叶片开启。
2、一、二次风机进口导流叶片开启,返料器风门开启。
3、检查
(1)
(2)的风门开度是否与表盘一致。
4、旋风筒底部放灰门关闭,燃烧室底部放渣门关闭。
5、给煤机进口闸门关闭。
三、检查燃烧室、料床、返料器等内部无焦渣及杂物;
各种风帽无堵塞现象;
各部分人孔门、检查门、完整,关闭严密,除灰门开关灵活,置于关闭状态;
除灰沟畅通;
盖板齐全。
四、检查转动机械,轴承润滑油洁净,油位正常;
开启冷却水门,水流正常,地脚螺丝及安全罩牢固。
五、与有关人员联系,做好下列准备工作:
1、汽机值班人员:
给水管上水。
2、热工值班人员:
将各仪表及操作装置置于工作状态,并负责更换点火用热电偶。
3、燃料值班人员:
电除尘投入,原煤斗上煤。
4、化学值班人员:
化验炉水品质。
5、电气值班人员:
电器设备送电。
6、准备好足够的点炉材料。
引火烟煤屑(粒度10mm)及沸腾炉渣(粒度8mm以下)。
7、检查点火油栓及供油系统是否正常,点火用轻柴油不少于10t。
8、检查与准备工作完成后,即可按规程要求进行锅炉上水。
第二节锅炉机组启动方法与步骤
一、冷态试验
该试验是为了检验安装质量,了解设备特性,为锅炉的热态运行提供科学的参考数据,如:
风机流量试验、风机风门特性试验、布风板阻力试验、临界流化风量试验、飞灰循环系统回灰试验等。
试验必须记录,试验后绘制好曲线,张挂在控制室内,以备运行人员参考。
具体试验措施按调试方案进行。
二、锅炉点火
1、司炉接到点火命令,按措施要求对锅炉设备进行全面检查,并做好点火准备。
2、进行炉内彻底清扫,清除一切杂物,插入点火热电偶,热电偶端部埋入料面约100毫米。
3、在炉底辅设一层0~8mm的沸腾炉渣及引火烟煤屑(粒度>3mm的应<20%)高度约500~600mm,厚度要均匀。
4、关闭炉门启动引风机和一次风机,保持燃烧室负压为50~100Pa,使底料流化。
5、投入点火油枪,调整油量及点火风门,控制风室温度<
850℃,待料层温度升至450℃~550℃时,启动给煤,适当投煤(建议间断给煤),维持床温稳定上升。
6、当炉温达到850℃左右,将油枪撤出,适当调整给煤机的转速和一次风门,控制炉温在850~950℃。
点火过程中,应适当调节返料风门(点火时投入回灰系统),使其流化循环,直到锅炉进入正常运行状态。
三、锅炉升压
1、随着点火过程,汽压在不断上升,当汽压达到0.1Mpa时,冲洗汽包水位计,并校对其它水位计指示是否一致,关闭汽包和过热器空气门。
2、当汽压升至0.15—0.2Mpa时,联系汽机后开母管来汽门前疏水门进行暖管。
3、当汽压升至0.2—0.3Mpa时,通知热控人员冲洗仪表导管。
4、当汽压升至0.3—0.5Mpa时,对水冷壁各联箱进行一次排污,检查排污门开启是否灵活,保持汽包水位正常。
5、当汽压升至1Mpa时,对锅炉设备再次进行一次全面检查.
6、当汽压升至2Mpa时,对锅炉机组进行全面检查,发现隐患应停止升压,待隐患消除后继续升压。
7、当汽压升到3.0—3.5Mpa、汽温380℃时,冲洗水位计,通知化学化验汽水品质,并对设备进行全面检查,调整汽包水位,通知并列炉减弱燃烧,汇报值长做该炉并列的准备。
8、当汽压达到额定压力,检查膨胀情况,如不正常应查明原因并消除。
四、安全阀的调整
锅筒的安全阀的始启压力为1.06倍工作压力即1.06×
5.83=6.18MPa,过热器的安全阀的始启压力为1.04倍工作压力即1.04×
5.3=5.51MPa。
五、过热器及主蒸汽管道的吹扫
为了消除过热器及主蒸汽管道内的杂物、油垢及焊渣,保证锅炉蒸汽品质合格,因此必须进行吹管工作。
一般采用降压吹管法,吹管工作必须认真作好记录,按有关规程检合格后方可进入锅炉机组的72小时试运阶段。
第三节.启动要求及注意事项
一、在上水过程中应检查锅筒,联箱的孔门及各部的阀门、堵头等是否有漏水现象。
当发现漏水时应停止上水并进行处理。
当锅炉水位升至锅筒水位的负100mm处,停止上水,以后水位应不变。
若水位有明显变化,应查明原因予以消除。
二、要求整个升温升压过程力求平缓、均匀,并在上水前后及升压后检查记录膨胀指示值。
整个冷态启动升温升压过程控制在6小时。
三、.升压过程中,禁止关小过热器出口集箱疏水门或对空排汽门赶火升压,以免过热器管壁温度急剧升高。
四.升压过程中,应开启过热器出口集箱疏水门,对空排汽门,使过热器得到足够的冷却,同时,应监视过热蒸汽温度及过热器管壁温度的变化,蒸汽温度不得超过额定值;
管壁温度不得超过允许承受的温度。
五、升压过程中,省煤器和锅筒再循环门必须开启,在锅炉进水时,应将再循环门关闭。
六、升压过程中,应利用膨胀指示器监视各承压部件的膨胀情况,如发现有膨胀不正常时,必须查明原因并消除不正常情况后方可继续升压。
一、并列应具备的条件
1、接到值长命令。
2、主汽压力低于蒸汽管压力0.1—0.2Mpa。
3、过热器出口温度在400℃以上。
4、保持汽包水位-50mm处。
5、蒸汽、炉水品质合格。
6、设备运行情况正常,燃烧稳定。
7、应与临炉联系,注意监视汽压和汽温的变化。
二、锅炉并列操作:
。
1、在并汽过程中,主蒸汽管道发生水击时,应立即停止并汽工作,减弱燃烧加强过热蒸汽管道疏水,待正常后重新并汽。
2、锅炉并列正常后,可逐渐增加负荷至50%,停留一段时间,然后在一般情况下将负荷增至额定负荷。
3、在带负荷时,司炉应集中精力调整燃烧,保证汽压、汽温、水位的稳定。
专人监视给煤机,防止给煤机断煤。
根据汽温情况及时投入减温器。
4、并列后应对锅炉机组进行一次全面检查,并记录点火至并列过程中的主要操作和发现的问题。
5、经大修后的锅炉并列后,应记录各部膨胀指示值。
6、并列后应再次检查对照水位计和各压力表的指示。
运行中除了按照运行规程对锅炉的水位、汽压和汽温进行监视和调整外,还需结合本炉的燃烧特点进行调整。
1、在锅炉负荷变化时,应及时调整给煤量和风量,保持锅炉汽压和汽温稳定,在增加蒸发量时,应先加风后加煤,减少锅炉蒸发量,应先减煤后减风,改变风煤量时应缓慢交替进行。
2、运行中应加强监视炉温,炉温过高时容易结焦,炉温过低时容易引起灭火,一般控制在850~960℃之间,最低不应低于800℃。
通过合理调整风量、燃料量、灰量的比例,可有效控制锅炉的稳定燃烧。
3、运行中要加强返料器床温的监视和控制。
一般返料器处的料温最高不应大于940℃,当返料器床温太高时,应减少给煤量和负荷,查明原因后消除。
4、运行中监视炉膛差压和料层差压,可通过放细灰和炉低放渣控制。
正常运行中保持炉膛差压约500~2000Pa之间,料层差压约8000~10000Pa之间。
5、投入和调整二次风的基本原则是:
一次风调整流化、炉温和料层差压,二次风调整总风量。
约130t/h负荷时开始投入二次风。
在一次风满足流化、炉温和料层差压需要的前提下,当总风量不足时,以过热器后的氧量为准,正常运行时氧量在3~5%左右,可逐渐投入二次风,随着锅炉负荷的增加,二次风量逐渐增大,当达到额定蒸发量后,一、二风的比例为53%和47%左右。
6、运行中最低运行风量的控制
最低运行风量是保证和限制循环流化床低负荷运行的下限风量,一般不应低于总风量的30%(该数值应通过冷态试验确定)。
风量过低就不能保证正常的流化,有结渣的危险。
在冷炉点火时,不宜低于最低运行风量。
运行调整:
1、正常运行中,流化床温度一般控制在850—950℃,根据床温的变化,调整给煤量、一次风量、循环灰量,控制流化床温度。
给煤量的调整操作要平稳,不得在短时内做大幅调整,给煤过量会引起爆燃,床温升高而结焦,给煤量过小或中断给煤会造成床温下降甚至熄火。
保证床温稳定以控制循环灰量为主,其次以风煤配比的变化来辅助床温的调整。
2、在床温正常范围内尽量保持在上限运行。
根据床温的变化,随时调整适当的风煤比以及循环灰量。
在增加负荷时应先加风量,再增加给煤量,然后根据床温变化及时调整循环灰量,减负荷时先减少给煤量,在减少风量,然后根据床温及时调整循环灰量。
3、风量的调节主要是以二次风作为变量调节的,可参照过热器后烟气含氧量,使之保持在3—5%范围内。
4、返料温度的监视与控制
运行中要加强对返料温度监视一般返料器入口烟气温度不超过950℃,当返料温度升得太高可适当减少给煤量和负荷,及时调整至正常范围。
若床温偏低,可以减少循环灰回送量以稳定床温。
运行中返料的温度高于床温20--30℃
5、料层阻力的控制
料层阻力是表征流化床料层厚度的量,一定的料层厚度对应一定的料层阻力,料层太薄,流化床上床料量少、易造成流化质量不良燃烧不稳定,同时炉渣含碳量高造成不经济。
料层太厚,使料层阻力增大,电耗损失增加,料层阻力应由排渣量来控制,排渣量大,料阻小,反之亦然,如排渣管堵,要尽快疏通;
如因排渣系统故障,应用事故排渣,并适当减负荷,一般料层阻力应保持在3~4kpa,正常运行后应投入排渣自动。
6、增加锅炉负荷时先增加循环灰的回送量,相应的增加一、二次风量,然后在增加给煤量,减负荷时相反,负荷调节过程中应维持床温,床压基本不变。
7、在达到满负荷时,一次风占总量50~60%,二次风量占总风量的20~45%,返料风控制在15~20%。
一、保持锅炉水位正常,值班人员必须坚守岗位,密切注意水位变化,保持水位在±
50mm范围内,最高最低不许超过±
75mm,在正常运行中不允许中断锅炉给水。
二、监视水位
1、应以汽包就地水位计为准,接班和值班期间应经常与低地水位计、电接点水位计校对每班不少于2次,就地水位计只做监视和参考。
2、注意给水压力的变化,母管压力保持6Mpa、不低于5.5Mpa,给水压力稳定,给水温度不得低于140℃以下。
3、给水流量变化平稳,避免给水流量变化太大给汽温、汽压带来影响。
三、水位计运行情况
1、汽包水位计指示应清晰,并有轻微波动,否则应及时冲洗,每班对汽包水位计冲洗一次。
2、不允许水位计各部的零件有严重的泄漏,否则将影响水位计指示的正确性。
3、水位计有良好的照明(正常照明和事故照明)。
四、当给水自动调节失灵,使水位不正常时,运行操作人员应将给水“自动”改“手动”,恢复水位至正常范围