大型火力发电厂节能管理的创新与实践Word格式文档下载.docx
《大型火力发电厂节能管理的创新与实践Word格式文档下载.docx》由会员分享,可在线阅读,更多相关《大型火力发电厂节能管理的创新与实践Word格式文档下载.docx(11页珍藏版)》请在冰豆网上搜索。
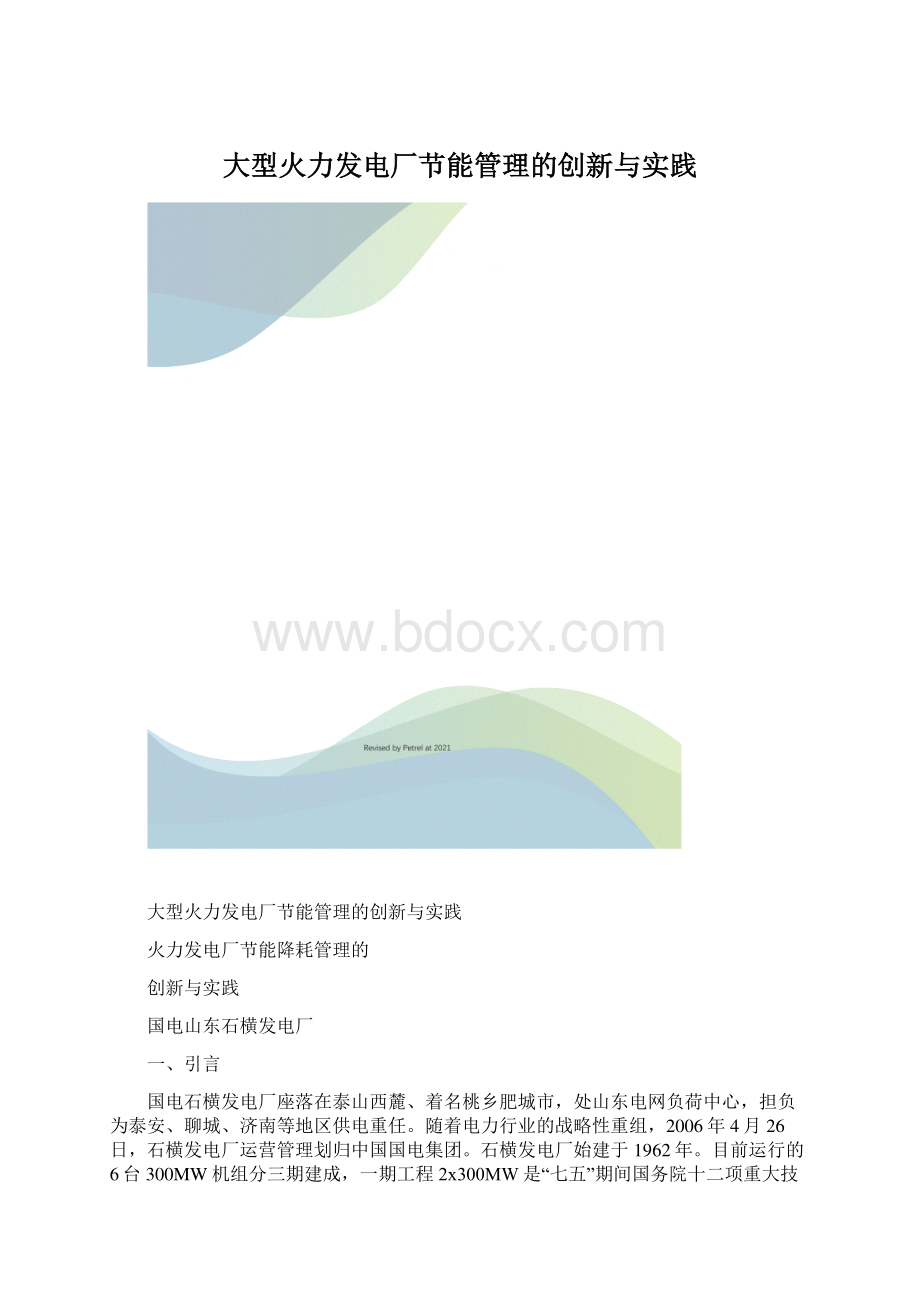
2、完善制度、规范运作
在建立健全管理组织的同时,进一步完善、补充各项节能管理制度,是节能工作更加科学、规范。
加强月度运行分析,及时开展专题分析,分析机组的主要运行参数和经济指标,对照设计值和同类型机组的先进指标,及时提出节能降耗调整意见和分析研究节能运行方案,分专业、分系统进一步细化节能降耗指导意见和可操作性措施。
制定了《周经济参数分析制度》,成立了以运行副总为组长、运行部主任和生技部主任为副组长、各分场分管生产副主任和专业专工位成员的指标管理小组。
指标管理小组对单机煤耗等重要技术经济指标进行日分析、周总结,及时发现运行方式、设备等存在的问题,及时部署运行调整或检修处理。
以下是某周参数对比情况(仅列举部分参数):
表一:
#5机组指标某周完成情况对比分析
序号
指标
单位
机组号
本周完成
上周同比
说明
上周完成
单机比较
平均
影响煤耗(g/kwh)
1
发电量
万kWh
4315.2
6992.6
-2677.4
2
厂用电率
%
#5、6
5.6
6.2
-0.7
-2.195
3
真空
KPa
#5
95.5
95.8
-0.3
0.607
4
排烟温度
℃
127.1
128.6
-1.5
-0.222
5
排烟氧量
4.6
4.8
-0.2
-0.220
#6
5.2
4.3
0.9
6
飞灰含碳量
1.51
1.4
0.1
0.115
7
大渣含碳量
1.3
1.7
-0.4
影响煤耗合计
-1.915
3、细化指标、强化责任、严格考核
按照精细化管理的要求,制订了《经济指标实时考核管理制度》,强化指标异常即缺陷的管理理念,加强节能目标日常管理,及时、合理调整指标定额,将节能指标分解到车间、班组,通过现场计量测试、历史数据库比较等方式核实指标定额,纳入内部承包责任书指标管理。
科学调整全厂指标考核体系,加大对供电煤耗率、厂用电率、发电水耗等关键指标的考核力度,增加了对二、三级支持指标的考核与监督,建立权责明晰、奖惩分明的激励约束机制,用分项指标保一级指标,日指标保月指标,月度指标保年度指标的控制机制。
形成了职责到位、目标明确、考核全面的节能管理体系。
通过此项节能管理的创新,有效的保证了各项指标的完成。
4、及时分析,动态管理
发电厂状态参数是系统或设备运行状况的映像。
机组在不同的方式和状态下相对应的最优控制参数的范围,即机组的正常状态参数。
一旦机组的某个(或某些)状态参数偏离了最优控制参数的范围,就说明机组不是运行在最佳的安全、经济状态下,这个(或这些)参数即视为机组异常状态参数。
通过对机组异常状态参数的分析,找出它们产生的原因,以便及时采取措施,消除缺陷或提出预防事故发生的对策,并为设备改进、运行操作和系统运行方式的优化提供依据,从而不断提高机组的安全、经济运行水平和运行人员的技术水平。
石横电厂按指标的重要程度,将指标进行了分类,一类指标主要包括发电量、厂用电率、发、供电煤耗。
二类指标主要包括凝汽器真空、排烟温度、补水率、飞灰含炭量、用油量、高加投入率等。
在日常工作中对一、二类指标密切追踪,及时开展班组在线和专业人员离线分析得异常参数分析制度。
如当日发现机组发电煤耗升高,应该有运行班组进行在线分析,如果运行人员未发现,则由指标专工在对发生异常参数的班组进行考核的同时,发出异常参数分析通知,运行部对影响发电煤耗的各个原因进行分析,对发现的问题能处理的进行处理,直至发电煤耗恢复正常;
若通过分析,采取一系列调整措施,发电煤耗仍高,并发现设备存在问题,再由指标管理小组进行分析,并制定出解决问题的措施,通过消缺可以解决的问题,严格执行《缺陷管理制度》,无备品的以备品采购管理规定时间来定,需停机处理的,根据系统情况安排,直至发电煤耗恢复正常;
若采取上述措施后,发电煤耗仍然偏高,则成立攻关小组来解决该问题。
图一:
石横电厂异常参数分析流程
2008年填写异常参数分析卡300余张,实现了各项经济技术指标的状态控制。
例如通过异常参数分析,对真空系统的仔细排查后,发现#3机高压扩容器与凝汽器结合面处漏气,经检修处理后#3机真空上升了0.8KPa,降低发电煤耗1.6g/kwh,年节约标煤2700余吨。
(二)应用新技术,促进节能技术进步
1、等离子点火装置
电厂在基建调试期间要消耗大量燃油,为降低基建费用,石横电厂三期2台300MW机组在基建期就采用等离子点火装置。
等离子点火装置安装在炉前最下层的A层燃烧器上,每一只火嘴对应一套等离子点火装置。
基建期间实现了锅炉无油点火,节省了大量燃油。
在投产后机组启动阶段和低负荷调峰运行时,也采用了等离子点火装置,实现了无油燃烧,大大节省了燃油费用。
2、高压电机变频技术的使用
由于高压变频器是一种技术含量高、难度较大的高新技术产品,前几年在国内还不成熟,机组的高压辅机原设计均为交流电动机,全部采用直接恒速拖动,能耗非常高。
随着高压变频技术的成熟,为了有效降低厂用电率,通过可行性研究分析,对部分设计裕量较大、长期在低负荷工况下运行的大功率辅机进行改造。
以一台1500KW电动机改变频调节为例:
阀门调节
调速调节
调速Vs调阀
流量(%)
功率(%)
转速(%)
(功率(%)
节电率(%)
75%
87%
42.20
44.8%
50%
70%
12.5%
57.5%
对于一台1500kW的电机来说,如经常需要运行在75%流量时,其年节电量(以一年运行300天计算)为:
W=1500(kW)*7200(h)*44.8%=4838400kW.h,即节电量483.84万度/年;
若0.3元/度,节电费145.15万元/年;
若经常运行在50%流量:
节电量为621万度/年,节电费为186.3万元/年。
以单台电机投资250万计算,两年左右即可收回投资。
3、双速电机技术的应用
高压电机除了改变频调速外,也可采用双速电机技术,在不同工况下采用不同的转速来达到节能效果。
石横电厂一、二期工程4台机组配备有4台循泵,冬季最少可开两台泵,夏季最高负荷要开四台泵。
经过收资调研,将其中的两台泵进行了双速电机改造,在不同季节,可根据负荷情况,灵活选择循泵最佳的运行方式,在确保凝汽器真空的前提下,最大限度的节约循泵的耗电量。
仅此一项每年可节电500万度左右,投资只需40万元,很短时间即可收回投资。
(三)加强设备治理改造,提高机组运行经济性
经过多年的实践,我们深深认识到设备管理是节能管理的基础,多年来,全厂上下一条心,加大设备改造投入力度,提高设备健康水平,提高机组运行经济性,降低各项损失。
通过改造我厂较好的对下列设备和系统进行了治理整顿。
1、对汽轮机通流部分进行改造
针对上汽厂300MW国产引进型机组高压缸效率低及汽封效果差的缺陷,石横电厂利用大修,对1-4号机的汽封片、隔板片全部进行了更换,通流部分间隙重新进行调整,有效地减少了汽轮机的损耗,同时对加热汽柜、门杆漏汽系统、汽封系统均进行了改造,既保证了机组的安全,又可降低机组的汽耗率。
2、降低主要耗电辅机的设计裕量,减少厂用电
如针对凝结水泵扬程设计裕量过大的特点,通过技术经济论证和试验比较,我们利用大小修对凝泵叶轮进行了改造,凝泵叶轮叶片去掉一级,在保证凝水流量在满足机组正常运行的前提下降低了凝泵扬程,仅此一项单台凝泵耗电降低100-120kWh,4台315MW机组年节约厂用电200多万kWh。
3、对真空系统进行治理,提高循环效率
坚持汽轮机的真空系统进行常态治理,主要是提高系统严密性及清洁铜管换热面,着重抓好了对真空系统管道阀门内外泄漏、8段抽汽口焊缝泄漏处理,有效的提高了机组的真空值,降低了发电煤耗。
4、生产区原照明设计很不合理,照明灯具为普通工业高压钠灯,存在数量多、亮度低、功率大、使用寿命短、维修量大等缺点。
为促进节能降耗,对现场照明进行了节能改造,将国产钠灯更换为高效节能、使用寿命较长的GE金属卤化物灯(其能耗比相当于节能灯)。
还将控制开关细分,实行分时分段控制。
由于新灯亮度高、安装位置合理,使现场照明灯减少1000盏左右,而且在每盏灯功率下降50W的情况下,仍能满足生产照明需要。
经测算,仅此一项每年可节电100万度以上。
5、对其他系统及设备的治理
(1)通过对制粉系统、锅炉本体的漏风问题治理后,制粉系统出力明显增加同时又有效地改善了锅炉的燃烧条件;
针对煤质的变化和中速磨的运行特点修改了风煤配比特性曲线,改善了锅炉煤粉的燃烧条件,有效的减少了低负荷炉膛灭火的次数。
提高了机组的可靠性与经济性。
(2)定期检查汽水系统阀门的内外泄漏,不合格的阀门及时予以更换或修复,从而有效地减少了汽水损失,使我厂的化学补充水率由2000年度的3.0%降低到2008年度的1.53%。
(3)将#1-4锅炉油枪系统进行改造,将原设计的大油枪改为小油枪,雾化蒸汽由辅汽改为压缩空气,通过改造将锅炉启动及低负荷助燃平均用油节省了60%以上,每年可节省数百万元。
通过对以上设备系统的治理,加上严格大小修管理及消缺管理、狠抓文明生产使得我厂设备健康水平明显提高,机组等效可用系数完成91%,有效的提高了机组运行的经济性。
(四)加强运行管理,优化运行方式,提高机组运行技术经济指标,追求发电效益最大化
1、强化市场意识,以盈亏平衡分析和燃料性价比为导向,立足减亏增盈。
加强市场调研和营销策划管理,按滚动控制要求,对全年电量市场和燃料市场进行季、月、旬、周等的分析预测,以追求最大利润为目标,做好电量进度的协调工作。
2、高度重视运行方式节能。
全面开展热力试验工作,对全厂主设备和主要辅助设备的能耗、效率、最佳工况点进行系统试验验证,为运行人员的操作提供了清晰依据。
在保证安全的前提下,使设备系统在最佳的节能方式下运行,越高越好的参数努力提上去,越低越好的参数努力降下来,可以停下的辅助设备坚决停下来,能并在一起的系统坚决合并起来。
近年来,实施了工业水、生活水、空预器冲洗水系统联络改造,一、二期开式水系统联络改造,#3、4机凝输水系统联络改造,部分公用设备进行了优化停运,每年可节电600万kwh。
按照边际贡献优先的原则合理安排六台机组电量计划,机组在不投AGC的情况下,尽量安排发电煤耗低的机组带高负荷,发电煤耗高的机组尽量带低负荷,辅汽尽量安排在发电煤耗低的机组上。
节日期间在机组需要调停时,通过协调采用深度调峰代替机组停运调峰的方式,大大减少了操作量,提高了全厂综合经济水平,统计数字表明,08年通过做工作共减少调停30余次。
当需要机组深度调峰时,有等离子点火装置的机组,减少助燃用油量。
3、优化机组启停方式,狠抓过程节能。
一是优化过程控制、缩短机组启停时间。
2008年我厂机组启停总计46次,每次机组启停运行部都制定了详细周密的控制方案,兼顾安全性和经济性,重点控制启动阶段辅机的启动和停机后辅机的停运,做好启停期间各节点的衔接,规范启动过程中的各项操作,并对影响机组启动的事件认真记录,按照经济责任制从严考核,增强了机组启动过程的可控性,缩短机组启动时间,减少了启停过程中的汽水损失、厂用电和燃油量。
制订了机组停运后的操作注意事项,对机组停运后辅助设备的停运做了明确规定,使机组停运后辅助设备管理时间化、数量化,能够及时停运风机、给水、凝水、循环水及各辅助设备,节约了大量厂用电。
二是不断探索开机过程中的辅机利用方式,深入开展过程节能。
比如,机组启动采用单侧引、送风机启动,每小时节省厂用电0.1万度,热态启动可少用4个小时,冷态启动可少用10小时;
锅炉冷态启动采用凝输泵和汽前泵,减少凝泵运行时间10余小时,电动给水泵的运行时间4小时,节约厂用电3万度;
在汽包上水时投运除氧器加热,提高了锅炉给水温度,减少了锅炉烧参数的时间,节约了大量燃油;
制订了《机组启动带旁路提前投粉运行措施》,当热二次风温达100℃左右时启制粉系统,将油枪油压减至0.4MPa,使启动过程中的燃油量大量减少。
4、加强对现场设备跑、冒、漏、滴的管理,对主要阀门加装温度测点并制订了《阀门内漏管理办法》,要求运行人员每日白班进行阀门测温的定期工作,每周四对每台机组全部的疏水、放水、承压排气阀门进行查漏工作,一旦发现温度异常,纳入缺陷管理,能立即处理的由检修人员当天处理,不能处理的利用调停机会对阀门进行修复或更换。
5、对关键指标进行精细化管理,确保全厂指标的先进性
(1)对主要辅机用电采取单耗管理办法。
以制粉单耗为例,石横电厂磨煤机为中速碗式磨,制粉系统的单耗主要包括给煤机和磨煤机电耗,现给煤机已改为变频电机,而降低磨煤机电耗的主要方法是调整制粉系统的运行方式,根据负荷及时启停磨煤机。
根据磨煤机的运行规律及检修经验,对磨煤机大修及定检后的最大出力作了详细规定:
磨煤机大修后至累计运行3000小时内,最大出力不小于45T/H;
累计运行3000~6000小时内,最大出力不小于42T/H;
累计运行6000~8000小时内,最大出力不小于40T/H。
当机组总煤量小于120T/H时,必须运行三台制粉系统,当煤量大于127T/H,且主汽压力较低时,可以启四台制粉系统。
如每台磨运行时的最小电流为30A,当磨煤量带至45T/H时,磨电流为43A左右,带30T/H时磨电流为35A左右,当机组煤量在130T/H时,若运行三台磨总电流120A左右,若运行四台磨总电流140A左右,因此在煤量相同的情况下,运行四台磨比运行三台总电流增加20A左右。
另外,在《磨煤机单耗管理办法》中规定,每台磨煤机单耗标准均为7.5kWh/吨煤,当磨煤机单耗≤6.8kWh/吨煤,奖维护单位100元,奖运行部100元。
当磨煤机单耗≥8.3kWh/吨煤,扣维护单位100元,扣运行部100元。
通过此办法的实施和对磨煤机运行方式及风量的调整,保证磨煤机单耗降至最低。
除《磨煤机单耗管理办法》外,我们还制订完善了《脱硫单耗管理办法》、《空压机单耗管理办法》、《制氢单耗管理办法》、《输煤单耗管理办法》、《取水单耗管理办法》、《除灰单耗管理办法》等。
(2)公用系统的管理(以水耗为例)
a、以全厂水平衡分析为手段,加强用水管理
从下图可以看出,我厂水源井供水分三路,水塔补水、化学用水、综合泵房补水,在理论上水源井供水量等于三路补水量总和,但由于表计存在测量误差,我们认为在5-10%内是合理的。
首先通过计算得出水源地供水与三路补水总和不平衡,肯定管道有泄漏的地方,然后组织人员进行地下管网排查,找出漏点后,进行消除,工业水用量每日从12000吨左右降至10000吨以下。
图二:
全厂水平衡图
b、改进操作方法,减少循环水排污损失
每台机循环水日补水量在2万吨左右,为减少水塔排污损失,在循环水Cl-含量增高时,采用呼吸排污法,即全开循环水塔排污门,关闭水塔补水门,大流量快速排水,待水位降至1.3米时,关闭循环水排污门,打开补水门,快速将水塔水位补至1.9米,重复该项操作,直至循环水合格为止。
采用此方法,大大减少了循环水塔补水量,每台机循环水平均日补水量降为1万吨左右。
通过采取以上措施,全厂平均日用水量由原来的40000多吨减少为20000吨左右。
6、以信息化管理为平台,大力开展运行人员劳动竞赛
石横电厂自主研发在线实时管理系统。
该系统以机组DCS系统实时数据为基础,通过建立数据库获取及存储现场数据,实现在线监测机组运行、经济指标监视、耗差分析、超限管理、机组运行方式的优化等目标。
本系统利用信息化手段,在线监测机组的运行状态,诊断机组耗能特点,绘制了主要参数对煤耗影响曲线,指导运行操作,挖掘机组节能的最大潜力,是提高机组运行经济性的重要措施。
图三:
生产实时系统示例图
制订了《运行指标竞赛管理办法》,利用实时数据系统将供电煤耗、厂用电率、真空、排烟温度等17个主要经济指标进行每班统计、实时竞赛、月度兑现。
表二:
某日值间竞赛情况统计表
参数名称
甲
乙
丙
丁
142.91
137.06
140.75
发电机功率
MW
246.45
265.66
262.9
%
5.54
4.94
5.97
再热汽温
537.86
541.13
539.47
主汽压力
MPa
16.72
16.74
16.81
凝汽器端差
1.43
-3.29
-0.99
补水量
t/h
6.8
11.1
7.34
主汽温度
541.16
541.94
540.5
1#高加下端差
12.45
13.19
12.05
2#高加下端差
11.16
11.94
11.73
3#高加下端差
8.77
9.21
9.1
5#低加下端差
15.18
15.61
15.65
6#低加下端差
18.33
18.11
18.04
凝汽器真空
-kPa
-95.03
-97.35
-96.27
0.00
通过激励机制的转变,运行人员在线优化参数的潜能得到了激发,调整参数的积极性得到了极大的提高,由“要我节能”转变为“我要节能”。
四、节能降耗管理的取得的效果
(一)各项指标优化,经济效益明显
1、各项指标优化对比
通过对2008年全年的机组经济指标完成情况进行统计并于2007年数据进行比较发现,主要经济指标均有不同程度的优化和提高。
如下所示:
表三:
主要经济指标完成情况对比
项目
2007年情况统计
2008年情况统计
5.38(无脱硫)
6.1(含脱硫)
排烟温度(年平均)
142
137
94.6
95.2
补水率
1.76
1.36
磨煤机单耗
kWh/吨煤
7.96
7.42
飞灰含炭量
4.03
3.56
8
燃油(年)
吨
2853
2291
2、经济效益分析
(1)火力发电厂各项指标优化最综合的反应就是供电煤耗的降低。
由于支持国家节能减排政策,2008年初二期脱硫系统投入运行,2008年10月份一期脱硫系统投入运行,影响厂用电率上升0.7%,增加供电煤耗2.4g/kwh,但石横发电厂通过对节能降耗的不断投入和细化管理,2008年一、二期供电标准煤耗完成340.78g/kwh,较2007年的342.1g/kwh仍然降低1.32g/kwh,考虑脱硫设备影响,供电标准煤耗下降1.32+2.4=3.72g/kwh,2008年全年完成发电量86.67亿kwh,全年节约标煤32000余吨,根据当年计算标煤价格,年创造效益3000余万元。
(2)全年节约燃油526T,以2008年轻质柴油均价每吨约6000元记,节约资金315万余元。
(二)为企业可持续发展奠定良好基础
通过对节能降耗管理模式的创新与实践,员工的市场意识增强,团队精神和执行力增强,员工素质不断提升,电厂的经济效益、社会效益进一步明显,竞争力不断增强,为企业可持续发展奠定良好基础。
主要创作人张爱军
参与创作人:
杜庆敏戚兴坤冯刚尹健