模具设计毕业设计Word格式文档下载.docx
《模具设计毕业设计Word格式文档下载.docx》由会员分享,可在线阅读,更多相关《模具设计毕业设计Word格式文档下载.docx(27页珍藏版)》请在冰豆网上搜索。
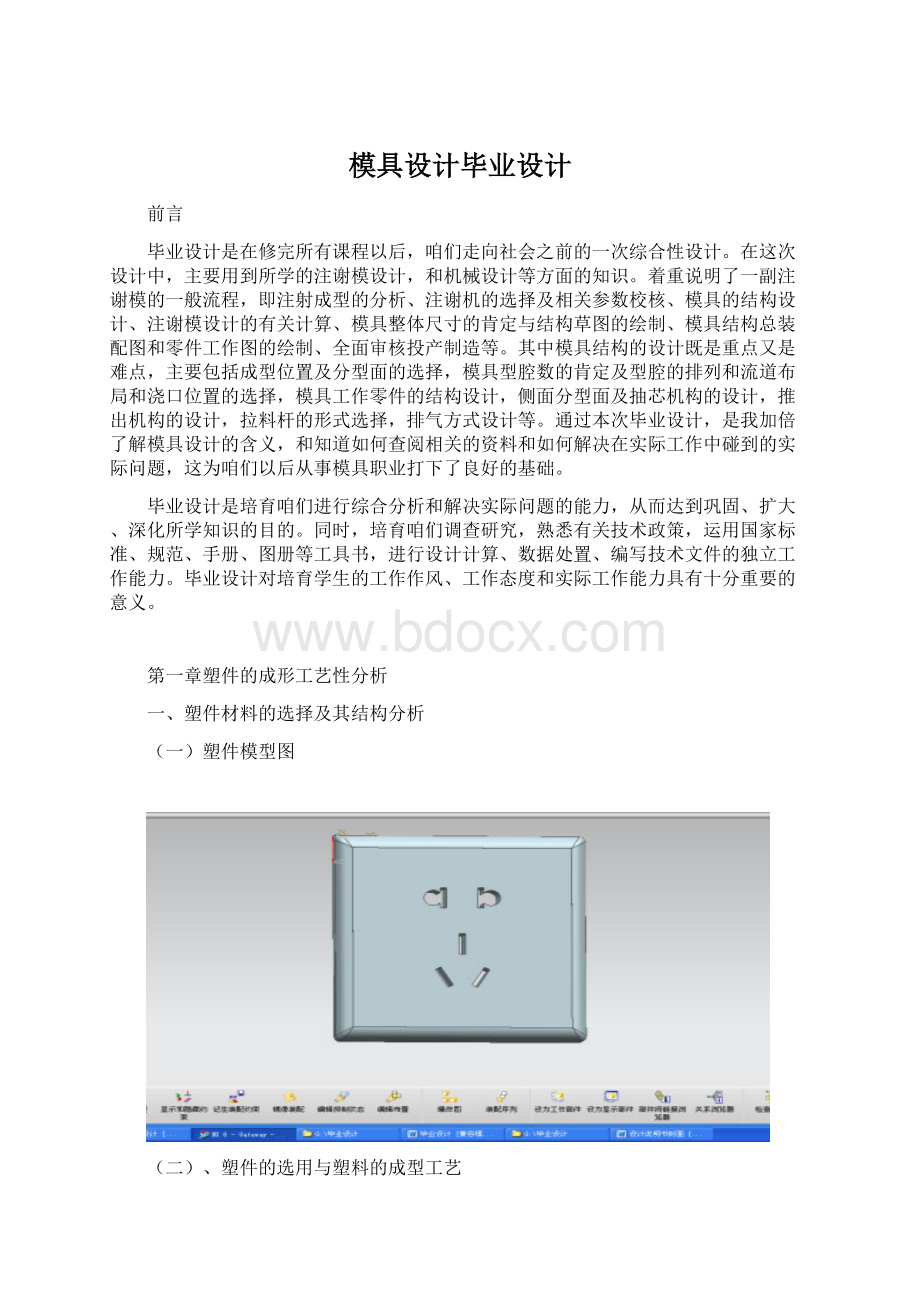
尽可能地利用高注射压力。
注射速度:
对于较小的浇口利用低速注射,对其它类型的浇口利用高速注射。
典型用途电气和商业设备(运算机元件、连接器等),器具(食物加工机、电冰箱抽屉等),交通运输行业(车辆的前后灯、仪表板等)。
(四)、成型特性
1.无定形料,流动性中等,吸湿大,必需充分干燥,表面要求光泽的塑件须长时刻预热干燥80~90度,3小时。
2.宜取高料温,高模温,但料温太高易分解(分解温度为270度)。
对精度较高的塑件,模温宜取50~60度,对高光泽、耐热塑件,模温宜取60~80度(模具温度将影响塑件光洁度,温度较低则致使光洁度较低)。
3.如需解决夹水纹,需提高材料的流动性,采取高料温、高模温,或改变入水位等方式。
4.如成形耐热级或阻燃级材料,生产3-7天后模具表面会惨存塑料分解物,致使模具表面发亮,需对模具及时进行清理,同时模具表面需增加排气位置。
成型塑件的主要缺点及消除办法:
主要缺点:
缺料、气孔、飞边、出现熔接痕、塑件耐热性不高(持续工作温度为70
左右,热变形温度约为93
)、耐气候性差(在紫外线作用下易变硬变脆)。
消除办法:
加大主流道、分流道、浇口、加大喷嘴、增大注谢压力、提高模具预热温度。
(五)、塑件的结构与工艺性分析
1.机构分析
塑件为插座外壳的上半部份,应有必然的结构强度,由于中间有插座的两孔板和三孔板的安装凹槽,下面有与下盖联接的唇,所以应保证它有必然的装配精度;
该塑件为插座的外壳,因此对表面粗糙度要求不高,表面粗糙度可取Ra=,而塑件内部没有较高的粗糙度要求。
该零件的重要尺寸,如:
的尺寸精度为3级,次重要尺寸
、
的尺寸精度为4级,其它尺寸均无公差要求,一般可采用8级精度。
由以上的分析可见,该零件的尺寸精度属中等偏上,对应模具相关零件尺寸的加工可保证。
从塑件的壁厚上来看,壁厚最大处为,最小处为1mm,壁厚差为较为均匀。
2.工艺性分析
塑件为一般的电器绝缘小薄壁塑件,工作条件要求这种塑件要具有良好的绝缘性能,具有必然的耐磨性,且塑件表面无云纹、冷疤现象。
为了避免在零件表面出现进料痕,保证进料均匀,模具采用点浇口进料,为了保证零件外观的美观,零件的外形位于上模,分型面位于插座底面处,1模2腔,对称排列。
脱模斜度:
塑件外表面为
,塑件内表面为
(脱模斜度不包括在塑件的公差范围内,塑件外形以型腔大端为准,塑件内形以型芯小端为准。
)
表常用塑料的脱模斜度
塑料名称或代号
脱模斜度
聚乙烯聚丙烯软聚氯乙烯
ABS尼龙聚甲醛
PC有机玻璃硬聚氯乙烯
热固性塑料
第二章注塑机的选用及参数的校核
一.注塑机的选用
(一)塑件的体积的计算:
对于形状复杂不规则的制品,能够利用UG,的“分析/模塑分析/模塑质量属性”来计算。
或采用估算塑料的用量,及保证足够的塑料用量为原则。
塑件的体积为:
V1=14264mm3
计算塑件的质量,查手册取塑料的密度为:
p=*
0-3kg/mm3
塑件的质量;
M1=V1*P=
计算塑件的重量是为了选用注塑机及肯定模具型腔数,按照注塑所需的压力和塑件的重量和其它的情形,可初步选用的注塑机为:
SZ-160/1000(卧式)型注塑机的主要技术规格如下表:
理论注射容积(cm3)
179
螺杆直径(mm)
44
注射压力(Mpa)
132
注射速率(g/s)
110
塑化能力(g/s)
螺杆转速(mm)
10-150
锁模力(KN)
1000
拉杆有较距离(mm)
360*260
移模行程(mm)
280
模具最大厚度
360
模具最小厚度(mm)
170
锁模形式
液压
模具定位孔直径(mm)
Ø
120
喷嘴球半径(mm)
SR10
表部分国产SZ系列塑料注塑机主要技术参数
SZ-60/40
SZ-100/80
SZ-160/1000
SZ-200/120
SZ-300/160
SZ-500/200
结构类型
卧
理论注射容积
60
100
200
300
500
螺杆(柱塞)直径
30
35
4042
45
55
注射压力
180
165150
150
注射速率
95
145
173
塑化能力
40
5570
82
螺杆转速
0~200
10~150
0~220
0~180
锁模力
400
800
1200
1600
2000
拉杆内间距
220~300
320~320
360~260
355~385
450~450
570~570
移模行程
250
305
350
380
最大模具厚度
450
最小模具厚度
230
模具定位孔直径
80
125
160
喷嘴球半径
10
15
20
二.注塑机参数量的校核
(一)注射量的校核
注塑机一个注射周期内所需注射量的塑料熔体的总量必需在注塑机额定注射量的80%之内。
在一个注射成型周期内,需注射入模具内的塑料的容量或质量,应为制件和浇注系统两部份容量或质量之和,即
V=NVz+VJ或M=nmz+mj
公式V(m)——一个成型周期内所需射入的塑料容积或质量(cm3或g);
n——型腔数量初定为2
V2(m2)——单个塑件的容量或质量(cm3或g)
Vj(mj)——浇注系统凝料和飞边所需塑料的容量或质量(cm3或g)
每件制品所需浇注系统的体积为制品体积的倍,现取
故应使
NVz+Vj<
=
或nmz+mj<
Vz(Vj)——注塑机额定注射量(cm3或g)
按照容积计算
NVz+Vj=(*2+**2=<
=100*
可见注塑机的注射量符合要求
(二)锁模力的校核
当高压塑料熔体充满型腔时,会产生专门大的压力,使模具沿分型面涨开,那个涨力,等于塑料制品和浇注系统在分型面上的投影之和乘以型腔内的熔体压力,应小于注塑机的锁模力
公式:
F>
=Pm(nAs+Aj)
式中F——注塑机的额定锁模力为1000(KN)
As—塑件在分型面上的投影面积(mm3)
Aj——浇注系统凝料在分型面上的垂直投影面积(mm3)
n—型腔数量
Pm—塑料熔体在型腔内的评价压力,MPa,一般取20~40MPa
则:
=Pm(nAs+Aj)=30*(2*6400+=<
=1000KN
所以符合要求
(三)最大注射力校核
注塑机的额定注射压力即为它的最高压力Pmax,应该承诺注塑机成型时所挪用的注射压力,即
Pmax>
=KP0
式中Pmax——注塑机的额定注射压力为132(MPa)
P-——成型时所需的注射压力范围取70~150(MPa)取100
K——安全系数,常取K=——
则KP=*100=130MP-<
Pmax=132MPa
符合要求
(四)开模行程校核
开模行程S(合模行程)指模具开合进程中动模固定板的移动距离。
注塑机的最大开模行程与召募厚度无关,对于单个分型面注射模:
Smax>
=S=H1+H2+5—10mm
式中H1——催出距离(脱模距离)(mm)
H2——包括浇注系统的凝料在内的塑件高度(mm)
开模距离取H1=20
包括浇注系统凝料在内的塑件高度取H2=130
余量取8
则有:
Smax=280>
=S=20+130+8=158
符合要求。
(五)模具与注塑机安装部份的校核
喷嘴尺寸注塑机头为球形,其球面半径与相应接触的模具主流道始端凹下的球面半径相适应。
第三章分型面的选择
一、肯定型腔数量及排列方式
本塑料制作为MP3的外壳,生产批量教大,为了提高生产效率,但又要保证产品的一致性,故不宜采用一模多腔的形式:
每增加一个型腔,由于型腔的制造误差和成型工艺误差的影响,塑件的尺寸精度要降低约4%~8%,因此多型腔模具(n>
4)一般不能生产高精度的塑件。
因此,本模具能够采用一模两腔的形式,其布局从分型面处能够看到
二、分型面的肯定
(一)分型面肯定因素
在塑料注射模制造进程中,总会碰到分型面肯定的问题,它是一个很复杂的问题,受到许多因素的制约,常常顾此失彼。
所以在选择分型面是应该抓住主要矛盾,舍弃次要因素。
不同设计的人有时候对主要因素的熟悉也不尽一致,与自身的工作经验有关。
有些塑件的分型面选择简单明确而且唯一;
有些塑件则有许多方案能够选择。
按照经验,能够按以下原则来肯定:
a)保证塑料制品能够脱模
这是一个首要原则,因为咱们设置分型面的目的,就是为了能够顺利从型腔中脱出制品。
按照那个原则,分型面应首选在塑料制品最大的轮廓线上,最好在一个平面上,而且此平面与开模方向垂直。
分型的整个分型的整个廓形应呈缩小趋势,不该有影响脱模的凹凸形状,以避免影响脱模。
b)使型腔深度最浅
模具型腔深度的大小对模具结构与制造有如下三方面的影响:
1)目前模具型腔的加工多采用电火花成型加工,型腔越深加工时刻越长,形象模具生产周期,同时增加生产本钱。
2)模具型腔深度影响着模具的厚度。
型腔越深,动、定模越厚。
一方面加工比较困难;
另一方面各类注射机对模具的最大厚度有必然的限制,故型腔深度不宜过大。
3)型腔深度越深,在相同起模斜度时,同一尺寸上下两头实际尺寸差值越大,如图2。
若要控制规定的尺寸公差,就要减小脱模斜度,而致使塑件脱模困难。
因此在选择分型面时应尽可能使型腔深度最浅。
c)使塑件外形美观,容易清理
虽然塑料模具配合超级精密,但塑件脱模后,在分型面的位置都会留有一圈毛边,咱们称之为飞边。
即便这些毛边脱模后当即割除,但仍会在塑件上留下痕迹,影响塑件外观,故分型面应该避免设在塑件滑腻表面上。
d)尽可能避免侧抽芯
塑料注射模具,应尽可能避免采用侧向抽芯,因为侧向抽芯模具结构复杂,而且直接影响塑件尺寸、配合的精度,且耗时耗财,制造本钱显著增加,故在万不得已的情形下才能利用。
e)使分型面容易加工
分型面精度是整个模具精度的重要部份,力求平面度和动、定模配合面的平行度在公差范围内。
因此,分型面应是平面且于脱模方向垂直,从而使加工精度取得保证。
如选择分型面是斜面或曲面,加工的难度增大,而且精度得不到保证,易造成溢料飞边现象。
f)使侧向抽芯尽可能短
抽芯越短,斜抽移动的距离越短,一方面能减少动、定模的厚度,减少塑件尺寸误差;
另一方面有利于脱模。
g)件制品精度
作为机械零件的塑件,平行度、同心度、同轴度都要求很高,保证塑件精度除提高模具制造精度外,于分型面的选择有专门大关系。
h)利于排气
对中、小型塑件因型腔教小,空气量不多,可借助分型面的裂缝排气。
因此,选择分型面时应有利于排气。
按此原则,分型面应设在注射时熔融塑料最后抵达的位置,而且不打型腔封锁。
i)使塑件留在动模内
模具开模时型腔内的塑件一般不会自行脱出,需要用顶出机构顶出,注射机上都有顶出装置,且设在动模一侧,因此设计模具分型面时应使开模后塑件能留在动模内,以便直接利用注射机的顶出机构顶出塑件。
若是塑件留在定模内,则要再另设计顶出装置才能脱模,模具结构复杂得多,且本钱爬升,加工周期延长。
j)腔内总压力较大的方向与分型面垂直
塑件注射时型腔内各方向的压强P相同,故某方向总压力F=P*S,S为某方向的投影面积,当S越大,则F越大,选择总压力较大的方向与分型面垂直,利用注射机的锁模力来经受较大注射压力。
因此模具结构简单,不然需另设计锁紧机构,模具结构复杂,本钱增加,加工周期延长。
综上所述,选择注射模分型面形象的因素很多,总的要求是顺利脱模,保证塑件技术要求,模具结构简单制造容易。
被选定一个分型面方案后,可能会存在某些缺点,再再针对存在的问题采取其他办法弥补,以选择接近理想的分型面。
(二)、成型方案
结合以上的因素为了便于模具加工制造,应尽是选择平直分型面工易于加工的分型面。
如下图所示,采用如此一个平直的分型面,前模(即定模)做成平行的就好了,胶位全数做在后模(即动模),大简化了前模加工。
分型面也是整个模具的主分模面。
分型面如下图的绿色部份:
模具结构设计
一、成型零件的工作尺寸计算
影响塑件尺寸精度的因素较为复杂,主要存在以下几方面
(1)、零件的制造公差;
(2)、设计时所估量的收缩率和实际收缩率之间的不同和生产制品时收缩率波动;
(3)、模具利用进程中的磨损。
以上三方面的影响表述如下:
1、制造误差:
ΔZ=aXi=a+
其中,D—被加工零件的尺寸,可被视为被加工模具零件的成型尺寸;
ΔZ—成型零件的制造公差值;
i—公差单位;
a—精度系数,对模具制造最常常利用的精度品级。
2、成型收缩率波动的影响
其中,—塑件成型收缩率;
LM—模具成型尺寸;
LS—塑件对应尺寸。
3、型腔磨损对尺寸的影响
为简便计算,凡与脱模方向垂直的面不考虑磨损量,与脱模方向平行的面才考虑磨损。
考虑磨损主要从模具的利用寿命来选定,磨损值随产量的增加而增大;
另外,还应考虑塑料对钢材的磨损情形;
同时还应考虑模具材料的耐模性及热处置情形,型腔表面是不是镀铬、氮化等。
有资料介绍,中小型模具的最大磨损量可取塑件总误差的1/6(常取~),而对于大的模具则应取1/6以下。
但实际上对于聚烯烃(如像PP)、尼龙等塑料来讲对模具的磨损是很少的,对小型塑件来讲,成型零件磨损量对塑件的总误差有必然的影响,而对大的塑件来讲影响很少。
在以上理论基础上,下面按平均收缩率来计算成型尺寸:
1.平均收缩率
从常见的塑料的收缩率中查到,ABS的收缩率为%~%。
则,
Scp=(Smax+Smin)/2
Scp=%+%)/2=%
式中:
Scp—平均收缩率;
Smax—最大收缩率;
Smin—最小收缩率。
2.型腔尺寸
由pro/e测量得Ls为80mm,塑件精度为MT2,对应的型腔加工精度为IT8,查塑件尺寸公差表,依照A类不受模具活动部份影响的尺寸公差表得Δ=,模具成型零件制造公差
δz=Δ/3=,系数X=3/4。
LM0+=[(1+Scp)Ls-XΔ]0+δz
LM0+=[(1+%)x80-3/]0+=0+0.14mm
LM—凹模径向公称尺寸(mm);
Ls—制品径向公称尺寸(mm);
δz—模具成型零件制造公差(mm);
Scp—塑件平均收缩率(%);
Δ—制品公差值(mm)。
3.型腔深度尺寸
由pro/e测量得制品高度为10mm,按B类受模具活动部份影响的尺寸公差值查表得
Δ=,δz=,系数X=2/3。
HM0+δz=[(1+Scp)Hs-XΔ]0+δz
HM0+11=[(1+%)x10-2/]0+=+
HM—凹模径向公称尺寸(mm);
Hs—制品高度公称尺寸(mm)。
型腔图如下:
4.型芯尺寸
由UG测量得As为80mm,塑件精度选为MT2,对应的型腔加工精度为IT8,查塑件尺寸公差表,依照A类不受模具活动部份影响的尺寸公差值查表得Δ=,模具成型零件制造公差δz=Δ/3=,系数X=。
A0M-δz=[(1+Scp)As+XΔ]0-δz
0M=[(1+%)x80+=式中:
AM—型芯的径向尺寸(mm);
As—塑件孔的径向尺寸(mm)。
5.型芯高度尺寸
由UG测量得型芯高度为10mm,按B类受模具活动部份影响的尺寸公差值查表得Δ=,δz=,系数X=2/3。
B0M-δz=[(1+Scp)Bs+XΔ]0-δz
0M=[(1+%)x10+2/]=式中:
BM—型芯高度尺寸(mm);
Bs—塑件孔的深度尺寸(mm)。
型芯如下图:
6.中心距的计算
由UG测量得塑件两孔中心间距离Cs=130mm,按A类不受模具活动部份影响的尺寸公差值查表得Δ=,δz=.
CM±
δz/2=(1+Scp)Cs±
δz/2
=(1+%)X130±
2=±
CM—中心距(mm);
Cs—制品中心距(mm)。
7.型腔侧壁和底板厚度的计算
①型腔侧壁和底板厚度的计算,按刚度计算:
S>
=
S—矩形型腔侧壁厚度(mm);
P—成型压力(Mpa);
取25~45MPa,取40
Hl—经受熔体压力的侧壁高度(mm);
l—型腔侧壁长边长(mm);
E—型腔钢材的弹性模量(一般取:
Mpa)
H—型腔侧壁总高度(mm);
[δ]—允许变形量(mm)(ABS≤0.05mm)
C—由H1/l决定的系数,查塑料模具设计的P107,表6-7()
C1-由型腔边长比l/b决定的系数,查表6—9()
②底板厚度的计算,按刚度计算:
H>
=0.54L0
H>
=(mm)
二、推出机构的设计
推出机构的选用
设计推出机构应遵循下列原则:
(1)由于推出机构的动作是通过装在注塑机和模机构上的顶杆来驱动的,所以一般情形下,推出机构应尽可能设置在动模一侧。
正因如此,分型面的设计也应尽可能使塑件开模后能留在动模一侧。
(2)为了保证塑件在推出进程中不变形、不损坏,必需仔细分析对模具的包紧里和粘附力的大小,选择合理的推出方式及推出位置,从而使塑件受力均匀。
(3)推出机构应使推出动作靠得住、灵活,结构简单、制造方便,机构本身要有足够的强度、风度,以经受推出进程中各类作使劲,确保塑件顺利地脱模。
(4)推出塑件的位置应尽可能设在塑件内部,以避免推出痕迹影响塑件的外观质量。
(5)必需考虑合模时推出机构的正确复位,并保证不与其他模具零件干与。
常常利用的简单推出机构包括以下几种:
推杆推出机构:
由于设置推杆位置的自由度较大,因此推杆推出机构是最常常利用的推出机构。
推杆的截面形状按照塑件的推出情形而定,可设计成圆形、矩形等。
其中以圆形最为常常利用,因为利用圆形推杆的地方,较容易达到推杆和模板或型芯上推杆的配合精度;
另外圆形推杆结构简单、改换方便、滑动阻力小。
但因推杆与塑件接触面积小,可能损坏塑件或使这变形,故不宜用在脱模力大的筒形和箱形塑件的脱模。
推管推出机构:
推管推出机构是用来推出圆筒形、环形塑件或带有孔的塑件的一种特殊结构形式,其脱模运动方式和推杆相同。
由于推管是一种空心推杆,故整个周边接触塑件,推出塑件的力量均匀,塑件不易变形,也不会留下明显的推出痕迹。
推板推出机构:
推板推出机构的推出零件是一块与凸模按必然配合精度的模板。
推板在塑件的整个周边端面上进行推出,因此,作用面积大,推出力大而均匀,运动平稳,而且塑件上无推出痕迹。
但如果是凸个推板配合不好,则在塑件会出现毛刺,而且塑件有可能会滞留在推板上。
对于大型的深腔的塑件或软塑料制件,推板推出是,塑件与凸模间容易形成真空,造成脱模困难,为此考虑增设进气装置。
靠大气压力,使中间引气阀进气,塑件便能顺利地从凸模上脱出。
另外与可采用中间直接设置推盘的结构,在推出时专门快进气。
型腔推出机构:
凡是薄壁容器、壳形塑件和表面不允许有推出痕迹的塑料制品,可采用推件板推出,推件板推出机构义称顶板顶出机构,它由一块与型芯按必然配合精度相配合的模板和推杆组成。
特点:
推件板推出的特点是顶出力均匀,运动平稳,且推出力大。
可是对于截面为非圆形的塑件,其配合部份加工比较困难。
组合推出机构:
在实际生产中往往还存在着如此一些塑件,若是采用上述单一的推出机构,不必然能保证塑件能顺利脱模,乃至会造成塑件变形、损坏等不良后果。
因此,就要采用两种或两种以上的推出形式。
如推杆、推板组合的推出机构,推杆、推管组合的推出机构等等。
由于电话面板是一个低部平脸部份较小,而且该塑件较厚,面积不算大。
该模具为了节省本钱方便制造所以选择推杆推出机构。
三、型芯的结构设计
成型塑件内的表面零件称凸模或型芯,其主要有:
主型芯、小型芯、活动镶件、螺纹型芯和螺纹型环等。
对于结构简单的容器、壳罩、盖之类的塑件,成型其主体部份内表面的零件称为主型芯或凸模,而将成型其他小孔的型芯称为小型芯或成型杆。
主型芯的结构设计
按结构主型芯可分为整体式和整体式两种。
采用整体式型芯,可简化结构复杂的型芯加工工艺,减少热处置变形,廉价模具的维修,节省珍贵的模具钢。
选择合理的整体式结构。
第五章统的设计
一、浇注系统的形成和浇口的设计
浇注系统是指模具中从接触注射机喷嘴开始到型腔为止的塑料流动通道。
其作用是使熔体平稳地引入型腔,使之按要求填充型腔;
使型腔内的气体顺利地排出;
在熔体填充型腔和凝固的进程中,能充分的把压力传到型腔各部份,以取得组织致密、外型清楚、尺寸稳固的塑件。
普通浇注系统一般由主流道、分流道、浇口、和冷料穴等四部份组成。
浇注系统十分重要,它的设计正确与否是注塑成型可否顺利进行,可否取得高质量塑件的关键。
对浇注系