solidworksandmastercam自动化加工说明书知识分享文档格式.docx
《solidworksandmastercam自动化加工说明书知识分享文档格式.docx》由会员分享,可在线阅读,更多相关《solidworksandmastercam自动化加工说明书知识分享文档格式.docx(33页珍藏版)》请在冰豆网上搜索。
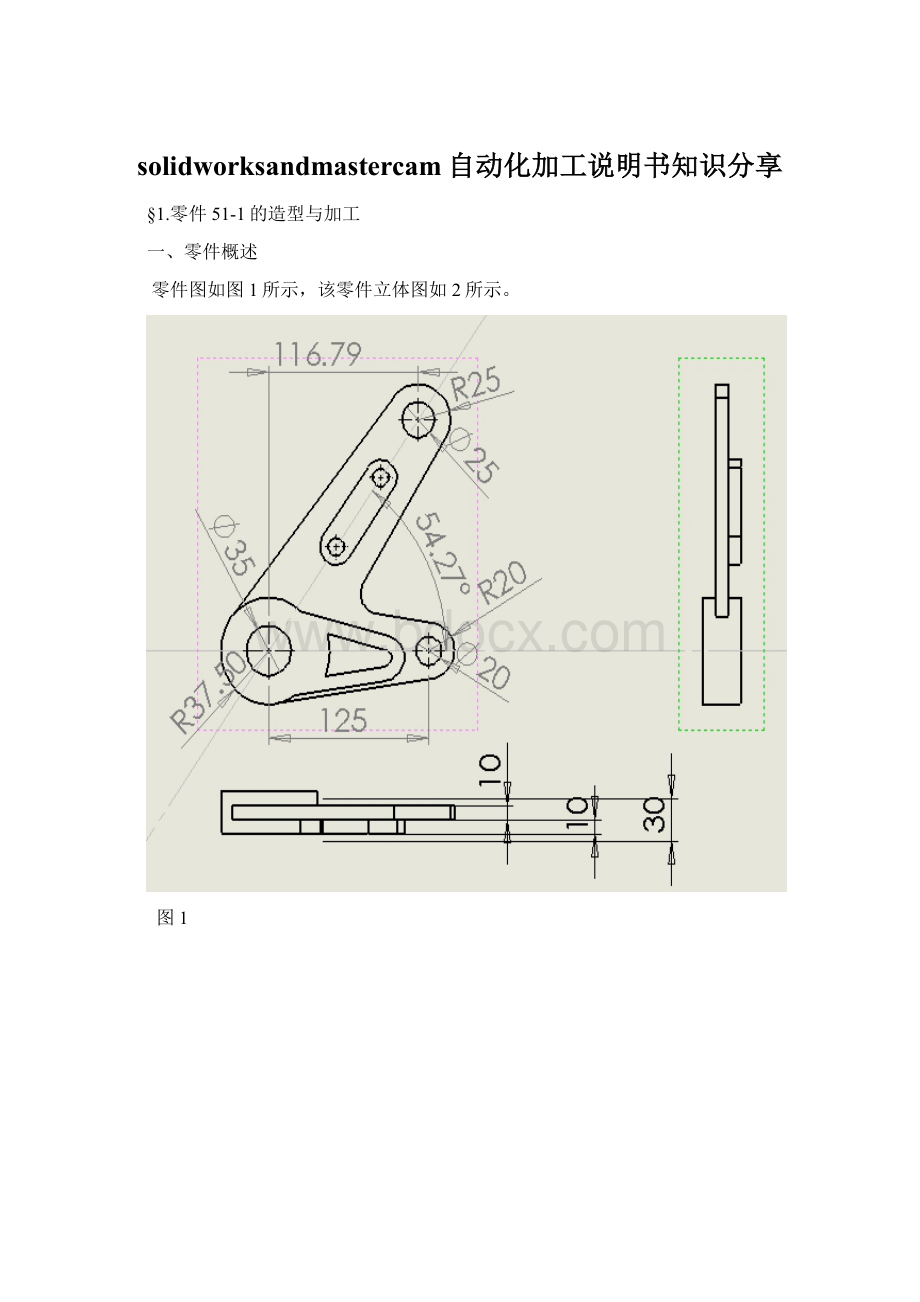
参数设置如图11,拉伸效果如图12。
图11图12
8.保存文件,文件名为51-1.SLDPRT。
另存文件,文件名为51-1.x_t
第4页
三、零件正面数控加工路径和NC程序
1.打开CAD模型的文件
(1)启动MastercamX软件。
(2)打开51-1.x_t文件,导入MastercamX中。
(3)进行坐标分析。
①选择A分析→P分析点坐标命令。
②选取若干个点,分析其坐标(如图1、2、3、4四点)
各点坐标如下:
1点,X=0.0Y=0.0Z=15.0
2点,X=90.0Y=-4.94874Z=15.0
3点,X=125.0Y=0.0Z=5.0
4点,X=116.79327Y=162.35558Z=5.0
图13
③综合ABCD四点坐标及其位置,把A点定为弓箭原点只需将整个图形向下移动15mm。
(4)图形平移。
①选择X转换→T平移命令
②选取移动;
ΔZ=-15.0→确定
③再作与步骤(3)相同的点坐标命令。
发现A点已是坐标原点。
2.初始设置
(1)选择机床设备。
M机床类型→M2D\MCAMX\CNC_MACHINES\MILL3-AXISVMC.MMD(立式3轴数控铣床)。
(2)设置毛坯尺寸。
材料设置→边界盒→延伸量X:
1.0Y:
1.0Z:
1.0,单击
。
3.面铣削
(1)创建一个190×
230的矩形。
(2)刀具路径→平面铣削→选取串连(190×
230矩形框)。
第5页
(3)在刀具管理器→刀库。
在刀库中选取229Endmill1…20.0…20.0.FLA…0.0000…None(Φ20平铣刀),双击→编辑刀具→定义刀具→刀具类型。
选取端面铣刀。
在刀具参数中把刀具名称改为1,刀具号改为1。
(4)单击平面铣削参数。
深度:
0其余采用默认参数。
(5)单击刀具参数。
设置参数如下:
进给速度:
500,下刀速度:
300,提刀速度:
1500,主轴转速800。
其余不变。
(6)单击
,系统产生面铣刀具路径。
(7)进行实体加工仿真。
(8)关闭面铣削刀具路径。
4.外形铣削
(1)创建一段圆弧:
C构图→A画圆弧→P极坐标
(2)刀具路径→外形铣削→选取串连
在刀库中选取221Endmill1…12.000…12.FLA…0.0000…None(Φ12平铣刀),双击→编辑刀具→定义刀具→刀具类型。
选取平铣刀。
在刀具参数中把刀具名称改为2,刀具号改为2。
(4)双击平铣刀图标,弹出定义刀具,单击参数。
XY粗铣步进(%):
75, Z向粗铣步进:
2.0, XY精修步进:
1,
Z向精修步进:
0.5,进给率:
300,下刀速率:
100,提刀速率:
1000,主轴转速800。
材料表面速率%:
100,每刃切削量%:
100。
其余采用默认参数。
设置完后按确定按钮√。
(5)外形→外形铣削参数。
-30,补正方向:
左,分别选中U平面多次铣削P分层铣削B贯穿。
其余采用默认参数。
1U平面多次铣削设置
粗切次数:
1,间距:
5,
精修间距:
0.5
选中所有深度和不提刀。
设置完后按确定按钮
2P分层铣削设置
最大粗切步进量:
2.0,精修次数:
0,精修步进量:
1.0
分层切削的顺序:
按轮廓。
设置完后按确定按钮
3B贯穿参数
贯穿距离:
1.0。
(6)单击确定按钮
系统产生外形铣削刀具路径。
(7)进行实体加工仿真。
(8)关闭面铣削刀具路径。
第6页
5.挖第一个槽
(1)创建一个辅助外轮廓线(与实际轮廓线相比,每条线向外扩展12mm.。
)如下图14所示。
C构图→A画圆弧→P极坐标;
L画直线→A平行线
图14图15
(2)刀具路径→挖槽→选取串连
选取串连和子串连如图15所示:
(3)在刀具管理器→刀库。
在刀库中选取219Endmill1…10.000…10.FLA…0.0000…None(Φ10平铣刀),双击→编辑刀具→定义刀具→刀具类型。
在刀具参数中把刀具名称改为3,刀具号改为3。
(5)挖槽→2D挖槽参数。
-10,选中E分层铣深。
E分层铣深设置如下:
最大粗切深度:
5.0,精修次数:
1.0,精修步进量0.5,选择不提刀,按区域。
挖槽→精切精修的参数。
选择等距环切,选择刀具路径最佳化,由内而外环切,精修,精修外边界等复选框,其余采用系统默认参数。
系统产生挖槽的刀具路径。
6.挖第二个槽
(1)刀具路径→挖槽→选取串连
选取串连为槽的轮廓线。
:
(2)用第5步定义的第3号刀
(3)在定义刀具中,单击参数。
第7页
(4)挖槽→2D挖槽参数。
(5)单击确定按钮
(6)进行实体加工仿真。
(7)关闭面铣削刀具路径。
7.用铣削的方法加工直径为Φ35、Φ20、Φ25的三个孔
(1)刀具路径→挖槽→选取串连,选取串连分别为三个孔的外轮廓。
(2)用第4步定义的第2号刀
-30,选中E分层铣深。
8.用铣削的方法加工直径两个为Φ12.5孔
(1)刀具路径→挖槽→选取串连。
选取串连分别为两个孔的外轮廓。
第8页
9.后处理
单击刀具路径中的G1选择合适的后处理器,单击
另存为51-1.NC。
删除程序中的第0003—0009的注释行,如下图16所示。
图16
10.保存刀具路径
选择文件→另存为,将刀具路径保存为51-1-1.MCX
四、零件反面数控加工路径和NC程序
1.打开CAD模型的文件
单击
(3)图形旋转。
①将图形转为前视图,单击
②选择X转换→旋转。
选取移动、选择角度为180度。
选择A分析→P分析点坐标命令。
③选取若干个点,分析其坐标将图形改为俯视图。
第9页
(4)进行坐标分析。
②选取若干个点,分析其坐标。
分析得Z的原点在零件的表面上。
可进入刀具路径创建阶段。
2.初始设置
1.0,选取线和弧及中心点。
(1)刀具路径→平面铣削→选取串连。
(2)在刀具管理器→刀库。
(3)单击平面铣削参数。
(4)单击刀具参数。
(5)单击
4.挖槽
(1)创建一个辅助外轮廓线(与实际轮廓线相比,每条线向外扩展12mm.。
)与正面第5步书画的图相同.
选取串连和子串连如图17所示:
图17
第10页
(3)在刀具管理器→刀库。
5.后处理
删除程序中的第0003—0009的注释行,如下图17所示。
图18
6.保存刀具路径
第11页
2.零件51-2的造型与加工
零件图如图19所示,该零件立体图如20所示。
图19
图20
2.在上视基准面绘制绘制草图1。
如下图21:
第12页
图21
参数设置如图22,拉伸效果如图23。
图22图23
如下图24:
图24第13页
参数设置如图25,拉伸效果如图26。
图25图26
6.切除-拉伸1。
参数设置如图27,拉伸效果如图28。
图27图28
7.绘制绘制草图3。
如下图29
第14页
图29
8.拉伸3。
参数设置如图30,拉伸效果如图31。
图30图31
第15页
9.切除-拉伸2。
参数设置如图32,拉伸效果如图33。
图32图33
三、零件反面数控加工路径和NC程序
1.打开CAD模型的文件
(3)图形旋转
(5)图形平移。
(1)刀具路径→平面铣削→选取串连
第16页
(5)单击刀具参数。
(1)创建辅助矩形。
(2)刀具路径→挖槽→选取串连
在刀库中选取221Endmill1…12.000…12.FLA…0.0000…None(Φ10平铣刀),双击→编辑刀具→定义刀具→刀具类型。
5.曲面粗加工流线
(1)刀具路径→曲面粗加工→曲面流线。
(2)选取要加工面(如图34)。
图34
在刀库中选取123Endmill1…6.000…6.BU…2.0000…corner(Φ6,R2的牛鼻刀)。
第17页
(4)双击平铣刀图标,弹出定义刀具,单击参数。
1.0, XY精修步进:
500,下刀速率:
300,提刀速率:
800,主轴转速2000。
(5)设置曲面参数和曲面流线粗加工参数。
使用系统默认参数。
系统产生粗加工刀具路径。
6.曲面精加工流线
(1)刀具路径→曲面精加工→曲面流线。
(2)选取要加工面(如图35)。
图35
在刀库中选取237Endmill1…3.000…2.BAL…1.50000…full(Φ3,球头刀)。
在刀具参数中把刀具名称改为4,刀具号改为4。
50, Z向粗铣步进:
800,主轴转速3000。
50,每刃切削量%:
50。
系统产生精加工刀具路径。
(8)关闭曲面铣削刀具路径。
7.后处理
另存为51-2反面.NC。
删除程序中的第0003—0010的注释行。
8.保存刀具路径
第18页
4.外形铣削
(1)刀具路径→外形铣削→选取串连
(2)在刀具管理器→刀库。
(3)双击平铣刀图标,弹出定义刀具,单击参数。
(4)外形→外形铣削参数。
-40,补正方向:
①U平面多次铣削设置
第19页
4P分层铣削设置
5B贯穿参数
(8)关闭曲面铣削刀具路径。
5.挖第一个槽
-15,选中E分层铣深。
1.0,精修步进量