新型工程材料及测试分析技术资料Word格式.docx
《新型工程材料及测试分析技术资料Word格式.docx》由会员分享,可在线阅读,更多相关《新型工程材料及测试分析技术资料Word格式.docx(15页珍藏版)》请在冰豆网上搜索。
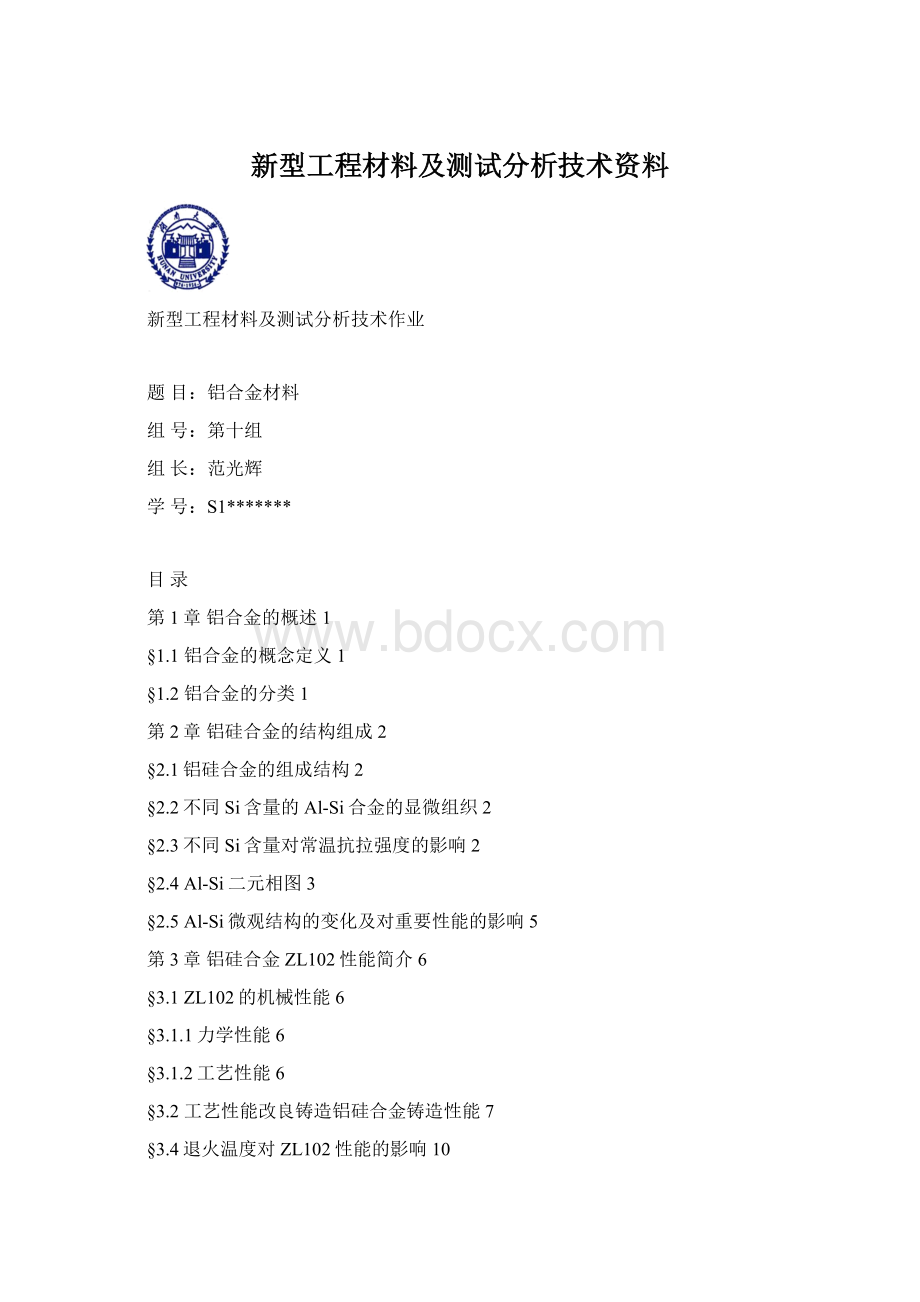
致谢14
本组成员14
第1章铝合金的概述
1.1铝合金的概念定义
铝合金就是以铝为基加入其他元素组成的合金。
纯铝的导电、导热和耐蚀性能良好,主要用作导电、导热材料,但强度低,不宜作结构材料。
铝可与许多化学元素形成合金以改善性能。
铝合金比重轻,比强度接近合金钢,比刚度超过钢,塑性好,铸造和可切削性也较好,适宜制造重量轻的结构部件,因此成为航空工业不可缺少的材料,在交通运输、建筑、轻工、化工、仪表机械等部门,在家用器具方面也得到广泛应用。
1.2铝合金的分类
铝硅系合金常称"
硅铝明"
或"
矽铝明"
(Silumin),与其他系铸造合金相比,该系合金成分位于共晶成分附近,有良好的铸造性能和耐磨性能,热胀系数小,是铸造铝合金中品种最多、用量最大的合金。
工业用铝硅合金的硅含量可高达25%。
分为过共晶铝硅合金(硅含量大于14%)、共晶铝硅合金(硅含量为10~14%)和亚共晶铝硅合金(硅含量小于10%)。
变质处理可提高铝硅合金的力学性能。
添加0.2~0.6%镁的铝硅合金(ZL101)广泛用于制作各种结构件如壳体、缸体、箱体和框架等。
添加适量的铜和镁能提高合金的力学性能和耐热性,此类合金(如ZL108)广泛用于制造活塞等部件。
铝铜系合金应用最早的铸造铝合金。
此类合金可以通过固溶-时效处理进行强化,含4.5~5.3%铜的合金强化效果最佳。
加入适量的锰和钛能显著提高室温、高温强度和铸造性能(ZL201),主要用于制作承受大的动、静载荷和形状不复杂的砂型铸件。
铝镁系合金密度最小的铸造铝合金。
含镁12%的合金强化效果最佳。
实用的合金中含镁量不超过11.5%。
典型的二元合金是ZL301。
该系合金在大气和海水中抗腐蚀性能好,在室温下具有良好的综合力学性能和可切削性能,常用作雷达底座,飞机的发动机匣、螺旋桨、起落架等零件。
由于加工后表面光亮呈银白色,可作装饰材料。
铝锌系合金铸造和耐蚀性能差,热裂倾向大,有应力腐蚀倾向。
为改善性能,常加入硅、镁元素,典型的合金为ZL401,常称为"
锌硅铝明"
。
在铸造条件下这种合金即可取得淬火的作用,有"
自行淬火"
之称。
这种合金不经热处理即可使用。
经变质处理后的铸件具有较高的强度。
经稳定化处理后,尺寸稳定,常用于制作模型、型板及设备支架等。
本论文重点论述铝硅系铝合金展开论述,最后再介绍铝硅合金ZL102。
第2章铝硅合金的结构组成
2.1铝硅合金的组成结构
铝硅合金铝硅合金(aluminiumsiliconalloy)一种以铝、硅为主成分的锻造和铸造合金,并加入铜、镁、锌、铁、镍等合金元素。
2.2不同Si含量的Al-Si合金的显微组织
图2-1为Si质量分数分别为5.0%、7.0%、9.0%、12.8%、15.0%、18.0%的合金显微组织。
从图2-1可以看出,随着Si含量的提高,共晶Si均为细小的、短杆状或颗粒状,对合金的力学性能影响不大。
当达到共晶区间时,开始出现初生Si相,且Si含量越高,初生Si相的尺寸越大。
由于初生Si相尺寸较大,又是硬脆相,导致合金的硬度提高,塑形、韧性急剧下降。
图2-1不同Si含量的Al-Si合金的显微组织
2.3不同Si含量对常温抗拉强度的影响
图2-2为不同Si含量对Al-Si合金常温抗拉强度的影响。
可以看出,随着Si含量的增加,常温抗拉强度先增加后减小,在共晶点附近达到最大值。
当Si含量在7.0%~12.8%范围内,Si含量的增加能增加低应变区的应变硬化速率,提高合金的抗拉强度;
通过变质、T6热处理,合金中会生成Mg2Si、Al2CuMg、W相(AlxMg5Si4Cu4)、Q相(Al5Mg8Cu2Si5)等弥散强化相。
这些相多为硬脆的金属间化合物,在合金中同样起阻碍位错运动的作用,因而能产生过剩强化相。
随着Si含量的增加,Al-Si合金中的过剩相数量增多,合金强度提高。
另一方面,在合金中,不可避免的会有少量的Fe进入熔液,会生成Al3Fe,Ni的加入会使Al3Fe熔解,同时生成细小的Al9FeNi相,从而提高合金的强度。
图2-2Si含量对常温抗拉强度的影响
当Si含量超过共晶点时,会产生粗大、硬脆的初生Si,即使变质,也只能改变其形貌和尺寸,而不能使其数量减少。
随着Si含量的增加,结晶温度范围变大,合金的疏松倾向加大,气密性降低,同时氢在合金中的溶解度降低,由此导致合金强度降低[1]。
2.4Al-Si二元相图
图2-3Al-Si二元相图
Al-Si二元合金属于简单的共晶合金,共晶点为12.5%(见图2-3)。
合金在温室下仅形成α和β两种相。
α相属于Si溶于Al中得固溶体,性能和纯铝相识,也可以写成(Al)相。
在共晶温度577℃时,Si的最大溶解度是1.65%,温室时只有0.05%。
β相是Al溶于Si中得固溶体,其溶解度极小至今尚未完全确定,故可将β相看做纯硅。
通常把共晶体中β相称为共晶硅,它在铸态下不经变质处理时,呈粗大的片状。
在二元Al-Si合金中,随着Si含量的增加,合金的结晶温度范围不断缩小,组织中的共晶体数量逐渐增加,因此,合金的流动性显著提高。
同时,纯铝的线收缩率较大,但Si几乎不收缩,因此,随Si含量的增加,合金的线性收缩率也随之下降,热裂倾向相应减小,并在共晶成分附近表现出优异的综合铸造性能[2]。
相关实验表明硅含量低的ZL102和AC8A(ZL109)合金的相变温度和潜热值均比硅含量高的AlSi20合金高;
对于硅含量相近的铝合金,杂质成分较低的ZL102合金的相变温度和潜热值较高,这是由于Al含量的不同[3]。
ZLl02、AC8A和AC9A.1合金的含硅量分别为10%-13%、11%-13%和22%-24%.固态组织均由固溶硅的αAl固溶体加初晶硅相或共晶硅相组成.根据经验电子理论(EET),可把这3种合金看作理想的不含Si和含Si的αAl晶胞、Si晶胞和少量含杂质的αAl晶胞堆砌构成。
由于Al-Si合金熔体中存在Si—Si短程偏聚,当温度升高时,合金的溶化是从αA1晶胞中某些较弱的但维系着晶胞稳定的键合处开始的.3种合金的αAl固溶体的的结构是相似的,所以相变温度差别不大,相变温度的实验值分别为572.8、561.3和570℃.由于AC9A.1合金的含Al量小于ZLl02和AC8A的含Al量,其所形成的αAl晶胞的数量也少,熔化时需要击断的键合数量也会少,所以其相变潜热数值也小,其实验值分别为:
507.0、470.5和430.9kJ/kg。
可见,在三种铝硅合金中,AC9A.1合金的潜热最小[4]。
相关实验表明中硅铝合金在加入稀土元素后抗拉强度和伸长率都有不同个程度的提高,而且最佳效果的稀土元素加入量都在一个峰值上。
在峰值稀土元素加入量(4.5%RE)之前随稀土元素加入量的升高抗拉强度和伸长率同步升高,在峰值稀土元素加入量(4.5%RE)之后稀土元素加入量的升高抗拉强度和伸长率同步降低。
中硅铝合金在加人稀土元素后熔体的表观粘度增大、流动性变差这一点说明稀土元素的溶解性能不是太好,达饱和后将析出ER—Si化合物的固体颗粒悬浮于熔体中.适当提高合金熔体的过热度和浇铸温度,对稀土元素在熔体中的溶解和保持稀土元素在合金中的作用都是有益的。
稀土元素的加入在一定程度上使原来较粗大的块状共晶颗粒分散形成小的支柱状骼络,使抗拉强度有所升高。
加入的稀土元素在共晶体与基体之间形成一个富含稀土元素的过渡相物质.该过渡相物质即为相关报道过的含16,68%RE的相,该相应为铝、硅、RE的三元化合物RE2Si2A13与稀土元素的固溶体,属六方晶系;
单位晶胞里有14个原子;
晶格常数a=6.24×
10_10m、c=7.30×
10—10m;
该过渡相物质在共晶体与基体相问的滑移变形导致合金的伸长率增大[5]。
2.5Al-Si微观结构的变化及对重要性能的影响
Al-Si系铸造铝合金的微观结构对其性能有很大的影响。
国内外学者对于Al-Si系铸造合金中的各种微观组织对其疲劳性能进行了大量的研究,couple等认为,微观结构缺陷对铸造铝合金的疲劳等寿命影响很大,缺陷尺寸越大,疲劳强度越低。
如孔洞,氧化物薄膜,二次枝晶壁间距,共晶硅颗粒的尺寸和形貌,金属间化合物,滑移带,晶粒尺寸等因素。
其中对疲劳寿命影响最大的是孔洞和氧化物薄膜。
并且随着温度的变化,其微观结构会发生显著的变化,当温度升高时,共晶铝合金过冷度逐渐增大,其凝固组织晶粒也逐渐变细,过共晶铝合金过冷度先减少后增大,其凝固组织晶粒也相应的先变粗大然后又细化,结合分子动力学模拟结果可以知道,随着温度的升高,原子团簇内的原子排列有序和方式要发生突变,这些突变必然会引起熔体原子间的结合能突然增大,从而导致熔体粘度突然增大。
Fe元素可能对Al-7%Si合金共晶相的形核起着重要的作用。
如参考文献
Al-Si合金宏观晶粒尺寸与Si量的关系及结构演化规律.结果表明:
宏观晶粒尺寸随含Si量增加呈峰谷变化,即在3%Si(质量分数,下同)左右达到谷底,在共晶点(12%Si)附近达到峰值;
未变质共晶Al-Si合金的宏观晶粒尺寸与纯Al相近.Al-Si合金宏观晶粒的结构随含Si量增加发生演化,其演化过程为:
单-α-Al→以α→Al为中心外围被共晶团环绕→单-共晶团组织-初生Si为核心、周围环α-Al及共晶团的三层组织结构、变质后Al-Si合金的延伸率也呈现出峰谷变化规律,并且在共晶点附近其力学性能达到了峰值.
第3章铝硅合金ZL102性能简介
3.1ZL102的机械性能
3.1.1力学性能
抗拉强度:
(MPa)≥180
伸长率:
(%)=5%
硬度
≥60(5/250/30)
3.1.2工艺性能
铝合金铸造工艺性能,通常理解为在充满铸型、结晶和冷却过程中表现最为突出的那些性能的综合。
流动性、收缩性、气密性、铸造应力、吸气性。
铝合金这些特性取决于合金的成分,但也与铸造因素、合金加热温度、铸型的复杂程度、浇冒口系统、浇口形状等有关。
●流动性
流动性是指合金液体充填铸型的能力。
流动性的大小决定合金能否铸造复杂的铸件。
在铝合金中共晶合金的流动性最好。
●收缩性
收缩性是铸造铝合金的主要特征之一。
一般讲,合金从液体浇注到凝固,直至冷到室温,共分为三个阶段,分别为液态收缩、凝固收缩和固态收缩。
合金的收缩性对铸件质量有决定性的影响,它影响着铸件的缩孔大小、应力的产生、裂纹的形成及尺寸的变化。
通常铸件收缩又分为体收缩和线收缩,在实际生产中一般应用线收缩来衡量合金的收缩性。
●热裂性
铝铸件热裂纹的产生,主要是由于铸件收缩应力超过了金属晶粒间的结合力,大多沿晶界产生从裂纹断口观察可见裂纹处金属往往被氧化,失去金属光泽。
裂纹沿晶界延伸,形状呈锯齿形,表面较宽,内部较窄,有的则穿透整个铸件的端面。
●气密性
铸铝合金气密性是指腔体型铝铸件在高压气体或液体的作用下不渗漏程度,气密性实际上表征了铸件内部组织致密与纯净的程度。
铸铝合金的气密性与合金的性质有关,合金凝固范围越小,产生疏松倾向也越小,同时产生析出性气孔越小,则合金的气密性就越高。
同一种铸铝合金的气密性好坏,还与铸造工艺有关,如降低铸铝合金浇注温度、放置冷铁以加快冷却速度以及在压力下凝固结晶等,均可使铝铸件的气密性提高。
也可用浸渗法堵塞泄露空隙来提高铸件的气密性。
●铸造应力
铸造应力包括热应力、相变应力及收缩应力三种:
热应力:
热应力是由于铸件不同的几何形状相交处断面厚薄不均,冷却不一致引起的。
在薄壁处形成压应力,导致在铸件中残留应力。
相变应力相变应力是由于某些铸铝合金在凝固后冷却过程中产生相变,随之带来体积尺寸变化。
主要是铝铸件壁厚不均,不同部位在不同时间内发生相变所致。
收缩应力:
铝铸件收缩时受到铸型、型芯的阻碍而产生拉应力所致。
这种应力是暂时的,铝铸件开箱是会自动消失。
但开箱时间不当,则常常会造成热裂纹,特别是金属型浇注的铝合金往往在这种应力作用下容易产生热裂纹。
铸铝合金件中的残留应力降低了合金的力学性能,影响铸件的加工精度。
铝铸件中的残留应力可通过退火处理消除。
合金因导热性好,冷却过程中无相变,只要铸件结构设计合理,铝铸件的残留应力一般较小。
●吸气性
铝合金易吸收气体,是铸造铝合金的主要特性。
液态铝及铝合金的组分与炉料、有机物燃烧产物及铸型等所含水分发生反应而产生的氢气被铝液体吸收所致。
铝合金熔液温度越高,吸收的氢也越多。
3.2工艺性能改良铸造铝硅合金铸造性能
●变质处理
化学成分
铜
硅
镁
锌
铁
锰
镍
钛
锡
≤0.3
10~13
0-0.1
≤1.0
0-0.7
≤0.5
≤0.2
表3-1.ZL102的化学成分
1、添加合金元素的目的
在铸造铝硅合金基础上,添加Cu、Ni、Mn、V和RE等合金元素研制了改良铸造铝硅合金[6],并检测了该合金的铸造性能。
结果表明,改良铸造铝硅合金不但改善了合金的高温力学性能,提高了其服役温度,而且保留了铸造铝硅合金优良的铸造性能。
改良铸造铝硅合金不但具有良好的常温和高温力学性能,而且还保持了铸造铝硅合金优良的铸造性能,是一种很有开发应用前景的新型铸造铝硅合金。
2、添加元素的作用分析[7]
(1)Cu元素的作用分析
铜在铝硅镁合金中可以起到固溶强化的作用,提高合金的强度。
另一方面,由于铜能与铝合金中的镁、铁、锰、镍等元素形成A12Cu、A12CuMg、A19FeNi等化合物,因此同时也能提高合金的高温强度。
(2)Ni元素的作用分析
一般在铝合金中Ni与Fe按1:
1加入时,可形成耐热性好的Al9FeNi相,提高铝合金的耐热性,并降低其热膨胀系数。
(3)Mn元素的作用分析
在铝硅镁合金中,Mn是一个中和铁的有害作用的元素。
熔炼时杂质Fe和Mn结合生成沉淀物进入渣中,Mn还会和合金中的Fe反应生成A16MnxFe1-x金属间化合物,从而有效地提高合金的耐蚀性。
添加少量的Mn可以细化材料的组织,提高再结晶温度,增强合金的耐热性。
(4)V元素的作用分析
铝合合金中加入钒元素,可以形成Al7V化合物,这些化合物可作为α固溶体的结晶核心,使晶粒细化,提高力学性能和改善工艺性能,但量不能多,过多则会出现大片状化合物,降低强度、耐蚀性等。
(5)RE元素的作用分析
①净化作用:
由于RE具有很高的化学活性,与H2、Fe、S等杂质元素具有很强的化学亲和力,可以与各种杂质元素形成化合物,因而能消除H2、Fe、S和过剩游离态Si等有害杂质的影响。
②变质作用:
加入适量的RE,能够有效减小铝合金的枝晶间距,细化铸态晶粒。
③微合金化作用:
RE与Al及其合金元素能发生微合金化作用,可以提高合金常温和高温力学性能。
3、添加合金元素后对性能的影响
用光学显微镜(OM)等分析研究Al-10Ce中间合金对ZL102共晶铝硅合金的变质处理效果。
结果表明,Al-10Ce中间合金用量、熔体中的杂质以及冷却速度对变质效果的影响很大,Al-10Ce中间合金用量为0.9%左右时达到最佳变质效果,用量少变质效果差,用量过多则形成过变质。
通过提高Al-Si的纯度可以获得变质组织。
冷却速度超过70℃/min时才具有明显的变质效果。
由于冷却强度不同,铸棒中心部位变质效果比边部差。
Al-10Ce中间合金对共晶铝硅合金变质处理时间较短。
在普通铸造条件下,ZL102组织几乎全部为共晶体,由粗针状的硅晶体和a固溶体组成,强度和塑性都较差。
生产上通常用钠盐变质剂进行变质处理,得到细小均匀的共晶体加一次a固溶体组织,以提高性能(见图3-1)。
变质后
变质前
图3-1变质处理前后变化
●热压作用
在成形过程中,金属液自始至终承受等静压,并在压力作用下发生结晶凝固,减少或消除了锻件的缩孔和疏松,提高锻件的致密度,提高合金组织的均匀性,使合金力学性能大为提高。
看出材料在压缩后抗拉强度σb明显变大,并且不同的压缩量下抗拉强度的增强情况也不同,其中压缩比为85.81%的试样抗拉强度增加最大(见表3-2)。
表3-2.ZL102的试验结果
铸态ZL102中组织相对比较差,Si呈针状或块状分布,对基体有割裂作用,没有形成紧密的组织,而是呈现比较分散的排列;
经过热处压缩以后随着变形量的增大,Si由最初的条状逐渐变小,最后呈颗粒状分布,Si的特殊分布形式和状态使Si类似于颗粒增强基体作用,强化了共晶体,改善了合金零件的力学性能。
●合金浇注温度、模具预热温度等工艺参数
浇注温度直接影响锻件的质量和模具寿命[8]。
浇注温度过高,使金属中吸气较多,且晶粒粗大,降低力学性能,同时,模具在使用前要进行均匀预热,以减小温差,降低热应力,防止模具裂纹产生而影响制件的力学性能。
各参数的影响如下:
图3-2浇注温度磨具预热温度对机械性能的影响
如图3-2,c和d合金浇注温度在640℃时得到的抗拉强度最高,而塑性在630℃时表现较好;
e和f显示了模具预热温度对于力学性能的影响。
根据对实验数据分析,抗拉强度和拉伸率随模具预热温度升高而呈现下降的趋势。
总之,根据不同工艺参数对力学性能的影响,在实生产中,可以按照要求而合理选择生产工艺。
●塑性变形对ZL102合金组织及性能
在350°
C时不同形状变量下其显微组织如图3-3所示。
由图可知随着压缩量的增大,晶粒明显得到细化,其中的a枝晶被明显拉长。
变形量到50%时,显微组织出现明显垂直于压缩方向的变形方向性及较明显的带状组织。
在同一等温压缩温度下随着变形程度的增加,存的变形能更多,更有利于热处理时大量再结晶晶核和强化相的形成,发生更加充分的回复与再结晶,得到更加细化的组织和优良的性能,故50%变形时显微组织的晶粒较其他变形程度更加细小。
图3-3显微组织
3.4退火温度对ZL102性能的影响
由二元合金相图可以得出,577°
C时Si在a(Al)固溶体中的溶解度为16.5%,温室时下降至0.05%。
但因为硅的沉淀和集聚速度很快,甚至固溶处理时都可能发生固溶体分解,析出硅质点,不形成共格或半共格的过渡相。
进而不能有效提高其强度,所以工业上一般只采用退火来消除内应力。
●热处理后的组织变化
图3-4晶相组织变化
经过不同温度退火,观察其金相组织[9]。
如图3-4,白色树枝状的为a(A1)以及依附在其上的共晶组织中的仅相.黑色部分为共晶组织中的B相。
经不同温度退火处理后,随退火温度升高,其组织发生明显变化,可以看出低倍下其沟槽明显增加,在退火过程中随温度的升高其缺陷发生变化。
●组织变化引起的材料硬度和防腐性能的变化
表3-3为硬度与退火温度的关系。
从图可以看出ZL102的铸态硬度为55.3HBS,250°
C退火时其硬度达到最高值57.1HBS,而到300°
C时其硬度值下降为54.3HBS,到400°
下降比较明显。
从这个曲线趋势上看,其硬度是先增后减。
之所以呈现这种状况[10],因为低温加热时,材料的内应力可能减小,但强度、硬度基本不变。
而温度升高到一定程度时其硬度明显下降,分析与其温度过高,晶粒长大明显,产生过热现象有关。
表3-3.硬度与退火温度的关系
图3-5铸态及不同温度退火后的腐蚀形貌
图3-5为铸态及不同温度退火后的腐蚀形貌。
可以看到,250°
C和300°
时耐蚀性要好一些,而铸态试样腐蚀坑相对明显一些,400°
C退火时其腐蚀空洞非常大。
其主要原因还是与其热处理后的显微组织有关,浸蚀剂里含有少量的盐酸,均能与铝合金表面的氧化铝反应,从而加快机体铝的腐蚀;
而经过热处理的铝合金虽然组织成分上没有发生太大的变化,但在加热过程中晶格中的位错发生变化、晶粒长大以及应力的降低都可能对其耐腐蚀性有影响。
第4章铝硅合金的应用
铝硅合金具有很多优良的性能,具有广阔的应用前景。
铝硅合金可以用于制造低中强度的形状复杂的铸件,如盖板、电机壳、托架等,也用作钎焊焊料。
当硅含量较低时(比如0.7),铝硅合金的延展性较好,常用来做变形合金;
当硅含量较高时(比如7%),铝硅合金熔体的填充性较好,常用来做铸造合金。
在含硅量超过Al-Si共晶点(硅12.6%)的铝硅合金中,硅的颗粒可量高达14.5%~25%时,再加入一定量的Ni,Cu,Mg等元素能改善其综合力学性能。
它们可用于汽车发动机中代替铸铁汽缸而明显减轻重量。
其中含硅量11%~13%的合金以其质轻、低膨胀系数和高耐蚀性能等特点而成为最佳的活塞材料之一。
在含硅量超过Al-Si共晶点(硅11.7%)的铝硅合金中,硅的颗粒可明显提高合金的耐磨性,组成一类用途很广的耐磨合金。
铝硅合金的衍生品AI—Si相变材料可应用于电力调峰。
利用铝基三元合金相变材料的显热及相变潜热将低谷电以热能的形式储存起来,待到用电高峰时,利用低温空气通过储能换热器将热能以热风的形式提取出来,另外还通过装置内的气一水换热器,将部分热风转换成热水,达到供暖和生活两用的目的。
中科院广州能源所在90年代初主要研究了以铝硅合金为储能材料、以普通碳钢为外壳的储能元件。
该元件具有储能密度大、热导辜高、腐蚀性小等特点,并能在700℃以上长期工作,研制出的电热锅和集电饭煲辞已转让生产。
同时,AI—Sl相变材料还可以可应用于太阳能的利用上。
我国科学家利用铝基舍垒作为相变储能材料,以耐热的Fe—C合金作为容器外壳组成储能元件。
通过聚光式太阳灶,实现太阳能600屯一700℃的高温储存,这种高温能源导热系数高,热交换速度快,可以用于煮饭、炒菜、烧水;
也可以作为建筑物的采暖辅助功能源。
还有一种高导铝硅合金,因其兼具良好的铸造性、高导电性、较高强度、耐腐蚀和耐摩擦等综合性能,是一种优异的结构功能材料。
铝硅合金相对于铜、钛等材料价格低廉,相对于钢铁具有轻质特性,在大规模电工基础建设工程方面的应用将会有广阔的前景。
日本目前已经把快速凝固高硅铝合金成功地应用于汽车制造业中,主要用来制造发动机及空调机的转子,叶片及活塞等。
马自达汽车公司利用喷射沉积Al-Si-Fe-Cu-Mg合金制造了一种新型发动机转子,使发动机效率大幅度提高,节油20%。
公司预计以每月10吨的速度生产这种发动机转子。
1993年他们将这种发动机安装在ENUOS800和XEDOS9新型轿车上投放日本、欧洲及北美市场。
Sumitomo电气公司利用快速凝固PMAi-Si-X高硅铝合金代替烧结钢,大批量制造汽车空调压缩机转子和叶片,使转子重量减轻60%,整个压缩机重量减轻40%,提高了机器的工作效率。
雅马哈汽车制造公司生产的快速凝固高硅铝合金活塞也投入市场,这种活塞与普通铸铁相比,重量减轻20%,寿命提高30%,而且显著降低噪音,减少污染。
此外还可以利用高硅快速凝固铝合金制造压缩机连杆,