数控加工理论与编程技术Word格式文档下载.docx
《数控加工理论与编程技术Word格式文档下载.docx》由会员分享,可在线阅读,更多相关《数控加工理论与编程技术Word格式文档下载.docx(46页珍藏版)》请在冰豆网上搜索。
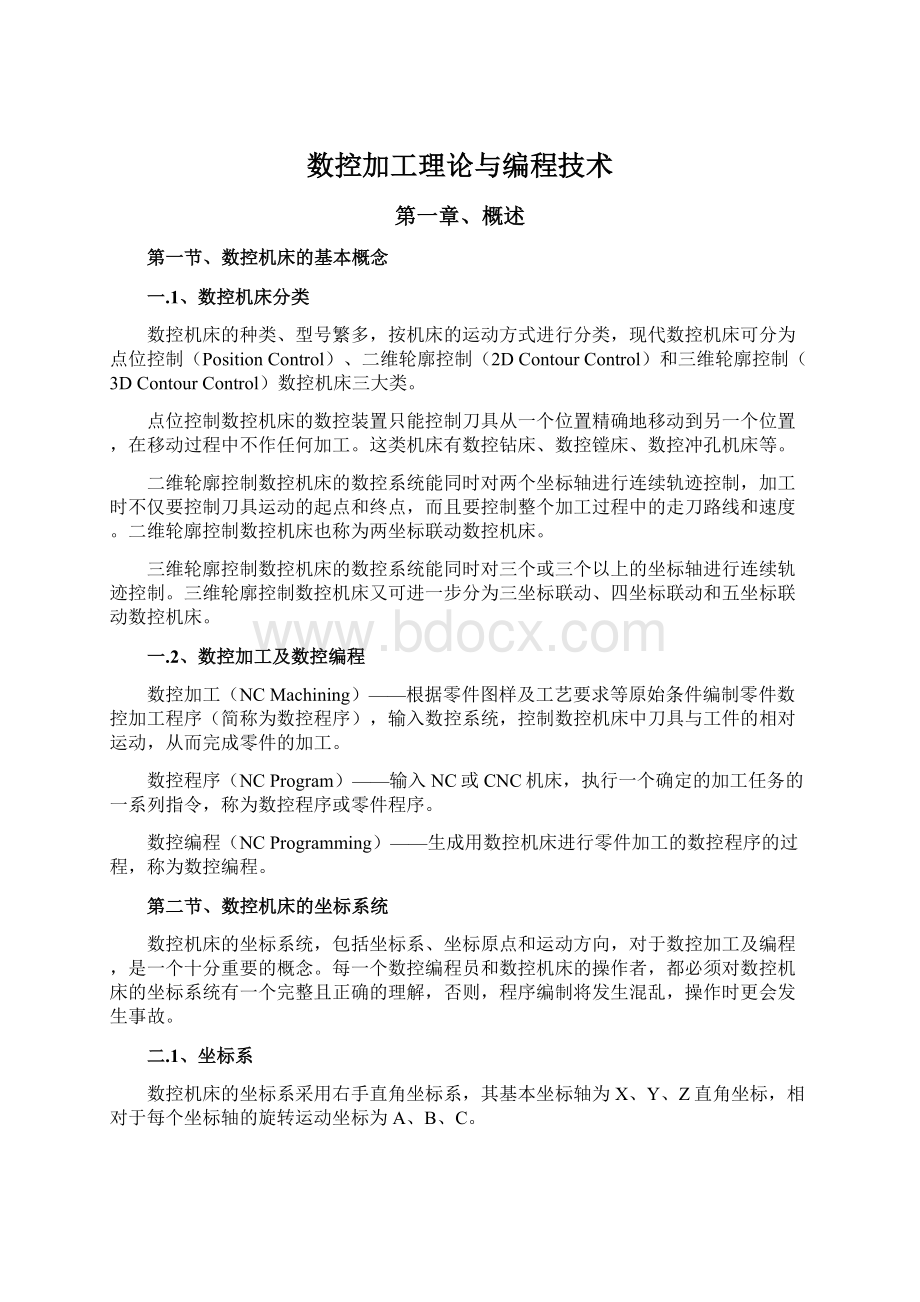
旋转坐标轴A、B、C相应地在X、Y、Z坐标轴正方向上,按右手螺纹前进方向来确定。
二.3、坐标原点
机床原点——现代数控机床一般都有一个基准位置(setlocation),称为机床原点(machineorigin或homeposition)或机床绝对原点(machineabsoluteorigin),是机床制造商设置在机床上的一个物理位置,其作用是使机床与控制系统同步,建立测量机床运动坐标的起始点。
机床参考点——与机床原点相对应的还有一个机床参考点(referencepoint),它也是机床上的一个固定点,一般不同于机床原点。
一般来说,加工中心的参考点为机床的自动换刀位置。
程序原点——对于数控编程和数控加工来说,还有一个重要的原点就是程序原点(programorigin),是编程人员在数控编程过程中定义在工件上的几何基准点,有时也称为工件原点(partorigin)。
程序原点一般用G92或G54~G59(对于数控镗铣床)和G50(对于数控车床)指定。
装夹原点——除了上述三个基本原点以外,有的机床还有一个重要的原点,即装夹原点(fixtureorigin)。
装夹原点常见于带回转(或摆动)工作台的数控机床或加工中心,一般是机床工作台上的一个固定点,比如回转中心,与机床参考点的偏移量可通过测量存入CNC系统的原点偏移寄存器(originoffsetregister)中,供CNC系统原点偏移计算用。
二.4、原点偏移
(由图1-8说明)现代CNC系统一般都要求机床在回零操作,即使机床回到机床原点或机床参考点之后,通过手动或程序命令(比如G92X0Y0Z0)初始化控制系统后,才能启动。
机床参考点和机床原点之间的偏移值存放在机床常数中。
初始化控制系统是指设置机床运动坐标X,Y,Z,A,B等的显示为零。
对于程序员而言,一般只要知道工件上的程序原点就够了,与机床原点、机床参考点及装夹原点无关,也与所选用的数控机床型号无关。
但对于机床操作者来说,必须十分清楚所选用的数控机床上上述各原点及其之间的偏移关系。
数控机床的原点偏移,实质上是机床参考点向编程员定义在工件上的程序原点的偏移。
二.5、绝对坐标编程及增量坐标编程
数控系统的位置/运动控制指令可采用两种编程坐标系统进行编程,即绝对坐标编程(absoluteprogramming)和增量坐标编程(incrementalprogramming)。
绝对坐标编程——在程序中用G90指定,刀具运动过程中所有的刀具位置坐标是以一个固定的编程原点为基准给出的,即刀具运动的指令数值(刀具运动的位置坐标),与某一固定的编程原点之间的距离给出的。
增量坐标编程——在程序中用G91指定,刀具运动的指令数值是按刀具当前所在位置到下一个位置之间的增量给出的。
第三节、现代数控机床的刀具补偿
为了简化零件的数控加工编程,使数控程序与刀具形状和刀具尺寸尽量无关,CNC系统一般都具有刀具长度和刀具半径补偿功能。
前者可使刀具垂直于走刀平面(比如XY平面,由G17指定)偏移一个刀具长度修正值;
后者可使刀具中心轨迹在走刀平面内偏移零件轮廓一个刀具半径修正值,两者均是对二坐标数控加工情况下的刀具补偿。
在现代CNC系统中,有的已具备三维刀具半径补偿功能。
对于四、五坐标联动数控加工,还不具备刀具半径补偿功能,必须在刀位计算时考虑刀具半径。
刀具长度补偿也要视情况而定,一般而言,刀具长度补偿对于二坐标和三坐标联动数控加工是有效的,但对于刀具摆动的四、五坐标联动数控加工,刀具长度补偿则无效,在进行刀位计算时可以不考虑刀具长度,但后置处理计算过程中必须考虑刀具长度。
三.1、刀具长度补偿
刀具长度补偿可由数控机床操作者通过手动数据输入方式实现,也可通过程序命令方式实现,前者一般用于定长刀具的刀具长度补偿,后者则用于由于夹具高度、刀具长度、加工深度等的变化而需要对切削深度用刀具长度补偿的方法进行调整。
在现代CNC系统中,用MDI方式进行刀具长度补偿的过程是:
机床操作者在完成零件装夹、程序原点设置之后,根据刀具长度测量基准采用对刀仪测量刀具长度,然后在相应的刀具长度偏置寄存器中,写入相应的刀具长度参数值。
当程序运行时,数控系统根据刀具长度基准使刀具自动离开工件一个刀具长度距离,从而完成刀具长度补偿。
在加工过程中,为了控制切削深度,或进行试切加工,也经常使用刀具长度补偿。
采用的方法是:
加工之前在实际刀具长度上加上退刀长度,存入刀具长度偏置寄存器中,加工时使用同一把刀具,而调整加长后的刀具长度值,从而可以控制切削深度,而不用修正零件加工程序。
(由图1-11说明)程序命令方式由刀具长度补偿指令G43和G44实现:
G43为刀具长度正补偿或离开工件补偿,G44为刀具长度负步长或趋向工件补偿。
使用非零的Hnn代码选择正确的刀具长度偏置寄存器号,正补偿将刀具长度值加到指令的轴坐标位置,负补偿则将刀具长度值从指令的轴坐标位置减去。
值得进一步说明的是,数控编程员则应记住:
零件数控加工程序假设的是刀尖(或刀心)相对于工件的运动,刀具长度补偿的实质是将刀具相对于工件的坐标由刀具长度基准点(或称刀具安装定位点)移到刀尖(或刀心)位置。
三.2、二维刀具半径补偿
对于铣削和车削数控加工,尽管二维刀具半径补偿的原理相同,但由于刀具形状和加工方法区别较大,刀具半径补偿方法仍有一定的区别。
铣削加工刀具半径补偿
在二维轮廓数控铣削加工过程中,由于旋转刀具具有一定的刀具半径,刀具中心的运动轨迹并不等于所需加工零件的实际轮廓,而是偏移零件轮廓表面一个刀具半径值。
如果之间采用刀心轨迹编程(cuttercenterlineprogramming),则需要根据零件的轮廓形状及刀具半径采用一定的计算方法计算刀具中心轨迹。
因此,这一编程方法也称为对刀具的编程(programmingthetool)。
当刀具半径改变时,需要重新计算刀具中心轨迹;
当计算量较大时,也容易产生计算错误。
数控系统的刀具半径补偿(cutterradiuscompensation)就是将计算刀具中心轨迹的过程交由CNC系统执行,编程员假设刀具半径为零,直接根据零件的轮廓形状进行编程,因此,这种编程方法也称为对零件的编程(programmingthepart),而实际的刀具半径则存放在一个可变成刀具半径偏置寄存器中。
在加工过程中,CNC系统根据零件程序和刀具半径自动计算刀具中心轨迹,完成对零件的加工。
当刀具半径发生变化时,不需要修改零件程序,只需修改存放在刀具半径偏置寄存器中的刀具半径值或者选用存放在另一个刀具半径寄存器中的刀具半径所对应的刀具即可。
(由图1-13说明)铣削加工刀具半径补偿分为刀具半径左补偿,用G41定义,和刀具半径右补偿,用G42定义,使用非零的Dnn代码选择正确的刀具半径偏置寄存器。
根据ISO标准,当刀具中心轨迹沿前进方向位于零件轮廓右边时称为刀具半径右补偿;
反之称为刀具半径左补偿;
当不需要进行刀具半径补偿时,则用G40取消刀具半径补偿。
(由图1-14说明)在实际轮廓加工过程中,刀具半径补偿执行过程一般分为三步:
、刀具半径补偿建立——刀具由起刀点以进给速度接近工件,刀具半径补偿偏置方向由G41(左补偿)或G42(右补偿)确定。
、刀具半径补偿进行——一旦建立了刀具半径补偿状态,则一直维持该状态,直到取消刀具半径补偿为止。
、刀具半径补偿取消——刀具撤离工件,回到退刀点,取消刀具半径补偿。
车削加工刀尖半径补偿
对于车削数控加工,由于车刀的刀尖通常是一段半径很小的圆弧,而假设的刀尖点并不是刀刃圆弧上的一点,因此,在车削锥面、倒角或圆弧时,可能会切削不足或切削过量的现象。
因此,当使用车刀来切削加工锥面时,必须将假设的刀尖点的路径作适当的修正,使之切削加工出来的工件能获得正确尺寸,这种修正方法称为刀尖半径补偿。
(由图1-17说明)与铣削加工刀具半径补偿一样,车削加工刀尖半径补偿也分为左补偿(G41指令)和右补偿(用G42指令)。
与二维铣削加工方法一样,采用刀尖半径补偿时,刀具运动诡计指的不是刀尖,而是刀尖上刀刃圆弧的中心位置,这在程序原点设置时就需要考虑。
二维刀具半径补偿仅在指定的二维走刀平面内进行,走刀平面由G17(X-Y平面)、G18(Y-Z平面)和G19(Z-X平面)指定,刀具半径或刀刃半径值则通过调用相应的刀具半径偏置寄存器(用H或D指定)来取得。
现代CNC系统的二维刀具半径补偿不仅可以自动完成刀具中心轨迹的偏置,而且还能自动完成直线与直线转接、圆弧与圆弧转接和直线与圆弧转接等尖角过渡功能。
三.3、三维刀具半径补偿
若干概念
加工表面上切触点坐标及单位矢量(由图1-18说明)
刀具类型及刀具参数(由图1-19说明)
刀具中心(由图1-19说明)
三维刀具补偿原理(由图1-20、1-21、1-22说明)
设刀具与加工表面切触点
的坐标为
,加工表面在
点的单位法矢向量为
,对于环形刀
,其刀心坐标为:
对于端铣刀
对于球形刀
需要注意的是:
当
时,其刀心坐标为:
第四节、数控编程概述
四.1、数控编程的定义
生成用数控机床进行零件加工的数控程序的过程,称为数控空编程(NCprogramming),有时也称为零件编程(partprogramming)。
数控编程可以手工完成,即手工编程(manualprogramming),也可以由计算机辅助完成,即计算机辅助数控编程(computeraidedNCprogramming)。
采用计算机辅助数控编程需要一套专用的数控编程软件,现代数控编程软件主要分为以批处理命令方式为住的各种类型的APT语言和以CAD软件为基础的交互式CAD/CAM—NC编程集成系统。
四.2、数控编程的步骤
一般来说,数控编程过程主要包括:
分析零件图样、工艺处理、数学处理、编写程序单、输入数控系统几程序检验。
(由图1-23说明)
图1-23数控编程过程
四.3、数控编程的方法
数控编程的分类方法有多种,大致可归纳为:
根据编程地点进行分类:
办公室和车间;
根据变成计算机进行分类:
CNC内部计算机,个人计算机(PC)或工作站;
根据变成软件进行分类:
CNC内部编程软件,APT语言或CAD/CAM集成数控编程软件。
图1-24数控编程的分类
手工编程
是指编制零件数控加工程序的各个步骤,即从零件图样分析、工艺处理、确定加工路线和工艺参数、几何计算、编写零件的数控加工程序单直至程序的检验,均由人工来完成。
APT语言自动编程
APT是一种自动编程工具(AutomaticallyProgrammedTool)的简称,是一种对工件、刀具的几何形状及刀具相对于工件的运动等进行定义时所用的一种接近于英语的符号语言。
把用APT语言书写的零件加工程序输入计算机,经计算机的APT语言编程系统编译产生刀位文件(CLDATAfile),然后进行数控后置处理,生成数控系统能接受的零件数控加工程序的过程,称为APT语言自动编程。
CAD/CAM集成系统数控编程
是以待加工零件CAD模型为基础的一种集加工工艺规划及数控编程为一体的自动编程方法。
其中零件CAD模型的描述方法多种多样,适用于数控编程的主要有表面模型和实体模型,其中以表面模型在数控编程中应用较为广泛。
CAD/CAM集成系统数控编程的主要特点是零件的几何形状可在零件设计阶段采用CAD/CAM集成系统的几何设计模块在图形方式下进行定义、显示和修改,最终得到零件的几何模型。
数控编程的一般过程包括刀具的定义或选择,刀具相对于零件表面的运动方式的定义,切削加工参数的确定,走刀轨迹的生成,加工过程的动态图形仿真显示、程序验证直到后置处理等,一般都是在屏幕菜单及命令驱动等图形交互方式下完成的,具有形象、直观和高效等优点。
第二章、手工编程
第一节、数控编程常用指令及其格式
一.1、程序段的一般格式
一个程序段中各指令的格式为:
N35G01X26.8Y32.Z15.428F152.
其中N35为程序段号,现代CNC系统中很多都不要求程序段号,即程度段号可有可无;
G代码为准备功能;
X、Y、Z为刀具运动的终点坐标位置;
F为进给速度代码。
在一个程度段中,可能出现的编码字符还有S、T、M、I、J、K、A、B、C、D、H、R等。
一.2、常用的编程指令
(1)准备功能指令
准备功能指令由字符G和其后的1~3位数字组成,常用的从G00~G99,很多现代CNC系统的准备功能已扩大到G150。
准备功能的主要作用是指定机床的运动方式,为数控系统的插补运算作准备。
常用的G指令如下:
、坐标快速定位与插补指令
这是一组模态指令,即同时只能有一个有效,缺省为G00。
G00——坐标快速定位
G01——线性插补
G02、G03——圆弧插补
、G17、G18、G19——坐标平面选择
、G40、G41、G42——刀具半径补偿
、G43、G44、G49——刀具长度补偿
、G54~G59——选择程序原点1~6
、G90、G91——绝对坐标及增量坐标编程
、G92——设定工件坐标系
、G73~G89——固定循环加工
(2)辅助功能指令
辅助功能指令亦称“M”指令,由字母M和其后的两位数字组成,从M00~M99共100种。
这类指令主要是用于机床加工操作时的工艺性指令。
常用的M指令有:
、M00——程序停止
、M01——计划程序停止
、M02——程序结束
、M03、M04、M05——分别为主轴顺时针旋转、主轴逆时针旋转及主轴停止
、M06——换刀
、M08——冷却液开
、M09——冷却液关
、M30——程序结束并返回
(3)其它常用功能指令
、T功能——刀具功能
、S功能——主轴速度功能
、F功能——进给速度进给率功能
第二节、车削数控加工及其手工编程
二.1、普通数控车床的车削加工
普通数据控车床能完成端面、内外圆、倒角、锥面、球面及成形面、螺纹等的车削加工,主切削运动是工件的旋转,工件的成形则由刀具在ZX平面内的插补运动保证,如图所示。
数控车削加工与普通车削加工的工艺和刀具选择没有本质的区别。
与普通车削加工不同的是,要保证车削加工精度,特别是锥面和成形表面的精度,需要准确测量车刀刀尖刀刃圆弧半径,并采用刀尖半径补偿(TNR)方法进行加工。
(1)坐标的取法及坐标指令数控车床以径向为X轴,纵向为Z轴。
从主轴箱指向尾架方向为+Z方向,而从尾架指向主轴箱方向为-Z轴,从主轴轴心线指向操作者方向为+X轴方向,如图所示。
(2)数控车削加工的程序原点一般取工件装夹端面(定位面)的中心位置为程序原点,工件坐标系的坐标方向与车床坐标系一致,当工件装在车床上时,其程序原点与工件坐标素如图所示。
一般来说,数控车床的参考点在Z坐标和X坐标的极限行程处,与机床原点一致,如图所示。
对于数控车削加工中心,其参考点为换刀位置。
当做,某些情况下,程序原点也可以取在工件轴心线上的其它位置,要根据工件的实际情况进行确定。
(3)X和Z坐标指令在按绝对坐标编程时使用代码X和Z,按增量坐标编程时使用代码U和W。
切削圆弧时,使用I和K表示圆心相对于圆弧起点的坐标值,I对应X轴,K对应Z轴。
在一个零件的程序中或一个程序段中,可以按绝对坐标编程或增量坐标编程,也可用绝对坐标与增量坐标混合编程。
由于车削加工图样上的径向尺寸及测量的径向尺寸使用的是直径值,因此在数控车削加工的程序中输入的X及U坐标值也是“直径值”,即按绝对坐标编程时,X为直径值,按增量坐标编程时,U为径向实际位移值的二倍,交附上方向符号(正向省略)。
二.2、轴类零件数控车削加工及其编程举例
已知某立由的待加工零件图如图所示,要求精车所有外形(不包括螺纹),一次成形,不留加工余量。
(1)工艺分析
此零件的车削加工包括车端面、倒角、外圆、圆弧过渡面和切槽加工,而且要分两次,从零件装夹才能完成全部加工。
、选择刀具从零件图样来看,除切槽加工外,可以采用90°
强力车刀(1#)进行所有车削加工,切槽加工采用3mm宽的切柄刀(2#),如图所示。
、零件的安装方式零件装夹于机床主由与尾架顶尖间,采用双顶鸡心夹方式定位。
、工艺路线第一次装增值完成右端的加工,其走刀过程为:
首先车削外形,然后切槽加工,程序原点定为W点,其走刀路线和工艺尺寸如图所示。
第二闪装增值完成左端的加工,只需采用90°
强力车刀进行外形加工,程序原点为O点,其走刀路线和工艺尺寸如图所示。
、切削用量车外圆主轴转速定了S630,进给速度为F140;
车端面主轴速度定为S400,进给速度为F100;
车倒角和圆弧过渡面主由速度定为S500,进给速度为F100;
切槽时,主轴速度为S300,进给速度为F10。
(2)数控编程
由于该工件的外形既有倒角又有圆弧过渡面,90°
强力车刀刀尖有R0.5mm的刀刃圆弧半径,为了保证车削工件的外形正确,需要采用刀尖半径补偿方法进行编程。
假定90°
强力车刀刀尖的起始位置为(300,214.5),其车削加工程序及程序说明如下:
二.3、盘类零件数控车削加工及其手工编程
已知某调节盘的待加工零件图样,其中两端面和中心孔已加工好,要求精车其它外形,一次成形,不留加工余量。
选择刀具——采用圆弧车刀和切槽刀;
零件安装方式——零件装夹于机床主轴与尾架顶尖间,采用专有心轴方式定位。
工艺路线——此工序为精车加工,其走刀过程是:
首先车外形,后切槽,程序原点为W点,其走刀路线和工艺尺寸如图所示。
编程参数计算——计算求得图中的中点坐标为:
数控编程——此零件加工采用圆弧车刀,应用刀具半径补偿进行编程,其数控程序及程序说明如下:
二.4、带螺纹的轴类零件数控车削加工及其手工编程
如图所示为某立轴的零件图样,需进行精车加工,图中不加工。
选用具有直线—圆弧插补功能的数控车床加工该零件,编制精加工程序。
(1)工艺路线
、先倒角→切削螺纹的实际外圆→切削锥度部分→车削外圆→倒角→车削外圆→切削圆弧部分→车削外圆
、切槽
、车螺纹
(2)选择刀具及画出刀具布置图根据加工要求,选用三把刀具。
I号刀车外圆,II号刀车螺纹。
III号刀车螺纹。
刀具布置如图所示。
采用对刀仪对刀,螺纹刀尖相对于I号刀尖在Z向偏置15mm。
编程之前,应正确地选择换刀点,以便在换刀过程中,刀具与工件,机床和夹具不会碰撞。
本例中,换刀点为A,如图所示。
(3)确定切削用量车外圆,主轴转速为S630,进给速度为F150。
切槽时,主轴转速为S315,进给速度为F10。
切削螺纹时,主轴转速为S200,进给速度为F150。
(4)编写程序确定O为工件坐标系的原点(参见图),并将A点(换刀点)作为程序的起点。
该零件的加工程序及程序说明如下:
第三节、镗铣数控加工及其手工编程
三.1、镗铣数控加工中的基本工艺问题
(1)工件坐标系的确定及程序原点的设置——工件坐标系采用与机床运动坐标系一致的坐标方向,工件坐标系的原点(即程序原点)要选择便于测量或对刀的基准位置,同时要便于编程计算。
(2)安全高度——对于铣削加工,起刀点和退刀点必须离开加工零件上表面一个安全高度,保证刀具在停止状态时,不与加工零件和夹具发生碰撞。
在安全高度位置时刀具中心(或刀尖)所在的平面也称为安全面,如图所示。
(3)进刀/退刀方式——对于铣削加工,刀具切入工件的方式,不仅影响加工质量,同时直接关系到加工的安全。
对于二维轮廓加工,一般要求从侧向进刀或沿切线方向进刀,尽量避免垂直进刀,如图所示。
退刀方式也应从侧向或切向退刀,刀具从安全面高度下降到切削高度时,应离开工件毛坏边缘一个距离,不能直接贴着加工零件理论轮廓直接下刀,以免发生危险,如图所示。
下刀运动过程不工要用快速(G00)运动,而要用(G01)直线插补运动。
对于型腔的粗铣加工,一般应先钻一个工艺孔至型腔底面(留一定精加工余量),并扩孔,以便所使用的立铣刀能从工艺孔进行型腔粗加工。
(4)刀具半径补偿——二维轮廓加工,一般均采用刀具半径补偿。
在刀具半径补偿有效之前,刀具应远离零件轮廓适当距离,且应与选定好的切入点和进刀当时协调,保证刀具半径补偿的有效。
(5)刀具半径确定——对于铣削加工,精加工刀具半径选择的主要依据是零件加工轮廓和加工轮廓凹处的最小曲率半径或圆弧半径,刀具半径应小于该最小曲率半径值。
另外还要考虑刀具尺寸与零件尺寸的协调问题,即不要用一把很大的刀具加工一个很小的零件。
对于粗加工,如果加工轮廓个别地方圆弧半径很小,可以考虑采用较大的刀具进行粗加工,但必须避免加工中的干涉。
三.2、点位数控加工及其编程
下面举例说明点位数控加工及其编程方法。
三.3、二维外形轮廓数控铣削加工及其编程
简单外形轮廓零件的数控铣削加工及其编程
简单凸轮的数控铣削加工及其编程举例
简单内轮廓及型腔的数控加工及其编程
简单连杆的数控加工及其编程
第四节、现代CNC系统中的高级编程方法
四.1、轮廓描述