结构件的机器人焊接工艺分析0829Word格式文档下载.docx
《结构件的机器人焊接工艺分析0829Word格式文档下载.docx》由会员分享,可在线阅读,更多相关《结构件的机器人焊接工艺分析0829Word格式文档下载.docx(10页珍藏版)》请在冰豆网上搜索。
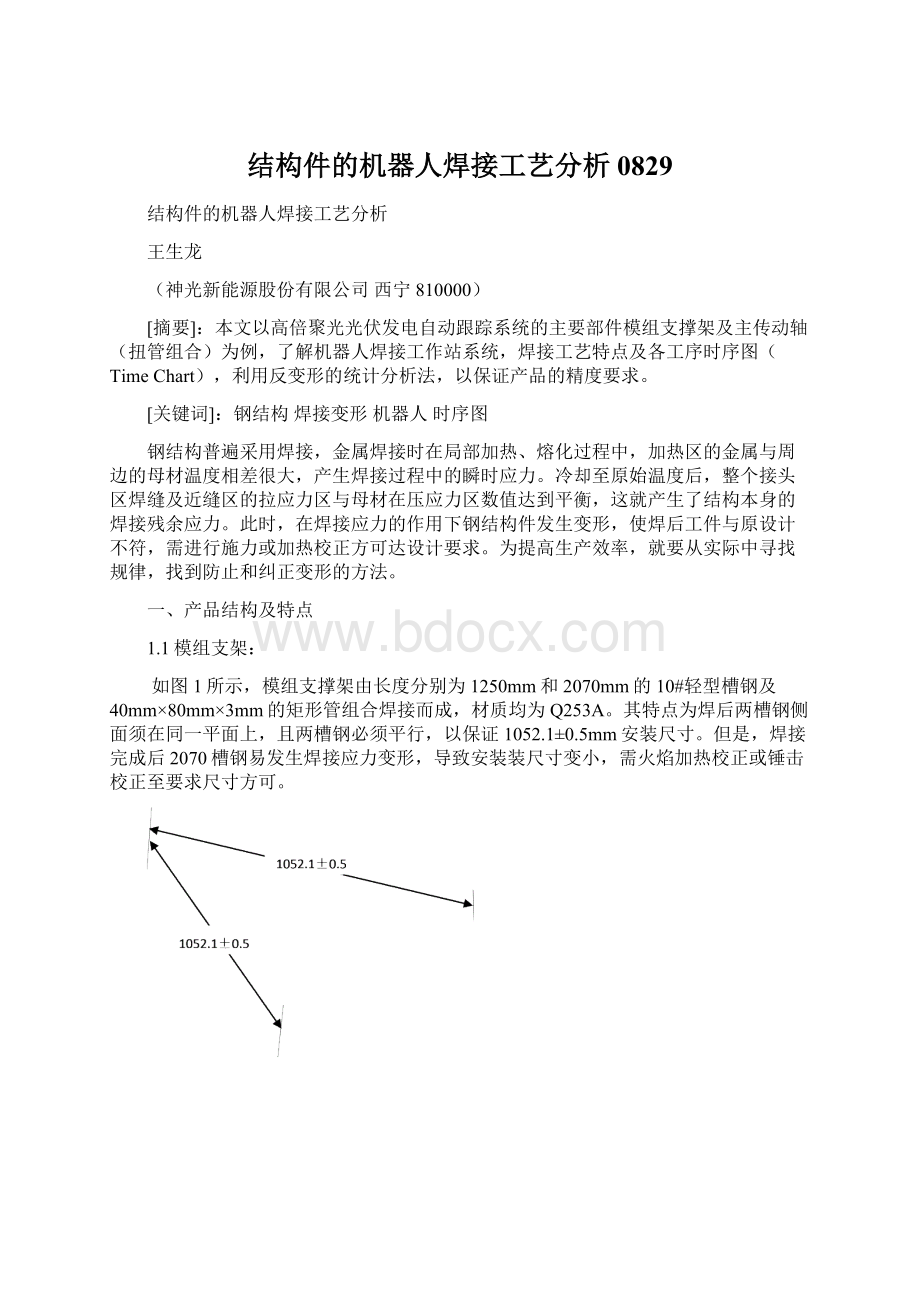
一、产品结构及特点
1.1模组支架:
如图1所示,模组支撑架由长度分别为1250mm和2070mm的10#轻型槽钢及40mm×
80mm×
3mm的矩形管组合焊接而成,材质均为Q253A。
其特点为焊后两槽钢侧面须在同一平面上,且两槽钢必须平行,以保证1052.1±
0.5mm安装尺寸。
但是,焊接完成后2070槽钢易发生焊接应力变形,导致安装装尺寸变小,需火焰加热校正或锤击校正至要求尺寸方可。
图1.模组支撑架
1.2主传动轴(扭管组合):
图2.主传动轴(扭管组合)
(A--法兰板组合件I,B--法兰板组合件II,C--M20×
55法兰螺栓,D--扭矩管,E--轴管组合见)
如图2所示为主传动轴组合焊接件,其材质全部为Q235A。
主要由两端法兰板组合件、轴管组合件和Φ168×
3mm圆管等焊接而成。
其特点为组焊零件多,易发生变形,对两法兰板与扭管之间的垂直度要求高;
为整个光伏发电光线追踪系统提供各方向的旋转支持,因此对于主传动轴焊接完成后的直线度及轴管与扭管的垂直度要求非常高。
一般要求主传动轴整体直线度为4000mm/2mm;
轴管与扭管垂直度为2mm。
2、工艺过程
2.1模组支架加工工艺:
根据加工方法的不同,模组支架的加工工艺分为传统加工工艺和现代加工工艺。
传统加工工艺为先焊后孔,即焊接完成后再钻安装孔;
现代加工工艺为先孔后焊,即将安装孔钻好后再焊接。
具体介绍如下:
1)传统加工工艺为人工焊接,劳动量大,效率低,生产成本高。
其一般生产步骤为:
人工上料至手工焊夹具→夹紧工件→点焊定型→松开工件→取件→手工焊接→将工件装卡至钻孔模具→钻孔→取件→完成。
依照生产步骤,如时序图所示,共耗时700秒左右。
时序图1
2)现代加工工艺为机器人焊接,装备先进,生产效率高,焊接质量好,可不间断作业。
人工上料→夹紧工件→机器人焊接→夹具翻转→机器人焊接→焊接停止,夹具翻转至取件位置→打开夹具→取件→补焊→校正→完成。
依照生产步骤,如时序图2所示,共耗时236秒。
时序图2
3)从以上时序图可发现,现代工艺在节约成本的基础上大大的提升生产效率,并且针对镀锌时工件的吊装姿态,对漏锌孔进行了改良,将所有的漏锌孔改至同一方向(如图3所示)。
如此,在镀锌时易于排锌,保证质量的同时减少了锌的残留,节约成本。
(图3.模组支架漏锌孔优化后)
4)现代加工工艺虽然在生产节拍上较占优势,但是在批量生产时,也存在一定的弊端。
因为机器人焊接轨迹是一定的,而矩形管在锯床下料时,存在一些不确定因素而导致所有零件尺寸并非一致,这就导致了偏差尺寸的零件与设定的焊接轨迹之间不吻合的矛盾,需人工补焊方可解决。
2.2主传动轴(扭管组合)加工工艺:
主传动轴的加工过程分为定位焊接、机器人焊接和人工补焊。
在此过程中要求加工时间的平衡,即t定位焊接=t机器人焊接=t人工补焊,以达生产效率最大化的目的。
以下具体介绍定位焊接、机器人焊接和人工补焊的生产工艺。
1)定位焊接
将所有的零件(见图2)装卡至定位焊接工装,并按照指定要求(见图4)进行定位点焊的过程称为定位焊接。
A.两端法兰板与扭管点焊位置B.轴管与扭管点焊位置
图4.主传动轴点焊位置示意图
(为点焊区域)
为了使机器人在焊接时不发生撞抢、粘丝以及避免定位焊缝与机器人焊接轨迹发生重合等情况,定位焊接时必须按照必须按照如图所示的位置进行点焊定位,定位焊缝一般10-15mm左右。
2)双机器人及变位机联动焊接
把定位焊接好的工件通过自行小车吊运至机器人焊接夹具,夹紧夹具并启动焊接程序,此时,变位机转动并通过制定的程序与双机器人之间联动配合焊接,这个过程就是双机器人和变位机的联动焊接。
三机联动在轴管处采用的对称焊接,不但生产效率快,而且使焊接所产生的拉压应力保持平衡,保证了两轴管的同心度。
在批量生产时,使产品质量得到了保证。
3)人工补焊
对上工序机器人焊接时有可能造成的漏焊、虚焊及定位焊接与机器人焊接衔接等情况进行检查并对不合格处进行补充焊接,以保证产品质量。
综上所述,现代机器人焊接工艺既有其优势,又存在一定的弊端。
但是在批量高效生产,追求效率的现代化企业,机器人代替人工焊接时必然趋势。
所以,怎样在缩短生产加工时间的同时能保证产品质量完全合格成为现在我们攻坚的课题。
在不久的将来,相信我们肯定会找到一种又快又好的生产工艺方法。
3、
工艺参数分析
3.1模组支架的工艺参数优化:
图5.模组支架主要工艺尺寸优化前
(“★”所示为关键尺寸,“☆”为优化尺寸,其余为重要尺寸。
)
图6.模组支架主要工艺尺寸优化后
根据实际生产情况,经反复多次试验得到(实验数据见表1)模组支撑架与模组梯形支架的最佳装配尺寸,即将尺寸927±
0.5优化为928±
0.5,如图6所示,并且对长槽钢与矩形管处焊缝的焊接顺序进行了调整(如图7所示)。
这样一来,一方面便于模组梯形支架的装配;
另一方面模组支撑架在焊接后1052.1±
0.5mm尺寸合格或微校正即可,保证了关键尺寸的精度,同时节约生产时间,提高产能。
机器人焊接轨迹调整前
机器人焊接轨迹调整后
图7.机器人焊接轨迹优化图
表1.模组支架的试验记录1
两矩形管长度一致
(尺寸1-尺寸5位置见图6)
表2模组支架的试验记录1
两矩形管长度不一致
由表1、表2(此处仅列部分数据)可知,焊接变形量最大处在尺寸1和尺寸4处槽钢2070的焊接变形。
结合实际情况,得知当矩形管尺寸在927.5-928.5mm范围内时,既满足装配尺寸的要求,又易于校正,降低劳动强度,提高了产能。
3.2扭矩管的工艺参数优化:
扭管在焊接时,两端法兰板处一般焊接变形量不大,可忽略不计;
但是在轴管的焊缝为两圆弧全面之间的焊缝,易产生焊缝虚焊、焊接变形导致两侧轴管不同心等情况,因此须采用对称焊摆动焊接,即将两台机器人焊接轨迹调整至对称状态,并在焊接程序中加上摆动焊接,以保证焊接完成后轴管两侧焊缝一致,提高产品合格率。
4、焊后矫正的方法
构件发生弯曲和扭曲变形的程度超过现行钢结构规范和设计要求时,必须进行矫正。
变形矫正的方法有:
机械矫正法、火焰矫正法和混合矫正法。
施工时,可以根据实际情况合理选用,矫正时要遵守以下原则:
先总体,后局部;
先主要,后次要;
先下部,后上部;
先主件,后副件。
其中机械与火焰矫正法分别为:
(1)机械矫正法:
所谓机械矫正法就是利用外力,使构件产生与焊接变形方向相反的塑性变形,与焊接变形相抵消,从而达到消除焊接变形的目的。
(2)火焰矫正法:
火焰矫正法是利用火焰在与焊接变形方向相反的对应部份局部加热产生压缩塑性变形,使较长的金属在冷却后收缩,来达到矫正变形的目的。
使用火焰矫正法的关键是正确选择加热位置和加热范围。
根据火焰矫正法加热时,有否采用水冷及水冷位置的不同,又可分为空冷、正冷和背冷三种。
空冷是指火焰加热时不用水冷的矫正方法;
正冷是在火焰加热面采用跟踪水冷的矫正方法;
而背冷则是指火焰加热时,在火焰加热背面采用跟踪水冷的矫正方法。
根据实际生产要求,本着以保护环境、降低生产成本和劳动强度及提高生产效率为目的,本单位选择以机械校正法为主对变形件进行校正。
五、结论
通过对机器人焊接的了解,以及机器人焊接在实际中的运用,掌握焊接变形规律,并在实践中总结出各类参数,在焊接前及焊接过程中采用一些预防性措施和科学合理的焊接工艺,避免一些不必要的焊后矫正工作,提高生产效率。
参考文献
[1]中国机械工程学会焊接学会主编《焊接手册——手工焊接与切割(第3版)》机械工业出版社,2003
[2]宋天民.焊接残余应力的产生与消除[M].北京:
中国石化出版社,2005
[3]方洪渊.焊接结构学[M].北京:
机械工业出版社,2008