135MW循环流化床锅炉设计特点及运行情况分析Word文档格式.docx
《135MW循环流化床锅炉设计特点及运行情况分析Word文档格式.docx》由会员分享,可在线阅读,更多相关《135MW循环流化床锅炉设计特点及运行情况分析Word文档格式.docx(14页珍藏版)》请在冰豆网上搜索。
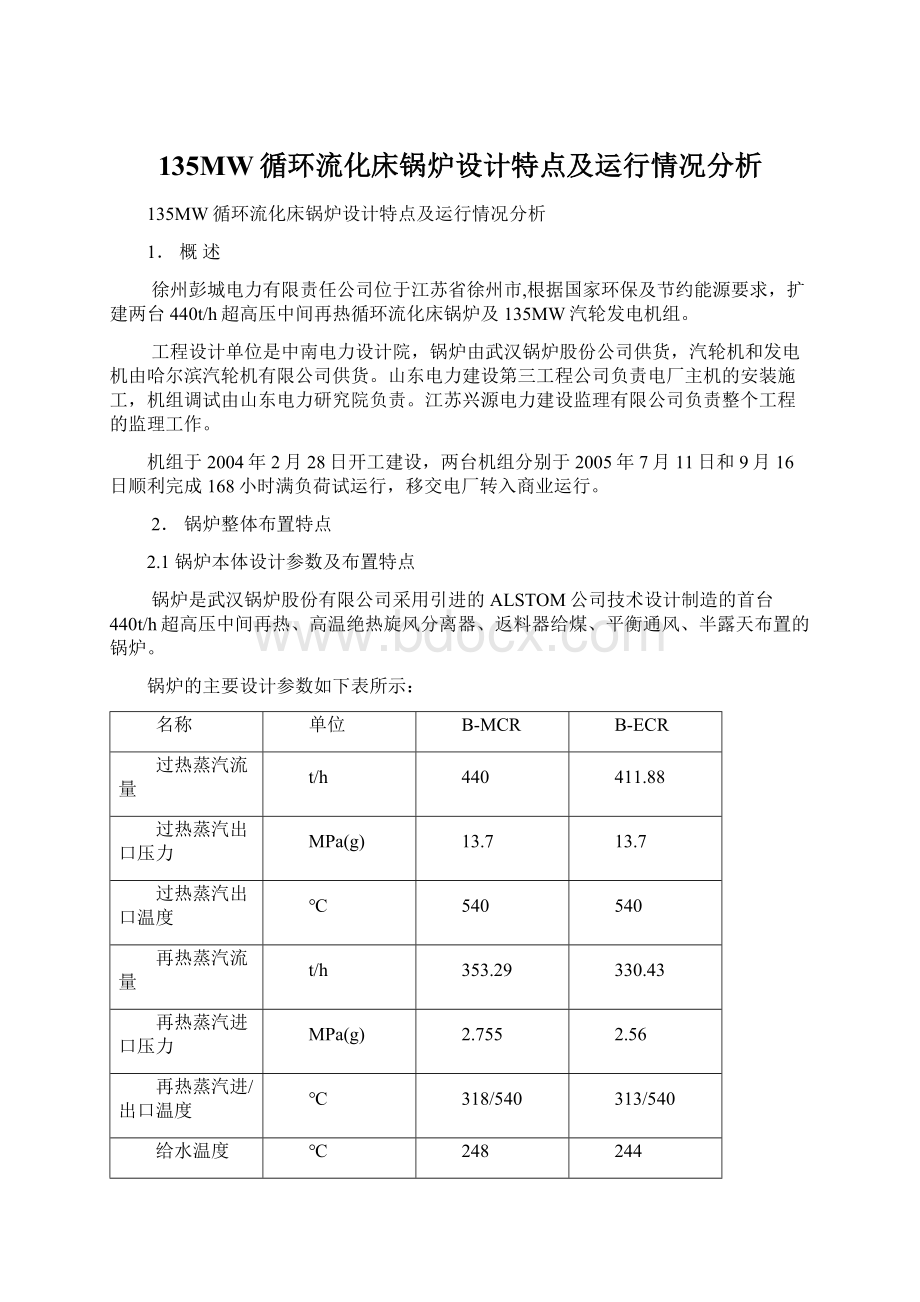
单位
设计煤种
校核煤种
全水份
Mt
%
5.5
5.50
收到基灰份
Aar
46.83
52.51
收到基挥发份
Var
19.23
17.28
收到基碳
Car
37.65
32.32
收到基氢
Har
2.80
2.57
收到基氮
Nar
0.69
0.60
收到基氧
Oar
5.89
5.94
全硫
Star
0.64
0.56
收到基低位发热量
Qnet.ar
Kcal/kg
3468
2968
锅炉与国产135MW高温超高压一次中间再热纯凝汽式汽轮发电机组相匹配。
锅炉由以下三部分组成:
(附图1)
第一部分为锅筒、炉膛及冷渣器。
炉膛采用全膜式水冷壁结构,炉膛内布置有一片双面水冷壁,炉膛前上部沿宽度方向还布置有屏式过热器和屏式再热器。
炉膛底部是水冷壁管弯制而成的水冷风室。
风室底部的点火风道内布置有床下点火燃烧器,炉膛下部密相区布置有床上启动燃烧器,用于锅炉启动点火和低负荷稳燃。
炉膛前墙布置流化床风水冷冷渣器,把渣冷却至150℃以下。
第二部分为炉膛与尾部烟道之间布置有两台高温绝热旋风分离器,每个旋风分离器下部布置一台非机械型分路回料装置。
回料装置将气固分离装置捕集下来的固体颗粒返送回炉膛,从而实现循环燃烧。
第三部分为尾部烟道及受热面。
尾部烟道中从上到下依次布置有过热器、再热器、省煤器和空气预热器。
过热器系统及再热器系统中设有喷水减温器。
管式空气预热器采用光管卧式布置。
锅炉整体呈左右对称布置,支吊在锅炉钢架上。
2.2锅炉岛系统布置特点
输煤系统:
原煤经两级破碎机破碎后,由皮带输送机送入炉前煤斗,合格的原煤从煤斗经二级给煤机,由锅炉返料斜腿进入炉膛燃烧。
床料加入系统:
启动床料经斗式提升机送入启动料斗,再通过输煤系统的给煤机,由锅炉返料斜腿进入炉膛。
一次风系统:
一次风经空预器加热成热风后分成两路,第一路直接进入炉膛底部水冷风室,第二路进入床下启动燃烧器。
二次风系统:
二次风共分四路,第一路未经预热的冷风作为给煤机密封用风,第二路经空预器加热成热风后分上、下行风箱进入炉膛,第三路热风作为落煤管输送风,第四路作为床上启动燃烧器用风。
返料器用风系统:
返料器输送风由单独的高压流化风机(罗茨风机)供应,配置为2x100%容量(一运一备)。
冷渣器用风系统:
冷渣器用风由单独的风机供应,配置为2x100%容量(一运一备)。
石灰石系统:
购买成品石灰石粉作为脱硫剂,采用气力输送的方式,由锅炉返料斜腿送入炉膛,配置2台高压流化风机(罗茨风机)作为石灰石系统风机。
除灰系统:
落入布袋除尘器灰斗中的粉尘借助气力输送系统送入灰仓。
除渣系统:
采用风水联合冷渣器,冷渣器排出的冷渣通过一级刮板输渣机、斗式提升机送入渣仓。
吹灰系统:
采用蒸汽吹灰。
在锅炉尾部烟道的对流受热面区域布置伸缩或固定式吹灰器。
3.锅炉本体设计特点
锅炉为武锅引进ALSTOM技术生产制造的首台135MW循环流化床锅炉。
同时,采用该技术生产的锅炉在中国国内已投运多台,针对上述项目在国内的运行情况,在本次锅炉设计过程中进行了局部优化设计,主要有以下几点:
3.1炉膛下部密相区耐磨层与水冷壁管过渡区域的防磨措施。
炉膛下部密相区耐磨层与水冷壁管过渡区域内由于沿壁面下流的颗粒与炉内向上运动的颗粒运动方向相反,因而在此处形成漩涡流,同时沿炉膛壁面下流的颗粒在交界区域产生流动方向的改变,因而对水冷壁产生磨损(见附图2)。
在本台锅炉的设计中,水冷壁管采用外让结构(见附图3),金属表面喷涂防磨材料,同时要求耐磨材料施工厂家,在耐磨材料施工中,严格按照锅炉厂设计要求,保证耐磨材料内表面与上部水冷壁管中心线平齐,避免颗粒在此处形成漩涡流,达到减轻磨损的目的。
采取了上述措施后,锅炉运行一年后,进行停炉检查,该区域水冷壁管基本未见磨损现象出现。
3.2炉膛内过热器屏及再热器屏的热有效系数的选取。
早期投运的锅炉在试运期间多次出现过热器、再热器超温爆管现象,测量发现,再热器管壁温度高达700℃左右,远高于设计值,管壁氧化涨粗现象严重。
分析认为是炉内屏面积布置过多,屏再、屏过吸热量偏大,同时,由于蒸汽流程或结构不合理,造成蒸汽流量偏差较大,使低流量管子得不到有效冷却而导致超温爆管。
针对上述现象,在本台锅炉的设计中,我们多次与ALSTOM公司相关人员展开讨论研究,分析认为国外循环流化床炉膛内多布置贯穿前后墙的Ω屏,而国内考虑到成本原因多采用平行前墙的L屏,ALSTOM公司认为L屏的换热低于Ω屏,而实际运行表明,两种型式屏的换热系数基本相同,根据上述情况,在我们的建议下,ALSTOM公司修改了设计导则,调整了炉内过热器屏、再热器屏的面积。
同时,优化了过热器(再热器)屏进出口集箱的引入引出形式,合理选择分配集箱和汇集集箱的规格,从蒸汽系统的连接方式及控制蒸汽流速出发,减小流量偏差;
经过上述调整,从锅炉运行情况来看,已完全消除了早期投运的135MW循环流化床锅炉普遍存在的过热器(再热器)超温现象。
3.3锅炉尾部烟道中省煤器的热有效系数的选取
目前国内已投运的同容量的循环流化床锅炉普遍存在排烟温度偏高的现象,而本工程配备的是布袋除尘器,相对于电除尘器来说,布袋除尘器对排烟温度更敏感。
若排烟温度高于180℃,将严重缩短布袋除尘器的使用寿命,布袋除尘器不能投入正常使用。
针对上述问题,我们与ALSTOM公司共同研究分析,认为国外循环流化床锅炉特别是ALSTOM-EVT公司设计的锅炉多燃用高水分的褐煤(水分35~58%,灰分1~40%,低位热值8~12MJ/kg),而国内由于政府政策的原因多燃用高灰分的劣质燃料,如本工程就是燃用的劣质烟煤(水分5.5%,灰分46.83%,低位热值14.52MJ/kg),因此,尾部烟道对流受热面特别是低温区域(省煤器、空预器)的积灰情况,存在较大差异。
在本台锅炉的设计中,对省煤器的受热面积进行了调整。
从目前的运行工况来看,达到了当初的设想。
但如果吹灰器不投入运行的情况下,锅炉排烟温度会高于设计值。
3.4布风板风帽的型式
布风装置结构和尺寸是否合理直接决定着流化床内物料的流化质量,从而影响锅炉的点火、运行,锅炉的燃烧、负荷特性,以及锅炉的安全性和经济性。
本工程采用的是大直径钟罩式风帽(附图4),风帽由内管和外罩两部分组成,合理设计内管开孔尺寸及数量使布风板具有合理的阻力特性。
风帽外罩采用水平开孔且孔径较大,因此不易被颗粒堵塞;
风帽采用高合金耐热钢精铸而成,使用寿命长;
风帽数量少,易于检修。
钟罩式风帽特有的结构布置有效的防止物料落入风室运行表明,钟罩式风帽充分满足了循环流化床锅炉流化的要求。
3.5风水联合式冷渣器的优化设计
锅炉装有风水联合式冷渣器(见附图5)。
锅炉炉膛的底渣通过炉底排渣口进入冷渣器,被流化风及水冷管束冷却到150℃以下溢流排渣到排渣系统。
该冷渣器对煤种的适应性强,运行稳定,进渣量大时溢流量增加,进渣量小时溢流量也随之减少。
风水联合冷渣器从理论上来讲是非常先进的,首先它能将进入冷渣器的细粒子直接送回炉膛,提高床内细物料的保有量及细粒子的停留时间,提高锅炉的燃烧效率,同时又能将热渣的物理热量充分吸收。
实际运行情况是国外的电厂大多运行良好,而在国内的应用中出现了很多问题,仅个别电厂运行较正常。
主要问题是当排渣颗粒偏大时,热渣较难进入冷渣器;
而进入的大颗粒热渣又流化不好,只好被迫加大流化风量,从而造成冷渣器内部管式受热面磨损加剧。
造成上述现象的主要原因是我国没有严格的配煤制度,燃煤的粒度仅仅依靠电厂的2级破碎是难以满足设计要求,煤中大颗粒偏多,导致冷渣器不能正常运行,正常排渣口排渣量偏少,需经常开启事故排渣况排放大渣。
针对上述问题,在冷渣器的设计上,我们主要从以下几方面着手提高运行可靠性:
1.在保证受热面不出现磨损加剧的前提下,适当提高流化速度;
2.将正常排渣口由溢流排渣改为下部排渣,保持排渣顺畅;
3.采用微倾斜布风板,且对隔墙结构和排渣口结构进行改进设计,同时根据大渣的粒度情况,定期排放大渣,防止堵塞;
4.在冷渣器的进渣口和空仓,增加吹扫空气管,防止堵塞。
经过上述调整,目前冷渣器均能正常运行,锅炉运行一年来没有出现由于冷渣器排渣不畅原因造成的非计划停炉。
4.锅炉整套启动过程中出现的问题及解决措施
锅炉于2005年6月19日开始整套点火启动,7月11日机组完成168小时试运行,并移交试生产。
锅炉运行主要技术数据见下表:
设计值
工况一
工况二
工况三
锅炉状况
吹灰后
高加切除
汽水系统
机组电功率
MW
135
136.1
132
138
给水流量
405.2/403.6
373/372.1
401.1/400.2
SH喷水量
23.16
10.7/20.1
23.7/25.0
17.6/19.6
RH中间喷水
3.48
3.8/1.6
4.7/4.8
4.6/1.5
Eco入口温度
°
C
241.9
164.3
246.3
SH3出口温度
534.9/533.8
543.5/531.3
535/537
RH1入口温度
313
312.1/230.1
240.7/347.4
248.5/229.8
RH2出口温度
529.1/530.7
531.6/534.9
533.9/539.4
Eco入口压力
MPa
15.45
14.4
14.7
SH3出口压力
12.9
12.5
13.3
RH1入口压力
2.6/2.7
2.7/2.8
2.7
RH2出口压力
2.565
2.5
2.6
烟气系统
炉膛下部平均温度
854
869
886
873
TAPH出口温度
154/157
137/144
154/148
布风板上部压力
kPa
8
7.83
7.72
7.74
分离器入口压力
-0.2
-0.67/-0.73
-0.6/-0.42
-0.9
TAPH后压力
-3.6
-3.29/-3.30
-2.82/-2.80
-3.42/-3.39
空气系统
总空气量
kNm3/h
404.52
385.7
413.55
408.16
一次风量
201.99
184.99
229.14
220.16
水冷风室压力
KPa
14
15.8
15.2
返料母管压力
42
35.6
36
37.3
含氧量
%wet
3.5
4.0/4.4
5.3/4.3
煤系统
1#给煤线
45.96
53.5
38.7/73.2
51.3
2#给煤线
53
41.6
锅炉整套启动过程中的运行情况表明,锅炉性能优越,机组功率达到135MW以上,主要运行参数均达到设计保证值,但在运行过程中也暴露了一些循环流化床锅炉特有的问题,主要表现在以下几个方面:
4.1锅炉点火过程中床层压力的控制
根据设计要求,锅炉炉膛静止床层厚度在0.8~1.0m。
床料太厚,则加热引燃时间增加,加热不均。
床料太厚,则不稳定,易吹穿,引起结焦、布风不均。
启动过程中应控制炉膛布风板压力为8KPa,水冷风室压力为14KPa。
而在锅炉整套启动初期,运行人员实际控制的压力均偏高,在炉膛内保持着较高的床料蓄积量,导致炉膛床温上升缓慢,特别是升温后期,床温上升非常困难,现场观察在床上、床下油枪全投的情况下,温升速度在2~3℃/小时。
采取措施:
加大排渣量,将炉膛布风板压力降低到设计值,同时,在保证炉膛充分流化及燃烧的条件下,降低一、二次风量。
通过采取上述措施,炉膛温升速度明显提高。
4.2锅炉投煤温度的选择
向炉内初次投煤的最低允许床温(简称允许投煤温度)是一个关键参数,该值定得太低,会造成煤粒着火不稳定,甚至引起爆燃、结焦等不安全现象产生;
若该值定得过高,则点火设备容量要加大,点火用油量增加,经济性差。
ALSTOM公司规定:
锅炉允许投煤温度应根据试验台的试验结果给出推荐值,最终在机组试运行期间由调试单位会同ALSTOM公司、业主共同确定。
锅炉投煤温度随燃煤挥发份的增加而降低,而ALSTOM公司的推荐值明显高于国内实际运行值(附图6)。
主要原因在于:
ALSTOM公司将投煤温度定得较高,以确保有足够的点火能量支持,投入给煤机后就连续给煤运行。
而国内是将投煤温度定得较低,通过数次断续给煤,试点火的方式不断升高床温,然后转入连续给煤。
后一种点火方式既能节省点火用油,又可减小点火设备的容量,而前种点火方式操作较简单和安全,缺点是点火油耗较大。
ALSTOM公司认为投煤后,应确保煤能尽快着火燃烧,迅速提高床温,做到先补煤再退油枪,尽量避免长时间的油煤混烧,有条件的话,尽早退出油枪运行。
投煤时一旦发现床温降低、氧量不变,说明煤未着火,此时,应立即停煤。
实际运行过程中,电厂为缩短启动时间,降低启动燃油消耗量,开始是间断点动投煤。
此时应特别注意点动投煤量不能多,投煤后密切监视床温及氧量的变化,一旦发现未着火,立即停止给煤。
4.3锅炉部分负荷时汽温的控制
锅炉在启动过程中,屏过、屏再出口工质温度高于设计值,尤其是半负荷时,实际减温水量远大于设计值。
实际操作中通过调整运行方式,加减负荷时适当缓慢些,避免大起大落。
在低负荷区,适当提升主汽压和减温水压力,利用主给水闸阀适当节流,再根据汽压由汽机侧增加负荷。
其原因初步分析为:
由于炉膛布置有屏式受热面,锅炉在低负荷时,炉膛内循环物料浓度较低,传热系数中辐射份额较大,屏式过热器的传热系数比炉膛壁面的略高,而高负荷时,随着炉膛内循环物料浓度的升高,传热系数中对流份额增加,屏式过热器的传热系数会比炉膛壁面略低。
而锅炉设计中屏式过热器面积是按BMCR工况下进行的,因此在锅炉启动过程中,特别是在半负荷时,会出现过热器超温现象。
建议在以后的炉膛内屏式受热面积及减温水量的选取上作适当调整。
4.5锅炉部分负荷时负荷调整的要求
锅炉在负荷调整过程中,返料立管压力曾出现过脉动。
具体表现为:
当负荷增加时,返料立管压力迅速升高,温度下降,由于返料器背压增高,返料风送不进,整个返料风管道剧烈晃动,严重威胁锅炉安全运行,锅炉被迫降低负荷,负荷降低后上述现象会突然消失,整个返料系统恢复正常。
与ALSTOM公司调试人员交流上述现象后认为:
锅炉在低负荷运行时,由于分离器中的烟气速度较低,在分离器锥段部分存在积灰现象,积灰到一定高度后,大量细灰会突然落入返料器,造成返料器堵塞。
当负荷降低,返料器与炉膛差压增大,当差压增大到一定程度后,会冲开受堵的返料器,系统恢复正常。
因此,锅炉在低负荷运行过程中,应保证负荷的平稳上升或下降,严格禁止负荷的大起大落。
5.锅炉消缺过程中发现的问题及解决措施
在锅炉通过试运行后的停炉消缺过程中,主要有以下几个影响锅炉安全稳定运行的问题。
5.1煤仓堵煤断煤问题
锅炉运行过程中,煤仓的事故率很高,煤仓的堵塞时有发生。
分析其原因,主要原因为煤仓的设计参照链条炉设计。
成品煤堆积在锥形煤仓内受到煤的挤压,使煤粒之间、煤粒与煤仓壁之间产生摩擦力,越接近下煤口,其摩擦力及挤压力越大。
其中,煤粒间的摩擦力呈双曲线形增大。
所以在靠近下煤口处的煤易搭桥,另一个原因为,由于结构设计原因,煤仓内直接受给煤冲击处的衬板易脱落,导致煤仓出口堵塞。
最终,电厂在煤仓受给煤直接冲击处内衬由超高分子聚乙烯衬板改为不锈钢板,同时煤仓下部加装空气炮,使得煤能够顺利进入给煤机,另外严格控制入炉煤外在水分,加大燃煤存放时间和外来煤调配,防止水分超高的湿煤进入煤仓。
5.2分离器后燃现象
对于循环流化床锅炉,分离器后燃现象普遍存在,运行中也是允许的。
分离器后燃主要是由于炉膛燃烧产生的烟气中携带大量未能完全燃烧的焦炭和CO,进入分离器后,在旋转分离过程中与氧气强烈混合而得以继续燃烧。
在现场运行中我们发现:
锅炉稳定在138MW负荷,氧量在4.8%时,分离器平均烟气温升为16.5℃。
由于尾部烟道入口温度的升高,影响锅炉主循环回路和尾部对流烟道热量分配,造成过热器、再热器喷水量的增加。
5.3炉膛内屏的变形问题
停炉检查时发现炉膛内过热屏、再热屏沿高度方向发生变形,再热屏比过热屏严重。
经调研发现,采用相同结构的同类型锅炉均出现相同问题。
过热屏、再热屏的布置型式见附图7,屏下端与前墙水冷壁固结在一起,屏上端通过衡力弹簧吊架悬吊在锅炉顶板上,屏上部穿炉顶处采用柔性膨胀节密封。
具体数据见下表:
水冷壁管
过热器屏
再热器屏
材质
20G
12Cr1MoV
TP304H
高度(m)
24.5
平均壁温(℃)
403
492
535
线膨胀系数(x10-6℃-1)
13.83
14.15
18.9
膨胀差(mm)
35
112
分析认为:
由于水冷壁与管屏存在膨胀差,屏的高度较大,刚性弱,同时整个管屏采用悬吊结构,中间无固定结构,因此,下部的膨胀量很难向上传递,屏的膨胀受阻,导致屏受热变形。
再热器采用奥氏体材料,膨胀量大,变形更严重。
采取的措施:
目前密切监视屏的变形情况,若有扩大趋势,建议进行喷涂处理,提高管屏抗磨能力。
6.循环流化床锅炉系统选型的几点体会
通过该台锅炉的成功试运行,对循环流化床锅炉的系统配置有了更新的认识,主要体现在以下几个方面:
6.1给煤方式的选择
目前循环流化床锅炉存在两种给煤方式:
返料器给煤和前墙给煤。
煤仓通常设置在锅炉前部,返料器给煤一般要采用二级给煤。
第一级采用称重式密封皮带给煤机,第二级采用埋刮板式给煤机。
而前墙给煤一般仅布置一级称重式密封皮带给煤机。
ALSTOM公司采用返料器给煤,该给煤方式可实现对燃料的提前干燥预热,对混合着火有力。
根据目前国内循环流化床锅炉运行情况表明,两种给煤方式对煤颗粒的混合过程及燃烧过程的影响甚微,而电厂普遍关心的是给煤的可靠性。
因此,前墙给煤因其系统简单可靠正被越来越多的用户所接受。
6.2燃煤粒度的控制
根据ALSTOM公司对循环流化床锅炉的性能研究认为:
分离器并不是影响循环流率的唯一参数,煤的破碎粒径对它会有影响。
在100μm范围内,除了分离器效率外,煤的粒径分布以及煤灰、石灰石的成灰特性、磨损特性均对循环流率有重要影响。
因此,要求入炉煤的颗粒有一定范围,颗粒级配有合理的比例,而国内大多数电厂所配备的破碎设备难以保证锅炉制造厂家要求的燃煤粒径,特别是不合格的大颗粒在炉内的沉积影响正常流化,风帽磨损严重,堵塞风水联合冷渣器。
下表是本工程燃煤粒径分布:
实际值
D50
Mm
1.8
0.6
最大尺寸
6
10
>5mm
2
9.43
>2mm
46
25.39
>1mm
74
39.48
>0.63mm
83
49.53
>0.09mm
95
83.81
从上表可以看出:
入炉煤粒度严重偏离设计值,大颗粒明显偏大。
目前,电厂对二级破碎设备进行调整,严格控制大颗粒进入炉膛,以防止风水联合式冷渣器结焦停炉。
6.3冷渣器选型
冷渣器的型式根据冷却原理分为机械式和非机械式两种。
其中机械式冷渣器的主要形式有水冷绞笼式、水冷滚筒式以及高强钢带式等,非机械式主要以流化床式为代表。
流化床风水联合冷渣器由于容量大,在国内中大型流化床中得到普遍应用。
风水联合冷渣器只要控制好入炉煤粒度,正确运用,是完全能够满足锅炉排渣要求,同时,风水联合冷渣器能够接受的原煤粒度,也是保证循环流化床锅炉能较好运行的基本原煤粒度。
7.结论
(1)锅炉顺利通过168小时满负荷试运行,各项指标达到国家试运优良标准,受到专家好评,一致认为该机组在同类机组试运时间最短、停机次数最少、耗油最少、运行最稳定的循环流化床机组,创国内同类机组的先进水平。
(2)锅炉能够满负荷长期连续稳定运行。
负荷适应能力强,可在40~138MW范围内全燃煤运行。
煤种的适应性强,可稳定燃用Qnet.ar为14.6~21MJ/kg的煤种。
(3)经优化设计的风水联合冷渣器效果显著,能够满足多煤种工况下锅炉的运行要求。
(4)由于实际燃用煤种与设计煤种存在差异、传热量分配、系统串风和吹灰器未正常工作等原因,锅炉目前的排烟温度高于设计值,需进一步研究解决。
(5)锅炉目前已投运一年多时间,我们仍需对燃煤煤质、给煤、冷渣和防磨等方面予以关注。