北科大济钢生产实习报告Word格式文档下载.docx
《北科大济钢生产实习报告Word格式文档下载.docx》由会员分享,可在线阅读,更多相关《北科大济钢生产实习报告Word格式文档下载.docx(35页珍藏版)》请在冰豆网上搜索。
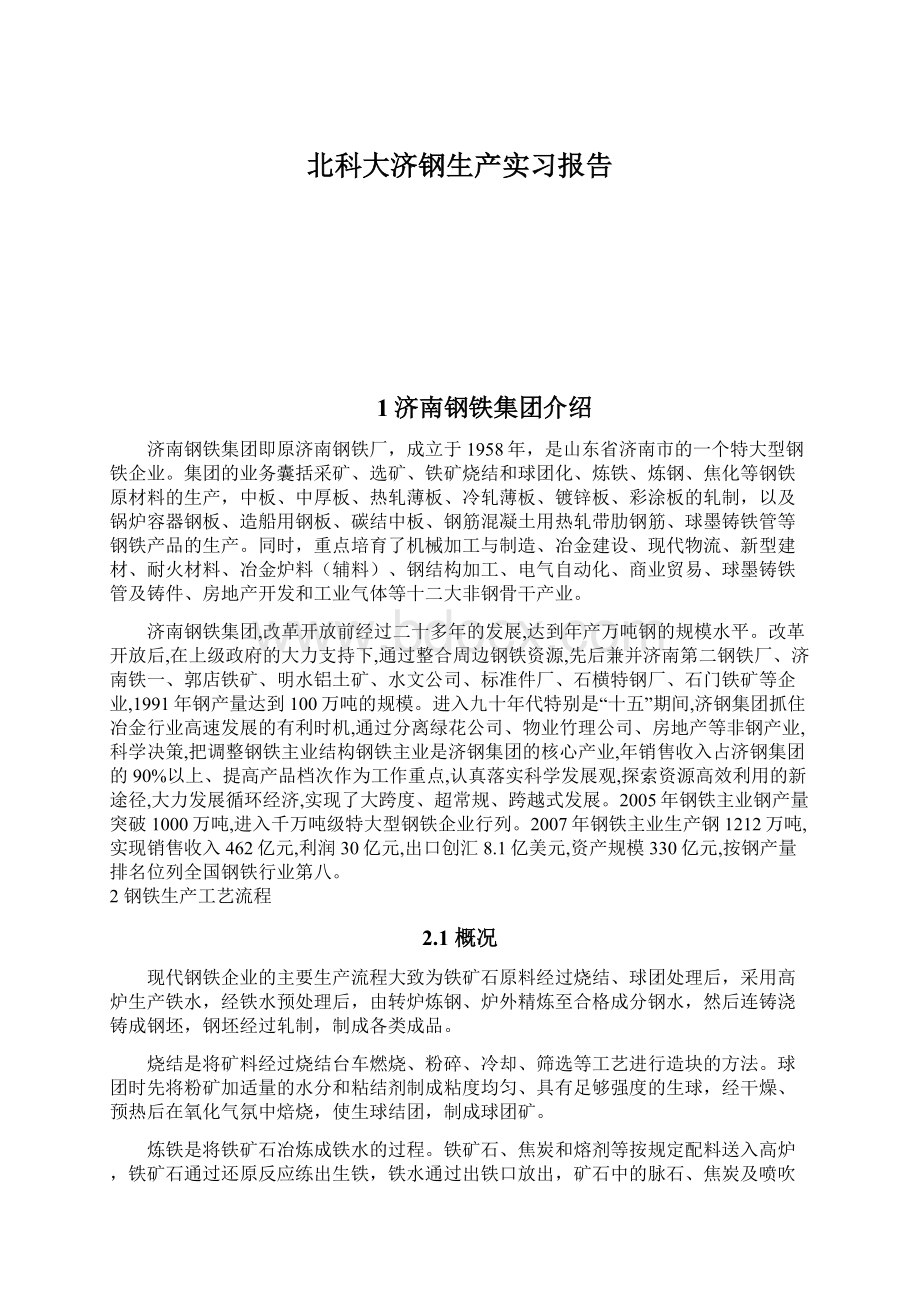
烧结就是将准备好矿粉/中和料、固体燃料、熔剂,按照一定比例进行配料,然后再配入一部分烧结整粒系统筛分返回的返矿,通过皮带送到圆筒混合机加水润湿、混匀和制粒,便得到可以烧结的混合料。
混合料由布料器铺到烧结台车上进行点火烧结。
烧结过程是靠抽风机从上向下抽进空气,燃烧混合料层中的燃料,自上而下不断进行。
烧成的烧结矿,经单辊破碎机破碎后进入带式/环式冷却机,然后进入整粒系统;
筛上物进入成品皮带送往高炉或者作为铺底料循环使用,筛下物为返矿,进入配料室重新烧结。
1)烧结用料
A.含铁原料:
铁矿粉是烧结生产的主要原料,其物理化学性质对烧结矿质量影响很大,主要要求铁矿石品位高、成分稳定,杂质少,脉石成分适用于造渣,粒度适宜。
烧结用的精矿粉粒度不宜太细,一般小于0.074mm的比例小于80%。
褐铁矿、菱铁矿的精粉或粉矿要考虑结晶水、二氧化碳的烧损。
国内褐铁矿的烧损为9-15%,菱铁矿烧损为17-36%,烧损大较高。
当含铁量低于35%时,需进行选矿处理。
菱铁矿化学成分为FeCO3,常见的菱铁矿致密坚硬,外表呈灰色或黄褐色,风化后转变为深黑色,有玻璃光泽,无磁性。
菱铁矿在造块时,因收缩量大,导致产品强度降低和设备生产能力低,燃耗也因碳酸盐分解而增加。
B.溶剂:
碱性氧化物(CaO+MgO)含量要高,而酸性氧化物(SiO2+Al2O3)含量要低。
质量良好的熔剂中,SiO2+Al2O3的含量一般不超过3.5%。
熔剂中的有害杂质S、P要低,含硫一般为0.01-0.08%,含磷一般为0.01-0.03%。
从目前生产条件来看,熔剂粒度一般控制在3mm以下,且粒度小于3mm的比例应大于90%。
若在烧结厂内破碎块状石灰石、白云石时,要求其进厂的粒度上限为80mm。
石灰石、白云石含水以1-3%为宜,消石灰含水一般不应超过15-20%。
水分过大,会给运输和破碎带来困难。
:
C.燃料:
要求固定碳含量高,灰分、挥发分、硫含量低。
灰分含量低,可以减少熔剂用量;
挥发分含量低,可以防止挥发物挥发时在温度较低的地方凝结下来,恶化料层透气性及黏附在抽风机翼板上,影响烧结作业的正常进行。
一般规定挥发分含量不应超过8%;
硫含量低,可以减少烧结矿中的硫含量,提高烧结矿质量。
燃料入厂粒度一般应小于25mm,在烧结厂进行破碎,破碎后一般粒度应控制在3mm以下。
研究表明,燃料最合适的粒度为0.5-3mm。
从经济角度出发,烧结厂一般只控制粒度上限,即合适的粒度范围为0-3mm。
2)配料方法
A.质量配料法:
质量配料法是按照原料的质量进行配料的一种方法。
其主要装置是皮带电子秤、自动控制调节系统、调速圆盘给料机。
配料时,每个料仓配料圆盘下的皮带电子秤发出瞬时送料量信号,此信号输入调速圆盘自动调节系统,调节部分即根据给定值信号与电子皮带秤测量值信号的偏差,自动调节圆盘转速,达到所要求的给料量。
B.化学配料法:
目前,国外已经有按化学成分配料的方法,这是在质量配料法基础上发展起来的一种较为理想的配料方法。
它借助于连续X射线荧光、光谱分析仪分析配合料的化学成分,并通过计算机来控制其化学成分的波动。
用此方法配料,烧结矿碱度波动范围降低到±
0.035。
3)工艺流程图如图2.2
图2.2烧结生产工艺流程图
4)烧结系统组成
A.溶剂上料系统:
运输和接受熔剂进入烧结机系统配料室料仓,其控制与相关的设备联动,根据各配料仓的料位信号,控制配料仓来料设备的启停,达到控制各配料仓的料位和储存量的目的。
B.燃料上料系统:
把通过汽车运送来的烧结使用的燃料,运送至燃料储料仓,再根据料位情况以及生产需要运送至烧结配料室
C.配料、混合系统:
把烧结所需要的各种含铁原料、燃料、熔剂等物料按一定配比进行配料,然后加水、混合、造球等工序,最后成为符合生产要求的混合料。
D.烧结、冷却系统:
把混合料布入烧结机,然后点火,烧结,经过热破碎,直接进环冷机把烧结矿冷却到一定温度的过程。
E.烧结矿整粒系统:
把冷却后的烧结矿,经过筛分分级成不同要求粒级物料,进入成品矿槽储存的生产过程。
F.铺底料系统:
把整粒二次筛分出的铺底料经皮带机倒运至铺底料矿槽,并通过皮带机的启、停来控制铺底料矿槽料位。
G.返矿系统:
把外返矿和整粒系统筛分出的内返矿经皮带机转运至配料室内的返矿仓,并依据返矿配料仓料位来控制外返皮带机的开停。
H.散料系统:
主要是把烧结机的散料集中起来,运至烧结矿筛分系统。
I.烧结-高炉上料系统:
主要是把生产的烧结矿或外送的烧结矿通过成品-7皮带机运送至高炉的上料过程。
2.2.2球团
球团就是将细磨铁精矿粉或其它含铁粉料添加少量粘结剂(膨润土)和熔剂混合后,在加水润湿的条件下,通过造球机滚动成球(8-15mm),再经过干燥、焙烧、固结、冷却筛分,成为具有一定强度和冶金性能的球型含铁原料。
1)生产工艺流程
球团矿是将精矿粉、熔剂(有时还有粘结剂和燃料)的混合物,在造球机中滚成直径8~15mm(用于炼钢则要大些)的生球,然后干燥、焙烧,固结成型,成为具有良好冶金性质的优良含铁原料,供给钢铁冶炼需要。
球团法生产的主要工序包括原料准备、配料、混合、造球、干燥和焙烧、冷却、成品和返矿处理等工序。
球团矿生产的原料主要是精矿粉和若干添加剂,如果用固体燃料焙烧则还有煤粉或焦粉。
这些原料进厂后都要经过准备处理,它包括:
所有原料的混匀;
将添加物磨碎到足够的细度;
将精矿粉(或富矿粉)磨碎到-200网目大于70%,上限不超过0.2mm;
将固体燃料破碎到小于0.5mm;
精矿粉中的水分过多时要进行干燥处理;
经过筛分粒度过大的还要重新进行破碎、磨碎处理。
经过上述准备处理的原料,在配料皮带上进行配料;
将配料后的混合料与经过磨碎的返矿一起,装入圆筒混合机内加水混合。
混合好的料再加到圆盘造球机上造球,造球时还要加适量的水。
生球焙烧前要进行筛分,筛出的粉末返回造球盘上重新造球。
用固体燃料焙烧时,生球加到焙烧机以前,其表面滚附一层固体燃料。
这样制成的生球用给料机加到焙烧设备上进行焙烧。
焙烧好的球团要进行冷却,冷却后的球团矿经筛分分成成品矿(>
10mm)、垫底料(5~10mm)、返矿(<
5mm),垫底料直接加到焙烧机上,返矿经过磨碎(至<
0.5mm)后再参加混料和造球。
目前主要的几种球团焙烧方法:
竖炉焙烧球团、带式焙烧机焙烧球团、链箅机一回转窑焙烧球团。
竖炉焙烧法采用最早,但由于这种方法本身固有的缺点而发展缓慢。
目前采用最多的是带式焙烧机法,60%以上的球团矿是用带式焙烧机法焙烧的。
链箅机一回转窑法出现较晚,但由于它具有一系列的优点,所以发展较快,今后很可能成为主要的球团矿焙烧法。
球团工艺流程图如图2.3
图2.3球团生产工艺流程图
2.2.3高炉炼铁
1)高炉冶炼工艺过程概述
高炉冶炼是一个非常复杂的物理化学过程。
通过炉缸上部风口鼓进的热风燃烧从高炉上部下来的焦炭和从风口喷入炉缸的煤粉,产生高温(理论燃烧温度在2000~2300℃左右)(初始)煤气,形成风口回旋区。
高温煤气向上运动。
从炉顶装入的矿石和焦炭,在重力作用下向下运动,被上升的煤气加热并逐步还原。
矿石在下降过程中随温度升高逐步软熔并被还原为液体初渣和铁滴,形成所谓的软熔带和滴落带。
初渣和铁滴在下降、最终进入炉缸的过程中进一步被还原为终渣和铁水。
另有非铁元素还原。
终渣和铁水从铁口排出。
煤气从炉顶上升管经过煤气处理系统除尘和降温后进入煤气总管。
2)高炉结构如图3.4所示
图2.4高炉结构图
3)高炉工艺流程
A.热风炉工艺流程
提高风温能够增加鼓风带入的物理热,提升焦炭燃烧率,降低焦比、提升鼓风动能,达到提升产量、改善生铁质量的目的,同时有利于喷吹煤粉的燃烧,提升煤粉的燃烧率。
卡鲁金热风炉实质上是一个热交换器,助燃空气与煤气经预热器预热后分别送入空气集气室和煤气集气室,在燃烧器空气喷嘴和煤气喷嘴喷射而出,气体混匀后进入预燃室,在格子砖上部完全燃烧产生高温烟气,高温烟气流自上而下经格子砖(蓄热室)将格子砖加热而本身逐渐冷却,低温烟气经地上烟道进入空气、煤气预热器,而后进入烟囱排出,格子砖被加热并贮备一定热量到规定条件(拱顶温度<
1450℃,废气温<
450℃)停止烧炉,换炉转送风,冷风从冷风阀进入热风炉经格子砖自下而上流动,被加热后送高炉,随格子砖温度降低,热风温度下降,当低于规定热风温度时停止送风,再转入烧炉,热风炉周期性工作。
正常情况下,采用两烧一送工作制度,即两座热风炉燃烧,一座热风炉送风,每座热风炉送风与燃烧交替进行。
热风炉正常换炉由计算机自动控制,各热风炉按规定顺序自动切换,各阀门也按规定的顺序自动转换。
B.喷煤工艺流程
喷煤的主要任务是,把原煤制成煤粉喷入高炉来代替焦炭,使高炉大幅度降低焦炭消耗,是降低生铁成本的重要手段,是炼铁系统结构优化的中心环节,提高高炉的竞争力。
天车把晾干后的原煤抓入异型煤仓,经给煤机、原煤皮带、原煤振筛、筛后进入原煤仓,原煤由原煤仓经密封皮带给料机可控地送到中速磨煤机磨成合格煤粉[-200目(0.074mm)占75%以上],由干燥(输送)气体将煤粉送到袋式收尘器,煤粉由布袋式除尘器收集后,经叶轮给料机、煤粉振动筛、将煤粉送入煤粉仓中,从而完成煤粉加工过程。
煤粉仓下部通过落粉管、软连接,气动圆顶阀和喷吹罐相连。
采用二~三个喷吹罐并列布置,煤粉仓内被流化的煤粉靠重力落入喷吹罐。
每喷吹一罐均装煤粉,加压、等待。
运行罐将要喷完之前,备用罐自动投入,以保证高炉连续均匀喷吹煤粉。
喷吹罐上部有氮气加压,罐下部用氮气流化,被流化的煤粉通过导出管排出罐外至补气器,在此加入二次风进行输送,送到高炉平台上的分配器中,经过喷吹支管由喷枪将煤粉送到高炉的每一个风口喷入高炉。
喷吹罐喷吹结束后,进行卸压,以便再从煤粉仓接受煤粉。
卸压气体通过卸压管道将罐内气体排入泄压布袋箱。
进入泄压布袋箱的气体通过卸压放散布袋排放,泄压布袋箱收集的煤粉,通过落粉管落入煤粉仓。
C.高炉煤气干法除尘及TRT工艺流程
高炉煤气净化采用干式布袋除尘器,其工艺过程是由高炉生产过程产生的高炉煤气经旋旋风(重力)除尘器除尘后,由荒煤气主管分配到呈二列式布置的布袋除尘器箱体内。
除尘器过滤方式采用外滤式,煤气进入除尘器荒煤气室后,煤气中颗粒较大的粉尘由于重力作用自然沉降而进入灰斗,颗粒较小的粉尘随煤气上升,经过布袋时,被阻留在布袋的外表面,煤气得到净化。
净化后的煤气进入净煤气室,由出气支管汇总到净煤气管道,然后经过减压阀组或TRT、消音器,喷水降温装置进入公司净煤气管网。
在荒煤气主管道处设置了可调事故放散,同时为满足环保要求对放散的荒煤气进行点火放散。
TRT发电系统在减压阀组前把高炉煤气引出,经过入口阀门后进入透平机入口,通过导流器使气体转成轴向进入叶栅,气体在动叶栅和静叶栅组成的通道中不断膨胀做功,压力和温度逐级降低,并转化为动能作用于工作轮使之旋转,工作轮通过联轴器带动发电机一起转动而发电。
叶栅出口的气体,经过扩压器进行扩压,以提高其背压达到一定值,然后经排气蜗壳流出透平,经过出口阀门经过喷水降温后与高炉净煤气管线汇合,供给用户。
D.冲渣工艺流程
高炉渣处理是把高炉生产的副产品熔渣进行水淬处理形成水渣的工艺过程。
高炉正常生产时,铁口熔渣经渣沟,流至冲渣水沟,熔渣与冲渣水接触进行冷却水淬。
然后落入粒化塔,后经水渣沟进入脱水器进行渣水分离,水渣则由脱水器内的受渣溜槽滑落至皮带,通过皮带输送机把成品粒化渣直接输送到渣场。
脱水器脱下的水经回水沟流回循环水池进行循环使用,水中含有的水渣沉淀后用天车抓取放置皮带机上方的受料斗,经皮带机输送到渣场储存外运。
3200高炉冲渣布局分南北两侧,每侧各有一个粒化塔、两套脱水器、一个干渣坑、一套独立的循环水池及泵房、操作室。
南侧脱水器分离的水渣由渣-1、3、4、5、6皮带机输送到渣场储存外运;
北侧脱水器分离的水渣由渣-2、4、5、6皮带机输送到渣场储存外运。
E.高炉供料工艺流程
高炉供料系统设备主要由皮带机、受料斗、卸料车等设备组成,全部自动化集中控制,正常情况下皮带的启停、上料系统的运行及卸料车行走全部在操作室完成。
供料主要任务是负责高炉生产所需各种原、燃物料的供应。
通过皮带机、转运站、卸料车将焦炭、球团矿、烧结矿、块矿分别从煤焦区域、烧结区域、综合料场输送至高炉的指定料槽;
在焦炭、球团、烧结矿不能正常供应的情况下,通过汽车运至各料场,经汽车受料斗通过皮带机、转运站、卸料车送至高炉的料槽。
在上料过程中岗位人员要严格关注各皮带机上所上料种及料的质量,确保不上错料、不混料,按要求保证高炉料槽中各原燃料的料位,确保无错料、无混料、无空料、料中无杂物。
4)高炉炼铁生产工艺流程图
图2.5高炉炼铁生产工艺流程
2.3炼钢及主要产品的生产工艺
2.3.1转炉炼钢
1)概述
转炉炼钢,即以铁水为主要原料,在转炉内,通过吹入氧化剂——氧气,将铁水中的杂质元素硅、碳、锰、硫、磷等氧化成各类氧气物,形成钢渣或气体后脱除,得到较纯净钢水的过程。
转炉炼钢是一个氧化过程。
以往从铁水到钢水的生产过程中,主要是高炉铁水→转炉炼钢→连铸(铸造)→钢坯,但随着对钢材新功能的不断开发,所要求的钢水洁净度也越来越高,硫、磷、碳、氢、氧、氮等含量要求越来越低,因此,目前普遍采用的新流程为高炉铁水→铁水预处理→转炉炼钢→炉外精炼→连铸→连铸坯。
图2.6转炉炼钢生产工艺流程
2)铁水预处理
为了减轻转炉工作任务,提高转炉的冶炼效率,降低转炉冶炼成本,将原来需要在转炉内完成的部分任务(脱S、脱P、脱Si)移到转炉外进行,这个过程称为铁水预处理。
先进的钢厂铁水预处理的比例可达到90%-100%。
铁水预处理主要过程:
以铁水脱硫为例,利用喷枪等设备,将脱硫粉剂碳化钙、石灰、镁粉等喷入装有铁水的鱼雷罐车或喷粉罐等,脱硫剂有效成分与铁水中的硫反应,生成CaS、MgS等固体渣,浮在铁水上面,扒出,从而达到脱硫的目的。
3)转炉炼钢
转炉炼钢的目的是降低铁水中的碳(生铁的含碳是一般为2.0%-4.3%,钢水的含碳量一般为0.02%-2.0%),并脱除有害杂质硫和磷,去除气体氧、氢、氮和非金属夹杂物(氧化物、硫化物、氮化物、磷化物等),最后按照所冶炼钢种的需求,加入合金,调整钢水的成分和温度后冶炼结束。
转炉炼钢形式有氧气顶吹转炉、氧气底吹转炉、顶底复合吹炼转炉等几种。
由于顶吹转炉和底吹转炉各有优缺点,目前应用最多的是将两者结合起来的顶底复吹转炉。
顶吹转炉冶炼一炉钢的操作过程主要由以下几步组成:
上炉出钢、倒渣,检查炉衬和倾动设备等并进行必要的修补和修理;
倾炉,加废钢、兑铁水,摇正炉体(至垂直位置);
降枪开吹,同时加入第一批渣料(起初炉内噪声较大,从炉口冒出赤色烟雾,随后喷出暗红的火焰;
3~5/后硅锰氧接近结束,碳氧反应逐渐激烈,炉口的火焰变大,亮度随之提高;
同时渣料熔化,噪声减弱);
3~5/后加入第二批渣料继续吹炼(随吹炼进行钢中碳逐渐降低,约12/后火焰微弱,停吹);
倒炉,测温、取样,并确定补吹时间或出钢;
出钢,同时(将计算好的合金加入钢包中)进行脱氧合金化。
4)炉外精炼
炉外精炼是指在钢包中进行冶炼的过程,是将真空处理、吹氩搅拌、加热控温、喂线喷粉、微合金化等技术以不同形式组合起来,出钢前尽量除去氧化渣,在钢包内重新造还原渣,保持包内还原性气氛。
炉外精炼的目的是降低钢中的C、P、S、O、H、N、等元素在钢中的含量,以免产生偏析、白点、大颗粒夹杂物,降低钢的抗拉强度、韧性、疲劳强度、抗裂性等性能。
这些工作只有在精炼炉上进行,其特点与功能如下:
A.可以改变冶金反应条件。
炼钢中脱氧、脱碳、脱气的反应产物为气体,精炼可以在真空条件下进行,有利于反应的正向进行,通常工作压力≥50Pa,适于对钢液脱气。
B.可以加快熔池的传质速度。
液相传质速度决定冶金反应速度的快慢,精炼过程采用多种搅拌形式(气体搅拌、电磁搅拌、机械搅拌)使系统内的熔体产生流动,加速熔体内传热、传质的过程,达到混合均匀的目的。
C.可以增大渣钢反应的面积。
各种精炼设备均有搅拌装置,搅拌过程中可以使钢渣乳化,合金、钢渣随气泡上浮过程中发生熔化、熔解、聚合反应,通常1吨钢液的渣钢反应面积为0.8~1.3mm2,当渣量为原来的6%时,钢渣乳化后形成半径为0.3mm的渣滴,反应界面会增大1000倍。
微合金化、变性处理就是利用这个原理提高精炼效果。
D.可以在电炉(转炉)和连铸之间起到缓冲作用,精炼炉具有灵活性,使作业时间、温度控制较为协调,与连铸形成更加通畅的生产流程。
5)炉外精炼工艺方法介绍
A.LF炉
是70年代初期在日本发展起来的精炼设备。
由于它设备简单,投资费用低,操作灵活和精炼效果好而成为冶金行业的后起之秀,在日本得到了广泛的应用与发展。
LF炉精炼主要靠桶内的白渣,在低氧的气氛中(氧含量为5%),向桶内吹氩气进行搅拌并由石墨电极对经过初炼炉的钢水加热而精炼。
由于氩气搅拌加速了渣一钢之间的化学反应,用电弧加热进行温度补偿,可以保证较长时间的精炼时间,从而可使钢中的氧、硫含量降低,夹杂物按ASTM评级为O~O.1级。
LF炉可以与电炉配合,以取代电炉的还原期,还可以与氧气转炉配合,生产优质合金钢。
此外,LF炉还是连铸车间,特别是合金钢连铸生产线上不可缺少的控制成分、温度及保存钢水的设备。
因此LF炉的出现形成了LD—LF—RH—CC(连铸)新的生产优质钢的联合生产线。
在这种联合生产线上钢的还原精炼主要是靠LF炉来完成的。
LF炉所处理的钢种几乎涉及从特钢到普钢的所有钢种,生产中可视质量控制的需要,采用不同的工艺操作制度。
在各种二次精炼设备中,LF炉的综合性价比高。
B.RH炉
在真空室的下部设有两根与其相通的环流管,脱气处理时将环流管插入钢液,靠真空室被抽成真空后建立的压差使钢液由环流管进入真空脱气室,同时从两根环流管之一(上升管)吹入驱动气体,利用气泡泵原理抽引钢液流过脱气室和下降管产生循环运动,并在真空室内脱除气体。
C.VOD炉
1965年西德首先开发应用的,它是将钢包放入真空罐内从顶部的氧枪向钢包内吹氧脱碳,同时从钢包底部向上吹氩搅拌。
此方法适合生产超低碳不锈钢,达到保铬去碳的目的,可与转炉配合使用。
他的优点是实现了低碳不锈钢冶炼的必要的热力学和动力学的条件-高温、真空、搅拌。
2.3.2连铸
将高温钢水浇注到一个个的钢锭模内,而是将高温钢水连续不断地浇到一个或几个用强制水冷带有“活底”(叫引锭头)的铜模内(叫结晶器),钢水很快与“活底”凝结在一起,待钢水凝固成一定厚度的坯壳后,就从铜模的下端拉出“活底”,这样已凝固成一定厚度的铸坯就会连续地从水冷结晶器内被拉出来,在二次冷却区继续喷水冷却。
带有液芯的铸坯,一边走一边凝固,直到完全凝固。
待铸坯完全凝固后,用氧气切割机或剪切机把铸坯切成一定尺寸的钢坯。
这种把高温钢水直接浇注成钢坯的新工艺,就叫连续铸钢。
图2.7连铸生产工艺流程
2.3.3中厚板
图2.8中厚板生产工艺流程
2.3.4宽厚板
图2.9宽厚板生产工艺流程
2.3.5热轧
生产流程
A.板坯由炼钢连铸车间的连铸机出坯辊道直接送到热轧车间板坯库,直接热装的钢坯送至加热炉的装炉辊道装炉加热,不能直接热装的钢坯由吊车吊入保温坑,保温后由吊车吊运至上料台架,然后经加热炉装炉辊道装炉加热,并留有直接轧制的可能。
连铸板坯由连铸车间通过板坯上料辊道或板坯卸料辊道运入板坯库,当板坯到达入口点前,有关该板坯的技术数据已由连铸车间的计算机系统送到了热轧厂的计算机系统,并在监视器上显示板坯有关数据,以便工作人员进行无缺陷合格板坯的核对和接收。
另外,通过过跨台车运来的人工检查清理后的板坯也需核对和验收,并输入计算机。
进入板坯库的板坯,由板坯库计算机管理系统根据轧制计划确定其流向。
B.常规板坯装炉轧制:
板坯进入板坯库后,按照板坯库控制系统的统一指令,由板坯夹钳吊车将板坯堆放到板坯库中指定的垛位。
轧制时,根据轧制计划,由板坯夹钳吊车逐块将板坯从垛位上吊出,吊到板坯上料台架上上料,板坯经称量辊道称重、核对,然后送往加热炉装炉辊道,板坯经测长、定位后,由装钢机装入加热炉进行加热。
碳钢保温坑热装轧制:
板坯进入板坯库后,按照板坯库控制系统的统一指令,由板坯夹钳吊车将板坯堆放到保温坑中指定的垛位。
轧制时,根据轧制计划,由板坯夹钳吊车逐块将板坯从保温坑取出,吊到板坯上料台架上上料,板坯经称量辊道称重、核对,然后送往加热炉装炉辊道,板坯经测长、定位后,由装钢机装入加热炉进行加热。
C.直接热装轧制:
当连铸和热轧的生产计划相匹配时,合格的高温连铸板坯通过加热炉上料辊道运到称量辊道,经称重、核对,进入加热炉的装炉辊道,板坯在指定的加热炉前测长、定位后,由装钢机装入加热炉进行加热。
其中一部分通过卸料辊道运输的直接热装板坯需通