数控机床的加工工艺毕业论文word格式Word格式文档下载.docx
《数控机床的加工工艺毕业论文word格式Word格式文档下载.docx》由会员分享,可在线阅读,更多相关《数控机床的加工工艺毕业论文word格式Word格式文档下载.docx(10页珍藏版)》请在冰豆网上搜索。
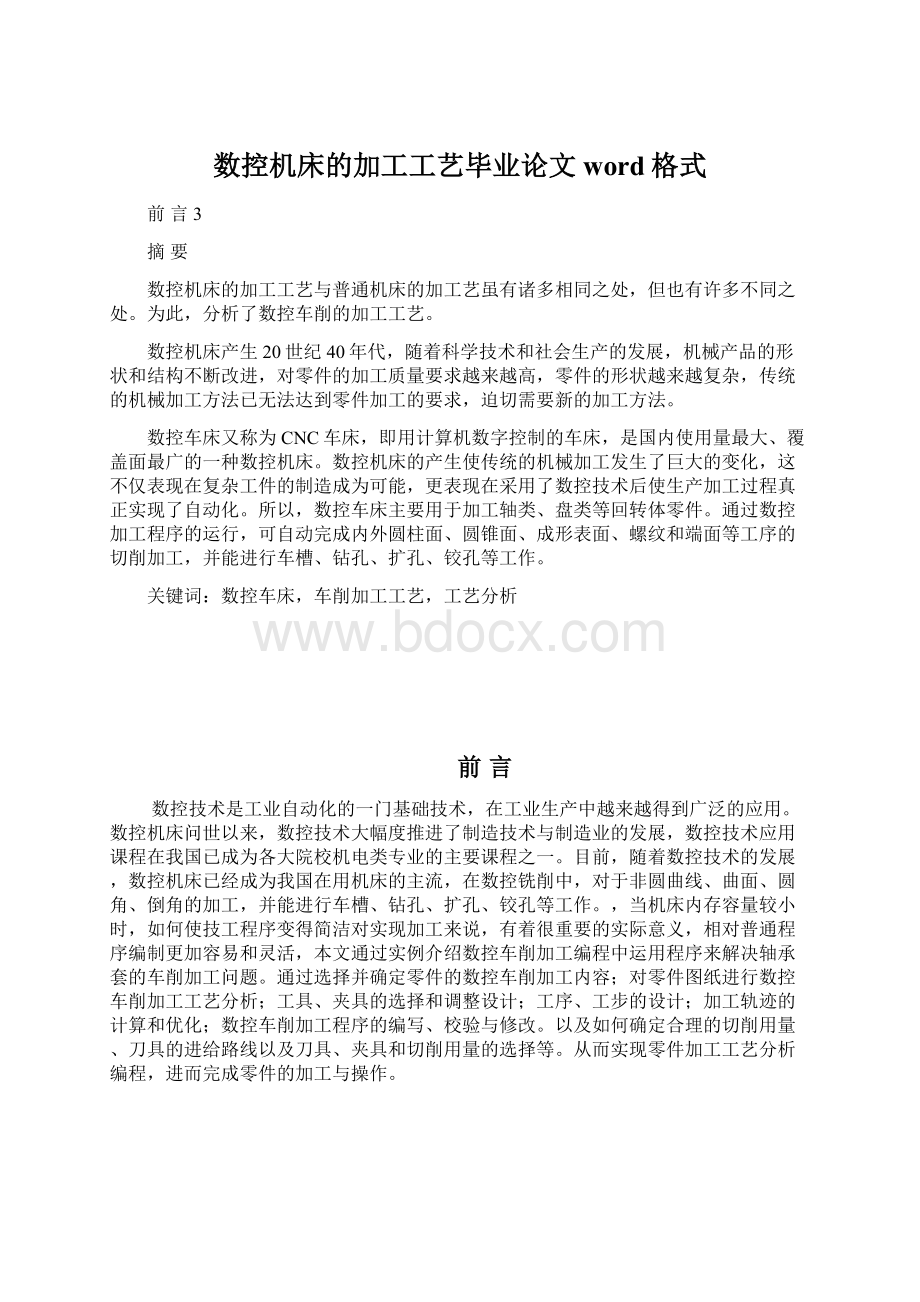
(如图1-1)
二、零件特点
从图纸中我们可以看出该零件轮廓由直线构成一个成型台阶回转轴。
加工部分包括外圆,一个孔和内孔,一个槽,倒角等。
(图1-1)轴承套
1.2工艺过程
1.2.1工艺过程的制定
由于每个零件结构形状不同,各表面的技术要求也有所不同,故加工时,其定位方式则各有差异。
一般加工外形时,以内形定位;
加工内形时又以外形定位。
因而可根据定位方式的不同来划分工序。
考虑到零件的形状不易装夹,故先加工零件的左边的部分,然后以左面的零件轴线为定位基准加工右面的部分。
并且考虑到加工原则中的先近后远先粗后精制定加工工艺如下:
为减少换刀,对刀次数及减少辅助时间,选用90°
外圆车刀进行粗加工和精加工、用切断刀进行切槽加工,选择镗孔刀进行孔的粗加工和精加工。
调头用三爪卡盘固定住左端Φ37外圆。
留有5mm长以防刀具与夹具发生干涉,保证同轴度和精度并防止工件转动时摇晃不定。
用内圆车刀依次进行孔的粗精加工;
用刀宽为2mm的切槽刀车槽,
1.2.2加工精度要求
加工图纸如上图,零件加工部分包括(Φ42,Φ37)外圆,一个C2,C1的倒角,一个2x0.5的槽,(Φ22,Φ24,,Φ12)孔等。
零件的主体尺寸长度为40mm,最大位置直径为Φ42。
1.2.3工步设计
该零件从棒料开始加工,要进行粗加工、精加工、车孔以及切槽等工步:
1)粗车外圆。
2)精车循环。
3)切槽。
1.2.4定位基准的选择
(1)基准重合原则
(2)基准统一原则
(3)便于装夹原则
(4)便于对刀原则
轴套类零件外圆表面、内孔、螺纹等表面的同轴度,以及端面对轴中心线的垂直度是其相互位置精度的主要项目,而这些表面的设计基准一般都是轴中心线。
用两中心孔定位符合基准重合原则,并且能够最大限度地在一次装夹中加工出多格外圆表面和端面,因此常用中心孔作为轴加工的定位基准。
当不能采用中心孔时或粗加工是为了提高工作装夹刚性,可采用轴的外圆表面作定位基准,或是以外圆表面和中心孔共同作为定位基准,能承受较大的切削力,但重复定位精度并不太高。
数控车削时,为了能用同一程序重复加工和工件调头加工轴向尺寸的准确性,或为了端面余量均匀,工件轴向需要定位。
采用中心孔定位时,中心孔尺寸及两端中心孔间的距离要保持一致。
以外圆定位时,则应采用三爪自定心卡盘反爪装夹或采用限未支承,以工件端面或台阶儿面作为轴向定位基准。
根据定位基准选择原则,避免不重合误差,便于编程,以工序的设计基准作为定位基准。
零件加工时,先以Φ42外圆的轴线作为轴向定位基准,加工零件;
然后以零件轴线作为轴向定位基准,以轴台的端面的中心作为该轴件剩余工序的轴向定位基准,并且把编程原点选在设计基准上。
1.3装夹方式
一、选择夹具
夹具的作用是保证工件在机床上的正确位置和牢固的安装,即定位和夹紧,
从而使数控加工顺序进行,保证工件的位置精度,同时也保证工件坐标系能够建立在正确的位置上。
车削加工的工件一般是回转体,对于回转体零件,一般选择三爪自定心卡盘。
本零件选择三爪自定心卡盘作夹具。
对于回转体零件,一般选择三爪自定心卡盘。
先用三爪自定心卡盘毛坯左端,加工右端达到工件精度要求;
再工件调头,用三爪自定心卡盘毛坯右端,再加工左端达到工件精度要求。
1.4刀具选择
为适应数控机床加工精度高、加工效率、加工工序集中及零件装夹次数少的要求,数控刀具具有很高的切削效率.高精度.高重复定位精度.可靠度和耐用度。
选择数控刀具的原则刀具寿命与切削用量有密切关系。
在制定切削用量时,应首先选择合理的刀具寿命,而合理的刀具寿命则应根据优化的目标而定。
一般分最高生产率刀具寿命和最低成本刀具寿命两种,前者根据单件工时最少的目标确定,后者根据工序成本最低的目标确定。
选择刀具寿命时可考虑如下几点根据刀具复杂程度、制造和磨刀成本来选择。
复杂和精度高的刀具寿命应选得比单刃刀具高些。
对于机夹可转位刀具,由于换刀时间短,为了充分发挥其切削性能,提高生产效率,刀具寿命可选得低些,一般取15-30min。
对于装刀、换刀和调刀比较复杂的多刀机床、组合机床与自动化加工刀具,刀具寿命应选得高些,尤应保证刀具可靠性。
车间内某一工序的生产率限制了整个车间的生产率的提高时,该工序的刀具寿命要选得低些当某工序单位时间内所分担到的全厂开支M较大时,刀具寿命也应选得低些。
大件精加工时,为保证至少完成一次走刀,避免切削时中途换刀,刀具寿命应按零件精度和表面粗糙度来确定。
与普通机床加工方法相比,数控加工对刀具提出了更高的要求,不仅需要冈牲好、精度高,而且要求尺寸稳定,耐用度高,断和排性能坛同时要求安装调整方便,这样来满足数控机床高效率的要求。
数控机床上所选用的刀具常采用适应高速切削的刀具材料如高速钢、超细粒度硬质合金并使用可转位刀片。
选择刀具通常要考虑
(1)被加工工件的材料及性能
(2)切削工艺的类别(3)被加工工件的几何形状,零件精度,加工余量(4)被吃刀量,进给速度,切削速度考虑到以上因素故粗车时,要选用强度高,耐用度高的刀具以满足粗车时大吃刀量,大进给量的要求.精车时要选用精度高,耐用度好的刀具以保证加工精度的要求.
1)粗车——90°
外圆车刀——T0101。
2)精车——90°
外圆车刀——T0202。
3)切槽——切断刀(刀宽2mm)——T0303。
4)镗孔——镗孔刀——T0404
刀具列表如下
工步号
工步内容
刀具名称
刀具图号
刀具规格
主轴转速
切削深度
备注
1
粗车
90°
外圆车刀
800
2
自动换刀
精车
700
3
切槽
切断刀
3
Ф5
300
4
镗孔
镗孔刀
1.5设计走刀路线
一、粗车循环
粗车的主要任务是去除余量,可以用复合循环指令来设定。
设计走刀路线时,应设定工件坐标系XOZ。
要求:
①画出刀具形状;
②标注工件坐标系;
③标明进刀点,起刀点,每层切深,退刀量,精车余量ΔU,ΔW;
④画出刀具运动轨迹。
起刀点(100,200)为安全位置,进刀点(45,3)为接近工件点,切深Δd=2,退刀量e=0.5,精车余量ΔU=1、ΔW=0.5。
二、精车
精车外圆即在粗车基础上车一刀即可,其走刀路线较为简单,主要需标出关键点,画出刀具轨迹,起刀点坐标为(100,100),进刀点(接近)坐标为(0,3),退刀点坐标为(32,-34),将每一走刀段都标上序号,以便编程时一一对应。
三、切槽线
切槽即在工件上切一个退刀槽,用切断刀加工,刀宽2mm。
切槽时,只能X向进退刀,不能Z向切削,否则易打刀(刀具折断),当刀宽等于槽宽,切槽刀只切一次;
当刀宽小于槽宽时,应根据情况切多次,路线为先X向退刀,Z向平移,再X向进刀。
起刀点坐标(100,100),进刀点坐标为(44,-34),基点A坐标为(31.5,-34)。
1.6切削用量
1.6.1选择切削用量
选择数控车削用刀具数控车削车刀常用的一般分成型车刀、尖形车刀、圆弧形车刀以及三类。
成型车刀也称样板车刀,其加工零件的轮廓形状完全由车刀刀刃的形伏和尺寸决定。
数控车削加工中,常见的成型车刀有小半径圆弧车刀、非矩形车槽刀和螺纹刀等。
在数控加工中,应尽量少用或不用成型车刀。
尖形车刀是以直线形切削刃为特征的车刀。
这类车刀的刀尖由直线形的主副切削刃构成,如90°
内外圆车刀、左右端面车刀、切槽切断车刀及刀尖倒棱很小的各种外圆和内孔车刀。
尖形车刀几何参数主要是几何角度的选择方法与普通车削时基本相同,但应结合数控加工的特点如加工路线、加工干涉等进行全面的考虑,并应兼顾刀尖本身的强度。
二是圆弧形车刀。
圆弧形车刀是以一圆度或线轮廓度误差很小的圆弧形切削刃为特征的车刀。
该车刀圆弧刃每一点都是圆弧形车刀的刀尖,应此,刀位点不在圆弧上,而在该圆弧的圆心上。
圆弧形车刀可以用于车削内外表面,特别适合于车削各种光滑连接凹形的成型面。
选择车刀圆弧半径时应考虑两点车刀切削刃的圆弧半径应小于或等于零件凹形轮廓上的最小曲率半径,以免发生加工干浅该半径不宜选择太小,否则不但制造困难,还会因刀尖强度太弱或刀体散热能力差而导致车刀损坏。
切削用量包括切削速度,背吃刀量和进给量.对于不同的加工方法需要选择不同的切削用量。
粗加工时一般以加工效率为主通常选择较大的背吃刀量和进给量,采用较小的切削速度.精加工时通常选择较小的背吃刀量和进给量采用较高的切削速度,对于原材料45#,粗加工时u取3㎜,s取800m/min,f取0.4mm/r;
精加工时u取0.25㎜,s取1000m/min,f取0.2㎜/r。
粗车S800,F100;
精车S700,F100;
切槽S300,F50;
1.6.2主轴转速的确定
主轴的转速是由切削刃上选定点相对于工件的主运动的线速度
主运动速度n=1000Vc/πd单位为r/min
第二章数控加工程序的编制
2.1数值计算
生活中,我们对几何信息的认知有多种方法,常用的有数形结合法(解析法)。
但有时面对复杂的图形,解析法会带来繁重的数学计算。
AUTOCAD作为一套专业的绘图软件,它强大的信息处理功能为图形中繁杂点的计算带来了可能。
我们在操作界面中绘制图形后就可以打开状态栏中的捕捉、对象捕捉按钮,在绘图区捕捉相关的点。
同时,在状态栏中就可以看到这些点的坐标。
数值计算的一般内容计算数控编程的主要工作就是把加工过程中刀具移动的位置按一定的顺序和方式编写成程序单,输入机床的控制系统,操纵加工过程。
刀具移动位置是根据零件图纸,按照已经确定的加工路线和允许的加工误差这一工作称为数控加工编程中的数值计算。
数值计算主要用于手工编程时的轮廓加工数控加工编程中的数值计算主要包括:
工件零轮廓中几何元素的基点插补线段的节点刀具中心位置辅助计算等内容基点基点就是构成零件轮廓的各相邻几何元素之间的交点或切点。
如两直线的交点、直线与圆弧的交点或切点、圆弧与二次曲线的交点或切点等等,均属基点。
一般来说,基点的坐标根据图纸给定的尺寸,利用一般的解析几何或三角函数关系不难求得。
节点节点是在满足容差要求条件下用若干插补线段(如直线段或圆弧段等)去逼近实际轮廓曲线时,相邻两插补线段的交点。
节点的计算比较复杂,方法也很多,是手工编程的难点。
有条件时,应尽可能借助于计算机来完成,以减少计算误差并减轻编程人员的工作量。
一般称基点和节点为切削点切削点,即刀具切削部切削点位必须切到的点。
刀具中心位置刀具中心位置是刀具相对于每个切削点刀具中心所处的位置。
因为刀具都有一定的半径,要使刀具的切削部位切过轮廓的基点和节点,必须对刀具进行一定的偏置。
对于没有刀具偏置功能的数控系统,应计算出相对于基点和节点的刀具中心位置轨迹。
对于具有刀具偏置功能的数控系统,加工某些内腔型面时,往往也要求计算出刀具中心轨迹的坐标数据。
辅助计算辅助计算包括以下内容:
1)增量计算对于增量坐标的数控系统,应计增量计算算出后一节点相对前一节点的增量值。
2)脉冲数计算通常数值计算是以毫米为单位脉冲数计算进行的,而数控系统若要求输入脉冲数,故应将计算数值换算为脉冲数。
3)辅助程序段的数值计算对刀点到切入点的辅助程序段的数值计算程序段,以及切削完毕后返回到对刀点的程序均属辅助程序段。
在填写程序单之前,辅助程序段的数据也应预先确定。
2.2刀位点
2.2.1定位刀位点
刀具究竟从什么位置开始移动到指定的位置呢所以在程序执行的一开始,必须确定刀具在工件坐标系下开始运动的位置,这一位置即为程序执行时刀具相对于工件运动的起点,所以称程序起始点或起刀点。
此起始点一般通过对刀来确定,所以,该点又称对刀点。
在编制程序时,要正确选择对刀点的位置。
对刀点设置原则是:
便于数值处理和简化程序编制。
易于找正并在加工过程中便于检查,引起的加工误差小。
在进行数控加工的编程时,往往将整个刀具浓缩视为一个点,那就是刀位点,它是在刀具上用于表现刀具位置的参照点。
对刀操作就是要测定出程序起点处刀具刀位点相对机床原点以及工件原点的坐标位置。
在对刀时,常用的仪器有:
对刀测头、千分表或对刀瞄准仪等。
对刀点可以设置在零件、夹具上或机床上面(尽可能设置在零件的设计基准或工艺基准上)。
2.2.2待加工毛坯的对刀
试切端面:
将两端面已经加工好的待加工毛坯装夹到主轴上,在工件的伸出端安装Z轴向设定器。
快移刀具接近到Z轴向设定器,改用增量方式控制刀具工进,至到指示灯亮时停止动作,保持Z轴向不动,取出轴向设定器。
然后在机床操作面板上调出刀具补偿菜单栏中刀偏表,在相关的试切长度填空栏中键入有关数值(当前刀具刀位点相对于程序原点的距离)。
试切外圆:
快速将刀具刀位点移动刀毛坯端面角附近,然后用增量方式调节X、Z轴向进给至刀位点刚好切到毛坯外表面,再用MDI方式运行进行外圆车削。
同时保持X轴轴向坐标不变,退出刀具。
用游标卡尺测量出试切外圆直径。
然后在刀偏表中键入试切直径。
2.3刀偏值的测定
刀偏值就是各刀具相对于基准刀具的几何补偿。
用点动或步进方式操作移动刀具,使基准刀具刀位点对准工件的基准点,然后进行X轴Z轴坐标清零,退刀。
换置刀具,再用点动或步进方式使该刀具刀位点对准工件上的同以一基准点,此时屏幕上显示的坐标既是该刀号刀具的几何偏置△Xj,△Zj.同理,可依次测定出其它刀具相对于基准刀具的几何偏置。
在相应的刀偏表中依次键入选用刀具刀位点的几何补偿。
2.4加工程序
附:
根据上述工艺分析所编制的加工程序,系统为FANUC-0T。
程序
车削(GSK980TD)
O0001(外圆加工程序号)
T0101S800M03;
(粗车部分,选一号刀具,设定1号刀补及主轴正转,速度800r/min)
G94X50Z2;
(快速定位到Φ50mm外圆,距端面2mm处)
G90X46Z-41F100;
X42.5(粗车Φ42mm的外圆,留径向余量0.5mm)
X38.5Z-34
X34.5(粗车Φ34mm的外圆,留径向余量0.5mm)
G00X44Z-37;
(快速定位到(44,-37))
G01X36Z-41;
(加工倒角C2)
X50;
G00X100Z100;
(快速返回换刀点)
M03S700T0202;
(主轴正传,转速700r/min,换2号刀)
G00X34Z2;
G01Z-34F100;
(精加工Φ34mm的外圆)
X42;
Z-38;
(精加工Φ42mm的外圆)
(快速返回换刀点)
M03S900T0303;
(调转速为900r/min,换3号刀切槽)
G00X45Z-34;
G01X33F80;
(切槽加工)
G04X3;
(槽底停留3s)
X45;
(退刀)
G00Z-42.5;
G01X-1F50;
(切断)
G00X100Z100;
M05;
(主轴停)
M30;
(程序结束)
O0002;
(加工内孔程序)
M03T0101S300;
(选一号刀具,主轴正转,速度300r/min)
G94X44Z0;
G01X20F50;
G00Z100
X100;
T0404;
(换4号刀)
G00X18Z2;
G90X21.6Z-41F80;
(粗车Φ22mm的内孔,留径向余量0.4mm)
X22Z-1;
(车倒角C1)
Z-39;
(精加工Φ22mm的内孔)
X26Z-41;
T0505;
(快速退刀至(100,100)换5号刀补)
G00X18Z2;
Z-16;
G01X24F50;
(切槽)
G00X20;
G94X24Z-20F50;
Z-24;
Z-28;
M05;
(快退至(100,100)点,主轴停)
M30;
结论
数控机床作为一种使用广泛、典型的机电一体化产品,综合应用了微电子技术、计算机技术、自动控制、精密测量和机床结构等方面的最新成就,是一种高效的自动化机床。
由于数控机床极高效率、高精度和高柔韧性于一身,很好的代表了机床的主要发展方向。
时代和社会生产力的不断发展,要求数控系统与数控机床向更高的水平与层次迈进(高精度化、运动高速化、高柔韧性化、智能化)。
近年来,在国外的数控系统与伺服系统制造技术突飞猛进的大背景下,通过大量的技术引进,我过现代制造工业在飞速发展(数控技术得到广泛的应用)。
同时,我们还要看清现阶段中国数控业与世界先进水平的差距。
我国只有拥有完全自主知识产权上的数控核心技术,才能实现真正意义上的“世界工厂”和“制造大国”乃至“工业强国”。
这使国人不得不开始重新思索中国数控在未来的发展之路………
参考文献
[1]嵇宁数控加工编程与操作高等教育出版社;
2008
[2]赵长明数控加工工艺及设备北京:
高等教育出版社;
2003
[3]夏凤芳数控机床北京:
2005
[4]詹华西数控加工与编程西安:
西安电子科技大学出版社;
2004
[5]袁哲俊金属切削刀具上海:
上海科学技术出版社;
1993
[6]蔡兰,王霄数控加工工艺学化学工业出版社;
[7]王爱玲数控机床加工工艺北京:
机械工业出版社;
2006
[8]蒋建强数控编程技术200例科学出版社北京希望电子出版社;
[9]刘靖华数控加工技术高等教育出版社;
[10]
陈志雄数控机床与数控编程技术电子工业出版社;
[11]徐宏海数控加工工艺化学工业出版社;
文档来源网络,版权归原作者。
如有侵权,请告知,我看到会立刻处理。