支座类成组工艺及夹具Word文档下载推荐.docx
《支座类成组工艺及夹具Word文档下载推荐.docx》由会员分享,可在线阅读,更多相关《支座类成组工艺及夹具Word文档下载推荐.docx(35页珍藏版)》请在冰豆网上搜索。
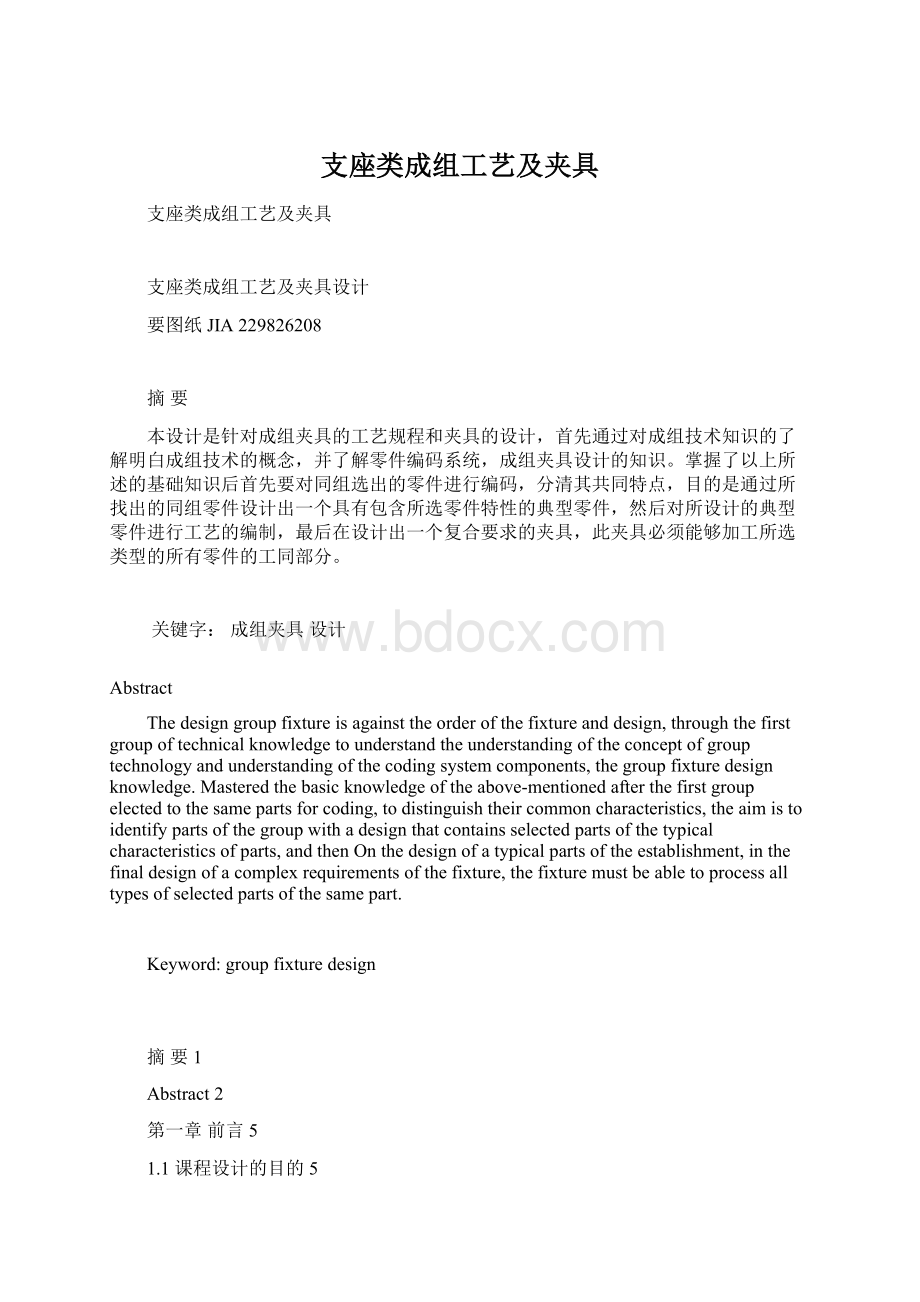
2.4零件的分类编码11
第三章复合零件的设计与工艺制定14
3.1零件的分析14
3.2零件的编码14
3.3复合零件的设计15
第四章对复合零件进行工艺编制17
4.1工艺路线的制定17
4.2加工基准面的选取17
4.3工艺路线的排制17
4.4机械加工余量,毛坯尺寸及工序尺寸的确定19
第五章机床专用夹具设计22
5.1.成组夹具设计设计概述22
5.1.1.成组夹具的基本概念22
5.1.2.成组夹具的调整方式22
5.1.3.成组夹具设计原则22
5.1.4.成组夹具设计步骤23
5.2.专用夹具的设计24
5.2.1.铣床专用夹具的主要类型24
5.2.2.铣床专用夹具的设计要点24
5.2.3.夹紧装置25
5.2.4.夹紧力的确定25
5.2.5.对刀,导向装置设计26
5.2.6.专用夹具的基准选择27
5.2.7.夹具体的设计27
5.2.8.定位误差分析与计算30
5.3.三维、二维图的绘制31
5.3.1二维软件的介绍31
5.3.2利用CAD绘图31
5.3.3所有零件图的绘制36
结束语37
参考文献37
前言
1.1课程设计的目的
机械制造工艺设计师检验我们将所学到的理论与生产实习相结合的极好的机会,也是接受机械工程师初步基本训练的必要过程。
通过这次设计,我希望能够达到如下目的:
具有制定中等复杂程度零件工艺规程的初步能力;
具有制成组夹具工艺规程的初步能力;
具有设计专用工艺装备的初步能力;
具有熟练的应用工艺计算方,正确地进行工艺计算的能力;
具有熟练的使用设计手册,参考资料和参考书的能力,为适应将来的工作为振兴祖国的机械行业,打下较为坚实的基础。
1.2课程设计的要求
本次设计要求学生通过对同一族零件的观察,涉及出一个复合零件,并对这个复合零件进行机械加工工艺规程的编制。
并在指导教师的指导下,选出所编工艺中的某到工序进行其专用夹具的设计。
而整个毕设过程具体要求完成的任务如下:
(1)选出多个同一种类的零件,对其进行编码分类;
(2)对分出的同一种族的零件进行二维图的绘制(利用AUTOCAD);
(3)综合所选同族的所有零件设计出一个复合零件并绘制三维图;
(4)对设计出的复合零件进行加工工艺的编制;
(5)设计指导老师指定的某到工序的专用夹具;
(5)绘制多有零件的零件图和夹具装配图和零件图,填写工艺卡片和检验卡片;
(6)编写课程设计说明书。
成组技术
2.1成组技术的基本原理
机械制造业中,小批量生产占有较大的比重,各类机械的生产大约70~85%属于单件,小批生产。
由于国内外市场竞争日益加剧和科技飞跃发展,要求产品不断改进和更新,因此,预计多品种,小批量生产方式的比重今后将有继续增长趋势。
统计资料表明,我国机械工业亦有此发展趋势。
传统的小批量生产方式会带来以下一些问题。
(1)生产计划,组织管理复杂化。
由于生产品种和生产过程的多样性是生产组织管理工作复杂化,科学地制定生产作业计划比较困难;
有关生产信息反馈到生产管理部门很慢,生产过程难于控制。
(2)零件从投料至加工成成品的总生产时间(生产周期)较长单件,小批量生产的工厂,车间布置一般皆采取机床功能的机群式布置,一个零件加工往往需要通过若干个机群式工段或小组,运行路线往返曲折,零件在车间运行时间很长。
此外,由于不易作到周密调度安排,零件在车间内停留等待时间也很长,这就增加了在制品数量,有时会延误交货时间。
据统计,在成批生产中,零件在车间等待和运输时间约占生产周期的93~95%,调整时间约占3.5%,其余用于机床加工时间(包括安装,切削,度量及空程等时间)仅占1.5~3.5%。
这样,零件作为车间在制品在车间停留的时间将占全生产周期的96.5~98.5%。
此外,由于零件品种多,小批量,使机床调整频繁,花费较多的机床调整时间。
可见,在小批量生产中,如何提高在工作时间内机床的实际利用率是急待解决的一个重要问题。
(3)生产准配工作量极大,在生产设计和工艺准备工作中,一般均采用传统“单打一”的工作方式,即总是分别的针对一种产品或零件进行产品设计和工艺准备工作,似乎一切皆“从头开始”,原有的经济劳动创造的声场信息很少重复使用。
所以,在设计和制造的生产准备工作中有不少是重复性劳动,付出了本来可以节约的时间与精力。
(4)产量小限制了先进生产技术的采用。
鉴于上述情况,与大批大量生产相比,小批生产水平和经济效益都是很低的。
据报道在美国,产量小于50的机械产品,其成本比大批量生产的成本高10~30倍;
在日本机械制造业中,多品种,小批生产企业的总产值比大批大量生产的企业高一倍,但人均产值前者仅及后者的一半。
因此,如何摆脱小批生产中由于品种多,产量小所造成的困境,而是只获得接近大批量生产的经济效益是一个值得重视的技术经济问题。
为此,近代在组织上,技术上提出了不少措施和方法,例如,生产专业化,产品设计的三化(标准化,系列化及通用化)及模块化,数控机床及加工中心的应用等等,这些都取得了一定的发展,但都有其局限性。
成组技术的科学理论及其实践表明,它能从根本上解决生产中由于品种多,产量小而带来的矛盾。
成组技术(GT-GroupTechnolopy)是一门生产技术科学,研究如何识别和发掘生产活动中有关事物的相似性,并充分利用它,即把相似的问题归类成组,寻求解决这一组问题相对统一的最有方案,以取得所期望的经济效益。
成组技术应用于机械加工方面,乃是将多种零件按其工艺的相似性分类以形成陆零件族,把同一零件族中零件分三的小生产量汇集成较大的成组生产量,从而使小批量生产能获得接近于大批生产的经济效果。
将品种众多的零件按其相似性分类以形成为数不是很多的零件族;
把同一零件族中诸零件分三的小生产量汇集成较大的成组生产量;
这样,成组技术就是巧妙的把品种多转化为“少”把生产量小转化为“大”,由主要矛盾有条件的转化,这就为提高多品种,小批量生产的经济效益开辟了广阔的道路。
成组技术的基本原理是符合辩证法的,所以它可以作为指导生产的一般方法。
实际上,人们很早以来已应用成组技术的哲理指导生产实践,诸如生产专业化,零部件标准化等皆可以认为是成组技术在机械工业中的应用。
现在发展了的成组技术已广泛应用于设计,制造和管理等各个方面,并取得了显著的效果。
生产中有关事物的相似性是客观存在的,这不仅为人们一般常识所认可,而且也为统计学所证实。
用统计学的方法统计事物某些特征属性的出现频率,可以从总体上定量的说明事物客观存在着的相似性。
零件统计学不仅为了成组技术的创立提供可以信赖的科学根据,也是实施成组技术过程中充分认识和利用有关事物相似性的有用的科学方法。
成组技术基本原理既然是要求充分认识并用客观存在着的有关事物的相似性,所以按一定的相似性标准将有关事物归类成组实施是成组技术的基本。
目前,将零件分类成组常用的方法有:
(1)视检法;
(2)生产流程分析法;
(3)编码分类法。
视检法是由有生产经验的人员通过对零件图纸仔细阅读和判断,把具有某些特征属性的一些零件归结一类。
他的效果主要取决一个人的生产经验,多少带有主观性和片面性。
生产流程分析法(PFA——ProducfionFlowAnalysis)是一零件生产流程为依据的。
为此,需要有较完整的工艺规程及生产设备明细表等技术文件。
通过对零件生产流程的分析,可以把工艺过程相近的,即使用同一组机床进行加工的零件归结为一类。
采用此法分类的正确性是与分析方法以及所依据的工厂技术资料有关,虽然,采用此法可以按工艺相似性将零件分类,以形成加工族。
按编码分类,首先需要将带分类的主零件进行编码,即将零件的有关设计,制造等反面功的信息转译为代码(代码可以是数字或数字,字母兼用)。
为此,需选用或制定零件分类编码系统。
由于零件有关信息的代码化,就可以根据代码对零件进行分类。
应指出采用零件分类编码系统使零件有关生产信息代码化,将有助于应用计算机辅助成组技术的实施。
关于零件分类成组方法将作为专门问题于第三章讨论。
2.2成组技术应用及其技术经济效果
目前,发展了的成组技术是采用系统工程学的观点,把中,小批生产中的设计。
制造和管理等方面作为一个生产系统整体,统一协调生产活动的各方面,全面实施成组技术,以取得最优的综合经济效益。
以下将从产品设计,制造及生产管理等方面简述成组技术的应用及其效果。
一.产品设计方面
产品设计图纸是后继生产活动的重要依据。
因此,在设计部门首先实施成组技术有着重要的意义。
用成组技术指导成品设计代替传统的设计方法,可以使设计合理化,扩大和深化设计标准化工作。
在深刻认识零件结构和功能的基础上,根据拟定的设计相似性标准可将设计零件分类成组形成设计族,针对设计族可以制定不同程度的标准化的设计规范,以备设计检索。
由于有关设计信息最大程度的重复使用,这就节约了时间,加快了设计速度。
据统计,从而减少新设计的零件,这不仅可免除设计人员的重复性劳动,也可以减少工艺准备工作和降低制造费用。
应特别指出的是,由于用成组技术指导设计,赋予各类零件以更大的相似性,这就为在制造管理方面实施成组技术奠定了良好的基础,使之取得更好的成绩。
此外,由于新产品具有继承性,使长年累积并经过考验的有关设计和制造的经验再次应用,这有利于保证产品质量的稳定。
已成组设计指导的设计合理化和标准化工作将为实现计算机辅助设计(CAD)奠定良好的基础。
二.制造工艺面
成组工艺在制造工艺方面最先得到的广泛应用。
开始是由于成组工序,即把加工方法,安装方法和机床调整相近得零件归结为零件组,设计出适用于全组零件加工的成组工序。
成组工序允许采用统一设备和工艺装置,以及相同或相近的机床调整加工全组零件,这样,只要拿那能按零件组安排生产调度计划,就可以大大减少由于零件品种更换所需要的机床调整时间。
此外,由于零件组内诸零件的安装方式和尺寸相近,可是基础应用于成组工艺的公用夹具——成组夹具。
只要进行少量的调整或更换某些元件,成组夹具就可适用于全组零件的工序安装。
成组技术亦可应用于零件加工的全工艺过程。
为此,应将零件按工艺过程相似性分类形成加工族,然后针对加工组设计成组工艺过程。
成组工艺过程是成组工序的集合,能保证按标准化的工艺路线采用统一组机床加工全加工组的诸零件。
应指出,设计成组工艺过程,成组工序和成组夹具皆应以成组年产量为依据,因此,成组加工允许采用进行先进的生产工艺技术。
有成组技术指导工艺设计工作,以代替孤立的针对一个零件进行工艺设计的传统方法,可以实现工艺设计工作合理化和标准化,这不仅大大缩减工艺准备工作的时间和费用,而且也有利于提高工厂生产技术水平。
例如,据报道美国某一公司为制造523种齿轮制定了477种工艺规程,在应用成组技术原理进行分析后,发展至少可减少400种以上的工艺规程。
如若制定一种零件的工艺规程花费2~3h,则仅就减少这类齿轮工艺规程制定工作而言就可节约800~1200h。
此外,制定的成组工艺设计指导文件资料,可被工艺员检索使用,这有助于提高新手的工作质量和效率。
以成组技术指导的工艺设计合理化和标准化为基础,不难实现计算机辅助工艺过程设计(CAPP)及计算机辅助成组夹具设计。
三.生产组织管理方面
如前所述,为取得综合的经济效果,应在生产系统中全面实施成组技术,即形成成组生产系统。
工厂生产组织管理机构是生产的规划,指挥和控制的机构,工厂实施成组技术,若不按照成组技术的基本原理更新工作方法和调整机构,就很难设想各部门能协调一致,以期达到既定的目标。
成组加工要求将零件按工艺相似性分类形成加工族,加工在同一种加工族有其相应的一组机床设备。
因此,很自然,成组生产系统要求按模块化原理组织生产,即采取成组生产单元的生产组织形成。
在一个生产单元内有一组工人操作一组设备,生产一个或若干个相近的加工族,再次生产单元内可完成诸零件全部或部分的生产任务。
因此可以认为,成组生产单元是以加工族为生产对象的产品专业化或工艺专业化(如热处理,磨削成组生产单元等)的生产基层单位。
在生产单元内,一般仅生产划分与本单元的加工族,其零件品种为数不是很多的,这样可以大大简化生产管理工作,提高管理效率。
所以成组生产单元是实施成组技术的一种有效的生产组织和劳动组织。
实施成组技术要求更新生产管理工作方式和内容。
例如,生产管理部门在计划安排上应设法把相似零件集中在一起,并在生产调度中保证实现成组加工。
若仍采用一般工业上常用的控制成品库,零件库存量的方式组织生产,则达不到减少库存,加工资金周转和缩短生产周期的目标,既不能获得实施成组技术所期望的效果。
据报导,采用成组生产单元组织生产可减少在制品数量约60%,缩短生产周期40~70%。
现代化工厂为管理和控制生产过程需要收集,分析和处理大量信息,并使信息迅速流通和反馈到有关工作机构和部门。
借助于计算机辅助管理系统技术基础之一。
这是因为运用成组技术基本原理将大量信息分类分组,并使之规格化,标准化,这将有助于建立结构合理的生产系统公用数据库,可大量压缩信息的存储量;
由于不再是分别正对一个工程问题和任务设计程序,可使程序设计优化。
此外,由于采用编码,则可借助于计算机使用信息得以迅速检索,分析和处理。
所以,随着成组技术推广实施和计算机广泛应用,必将加速品种,中小批生产中计算机辅助管理系统的建立。
如上所述,高水的全面实施成组技术会获得最佳的综合经济效果。
但应注意到,全面实施成组技术将会涉及到工厂企业诸方面深刻的技术改造和对职工的宣传教育及培训工作;
需要坚强的组织领导,周密的统筹规划;
需要一定的技术和物质条件;
需要花费大量的精力时间和投资。
对此在做出采用成组技术的决策之前不能有充分的认识。
一般应全面实施成组技术,因为作为一个生产系统的各个职能部门及生产环节都是密切相关的。
为此,首先应作全面的调查研究,明确实施成组技术的目标和任务,制定切实可行的近期和远期的规划和实施步骤,以便有成效的按计划推进成组技术的实施。
应指出,国内外实践经验也表明,不少工厂根据生产上急需要解决的问题和现有的生产条件,花费不大的投资,仅局部的在一定范围内实施成组技术,也能取得较好的经济效果。
但是,若事先就能从局部看到全局,把近期与远期目标结合起来,制定阶段性实施成组技术规划应是可取的。
如前所述,成组技术的核心是充分利用生产活动中有关事物的相似性。
从更广泛的意义来说,它的应用可概括为以下三种主要方式。
(1)事物的集中进行把具有一定相似和重复性的事务集中起来进行,由此可避免总是频繁的又一种事物传换到与之无联系的另一种事物时所必须花费的时间。
要求摒弃“单打一”的工作方式。
(2)事物的标准化,规范化把具有一定相似性和重复性的事物汇集起来并使之标准化,规范化。
由此可腾出手来集中精力解决各种事务中属于个性的问题,从而可避免重复性的懒动。
要求对具有相似性的一组事物提出统一的最优解决方案。
(3)信息的重复使用把具有一定相似性和重复性的有关事物的信息进行合理化处理,使之更有效的存储和重复使用这些信息。
要求摒弃“一切从头开始”的工作方式。
所以,成组技术有着极其广泛的应用领域,目前日益为生产工程界所重视。
2.3成组技术发展概况
成组技术的哲理是符合唯物辩证法的,因此作为指导生产实践的一般方法,很早以来就已在不同领域没有所应用。
但是,作为较完整的科学理论体系是由苏联斯.帕.米特洛范诺夫于50年代中期提出来的。
她在1959年出版的《成组工艺科学原理》一书总结了苏联早期在成组工艺方面的实践经验和研究工作。
当时苏联着重应用于各种类型机床的成组加工,即成组工序。
然而,在上述著作中作者即提出不仅可应用于个别工序,也可应用于工序顺序相同的诸零件的全部制作过程;
并论述了成组技术在生产组织管理方面,如生产组织,计划,技术定额和流水生产等方面的应用;
还提出成组技术应用的成功条件在于提高成组生产量,并认为可借助机器零部件和工艺规程的标准化和统一化来提高成祖生产量。
由此可见,在50年代米特洛范诺夫就较全面地提出了成组技术科学理论,当然,由于当时的历史条件,它还有一定的局限性。
例如,采用的是无编码分类,零件的分类还局限用于工序成组,等等。
50年代末60年代初,成组技术传入东欧和西欧各国。
在东欧各国,成组技术被积极采用并取了进展。
即可斯洛伐克机床与金属切削研究所(VUOSO)提出了一个十分简明实用的零件分类码系统(Aachen)工业大学奥匹兹(H.Opitz)教授进行了很多使用研究,研制了奥匹兹零件分类编码系统,并提出了计算机辅助零件分类成组方法。
较早公开发表的乌尔索和奥匹兹零件编码系统为研制编码系统提供了一些宝贵的经验。
英国也是应用成组技术较早的国家,他发展成组技术的特点是较重视生产单元的建立,则重于生产单元的设备布置,组织管理和经济效果的评定等工作。
60年代以后,日本,美国也积极采用成组技术,并取得了效果。
日本十分重视零件分类便把系统对推广成组技术的作用,机械技术研究所和中小企业振兴事业团,在各企业合作下,自1986年自1976年适应技术的进步主次开发了五个零件分类编码系统(KC-1,2及KK-1,2,3),以供各企业实施成组技术采用或制定本企业系统的参考。
数控机床自1952年在美国问世以来,近30年的生产实践显示了他的一系列优越性。
首先是它具有较大的柔性,能适应不断更新换代的产品加工需要;
是多品种,小批量生产基本上实现了工序自动化,并能获得较高的工序生产率和稳定的加工质量,自70年代以后,美国和其他先进工业国家已认识到,为进一步发挥数控机床的优越性,必须与成组技术相结合,并用成组技术指导它的应用。
现代成组生产单元已广泛采用数控机床和加工中心。
60年代初,苏联注意到现代技术(尤其是计算机技术和数控技术)的迅速发展,注意到联邦德国等欧洲国家开展成组技术的成就和经验,为进一步发展成组技术采取了积极的步骤与措施。
苏联国家计委,国家标准局委托全苏技术信息分类编码研究所,即使用大量人力,花费十年左右时间,于1971年出版了该所研制的苏联农业产品高等分类系统;
并大力发展了包括生产准备(产品设计和工艺设计等)子系统在内的计算机生产管理系统。
由于分类编码方法和技术未见的统一化,使全苏各级技术及管理系统便于联网,由此可实现技术经济信息这一社会智力资源的共享。
成组技术的推广应用及其与计算机,数控等生产技术的机密相结合,必然会推进柔性制造系统(FMS)的创建。
柔性制造系统可理解为由计算机控制,管理的若干台数控机床(包括加工中心)和物料(工件,刀具等)输送机储存系统所组成的一个生产系统,用于加工制造中小批量的多种零件。
所以,可以认为柔性以外,还可以提高设备利用率,这是因为它是计算机控制管理的生产系统,能很好的协调机床,运储装置及工件的工作和运行。
由于柔性制造系统适应目前多品种,小批量生常日益发展的趋势及其技术经济上的优越性,它自60年代末,70年代初一经问世以来,尤其是今年来得到了很大的发展。
据调查,截至1982年至,世界各国共建了203柔性制造系统(包括32个板材,冲柔性制造系统),其中日本和美国分别建立了60套和44套,目前居于领先地位。
柔性制造系统更高级的形式应是把设计,制造和经营管理等方面综合而成为一个计算机辅助的自动生产系统,有人把这种系统称为计算机制造系统(CIMS),它是发展未来的计算机辅助自动化(无人化),最佳化和综合化工厂的基础。
柔性制造系统的出现,标志着人类基本上解决了中小批生产自动化问题,他举有划时代的意义。
成组技术作为一门综合性的生产技术科学是计算机辅助设计,计算机辅助工艺过程设计,计算机辅助制造(CAM)和柔性制造系统等方面的技术基础。
由于多品种,小批生产比重日益增长,工业发达国家均十分重视成组技术的推广应用,据980年国际德尔菲预测,预计到1990~1995年,世界工业先进国家在制造业方面(包括机械及工,装配及电子业装配)成组技术的应用将每年增长10~12%。
我国早在60年代初就在纺织机械,飞机,机床及工程等机械制造业中推广应用成组技术,并初见成效。
当时第一机械工业部制定的“机械加工工艺及其设备十年(1963~1972年)科学发展规划纲要”包括了成组技术的研究与应用。
十年动乱期间,向其他很多科学技术一样,成组技术的研究会与推广工作几乎处于停滞状态,而在此期间,国外成组技术发展迅速,这就加大了我国与世界先进水平的差距。
近年来,为适应我国社会主义四化建设的需要,要求机械工业加速技术改造的步伐,尤其是需要对占重要比例的中小企业进行生产技术和组织管理的革新工作。
因此,成组技术再度受到国家有关部,局和工厂企业,研究院所等院校重视。
目前,正积极开展这方面的科学研究,人才培训和推广应用等工作。
机械委设计研究总院负责组织研制了全国机械零件分了类编码系统JLBM-1,它将对我国推广应用成组技术起到推进作用,某些工业部,局制定了实施成组技术的规划,并选定了试点工厂。
近几年来,一些工厂实践经验表明