t顶底复吹转炉炉型设计说明书DOCWord文件下载.docx
《t顶底复吹转炉炉型设计说明书DOCWord文件下载.docx》由会员分享,可在线阅读,更多相关《t顶底复吹转炉炉型设计说明书DOCWord文件下载.docx(16页珍藏版)》请在冰豆网上搜索。
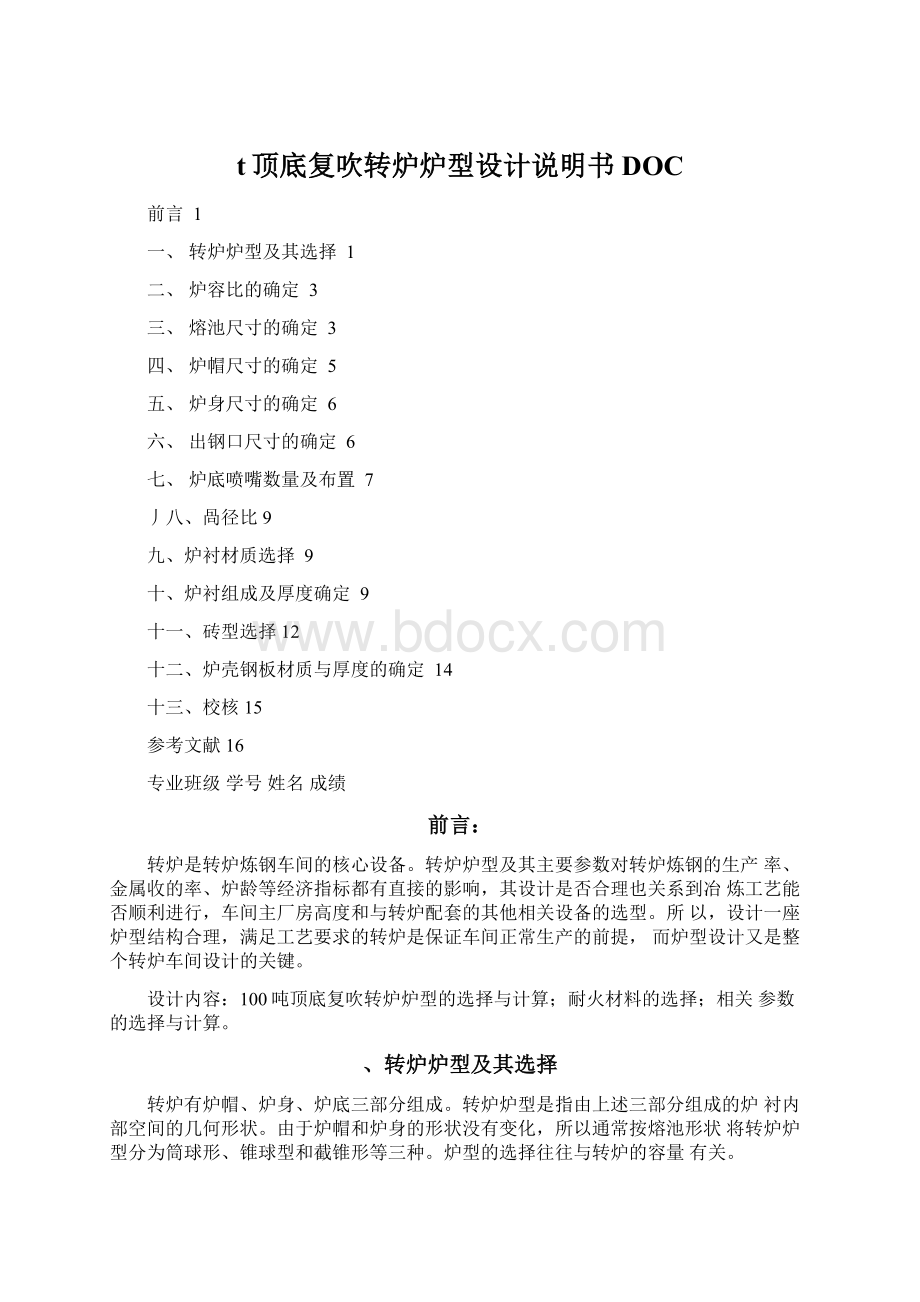
炉粤*2炉障』3炉帽*4出钩口*
5-妒底*6—蟻乂砖
顶底复吹转炉炉型的基本特征如下:
(1)吹炼的平稳和喷溅程度优于顶吹转炉,而不及底吹转炉,故炉子的高宽比略小于顶吹转炉,却大于底吹转炉,即略呈矮胖型。
(2)炉底一般为平底,以便设置喷口,所以熔池常为截锥型。
(3)熔池深度主要取决于底部喷口直径和供气压力,同时兼顾顶吹氧流的穿透
深度,力求保持吹炼平稳。
综上所述,loot顶底复吹转炉采用截锥型炉型较为合适。
二、炉容比的确定
炉容比系指转炉有效容积V与公称容量G之比值Vt/G(m3/t)。
转炉炉容比主要与供氧强度有关,与炉容量关系不大。
当供氧强度提高时,随着炉内反应加剧,如果炉膛自由空间不足,必然会发生大量的渣钢喷溅或泡沫渣翻滚溢出,造
成较多的金属损失。
为了在较高金属收的率基础上增大供氧强度,缩短吹炼时间,
必须有适当的炉容比。
由于顶底复吹转炉吹炼过程比单纯顶吹平稳,且钢渣喷溅
高度也比较低,所以顶底复吹转炉的炉容比可略小于顶吹转炉。
一般取
0.80~1.00m3/t。
对于容量较小的炉子,铁水比大且Si、P、S含量高,以及供
氧强度增加和底部喷口直径大者,取上限。
综上所述,炉容比Vt/G取值为0.95。
乂=0.95G=95m3
三、熔池尺寸的确定
(1)熔池直径D。
熔池直径指转炉熔池在平静状态时金属液面的直径。
转炉吹氧时间t与金属装入量G成正比,而与单位时间供氧量Q成反比,即:
(2-1)
在供氧量增大的情况下,若要避免喷溅趋于严重,就必须扩大熔池面积。
也就是说,单位时间供氧量Q与熔池直径D的平方成正比,即:
(2-2)
2
Q=D
将式(2-1)与式(2-2)合并,得:
(2-3)
上式可写为:
式中D熔池直径,m;
K――系数,参见表2-1;
G新炉金属装入量,t,可取公称容量;
t——平均每炉钢纯吹氧时间,min,参见表2-2
表2-1系数k的推荐值
转炉容量/t
<
30
30~100
>
100
备注
K
1.85~2.10
1.75~1.85
1.50~1.75
大容量取下限,小容量取上限
表2-2平均每炉钢吹氧时间推荐值
冶炼时间/min
12~16
14~18
16~20
结合供氧强度、铁水成分和所炼
钢种等具体条件确定
综上所述,系数k取值为1.75,吹氧时间t取值为16min
熔池直径:
D*;
"
75將4.3枷取D=438°
mm
已知:
「铁二6.9t/m3
贝U:
V池=100=14.4928m3
6.9
(2)熔池深度h。
熔池深度指转炉熔池在平静状态时,从金属液面到炉底的深度。
对于一定容量的转炉,炉型和熔池直径确定后,可利用几何公式计算熔池深度h0
截锥型熔池:
通常倒截锥体顶面直径b:
0.7D。
熔池体积V也和熔池直径D
及熔池深度h有如下关系:
V池二0.574hD2
因而
h4
0.574D
四、炉帽尺寸的确定
顶吹转炉一般都是正口炉帽,其主要尺寸有炉帽倾角、炉口直径和炉帽高度。
(1)炉帽倾角"
倾角过小,炉帽内衬不稳定,容易倒塌;
过大则出钢时容易
钢渣混出和从炉口大量流渣。
倾角一般为60~68,小炉子取上限,大炉子取下
限,这是因为大炉子的炉口直径相对要小些。
综上所述,取二=64
(2)炉口直径d。
在满足顺利兑铁水和加废钢的前提下,应适当减小炉口直径,以减少热损失。
一般炉口直径为熔池直径的43%~53%较为适宜。
小炉子取上限,大炉子取下限。
综上所述,取d=50%D=50%4.380=2.19m=2190mm
(2)炉帽高度H帽。
为了维护炉口的正常形状,防止因砖衬蚀损而使其迅速扩
大,在炉口上部设有高度为H口二300~400mm的直线段。
因此炉帽高度H帽为:
H帽=1/2(D-d)taH口
炉帽总容积V帽为:
V帽(H帽-H口)(D2Ddd2)—d2H口
124
综上所述,取H口=350mm
H帽二-(D-d)tan64H口二1(4.380-2.19)tan640.350=2.595m22
取H帽二2600mm
V帽(H帽-H口)D2Ddd2d2H口二21.0943m3
五、炉身尺寸的确定
转炉炉帽以下,熔池面以上的圆柱体部分称为炉身。
其直径与熔池直径是一
致的,故需确定的尺寸是炉身高度H身。
4V身4(Vt-V帽-V池)
H身22
nDnD
式中:
V帽、V身、V池――分别为炉帽、炉身和熔池的容积;
Vt――转炉有效容积,为y冒、V身、V池三者之和,取决于炉容量和炉容比。
综上所述:
4V身MVt—Vf—V池)4^(95—21.9043—14.4928)—
H身2223.9431m
nDnD兀x4.380
取H身二3950mm
六、出钢口尺寸的确定
出钢口内口一般都设在炉帽与炉身交界处,以使转炉出钢时其位置最低,便
于钢水全部出净。
出钢口的主要尺寸是中心线的水平倾角和直径。
(1)出钢口中心线水平倾角刊。
为了缩短出钢口长度,以利于维修和减少钢液
二次氧化及热损失,大型转炉的弓趋于减小。
国外不少转炉采用0,—般为
O0
15~20。
综上所述,取弓=15
(2)出钢口直径d出。
出钢口直径决定着出钢时间,因此随炉子容量而异。
出钢
时间通常为2~8min。
出钢时间过短(即出钢口过大),难以控制下渣,且钢包内静压力增长过快,脱氧产物不易上浮。
时间过长(即出钢口过小),钢液容易二
次氧化和吸气,散热也大。
通常d出(cm)按下面的经验公式确定:
d出二631.75G
式中G转炉的公称容量,t
d出=:
:
-631.75G=.631.75100=15.43cm
取d出=154mm
七、炉底喷嘴数量及布置
目前对最佳喷嘴数量和布置方式尚无一致看法。
一般说来,喷嘴多而直径小些好。
生产中喷嘴数量常为2~4个,具体视炉子容量和布置形式而定。
本炉喷嘴取3个。
合理的布置应使底吹和顶吹产生的熔池环流运动方向相同,以获得最佳的搅
拌效果,即最快的熔池混匀时间。
为此,应满足以下关系:
RcEXma「1.3RC(7-1)
而
1Rc=H1tan(十一日2)(7-2)
式中Xma炉底喷嘴至炉底中心的最大距离,mm;
Rc——顶吹氧流对熔池的冲击半径,mm;
H1——顶吹氧枪枪位,mm;
4――顶吹氧枪喷孔夹角;
E――顶枪喷出射流的扩张角
顺便指出,如果炉底喷嘴较多,一般只要半数以上能满足式(7-1)的要求
也就可以了。
另外,从实际情况来看,喷嘴呈非对称布置似乎更好些。
要想算出Xmax,必先算出d喉,进而求出H1。
对于普通铁水,每吨钢耗氧量为55~65m3/t(标态),对高磷铁水,每吨钢
耗氧量为60~69m3/t(标态)。
计算氧枪喷头喉口直径:
计算氧流量。
取每吨钢耗氧量为60m3(标态),纯吹氧时间为16min,出钢量按公称容量100t计算,则通过氧枪的氧气流量:
Q=60100=375m3/min(标态)
16
当Ma=2.0时,p/p.=0.1278;
取喷头出口压力p二储二0.101MPa,则喷口滞
止氧压为:
0.101
p0.790MPa
0.1278
每个喷孔氧气流量为:
q---93.75m/min(标态)
44
由于
AMp0
q=1.783Cd牛」0xjT0
取Cd-0.95,To=300K,又p。
=0.790MPa,代入上式,则
93.75=1.7830.95込0790忖
4V300
由上式可求出
d喉二39.3mm
顶吹氧枪枪位H1一般为35~50倍的d喉
取弓=10=10
A__
Rc^HNanQ—^)=1783tan(105)=473.9mm
则
473.9乞Xmax乞616.07
Xmax二550mm
八、咼径比
高径比系指转炉炉壳总高度H总与炉壳外径D壳之比值。
实际上它只是作为
炉型设计的校核数据。
因此当炉膛内高H内和内径D确定后,再根据所设计的炉
衬和炉壳厚度,高径比也就被确定下来了。
增大高径比对减少喷溅和溢渣,提高
金属收的率有利。
但是高径比过大,在炉膛体积一定时,反应面积反而小,氧气
流股易冲刷炉壁,对炉衬寿命不利,而且导致厂房高,基建费用大,转炉倾动力
转炉由细高型趋于矮胖
1.25~1.45。
大炉子取下
Si、P、S含量高,以及
矩大,耗电大。
随着转炉大型化和顶底复吹技术的采用,
型,即高径比趋于减小。
顶底复吹转炉高径比推荐值为限,小炉子取上限。
对于容量较小的炉子,铁水比大且
供氧强度增加和底部喷口直径大者,取上限。
九、炉衬材质选择
转炉炉衬寿命是一个重要的技术经济指标,受许多因素的影响,特别是受冶炼操作工艺水平的影响较大。
但是,合理选用炉衬(特别是工作层)的材质是提高炉衬寿命的基础。
根据炉衬的工作特点,其材质选择应遵循一下原则:
(1)耐火度(即在高温条件下不熔化的性能)高;
(2)高温下机械性能高,耐急冷急热性能好;
(3)化学性能稳定;
(4)资源广泛,价格便宜。
近年来氧气转炉炉衬工作层普遍使用镁碳砖,炉衬寿命显著提高。
但由于镁碳砖成本较高,因此一般只用于诸如耳轴区、渣线等炉衬易损部位。
十、炉衬组成及厚度确定
通常炉衬由永久层、填充层和工作层组成。
有些转炉则在永久层与炉壳钢板
之间夹有一层石棉板绝热层。
永久层紧贴炉壳(无绝热层时),修炉时一般不予以拆除。
其主要作用是保护炉壳,该层常用镁砖砌筑。
填充层介于永久层和工作层之间,一般用焦油镁砂捣打而成,厚度约80~100mm。
其主要功能是减轻炉衬受热膨胀时对炉壳产生挤压和便于拆除工作层,也有的转炉不设填充层。
工作层系指与金属、熔渣和炉气接触的内层炉衬,工作条件及其苛刻。
目前,该层多用镁碳砖和焦油白云石砖综合砌筑。
炉帽可用二步煅烧镁砖,也可根据具体条件选用其他材质。
转炉各部位的炉衬厚度设计参考值如下表所示
炉衬各部位名称
100~200
200
永久层厚度/mm
60~115
115~150
工作层厚度/mm
400~600
500~600
550~650
炉身(加料侧)
115~200
550~700
700~800
750~850
炉身(出钢侧)
500~650
600~700
650~750
炉底
300~450
350~450
550~600
600~650
600~750
综上所述,转炉各部位的炉衬厚度为:
115
500
700
600
450
炉衬材质性能及使用部位
气孔率%
体积密度
g/cm
常温耐压强
度MPa
咼温抗折强
使用部
位
优质镁碳砖
2.82
38
10.5
耳轴、渣线
普通镁碳砖
4
2.76
23
5.6
耳轴部位、
炉帽液面以
上
复吹供气砖
2.85
46
14
及保护砖
高强度镁碳
砖
10〜15
2.85〜3.0
40
炉底及钢液
面以下
合成高钙镁
2.85〜3.1
50
装料侧
咼纯镁砖
2.95
60
镁质白云石
烧成砖
2.8
38.4
(3)炉衬的装料侧。
这个部位除受吹炼过程熔渣和钢水喷溅的冲刷、化学侵蚀
外,还要受到装入废钢和兑入铁水时的直接撞击与冲蚀,给炉衬带来严重的机械
性损伤,因此应砌筑具有高抗渣性、高强度、高抗热震性的镁碳砖。
(4)炉衬出钢侧。
此部位基本上不受装料时的机械冲撞损伤,热震影响也小,
主要是受出钢时钢水的热冲击和冲刷作用,损坏速度低于装料侧。
若与装料侧砌
筑同样材质的镁碳砖时,其砌筑厚度可稍薄些。
(5)渣线部位。
这个部位是在吹炼过程中,炉衬与熔渣长期接触受到严重侵蚀而形成的。
在出钢侧,渣线的位置随出钢时间的长短而变化,大多情况下并不明显,但在排渣侧就不同了,受到熔渣的强烈侵蚀,再加上吹炼过程其他作用的共同影响,衬砖损毁较为严重,需要砌筑抗渣性能良好的镁碳砖。
(6)两侧耳轴部位。
这部位炉衬除受吹炼过程的蚀损外,其表面又无保护渣层覆盖,砖体中的碳素极易被氧化,并难于修补,因而损坏严重。
所以,此部位应砌筑抗渣性能良好、抗氧化性能强的高级镁碳砖。
(7)熔池和炉底部位。
这部位炉衬在吹炼过程中受钢水强烈的冲蚀,但与其他部位相比损坏较轻。
可以砌筑含碳量较低的镁碳砖,或者砌筑焦油白云石砖。
若是采用顶底复合吹炼工艺时,炉底中心部位容易损毁,可以与装料侧砌筑相同材质的镁碳砖。
(8)转炉出钢口。
转炉的出钢口除了受高温钢水的冲刷外,还受温度急变的影
响,蚀损严重,其使用寿命与炉衬砖不能同步,经常需要热修理或更换,影响冶炼时间。
改用等静压成型的整体镁碳砖出钢口,由于是整体结构,更换方便多了,材质改用镁碳砖,寿命得到大幅度提高,但仍不能与炉衬寿命同步,只是更换次数少了而已。
十一、砖型选择
砌筑转炉炉衬选择砖型时应考虑以下一些原则:
(1)在可能条件下,尽量选用大砖,以减少砖缝,还可以提高筑炉速度,减轻劳动强度;
(2)力争砌筑过程中不打或少打砖,以提高砖的利用率和保证砖的砌筑质量;
(3)出钢口用高压整体成形专用砖,更换方便、快捷;
炉底用带弧形的异形砖;
(4)尽量减少砖型种类
炉衬的砌筑
砌筑过程:
第一步:
炉底工作层预砌筑、搭建耐火泥浆搅拌站、搭设临时切砖房、耐火砖的加工、出钢口座砖施工、炉底施工。
第二步:
砌筑永久层第一层和第二层的镁质砖,先沿中心线砌出十字形,后分四部分采用人字形方式砌筑。
各层之间错开45度。
第三步:
砌筑炉底中心砖和第一环工作层砖。
第四步:
砌筑永久层第三层砖,其砌筑方式与第一和第二永久层相同。
第五步:
砌筑炉底工作层砖,整个炉底工作层1〜8砖环缝全部用泥浆湿砌,1〜24环砖放射缝要求每隔5块中有1块砖放射缝打灰湿砌。
砌筑时若每环砖环缝面有错台时,则可用角向磨光机进行研磨。
第六步:
炉底风口部位的砌筑,当炉底工作层砖钢至风口旁时,先干摆并调整风口工作层砖,量出加工砖的上下口尺寸。
第七步:
砌筑炉底结合部的工作层砖,将已预加工好的炉底工作层砖,在顺序进入炉内砌筑,局部不平处,可用研磨机磨平。
然后在最外环底部充填捣打料,并砌筑接头层砖。
十二、炉壳钢板材质与厚度的确定
转炉吹炼过程中,炉壳承受多种负荷,有炉壳、炉衬自重和炉料重引起的静负荷,有兑铁水、加废钢时的冲击以及炉体旋转时产生的动负荷,还有炉衬热膨
胀和炉壳本身温度分布不均匀引起的热负荷。
这些负荷必然使炉壳承受相应的应力,以致引起不同程度的变形。
研究表明,其中热应力起主导作用,所以设计时力求选用抗蠕变强度高、焊接性能好的材料。
大中型转炉多用耐高温、高压的锅炉钢板制作炉壳,也有用合金钢板的。
国内用于制作炉壳的低合金高强度钢有16Mn、14MnNb、20g等。
由于应力计算相当复杂,所以炉壳钢板的厚度常按下表中的经验公式确定
01mm
62/mm
d/mm
(0.8~1.0)6
(0.0065~0.0008)D壳
0.8芳2
6:
炉帽钢板厚度
§
2:
炉身钢板厚度
(0.8~0.9疋2
(0.008~0.011)D壳
(0.8〜1.0)E
6:
炉底钢板厚度
D壳:
炉壳外径
几种炉子容量的实际炉壳尺寸
炉子容量/t
15
120
150
300
炉帽钢板厚度/mm
24
55
58
75
炉身钢板厚度/mm
70
80
85
炉底钢板厚度/mm
20
45
62
炉壳咼度/mm
5530
7000
7470
9750
8992
11575
炉壳外径/mm
3548
4220
5110
6670
8670
综上所述,loot顶底复吹转炉选定各部位钢板厚度为:
炉帽钢板厚度:
「=55mm
炉身钢板厚度:
学=65mm
炉底钢板厚度:
=65mm
十三、校核
H总=H帽H身h工作层'
永久层、3=26003950132060045065二8985mm
11
D壳=2(—D、加料侧工乍层'
填充'
永久层、2)=2(—43807008011565)6300mm22
H总/D总=8985/63001.43
顶底复吹转炉高径比推荐值为1.25~1.45,大炉子取下限,小炉子取上限。
故对于100t顶底复吹转炉符合要求。
参考文献
[1]王令福•炼钢厂设计原理•北京:
冶金工业出版社,2009.
[2]李传薪•钢铁厂设计原理(下册)•北京:
冶金工业出版社,1995.
[3]汪海涛•冶金机械设计手册•北京:
中国科技文化出版社,2006.
[4]冯聚和•炼钢设计原理•北京:
化学工业出版社,2005.
⑸徐文派•转炉炼钢学•北京:
冶金工业出版社,1988.
⑹文U浏•中国转炉炼钢技术的进步•钢铁,2005,40
(2):
1~5