最新单晶炉异常处理Word下载.docx
《最新单晶炉异常处理Word下载.docx》由会员分享,可在线阅读,更多相关《最新单晶炉异常处理Word下载.docx(7页珍藏版)》请在冰豆网上搜索。
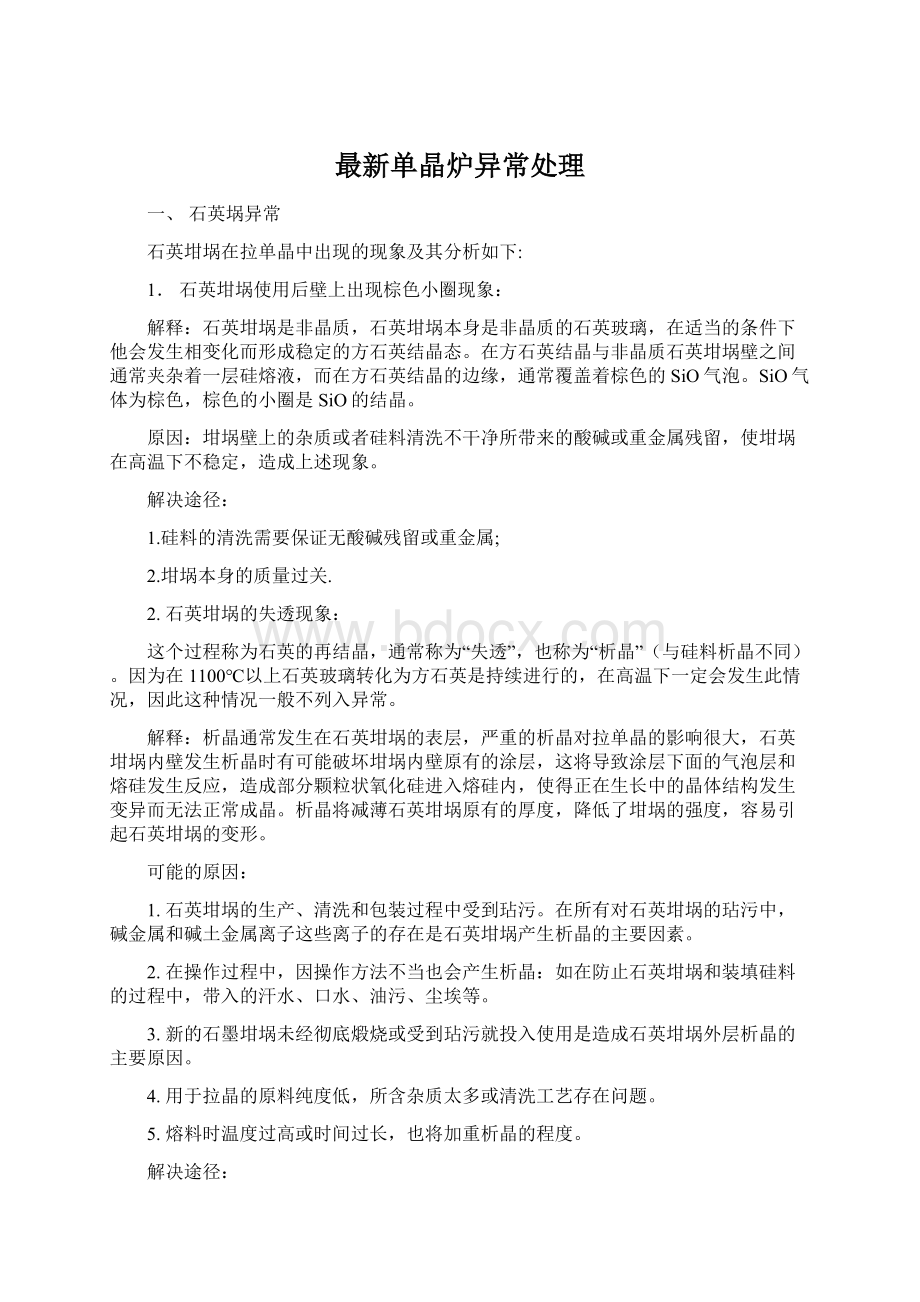
析晶通常发生在石英坩埚的表层,严重的析晶对拉单晶的影响很大,石英坩埚内壁发生析晶时有可能破坏坩埚内壁原有的涂层,这将导致涂层下面的气泡层和熔硅发生反应,造成部分颗粒状氧化硅进入熔硅内,使得正在生长中的晶体结构发生变异而无法正常成晶。
析晶将减薄石英坩埚原有的厚度,降低了坩埚的强度,容易引起石英坩埚的变形。
可能的原因:
1.石英坩埚的生产、清洗和包装过程中受到玷污。
在所有对石英坩埚的玷污中,碱金属和碱土金属离子这些离子的存在是石英坩埚产生析晶的主要因素。
2.在操作过程中,因操作方法不当也会产生析晶:
如在防止石英坩埚和装填硅料的过程中,带入的汗水、口水、油污、尘埃等。
3.新的石墨坩埚未经彻底煅烧或受到玷污就投入使用是造成石英坩埚外层析晶的主要原因。
4.用于拉晶的原料纯度低,所含杂质太多或清洗工艺存在问题。
5.熔料时温度过高或时间过长,也将加重析晶的程度。
1.石英坩埚的生产厂商要保证其生产的坩埚从用料到生产的各个环节都符合质量要求。
2.在单晶生产的整个过程中应严格按照工艺规程认真操作。
3.拉晶所用的原料纯度一定要符合生产要求,如果原料本身所含杂质较多,在熔料过程中也会造成析晶。
尤其是碱金属离子的存在,将会降低析晶温200~300℃.
4原料的清洗一定要符合工艺要求,经过酸或碱处理的原料如果未将酸碱残液冲洗彻底,易造成析晶。
5新的石墨器件,如石墨坩埚因含有一定的灰粉和其它杂质,在投入使用前须经过彻底的高温煅烧才能使用。
6.熔料时应选用合适的熔料温度以减少析晶或降低析晶的程度。
3.石英坩埚的变形现象:
石英坩埚使用后变形影响:
1.石英坩埚变形后,在拉晶过程中随着埚位的上升,石英坩埚变形的凸出部分将碰撞到导流筒,影响或无法继续正常的拉晶。
2.溶料中发生挂边造成的石英坩埚变形,坩埚上口向内凸出过多,当熔完料埚位上升到正常引晶位置时,已碰撞到导流筒,这将直接导致不能拉晶的严重后果。
3熔料中发生鼓包且鼓包较大时,在拉晶过程中随着液位的下降,鼓包会渐渐露出液面,这时已经拉出的晶棒会碰擦鼓包,如不及时停炉会发生晶棒跌落的严重事故。
1.装料方法不当,在液位线上的料与石英坩埚的接触呈面接触状态,这在熔料过程中容易发生挂边导致坩埚变形。
坩埚最上部全部装了碎小细料,这在熔料时易发生下部已溶完,上部呈结晶状态而造成坩埚变形。
2熔料时温度过高或时间过长,由于硅熔点为1420℃,一般的熔料温度在1550~1600℃左右,如果熔料温度过高,在熔料过程中极易发生变形。
3温度过低,当熔料料温度偏低时,坩埚上部的料与埚壁接触处易发生似熔非熔的状态,当下部料熔完上部已挂边的块料将石英坩埚下拉而发生变形。
4原料质量参差不齐,所含杂质远高于原生多晶,酸洗工艺不尽完善,这对坩埚的正常使用影响也非常大,主要表现在容易发生严重析晶。
5石英本身存在质量问题。
石英坩埚在生产,清洗,包装中受到玷污,发生析晶(包括液位线以上的部分)这样石英坩埚原有的厚度会减薄,强度也随之下降,容易发生变形。
6.石英埚与新石墨埚反应,若石墨埚为新石墨埚则可能会因为石墨埚结合紧密,石英埚在高温下扩散到表面的二氧化硅与石墨埚反应产生的气体或新石墨埚未彻底煅烧在加热后挥发出的挥发物不能及时排出导致变形的发生。
1石英坩埚的生产厂商要保证其生产的坩埚从用料到生产的各个环节都符合质量要求。
2在单晶生产的整个过程中应严格按照工艺规程认真操作。
3拉晶所用的原料纯度一定要符合生产要求,如果原料本身所含杂质较多,在熔料过程中也会造成析晶。
尤其是碱金属离子的存在,将会降低析晶温200~300℃.
4原料的清洗一定要符合工艺要求,经过酸或碱处理的原料如果未将酸碱残液冲洗彻底或混入杂质,易造成析晶。
5.熔料时应选用合适的熔料温度以降低析晶的程度。
4.硅料于石英坩埚壁析晶
这个过程为硅料结晶,称为“析晶”(与石英的析晶不同)。
现象:
在石英坩埚壁被熔硅浸泡过的区域,出现黑点,严重时会有大块硅料附着在坩埚壁上。
1石英坩埚的生产,清洗,包装过程中受到玷污,在所有对石英坩埚的玷污中,碱金属和碱土金属离子这些离子的存在是石英坩埚产生析晶的主要原因。
2在操作过程中,因操作方法不当也会产生析晶:
3用于拉晶的原料纯度低,所含杂质太多或清洗工艺存在问题。
4熔料时温度过高或时间过长,也将加重析晶的程度。
石英坩埚在生产、清洗、包装中受到玷污,也将发生析晶。
3拉晶所用的原料纯度一定要符合生产要求,经过酸、碱处理的原料如果未将酸碱残液冲洗彻底或混入杂质,易造成析晶。
4.熔料时应选用合适的熔料温度以降低析晶的程度。
二、漏硅&
渗硅
漏硅和渗硅的处理在于:
拆炉时找到石英坩埚的初始漏点或裂纹,再根据漏点或裂纹情况(位置、形状、异常发生时间等),仔细分析可能存在的情况,主要看石英坩埚在装料结束之前是否受损。
再去确定原料的原因以及石英坩埚本身质量原因。
由于导致坩埚渗硅漏硅的因素并不是很多,但在没有明显特征的情况下很难定性到底是什么原因,可能是其中的一种也可能是其中几种共同作用的结果。
原因可以大胆分析,判定要谨慎!
1熔料的方法不当,上部硅料熔化后沿着坩埚内壁向下流到底部如果底部温度过低会发生二次结晶,硅料在二次结晶时会膨胀而把石英埚撑破。
2上部硅料熔完后,由于硅的液体密度比固体密度大,底部没熔完的料往往会翻上来,上翻的过程中有可能将埚拉破。
3熔料温度太高加剧析晶的程度,增大的破裂的可能性。
4原料内杂质太多对石英埚腐蚀严重导致漏硅。
5新的石墨埚因煅烧不彻底就使用,使石英坩埚外层严重析晶而破裂。
6石英埚在使用时因操作不当,如与石墨埚磕碰,或装料时与料磕碰或塌料时料与埚磕碰等原因产生隐裂而导致漏硅。
7当石墨埚与加热器打火时,则有可能由于打火将石墨件打穿,导致石英埚破裂漏硅。
2在单晶生产的整个过程中应严格按照工艺规程认真操作,防止装料时硅料磕碰石英埚,不得将大块料尖角对准底部,石英埚底部放小块料防止化料过程底部没熔完的料翻上来把坩埚拉破。
3化料过程中加热功率不能过高,埚位不能降得太低。
4拉晶所用的原料纯度一定要符合生产要求,经过酸、碱处理的原料如果未将酸碱残液冲洗彻底或混入杂质,易造成原料与坩埚起反应导致漏硅。
三、石墨件异常
由于石墨件是可反复使用的部件,同时石墨件不直接接触原料,因此石墨件发生异常主要由人为操作不当、石墨件质量差两个可能原因引起。
表现出来的现象主要为裂纹、打火。
石墨件出现裂纹时,应首先考虑四点可能原因:
1.石墨件是否被磕碰过。
在操作过程中,石墨件被磕碰而产生隐裂甚至裂纹。
2.若出现打火的情况,也有可能由于打火起弧产生瞬间的高压、高温导致裂纹。
3.存放环境,长期不用后未煅烧就使用或未煅烧彻底。
4.升温、降温时的加热功率是否按照工艺进行,主要在冷却降温拆炉这段时间。
使用者在拉晶的时候又会有一个缩短升温时间和冷却时间以及拆炉时间的想法,提高生产效率无可厚非,这个可以理解。
但是石墨这种材质能不能顶得住这个降温速度是表问题。
石墨材料在温度升高的情况下,强度方面会提高;
换言之就是在温度降低的时候强度会降低。
降温过快,外壁和内壁之间的温差引起的应力,是否超过了坩埚所能承受的范围,
排除以上四点后,方可考虑石墨件质量问题。
预防措施:
1.在安装热场前,须认真检查石墨件是否出现裂纹。
确认无误后,方可安装。
2.升温、降温阶段须严格按照作业指导书进行,特别是加热化料阶段,温度变化大,则可能导致产生裂纹。
3.加热器与石墨电极,石墨电极与铜电极,加热器与加热器螺栓之间必须紧密接触。
石墨件出现打火时,则应考虑以下可能原因:
1.装料时是否有硅料掉落在加热器与保温筒之间;
若有则在加热过程中会导致加热器与保温筒打火。
2.化料时埚位是否降得太低;
若有则在加热过程中会导致加热器与埚托打火。
3.石墨件打火前,就因为某些原因出现裂纹;
4.石墨件未清洗干净导致打火。
2.加热器与石墨电极,石墨电极与铜电极,加热器与加热器螺栓之间必须紧密接触。
否则就可能
3.埚位不能降得太低,若埚位降得太低,加热器电极脚和埚托之间可能由于距离太近而导致打火。
4.石墨件必须清洗干净。
特别是加热器片与片之间,若石墨件未清扫干净,则可能由于挥发物突起或挥发物遇热变为气体导致起弧打火。
四、拉制异常
1.晶棒高、低阻:
晶棒的电阻率超出要求的1—3Ω/cm范围,即为晶棒电阻率异常。
晶棒电阻率异常的主要原因:
人为操作不当,原料电阻率分布不均,计算公式的误差。
人为操作不当:
1.备料时,混入杂质,料未洗净。
2.装料时,原料被污染(汗水、灰尘等)
3.未放入母合金。
原料电阻率分布不均:
原料由于品质差,电阻率波动大。
计算公式的误差:
由于计算公式是将原料按电阻率分档,再按所在档区的平均电阻率计算由此产生误差。
1.在整个过程中应严格按照工艺规程认真操作。
2.装料应勤换PVC手套,尽量快的装完料。
3.装料前先将合金放入石英埚,防止遗忘。
4.装料时不要接触其他物体防止交叉污染。
2.晶棒裂纹:
晶棒产生裂纹的原因很多,主要有晶棒冷却不足导致裂纹,还有在晶棒搬运过程中由于磕碰产生裂纹或截断时产生裂纹。
晶棒裂纹的可能原因有:
1.A段冷却时间未达到规定的3个小时或收尾未按规定冷却5个小时
2.在晶棒取出、搬运或磕碰产生裂纹
3.截断时由于各种原因产生裂纹(具体原因应询问此步骤相关人员)
1.A段:
应在提断后给定晶升拉速2.0mm/min提升单晶上升1.5小时至导流筒中上部;
然后看晶升计长提升单晶100mm至导流筒上部;
拉速保持在3mm/min提升20min后看计长按晶快速提升单晶500mm;
拉速保持在3mm/min提升单晶20min后看计长按晶快速上升单晶至副室,将晶升归零并关闭电源。
2.收尾完成提断后:
晶升拉速调整到1.0mm/min,使单晶自动上升,晶转设定为2r/min,埚转为0转。
18寸热场冷却4小时,20寸热场冷却5小时,22寸热场冷却5.5小时
3.其他工段也应小心谨慎,避免磕碰。
3.晶棒未拉出(闷炉):
晶棒未拉出导致闷炉或提料,其可能的原因可以分为:
1.原料太脏,由于原料中渣太多,导致引放转不活或等径长度不够就断棱。
2.坩埚质量太差,由于坩埚质量有问题,于是出现坩埚涂层脱落、石英砂脱落等导致闷炉。
3.清炉未清干净,由此导致引放转、等径时有渣落下,导致闷炉。
排气孔未清理彻底导致气流紊乱,产生闷炉
4.部件老化:
如重锤老化导致拉制过程中掉渣下去,导致闷炉。
5.人为操作:
如拉制时氩气未开,导致拉不出晶棒闷炉。
闷炉,预防措施:
1.控制原料的杂质含量和清洗质量,防止原料中渣太多,导致的闷炉。
2.石英坩埚的生产厂商要保证其生产的坩埚从用料到生产的各个环节都符合质量要求。
3.车间应按作业指导书操作,防止清炉未清干净,排气孔不通。
4.每炉必须检查部件是否老化。
三瓣埚可能的质量缺陷:
1.设计缺陷。
因为这个原因坩埚断裂后表现一般就是在r部与上部坩埚结合部位,一般为横向断裂,且一般是两侧断口低中间高;
如果是全部裂开后再拼到一起的话,可以明显发现两端拼接口不能重合。
真正的原因是在使用后坩埚上部壁厚均匀部分和下部逐渐变厚部分的应力集中在这个部位,造成应力集中,最终造成三瓣坩埚断裂。
2.加工缺陷。
这类原因造成的坩埚断裂后表现一般是从接缝处开裂,然后蔓延开。
通常是沿垂直方向裂开,这类问题发生后比较容易发现。
造成这类问题的原因主要是接缝过渡的角度(一般是105°
或者115°
)在相交点部分,没有采用倒圆角缓冲,加之加工过程中刀尖部分对埚体的微观撕裂,以及使用过程中坩埚本身的应力,造成开裂。
3.原料缺陷。
这个原因其实是最大的原因。
因为石墨坩埚本身的物理性能,主要是导热、热膨胀这两方面的原因,导致坩埚在速冷速热的情况下,容易产生应力且不容易消除;
另外在石墨生产过程中,石墨的压型、浸渍、焙烧、石墨化和提纯过程时间长,不容易监测检验,虽然整体表现比较均一,但是在同一块石墨内部各个部分之间还是存在一定的差异性,这就决定了石墨从根本上会存在一定的问题。