苏州三光慢走丝培训资料Word下载.docx
《苏州三光慢走丝培训资料Word下载.docx》由会员分享,可在线阅读,更多相关《苏州三光慢走丝培训资料Word下载.docx(63页珍藏版)》请在冰豆网上搜索。
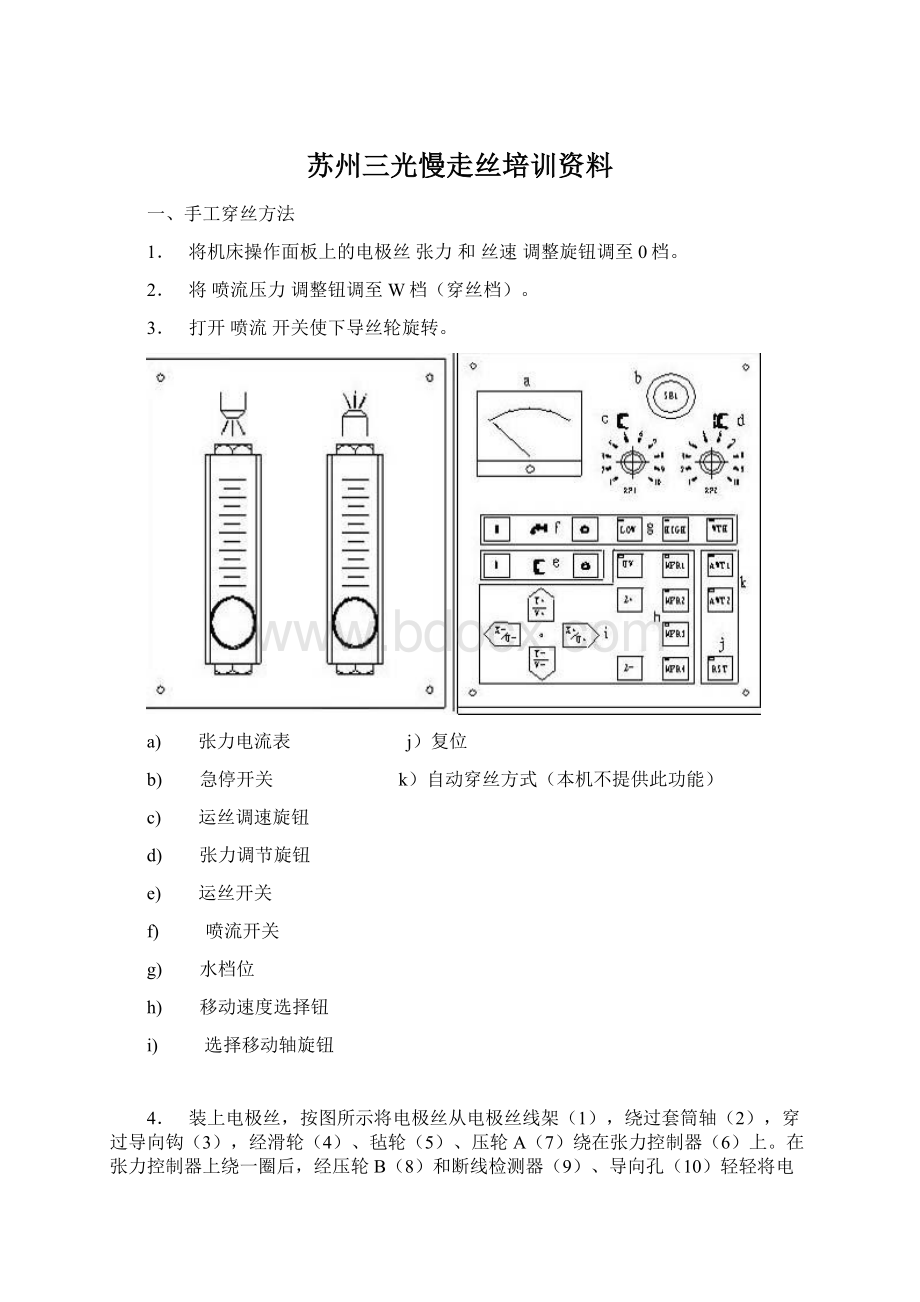
夹具超过工作台
工件安装好以后用千分表将工件拉平。
(工件的基准面对工作台移动方向倾斜时,可移动X轴或Y轴根据千分表上的读数变化,用铜棒等轻打工件,调整工件使工件基准面与移动方向平行,拧紧固定螺丝。
)
工件装夹不平,会造成上下喷流的流量差异,将会使断丝的次数明显增加,还会直接影响到加工精度。
工件的定位
对边(端面定位)
即边缘找正。
用于X及Y轴的四个方向的边缘找正。
在移动菜单下按F3键进入对边的操作界面,可以选择X、Y轴的四个方向(+X、-X、+Y、-Y)任一方向进行边缘找正。
边缘找正的开始时铜丝沿指定的方向高速接近工件直至接触,然后回退,降低移动速度后重复上述过程,边缘找正完成。
(为了提高找正精度,在边缘找正开始前,把反张力电位器顺时针旋至最大位置,把张力电位器逆时针旋至底,即张力减至最小。
)按F9键返回上一级菜单。
N注:
铜丝的回退距离系统默认为0.02mm,在系统菜单中可以设定回退的距离。
2.内孔定位
即中心找正,此命令完成对称图形内孔的中心找正。
在移动菜单下按F4键进行定中心操作,按F9键返回上一级菜单。
定中心的操作可以参照边缘找正时张力、反张力电位器的调整方法来提高精度。
“对边”与“定中心”要求工件侧面或内孔干净、光滑,否则会影响找正精度。
五、端面加工方法
端面定位已经终了,电极丝在开始位点。
选择适当的加工条件:
C000或C890。
(此为端面加工专用条件)
移动Z轴,使之离工件上表面10~20mm处(见图例)
操作面板上的电极丝张力旋钮调至0.2A(1200gf),电极丝速度旋钮调至6段以上。
打开喷流开关,调节流量。
(下侧流量:
微量,上测流量:
1~2公升/分,使包在铜丝四周的水柱不散开、不跳跃。
)
<
1>
喷流调节很好时,放电产生的火花很均匀且呈青白色。
(图A)
2>
下部有橙黄色的火花产生(图B)。
由于上部流量太少,电极丝下部淋不到冲液,所以产生在空中放电,有断丝之虑。
解决方法:
调大上部流量使水柱包住电极丝。
3>
在上部橙黄色火花产生(图C)。
由于上部流量太多,在工件上面产生空隙,放电在空气中进行,有断丝之虑。
调小上部流量使水柱包住电极丝。
4>
加工到端面的2~4mm地方时,通常喷流的状态会发生变化,所以要观察橙黄色火花在工件端面的位置,不断调节上喷流的流量。
5>
当上喷流的水柱越过工件的端面后,下部的喷流也要开始打开。
Z轴方向定位
用缝隙规定位
放厚度0.1mm左右的缝隙规在喷嘴的正下方。
按移动键下降Z轴,把喷嘴贴在缝隙规上。
Z轴上升一点点,要确认缝隙规的滑动好不好。
缝隙规的滑动不好时,再如上重复做一次。
看着流量计定位(常用方法)
嘴移动到离端面10mm以上的工件上面。
(喷嘴正下方没有孔的地方等)
把上部和下部的流量调节阀开足,打开冲液开关,把高压泵开
关打开。
(这时候本来的压力是15~18kg/cm2。
为了防止水飞溅出来,请预先安装防水罩
一边缓慢下降Z轴,一边看上部和下部的流量
上部和下部的流量到5~7公升时停止下降Z轴。
(上下喷嘴流量基本相等)
Z轴接近工件时小心千万不要和工件撞上!
!
六、锥度加工的各类项目输入方法
Z轴移动到正极限,设定Z轴坐标为270mm
下降Z轴,把上部喷嘴接进工件的上表面做Z轴方向的定位。
(由于工件的形状而不能接近喷嘴的时候,防止喷嘴与工件接触要仔细调整Z轴的高
度。
正确读取Z轴的读数。
在形参数HA、HB、HC、HD、HP中输入合适的数据。
(见图)
A:
下侧导丝模的位置
B:
在Z轴读数为零时上侧导丝模的极限位置
C:
加工时上侧导丝模的位置
HA:
下导丝模与夹具体之间的距离(机床固有值,不要改变。
HB:
夹具体与编程面之间的距离
HC:
夹具体与参考平面之间的距离,注意HB必须不能等于HC
HD:
锥度加工时的Z轴坐标
HP:
上、下导丝模之间的距离减去Z轴坐标所得的值,即Z轴的极限
距离。
(机床固有值,不要改变)
加工条件的设定
加工条件参数的说明
加工条件参数
功能
设定范围
on
放电脉冲时间
00~09,10~19
OFF
休止脉冲时间
00~31
IP
主电源峰值电流
00~17
HP
辅助电源电路
0~9
MA
休止脉冲时间调节
M:
0~9,A:
0~9
SV
伺服基准电压
V
主电源电压
00~03
SF
伺服速度
00~09
C
极间电容回路
00~04
WT
电极丝张力
00~15
WS
电极丝速度
ON
放电脉冲时间
放电脉冲时间(在极间施加电压的时间)的设定,数值越大放电能量越大。
OFF
休止脉冲时间(在极间不施加电压的时间)的设定,数值越大放电能量越小。
IP
主电源峰值电流
设定放电电流的最大值。
一个脉冲能量的大小,基本上由IP、ON和V来决定,
设定范围为0~17,其值越小,断丝的可能性越小,但加工效率和加工电流会降低。
粗加工时:
IP=16或17(电流表0~40A档)
精加工时:
IP=15,16
(IP≤15时,电流表0~4A档)
HP
辅助电源电路
设定加工不稳定时放电脉宽时间,其设定值不能比ON大,设定范围为0~9。
其值越小,断丝的可能性越小,但加工效率和加工电流会降低。
MA
休止脉冲时间调整
M:
设定加工过程中的检测电平,设定范围为0~9。
A:
设定加工不稳定时的放电休止脉冲时间,设定范围为0~9
M、A的值越大,加工越稳定,不容易断丝,但加工效率会降低。
SV
伺服基准电压
放电间隙设定的功能。
电极丝和工件间的加工电压设定。
数值越大平均加工电压越高,加工越稳定,但电压越高放电间隙越大,加工效率越低。
V
主电源电压
跟IP、ON一起决定放电脉冲的能量。
粗加工时:
03
精加工或细电极丝加工时:
00~02
SF
伺服速度
为了维持极间基准电压设定各轴追随移动的速度。
WT
电极丝的张力设定
设定施加在电极丝上的拉力,也可以通过操作面板上的张力旋钮来调整。
WS
电极丝的速度设定
设定电极丝的运行速度,加工能量越大,电极丝的运行速度须越快。
运丝速度
太慢,则容易造成断丝。
也可以通过操作面板上的丝速旋钮来调整。
工作液电导率
工作液电导率的高低,对加工起着重要的作用。
如果工作液电导率太低,将导
致不能放电加工。
通常工作液电导率为5×
104Ω·
cm,
工作液电阻和工作液电导间的关系如下:
工作液电导率(μs)=1/工作液电阻(Ω·
cm)×
106
喷流
在电火花线切割机床中,喷流对加工的稳定性、生产效率和加工精
度起着至关重要的作用。
为了高速、高精度加工,要处理好喷流。
【几种不同的加喷流状态】
F水准——高速加工
上下喷嘴都贴紧…………………图
(1)
E水准——形状精度加工
D水准——单侧开放加工
上侧或下侧有一侧没有贴紧……图
(2)
两侧开放加工
………………………………………………………图(3)
多次加工时用E水准的加工条件
喷嘴靠近加工时:
上下喷嘴与工件的间隙0.05~0.1mm
压力12kg/cm2,上下喷嘴流量5~6公升/分
把喷嘴靠近工件时的加工速度当作100%时
上部开放加工(图例2)60~70%
上下开放加工(图例3)30~40%
所以要高速、高精度加工,应使喷嘴贴紧工件表面加工,上下导丝膜的距离越长,电极丝的振幅越大,精度越低。
七、加工问题的对策和保养项目
1.短路
【加工开始时发生短路】
加工开始时电极丝一接触工件,就发生短路。
减低张力,用手振动电极丝,使加工再开始。
B:
去除工件表面的铁锈。
在开始孔内短路停止加工。
(由于孔的位置差距,电极丝已经接触工件)
从不接触位置至加工开始位置做直线加工。
导电块、导向器老化,极间电线损耗引起的短路。
解决办法:
移动导电块位置,更换导向器,清洗极间电线。
【加工中发生短路】
(1)使Z轴上升观察加工部位,明确接触的原因,用气枪扫除。
再试一次加工,不能加工时回到加工开始位置进行加工。
(已经加工的地方再来一次加工时,把参数降低再加工,可用C888的电参数。
(2)二次加工以后发生短路时,要确认加工条件、流量、压力及张力,跟
(1)一样
的办法实行。
在第三次加工短路停止加工时,从第二次再开始加工。
(回到第二
次加工开始位置,用第二次加工条件再开始加工。
2.断丝(加工中断丝频繁发生。
把加工条件参数的OFF与ON减弱。
(例如OFF从14换至16)要考虑到工件内有无杂质。
跟据工件的材质、电极丝的直径、上下喷嘴的位置,选择适当的加工条件,再加以考虑工作液电导率的影响。
调整喷流,特别是从端面开始加工或端面附近加工时。
除去生锈工件表面的铁锈,(工作液的电阻太低时或用未处理的工件时容
易生锈,要注意。
(4)
其它原因
导电块的损耗
极间电线的损耗
喷流压力的大小
丝的张力太高
丝的速度太低
丝的安装方法不好,有叠丝
在丝的排出部位有缠丝
下臂的滑轮不旋转
……
在加工面上有黄铜附着
黄铜附着是1次加工后在加工端面上附着的一层黄色异物。
(附着量太多时凸部与凹部两方会粘在一起)用φ0.15mm以下的电极丝加工时容易发生黄铜附着。
黄铜附着的处理方法如下:
①
在只做1次加工时,把水阻调节到3万Ω•cm,黄铜附着量就很少,但在2次加工后水阻再调到5万Ω•cm。
②
把加工电压上升。
(比目前的电压上升10~20V)
这个方法是把SV上升。
例如SV从02升至03
③
用喷嘴压紧加工时,把上部喷嘴上升1mm左右,加工条件减弱。
④
上侧喷流减弱,下侧喷流增强。
⑤
用其它质量的电极丝。
如锌合金丝、铝合金丝等。
⑥
确认极间电线与导电块是否损耗。
⑦
在极间电线附近加工。
N
注意:
用普通黄铜丝只做1次加工时要完全防止黄铜附着是不可能的,只有做2次加工后才能、除去铜附着。
加工的速度太慢
如果加工速度太慢,请确认以下事项:
①_导电块损耗时挪动导电块的位置。
②_极间电线松动或损耗,要拧紧接头处、研磨极间电线的接头处,必要时更换极间线。
③_确认工作液的阻值。
液臭时要更换,电阻计的探头要时常清洗。
④_下部喷嘴至工件下面的间隙需要0.05mm左右。
⑤_电极丝是否氧化,电极丝的传动系统是否正常。
⑥_确认加工条件是否符合目前的加工。
(喷嘴开放加工时加工速度慢一点)
加工垂直度
减少中凸或中凹的方法:
(厚度100mm以下时有效)
只用1次加工时电极丝张力增强200—300gf/cm,上下喷嘴要尽量
靠近工件。
加工条件参数的SF值选择比目前的加工速度快20—30%的值,
用以上办法形状精度可以提高。
防止中凹的对策是2次加工的SV值减少5—10V,还有3次加工的SV值减小5V。
(SV减少5—10V的方法是:
SV的数值减小1—2。
如:
从08减至07或06)
改变电极丝的偏移量来减少中凹或中凸。
降低加工条件
改善水阻,降低水阻率改善铜附着
调整喷流
例子:
1stOFFSET=190
2ndOFFSET=125
3rdOFFSET=115
4thOFFSET=110
防止中凹的对策:
防止中凸的对策:
1stOFFSET=200
1stOFFSET=180
2ndOFFSET=125
3rdOFFSET=115
3rdOFFSET=115
4thOFFSET=110
用③的方法不能防止中凸或中凹时,请用②的办法加工。
加工精度不好,主要有以下几种原因:
(1)加工表面光洁度差
a加工条件及偏移量不合适;
b水阻太低;
c喷流调整不好,凹模加工时,第二刀要特别注意;
d工件变形;
e电极丝传动系统有问题。
(张力、卷轴等)
形状精度插差
a喷嘴与工件的距离太近或太远;
b喷嘴碰到障碍物或极间电线被牵住;
c电极丝的张力太低;
d导电块有划伤或松动;
eU、V轴晃动;
f加工条件及偏移量不适当。
上下尺寸大小不一样
a喷流调整不好(上下流量不一样)
b电极丝的运行速度太慢
c导电块松动
(4)拐角处的精度不好
a由于放电的反作用力使电极丝滞后
b加工条件太强(加工速度越快,拐角误差越大)
c电极丝的张力太低
d喷流的压力太大
c加工条件设定不适合(SF及SV不合适)
8.锥度加工中提高斜度的精度
在锥度加工过程中,形参数HA、HB、HC、HD、HP影响加工工件的角度和形状尺寸。
其中HB、HC、HD需要用户在加工开始前正确设置,HA、HP一般在出厂前已由厂家设置好,用户不需改动,但是如果用户在加工过程中发现锥度有偏差或用户更换过上下导丝模,则需要重新调整HA、HP这两项参数,调整方法如下:
Z轴回零点
进入移动下面的测斜度菜单,由系统自动检测获得HA、HP。
加工一个40mm厚,10mm×
10mm斜度为1.5°
的四棱台,HB设为0mm,HC设为40mm,加工开始前调整喷流,记下调整后的Z轴的坐标,并将该值输入到运行下的形参数菜单中,用户在加工时除导引程序段外都必须将Z轴移动到该坐标处进行加工。
加工结束后测量四棱台的斜度和编程面的对边尺寸。
假设测出的斜度为θ,编程面的对边尺寸为L,则有:
HP1=(HP+HD)×
tg1.5/tgθ-HD
HP2=(5-L/2+tg1.5×
HA)/tgθ
进入运行下的形参数菜单中,将HA和HB设定为HA1和HP1的值。
进入移动下的测斜度菜单后由系统自动检测获得HA=10mmHP=30mm,调整喷流后的Z坐标为42mm,即HD=42mm,假定加工后测量出的斜度值为θ=1.6°
,编程面对边尺寸L=9.8mm,则将形参数HA、HP设为以下值。
HP=HP1=(30+42)×
tg1.5/tg1.6-42=25.489mm
HA=HA1=(5-L/2+tg1.5×
HA)/tgθ=(5-9.8/2+tg1.5×
10)/tg1.6=12.955mm
重复以上方法直到斜度尺寸符合要求为止。
9.
凸模全周精加工的方法
先对除残留部位以外进行精加工
用气枪将切割缝隙中的水吹干
把小铜片或Ф0.3的铜丝或铜片插入切缝中
用快干胶(502胶水)将凸模与外周粘牢
粘合剂干后,开始最后切割部位的加工
加工结束后,用丙酮剥掉粘合剂
加工流程示意
接通电源
↓
打开SOURCE开关
等计算机完全启动后,打开POWER开关
将X、Y轴机械回零。
(移动至机械原点,切割斜度时Z轴也要回零)
电极丝校垂直
6.
装夹工件
7.
电极丝定位
8.
输入编辑的程序(可磁盘输入或手工输入)
加工前准备(运丝、开喷流、调丝速、调张力等)
10.
开始加工
八、程序的制作
1代码概述
【G代码】
*G00:
直线移动(不放电进行快速直线移动)
格式:
G00X___Y___
(X、Y为终点坐标)
*G01:
直线插补(从起点放电加工至终点)
G01X___Y___
*G02:
顺时针圆弧插补(从起点以圆弧形式顺时针加工至终点)
G02X___Y___I___J___
(X、Y为终点坐标,I、J为圆心相
对起点的增量坐标)
*G03:
逆时针圆弧插补(从起点以圆弧形式逆时针加工至终点)
G03X___Y___I___J___
G04:
延时
(把下一条指令延迟一段时间执行)
G04F___
(F为延时的时间,从0—999秒)
G05:
X轴镜像(关于Y轴对称)
G05
G06:
Y轴镜像(关于X轴对称)
G06
G08:
X、Y同时镜像(以原点对称)
G08
G09:
镜像取消
(取消所有对称)
G09
G11:
跳跃允许
G11
G12:
跳跃取消
格式;
G12
G13:
断丝复归方式一(断丝后暂停,用户穿好丝后,按Enter键继续
加工,按Esc键退出加工)
G13
G14:
断丝复归方式二(断丝后退至参考点,用户穿好丝后,按Enter
键电极丝沿原轨迹移动至断丝点继续加工,按Esc键退出加工)
G14
G15:
断丝复归方式三(断丝后退至参考点,用户穿好丝后,按Enter
键系统将自动调用C888加工条件继续加工至断丝点,然后以断丝
前的加工条件继续加工,按Esc键退出加工。
G15
*G16:
比例缩放(可将图形按比例放大或缩小)
G16S___
(S为比例系数)
G20:
英制单位(选用英制单位)
G20
G21:
公制单位(选用公制单位)
G21
*G26:
旋转允许(可将图形旋转一定角度)
G26R___
*G27:
旋转取消
G27
G29:
指定参考点(当断丝后可以回到参考点进行加工)
G29
*G40:
取消偏移
G40
*G41:
左偏移
G41H000
(注:
H后跟偏移量)
*G42:
右偏移
G42H000
*G50:
取消锥度
G50
*G51:
锥度左倾(铜丝向左倾斜)
G51A___
(A为倾斜的角度)
*G52:
锥度右倾(铜丝向右倾斜)
G52A___
G83:
记录加工时间(记录从开始加工至加工结束的总时间)
G83
*G90:
绝对方式编程
(它的移动量用移动后终点位置在工件坐标系
中的标值来表示,用此坐标值来编程的方法)
G90
*G91:
增量方式编程
(把移动