汽车发动机气缸盖低压铸造工艺研究Word文档下载推荐.docx
《汽车发动机气缸盖低压铸造工艺研究Word文档下载推荐.docx》由会员分享,可在线阅读,更多相关《汽车发动机气缸盖低压铸造工艺研究Word文档下载推荐.docx(14页珍藏版)》请在冰豆网上搜索。
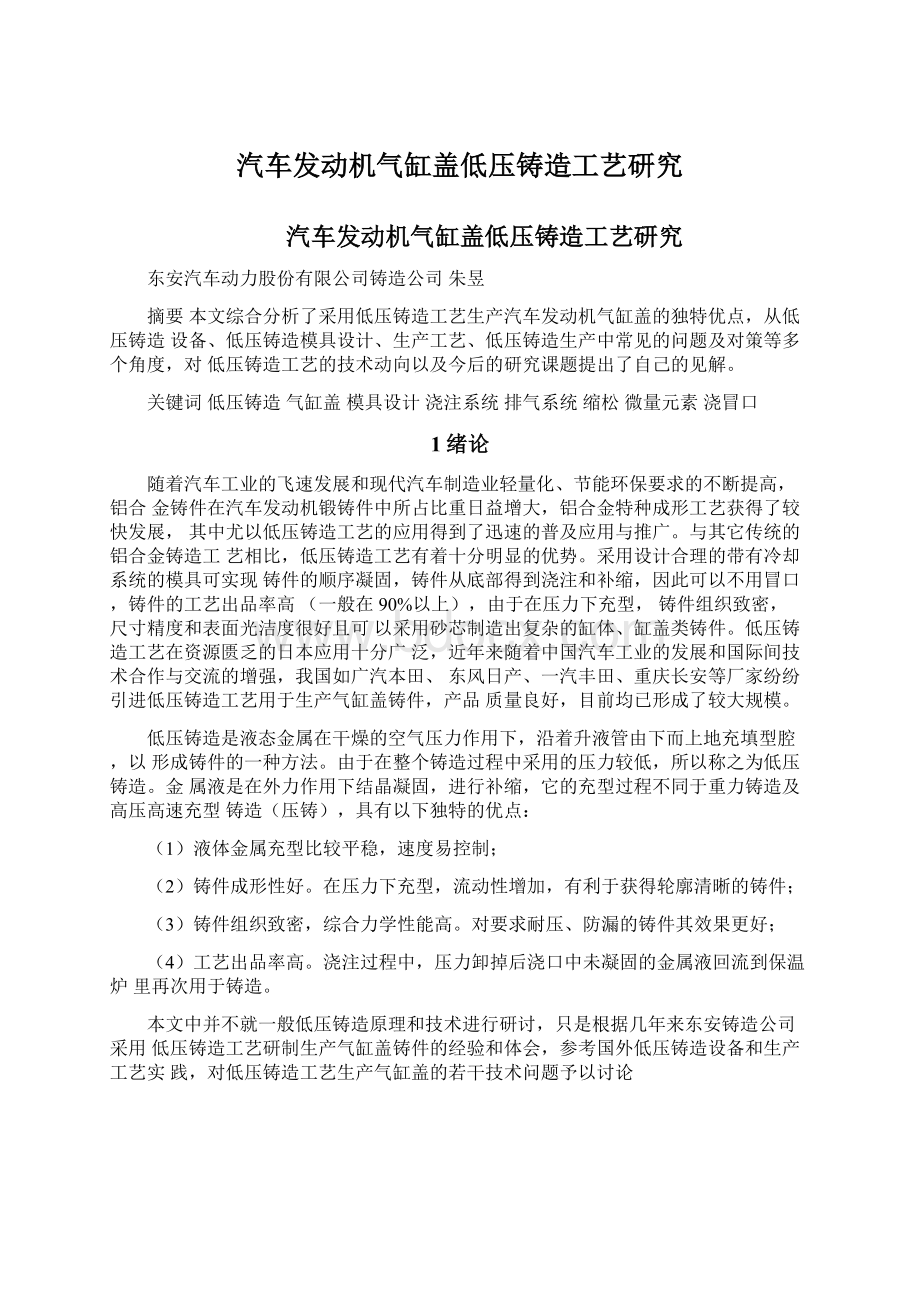
低压铸造机保温炉的形式与密封目前低压铸造机保温炉有炉体密封(采用整体打结炉衬)和坩埚密封两种形式。
前者由于采用打结炉衬可防止铝合金增铁,且不必频繁清理、喷刷涂料,优化了生产条件,但炉膛内空间较大,要有相应液面加压补偿装置。
采用坩埚密封则要用铸铁或铸钢坩埚,长时间保温容易造成铝合金增铁,且每个班次都要清理和更换坩埚。
国外低压保温炉的炉盖、加热器和炉门多采用石墨陶瓷盘根或耐高温陶瓷纤维绳密封,有标准的密封槽,密封良好,可以不开大盖,在专用加料口增补铝水。
液面加压控制系统液面加压控制系统决定着低压铸造机的先进性。
在实际生产中,由于保温炉密封不严造成漏气;
1—程序控制器2—信号放大器3—干燥空气源4—压力表5—压力开关6—电控比例阀
7—排气减压阀8—(炉内)排气系统9—手动阀10—保温炉11—模具国外如日本福助、ISUZU、德国GIMA、KURTZ等先进的低压铸造机液面加压控制系统均有以下先进功能:
①能以曲线和图形适时显示各种工艺参数和工艺过程;
②能记录、监视、诊断、检查,还能保证工艺参数的重复再现性;
(3)具有压力自动监控和补偿功能,补偿范围为炉内液面波动、炉子气压泄漏和管道气压波动等的影响。
(4)加压压力控制采用电空比例阀控制,控制精度≥±
,响应时间≤1ms。
目前国内低压铸造机的液面加压装置有很多种,但设计的各种加压方案(曲线)只能在
控制台上实现,压缩空气被引入保温炉或坩埚内就完全不是预先设计的加压曲线了,铝合金液体也不能按原来设想升液、充型和增压、保压,最主要原因在于:
①稳压阀和大流量减压阀流量不足;
②管路阻力较大;
③保温炉内空间容积较大。
低压铸造机的升液管和浇口保温套低压铸造机升液管价廉物美的应数球铁升液管。
在球铁升液管内外喷涂料,每班更换一次,寿命比钢质升液管好,目前在国内许多大型铝轮毂厂均有应用,但其寿命短、更换繁琐,缺点较为突出。
升液管使用耐火陶瓷材料作成——陶瓷升液管,具有使用寿命长、防止增铁等优点,但高昂的价格影响了它的应用和普及,多从国外进口。
为了精确控制浇口部位的温度,在升液管与模具之间增设一个中间升液管(喉管),采用铸铁材料作成,内衬硅酸钙板等保温隔热材料,顶部内置高温电加热器替代电阻丝和燃汽预热装置,可根据设定值自动控制加热温度,使保温套加热温度可稳定在550~600℃,且寿命可达500h以上
压缩空气净化系统低压铸造的浇注及模具冷却过程均要依靠压缩空气完成,而熔融的铝合金液极易与水份、油发生反应,形成氢溶于合金液中,造成合金含气量严重超标,因此气体干燥过滤装置和储气罐是绝对必要的,一些厂家忽视气体干燥,引起铸件针孔度升级,力学性能下降,且使液面加压装置中的浇铸阀、换向阀生锈,发生设备故障。
根据多年的低压铸造实践经验,铝合金低压铸造工艺对压缩空气的质量要求如下:
表1低压铸造工艺对压缩空气的质量要求
压缩空气杂质
级别(ISO8573)
杂质含量要求
设备配置
水份
2
压力露点-40C,含量
<
0.11g/m3
微加热吸附式干燥器
油
5
10mg/m3(8ppm)
LNB精密除油过滤器(过滤精度可达
m3)
灰尘
4
10mg/m3(10)
LJA后置过滤器(过滤精度可达
1mg/m3
(1)
低压铸造机的控制系统
PLC采用模块式结构,能自动完成设备运行控制、铸造工艺过程控制、加热控制、冷却控制等,能通过控制压力、时间、温度等工艺参数来完成对整个铸造过程的控制,确保铸造生产全过程的工艺条件稳定。
3气缸盖低压铸造模具设计
气缸盖铸件工艺性评审
由于气缸盖设计壁厚控制在~mm,低压铸造气缸盖时合金液总是从铸件底平面浇口引入,流经水套芯和进排气道芯,流向铸件安装边及顶平面,在流动中合金液不断损失热量,自然会形成一定温度梯度,有由远及近(向浇口部位)的顺序凝固趋势。
但若局部壁厚(加上加工余量)大大超过相邻部位的壁厚,就不能形成远端安装边最先凝固、燃烧室底平面再凝固,最后由浇口部位铝液补缩铸件的顺序凝固方式,极易在热节部位形成缩孔、缩松缺陷,造成产品报废,因此在铸件工艺性评审和模具设计过程中要格外注意这一问题,从模具结构、铸造工艺、局部强制冷却等方面采取措施予以克服。
模具的选材和壁厚气缸盖低压铸造模具由于结构复杂、制造成本较高,为保证有较长的使用寿命和较小的热变形量,型面通常采用优质模具钢制造(欧美国家采用H13,日本采用SKD61,材质与使用寿命基本相当),而模具结构件均采用优质球墨铸铁。
模具设计时在四个侧模部位模具壁厚要减薄,以减少模具蓄热能力,提高该处模温,以形成顺序凝固所需温度场。
模具的排气系统设计低压铸造时由下至上升液、充型,有利于排气。
好的排气系统设计会大大提高铝液的充型能力,减少充型过程中的“背压”,提高一次浇注成品率。
模具上应相应设计各种排气设施,如:
上型模块采用分体镶嵌式结构,结合部位留有~0.2mm的缝隙以利于排气;
顶杆直径上留O.1mm间隙,并沿周均匀线切割0.2mm的排气道;
分型面、抽芯滑块上加工间距5mm、深~O.15mm的排气道;
砂芯采用壳芯,砂芯定位芯头的后部应做成空腔以加强排气;
局部憋气的地方设计可方便拆装清理的柱状排气塞,再喷上适当涂料、调整模温,可保证铸件完全充型,不出现气窝、欠铸等缺陷。
模具内部的空气、砂芯产生的气体需要充分考虑分型方法和排气道,应该在尽量减少随着熔汤充填而产生的背压的情况下排出去。
如果背压高到影响加压速度时,会产生熔汤流动不良、表面缩孔等,因此希望控制在以下。
关于凸台、加强筋、叶片等形状的部位,可以考虑嵌入式排气孔插入模具。
在分型面和平面部设计排气槽,再加上排气孔、拉深加工等手段尽量做到排气良好的设计。
另外砂芯产生的气体量较大、时间也较长,可以在模具结构上设计确定的排气路线,追加吸引机构。
模具的浇注系统设计低压铸造的浇冒口设计相对简单,由于零件结构和工艺方案所限,一般只能在底部安装孔位置设计2~4个浇口,为保证充型浇注效果,在允许的条件下浇口直径可设计略大一些,同时可设计环形的辅助浇道以分流铝液。
由于浇口部位最后凝固温度很高,不易脱模,有时甚至会产生浇口折断,因此浇口的出模斜度应设计为5~7。
由于气缸盖低压铸造多采用单升液管经升液箱将铝液分配至多处浇口的形式,因此升液高度和升液管内径非常重要,升液高度过大、升液管内径过小会造成铝液充型时流速过高,在浇口处形成“喷溅”,严重影响型腔排气,造成成品率降低,且会使砂芯过早溃散形成“粘砂”,因此气缸盖低压铸造升液管内径一般在100~150mm。
低压铸造品的设计基本要求是将壁厚整体平均化,或是将壁厚的分布考虑容易实现方向性凝固的地方。
也就是说对于浇口而言,断面从小到大逐渐变化是产品设计的必要条件,因此如果产品的性能上无法进行这种设计时最好避开使用低压铸造法。
充分考虑铸件整体的方向性凝固和浇口周围的冒口效果的浇口位置、大小、数量的设定也是非常必要的。
浇口的位置应该是铸件整体的最大壁厚部位,并且要设在从熔汤前方和上方可能达到方向性凝固的部位。
因产品形状、大小等原因浇口数量有所差异,但通常是1-4个。
在远离浇口的位置如果壁较厚冒口无法到达时,有时也加上无顶冒口。
浇注方案上对这些问题进行为维持方向性凝固的严格的温度控制和条件管理等,根据情况还可以在成为热点的部位进行空气、水等的冷却。
浇口部位的截面做成圆形是较理想的,但事实上由于产品形状的限制经常是不得不做成不规则的形状。
在这种情况下为了防止该部分的过冷,最小截面积最好应是浇口附近产品壁厚的2倍以上。
浇口的高度h比较低时可以得到较大的因浇口处热量提供和加压而引起的补缩效果,而且也容易实现方向性凝固,但这是防止氧化物的滤渣网的固定部位,由于因铸造条件的变动引起浇口长度的变化,因而一般情况下考虑30-40mm较多。
缩尺与加工余量缩尺与加工量设计不当不仅造成铸件肥厚影响机械加工,更主要会影响铸件顺序凝固次序,造成各种铸造缺陷。
气缸盖在全金属模中低压铸造,收缩严重受阻,故缩尺比一般铝合金金属型铸造时要小,尺寸精度较高。
根据气缸盖的结构和尺寸不同,缩尺一般为%~%左右。
加工余量考虑到气缸盖要用数控机床加工,加工余量单面不超过2mm,一般~2mm为好。
此外还要考虑涂料厚度,留出~0.3mm。
模具的引导装置低压铸造模具由于温度高、尺寸大且动静模有较大温度差,动模与静模之间一般不能使用圆销,以避免高温时“咬死”。
可设计方形导柱和开口销套,销与销套材料应采用40Cr,以提高耐磨性。
模具的温控装置低压铸造模具应设计有精密的冷却和加热装置,并预埋热电偶配合计算机控制,方可实现铸造条件的稳定,使铸件保持高品质。
低压铸造模具通常在上型中部、侧型、下型二三燃烧室之间、浇口附近及升液箱盖板等五处设置有测温热电偶,可实现对低压铸造生产中的重点部位温度控制。
为了改善内部品质(强化方向性凝固)、缩短铸造周期,可以进行上型和横型的冷却(水冷、风冷或雾冷,一般冷却模具整体的线式冷却比较多)。
开始低压铸造作业初期,由于缺乏经验,只需采用风冷,随着铸造作业条件的稳定,可逐步进行雾冷和水冷的试验,但在模具准备过程中要特别注意接口部位的测漏工作。
水冷应用得好,可大大提高生产效率缩短铸造周期。
3.7.1中间升液箱温度控制
采用自动电加热控制,第一模浇注时升液箱温度应控制在520℃以上,以后控制在
580℃左右时开始下芯作业,温度过低时,容易被“冻死”。
3.7.2浇注温度的控制铝水浇注温度一般控制在700℃±
10℃,在不影响铸件充型的前提下可将浇注温度适当降低,可减少厚大部位缩孔的产生及“粘砂”,缩短铸造周期。
3.7.3铸型温度的控制
低压缸盖模具一般在模具上型为350±
20℃左右,侧型为380±
20℃左右,下型为440±
20℃左右,浇口附近为500±
20℃左右,温度过低会造成铝液充型能力下降,成品率低,温度过高会延长铸件固化时间,控制不好还会造成铸件浇口折断、。
3.7.4铸件凝固温度场的计算机数值模拟。
目前国内外在模具设计制造过程中应用专业软件对铸件充型、凝固过程进行数值模拟,辅助进行工艺设计与优化十分普遍,可大大缩短模具开发定型周期,提高模具制造质量,目前国际上应用较为广泛的有美国ProCAST、德国MAGMA、韩国Anycasting软件等。
图3采用MAGMA软件对4G1气缸盖凝固过程进行的数值模拟与实际缺陷对比
低压铸造气缸盖的生产工艺低压铸造生产工艺就是将低压铸造机、模具与合金材料三大要素有机结合的过程,这些因素之间关系密切,且相互影响和相互制约。
低压铸造的主要工艺参数有:
压力、时间(速度)、温度,关键过程有:
制芯、模具准备、合金熔炼、浇注,这些工艺参数与关键过程的合理控制与管理是保证铸件质量的关键,同时也直接影响生产效率和模具寿命。
浇注工艺参数的确定
低压铸造的核心在于浇注工艺。
根据缸盖铸件的特点,在燃烧室平面开设2~4个浇
口,同时进铝液浇注。
在升液管与模具之间增设一个中间升液管,分配铝水进入浇口。
低压浇注过程一般包括升液、充型、增压、保压、卸压、冷却几个阶段。
低压浇注的主要工艺参数有压力、温度和时间,其中压力是最基本的工艺参数,对浇注过程及铸件质量KPa
的影响最大。
低压铸造中,如果铸型内排气顺利,则压力每上升0.001Kg/cm2,升液管内的铝液就上升4mm。
经过试验,浇注工艺曲线如图4所示,工艺参数见表2。
(1)O-A升液阶段——铝液沿着升液管平稳上升到铸型浇道处。
液面到中间型腔的高度-50mm
P1=
4×
1000
ΔT1由铸造机空压控制辅助阀门的能力决定。
(国外低压铸造机保温炉M/C在0.15Kg/cm2的程度,阀门在最大能力下,ΔT1设定为约7秒;
考虑到①熔液液面高度公差:
目测、传感器中的铝附着⋯⋯20mm;
②气压控制公差(正常工作时)切换时间下
0.005Kg/cm2=20mm;
③反馈管路中的杂质、辅助阀门的不畅通等的影响0.002Kg/cm2=8mm,计算公差设定为-50mm)。
(2)A-B充型阶段——铝液由浇道进入型腔,将型腔充满。
充型速度过大,加剧紊流,会产生包气、氧化夹渣,铸件可能会出现轮廓不清的缺陷;
速度过低,影响充填性,会造成浇不足、冷隔等缺陷。
50+液面到中间型腔的高度+铸件高度+200
P2=P1+
7×
(P2-P1)
ΔT2=
1000(升压速度基本定为0.007Kg/cm2/sec)
(3)B-C增压阶段——充满型腔后再继续增压,使铝液在压力下结晶凝固。
压力越大,补缩效果越好,铸件组织愈致密。
但压力过大,易造成跑火;
压力过小,铸件可能会有缩孔、缩松、致密度低等缺陷。
增压压力P3=P2+5(KPa),增压时间△T3=5~10(s)
参数
时间
压力
加压速度
阶段
(s)
(KPa)
(KPa/s)
O—A升液阶段
ΔT1
P1
V1=P1/ΔT1
A—B充型阶段
ΔT2
P2
V2=(P2-P1)/ΔT2
B—C增压阶段
ΔT3
P3
V3=(P3-P2)/ΔT3
C—D保压阶段
ΔT4
——
D—E冷却阶段
ΔT5
表2浇注工艺参数
(4)C-D保压阶段——铝液在压力下,完成由液态到固态的转变,保压时间过长,使生产周期延长,生产率下降,严重时会使升液管上部“冻死”,使铸件出型困难,增加清理工作量;
保压时间不足,易出现缩孔、缩松,严重时浇口部位的铝水会倒流,造成铸件“中空”报废。
在低压铸造中加压时间为持续加压中完成铸件最终凝固部位的凝固,等到可以取出浇口(凝固90%以上)时,持续加压结束。
保压时间△T4=180~220(s),
保压压力为P3
(5)D-E卸压冷却阶段——卸压指铸件凝固完成后,立即卸掉液面加压压力,使升液管和浇道中尚未凝固的铝液回落到保温炉中,排气时间为待铸件内部铝液温度达到浇口上面560℃、浇口铁丝网部590℃时结束加压保持,然后排气。
冷却指压力卸掉后,铸件留在模具中的过程。
冷却时间根据铸件厚度及重量而定。
冷却时间过短铸件会变形、开裂。
冷却时间是从卸压后开始计算。
△T5=t5-t4=160(s)
(6)安置浇口滤渣网此工序的目的为了防止从升液管进来的氧化物、砂子等杂物以及加强铝液充型时的层流化,减少紊流以利于平稳充型。
把做成浇口形状的成型镀锌钢丝网(线径-0.6mm,12-14个网孔)用专用夹具固定在浇口部位,这样做采用人工安置的比较多,但也可以试一试进行自动化设计或给汤管内吹惰性气体等方法。
制芯工艺
采用任何常用的制芯工艺如壳芯、冷芯盒、热芯盒等制造的砂芯都可以用于低压铸造。
目前国内引入日本的生产工艺,多采用覆膜砂热芯盒工艺制芯,进排气芯采用KC600型全
自动垂直分型壳芯机生产,两面翻转射砂,模具上装震动器,可射制壁厚在2~3mm的中
空壳芯,水道、油道砂芯形状复杂,尺寸较大,厚薄不均,采用KA600型全自动水平分型热芯盒制芯机生产,一模两件。
同其它铸造方法一样,砂芯必须固化充分,金属型上有必
要的排气结构,以避免在铸件里产生气体方面的铸造缺陷。
对于气缸盖类复杂铸件通常使用预组装的芯组(如图5),
可以快速地插放到金属型内,简化操作,缩短铸造周期。
低压铸造对于制芯用覆膜砂质量要求较高,既要求有适宜的粒度,又要有较高的热强度和较低的发气量,需要根据实际生产情况进行摸索调整,
模具涂料选择及喷涂工艺
人们常讲“三分浇注、七分准备”,对于低压铸造生产而言,由于模具重量大、拆装困难,要求有较长的连续生产周期,因而模具涂料的选择及喷涂工艺的掌握至关重要。
4.3.1型腔涂料的选择与喷涂
型腔底层涂料使用日本Acheson金属模脱膜剂Prodag(石墨基),浇口和燃烧室使用日本Acheson低压铸造涂料Dag632,型腔充分预热至230±
10℃,取出后在模具保持190±
10℃时将涂料稀释后用喷枪均匀喷涂,喷枪距型腔之间一般保持150~200mm。
为提高
涂层的粘附强度,喷涂完毕后模具须在510±
10℃保温~小时。
4.3.2升液管涂料的选择与涂刷
升液管(包括中间升液管)使用日本Acheson涂料Dag696。
预热至200oC左右时,用毛刷均匀涂刷,一般需刷2~3次,每次涂刷完毕后需充分烘烤。
4.3.3涂料喷涂时模具温度控制及涂层
模具喷涂时要考虑铸型的大小或壁厚、温度分布均匀,充分进行预热。
模具取出后要
使用表面温度计,在铸型的各个部位测几次,确认铸型表面温度是否在200±
10℃。
涂层
顺序为:
①在整个铸型上薄薄地喷一下底层涂料;
②从铸型的突起部位、薄壁部位等容易冷却的部位开始再精心喷涂。
如果模具温度低,则喷涂时涂料的水分蒸发少,导致模具表面潮湿,无法保证粗糙度;
如果铸型表面温度更低,就出现平滑的涂层,导致模具内透气性差,预热时出现涂层膨胀、脱落现象。
为防止铸件局部缩孔、缩裂,可将模具局部涂料刮掉或减薄,加速冷却。
在喷涂复杂的模具时,需要熟练地进行操作,但为了保持稳定的上涂料的效果应尽快使操作标准化,涂层厚度粗糙度等因部位不同而存差异。
一般而言,工作面是-0.2mm,光
洁度要求高的加工基准面,燃烧室面等应用粒子细小的涂料涂0.05mm的厚度,涂料一般利用市场上的,基本构成是骨材(碳酸钙、陶土、氧化铝、云母、石墨等)、粘接剂(硅酸钠)和水等。
合金熔炼工艺
气缸盖低压铸造多采用AC4B牌号铝合金(日本JIS5202技术标准)铸造,材料成份类似于我国ZL106合金,但略有差异。
该铝合金为亚共晶铝硅系合金,铸造性能优良,综合力学性能高,冶金质量稳定成本较低,经(480±
10)C、1~2小时的热处理后抗拉强度可达155Mpa以上,延伸率达%以上。
4.4.1熔化工艺
采用MHII-N-2000/1500型高效燃汽熔铝炉进行合金的集中熔化,该炉为三炉一体ETAmax式结构,LPG加热系统,预热、熔化、保温区分别独立,效率高,且炉料可利用废气充分预热,热效率>
55%,即使加入潮湿、不洁的炉料也不会影响合金液的熔炼质量,安全性高,熔化过程中合金的烧损仅在(~)%,铝水出炉温度为(740C±
5)C。
4.4.2精炼工艺
电加热石墨坩埚转水保温炉或燃汽预热转水包内精炼处理,铝液精炼保温温度为(720±
5)℃,在此温度下进行除渣、除气。
采用FOSECO公司FDU旋转除气装置,转子转速300~350rpm,氩气纯度为%,压力,流量15~20L/min,除气时间设定为10分钟,现场检验合格(含氢量100g,含渣量K1/20)后转入低压铸造机的保温炉里。
4.4.3合金的金相组织
AC4B合金为亚共晶型铝硅系合金,含硅量为于未进行变质,共晶硅呈短杆状或针状,由于合金含硅量较高,又加入了微量的Ti、Mn,使得合金的铸造性能和高温性能优良,气密性、耐蚀性也较好,适合于砂型及金属型铸造。
目前在气缸盖低压铸造工艺生产中多采用AC4B合金,无需进行变质处理即可获得优良的机械性能和高品质的铸件。
4.4.4合金的凝固区间
对于AC4B合金,其凝固范围为(516~604)C。
在604C合金中的铝开始凝固,565CAl-Si共晶相出现并凝固,545C出现Al-Si-Cu三维共晶,516C出现不纯物等多元共晶。
掌握好气缸盖铸造凝固过程中铝合金的温度变化,可优化模具铸造方案,确保铸件从凸轮轴室向浇口方向顺序凝固,提高铸件品质。
5低压铸造生产中常见的问题及对策
浇口折断
防止方法:
保持浇口衬套的高温(Min.450℃);
不应将加压结束后的冷却(排气)时间随意加长。
为了保持