课题宏程序实例Word文档下载推荐.docx
《课题宏程序实例Word文档下载推荐.docx》由会员分享,可在线阅读,更多相关《课题宏程序实例Word文档下载推荐.docx(13页珍藏版)》请在冰豆网上搜索。
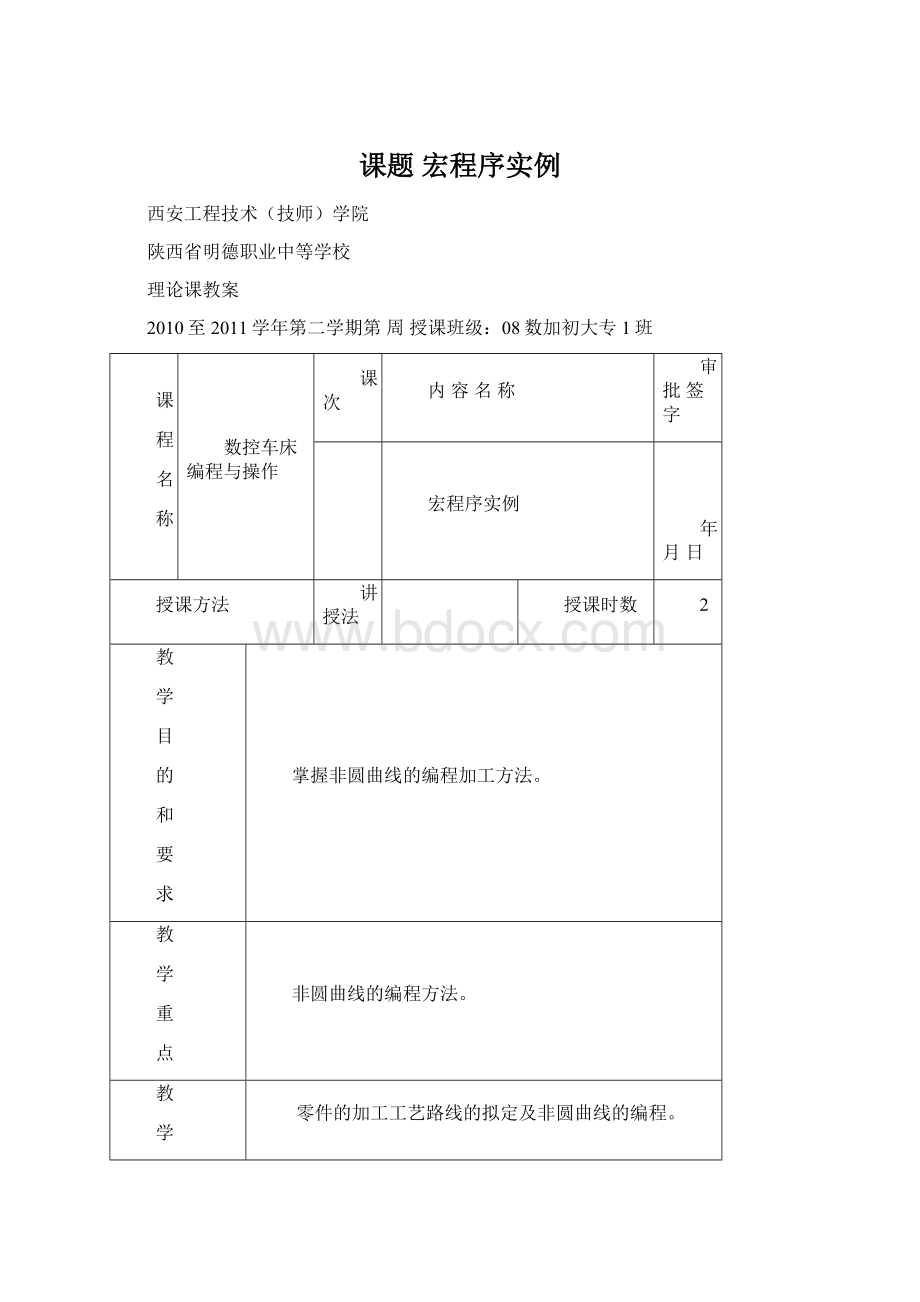
习
提
问
什么叫拟合处理?
课外作业题号
自拟题
教学过程
新课讲授→练习→小结→布置作业
任课教师:
向成刚
课题宏程序实例
案例:
编制如图所示零件的数控车加工程序并加工,材料为45钢,毛坯为φ50×
107mm和φ50×
56mm。
1.案例分析
本例工件是一个两件组合件。
加工时先加工件二的左端;
然后在件一毛坯钻出直径为φ20mm,深30mm的底孔,调头以毛坯表面作为装夹表面,加工件一的左端及梯形槽达图纸要求,工件调头后以已加工的φ35外圆作为装夹表面,加工右端内轮廓及螺纹等达图纸要求,不拆除工件,将件二与件一进行配合,保证配合精度。
最后加工件一与件二外轮廓达图纸要求。
2.数控加工工艺卡
数控车床加工工艺卡
零件图号
数控车床加工工艺卡片
设备型号
设备编号
零件名称
组合零件2
CKA6140
02
刀具表
量具表
工具表
T01
93°
外圆车刀
1
游标卡尺(0~150mm)
螺纹对刀样板
T02
外沟槽车刀(刀宽2mm)
2
外径千分尺(25~50mm)
0.2mm厚铜皮
T03
外沟槽车刀(刀宽5mm)
3
螺纹环规(M30×
1.5-6H)
垫刀片若干
T04
三角形外螺纹车刀(牙型角为60°
)
4
内径表(18~35mm)
常用车床辅具
T05
盲孔车刀
5
螺纹塞规(M30×
1.5-6g)
计算器(具有函数功能)
T06
内沟槽车刀(刀宽4mm)
6
万能角度尺(0~320°
)
T07
三角形内螺纹车刀(牙型角为60°
序号
工艺内容
切削用量
主轴转速
(r/min)
进给速度
(mm/r)
背吃刀量(mm)
用三爪卡盘夹持(件二)毛坯外圆,伸出长约30mm,找正后夹紧
手动车左端面(Z向对刀)
600
粗车(件二)左端外轮廓,留加工余量0.3mm
0.2
1.5
精车(件二)左端外轮廓达图纸要求
1200
0.05
0.3
车退刀槽
500
0.15
车外螺纹M30×
1.5-6g达到图纸要求
单侧刃进刀
7
用三爪卡盘夹持件一毛坯外圆,车端面并用φ20mm的钻头钻孔,深30mm
400
10
8
调头夹(件一)毛坯外圆,伸出长约65mm,找正并夹紧,手动车左端面(Z向对刀)
9
粗车(件一)左端外轮廓,留加工余量0.3mm
精车(件一)左端外轮廓达图纸要求
11
粗、精加工(件一)左端的梯形槽达要求
12
调头夹(件一)φ38mm外圆,手动车右端面(Z向对刀)
13
粗车(件一)右端内轮廓,留加工余量0.3mm
1.0
14
精车(件一)右端内轮廓达图纸要求
1000
15
3.0
16
车内螺纹M30×
1.5-6H达到图纸要求
17
不拆除件一,将件二与件一进行配合
18
手动车右端面(Z向对刀)
19
粗车(件一)及(件二)外轮廓,留加工余量单边0.3mm
20
精车(件一)及(件二)外轮廓达图纸要求
21
工件精度检测
共1页第1页
3.相关计算
外螺纹总切深:
h=0.6495P=0.6495×
1.5≈0.975mm。
内螺纹总切深:
h=0.5413P=0.5413×
1.5≈0.812mm。
4.参考程序
程序
注释
件二左端加工程序
O6181;
程序名
N10G21G40G99;
程序初始化
N20T0101;
换1号外圆车刀,导入1号刀补
N30M03S600;
主轴正转,转速600r/min
N40M08;
切削液开
N50G00X52.0Z2.0;
快速到达循环起点
N60G71U1.5R0.5;
外圆粗车循环,加工路线N80~N160,X向精车余量0.3㎜,Z向无精车余量,粗加工进给量0.2mm/r
N70G71P80Q160U0.3WO.0F0.2;
N80GOOX27.8S1200F0.05;
精加工轮廓起点,设置精加工参数
N90G01Z0;
精加工轮廓描述
N100X29.8Z-1.0;
N110Z-9.0;
N120X32.0;
N130Z-16.0;
N140X36.0;
N150Z-22.0;
N160X51.0;
N170G70P80Q160;
精加工外轮廓
N180G00X100.0Z200.0;
刀具快速退至换刀点
N190T0202S500;
换2号切槽刀,导入刀具刀补
N200G00X35.0Z-9.0;
快速定位至切槽起刀点
N210G01X28.0F0.15;
切槽
N220X32.0;
退刀
N230G00X100.0Z200.0;
刀具快速退回至换刀点
N240T0404;
换4号螺纹车刀,导入4号刀补
N250S600;
主轴变速,转速600r/min
N260G00X32.0Z2.0;
快速定位至螺纹循环起点
N270G76P020560Q50R0.05;
调用螺纹切削复合循环G76车螺纹,设置加工参数
N280G76X28.10Z-8.0R0P975Q400F1.5;
N290G00X100.0;
刀具沿径向快速退出
N300Z150.0;
刀具沿轴向快速退出
N310M30;
主程序结束并返回程序起点
件一左端加工程序
O6182;
外圆粗车循环,加工路线为N80~N150,X向精车余量0.3㎜,Z向无精车余量,粗加工进给量0.2mm/r
N70G71P80Q150U0.3WOF0.2;
N80GOOX0S1200F0.05;
N100G03X35.0Z-5.0R35.0;
N110G01Z-35.0;
N120X44.0;
N130Z-40.0;
N140X48.0;
N150Z-60.0;
N160G70P80Q150;
精车外轮廓
N170G00X100.0Z150.0;
N180S500;
主轴变速,转速500r/min
N190T0303;
换3号车槽刀,导入3号刀补
N200G00X50.0Z-50.91;
粗车槽
N210G01X32.0F0.05;
N220X48.0;
N230Z-48.0;
N240X32.0Z-50.91;
精车槽
N250X48.0;
N260Z-53.82;
N270X32.0Z-50.91;
N280X50.0;
N310M05M09;
主轴停转,切削液关
N320M30;
件一右端加工程序
O6183;
N10G40G21G99;
N20M03S600;
N30T0202M08;
换2号内孔刀,导入刀具刀补,切削液开
N40G00X20.0Z3.0;
快速定位至循环起点
N50G71U1.0R0.5;
调用内径粗车循环,设置加工参数
N60G71P70Q150U-0.2W0F0.2;
N70G01X37.0Z0F0.05S1000;
N80X36.0Z-0.5;
N90Z-6.0;
N100X32.0;
N110Z-13.0;
N120X30.5;
N130X28.5Z-14.0;
N140Z-25.0;
N150X20.0;
N160G70P70Q150;
精加工内轮廓
N160M05;
主轴停转
N170M00;
程序暂停,对加工后的轮廓进行测量
N180M03S500;
主轴正转,转速500r/min
N190T0303M08;
换3号内沟槽刀,导入刀具刀补
N200G00X26.0Z5.0;
快速接近工件
N210Z-25.0;
到达切槽起点
N220G01X32.0F0.15;
第一次切槽
N230X26.0;
N240Z-24.0;
刀具沿Z向移动
N250X32.0;
第二次切槽
N260X26.0;
N270G00Z150.0;
N280X100.0;
N290T0404;
换4号内螺纹刀,导入刀具刀补
N300G00X25.0Z5.0;
定位至螺纹循环起点
N310G76P020560Q50R-0.05;
N320G76X30.0Z-23.0R0P810Q400F1.5;
N330G00Z150.0;
N340X100.0;
N350M30;
件一件二配合后加工程序
O6184;
N10M03S600;
N30G00X80.0Z2.0;
N40G73U25.0W0R10;
调用平移粗车循环,设置加工参数
N50G73P60Q150U0.2WOF0.1;
N60G01X0Z0S1000F0.05;
精加工轮廓起点,精加工参数设置
N70#1=40.0;
赋长轴坐标(Z坐标)初值
N80#2=24.0*SQRT[1600.0-#1*#1]/40.0;
根据椭圆方程计算X坐标的绝对值
N90#3=2*#2;
N100#4=#1-40.0;
N110G01X#3Z#4F0.1;
直线拟合加工椭圆
N120#1=#1-0.05;
加工循环步距赋值
N130IF[#1GE-30.0]GOTO80;
设置粗加工循环跳转语句
N140G01Z-77.09;
加工φ32的圆柱
N150X48.0Z-80.0;
加工锥面,精加工轮廓结束
N160G70P60Q150;
N140G00X100.0;
N150Z150.0;
N160M30;
5.操作步骤
⑴开机,回参考点;
⑵装夹(件二)毛坯和刀具;
⑶试切法对刀;
⑷编写并输入(件二)左端加工程序,检查程序;
⑸单步加工无误后自动连续加工;
⑹测量,修改磨损值后加工;
⑺测量合格后卸下(件二);
⑻装夹(件一)毛坯,编写并输入(件一)左端加工程序,检查程序;
⑼单步加工无误后自动连续加工;
⑽测量,修改磨损值后加工;
⑾测量合格后卸下(件一);
⑿调头装夹(件一),编写并输入(件一)右端加工程序,检查程序;
⒀单步加工无误后自动连续加工;
⒁测量,修改磨损值后加工;
⒂不拆除(件一),将(件二)与之组合,编写并输入组合后加工程序,检查程序;
⒃单步加工无误后自动连续加工;
⒄测量合格后卸下工件;
⒅数控车床的维护保养及场地的清扫。
案例小结:
不同的数控机床,选择的刀架也不相同,而不同刀架的刀位数也各不相同。
目前常用的数控车床刀架有四工位前置式刀架、六工位前置或后置式刀架和多工位后置转塔式刀架。
当使用四工位刀架加工本例工件时,由于无法一次装夹七把刀具,因此,在加工完件二及件一左端后拆下外沟槽刀(刀宽2mm)外螺纹刀和外沟槽刀(刀宽5mm),再安装内孔车刀、内沟槽车刀和内螺纹车刀加工件一右端。
在加工中应加以注意。
车削椭圆表面时,为了避免加工时产生干涉,外圆车刀应具有较大的副偏角。