圆体成形车刀设计.docx
《圆体成形车刀设计.docx》由会员分享,可在线阅读,更多相关《圆体成形车刀设计.docx(22页珍藏版)》请在冰豆网上搜索。
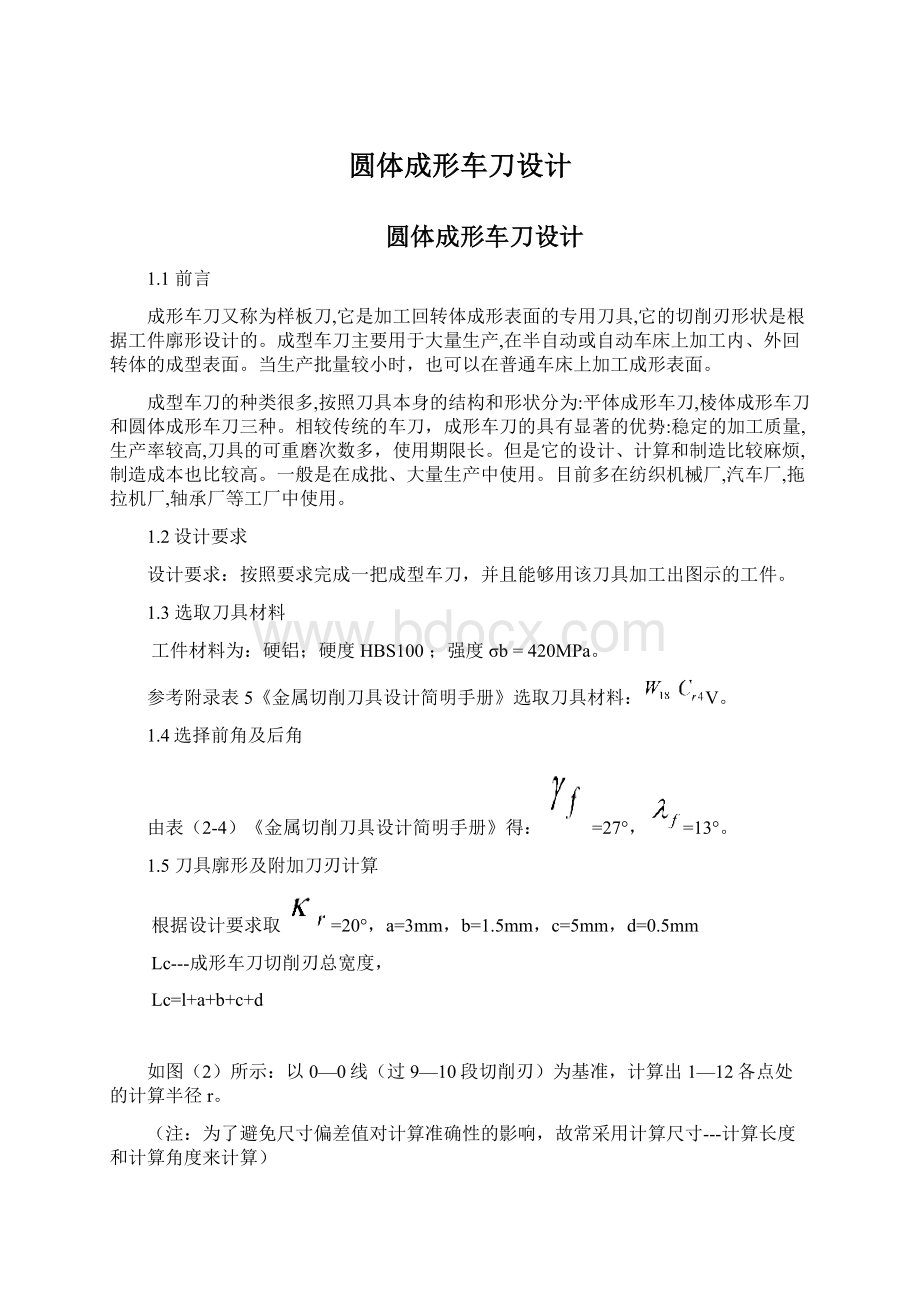
圆体成形车刀设计
圆体成形车刀设计
1.1前言
成形车刀又称为样板刀,它是加工回转体成形表面的专用刀具,它的切削刃形状是根据工件廓形设计的。
成型车刀主要用于大量生产,在半自动或自动车床上加工内、外回转体的成型表面。
当生产批量较小时,也可以在普通车床上加工成形表面。
成型车刀的种类很多,按照刀具本身的结构和形状分为:
平体成形车刀,棱体成形车刀和圆体成形车刀三种。
相较传统的车刀,成形车刀的具有显著的优势:
稳定的加工质量,生产率较高,刀具的可重磨次数多,使用期限长。
但是它的设计、计算和制造比较麻烦,制造成本也比较高。
一般是在成批、大量生产中使用。
目前多在纺织机械厂,汽车厂,拖拉机厂,轴承厂等工厂中使用。
1.2设计要求
设计要求:
按照要求完成一把成型车刀,并且能够用该刀具加工出图示的工件。
1.3选取刀具材料
工件材料为:
硬铝;硬度HBS100;强度σb=420MPa。
参考附录表5《金属切削刀具设计简明手册》选取刀具材料:
V。
1.4选择前角及后角
由表(2-4)《金属切削刀具设计简明手册》得:
=27°,=13°。
1.5刀具廓形及附加刀刃计算
根据设计要求取=20°,a=3mm,b=1.5mm,c=5mm,d=0.5mm
Lc---成形车刀切削刃总宽度,
Lc=l+a+b+c+d
如图
(2)所示:
以0—0线(过9—10段切削刃)为基准,计算出1—12各点处的计算半径r。
(注:
为了避免尺寸偏差值对计算准确性的影响,故常采用计算尺寸---计算长度和计算角度来计算)
图
(2)
=基本半径
=9mm;
;
;
;
;
;
;
(以上各个半径就是标注点的相对0—0线的半径长度,半径是进行刀具切削的各个点的设计绘制的。
)
再以1、2点为基准点,计算长度:
;
;
;
;
1.6计算切削刃的总长度
;
(由于刀具的一部分是辅助用的加工部分,则可以对刀具的外部半径进行圆整,最后考虑到加工刀具的精度问题取为58mm.)
取
则L
1.7确定结构尺寸
为了达到加工结构的优化和合理的加工工艺,应使:
(见表2—3)
由表(2—3)查得《金属切削刀具设计简明手册》:
C1312车床(刀具结构为C型);;
选用毛坯直径为28mm,则;
代入上试,可得;
最终取m=8mm.
1.8用计算法求原体成形车刀廓形上的各个点所在圆半径
1.8.1计算廓形上的各个点所在圆半径
计算过程如表(1—1)《金属切削刀具设计简明手册》所示:
表(1—1)
廓形组成点
精度为0.01
9,10
作0点
7.94
24.272-25=
-0.7280.01
1,2
9
23.61
0.54
18.63
40.78
24.60
0
3,4
9.975
21.18
1.60
17.57
42.45
23.81
1.9560.01
5,7
7.788
26.57
0.3
18.87
40.42
24.78
3.650.02
6
12.675
16.52
5.08
14.09
48.76
21.37
0.7450.04
8
8.29
25.77
0.39
18.78
40.55
24.72
-0.260.04
11,12
9.928
21.29
2.18
16.99
43.41
23.38
0.430.02
备注:
以上各个值的计算公式为:
,
;;
;;
标注廓形径向尺寸时,应该选公差要求最严的1—12段廓形为尺寸标准基准,其它各点用廓形深度见表(1—1)。
1.8.2根据表(1—1)可确定各个点廓形深度的公差
1)的为:
0;
2)的为:
0.01;
3)的为:
0.02;
4)的为:
0.04;
5)的为:
0.1;
6),的为:
0.04;
1.9最小后角的校验
由于7—11段切削刃与进给方向的夹角最小,所以这段切削刃上后角最小。
则有:
所以后角校验合格。
1.10车刀廓形宽度即为相应工件廓形的计算长度
其数值及公差按表(2—5)确定
各个值分别为:
;
;
;
;
1.11绘制刀具的加工工作图和样板工作图
根据以上得到的结果,按照数据进行刀具图的绘制,绘制图一张。
根据相关的要求制定粗糙度等等的标注。
(详细说明见图纸)
矩形花键拉刀的设计
2.1前言
拉刀上有很多刀齿,后一个刀齿(或后一组刀齿)的齿高要高于(或齿宽宽于)前一个刀齿(或前一组刀齿),所以当拉刀作直线运动时(对某些拉刀来说则是旋转运动),便能依次地从工件上切下很薄的金属层。
所以拉刀具有以下优点:
加工质量好,生产效率高,使用寿命长,而且拉床结构简单。
但拉刀结构复杂,制造麻烦,价格也比较高,一般是专用刀具,因而多用于大量和批量生产的精加工。
拉刀按加工表面的不同,可分为加工圆形、方形、多边形、花键槽、键槽等通孔的内拉刀和加工平面、燕尾槽、燕尾头等外表面的外拉刀。
按结构的不同,可分为整体式拉刀和装配式拉刀。
2.2选定刀具类型和材料的依据
1选择刀具类型:
采用的刀具类型不同将对加工生产率和精度有重要影响。
总结更多的高生产率刀具可以看出,增加刀具同时参加切削的刀刃长度能有效的提高其生产效率。
例如,用花键拉刀加工花键孔时,同时参加切削的刀刃长度l=B×n×Zi,其中B为键宽,n为键数,Zi为在拉削长度内同时参加切削的齿数。
若用插刀同时参加切削的刀刃长度比插刀大得多,因而生产率也高得多。
2正确选择刀具材料:
刀具材料选择得是否恰当对刀具的生产率有重要的影响。
因为硬质合金比高速钢及其他工具钢生产率高得多,因此,在能采用硬质合金、的情况下应尽力采用。
由于目前硬质合金的性能还有许多缺陷,如脆性大,极难加工等,使他在许多刀具上应用还很困难,因而,目前许多复杂刀具还主要应用高速钢制造。
拉刀结构复杂,造价昂贵,因此要求采用耐磨的刀具材料,以提高其耐用度;考虑到还应有良好的工艺性能,根据《刀具课程设计指导书》表29,选择高速工具钢,其应用范围用于各种刀具,特别是形状较复杂的刀具。
2.3刀具结构参数及各部分功用
1拉刀的结构
图1
表1
代号
名称
功用
1
柄部
夹持拉刀,传递动力
2
颈部
连接柄部和后面各部,其直径与柄部相同或略小,拉刀材料及规格等标记一般打在颈部。
3
过度锥
颈部到前导部的过渡部分,使拉刀容易进入工件孔中。
4
前导部
起引导拉刀切削部进入工件的作用,
5
切削部
担负切削工作,包括粗切齿、过渡齿及精切齿。
6
校准部
起刮光、校准作用,提高工件表面光洁度及精度,并作为切削部的后备部。
7
后导部
保持拉刀与工件的最后相对位置,防止在拉刀即将离开工件时因工件下垂而损坏工件已加工表面及刀齿。
8
尾部
支持拉刀使之不下垂,多用于较大较长的拉刀,也用于安装压力环。
2切削方式:
采用分层拉削方式中的同廓式拉削方式
3拉削余量:
对于花键孔A=De-Do
4拉刀刀齿结构:
表2
名称
功用
前刀面
切削流出的表面
后刀面
最终形成已加工表面的面
副后刀面
刀齿上和已加工表面相对的表面、分屑槽两侧面
刃带
也称第一后刀面,是主切削刃和后刀面之间的后角为零的窄面,它有稳定的拉削过程,防止拉刀摆尾的作用
主切削刃
是前后刀面的交线
副切削刃
是前刀面和副后刀面的交线,分屑槽中也有两条副切削刃
过渡刃
可以是直线或圆弧,它有助于减缓刀尖的磨损
刀尖
主副切削刃的相交点
容屑槽
其形状必须有利于切屑卷曲,并能宽敞地容纳切屑
分屑槽
减小切削宽度,降低切削卷曲阻力,便于切削容纳在容屑槽内,从而改善拉削状况
棱
刀齿后刀面与齿背的交线
齿背
容屑槽中靠近后刀面的部分
2.4拉刀几何参数的选择和设计
1:
选择拉刀材料:
V
2:
拟订拉削余量切除顺序和拉削方式
拉削余量切除顺序为:
键测与大径——小径,拉刀切削齿的顺序是:
花键齿——圆形齿。
实际采用分层拉削渐成式。
后面用d、h和y表示角齿、花键齿和圆形齿;用c、g、j和x表示粗切、过度、精切和校准齿;用w和m表示工件预制孔和拉削孔。
3:
选择切削齿几何参数
前脚:
=20°,精切齿与校准齿倒棱前脚=20°
后脚:
粗切齿:
=2°30′+1°=0.10
精确齿:
=2°+30′=0.15
校准齿:
=1°+30′=0.2
4:
确定校准齿直径倒角齿不设校准齿
查表4—16(《刀具课程设计指导书》)得,花键齿、圆形齿的扩张量均为4um,则花键齿校准齿和圆形齿校准齿直径为
=34.10-0.004=34.096mm;
=28.021-0.002=28.0019mm;
5:
计算切削余量;
按表4-1(《刀具课程设计指导书》)计算圆形拉削余量为1mm,预制孔径为27mm,
实际拉削余量=28.0019-27=1.0019mm
花键余量=34.096-(29.898-0.1)=4.298mm
6:
选择齿升量;
查表4-4(《刀具课程设计指导书》)选择为
花键齿:
=0.050mm(矩形花键拉刀栏)
7:
设计容屑槽
⑴齿距计算
查表4-7
P=(1.2~1.5)=(1.2~1.5)=8mm=
==(0.6~0.8)p=6mm
⑵选择容屑槽
查表4-8
采用曲线槽,粗切齿用深槽,h=3mm,
精切齿用基本槽h=2.5mm
(3)校验容屑系数:
查表4-9得,容屑系数K=3
(4)校验同时工作齿数
查表4-7得l/p=30/8=3.8
所以:
=4=4+1=5,满足3≤≤8的校验条件
8:
花键齿截形设计
花键齿键宽按下列式子计算
=-
=-
式中,为花键键槽宽最大极限尺寸;为拉削扩张量(查表得=0.004mm);
为拉刀键齿制造公差带宽,为保证键赤耐用度高,应在制造范围内取最小值,这里取
=0.010mm。
则
=7.036-0.004=7.032mm
=7.032-0.010=7.022mm
拉刀键齿侧面应制出=0°的修光刃f,其下应磨出侧隙角1°30′。
(工厂常在齿高为1.25mm及以下的刀齿上磨侧隙。
)
9:
确定分屑槽参数
除校准齿和与其相邻的一个精切齿外,拉刀切削齿均磨制三角形分屑槽(表4-13)。
由于在每个圆形齿上都存在着不工作刃段,圆形齿段不必磨分屑槽。
10:
选择拉刀前柄
按表4-17选择Ⅱ型——A无周向定位面的圆柱形前柄,
公称尺寸=25mm
卡爪底径=19mm
11:
校验拉刀强度
通过计算分析,确认倒角齿拉削力最大,因而应计算拉刀倒角齿拉削力(表4-20、4-21和4-22)
=z(+2f)=6*(7.032+2*0.5)mm=48.192mm
=′*=98.55KN
拉刀最小截面积在卡槽底颈处,则拉应力
4×)=0.2GP
(表4-25),拉刀强度校验合格
12:
确定拉刀齿数及每齿直径
1)花键齿齿数初拟花键过渡齿与精切齿的齿升量为0.04,0.03,0.02,0.01,0.005mm,逐步递减,共切除余量A``=0.21mm。
花键粗切齿齿数
取46齿,多切去了的余量,应减去0.0125mm的齿升量。
因此,减去一个精切齿并将齿升量调整为0