第二章 现代设计技术Word文件下载.docx
《第二章 现代设计技术Word文件下载.docx》由会员分享,可在线阅读,更多相关《第二章 现代设计技术Word文件下载.docx(24页珍藏版)》请在冰豆网上搜索。
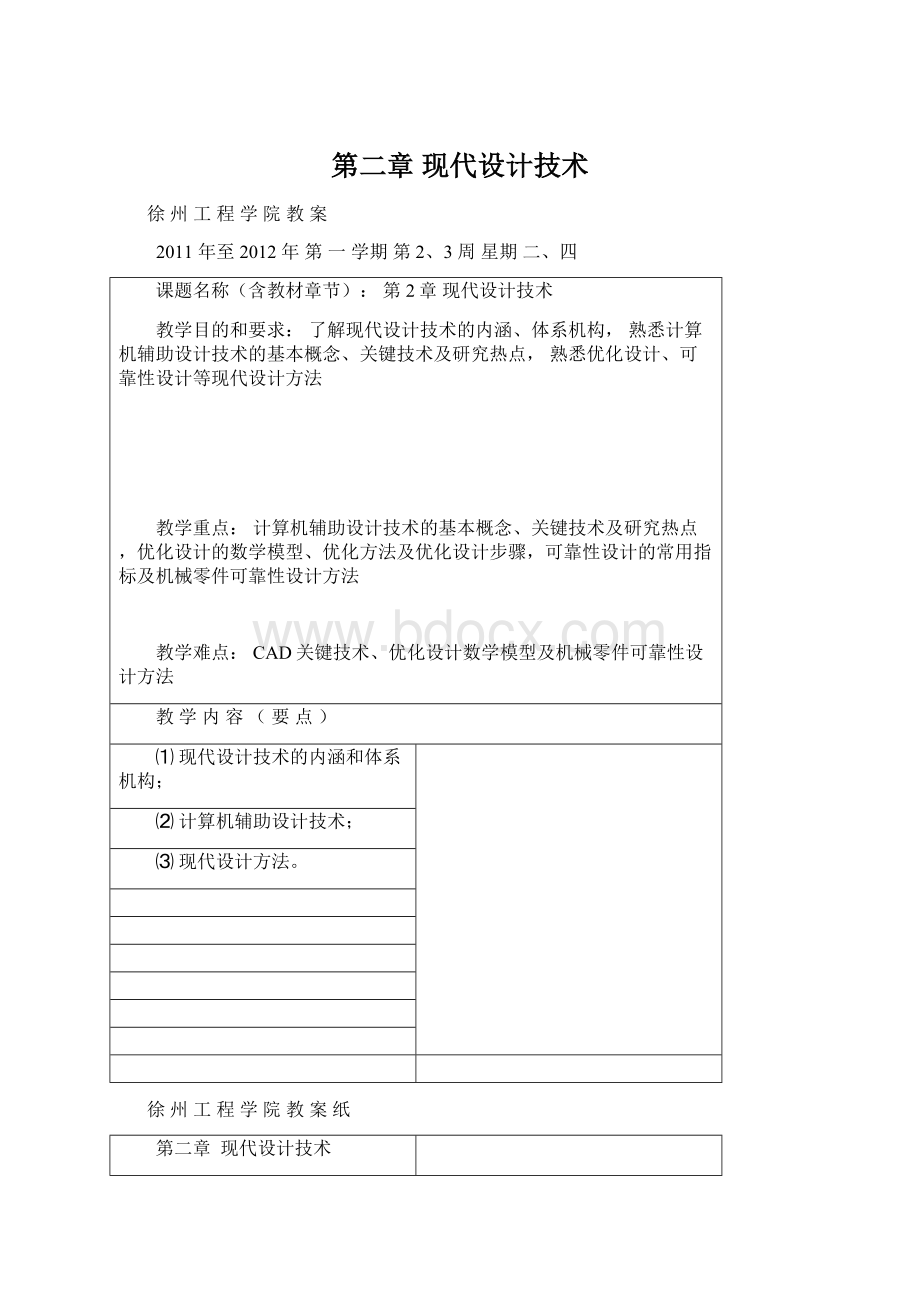
(5)并行化、最优化、虚拟化和自动化
(6)主动性
二、现代设计技术体系
现代设计技术内容广泛,涉及的相关学科门类多。
为了便于对现代设计技术的全貌了解,可将现代设计技术分解为有基础技术、主体技术、支撑技术和应用技术四个不同层次的技术组成。
1、基础技术
是指传统的设计理论与方法,包括运动学、静力学、动力学、材料力学等。
2、主体技术
现代设计技术的诞生和发展与计算机技术的发展息息相关,相辅相成。
计算机辅助设计技术以其对数值计算和对信息与知识的独特处理能力,成为现代设计技术的主干。
3、支撑技术
设计方法学、可信性设计技术以及设计试验技术,为设计信息的处理、加工、推理与验证提供了多种理论、方法和手段的支撑。
现代设计方法学包括系统设计、价值工程、绿色设计等;
可信性设计主要指可靠性与安全性设计、疲劳设计等;
设计试验技术包括通常的产品性能试验以及可靠性试验等。
4、应用技术
应用技术是针对实用的目的,解决各类具体产品设计领域的技术,如机床、汽车、工程机械、精密机械等设计的知识和技术。
第二节计算机辅助设计技术
一、计算机辅助设计的基本概念
1、概念
计算机辅助设计(ComputerAidedDesign,CAD)指利用计算机软件、硬件系统辅助工程技术人员对产品或工程进行设计、分析、修改以及交互式显示输出的一种方法(或手段),是一门多学科的综合性应用技术。
该技术已广泛应用于机械、电子、建筑、航空、航天、汽车、化工、冶金、环境工程等领域。
2、功能
■几何建模:
主要指产品的三维建模,是CAD研究的重要内容。
由于产品都是具有一定功能的几何体,为设计人员提供直观的、正确的产品图形具有重要意义。
■工程分析:
工程分析是产品设计的关键,主要包括产品常规设计和优化设计、有限元分析、可靠性分析、动态分析等科学计算。
■评价仿真:
主要通过动态仿真的方式为设计者提供逼真的运动图象以供决策。
■自动绘图:
CAD设计结果往往需要通过二维工程图或其他方式输出。
3、特点
(1)CAD技术是多学科综合性应用技术
经过近50年的不断发展和完善,CAD技术已由初期单一的图形交互处理功能转化为综合性的、技术复杂的系统工程,所涉及的学科领域在不断扩大,是多学科相互交融、综合应用的产物,并逐渐向集成化、网络化和智能化发展。
CAD技术主要涉及的学科领域包括计算机科学、计算机图形学、计算数学、工程分析技术、数据管理及数据交换技术、软件工程技术、网络技术、人机工程、人工智能技术、多媒体技术及文档处理技术等。
(2)CAD技术是现代设计方法和手段的综合体现
设计是一项复杂的创造性工作。
人们一直在探索各种设计理论,以期利用它们来有效地指导实际的设计工作。
基于计算机的先进设计理论与方法集中体现在CAD技术中,该技术涵盖了现代产品设计的主要设计活动,其中包括传统的几何造型设计、工程分析以及目前广泛研究的支持概念设计和基于Web的设计等。
(3)CAD技术是人的创造性思维活动同基于计算机的系统的有机融合
随着基于计算机的先进设计理论与方法的不断发展,CAD系统的智能化程度也会越来越高。
但任何智能化的CAD系统都只是一个辅助设计工具,都离不开使用者(人)的创造性思维活动和主导控制。
将人的创造性思维能力、综合分析和逻辑判断能力同CAD系统强大的数据、图形以及文档处理能力结合起来,才能使CAD技术发挥出巨大作用。
4、产生与发展
20世纪50年代,以美国为代表的工业发达国家处于航空和汽车等工业的生产需要,开始将计算机技术应用于产品的设计过程,逐渐发展形成具有重大影响力的计算机辅助设计技术。
其发展过程大致经历了如下几个发展阶段:
(1)20世纪50年代——CAD技术的萌芽期
(2)20世纪60年代——CAD技术的成长期
(3)20世纪70年代——CAD技术的发展期
(4)20世纪80年代——CAD技术的普及期
(5)20世纪90年代——CAD技术集成化期
二、CAD技术的应用
CAD技术是适应现代生产技术发展和市场需求快速变换的产物。
目前,CAD技术在产品或工程设计中主要应用于以下几个方面:
(1)绘制二维、三维工程图
主要用来取代传统的手工绘图工作,这是最普遍和最广泛的一种应用,也是中小企业采用得最多的一种CAD应用方式。
(2)建立图形及符号库
主要用于建立常用图形和符号库,以便于设计时调用,提高设计效率。
(3)参数化设计
对于那些具有相似结构的标准化或系列化零部件,通过对其结构尺寸和几何约束关系进行参数化定义,建立专用的图形程序库,调出时通过对设计参数进行赋值,即可生成所需的几何图形。
例如,对标准件、典型零件的设计(轴类零件、齿轮、皮带轮等)以及形状相似但尺寸不同的系列产品的设计等。
(4)三维造型
根据设计需求,采用线框、曲面或实体造型技术对产品的零部件进行三维造型设计,并可进行装配和运动仿真。
(5)工程分析
现代CAD技术提供强大的工程分析工具,如有限元分析、优化设计、运动学以及动力学分析、模拟仿真等。
这些分析工具可帮助设计人员进行合理的结构、强度、运动等设计工作。
(6)生成设计文档或报表
可以将设计属性制成说明文档或输出报表,其中有些设计参数可以用各种形式的图表表示,如直方图、扇形图、曲线图等,以使设计实施过程更清晰、形象、直观。
三、采用CAD技术的优点和风险
从CAD技术的特点和应用范围来看,采用CAD技术具有以下优点。
(1)提高设计效率、缩短设计周期
利用CAD技术,可减小设计人员的工作量和劳动强度,降低设计成本,从而能够提高设计效率、缩短设计周期、加速产品的更新换代、增强产品的市场竞争力。
(2)提高设计质量
利用计算机所提供的标准数据库、图形库和应用软件提供的优化技术和设计计算功能,可以减少人为的设计误差,达到最佳设计效果。
(3)便于产品标准化、系列化
利用CAD技术的参数化设计功能,可以方便地实现产品的系列设计;
利用存储于计算机中的标准设计信息,能够实现设计过程中的资源共享。
(4)在设计阶段可预估产品的特性
利用CAD技术中的运动分析、有限元分析、动态仿真等技术,可以在设计阶段预估产品的特性。
因此,可及早发现设计缺陷,从而能够提高设计质量、提高产品的可靠性、缩短新产品的试制周期。
(5)易于实现网络化设计
随着网络技术的迅速发展,基于网络的CAD系统也越来越多。
利用这样的系统,工程技术人员可以实现不同部门、不同地点之间的设计信息交流,提高设计工作的效率与灵活性,实现设计资源的跨平台共享。
(6)为实现CAM提供了基础
采用CAD技术生成的零件模型可以直接由计算机的CAM(ComputerAidedManufacturing,计算机辅助制造)软件转化为加工、管理信息,并传送给数控机床和生产组织者,实现产品设计与制造的一体化。
(7)使产品快速进入市场
在产品设计完成以后,即可根据设计文件及有关数据,利用仿真技术和多媒体技术生成数字样机,通过网络等各种媒体进行产品宣传,提前进行市场拓展。
采用CAD技术可以提高设计质量、缩短设计周期、降低设计成本、加快产品的更新换代速度,使企业可以保持良好的竞争能力。
但采用CAD技术也会给企业带来一定的风险和问题,具体体现在以下几个方面。
(1)一次性资金投入较大
采用CAD技术需要较大的资金投入来购买计算机的软硬件系统、支付相关的培训和开发费用,并且需要为软硬件的不断升级提供资金支持,但这些投资可能不会在短期内产生效益,需要有一段滞后期。
(2)对工程技术人员的素质和技能要求较高
设计人员是CAD系统的重要组成部分,并在系统中发挥着主导作用。
如果缺乏具有良好素质并能掌握CAD技术的工程技术人员,则很难使所配置的CAD系统发挥应有的作用。
因此,企业在采用CAD技术时,应根据自身资金及人员结构情况综合考虑,以寻求系统的最佳配置。
第三节现代设计方法
一、优化设计
所谓优化就是一种对问题寻优的过程,人们所从事的任何工作都希望尽可能做好,以期得到一个理想的目标。
要实现问题的优化必须具备两个条件:
一是存在一个优化目标,另一是具有多个方案可供选择。
优化设计是20世纪60年代发展起来的一门新的学科,它是最优化技术和计算机技术在设计领域应用的结果。
1、优化设计的数学模型
工程设计问题的优化,可以表达为一组优选的参数,在满足一系列限制条件下,使设计指标达到最优。
因此,优化设计的数学模型可由设计变量、目标函数和设计约束三部分组成,被称之为优化设计的三要素。
(1)设计变量
在优化设计的过程中,不断进行修改、调整,一直处于变化的参数称为设计变量。
设计变量可以是表示构件形状、大小、位置等几何量,也可以是表示质量、速度、加速度等物理量,设计变量的全体实际上是一组独立的变量,可用一个列向量表示:
由n个设计变量所组成一个向量空间,称之为设计空间。
(2)目标函数
目标函数是设计变量的函数,是设计中所追求的目标。
如:
轴的质量,弹簧的体积,齿轮的承载能力等。
在优化设计中,用目标函数的大小来衡量设计方案的优劣,故目标函数也可称评价函数。
目标函数的一般表示式为:
优化设计的目的就是要求所选择的设计变量使目标函数达到最佳值,通常
。
在工程设计中,所追求的目标可能是多种多样。
当目标函数只包含一项设计指标时,被称为单目标优化;
当目标函数包含多项设计指标时,称为多目标优化。
目前处理多目标设计问题的方法是组合成一个复合的目标函数,如采用线性加权的形式,即
(3)设计约束与可行域
优化设计不仅要使所选择方案的设计指标达到最佳值,同时还必须满足一些附加的设计条件,这些附加条件都构成对设计变量取值的限制,在优化设计中被称之为设计约束。
设计约束的表现形式有两种:
一种是等式约束;
另一种是不等式约束。
等式约束:
不等式约束:
可行域:
凡满足所有约束条件的设计点,它在设计空间的活动范围。
(4)数学模型的规格化
优化设计的数学模型是对优化设计问题的数学抽象。
为便于表达和计算的方便,一般将数学模型写成如下规格形式:
2、优化设计步骤
(1)设计对象的分析
(2)设计变量和设计约束条件的确定
(3)目标函数的建立
(4)合适的优化计算方法的选择
(5)优化结果分析
二、可靠性设计
1、可靠性的概念
可靠性(Reliability):
在规定的条件和规定的时间内,完成规定功能的能力。
2、可靠性设计的主要内容
(1)故障机理和故障模型研究
(2)可靠性试验技术研究
(3)可靠性水平的确定
3、可靠性设计的常用指标
(1)产品的工作能力
在保证功能参数到达技术要求的同时,产品完成功能所处的状态,称为产品的工作能力。
(2)可靠度
可靠度是指产品在规定的工作条件下和规定的时间内完成规定功能的概率。
可靠度越大,说明产品的可靠性越大。
假设有N0个相同的产品在相同的条件下工作,从他们开始运行到t时刻的时间内,有Nf(t)个产品失效,Ns(t)个产品工作完好。
则,该产品到时间t的可靠度可表示为:
系统的不可靠度F(t)可相应地表示为:
因为一个系统发生故障和无故障是互斥事件,必须满足R(t)+F(t)=1。
故可靠度还可以写成:
例如,某种系统(或部件或元件)1000个,工作1000h,有10个发生故障。
我们可以计算出这种系统(或部件或元件)千小时的可靠度为:
(3)失效率
失效率又称故障率,它表示产品工作到某一时刻后,在单位时间内发生故障的概率。
失效率越低,产品越可靠。
(4)平均寿命
描述可靠性的另一个重要参数称为平均故障间隔时间MTBF或平均无故障时间(也称为故障前平均时间)MTTF。
前者用来描述可修复的产品;
后者用于描述不可修复产品。
将MTTF与MTBF统称为平均寿命,用θ表示:
N——试验品数(不可修复产品),总故障次数(可修复产品)
ti——第i个产品失效前工作时间(不可修复产品),第i次故障前的无故障工作时间(可修复产品)
例如,1000台微型计算机,运行1000h,累计出现10次故障,则这种微型机的MTBF计算如下:
4、机械零件可靠性设计
(1)应力、强度定义:
在机械产品中,广义的应力是引起失效的负荷,强度是抵抗失效的能力。
由于影响应力和强度的因素具有随机性,所以应力和强度具有分散特性。
要确定应力和强度的随机特性,首先应了解影响应力和强度随机性的因素。
影响应力的因素:
影响应力的主要因素有所承受的外载荷、结构的几何形状和尺寸,材料的物理特性等。
影响强度的因素:
影响强度的主要因素有材料的机械性能、工艺方法和使用环境等。
1)应力-强度干涉理论
在机械产品中,零件(部件)是正常还是失效决定于强度和应力的关系。
当零件(部件)的强度大于应力时,其能够正常工作;
当零件(部件)的强度小于应力时,其发生失效。
因此,要求零件(部件)在规定的条件下和规定的时间内能够承载,必须满足以下条件
S——零件(部件)的强度;
s——零件(部件)的应力。
实际工程中的应力和强度都是呈分布状态的随机变量,把应力和强度的分布在同一座标系中表示(如图2-1所示)
当强度的均值大于应力的均值时,在图中阴影部分表示的应力和强度“干涉区”内就可能发生强度小于应力——即失效的情况
这种根据应力和强度干涉情况,计算干涉区内强度小于应力的概率(失效概率)的模型,称为应力—强度干涉模型。
在应力—强度干涉模型理论中,根据可靠度的定义,强度大于应力的概率可表示为
图2-1应力-强度概率密度分布
2)可靠度的一般表达式
根据以上干涉模型计算在干涉区内强度大于应力的概率——可靠度。
如图2-2所示,当应力为时,强度大于应力的概率为
——强度分布密度函数
——应力s0处于ds区间内的概率为
——应力分布密度函数;
图2-2概率密度函数联合积分求可靠度
假设
与
为两个独立的随机事件,因此两独立事件同时发生的概率为
因为上式s0为应力区间内的任意值,现考虑整个应力区间内的情况,有强度大于应力的概率(可靠度)为:
当已知应力和强度的概率密度函数时,根据以上表达式即可求得可靠度。
3)可靠度的计算方法
利用强度应力干涉理论,可靠度定义为强度大于应力的概率:
当应力和强度均为正态分布时,有
式中Z——安全余量,z=S-s由于应力和强度均为正态分布,根据正态分布的和(差)仍为正态分布的性质,安全余量也为正态分布。
可靠度:
将上式化为标准正态分布形式
式中:
(1)
从
(1)式可知,当已知应力和强度的分布参数后,就可算得,从正态分布表就可查得可靠度。
因此,
(1)式把应力分布参数、强度分布参数和可靠度直接联系起来,称之为“连接方程”,称之为连接系数,也称为可靠性系数。
现定义:
(2)
称为可靠度指标,根据
(1)和
(2)式得
(3)
式(3)即强度与应力都是正态分布时,可靠度的计算公式
5、系统的可靠性预测
可靠性预测,即用已知组成系统的各个独立单元的可靠度计算系统的可靠性指标。
1)可靠性预测的目的:
协调设计参数及指标,提高产品的可靠性;
对比设计方案,以选择最佳系统;
预示薄弱环节,采取改进措施。
系统的组成形式通常有:
串联、并联、混合联三种形式。
2)各种不同组成形式的可靠度计算
(1)串联系统的可靠度计算
设各元件的失效事件是相互独立的,其可靠度分别为R1、R2…Rn,系统的可靠度为Rs,则由概率乘法定理可得:
由上式可知,串联系统的可靠度比系统中最不可靠的元件可靠度还低,并且随着元件可靠度的减小和元件数量的增加,其可靠度迅速降低。
因此,为确保系统的可靠度不至过低,应尽量减少串联元件数量,并尽可能提高各元件的可靠度。
(2)并联系统可靠性计算
由概率乘法定理可知,并联系统的可靠度为:
当R1=R2=…=Rn=R时,则
并联系统的单元数目越多,系统的可靠度越高,但系统的体积、重量及成本等也随之增加。
(3)混合系统可靠度计算
混合系统:
即由串联系统及并联系统组合而成的系统。
计算方法:
先将并联单元转化为一个等效的串联单元,然后再按照串联系统的可靠度进行计算。
例:
该系统可靠度为:
三、价值工程
1、价值工程的基本概念
价值工程(ValueEngineering,简称VE),亦称价值分析(ValueAnalysis,简称VA),是研究如何以最低的寿命周期成本,可靠地实现对象(产品、作业或服务等)的必要功能,而致力于功能分析的一种有组织的技术经济思想方法和管理技术。
(1)价值
价值工程中的价值指的是产品功能与成本之比,是一个相对量。
用公式表示如下:
V=F/C
式中:
V—产品的价值
F—产品的功能
C—产品的成本
(2)功能
功能是对象能满足某种需求的一种属性。
具体来说,功能就是功用、效用。
(3)寿命周期成本
指整个寿命周期(从产生到结束)过程中发生的全部费用。
C=C1+C2+(-)C3
C—寿命周期成本
C1—设计制造费用
C2—使用费用
C3—残值费用(残值收入为-,清理费用为+)
2、价值工程的特点和作用
(1)价值工程的特点
价值工程是一种以提高产品和作业价值为目标的管理技术,它具有以下特点:
1)价值工程强调产品的功能,重点放在对产品功能的研究上;
2)价值工程将确保功能和降低成本作为一个整体同时来考虑,以便创造出总体价值最高的产品;
3)价值工程强调不断改革和创新,开拓新构思和新途径,获得新方案,创造新功能载体,从而简化产品结构,节约原材料,提高产品的技术经济效益;
4)价值工程要求将功能定量化,即将功能转化为能够与成本直接相比的货币值;
5)价值工程是以集体的智慧开展的计划、有组织的活动。
(2)价值工程在企业管理中的作用
1)可以有效地提高经济效益
2)可延长产品市场寿命期
3)有利于提高企业管理水平
4)可促进技术与经济相结合、软技术与硬技术相结合。
3、价值工程研究对象的选择
(1)对象选择的定性分析
(2)对象选择的定量分析
ABC法、价值系数法、百分比法、产品寿命周期选择法等。
4、价值工程的功能分析
功能分析是价值工程的核心。
它是对研究对象系统地分析其功能,科学的评价其重要性,通过功能和成本匹配关系定量计算对象价值大小,确定改进对象的过程。
功能分析一般分为功能定义、功能整理、功能评价三个步骤进行。
(1)功能定义
功能定义是对价值工程对象及其组成部分的功能所作的明确表述。
常采用“两词法”(即动宾词组法)来简明扼要地表述。
(2)功能整理
功能整理是对定义出的功能进行系统分析、整理,明确功能之间的关系,分清功能类别,建立功能系统图。
其步骤如下:
1)建立功能卡片
2)明确功能的上下位和并列关系
3)建立功能系统图
(3)功能评价
功能评价就是用V=F/C公式计算出各个功能的价值系数,以解决功能数量化的问题。
四、绿色设计
1.绿色设计产生的背景
20世纪70年代以来,工业污染所导致的全球性环境恶化到了前所未有的程度,迫使人们不得不重视这种环境污染的现实。
20世纪90年代,全球性的产业结构开始调整,向着资源利用合理化、废弃物产生少量化、对环境无污染或少污染的方向发展。
绿色设计与绿色制造技术应运而生。
绿色设计是由绿色产品的诞生所引申的一种设计技术。
2.绿色产品的定义和特点
(1)定义:
绿色产品:
在产品生产周期内,包括原材料制备、设计、制造、包装、运输、使用、回收、再用或再生过程,能节约资源和能源,对生态环境无危害或少危害,且对生产者及使用者具有良好保护性的产品。
(2)特点:
1)优良的环境友好性;
2)最大限度地利用材料能源;
3)最大限度地节约能源。
3.绿色设计与传统设计
传统设计:
以企业的发展战略和获取自身最大经济利益为出发点,主要考虑产品的功能、质量和成本等基本属性。
绿色设计:
以保护环境资源为核心,在产品全生命周期内优先考虑产品的环境属性,使产品在整个寿命周期内对环境影响最小,资源效率最高,在满足环境目标的同时保证产品的基本性能和使用寿命。
4、绿色设计的主要内容
(1)绿色产品的描述与建模;
(2)绿色设计的材料选择;
(3)面向拆卸性设计;
(4)产品的可回收性设计;
(5)绿色产品的成本分析
(6)绿色产品设计数据库。
5、绿色设计原则
(1)资源最佳利用原则
(2)能量消耗最少原则
(3)“零污染”原则
(4)“零损害”原则
(5)技术先进原则
(6)生态经济效益最佳原则