图形电镀铜锡操作手册Word文件下载.docx
《图形电镀铜锡操作手册Word文件下载.docx》由会员分享,可在线阅读,更多相关《图形电镀铜锡操作手册Word文件下载.docx(18页珍藏版)》请在冰豆网上搜索。
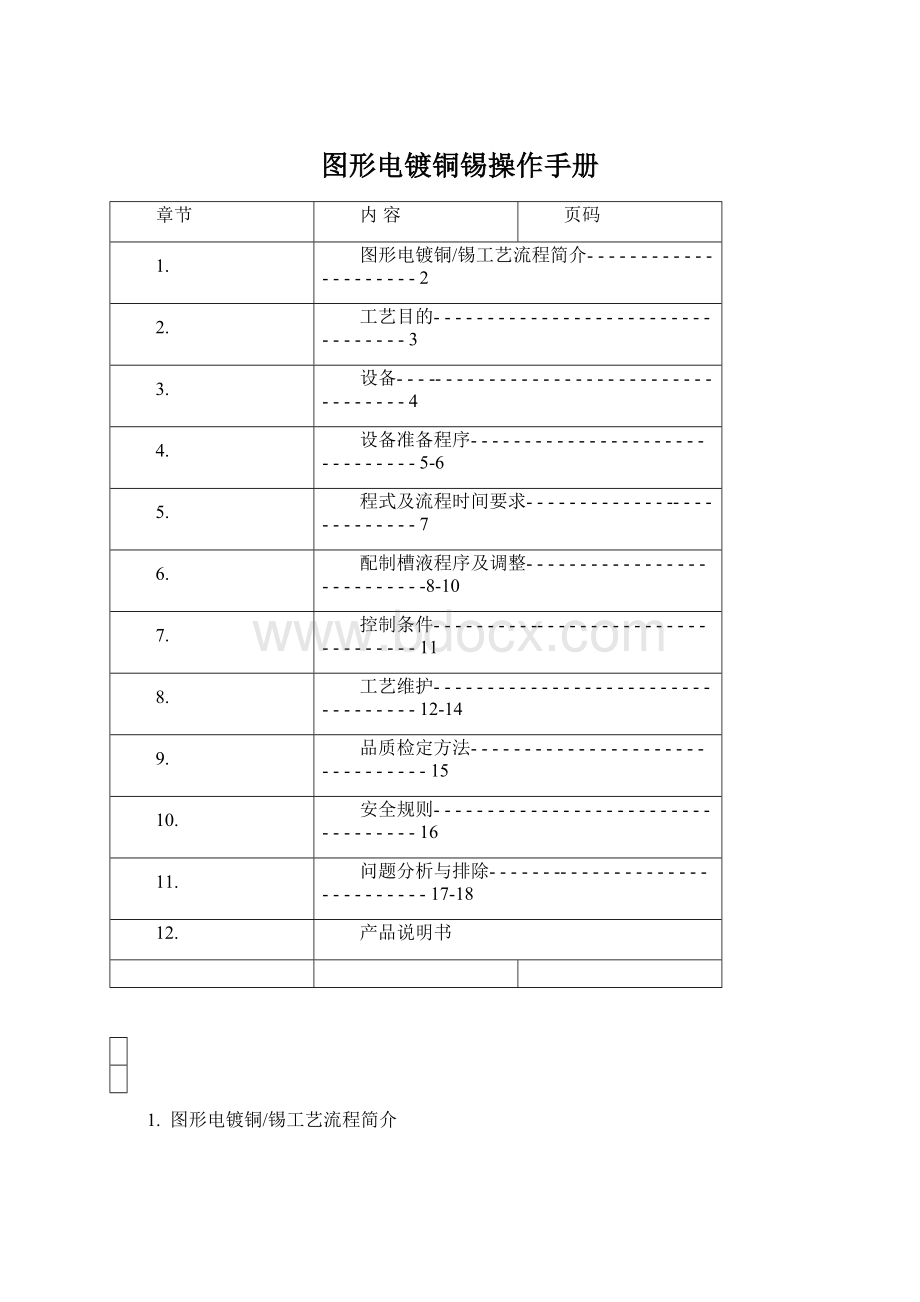
减轻前处理清洗不良对镀铜溶液之污染,并保持镀铜溶液中硫酸含量之稳定。
2.4电镀铜CopperGleam125T-2(CH)
实现孔壁及线路之厚度要求,保证其优良之导电性能。
2.5浸酸⑵
减轻前处理清洗不良对镀锡溶液之污染,并保持镀锡溶液中硫酸含量之稳定。
2.6电镀锡RonastanEC
作为碱性蚀刻之抗蚀层,形成良好之线路图形。
2.7退夹具
去除挂具上之金属铜/锡
3.设备
缸号
工序
材料
温度
(℃)
过滤
(每小时循环次数)
摆动/搅动
用水
加热器
备注
31
镀铜
P.P.
22-28
4-6
M/A
DI
--
C.C.S
&
TEF
30
29
28
27
26
25
24
23
22
21
20
水洗
CW
19
18
酸浸
1-2
M
17
16
15
微蚀
28-32
QTZ
14
13
12
11
除油
25-40
SS
10
9
镀锡
18-25
8
7
6
5
褪镀
35-45
4
3
2
热风干
70-80
-
1
上/下板
P.P.:
聚丙烯SS:
不锈钢M:
机械摆动
A:
空气搅动DI:
去离子水CW:
自来水
C.C.S:
冷却控制系统TEF:
铁氟龙
QTZ:
石英
4.设备准备程序
4.1槽子的清洗
在配槽之前,工艺槽及附属设备必须彻底清洁,并随后用硫酸溶液中和。
对于新设备或先前使用其它工艺的设备,本清洗程序更显得重要。
4.1.1清洁液──氢氧化钠20-50g/l
中和液──硫酸20-50ml/l
4.1.2程序
A.用清水清洗各缸及其附属设备
B.各缸注满清水浸洗,如有打气及过滤系统则开启清洗(无需加滤芯)
C.排走废水
D.加入清洁液(NaOH20-50g/l)到槽内,浸洗8小时以上,并开启所有打气及过滤泵。
E.排走氢氧化钠清洁液
F.注入清水,清洗干净。
G.排走废水
H.加入中和液(H2SO420-50ml/l)到槽内,浸洗8小时以上,并开启所有打气及过滤泵。
I.排走硫酸溶液
J.再以清水清洗,排走废水。
K.各槽注满清水浸洗,开启打气及过滤泵,清洗整套设备。
L.排走废水,槽子已清洗完毕。
4.2新阳极袋的清洗
A.用50g/l氢氧化钠溶液加热至50℃左右将阳极袋放入该溶液中浸泡8小时。
B.取出阳极袋用清水清洗干净。
C.用100ml/l硫酸溶液浸泡8小时以上。
D.用纯水彻底清洗干净。
4.3阳极钛篮/锆篮的清洗
A.用50g/l氢氧化钠溶液加热至50℃左右,将阳极篮放入该溶液中浸泡8小时。
B.取出阳极篮用清水清洗干净。
C.用100ml/l硫酸溶液浸泡8小时以上
D.用纯水彻底清洗干净
4.4聚丙烯过滤芯的清洗
A.以热纯水清洗
B.以100ml/l硫酸浸泡8小时以上
C.用纯水彻底清洗干净
4.5新铜阳极的清洗
A.用50g/l氢氧化钠溶液浸泡8小时以上
B.用清水冲洗干净
C.再以50ml/l硫酸+50ml/l双氧水浸泡,阳极呈鲜红色即可。
D.用清水清洗干净
E.用100ml/l硫酸浸泡
F.用纯水彻底冲洗干净即可使用
4.6新锡阳极的清洗
A.在10%CP级H2SO4(V/V)溶液中浸泡2小时
B.用纯水冲洗干净
5.程式及流程时间要求
Items
Process
DippingTime
(min)
DroppingTime
(sec)
CopperPlate
80/120
15-30
WaterRinse
5-10
AcidDip
MildEtch
3-4
2-3
AcidClean
TinPlate
10-13
StrippingBars
7-8
HotAirDry
6-7
Load/Unload
6.配制槽液程序及用量
1.)配制槽液用量
所用药品名称
浓度
21-31
CuSO4.5H2O
H2SO4(98%)
HCl(1N)
125T-2(CH)Additive
125T-2(CH)Carrier
65g/l
120ml/l
2.1ml/l
5ml/l
10ml/l
浸酸
100ml/l
70g/l
20ml/l
开新缸时留10%体积原液
RonacleanSE250
250ml/l
8-9
SnSO4
RonastanECPartA
RonastanECPartB
40g/l
40ml/l
2.)配制槽液程序
1.除油缸
a.加入2/3体积之DI水
b.根据槽体积按250ml/l加入所需的RonacleanSE250
c.补加DI水标准液位后,开启循环泵,混合均匀。
2.微蚀缸
a.预留10%体积原液,加入3/4体积之DI水并开启打气搅拌。
b.加入20ml/lAR硫酸(98%),冷却至50℃,停止打气。
c.加入70g/l的NaPS
d.开动打气,直至完全溶解。
e.补加DI水至标准液位,开启循环泵,混合均匀。
3.浸酸缸
a.加入2/3体积之DI水并开启打气搅拌
b.缓缓加入100ml/l之AR硫酸(98%)
c.补加DI水位至标准液位
4.电镀铜缸
1新配槽药水碳处理步骤
配制3倍开缸浓度的硫酸铜浓缩液
a.加入2/3体积之DI水,开启打气搅拌。
b.缓缓加入50ml/lARH2SO4(98%)
c.加入200g/lCuSO4.5H2O,补加DI水至最后体积。
d.将溶液升温至45-55℃,加入30%双氧水5ml/l,保温2小时,开轻微打气搅拌。
e.开大打气,升温至70℃
f.停止升温,加入活性炭粉5g/l,搅拌2小时。
g.停止打气,静置4-8小时。
h.用5-10μm滤芯及助滤粉,将镀液过滤至缓冲缸内。
i.再用5-10μm滤芯及助滤粉,将镀液由缓冲缸过滤至铜缸。
j.分析各成份并作记录,以备配槽时使用。
2CopperGleam125T-2(CH)配槽步骤
a.计算配槽所需的已碳处理好的硫酸铜浓缩液的体积并加入至槽中,补加DI水至60%液位。
b.根据计算在打气搅拌下补充不足的AR硫酸,开启循环泵。
c.加入DI水至标准液位
d.分析硫酸铜、硫酸含量并补加不足量。
e.分析氯离子含量并用AR级盐酸补至50ppm
f.在温度降至32℃以下,添加5ml/lCopperGleam125T-2(CH)Additive和10ml/lCopperGleam125T-2(CH)Carrier。
g.分别以如下电流密度及时间进行拖缸
5ASF6小时
15ASF4小时
20ASF2小时
h.根据HullCell试验及CVS分析,补加光剂至正常范围。
5.电镀锡缸
a.加入2/3缸体积之DI水至工作槽中
b.缓缓地加入100ml/lCP级98%硫酸
c.加入40g/l硫酸亚锡并保证其完全溶解
d.待温度冷却至23-29℃后,开启循环泵。
e.加入20ml/lRonastanECPartA及40ml/lRonstanECPartB
f.补加DI水至标准液位后,搅拌均匀。
g.分别以10ASF、15ASF各拖缸4小时。
h.对镀液作含量分析并调整
7.控制条件
工序
控制项目
控制范围
控制点
分析频率
温控范围
H2SO4(96%)
40-60ml/l
50ml/l
1次/天
25-37℃
微蚀
Cu
60-80g/l
1-3%(V/V)
<
15g/l
2%(V/V)
2次/天
28-32℃
浸酸⑴
9-12%(V/V)
10%(V/V)
1次/2天
室温
Cl-
55-68g/l
100-120ml/l
40-80ppm
2.5-10ml/l
10-40ml/l
60ppm
1次/3天
1次/周
22-28℃
35-45g/l
90-110ml/l
15-25ml/l
30-50ml/l
18-25℃
8.工艺维护
1.)维护项目、频率及方法
工序名称
维护项目
维护频率
方法
125T-2(CH)Additive
AH调整
自动添加
320ml/1000AH
HullCell调整
按HullCell结果补加
磷铜球补加及拖缸
拖缸5ASF,10ASF各4小时
阳极清洗
1次/2月
见
(2)A
滤芯更换
见
(2)B
阳极袋清洗
见
(2)C
碳处理
1次/4-6个月
见
(2)D
ECPartA
自动补加
500ml/1000AH
ECPartB
锡球补加及拖缸
拖缸10ASF,15ASF各4小时
2.)电镀铜缸维护方法
A.旧磷铜球处理
a.将旧磷铜球用10%(V/V)CPH2SO4和10%(V/V)H2O2(30%)混合浸泡至黑膜退除尽。
b.以DI水冲洗后,用5%(V/V)CPH2SO4浸泡10-15分钟。
c.每次补加铜球后,须以5ASF,10ASF电流密度拖缸各4小时。
B.滤芯更换
新滤芯的清洗
a.以热DI水清洗
b.以100ml/l硫酸浸泡8小时以上
c.用DI水彻底清洗干净
C.阳极袋清洗
a.用毛刷擦去表面脏物
b.在10%(V/V)CPH2SO4和10%(V/V)H2O2(30%)混合溶液浸泡2小时
D.电镀铜溶液维护
a.每月以碳芯过滤镀液1次
b.根据HullCell试验或CVS分析,判断镀液有机物污染程度,4-6个月时进行一次活性炭处理。
c.镀液活性炭处理步骤
将需进行碳处理之溶液移至碳处理缸,以DI水补至液位并调整成份至正常
范围。
将溶液加热到40-50℃,按5ml/l加入H2O2(30%),搅拌4-6小时
继续加热至60-80℃,缓慢加入4-5g/l活性炭粉,于60℃搅拌2-4小时。
停止加热及搅拌,静置8-12小时。
用5-10µ
m滤芯及助滤粉,将镀液过滤至缓冲缸内。
再用5-10µ
m滤芯及助滤粉,将镀液过滤至铜点。
以DI水补加镀液至正常液位,并分析镀液成份,调整至工艺范围内。
用10ASF,20ASF电流密度各拖缸4小时。
加入125T-2(CH)Additive5ml/l,125T-2(CH)Carrier10ml/l。
再以20ASF电流密度拖缸2小时即可生产。
3.)电镀锡缸维护方法
A.锡阳极清洗处理
a.将锡阳极球用DI水冲洗干净后,在10%(V/V)CP级H2SO4溶液中浸泡2小时。
b.用DI水冲洗干净
c.每次补加锡阳极球后,须以10ASF,15ASF电流密度拖缸各4小时。
4)设备维护
A.阳极杆及V座维护
在每次阳极维护期间,用10%(V/V)CP级H2SO4擦净阳极杆及V座上之污痕,并用自来水洗净。
B.阴极飞巴维护
用10%(V/V)CP级H2SO4擦净飞巴上污痕,并用自来水洗净。
C.每天需检查生产线上如下项目
整流器表现
电流输出
循环系统
空气搅拌
药水温度
飞巴及阳极巴接电位置
自动加药系统工作状况
9.品质检定方法
1.)热冲击测试
样品孔铜规格:
孔内铜厚≥1mil
测试方法:
把样品截成10×
10cm,然后在145±
5℃的烘箱内烘烤4小时,自然冷却后,在288±
5℃的锡炉(Pb/Sn=37/63)漂浮10±
1秒,3Cycle,切片后在显微镜下观察孔内状况,不允许有铜层断裂现象。
2.)延展性测试
测试方法
a.用不锈钢片在镀槽或延展性测试槽上电镀上2mil铜厚。
b.以130℃把铜片烤2小时。
c.用延展性测试机进行测试。
d.测试结果,延展性≥12%为合格。
3.)HullCell测试
A.铜缸药水HullCell测试参数
a.电流:
2A
b.时间:
10分钟
c.搅拌:
d.温度:
26℃
B.锡缸药水HullCell测试参数
1A
5分钟
机械搅拌
23℃
10.安全规则
1)安全设备
洗眼器:
操作人员不慎溅到化学药水时使用
手套:
戴细棉手套用于搬板子或检验板子时
耐酸碱手套:
操作人员操作化学药品时使用
药水添加时必须戴防护面罩及手套
2)机械操作安全规定
a.机械设备之抽风每日需检查畅通无阻,否则请维修人员协助排除问题。
b.每日保养由操作人员执行,设备外观清洁及槽内液位检查或更换药水,并检查连线管路要求完整,各项指示灯操作开关要求正常驱动,否则即须反应,通知维修。
c.现场操作时须检查各阀门开关是否定位,换槽时,须先关掉加热器,以免损坏。
d.每班须检视自动添加桶药水液位,不得低于标示点。
e.每周测量自动添加DosingPump之流量。
f.全线震荡器每月保养一次,以维持良好功能。
11.问题分析与排除
1)各镀铜层间附着力不良
原因
改善方法
1.电镀前清洁处理不当,底铜表面氧化或钝化皮膜未除尽.
提高除油槽液的温度以利于除油污和指纹
检查除油槽和微蚀槽液的活性并改善之
2.除油缸中的湿润剂被带出或水洗不足造成底铜的钝化
检查水洗程序,增加水洗水流量
提高水洗水温度
3.板子进入镀槽后电源并未立即开启
重新检查整流器之自动程序
4.干膜显影后水洗不足
检查干膜工序之显影水洗条件并改善之
2)线路镀铜出现局部漏镀或阶梯镀
1.干膜显影不干净
重新检查干膜之显影作业条件
2.板面上已有指纹印及油渍的污染
提高电镀前处理除油槽液之温度
改善持板方法,不可用手指抓取板面
3.镀液中有机物含量过多
活性炭处理镀铜液
4.干膜表面渗出显影液之残迹
显影过后须放置30分钟才可电镀以使反应达到平衡
3)镀层过薄
1.电镀过程中,电流或时间不足。
确认板子面积以决定总电流的大小,并确认电流密度及时间无误。
2.板子与挂架或挂架与阴极杆的接触导电不良
检查整流器、板子等所有的电路接点。
4)镀铜层出现凹点
1.镀铜槽中空气搅拌不足或不均匀
增加空