PCB工艺总结DOCWord文档下载推荐.docx
《PCB工艺总结DOCWord文档下载推荐.docx》由会员分享,可在线阅读,更多相关《PCB工艺总结DOCWord文档下载推荐.docx(24页珍藏版)》请在冰豆网上搜索。
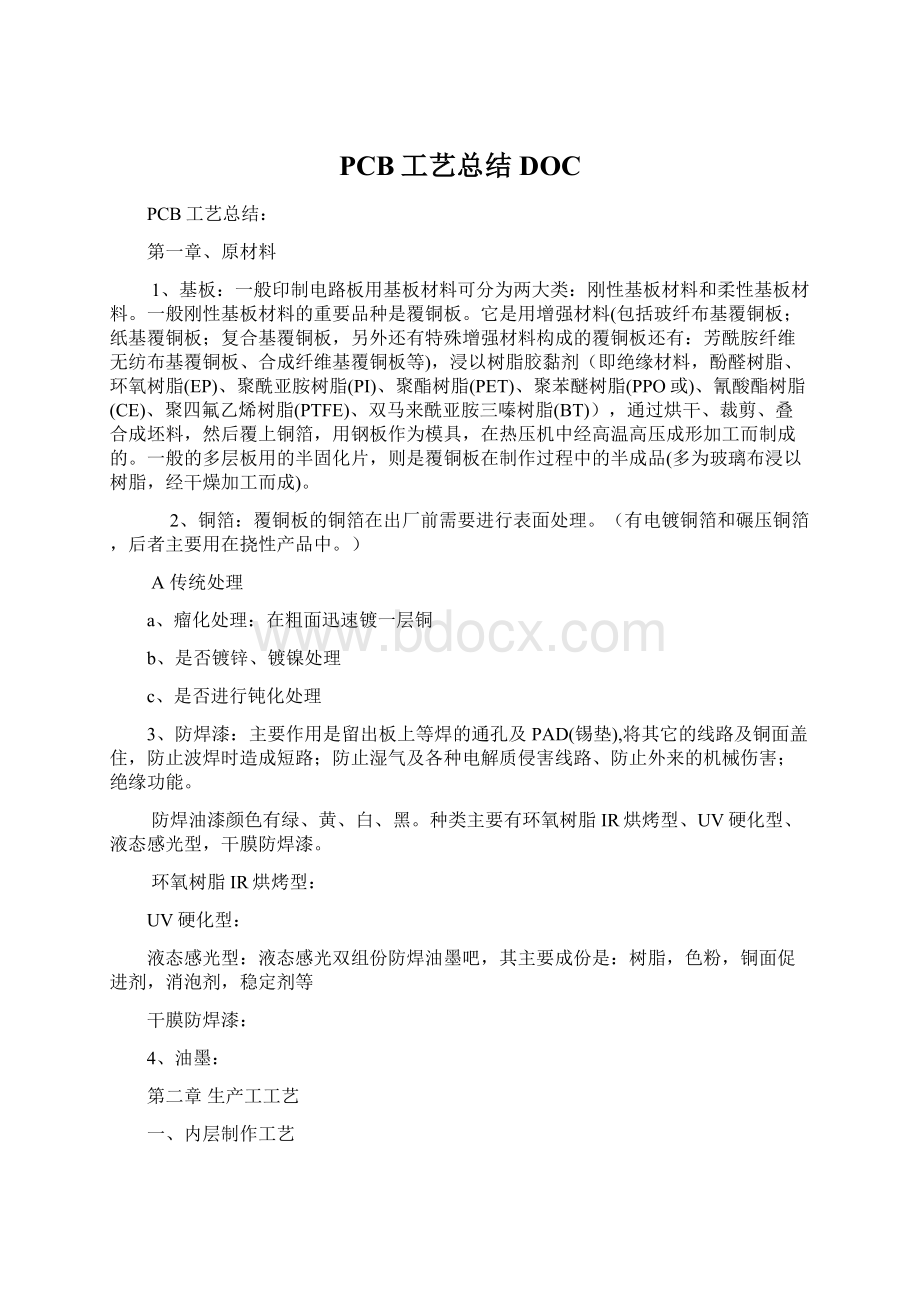
将一张大料根据不同拼板要求用机器切成小料的过程。
开料后的板边尖锐,容易划伤手,同时使板与板之间擦花,所以开料后再用磨边机磨边。
2、铜面处理:
在印刷电路板制程中不管那一个步骤,铜面的清洁与粗化的效果关系着下一工序的成败。
以下工序需要进行铜面处理:
a.干膜压膜;
b.内层氧化处理前;
c.钻孔后;
d.化学铜前;
e.镀铜前;
f.绿漆前;
g.喷锡(或其它焊垫处理流程)前;
h.金手指镀镍前
除a.c.f.g.外,其余工序的铜面处理皆属制程自动化中的一部分。
(1)铜面处理工艺(a.刷磨法、b.喷砂法、c.化学法)
刷磨法:
需要做刷良试验,确定刷深及均匀性。
a、优点:
成本低、制程简单弹性;
b、缺点:
薄板细线路板不易进行、基材拉长不适内层薄板、刷痕深时易造成D/F附着不易而渗镀、有残胶之潜在可能
c、工艺流程:
利用刷磨均匀抛刷铜面其平整且刷痕一致,获得均匀的粗糙度,对油墨有良好的附著力。
刷磨轮分三种:
尼龙刷磨;
白毛清洗刷磨(无研磨剂)、不织布刷磨轮;
.喷砂法:
喷砂材料由70%矿物化火山岩组成,去除氧化物,粗糙铜面。
化学微蚀法(发展趋势,因为产品向着超薄方向发展):
只针对内层薄片(厚度小于8mil)使用。
有时与刷磨工序联合使用。
主要微蚀液为sps(过硫酸钠)+硫酸,过硫酸铵+硫酸体系;
双氧水+硫酸体系.微蚀速度40~60u/s.
3、图像转移
(1)印刷法(将逐步被干膜法替代):
下列是目前尚可以印刷法cover的制程:
a.单面板之线路,防焊(大量产多使用自动印刷,以下同)
b.单面板之碳墨或银胶c.双面板之线路,防焊
d.湿膜印刷
e.内层大铜面
f.文字
g.可剥胶(Peelableink)
(2)丝网印刷:
丝网印刷中几个重要基本原素:
网材,网版,乳剂,曝光机,印刷机,刮刀,油墨,烤箱等,.
a.网布材料
(1)依材质不同可分丝绢(silk),尼龙(nylon),聚酯(Polyester,或称特多龙),不锈钢,等.电路板常用者为后三者.
(2)编织法:
最常用也最好用的是单丝平织法PlainWeave.
b.网版(Stencil)的种类
(1).直接网版(DirectStencil)
将感光乳胶调配均匀直接涂布在网布上烘干后连框共同放置在曝光设备台面上并覆以原稿底片再抽真空使其密接感光经显像后即成为可印刷的网版通常乳胶涂布多少次,视印刷厚度而定.此法网版耐用,安定性高,用于大量生产.但制作慢,且太厚时可能因厚薄不均而产生解像不良.
(2).间接网版(IndirectStencil)
把感光版膜以曝光及显像方式自原始底片上把图形转移过来然后把已有图形的版膜贴在网面上待冷风干燥后撕去透明之载体护膜即成间接性网版其厚度均匀,分辨率好,制作快,多用于样品及小量产.
c.油墨
油墨的分类有几种方式
(1).以组成份可分单液及双液型.
(2).以烘烤方式可分蒸发干燥型化学反应型及紫外线硬化型(UV)
(3).以用途可分抗蚀,抗镀,防焊,文字,导电,及塞孔油墨.不同制程选用何种油墨,须视各厂相关制程种类来评估,如碱性蚀刻和酸性蚀刻选择之抗蚀油墨考虑方向就不一样.
d、烘烤
不同制程会选择不同油墨,烘烤条件也完全不一样,须根据厂商提供的datasheet,再依厂内制程条件的差异而加以修改.一般因油墨组成不一烘烤方式有风干,UV,IR等烤箱须注意换气循环温控时控等.
3、干膜法:
4、蚀刻:
用于蚀刻的化学药液种类常见者有两种:
一是酸性氯化铜(CuCl2)蚀刻液,一种是碱性氨水蚀刻液,主要配方见下图:
酸性蚀刻液中CU2+浓度控制:
a.CuCl2酸性蚀刻反应过程之分析
铜可以三种氧化状态存在原子形成Cu°
蓝色离子的Cu++以及较不常见的亚铜离子Cu+金属铜可在铜溶液中被氧化而溶解见下面反应式1
Cu°
+Cu++2Cu+-------------
(1)
在酸性蚀刻的再生系统就是将Cu+氧化成Cu++,因此使蚀刻液能将更多的金属铜咬蚀掉
以下是更详细的反应机构的说明
b.反应机理及过程
直觉的联想在氯化铜酸性蚀刻液中Cu++及Cu+应是以CuCl2及CuCl存在才对但事实非完全正确两者事实上是以和HCl形成的一庞大错化物存在的
+H2CuCl4+2HCl2H2CuCl3-------------
(2)
金属铜铜离子亚铜离子
其中H2CuCl4实际是CuCl2+2HCl
2H2CuCl3实际是CuCl+2HCl
在反应式
(2)中可知HCl是消耗品即使
(2)式已有些复杂但它仍是以下两个反应式的简式而已
+H2CuCl42H2CuCl3+CuCl(不溶)----------(3)
CuCl+2HCl2H2CuCl3(可溶)----------(4)
式中因产生CuCl沈淀会阻止蚀刻反应继续发生但因HCl的存在溶解CuCl维持了蚀刻的进行由此可看出HCl是氯化铜蚀刻中的消耗品而且是蚀刻速度控制的重要化学品。
1)
蚀刻机理:
Cu+CuCl2→Cu2Cl2
Cu2Cl2+4Cl-→2(CuCl3)2-
2)
影响蚀刻速率的因素:
影响蚀刻速率的主要因素是溶液中Cl-、Cu+、Cu2+的含量及蚀刻液的温度等。
a、Cl-含量的影响:
溶液中氯离子浓度与蚀刻速率有着密切的关系,当盐酸浓度升高时,蚀刻时间减少。
在含有6N的HCl溶液中蚀刻时间至少是在水溶液里的1/3,并且能够提高溶铜量。
但是,盐酸浓度不可超过6N,高于6N盐酸的挥发量大且对设备腐蚀,并且随着酸浓度的增加,氯化铜的溶解度迅速降低。
添加Cl-可以提高蚀刻速率的原因是:
在氯化铜溶液中发生铜的蚀刻反应时,生成的Cu2Cl2不易溶于水,则在铜的表面形成一层氯化亚铜膜,这种膜能够阻止反应的进一步进行。
过量的Cl-能与Cu2Cl2络合形成可溶性的络离子(CuCl3)2-,从铜表面上溶解下来,从而提高了蚀刻速率。
b、Cu+含量的影响:
根据蚀刻反应机理,随着铜的蚀刻就会形成一价铜离子。
较微量的Cu+就会显著的降低蚀刻速率。
所以在蚀刻操作中要保持Cu+的含量在一个低的范围内。
c、Cu2+含量的影响:
溶液中的Cu2+含量对蚀刻速率有一定的影响。
一般情况下,溶液中Cu2+浓度低于2mol/L时,蚀刻速率较低;
在2mol/L时速率较高。
随着蚀刻反应的不断进行,蚀刻液中铜的含量会逐渐增加。
当铜含量增加到一定浓度时,蚀刻速率就会下降。
为了保持蚀刻液具有恒定的蚀刻速率,必须把溶液中的含铜量控制在一定的范围内。
d、温度对蚀刻速率的影响:
随着温度的升高,蚀刻速率加快,但是温度也不宜过高,一般控制在45~55℃范围内。
温度太高会引起HCl过多地挥发,造成溶液组分比例失调。
另外,如果蚀刻液温度过高,某些抗蚀层会被损坏。
5、剥膜:
剥膜在pcb制程中有两个工序会使用:
一是内层线路蚀刻后之D/F剥除,二是外层线路蚀刻前(剥除(若外层制作为负片制程))。
化学药液多为NaOH或KOH浓度在1~3%重量比。
内层之剥膜后有加酸洗中和也有防铜面氧化而做氧化处理者。
6、AOX检测:
内层板线路成完后,必须保证通路及绝缘的完整性(integrity),即如同单面板一样先要仔细检查因一旦完成压合后,不幸仍有缺陷时,则已为时太晚,对于高层次板子而言更是必须先逐一保证其各层品质之良好,始能进行压合,由于高层板渐多,内层板的负担加重,且线路愈来愈细,万一有漏失将会造成压合后的昂贵损失.传统目视外,自动光学检查(AOI)之使用在大厂中已非常普遍,利用计算机将原图案牢记,再配合特殊波长光线的扫瞄,而快速完美对各层板详作检查但AOI有其极限,例如细断路及漏电(Leakage)很难找出,故各厂渐增加短断路电性测试。
7、压合:
(1)表面氧化处理:
A.增加与树脂接触的表面积,加强二者之间的附着力(Adhesion).
B.增加铜面对流动树脂之润湿性,使树脂能流入各死角而在硬化后有更强的抓地力
C.在裸铜表面产生一层致密的钝化层(Passivation)以阻绝高温下液态树脂中胺类(Amine)对铜面的影响
主要有黑化与棕化工艺:
黑化:
黑化工艺:
它是一种氧化处理在碱性介质中的一种化学反应,使得树脂与铜面的接触面积增大,结合力加强。
在化学反应中通常使用强氧化剂亚氯酸钠(NaclO2)、高锰酸钾(K2MnO4)等,以NaclO2化学反应为例:
4Cu+NaCLO2
------
2Cu2O+NaCL
2Cu2O+NaCLO2
4CuO+NaCL
黑氧化处理的产物主要是氧化铜(CuO),
黑化层因液中存有高碱度而杂有Cu2O,此物容易形成长针状或羽毛状结晶。
此种亚铜在高温下容易折断而大大影响铜与树脂间的附着力,并随流胶而使黑点流散在板中形成电性问题,而且也容易出现水份而形成高热后局部的分层爆板。
黑化因结晶较长,厚度较厚,一般铜面的瑕疵较容易盖过去而能得到色泽均匀的外表。
但光面的黑化层却容易受酸液之侧攻而现出铜之原色,有些人认为黑化的产物是氧化铜和氧化亚铜,这是业内的一些错误论调,经过分析,可以测定铜原子和氧原子之间的结合能,氧化物表面铜原子和氧原子之间的比例;
黑化同时也带来了一种缺陷,黑化层较厚,经PTH后常会发生粉红圈,
这是因
PTH中的微蚀或活化或速化液攻入黑化层而将之还原露出原铜色之故。
对于粉红圈的处理又分为还原法和溶解法,其解决方法是提高黑化膜的抗酸能力,但是整个生产成本明显增高。
棕化:
棕化过程是铜在一种酸性的介质中的一种化学反应,棕化处理的产物主要是氧化亚铜(CU20),棕化层则呈碎石状瘤状结晶贴铜面,其结构紧密无疏孔,与胶片间附着力远超过黑化层,不受高温高压的影响,成为聚亚醯胺,另外氧化亚铜膜具有致密、完整、均匀提供一致性的粗糙度,为下一步有机金属转化膜提供了良好的物理结构。
棕化液的组成[3~6]:
①
硅烷类化合物,特别是易水解成膜的硅烷偶联剂,使用一种或多种,有些不易溶于水,需要使用醇类有机溶剂,辅助溶解,最佳使用浓度质量百分比1%-5%(未水解时的浓度)。
加入棕化液前,令硅烷部分或完全水解。
水解处理就是把硅烷与酸性水混合搅拌,或者与含醇类化合物的水混合。
②
唑、吡咯等化合物。
咪唑、苯并咪唑、三唑、苯并三唑等衍生物。
如1,2,3-三唑,1,2,4-三唑,3-甲基-1,2,4-三唑,羟基苯并三唑等。
使用浓度:
重量百分比0.1%-10%。
最佳1%-3%。
③
氧载体。
如过氧化氢。
有助于唑类化合物吸附于铜表面,若缺少,则唑类化合物无法吸附于铜面上。
原因:
很薄的一层铜被氧氧化后,铜表面很可能首先形成了铜-唑类化合物。
用量:
重量百分比0.1%-5%,最好1%-2%。
太少则处理时间过长,太多则微蚀过度。
过氧化氢在这里的作用不是微蚀形成粗糙铜,而是去除一薄层铜,有利于有机铜层的沉积,该层能有效地提高结合力。
④
有机或无机酸。
如硫酸、磷酸、硝酸,醋酸、甲基磺酸、乙醇酸、柠檬酸等。
其中硫酸最好,成本低,不会增加废液处理难度。
硫酸作用:
一方面有利于硅烷水解,另一方面有利用去除一薄层铜。
重量百分比1%-40%,最好5%-15%。
⑤
锌化合物。
可溶性的有机或无机锌盐。
如硝酸锌、硫酸锌、磷酸锌、醋酸锌、甲烷磺酸锌。
重量百分比0.01%-20%。
最佳0.2%-2%。
作用:
在铜面吸附的第一层唑类化合物与后续吸附的唑类化合物之间,锌化合物参与形成配位络合物,这样可以形成足够厚的沉积层,该沉积层表现为暗棕色,适合应用于线路板制造。
如果不使用锌化合物,则沉积层厚度很薄、颜色很淡,并且沉积层非常不均匀。
⑥
过氧化氢稳定剂:
苯磺酸、乙二胺四乙酸、巯基乙酸、硅酸钠。
重量百分比浓度0.001%-1%,依稳定剂种类不同,选择相应浓度。
棕化工序:
碱清洗→DI水洗→预浸液→棕化液→DI水洗→烘干。
碱洗目的是除去铜表面的有机残渣和轻微的氧化层。
预浸目的是保证铜表面的化学活泼性,使棕化变得快速和均匀,其中棕化是整个生产线的关键。
工艺条件:
使用PVC或聚四氟乙烯槽,采用摇摆或轻微搅拌。
②
浸渍或水平喷淋。
③
处理温度为
30℃~38℃。
温度低则耗时长,温度高则铜易微蚀过度,且过氧化氢会分解。
④
处理时间为30秒~75秒
(水平喷淋)。
各组分的作用
①
硫酸:
帮助双氧水微蚀铜,水解含OH的有机聚合物,使其中的R基团变为H,以增强有机聚合物与铜的结合力。
双氧水作用是蚀刻一层很薄的铜,促使有机金属层沉积在金属铜面上。
过硫酸铵(钠)等也可以使用,但文献认为双氧水更好[7]。
含OH的有机A:
其与相同分子之间反应的同时与半固化环氧树脂聚合;
同时与含N
的杂环化合物B、金属铜(含OH)形成化学键。
含N的杂环化合物B:
与基体铜结合外,通过A的桥键与环氧树脂结合,含N的杂环化合物分子间通过铜离子以配位键的形式连接起来,增加了棕化层的厚度和平整性。
⑤
氯离子:
对板子的颜色、微蚀厚度、抗撕强度有很大影响。
需要监测其浓度。
3,5-二硝基水杨酸等含硝基的有机化合物[7],可以与金属表面反应,特别是铜和铜合金,以提供均匀的金属转化层,该层有利于和聚合物材料成键。
棕化液再生:
棕化处理是一个化学蚀铜反应过程,随着棕化生产的进行,棕化液中的铜离子浓度不断上升,当铜离子超过一定限量后,棕化液便会因铜离子过多而产生棕化铜面发白、棕化铜面色泽不均等品质问题,因此,此时棕化槽液必须进行处理,使铜离子控制在一定范围内,从而保证棕化产品的品质。
通常棕化过程中铜离子浓度达到一定限量后,需要不断排放棕化液,同时补充添加液以降低铜离子浓度,且保持棕化槽各有效组分含量的稳定。
为了提高棕化液的利用率,可以收集排放的棕化液A,经过除铜和调整处理后作为棕化添加液B使用,即将棕化液A经过浓缩,成为铜离子含量较高的浓缩液,然后经过冷却结晶析出硫酸铜晶体,使溶液铜离子含量降低,最后通过对棕化液有效成分分析调整,得到添加液B,再添加到棕化生产过程中,达到棕化液循环使用的目的。
主要工艺流程:
A.碱性清洗-也有使用酸洗.市售有多种专业的化药,能清除手指纹油脂,scum或有机物
B.酸浸-调整板面PH,若之前为酸洗,则可跳过此步骤.
C.微蚀-微蚀主要目的是蚀出铜箔之柱状结晶组织(grainstructure)来增加表面积,增加氧化后对胶片的抓地力通常此一微蚀深度以50-70微英吋为宜微蚀对棕化层的颜色均匀上非常重要,
D.预浸中和-板子经彻底水洗后,在进入高温强碱之氧化处理前宜先做板面调整,使新鲜的铜面生成-暗红色的预处理,并能检查到是否仍有残膜未除尽的亮点存在
E.氧化处理-市售的商品多分为两液,其一为氧化剂常含以亚氯酸钠为主,另一为氢氧化钠及添加物,使用时按比例调配加水加温即可通常氢氧化钠在高温及搅动下容易与空气中的二氧化碳形成碳酸钠而显现出消耗很多的情况,因碱度的降低常使棕化的颜色变浅或不均匀,宜分析及补充其不足温度的均匀性也是影响颜色原因之一,加热器不能用石英,因高温强碱会使硅化物溶解操作时最好让槽液能合理的流动及交换
F.还原此步骤的应用影响后面压合成败甚巨.
G.抗氧化此步骤能让板子的信赖度更好,但视产品层次,不一定都有此步骤.
H.后清洗及干燥-要将完成处理的板子立即浸入热水清洗,以防止残留药液在空气中干涸在板面上而不易洗掉,经热水彻底洗净后,才真正完工
(2)、叠板
胶片相态变化:
胶片中的树脂为半硬化的B-Stage材料,在受到高温后即会软化及流动,经过一段软化而流动的时间后,又逐渐吸收能量而发生聚合反应使得黏度增大再真正的硬化成为C-Stage材料。
压合机种类:
a、舱压式压合机:
压合机构造为密闭舱体,外舱加压、内袋抽真空受热,压合成型。
各层板材所承受之热力与压力来自四面八方加压加温之惰性气体
优点:
因压力热力来自于四面八方故其成品板厚均匀流胶小可使用于高楼层
缺点:
设备构造复杂成本高且产量小
b、液压式压合机:
液压式压合机构造有真空式与常压式。
其各层开口之板材夹于上下两热压盘间,压力由下往上压,热力藉由上下热压盘加热传至板材。
a.设备构造简单成本低且产量大b.可加装真空设备有利排气及流胶
板边流胶量较大板厚较不均匀
C.ADARASYSTEMCedal
压合机Cedal为一革命性压合机,其作动原理为在一密闭真空舱体中利用连续卷状铜箔迭板。
在两端通电流,因其电阻使铜箔产生高温,加热。
Prepreg用热传系数低之材质做压盘,藉由上方加压达到压合效果。
因其利用夹层中之铜箔加热,所以受热均匀,内外层温差小,受压均匀。
比传统式压合机省能源故其操作成本低廉。
a.利用上下夹层之铜板箔通电加热省能源操作成本低
b.内外层温差小受热均匀产品品质佳
c.可加装真空设备有利排气及流胶
d.Cycletime短约4Omin.
e.作业空间减小很多.
f.可使用于高楼层
设备构造复杂成本高且单机产量小迭板耗时
压合机热源:
a、电加热式:
于压合机各开口中之压盘内安置电加热器直接加热
设备构造简单成本低保养简易
a.电力消耗大;
b.加热器易产生局部高温使温度分布不均
b、加热软水使其产生高温高压之蒸汽直接通入热压盘:
因水蒸汽之热传系数大热媒为水较便宜
a.蒸气锅炉必需专人操作设备构造复杂且易锈蚀,保养麻烦;
b.高温高压操作危险性高
C.藉由耐热性油类当热媒以强制对流方式输送将热量以间接方式传至热压盘
升温速率及温度分布皆不错操作危险性较蒸汽式操作低
设备构造复杂价格不便宜保养也不易
D.通电流式:
利用连续卷状铜箔迭板在两端通电流因其电阻使铜箔产生高温加热Prepreg用热传系数低之材质做压盘减少热流失
a.升温速率快(35/min.)内外层温差小及温度分布均匀;
b.省能源操作成本低廉
a.构造复杂设备成本高
叠板结构:
若压合机有十二个开口,每一开口有上下热压盘,共十三个热压盘。
迭板方式以钢质载盘为底盘,放入十二张牛皮纸及一张铜箔。
基板中间以一层镜面钢板一层板材的方式迭入十二层板材,上面再加一层镜面钢板及一张铜箔基板和十二张牛皮纸再盖上钢质盖板.
A-1迭板结构各夹层之目的
a.钢质载盘,盖板(Pressplate):
早期为节省成本多用铝板,近年来因板子精密度的提升已渐改成硬化之钢板,供均匀传热用.
b.镜面钢板(Separatorplate):
因钢材钢性高,可防止表层铜箔皱折凹陷,拆板容易。
钢板使用后如因刮伤表面或流胶残留无法去除,就应加以研磨。
c.牛皮纸:
因纸质柔软透气的特性可达到缓冲受压均匀施压的效果,且可防止滑动。
因热传系数低可延迟热传均匀传热之目的,在高温下操作牛皮纸逐渐失去透气的特性,使用三次后就应更换。
d.铜箔基板:
其位于夹层中牛皮纸与镜面钢板之间,可防止牛皮纸碳化后污染镜面钢板或黏在上面,缓冲受压均匀施压
e.其它有脱模纸(Releasesheet)及压垫(Presspad)Conformalpress的运用,大半都用在软板coverlayer压合上.
压板过程中压力变化:
a.初压(吻压Kisspressure):
每册(Book)紧密接合传热,驱赶挥发物及残余气体
b.第二段压:
使胶液顺利填充并驱赶胶内气泡,同时防止一次压力过高导致的皱折及应力
c.第三段压:
产生聚合反应使材料硬化而达到C-stage
d.第四段压:
降温段仍保持适当的压力,减少因冷却伴随而来之内应力
压板后处理:
a、后烤:
通常后烤条件是150,4小时以上.如果先前压合步骤curing很完整,可不做后烤,否则反而有害(降低Tg).
目的:
a.让聚合更完全.b.若外表有弯翘,则可平整之.c.消除内部应力并可改善对位.
B.铣靶,打靶-完成压合后板上的三个箭靶会明显的出现浮雕(Relief),
手动作业:
将之置于普通的单轴钻床下用既定深度的平头铣刀铣出箭靶及去掉原贴的耐热胶带,再置于有投影灯的单轴钻床或由下向上冲的冲床上冲出靶心的定位孔,再用此定位孔定在钻床上即行钻孔作业注意要定时校正及重磨各使用工具,
b.X-Ray透视打靶:
有单轴及双轴,双轴可自动补偿取均值,减少公差.
C.剪边(CNC裁板):
-完成压合的板子其边缘都会有溢胶,必须用剪床裁掉。
以便在后续制程中作业方便及避免造成人员的伤害,剪边最好沿着边缘直线内1公分处切下,切太多会造成电镀夹点的困扰,最好再用磨边机将四个角落磨圆及边缘毛头磨掉,以减少板子互相间的刮伤及对槽液的污染。
或者现在很普遍直接以CNC成型机做裁边的作业。
8、钻孔
钻孔房环境设计
A.温湿度控制:
一般钻房的温度应控制在18-22℃、相对湿度≦50€‚当温湿度不符合要求,会影响钻机的性能表现。
B.干净的环境:
钻房环境力求清洁。
钻机清理时不可使用高压风枪吹尘,此举一方面会影响操作员健康,另一方面会影响钻机的寿命及精度。
C.地板承受之重量
D.绝缘接地的考量
E.外界振动干扰
钻孔过程使用的物料:
钻针(a.硬度高耐磨性强的碳化钨(94%b.耐冲击及硬度不错的钴(4%)、c.有机黏合剂)、盖板、垫板。
9、镀通孔:
其目的使孔壁上之非导体部份之树脂及玻纤束进行金属化(metalization),以进行后来之电镀铜制程,完成足够导电及焊接之金属孔壁。
主要包括以下几个步骤:
(1)去巴里:
钻完孔后,若是钻孔条件不适当,孔边缘有1.未切断铜丝2.未切断玻纤的残留,称为burr.因其要断不断,而且粗糙,若不将之去除,可能造成通孔不良及孔小,因此钻孔后会有de-burr制