唐山港陆焦化方案Word文档格式.docx
《唐山港陆焦化方案Word文档格式.docx》由会员分享,可在线阅读,更多相关《唐山港陆焦化方案Word文档格式.docx(22页珍藏版)》请在冰豆网上搜索。
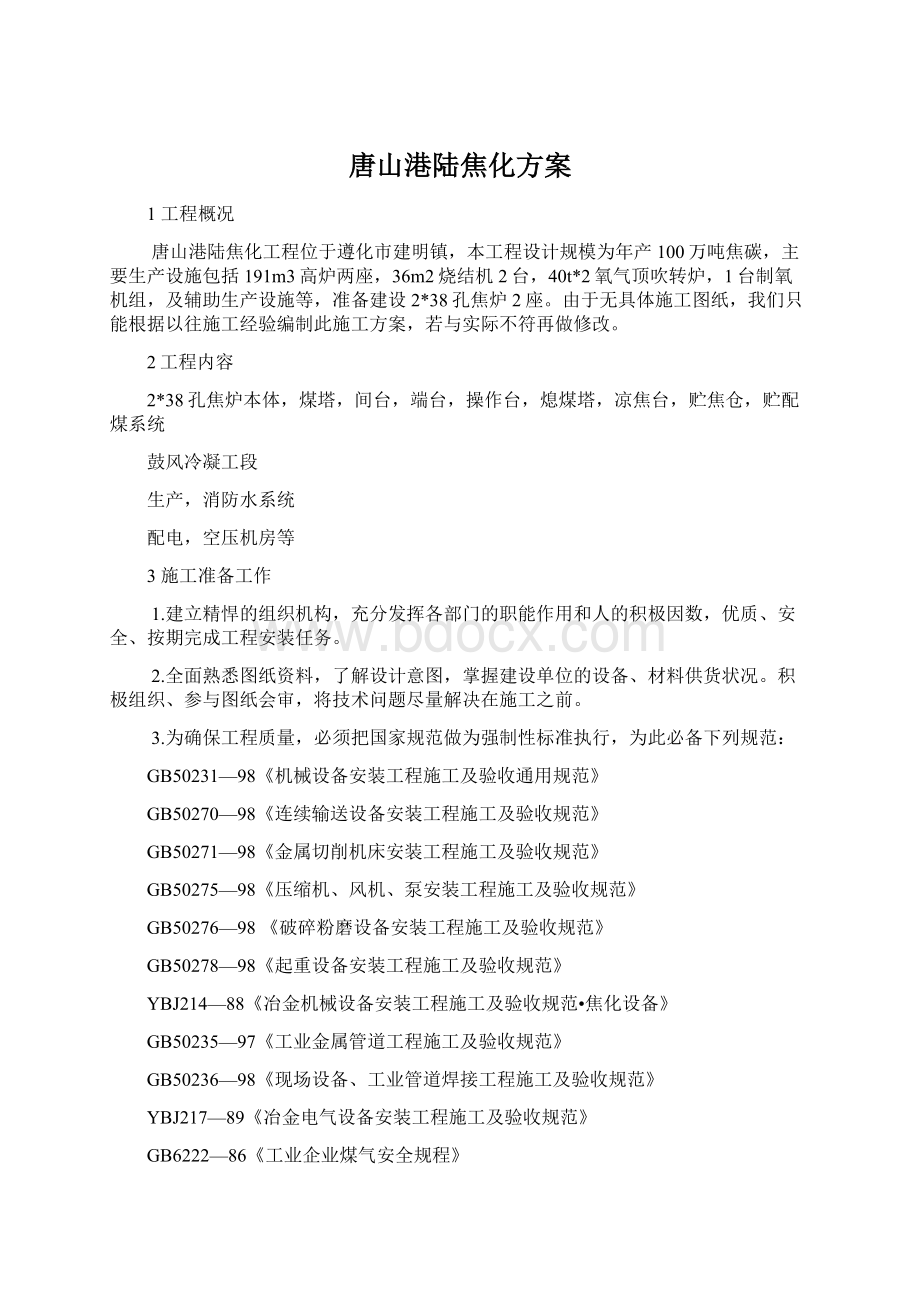
准线:
炉端炭化室中心线;
机、焦两侧正面线;
推焦机轨道中心线;
拦焦机轨道中心线;
熄焦车轨道中心线;
废气交换开闭器中心线;
消烟除尘车轨道中心线。
表二、设备基础的尺寸极限偏差及水平度、铅垂度公差
项次
项目
极限偏差(mm)
公差
1
基础坐标位置(纵、横向轴线)
±
20
2
基础各不同平面的标高
-20
3
基础上平面外形尺寸
凸台上平面外形尺寸
凹穴尺寸
0∽-20
+20∽0
4
基础上平面的水平度:
每米
全长
5
铅垂度:
每米
全高
6
预埋地脚螺栓:
标高(顶端)
中心距(在根部和顶部两处测量)
7
预留地脚螺栓孔:
中心距
深度
孔壁的铅垂度
10
8
预埋活动地脚螺栓锚板:
标高
水平度(带槽的锚板)
水平度(带螺纹孔的锚板)
0∽+20
表三、砌筑焦炉的允许误差
误差名称
误差数值
(mm)
线尺寸误差:
(1)主轴线、正面线和边炭化室或边燃烧室中心线的测量、
(2)小烟道的宽度及小烟道承插口的宽度和高度
(3)相邻炭化室墙的中心线的间距
(4)炭化室的炉头肩部脱离正面线
(5)保护板砖座到炭化室底的距离
(6)沿炭化室长度方向的上升管中心线的间距
±
0∽-3
标高误差:
(1)主要部位标高控制点的测量
(2)炭化室底
(3)相邻炭化室保护板砖座的标高误差
(4)相邻炭化室底的标高差
表面平整误差:
(1)蓄热室炉头正面
(2)炭化室墙炉头肩部
垂直误差:
炭化室墙炉头肩部
4.1.3保护板安装
焦炉砌体复检合格后,首先安装保护板。
保护板是护炉铁件的主要部件,是直接将保护性压力均匀地传递给砌体的铁件。
保护板与炉肩之间垫以石棉绳(SY-28φ32),石棉绳即传递压力又起密封作用。
安装保护板前,在保护板内侧焊接铁丝钩(8#铁线即可),增强内侧耐火灰浆的强度。
石棉绳的粘接位置要正确,斜接头位置不准在两相邻保护板对接处。
采用Π型卡具和临时拉条对保护板加压,不得用其他方法。
保护板与砌体的压紧程度从保护板与炉肩之间隙判断,以3—12mm为宜,图中尺寸a力求相等;
保护板中心线应与燃烧室中心线重合,极限偏差3mm;
两相邻保护板之间隙大于5mm,磨板面高差不大于2mm。
4.1.4炉柱、纵横拉条安装
1.炉柱安装前,应检查其长度及各连接孔的位置的正确性;
检查其柱身挠曲矢高,不应超过5mm。
炉柱安装前,应将蓄热室小保护板点焊在炉柱上,炉柱加压时将此点焊割掉。
炉柱立起之后,调整其中心,使炉柱、保护板、燃烧室三者中心相吻合,极限偏差不超过3mm。
炉柱底板面与垫板之间涂以润滑脂,地脚螺栓不宜过度拧紧,当炉体受热膨胀时,炉柱可向外滑移。
炉柱中心和标高调整好之后,可安装上下横拉条,固定炉柱。
2.纵横拉条安装
纵横拉条安装前,应根据弹簧制造厂交付的压缩记录,按负荷编组。
弹簧编组方法是在同类弹簧中使用压力范围的累计压缩量在±
1mm的分类组合,配套编成弹簧组,编组后妥善管理。
焦炉的炉顶和炉底均设有拉条,其作用是拉紧炉柱。
上部横拉条每对炉柱由两根组成,置于炉顶拉条沟内;
下部横拉条每根炉柱只用一根。
其一端固定在基础顶板的边梁上,另一端通过弹簧压紧炉柱。
纵拉条共六根,设置在炉顶横拉条之上。
纵横拉条安装时,中间垫以木块,减少下挠度。
纵拉条两端固定于抵抗墙上,固定端无横向膨胀,当炉体横向膨胀结束后,纵拉条则落入沟槽内。
故在冷态下安装后,要检查其位置是否符合膨胀值的要求。
弹簧在冷态下加压值,严格执行设计规定。
弹簧加压后,炉柱弯曲度不应超过15mm,并做出记录。
4.1.5炉门框安装
炉柱加压后进行炉门框安装。
炉门框安装在相邻两块保护板中间,并压在保护板上。
炉门框与保护板接触部位垫以石棉绳(SY—28φ25)。
因此要求两块保护板接口处应保持在同一平面,上下错位不应超过1毫米;
炉门框与保护板内侧面的错位应左右相等,炉门框边缘不应凸出保护板之边缘。
调整炉门框中心线与炭化室中心线相重合,极限偏差为2mm,垂直度公差值为4mm。
炉门框与保护板间的各层石棉绳应将接头错开,采用斜接,全周长要压紧塞实。
进行加压紧固过程中应防止炉门框变形。
加压后的间隙不得大于3mm。
磨板面应保持水平,水平度公差值2mm/m,且磨板面低于炭化室7—10mm。
4.1.6炉门安装
炉门框、炉门安装前应进行合套检查,检查炉门刀刃的平直度,与炉门框结合的严密性,合格后编号。
4.1.7加热煤气管道安装
1.管道安装
分配主管标高、中心线的极限偏差均为±
5mm;
支管中心线与中心距的极限偏差均为±
3mm。
在分配主管上开孔接出支管时,开孔直径大于支管外径不超过5mm,支管插入主管深度不大于3mm。
支管法兰的水平度公差为1/500;
各支管法兰应在同一水平面,高度差不大于5mm。
下喷横管应作校直处理,组装后应保证管的中心同轴性。
每根下喷横管的两端各有两个孔必须留待炉温达650°
C后开孔与下喷管连接。
中间部分的22根下喷管允许按冷态尺寸安装。
热态下连接的下喷管204根,只许在3—4天内完成。
下喷横管标高安装时保证其轴线水平,不得倾斜。
2.旋塞安装
煤气旋塞安装前,在全开状态下检查孔的侧边错台不超过1mm,
底边错台不超过3mm。
检查合格后清洗干净,薄涂一层50号机油进
行单体严密性试验。
旋塞单体严密性试验两种位置:
一为全开状态,一为全闭状态,转动阀芯,有两次全关闭,均作试验。
试验时应用2×
104Pa
(2040mmH2O)的压缩空气进行严密性试验,经30分钟后压降不超
过5×
102Pa(51mmH2O)为合格。
旋塞应做好全开全闭的印记,注意方向,分清左、右旋。
安装后进行总体试压。
试压时进行交替开闭和阀芯转动三种状态的检查,试验压力同旋塞单体严密性试验的标准。
泄露率为4%。
4.1.8交换装置安装
1.交换传动系统安装
液压传动装置安装执行YBJ202—85《冶金机械设备安装工程施工及验收规范——液压、风动和润滑系统》之规定。
但强度试验压力为系统工作压力。
油缸与前后链输的中心线极限偏差为±
行程余量宜两端对称。
各废气拉条的支撑滑轮应位于同一中心线上,极限偏差为3mm;
滑轮标高一致,极限偏差±
5mm。
拉条的行程,极限偏差±
10mm。
拉条上滑块在搬把中滑动应灵活。
2.空气废气交换开闭器安装
空气废气交换开闭器安装前进行煤气铊及废气铊的严密性试验。
试验标准是:
煤气铊以4500Pa的空气压力进行试验,5分钟压力降不大于1500Pa;
废气铊以1750Pa的空气压力进行试验,5分钟压力降不大于750Pa;
空气盖在全关闭状态下,接触面以0.05mm塞尺检查塞不进为合格。
废气开闭器纵向中心线极限偏差+3mm,横向中心线与小烟道中心对正;
水平度公差为1/1000。
4.1.9集气系统设备安装
集气系统设备包括上升管、桥管及阀体、集气管和吸气弯管等。
安装时执行下列标准:
1.集气管中心线应平行于焦炉纵向中心线,平行度公差值为±
3mm;
标高(设计为▽+10.310)极限偏差为±
2.集气管与全部桥管连接法兰应在同一垂直平面内,偏离及标高的极限偏差均为±
各个法兰中心线均与相应上升管中心对正,极限偏差为±
水封阀安装后,阀体呈水平状态。
3.焦油盒、放散水封阀应逐个进行外观检查与渗透试验,合格后安装。
4.上升管安装前应进行隔热夹层试漏试验,灌满水30分钟不渗水为合格或作煤油渗透试验。
上升管安装前在铸铁座套口上盖以5mm石棉板,其垂直度公差为1/500;
坐标位置的极限偏差为±
炉温升至650°
C后,用石棉绳(SY—32φ19)塞紧四周并抹好灰浆。
桥管与水封阀承插口处的四周间隙应均匀。
当炉温升至650°
C之后进行密封。
5.吸气弯管与吸气管待炉温升至750°
C之后,方可进行连接。
4.1.10烟道翻板安装
1.安装时保持其垂直,转动灵活。
2.翻板与两侧墙面间隙大于40mm;
与底部转面间隙大于60mm。
3.翻板的实际开度与顶部刻度盘应一致,应进行全开试验,密封盖板应严密。
4.2工艺管道安装
4.2.1消防水系统管道安装
管道安装一般有直埋敷设、管沟敷设及架空敷设等方式,其安装时应注意:
1.管子、管件、阀及其他材料等,在施工前应按设计要求核对其型号、规格、材质,并具有出厂合格证明书。
2.铸铁管件除应有制造厂名和商标、制造日期及工作压力等标识外,其内外表面应整洁、无裂纹、冷隔和凹陷,承插口应光洁完整。
3.低压阀门应从每批(同制造厂、同规格、同型号)中抽查10%(最少1个),进行强度和严密性试验。
4.铸铁管在安装前应清除承插口处的沥青及其他杂质,对口最小轴向间隙应根据介质温度和施工时的气温而定。
5.在昼夜温差较大或负温下施工时,应采取防护措施。
6.管道支、吊架安装,要求位置正确、平整牢固,与管道接触良好。
7.从抵抗墙引至焦炉的工业水管须待烘炉至650°
C时与外管进行连接。
4.2.2热力管道安装
热力管道的敷设形式为架空敷设,介质为蒸汽。
安装时应注意下列事项:
1.热力管道设有一定坡度,蒸汽管道的坡度坡向疏水器,室内蒸汽管坡度与介质流向一致。
2.蒸汽热力管道的方型补偿器垂直安装时,在补偿器的最低点安装疏水器或放水阀;
若水平安装方型补偿器,其横臂应符合设计坡度,竖臂水平安装即可。
3.水平管道变径时,宜采用偏心异径管,取管底平,以利排水。
4.蒸汽支管从主管接出的方式,是支管从主管的上方或两侧接出,以免凝结水流入支管。
5.疏水器安装应根据设计进行,一般装有旁通管的疏水装置应装设活接头或法兰。
6.热力管网上的蒸汽压力较高时,往往设减压装置。
组装时减压阀的阀体应垂直安装在水平管道上,进出口正确,前后装截止阀,并应设旁通管。
减压前的高压管与减压后的低压管上应装压力表。
低压管上应设安全阀,其排汽管引出室外。
7.不同压力的疏水管不能接入同一管道。
8.两个补偿器之间应设置固定支架,两个固定支架之间应设置导向支架。
9.方型补偿器两侧的第一个支架,在距弯头起弯点0.5—1米处,宜设滑动支架,不得设导向支架,以保证补偿器伸缩时管微量的横向滑动。
10.其他部位的导向支架、滑动支架的安装亦严格按设计要求施工。
11.从抵抗墙至焦炉的蒸汽管道须待烘炉至650°
4.2.3压缩空气管道安装
压缩空气管道采用架空敷设,安装时应注意下列问题:
1.水平干管必须设有2/1000以上的坡度,以便排除管道内的凝结水和废油。
2.为防止干管内水分和废油流入立管,立管必须从干管上部接出。
立管从干管接出后弯成U形管向下接至用户。
3.从抵抗墙至炉顶的压缩空气管道须待烘炉至650°
4.2.4煤气管道安装
1.根据两个支架之间的管道长度,将几根管子在地面上组装成整体。
组装时应考虑到管道就位后环形焊缝距管托边缘不小于300mm,纵向焊缝距管托边缘不小于200mm;
组装时相邻两根管子的纵缝错开100mm以上;
加固圈位置与管道的环缝错开50mm以上;
加固圈的接口与管道纵缝错开100mm以上。
组装管道的连接均应采用对接;
个别情况下可以采用搭接板连接。
2.首先安装管托。
安装管托要特别注重其水平位和标高。
水平位置以支架的中心线为依据而确定;
其标高根据支架上的水准点标记计算。
3.管托固定后,组装好的管段即可吊装就位,一端置于支架上,另一端则置于上节管段的搭接板上,然后找正、对口、焊接。
4.鼓形补偿器或波形补偿器安装时应注意方向。
补偿器安装时要按设计要求即冷紧值,调整其安装长度,即按当时的气温把补偿器预拉伸或预压缩。
若设计无说明,可用下面公式计算:
受温度影响管道引起的热胀冷缩值即补偿量△L:
△L=α(t1-t2)L
再根据补偿量△L计算冷紧值△Lt:
△Lt=△L[(t1+t2)/2-t]/(t1-t2)
以上两公式中:
α——管道线膨胀系数,t<
75°
C时,α=0.0012cm/m·
°
C;
t1——管壁计算最高温度,°
C,冷煤气管道考虑太阳的照射或蒸气吹刷,取t1=60°
t2——当地采暖室外计算温度,°
L——管道计算长度,m;
t——冷紧时大气温度,°
C,可用实际温度。
5.流量孔板安装时要注意方向且同心。
6.安装结束后进行清洗或吹刷。
吹刷时分段进行,先干管后支管。
吹刷前应拆除阀门、孔板等,以短管代之。
7.安装结束后进行压力试验。
4.2.5管道试压标准
此标准仅供参考,若与图纸相抵触,则以图纸为准。
1.蒸汽管道:
试压标准为水压1Mpa,10分钟不漏为合格。
2.工业水管道:
试压标准为水压0.6Mpa,30分钟不漏为合格。
3.压缩空气管道:
试压标准为水压0.8Mpa,30分钟不漏为合格。
4.煤气管道:
煤气管道的计算压力等于或大于105pa(1.02kgf/cm2)应进行强度试验,合格后再进行严密性试验;
计算压力小于105pa(1.02kgf/cm2),可只进行严密性试验。
焦炉煤气抽气管的煤气计算压力等于煤气抽气机所产生的最大负压力的绝对值;
净煤气管道计算压力等于煤气自动放散装置的最大设定压力。
若净煤气管道系统没有自动放散装置,计算压力等于抽气机最大工作压力。
进行严密性试验压力为:
加压机前的室外管道为计算压力加5×
103pa(510mmH2O),但不小于2×
104pa(2040mmH2O);
加压机前的室内管道为计算压力加1.5×
104pa(1530mmH2O),但不小于3×
104pa(3060mmH2O);
位于抽气机、加压机后的室外管道应等于加压机或抽气机最大升压加2×
104pa(2040mmH2O)。
煤气管道严密性试验允许泄漏率为:
管道计算压力<105pa(1.02kgf/cm2),试验时间2小时,每小时平均泄漏率1%;
管道计算压力≥105pa(1.02kgf/cm2),试验时间24小时,每小时泄漏率0.5%。
4.2.6工艺管道涂漆,工艺管道涂漆要求见下表。
工艺管道涂漆要求
序号
被涂对
象名称
防腐层
标准用量g/m2
面层
备注
油漆名称
道数
油漆名称及颜色
工业水管
灰酚醛防锈底漆
二
120
绿色调合面漆
100
事故水管
蒸汽管
银白色有机硅耐热漆
红色调合面漆
保温层外
压缩空气管
深兰色调合面漆
氨水管
黄色调合面漆
荒煤气管
沥青漆
90
焦炉区内
回炉煤气管
集气管、炉柱、水封槽、除尘车上下水槽
9
上升管水封下水、除尘车上下水管
绿色调合面漆加黑色环
色环表志法和介质流向箭头的确定如下:
管子(或保温的)外径D(mm)
<150
150-300
>300
色环宽度B(mm)
50
70
色环间距L(m)
1-6
200-400
D
BLB
1/2φ1/4φ
1/4φφ
φ——为管道的内径
箭头涂色视底色而定,当底色为深色时,箭头为白色,当底色为浅色时,箭头为红色。
4.3通用设备安装
通用设备包括带式输送机、斗式提升机、刮板输送机、破碎机、卷扬机、泵及风机等一般设备。
安装上述设备应执行GB50231—98《机械设备安装工程施工及验收通用规范》、GB50270—98《连续输送设备安装工程施工及验收规范》、GB50275—98《压缩机、风机、泵安装工程施工及验收规范》、GB50276—98《破碎粉磨设备安装工程施工及验收规范》等规定之标准。
4.3.1输送设备安装
输送设备包括备煤系统的带式输送机、炼焦系统的斗式提升机、刮板放焦机和筛焦系统的带式输送机。
1.带式输送机安装
吊装方法:
带式输送机的吊装,通过厂房的电动葫芦或手拉葫芦,可将设备吊装至安装位置。
其起重量和提升高度一般均能满足安装要求。
其他设备吊装亦可利用此装置。
安装技术要求:
输送机纵向中心线与基础轴线允许偏差+20mm。
机架(头架、尾架、中间架及其支腿)安装。
其中心线与输送机纵向中心线应重合,其偏差不大于3mm;
机架中心线的直线度偏差在任意25m长度内不应大于5mm;
机架横截面两对角线长度之差,不应大于两对角线长度平均值的3/1000;
机架支腿垂直度偏差不应大于
2/1000;
中间架的间距,其允许偏差为+1.5mm,高低差不应大于间距的2/1000;
机架接头处的左右偏移偏差和高低差均不应大于1mm。
传动滚筒、改向滚筒和拉紧滚筒安装要求:
滚筒横向中心线与输送机纵向中心线应重合,其偏差不应大于2mm;
滚筒轴线与输送机纵向中心线的垂直度偏差不应大于2/1000;
滚筒轴线的水平度偏差不应大于1/1000。
组装托辊应符合下列要求:
托辊横向中心线与输送机纵向中心线应重合,其偏差不应大于3mm;
对于非用于调心或过渡的托辊,其上表面母线应位于同一表面上或同一半径的弧面上,且相邻三组托辊辊子上表面母线的相对标高差不应大于2mm。
输送带的连接采用硫化法胶接。
连接后应平直,其直线度允许偏差为25mm(测量长度为7m)。
2.斗式提升机安装
斗式提升机安装应符合下列技术要求:
主轴水平度偏差不应大于0.30/1000;
上下轴安装参照GB50270—98第11、12页;
机壳铅垂度允许偏差7mm;
料斗中心线与牵引带中心线应重合,其偏差不应大于5mm。
3.刮板放焦机安装
刮板放焦机安装应符合下列要求:
横梁安装:
横梁横向中心线与刮板放焦机的纵向中心线应重合,其偏差不应大于2mm;
其标高允许偏差为+20∽-10mm;
其水平度不应大于2/1000。
托辊组装:
托辊横向中心线与刮板放焦机纵向中心线应重合,其偏差不应大于2mm;
两托辊轴线应平行,且与刮板放焦机纵向中心线的垂直度偏差不应大于1/1000;
托辊水平度偏差不应大于0.5/1000;
相邻托辊水平度偏差不应大于0.5/1000。
拉条组装:
拉条
(二)与拉条
(一)的连接销和耳板保证0.5mm间隙;
拉条与托辊保证接触;
刮板对放焦口的中心线左右行程相等。
驱动装置安装:
其标高应与拉条标高一致,允许偏差不应大于
1mm;
圆盘轴对刮板放焦机纵向中心线垂直度偏差不应大于1/1000;
两驱动装置对刮板放焦机纵向中心线对称布置,其位置偏移不应大于1mm;
滑动体滚轮轮缘与滑道保持3mm的间隙,滚轮与滑道要接触。
4.3.2泵、破碎机安装
1.泵安装:
平面位置安装基准线对基础实际轴线的允许偏差为±
20mm;
标高允许偏差为+20∽-10mm;
中心线允许偏差为±
找平找正应在轴的外伸部分或底座的水平加工面等为基准进行测量。
2.破碎机安装:
因破碎机与其他设备有衔接关系,在安装定位时,其定位基准面、线或点与安装基准线的平面位置和标高的允许偏差应符合下列规定:
纵、横向平面位置的允许偏差为±
3mm;
标高允许偏差为±
5mm;
水平度偏差为0.10/1000。
整体出厂的破碎机在安装时,只进行找正、调平和试运转,即可办理工程验收。
4.4电气设备安装
本方案分设备安装、电缆敷设和防雷接地系统三部分。
4.4.1设备安装
1.基础槽钢安装
根据图纸要求,验收予埋件、电缆沟尺寸。
检查材