东方希望6机组化学清洗方案全解Word文档格式.docx
《东方希望6机组化学清洗方案全解Word文档格式.docx》由会员分享,可在线阅读,更多相关《东方希望6机组化学清洗方案全解Word文档格式.docx(53页珍藏版)》请在冰豆网上搜索。
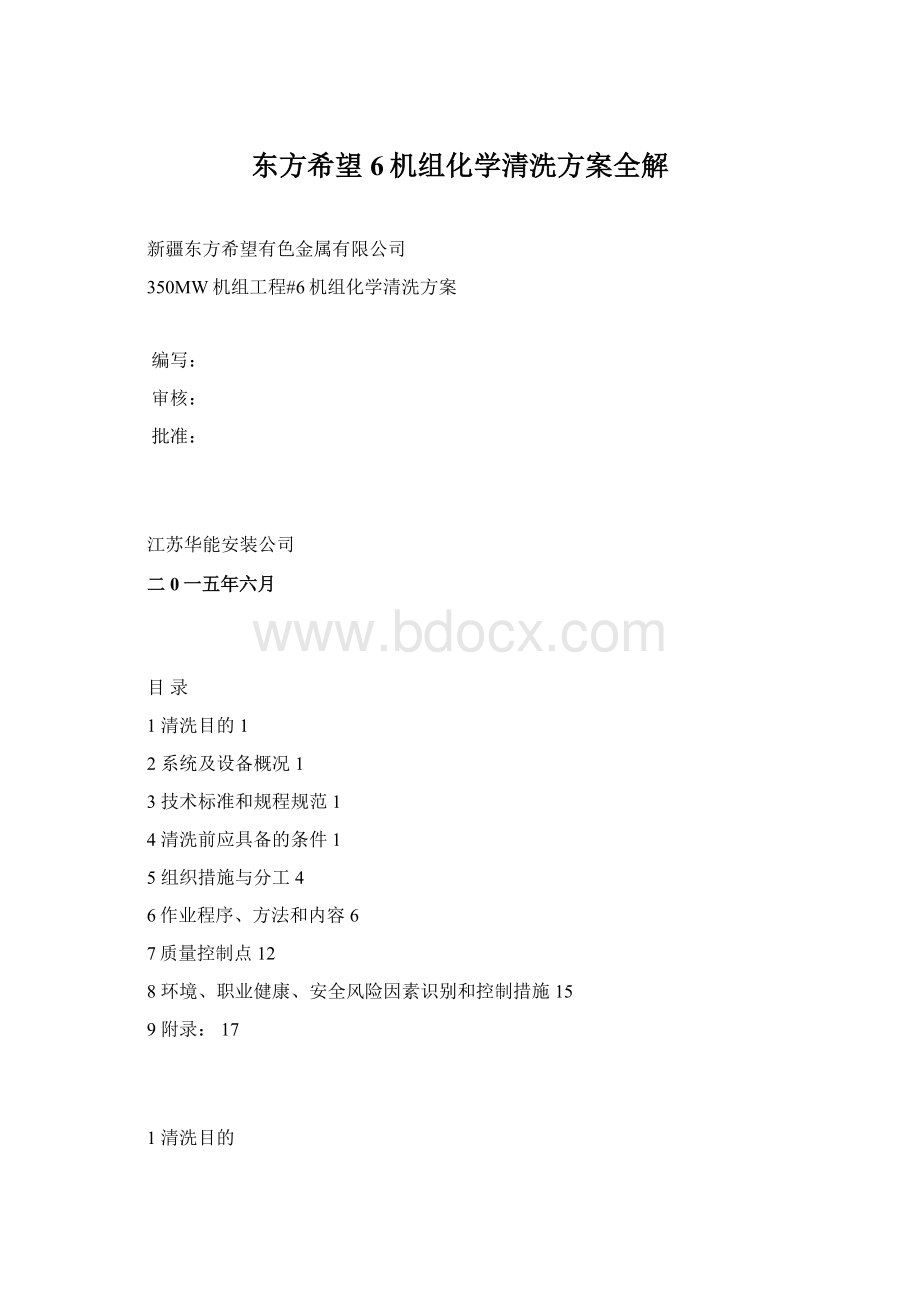
整体工程所需除盐水约2500m3,为此除盐水箱在清洗前应贮满除盐水,将化学制水系统设备投备用。
清洗泵的电源、轴封水在清洗期间可靠且连续不间断,锅炉进酸后不允许电源中断。
炉本体化学清洗用水量表
清洗过程
临时系统水压及水冲洗
碱煮及水冲洗
酸洗及
水冲洗
漂洗及
钝化
合计
除盐水t
600~800
600~700
300~400
2100~2600
4.6取样、压力、温度测点装好,仪表校验合格。
4.7清洗临时值班室和化验间的通讯与照明装配好,并能满足酸洗工作的要求,化验台、仪器、仪表、药品及记录报表齐全,有关电源座安装好。
4.8操作人员、化验人员经过演习和培训,操作无误、化验准确、熟悉系统,各负其责,为了保证参与清洗的重大关键设备的安全,可靠运行,有关专业根据本次化学清洗的方案要求应制定相应的操作措施和反事故措施。
4.9化学清洗的药品经检验确证无误,并按方案要求备足品种和数量(药品清单如下)。
化学清洗药品清单
品名
分子式
纯度
数量
检验标准
工业盐酸
HCL
30%
33t
GB320-1993
工业烧碱(液态)
NaOH
35t
GB209-1993
工业磷酸三钠
Na3PO4.12H2O
95%
2t
GB/T2517-1993
中性除油剂
复合
500kg
---
联氨
80%
0.2t
工业磷酸氢二钠
Na2HPO4.12H2O
1.5t
-HG/T2965-2000--
工业氨水
NH3.H2O
20%
12t
GB3060-82
柠檬酸
H3C6H5O7.H2O
食品级
1t
GB/T8269-1998
缓蚀剂
Lan-826
1.5t
HG/T2387-92
三价铁抑制剂A
300kg
---
消泡剂
200kg
酸洗促进剂
1t
钝化剂
二甲基酮肟
300kg
化学清洗设备材料清单
各称
规格
备注
清洗平台
Q:
500m3/h×
2H>125mH2O
1套
浓酸泵
Q>25m3/h;
H>15mH2O
两台
耐腐蚀
闸阀
DN200,PN16~25
20个
配法兰20对
截止阀
12个
配法兰12对
耐酸胶管
2寸或2.5寸
100m
浓酸系统用
透明塑料管
1寸
30m
临时水位计用
耐酸胶垫
4mm~6mm厚
360kg
无缝钢管
φ219×
8
200m
φ108×
4
φ57×
3.5
50m
弯头
φ200,90度
现场定
φ159,90度
30个
φ159,60度
5个
φ133,90度
φ133,60度
15个
φ108,90度
φ57,90度
其它三通大小头
各种规格
若干
耐酸盘根
10kg
电焊条
碳钢
200kg
塑料布
20kg
电缆
容量300KW
泵电源控制保护柜
两台,总功300KW
一个
枕木、压块
两台泵用
4.10清洗系统中的阀门已挂牌编号,安全措施的准备工作就序,检修的器材和工具已准备就序。
4.11凡是不参加化学清洗的设备和系统应与化学清洗系统完全隔离,如阀门隔离不严密,则必须采用加堵板隔离,以防止清洗液的侵蚀。
隔离阀门应挂禁止操作牌,清洗期间一直全开或全关的电动阀门在操作到位后应退电,防止清洗时有人误动。
清洗期间禁止机组清洗系统与清洗相关系统范围内任何阀门调试工作与系统试运工作。
4.12过热器出口加装堵板阀,过热器若不参加清洗应采取保护措施(充联氨保护液)。
4.13锅炉上的仪表管道、加药管道、排污管道、取样管道、疏水管道等凡与清洗系统相连接的管道,清洗前其一次门均应全关,确保隔离到位。
4.14防汽缸进清洗液,各抽汽电动门前疏水门应全开,加热器水侧、汽侧水压试验合格。
4.15凝结水、给水系统中连接的各减温水、冷却水等不参加清洗的系统清理、冲洗干净。
4.16现场检修人员应备齐抢修器材和工具,酸洗或钝化阶段,现场必须备齐专用的急救药品。
4.17安全水源(靠近清洗操作台的自来水)24小时不得断水,化学清洗的安全防护用品配备齐全,并已运至施工现场。
4.18清洗前安全技术交底工作已完成,安全技术措施已落实。
5组织措施与分工
原则性分工:
化学清洗期间,原则上是正式系统的操作由安装单位与业主负责;
临时系统的操作由清洗公司负责。
由清洗公司负责化学清洗工艺与技术的实施,安装单位负责总体协调,其他各参加单位作好协作工作。
5.1安装单位:
5.1.1负责组织工作。
负责提供正常的施工条件与现场协调,负责酸洗工作的统一指挥,协调酸洗各单位的配合,保证整个化学清洗工作的顺利进行。
5.1.2负责永久设备上各临时系统接口的制做、安装及接点断口的恢复。
并且负责正式设备的操作,正式管道、设备的拆除及恢复工作。
5.1.3负责汽包及压力容器内的工作。
5.1.4负责化学清洗过程中脚手架的搭设,临时系统的保温工作。
5.1.5提供可靠水源、电源、汽源、氧气、乙炔。
5.1.6负责组织化学清洗中,及清洗后的化学监督和清洗质量评定。
5.1.7负责化学清洗过程中大件设备的起吊工作。
5.1.8负责化学清洗过程中正式设备的隔离工作。
5.1.9负责酸洗现场的保卫、消防、临时照明及救护工作。
5.2清洗公司:
5.2.1提供化学清洗临时系统所需的清洗箱、清洗泵、管道、阀门等设备和材料。
5.2.2负责化学清洗临时系统的安装、操作、检修。
5.2.3负责自己参加化学清洗施工人员的培训,审核工作;
化学清洗前对所有参加化学清洗的工作人员进行技术交底。
5.2.4负责化学清洗工艺的实施,化学清洗各阶段的质量控制。
5.2.5化学清洗措施的编写与实施,在水、电、汽确保正常供应的条件下,对清洗质量负责。
5.2.6参加化学清洗后的效果评价及检查工作。
5.2.7负责化学清洗工作结束后总结报告的编写。
5.2.8清洗工作结束后,尽快拆除临时管道及设备,并尽快运回自带全部设备、材料。
将现场清理干净。
5.3业主
5.3.1参加化学清洗方案的审查;
负责提供足量、合格的除盐水。
5.3.2负责已调试好的正式系统的操作。
5.3.3负责化学监督工作。
5.3.4参加化学清洗后的效果评价及检查工作。
5.4监理
5.4.1参加化学清洗方案的审查;
5.4.2负责化学清洗过程中的质量、安全监督;
5.3.3组织化学清洗后的效果评价及检查工作。
5.5调试单位
5.5.1配合化学清洗过程中正式系统的相关协调、指导、监督工作;
5.5.2已调试好的正式系统的操作指导、监督;
5.5.3参加化学清洗后的检查、评定工作。
5.6施工进度表
工日
施工分项
12
3
1
临时设施安装
化学清洗
验收
拆除临时系统
清理现场
6作业程序、方法和内容
6.1炉本体化学清洗范围
其范围包括炉侧部分给水管道、省煤器、汽包下半部、水冷壁、下联箱、下降管及连接管道。
6.2清洗工艺:
6.2.1炉本体化学清洗工艺:
本次锅炉本体清洗选定的清洗工艺为:
水冲洗→碱洗→碱洗后的水冲洗→盐酸酸洗→酸洗后水冲洗→柠檬酸漂洗→二甲基酮肟钝化→排放。
6.2.2炉本体化学清洗回路(水容积约270m³
):
本次炉本体清洗分为三个循环回路:
回路一:
清洗箱→清洗泵→省煤器→汽包→水冷壁→下联箱→清洗箱。
回路二:
清洗箱→清洗泵→临时进液母管→右前、左前水冷壁(下降管)→汽包→右后、左后水冷壁(下降管)→临时回液母管→清洗箱
回路三:
清洗箱→清洗泵→临时进液母管→右后、左后水冷壁下联箱(下降管)→汽包→右前、左前水冷壁下联箱(下降管)→临时回液母管→清洗箱
清洗循环流速及清洗泵选择:
根据《火力发电厂锅炉化学清洗导则》(DL/T794-2012)的规定,清洗液在水冷壁流速应在0.2m/s~0.5m/s左右,在省煤器流速应在0.1m/s~0.2m/s左右,清洗泵流量应在300t/h~500t/h,泵扬程应大于锅炉汽包静液位及系统流动沿程阻力之和,约为80mH2O。
根据上述考虑,清洗选用的临时进液和回液母管内径应大于150mm,选用2台流量为500t/h的清洗泵。
6.2.3炉本体化学清洗步骤及方法:
1)系统水冲洗及过热器冲保护液
先用除盐水冲洗锅炉水系统,冲洗干净后,用氨水调节,配置PH9.5~10的联氨保护液,抬高汽包液位,向过热器进保护液,过热器排空门见水后,依次关排空门。
2)碱洗
剂量:
0.2%Na2HPO4.+0.3%Na3PO4.+0.3%除油剂
温度:
70-80℃
碱洗时间:
8-12h
将系统表面的油污除去,为盐酸清洗创造良好条件。
3)碱洗后的水冲洗
可将碱洗液排尽后,用除盐水冲洗,至排水PH≤9。
4)盐酸酸洗
3-4%盐酸+0.3%缓蚀剂+适量三价铁抑制剂A
时间:
4-6h
进除盐水至清洗箱水位2/3,启泵,进行循环。
投入监视管,保持汽包水位约-150mm,清洗箱水位1/4。
投入混合加热器加热,加入0.3%缓蚀剂,充分混合均匀,各回路分别循环30分钟。
开喷射器的进出口门,进酸至出口HCL浓度为3-4%。
控制汽包液位在-50-0mm之间。
如果Fe3+≥300mg/L,就加入适量的三价铁抑制剂A。
当酸洗时间约4-6小时,或二价铁离子浓度基本稳定,拆下监视管,确定酸洗结束时间,取出腐蚀指示片称重,计算腐蚀速率。
酸洗结束时,维持汽包水位,关闭全部阀门后,排空清洗箱。
5)酸洗后水冲洗
首先用工业水冲洗,再用除盐水冲洗,直至出口PH≥4,总铁<50ppm。
6)柠檬酸漂洗
0.2-0.4%柠檬酸+0.1%缓蚀剂+氨水
PH:
氨水调节PH3.5~4.0
50~60℃
2-3h左右
如果总铁≤300mg/L就可转入钝化,否则就用除盐水置换掉部分漂洗液。
每台清洗水泵依次开30min。
7)二甲基酮肟钝化
800~1000ppm钝化剂PH≥10.5
80~90℃
大于12h
漂洗时汽包液位比酸洗时略高,钝化时汽包液位比漂洗时略高。
钝化结束后,将钝化液快速排空。
6.2.4以上过程所产生的废水排放至废水池,中和至PH6-9之间。
6.3清洗临时系统及安装要求
6.3.1进酸、回酸母管及排酸管用无缝钢管,进口可布置在给水操作平台的给水逆止门后,出口用钢管连接下联箱的酸洗接口,排酸管应有千分之一的坡度,以便把残液排尽。
6.3.2清洗箱1个,清洗箱内设有混合加热器,内部应清理干净。
清洗箱不能布置在电缆沟附近或靠近重要设备。
清洗箱必须有足够的机械强度,内设有混合加热器,两台清洗泵并列布置,设置再循环回路,箱底部要安装排污管。
泵入口处加装滤网,滤网孔径小于5mm。
6.3.3供汽管可从辅汽联箱接出,入清洗箱内的混合加热器,并用外包保温材料和设2-3个疏水点。
6.3.4利用喷射器向清洗箱进酸(或氨水),喷射器并联接在再循环管上,用一耐酸软管与酸槽车连接。
6.3.5清洗泵的机械密封应能耐腐蚀,阀门在安装前必须研磨,填料必须耐酸,阀门本身不得带有铜部件。
系统中各进、出酸阀门安装尽量集中,以便操作。
6.3.6安装用的临时管道内不得有砂石和其它杂物,焊口不宜对着重要设备。
焊工应持有焊工证。
6.3.7临时系统中安装的温度计、压力表等都要校验合格后,才能使用。
6.3.8监视管系统:
挂设腐蚀指示片2片在汽包内部,挂设1片在侧水冷壁下部或酸洗进、出水母管上(临时管前后应装设手动门)。
6.3.9保证汽包处和酸洗现场的通讯畅通。
6.3.10汽包水位计暂不装入,水位计阀门后管口接一透明Φ32塑料管作临时液位计,标出水位刻度线(“0”水位位于汽包中心线下50mm)。
6.3.11汽包的排气门清洗期间要全开作为排氢管,总截面积不应小于DN80,如果过小,则考虑拆除一个安全阀作为临时排氢管。
6.3.12汽包内下降管安装节流孔板,并可靠固定。
6.3.13事故放水接高至汽包高水位以上作为溢流管。
6.3.14除盐水水源用φ159钢管从除盐水母管或除氧器溢放水管上接至清洗箱。
6.3.15在锅炉主进水管合适位置开口,接一根φ219×
4的临时管道作为临时系统进水口。
6.3.16进酸和回酸母管上要安装温度计和取样管,排酸母管上安装取样管。
6.3.17酸洗废液排放系统、废水处理系统安装完毕,能投入使用。
(本次酸洗废液处理采用液态碱液与盐酸进行中和处理,废液经排水管道进入废水池,中和过程中启动罗茨风机搅拌均匀至PH6-9。
)
6.3.18清洗箱加热管可从附近热源引一根φ100×
4临时管至清洗箱,要求蒸汽参数:
压力0.6~0.8Mpa,温度160℃,最大流量20t/h,总用量500t~600t。
6.3.19汽包内部汽水分离装置在化学清洗时不能参加酸洗,在集中下降管口要加装节流孔板,并采用临时措施可靠固定,以避免清洗经过下降管造成短路。
6.3.20电源:
设清洗泵专用电源(280kW),电缆容量能满足一台泵连续运行而不致发热跳闸及中断。
6.3.21酸洗临时系统应在清洗前安装完毕,并进行整个系统的检查。
6.3.22临时管道系统做1.0MPa水压试验合格,无泄漏。
6.3.23所需的一切药品均已运至现场,抽样检验合格。
6.3.24分析仪器、化验药品、记录表格和安全劳保用品等备齐,酸洗前搬到现场,现场应有工作棚及临时化验分析的地方。
6.3.25酸洗操作、检修、化验、加药、医务人员落实,并对操作措施和酸洗安全注意事项进行学习掌握。
6.3.26临时系统所有阀门编号挂牌,检查所有阀门开关灵活可靠,接触酸液的阀门用塑料薄膜包扎好。
6.3.27检查与酸洗系统相连的所有阀门是否隔离关严。
6.3.28清洗现场道路畅通,照明充足,并设有自来水龙头和临时电源。
6.3.29锅炉各人孔门、看火门、风门、风道、烟道等全部关闭。
6.3.30腐蚀指示片选用国家标准腐蚀指示片。
用无水乙醇洗去表面油污,然后编号,精确量尺寸,称重备用。
6.3.31酸洗应在锅炉具备点火吹管条件的二十天内进行。
7质量控制点
7.1化学清洗过程中的取样化验要求:
化验项目
分析周期(分)
控制范围
炉本体碱洗
Na3PO4
60
0.3-0.5%
同时测
进出口样
Na2HPO4
0.1-0.2%
盐酸酸洗
30
3-4%
Fe3+
≤300mg/L
Fe2+
/
温度
35±
5℃
酸洗后水冲洗
PH
≥4.0
测排水样
全铁
≤50mg/L
漂洗
0.2-0.3%
3.5-4.0
55±
≥10.5
80-90℃
7.2化学清洗测定方法
7.2.1碱洗和水冲洗液测定
测定项目:
磷酸三钠、磷酸氢二钠、pH值。
测定方法:
pH值pH计直接测定;
磷酸三钠、磷酸氢二钠测定:
试剂:
C(H2SO4)=0.05mol/L硫酸标准溶液,酚酞、甲基橙指示剂。
方法:
取10mL碱洗液于250mL锥型瓶中,用除盐水稀释至100mL,加2~3滴酚酞指示剂,用C(H2SO4)=0.05mol/L硫酸标准溶液滴定至红色消失,记录消耗量为amL,再加2滴甲基橙指示剂,继续滴定至橙色,记录第二次消耗量为bmL(不包括a);
Na3PO4%=2×
0.05×
164×
a×
100÷
(V×
1000)%
Na2HPO4%=2×
142×
(b-a)×
7.2.2酸洗液的测定
7.2.2.1盐酸浓度的测定
试剂:
c(NaOH)=0.1mol/L氢氧化钠标准溶液,甲基橙指示剂。
测定方法:
取酸洗液1mL用于250mL锥形瓶中,用除盐水稀至100mL,加入5滴甲基橙溴甲酚绿指示剂,用c(NaOH)=0.1mol/L氢氧化钠标准溶液滴至由红变绿,记录耗碱量amL;
HCl%=0.1×
36.5÷
ρ×
1000)×
100%=0.365×
a%
式中:
a-c(NaOH)=0.1mol/L标准溶液消耗体积,mL;
V-取样体积,mL;
ρ-酸洗液密度,g/mL,按1g/mL计算。
7.2.2.2酸洗液中铁的测定
c(EDTA)=0.1mol/LEDTA标准溶液,10%磺基水杨酸,(NH4)2S2O8晶体或10%(NH4)2S2O8溶液,25%AlCl3。
量取5mL~10mL(VmL)酸洗液于250mL锥形瓶中,用除盐水稀至100mL,加入2mL25%AlCl3溶液摇匀,加入1mL10%磺基水杨酸溶液,用c(EDTA)=0.1mol/LEDTA标准溶液滴至红紫色消失,记录耗量amL;
加入少量(NH4)2S2O8晶体或5mL10%(NH4)2S2O8溶液,加热至70℃,继续用c(EDTA)=0.1mol/LEDTA标准溶液滴至红紫色消失,记录耗量bmL;
CFe3==0.1×
56÷
100%=0.56×
a÷
V(%)
CFe2==0.1×
b×
b÷
式中:
a-第一次滴定所消耗c(EDTA)=0.1mol/LEDTA标准溶液的体积,mL;
b-第二次滴定所消耗c(EDTA)=0.1mol/LEDTA标准溶液的体积,mL;
7.2.2.3水冲洗液中全铁的测定
c(EDTA)=0.01mol/LEDTA标准溶液,10%磺基水杨酸,10%(NH4)2S2O8溶液。
量取50mL~100mL水冲洗液于250mL锥形瓶中,加入少量(NH4)2S2O8晶体或5mL10%(NH4)2S2O8溶液,加入1mL10%磺基水杨酸,用c(EDTA)=0.01mol/LEDTA标准溶液滴至红紫色消失,记录耗量amL;
∑Fe=560×
V(mg/L)
a-滴定所消耗c(EDTA)=0.01mol/LEDTA标准溶液的体积,mL;
7.2.3漂洗液及钝化液pH及全铁的测定
测定仪器:
pH计
pH值、全铁。
7.2.3.1pH值
用pH计、试纸直接测定。
7.2.3.2全铁测定
c(EDTA)=0.01mol/LEDTA标准溶液,1:
4HCl,10%磺基水杨酸,10%(NH4)2S2O8溶液。
量取25mL~50mL漂洗液于250mL锥形瓶中,加入100mL蒸馏水,加入1mL1:
4HCl,在电炉上加热沸3~5分钟,取出冷至70℃,加入5mL10%(NH4)2S2O8溶液,加入1mL10%磺基水杨酸,用c(EDTA)=0.01mol/LEDTA标准溶液滴至红紫色消失,记录耗量amL;
∑Fe=560×
7.3清洗质量目标
7.3.1清洗后的金属表面清洁,基本上无残留物和焊渣,无明显粗晶析出的过洗现象。
7.3.2腐蚀指示片测量的金属平均腐蚀速度<8g/(m2·
h);
腐蚀总量<80g/m2,除垢率>95%。
7.3.3清洗后的表面应形成良好的钝化保护膜,保护膜完整,无点蚀及二次生锈。
7.3.4固定设备、系统上的阀门、仪表等不应受到损伤。
7.3.5清洗废液的排放到废水池,中和至PH6-9之间,。
8环境、职业健康、安全风险因素识别和控制措施
8.1环境影响因素识别及控制措