数控铣床的主轴箱结构设计Word文档下载推荐.docx
《数控铣床的主轴箱结构设计Word文档下载推荐.docx》由会员分享,可在线阅读,更多相关《数控铣床的主轴箱结构设计Word文档下载推荐.docx(27页珍藏版)》请在冰豆网上搜索。
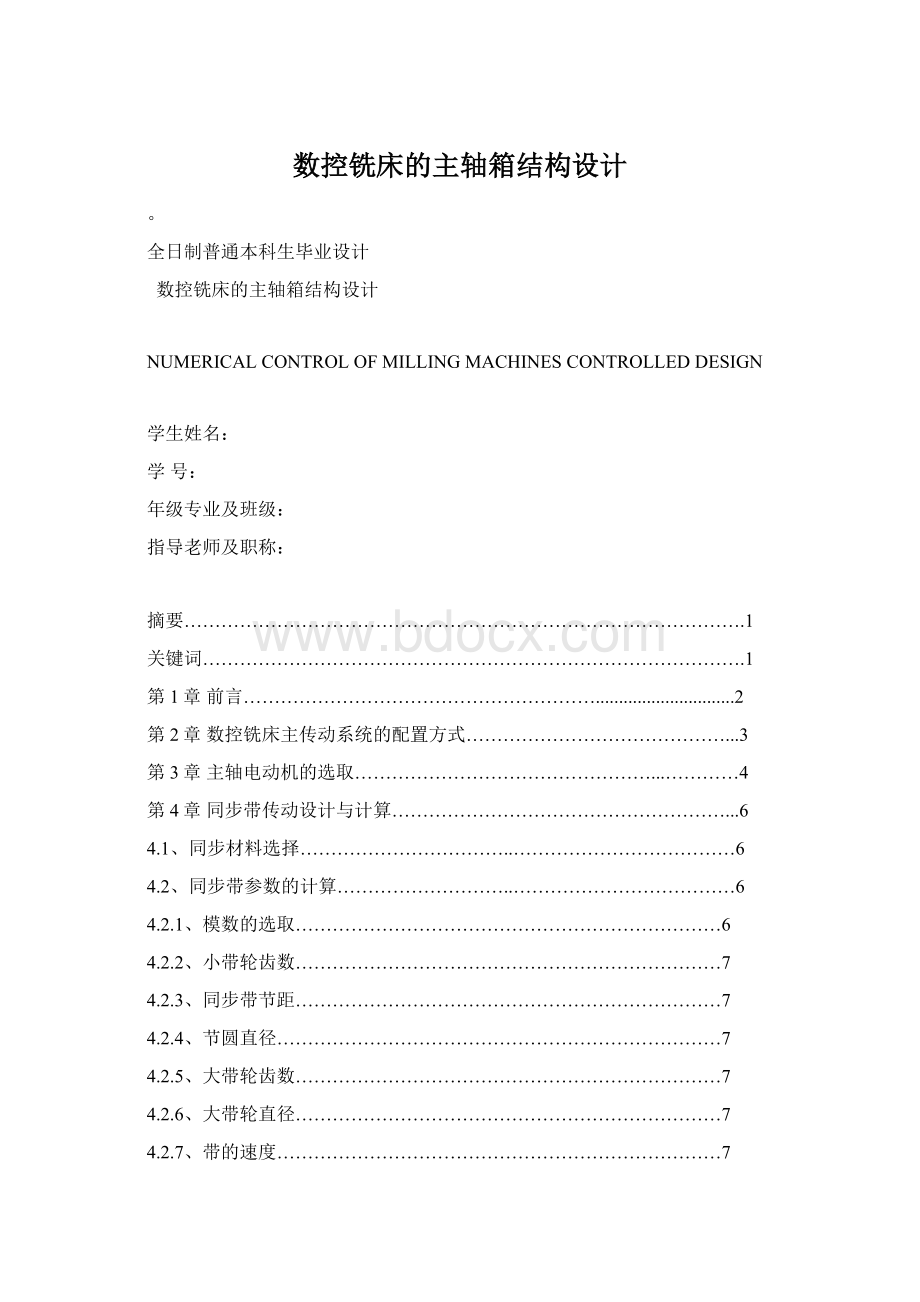
4.2.13、作用在轴上的力……………………………………………………..8
4.2.14、小带轮的最小包角…………………………………………………..8
4.2.15、带轮宽度……………………………………………………………..8
第5章主轴组件的设计…………………………………………………………..9
5.1、主轴组件的设计要求……………………………………………………...9
5.1.1、回转精度………………………………………………………………9
5.1.2、主轴刚度………………………………………………………………10
5.1.3、主轴的抗振性…………………………………………………………10
5.1.4、主轴温升………………………………………………………………10
5.1.5、主轴耐磨性……………………………………………………………10
5.1.6、提高主轴组件抗振性的措施…………………………………………11
5.2、减少主轴组件热变形的措施……………………………………………...11
5.3、主轴材料的选择及尺寸、参数的计算…………………………………...11
5.4、主轴转动装置箱体的作用………………………………………………...15
5.5、主轴箱体的截面形状和壁厚的计算……………………………………...15
第6章主轴轴承的选择…………………………………………………………….15
6.1、轴承的选择和轴承的精度…………………………………………………..16
6.2、轴承预紧力的要求…………………………………………………………..16
6.3、主轴轴承的润滑与密封……………………………………………………..16
6.4、选取轴承求…………………………………………………………………..16
6.5、轴承寿命校核………………………………………………………………..19
6.6、轴承座孔的设计要求………………………………………………………..20
第7章联接键的选择碟形弹簧的选择与计算……………………………………21
7.1、碟形弹簧的特点……………………………………………………………...21
7.2、碟形弹簧材料及热处理厚度和脱碳………………………………………...21
7.3、碟形弹簧的强压处理………………………………………………………...21
7.4、表面强化处理和防腐处理…………………………………………………...22
第8章螺钉联接的设计…………………………………………………………….23
8.1、根据设计要求计算…………………………………………………………...24
8.2、螺钉的强度计算与校核……………………………………………………...24
第9章液压缸的设计……………………………………………………………….24
9.1.液压压缸安装应注意的问题…………………………………………………25
9.2.压缸各部分的结构及主要尺寸的确定………………………………………25
9.3.强度校核………………………………………………………………………25
第10章润滑与密封件设计………………………………………………………..26
10.1、封件的作用及其意义………………………………………………………26
10.2、密封的分类及密封件的材料要求………………………………………..26
10.3、防尘圈的设计要求…………………………………………………………27
结论……………………………………………………………………………….....27
致谢……………………………………………………………………………….....................28
参考文献………………………………………………………………………….....................29
摘要:
数字控制是近代发展起来的一种自动化控制技术是用数字化信号对机床运动极其加工过程进行控制的一种方法,随着科学技术的迅猛发展,数控机床已经是一个国家机械工业水平的重要标准。
数控机床是装有程序控制系统的机床。
该系统能够逻辑地处理具有使用号码,或其他符号编码指令规定的程序。
数控机床是以数控技术为代表的新技术对传统制造产业的渗透形成的机电一体化产品,起技术范围覆盖很多领域:
(1)机械制造技术
(2)信息处理、加工、传输技术;
(3)自动控制技术;
(4)伺服驱动技术;
(5)传感技术;
(6)软件技术等。
计算机对传统机械业的渗透,完全改变了制造业。
制造业不但成为工业化的象征,而且由于信息技术的渗透,使制造业犹如朝阳产业,具有广阔的发展天地。
数控机床就是将加工过程所需的各种步骤以及刀具与工件之间的相对位移量都是用数字化的代码来表示。
通过控制介质数字信息送入专用区域通用的计算机。
计算机对输入的信息进行处理,发出各种指令来控制机床的伺服系统或其他执行元件,使机床自动加工出所需要的工件。
关键词:
机械设计,数控三坐标铣床,主轴,数控系统。
NumericalControlofMillingMachinesControlledDesign
Student:
heyi
Tutor:
chenzhiliang
(OrientalScience&TechnologyCollegeofHunanAgriculturalUniversity,Changsha410128)
Summary:
Digitalcontrolthemoderndevelopmentofautomationcontrolofdigitaltechnologyisasignalformachinetoolsareprocessestocontrolmovement,asamethodofscienceandtechnologyhasdevelopedrapidlyandNumericalControlmachineisanationalmachineryindustrystandardsofimportantstandard.themachineisaprogramNumericalControlcontrolsystemofmachinetools.thesystemtobelogicaltouseanumberorothersymbolsspecifiedprocedure.theinstructionencoding.
NumericalControlmachinetoolsinNumericalControltechnologyofnewtechnologyindustriesthroughthetraditionalmanufacturingaproductoftheelectromechanicalintegrationtechnology,coveringmanyareas:
(one)machinerymanufacturingtechnology(tow)informationprocessing,processingandtransmissiontechnology;
(three)automatictechnology;
(four)servodrivingtechnological;
(five)sensingtechnology;
(six)softwaretechnology,etc.thecomputertotraditionalservicetradethemanufacturingindustry,haschangedcompletely.andhasbecomeindustrialized,andbecauseoftheinformationtechnology,manufacturingintoarisingindustry,havebroaddevelopmentoftheworld.
NumericalControlmachinetoolsaretheprocessesofthevariousstepsandthetoolrelativetotheworkpiecebetweentheamountofdisplacementistheuseofdigitalcodetorepresentinformationmedia.bycontrollingfiguresintoaspecialareaofthecomputer.computerfortheprocessingofinformationandinstructionstocontrolthemachinetoolsorotherenforcementservosystemcomponentsandtoolsautomaticallyprocessedoutthework.
Keywords:
Mechanicaldesign,NumericalControlthreecoordinatesofmillingmachines,Spindle,NumericalControlsystem.
1前言
主传动系统设计概述
数控机床的主传动系统包括主轴电动机,传动系统和主轴组件。
与普通机床的主传动系统相比数控机床在结构上比较简单,这是因为变速功能全部或大部分由主轴电动机的无级调速来承担。
省去了繁杂的齿轮变速机构,还有一些数控机床设计中还存在二级或三级齿轮变速机构用以扩大主轴电动机无级变速的范围。
对主传动系统的要求:
范围:
各种不同的机床对调速范围的要求不同,多用途,通用性比较大的机床,要求主轴的调速范围大,不但有低速大转距的功能,而且还要有比较高的速度。
热变形:
电动机、主轴及传动件都有热源。
降低温升,减少热变形是对主传动系统要求的重要指标。
旋转精度和运动精度:
主轴的旋转精度:
是指装配后,在无载荷,低速转动条件下,测量主轴前端和300mm处的径向和轴向跳动值。
主轴在以工作速度旋转时,测量上述两项精度称为运动精度。
数控机床要求有较高的旋转精度和运动精度。
主轴的静刚度和抗振性;
由于数控机床的加工精度比较高,主轴的转速又很高。
因此,主轴组件的质量分布是否均匀以及主轴组件的阻尼等,对主轴组件的静刚度和抗振性都会产生影响。
主轴组件的耐磨性;
主轴组件必须有足够的耐磨性,使之能够长期保持要求的准确精度。
凡是有机械摩擦的部位,轴承,锥孔等都要有足够的硬度,轴承还应具有良好的润滑。
第2章数控铣床主传动系统的配置方式
数控铣床的主传动系统要求有较大的调速范围,以保证进行加工时能选用合理的切削用量,从而获得最佳的生产效率、加工精度和表面质量。
数控机床的变速是按照控制指令自动进行的,因此机构必须适应自动操作的要求。
大多数的数控铣床是用无级变速系统控制的。
数控机床主传动系统主要有以下三种配置方式:
带有变速齿轮的主传动
这种配置方式在大中型数控机床中采用比较普遍。
它通过少数几对齿轮进行降速,使之能够分段变速,确保低速时拥有足够的扭矩,以满足主轴输出扭矩特性。
但也有一部分小型数控机床也采用这种传动方式,以获得强力切削时所需要的扭矩。
通过带传动的主传动
主要应用在中小数控机床上,可以避免齿轮传动时引起的振动和噪声,但它只能适用于低扭矩特性要求的主轴。
同步带有多楔带,齿形带,圆弧带等,是一种综合了带传动和链传动优点的新型传动。
带的工作面及带轮外圆上均制成齿形,通过带轮与轮齿相嵌合,做无滑动的啮合传动。
带内采用了承载后无弹性伸长的材料作强力层,以保持带的节距不变,使主动和从动带轮可做无相对滑动的同步传动。
与一般带传动相比,同步带传动具有以下优点:
1.无滑动,传动比准确。
2.传动效率高,可达98%以上。
3.传动平稳可靠,噪声小。
4.使用范围广,速度要达到50m/s,速比可达10左右,传动功率由几瓦到数千瓦。
5.修保养方便,不需要润滑。
但是同步带也有不足之处,其安装时中心距要求严格,带与带轮制造工艺较复杂,成本高。
由调速电动机直接驱动的主传动:
这种主传动方式大大简化了主轴箱与主轴的结构,有效地提高了主轴部件的刚度。
但主轴输出扭矩小,电动机转动时发出的热量对主轴的精度影响比较大。
在低于额定转速时为恒转矩输出,高于额定转矩时为恒功率输出。
使用这种电动机可实现电气定向。
我们把机床主轴驱动与一般工业的驱动相比较,便可知机床要求其驱动系统有较高的速度精度和动态刚度,而且要求具有能连续输出的高转距能力和非常宽的恒功率运动范围。
随着功率电子,计算机技术,控制理论,新材料和电动机设计的进一步发展和完善,矢量控制交流主轴电动机驱动系统的性能已经达到甚至超过了直流电动机驱动系统,交流主轴驱动系统正在逐步取代直流系统。
第3章主轴电动机的选取
正确选择电动机的类型、型号及容量是机床设计的重要问题之一,它直接影响着机床的结构和寿命,选择时要根据机床的功能要求,所设计的结构,工作状况等全面考虑,然后选择适宜的结构型式及容量。
图3-1主轴电动机
电动机功率的选择:
工作机所需的有效功率为:
Pw=Fv/1000=17.5kw,为了计算电动机所需的功率,先要确定从电动机到工作部件的总效率η,设η1、η2、分别为同步带轮和同步带的传动效率,查表所得η1和η2都等于0.97。
则传动的总效率为η=η1×
η2=0.94,所以电动机所需的功率为Pd=Pw/η=18.5KW
电动机传速的选择:
此次设计要求电动机必须有额定转速1500r/min,最高转速必须达到4000r/min.
电动机型号的选取:
根据设计要求,本次设计中选取兰州电机厂生产的1PH5167-4CF4型号交流主轴电动机。
其主要参数如下表:
表3-1
额定转速(r/min)
最高转速(r/min)
额定转矩
惯性矩(N.M)
电机功率(KW)
恒功率范围
1500
6000
117.7
0.046
18.5
1:
90
第4章同步带传动设计与计算
同步带传动,综合了带、链和齿轮传动的优点,带的工作面呈齿形,与带轮的的齿槽作啮合传动,使主、从带轮间作无滑差的同步运动,其特点是传动比准确,对轴作用力小,结构紧凑,耐油耐磨损,抗老化性能好,传动效率可达99.5%,传动功率从几瓦到数百千瓦,传动比可达10,线速度可达40m/s以上。
此次设计选用梯形同步带,它靠齿啮合传动,速比准确,传动效率高,初张紧力最小,轴承承受压力最小,瞬时速度均匀,单位质量传递的功率最大,与链和齿轮传动相比,噪声小,不需要润滑,传动比、线速度范围大,传递功率大,而冲击振动较好,维修简单,经济。
广泛用于各种机械传动中。
4.1、材料选择:
根据设计要求,选用聚氨酯同步带,由带背、带齿、抗拉层三部分组成。
带背和带齿材料为聚氨酯,抗拉层采用钢丝绳,适用于中小功率的高速运转部分。
4.2、参数计算:
设计计算的内容主要是:
齿形带的模数、齿数、和宽度的结构和尺寸,传动中心距,作用在轴上载荷以及结构设计。
4.2.1、模数的选取:
模数主要根据齿形带所传递的计算功率Pd和小带轮转速n1确定的,通过查《现代数控机床》表4-33查得Pd=KA*P,式中P———传动功率
表4-1
载荷性质
一天运转时间/h
≤10
10~16
16以上
载荷平稳
1.0
1.1
1.2
载荷变化小
1.4
1.6
载荷变化大
1.7
2.0
选取KA=1.7,所以PC=5.5×
1.7=9.35KW
由齿形带模数选用图可选m=4
4.2.2、小带轮齿数Z1:
由《机械传动装置设计手册》表8-38得Zmin=22,所以取Z1=24
4.2.3、同步带节距Pb:
由PD=9.35KWn1=1500r/min,查表选取节距Pb=12.566mm,齿形角2β=40。
齿根厚S=5.75mm。
齿顶厚St=4mm,齿高hg=ht+e=2.4+2.7=5.1mm,齿根圆半径Rr=齿顶圆半径Ra=0.40mm,带高hs=4.4mm,节顶距δ=1.000mm,带bs=35~40mm.
4.2.4、节圆直径d1:
d1=
=96㎜
4.2.5、大带轮齿数z2与直径:
z2=iz1=36
4.2.6、大带轮直径d2=id1=1.5×
96=144㎜
4.2.7、带的速度V:
V=
=7.536,(式4-1)
由表查得
Vmax=35~40V<
Vmax所以合格。
4.2.8、定中心距a0:
5(d1+d2)≤a0≤2(d1+d2)
所以:
0.7(96+144)≤a0≤2(96+144)
则有168≤a0≤480初选a0=300
4.2.9、带的节线长度Lp以及齿数Zb:
Lp0=2a0+
(d1+d2)+
=2300+
×
240+
=978.72(式4-2)
查表选取Lp=1005㎜Zb=80
4.2.10、计算中心距a(采用中心距可调)
a≈a0+
=300+
㎜(式4-3)
选取a=314㎜
4.2.11、带轮与带的啮合齿数Zm:
Zm≈
=11.82取Zm=12(式4-4)
因为当m≥2时,Zm应不小于6,所以计算的Zm满足条件。
4.2.12、带宽bs:
bs≥
查表取Kz=1.20,Fa=20N/mm(式4-5)
Fc=mbV2=4.8×
10-3×
7.5362=0.273
所以bs≥
㎜选取bs=40㎜
4.2.13、作用与轴上的力Fr:
Fr=
(式4-6)
4.2.14、小带轮最小包角ɑ:
α≈180º
-60º
(d2-d1)/a=180。
-60。
(144-96)/314=170.8。
5.2.15、带轮宽度bf,bf1,bf2
bf=bs+(1.5~3)=41.5~43
bf1=bs+(6~7)=46~47
bf2=bs+(3~5)=43~45
第5章主轴组件的设计
主轴组件主要包括:
主轴、主轴支撑和安装在主轴上的传动件、密封件等,因为主轴带动工件或刀具直接参加工件表面形成运动,所以它的工作性能对加工质量和生产率产生直接影响,是机床最重要的部件之一。
5.1.主轴组件的设计要求:
主要体现在如下方面:
5.1.1回转精度:
主轴组件的回转精度,是指主轴的回转精度。
当主轴做回转运动时,线速度为零的点的连线称为主轴的得回转中心线。
回转中心线的空间位置,每一瞬间都是变化的,这些瞬间回转中心线的平均空单位转移不为理想回转中心线。
瞬时回转中心线相对于理想回转中心线在空间位置的距离,就是主轴的回转误差,而回转误差的范围,就是主轴的回转精度。
纯径转误差、角度误差和轴向误差,它们很少单独存在。
当径向误差和角度误差同时存在构成径向跳动,而轴向误差和角度误差同时存在构成端面跳动。
由于主轴的回转误差一般都是一个空间旋转矢量,它并不是在所有的情况下都表示为被加工工件所得的加工形状。
主轴回转精度的测量,一般分为三种静态测量、动态测量和间接测量。
目前我国在生产中沿着传统的静态测量法,用一个精密的检测棒插入主轴锥孔中千分表触头触及检测棒圆柱表面,以低速转动主轴进行测量。
千分表最大和最小的读数差既认为是主轴的径向回转误差。
端面误差一般以包括主轴所在平面内的直角坐标系的垂直度,数据综合表示。
动态测量是用一标准球装在主轴中心线上,与主轴中心线上,与主轴同时旋转;
在主轴同时旋转;
在工作台上安装两个互成90度角的非接触传感器,通过仪器记录回转情况。
间接测量是用小的切削量用小的切削量回工有色金属试件,然后在圆度仪上测量试件的圆度来评价。
出厂时,普通级加工中心的回转精度用静态测量法测量,当L=300mm时允许误差应小于0.02㎜。
造成主轴回转误差的原因主要是由于主轴的结构及其加工精度、主轴轴承的选用及刚度等,而主轴及其回转零件的不平衡,在回转时引起的激振力,也会造成主轴的回转误差。
因此加工中心的主轴不平衡量要控制在0.4㎜/s以下。
5.1.2、主轴刚度:
主轴组件的刚度是指受外力作用时,主轴组件抵抗变形的能力。
通常抵以主轴前端产生单位位移时,在位移方向上所施加的作用力大小来表示。
主轴组件的刚度越大,主轴受力的变形就越小。
主轴组件的刚度不足,在切削力及其他力的作用下,主轴将产生较大的弹性变形,不仅影响工件的加工质量,还会破坏齿轮、轴承的正常工作条件,使其加快磨损,降低精度。
主轴部件的刚度与主轴结构尺寸、支撑跨距、所选轴承类型及配置形势、砂间隙的调整、主轴上传动元件的位置等有关。
5.1.3、主轴抗振性:
主轴组件的抗振性是指切削加工时,主轴保持平稳的运转而不发生振动的能力。
主轴组件抗振性及在必要时安装阻尼(消振)器。
另外,使主轴固有频率远远大于激振力的频率。
5.1.4、主轴温升:
主轴组件在运转中,温升过高会起两方面的不良结果:
一是主轴组件和箱体因热膨胀而变形,主轴的回转中心线和机床其他件的相对位置会有变化,直