脱硫系统检修规程Word文件下载.docx
《脱硫系统检修规程Word文件下载.docx》由会员分享,可在线阅读,更多相关《脱硫系统检修规程Word文件下载.docx(8页珍藏版)》请在冰豆网上搜索。
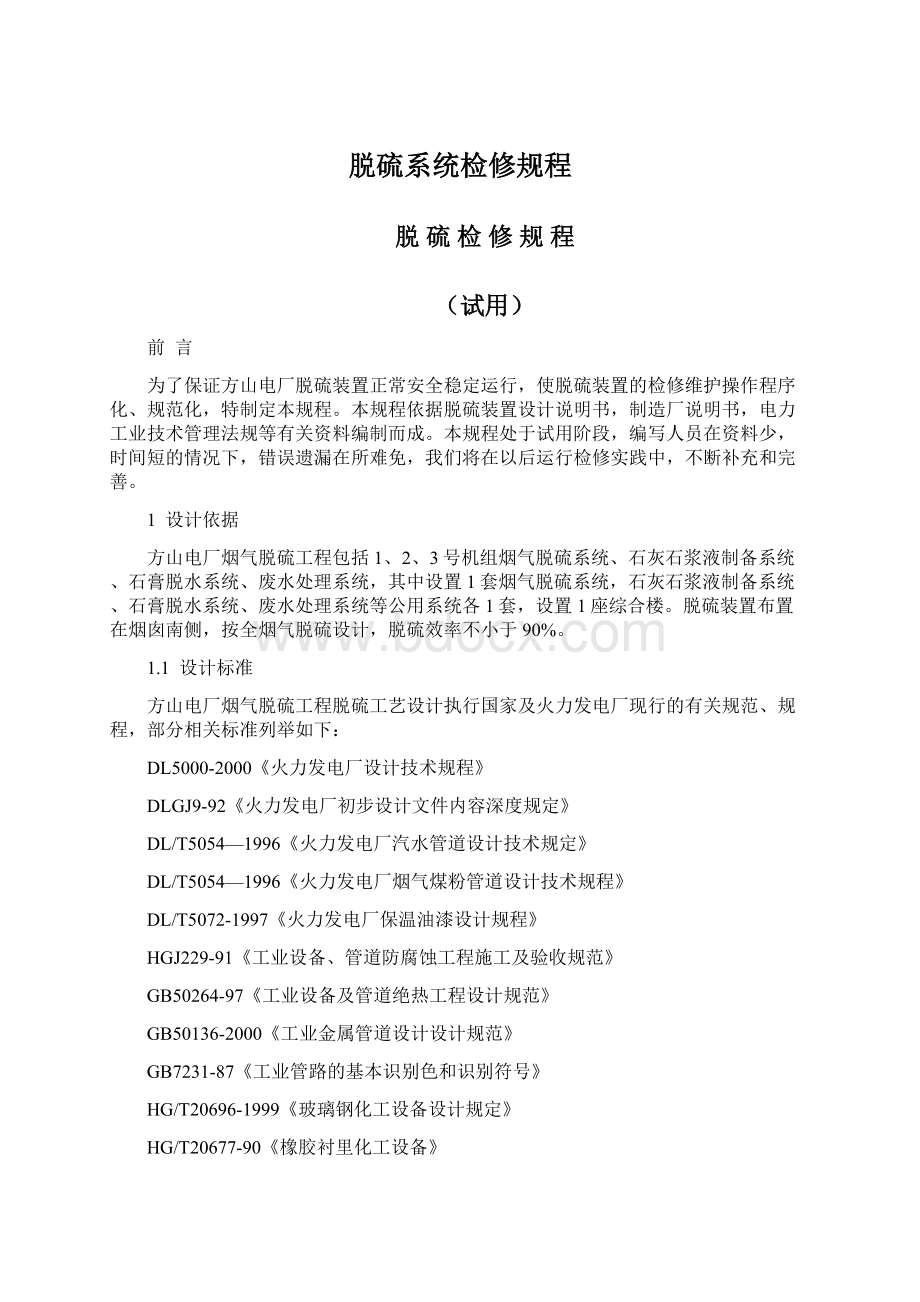
HG/T20696-1999《玻璃钢化工设备设计规定》
HG/T20677-90《橡胶衬里化工设备》
HG/T20678—2000《衬里钢壳设计技术规定》
JB/T4735-1997《钢制焊接常压容器》
GB13223-2003《火电厂大气污染排放标准》
GB16297-96《大气污染物综合排放标准》
HJ/T75-2001《火电厂烟气排放连续监测技术规范》
DL5007-92《电力建设施工及验收技术规范》
1.2
设计界限
1.2.1设计范围
烟气脱硫工程的工艺、电气、控制仪表、土建(包括总平面、建筑、结构、采暖通风、给排水、通讯、消防)专业的初步设计和施工图设计。
具体范围如下:
-湿式脱硫系统装置(1套)
-石灰石浆液制备和供应系统(1套)
-石膏浆液脱水系统(1套)
-脱硫废水处理系统(1套)
-事故浆液罐系统(1套)
-工艺水供应系统
-电气系统
-仪表与控制系统
-土建工程
供方同时还负责烟气脱硫工程工艺系统的接口设计。
1.2.2设计接口
-烟气
入口:
原烟气从主烟道引出。
从引出点开始的所有烟道,包括对原有主烟道的改造均为设计范围。
接口处设非金属膨胀节。
出口:
净烟气需接入主烟道,所有净烟气烟道,从接入点到烟囱入口之间的主烟道,包括对原有主烟道的改造均为设计范围。
旁路烟道:
旁路烟道及其旁路挡板门、膨胀节等的设计,包括对原有主烟道的改造。
旁路烟道的防腐设计等。
-石灰石浆液制备
进口:
综合楼石灰石粉仓入口。
FGD岛内部。
-石膏
石膏库出口(车辆买方自备)。
-工艺水
FGD工艺水箱入口阀门外脱硫岛南侧供水干管上。
接口为1处,应在此处接口管道上安装流量计量装置。
-废水排放
脱硫废水处理系统脱硫区域外1m。
废水排水压力应不小于0.6MPa。
-压缩空气(如果用)
FGD岛内部
-电源:
脱硫控制楼脱硫6kV配电室断路器电源进线端。
1.3
设计基础资料
1.3.1脱硫装置入口烟气参数见表3-1。
表3-1FGD入口烟气参数
项目
单位
单台机组
烟气流量
Nm3/h.台(干基)
274767
Nm3/h.台(湿基)
305581
温度
℃
134
压力
Pa
脱硫装置旁路温度
144
N2
%
72.189
CO2
11.549
H2O
10.08
O2
6.036
SO2
mg/Nm3
4039.14
烟尘
70
1.3.2石灰石成分见表3-2。
表3-2石灰石成分
数据
SiO2
1.59
CaO
52.62
MgO
2.39
Al2O3
0.80
Fe2O3
0.10
CaCO3
93.92
酸不溶物
1.81
SO3
0.067
F-
0.006
Cl-
0.030
1.3.3水质分析
本脱硫装置用水来自脱硫岛南侧,供水压力0.3MPa,管径DN100。
室外生产供水管管材采用钢丝网骨架塑料复合管。
水质分析报告表见表3-3。
表3-3水质分析参数
序号
分析项目
单位
含量
备注
1
pH值
8.27
2
悬浮物
mg/l
10.4
3
总固体
310.8
4
(COD)Mn
1.42
5
钠(Na+)
23.0
6
氯根(CI-)
18.5
7
硫酸根(SO42-)
26.83
8
重碳酸根(HCO3-)
mmol/l
4.17
9
全碱度
mmol/l
1.4工艺设计的主要特点
-本脱硫工艺设计采用石灰石/石膏湿法(以下简称FGD),其中FGD不设GGH烟气再热系统。
-脱硫装置的烟气处理能力为三台锅炉BMCR工况时的烟气量(按35~110%考虑烟气量波动),脱硫效率≥90%。
-脱硫系统设置100%烟气旁路,以保证脱硫装置在任何情况下不影响发电机组的安全运行。
-脱硫副产品石膏回收贮存或利用。
—脱硫系统关键设备(如搅拌器、调节阀、关键部位的执行器)采用进口。
-脱硫装置按年运行6000小时设计,FGD系统可利用率≥95%。
-脱硫装置出口烟气温度按54℃设计。
-公用系统(石灰石浆液制备系统、石膏浆液脱水系统、废水处理系统)按3台机组烟气脱硫总量设计,
-设置DCS控制系统。
2
脱硫工艺用吸收剂
石灰石-石膏湿法脱硫工艺使用的吸收剂为浓度25%的石灰石浆液,固体粒度-325目占90%以上,石灰石浆液由石灰石粉配制而成。
石灰石浆液制备系统为全厂3台机组脱硫系统共用。
石灰石浆液制备用石灰石纯度按93.92%计(按CaO=52.60%换算),粒度-325目占90%以上,含水<1%。
1、2、3号燃煤机组烟气脱硫装置石灰石(CaCO3含量为93.29%)消耗量为5.68t/h(锅炉BMCR工况蒸发量为260t/h,脱硫率≥90%)。
3
脱硫副产物的处置
烟气脱硫装置生成的石膏经真空皮带脱水机脱水后存放在石膏库,装载机装料后由汽车输送到灰场或销售。
石膏(含水10%)产量10.07t/h,约6.29m3/h。
4
脱硫装置工艺系统及主要工艺设备选型
4.1石灰石浆液供应系统
石灰石浆液制备系统为3台机组共用,包括石灰石粉仓、石灰石浆液制备、石灰石浆液输送等。
石灰石粉制浆系统设计出力为产石灰石浆液21.53m3/h,其中含石灰石5.68t/h。
主要设备包括:
石灰石粉仓1个,规格为Φ7×
14m,能贮存3台锅炉烟气脱硫3天所需石灰石粉;
流化态风机2套(其中1套备用),包括鼓风机、空气过滤器及进、出口消音器等;
流化风机流量为7.6m3/min,升压为58.8KPa。
流化态风机用于向石灰石粉仓底部充气箱充气,使贮仓底部的石灰石粉流态化以便于卸料。
行星给料机1台,给料能力为0~6t/h,用于将贮仓中的石灰石粉送到给料称重机;
给料称重机1台,给料能力为0~6t/h,用于将经过计量的石灰石粉送到石灰石浆配制槽;
石灰石浆配制槽1台,规格为Φ5000×
5000,用于将石灰石粉和水按照一定的比例,配制成25%的石灰石浆。
石灰石浆配制泵2台,1台备用,用于将配制好的石灰石浆液输送到吸收塔中。
4.2烟气系统
烟气系统按3台机组配备一套脱硫装置设计。
烟气从原烟道烟气引出,经烟道进口挡板、升压风机后,进入吸收塔。
烟气在吸收塔内与自上而下的循环石灰石/石膏浆液逆流充分接触后,烟气中的SO2溶解于石灰石/石膏浆液,并被吸收,大部分烟尘被截流,进入石灰石/石膏浆液。
洗涤后的烟气通过除雾器出吸收塔,经烟道出口挡板回到钢烟道净烟气接口,并通过烟囱排放。
一台静叶可调轴流式增压风机。
通过切换旁路挡板和脱硫装置进、出口挡板的开关,实现“脱硫装置的运行”和“脱硫装置的旁路运行”,保证在任何情况下不影响发电机组的安全运行。
烟气系统主要由下列设备组成:
-静叶可调轴流式增压风机1台,设计流量V=444.4m3/s、设计压力P=2800Pa
-进口挡板2台,规格为3000×
4000,4000×
6000
-出口挡板1台,规格为4200×
-旁路挡板2台,规格为4000×
3000,4000×
-挡板密封风机2台流量3963-4792m3/h
压力4661-4256pa
-挡板电加热器1台
-烟道、膨胀节
4.3
SO2吸收系统
SO2吸收系统是石灰石-石膏湿式脱硫装置的核心部分,所有脱除SO2的物理、化学反应过程都在吸收塔内进行并完成。
SO2吸收系统由吸收塔(包括壳体、喷淋层、搅拌器、氧化系统、除雾器)、浆液循环泵及管线、石膏浆液排出泵及管线等组成。
吸收塔采用逆流接触型洗涤喷淋塔,在吸收塔内将同时完成SO2的溶解、与石灰石浆液的反应、亚硫酸钙的氧化、石膏的结晶等过程。
主要反应如下:
H2O+SO2
?
H2SO3
H2SO3
H++HSO3-
HSO3-
+CaCO3+H+=CaSO3+H2O+CO2↑
CaSO3+1/2O2+2H2O=CaSO4·
2H2O
塔的上部为溶解、洗涤、吸收区,该区域布置有喷淋层,浆液循环泵将循环浆液(石灰石/石膏浆液组成)送入喷嘴喷淋,浆液自上而下与自下而上的烟气逆流接触后,除去烟气中的尘杂、溶解烟气中的SO2,并与CaCO3发生化学反应而被吸收,生成的CaSO3向下汇集至吸收塔的下部。
吸收塔下部分为氧化区和结晶区。
在氧化区,由氧化风机向氧化区浆液鼓送压缩空气,利用其中的O2将CaSO3氧化成CaSO4。
石膏浆液由结晶区排出经石膏浆液排出泵送至石膏旋流站。
在吸收塔上部设置二层除雾器,以除去脱硫净化后烟气夹带的液滴,烟气由塔顶引出,经出口挡板进入旁路钢结构烟道,从烟囱排放。
烟气中SO2的脱除效率取决于供给吸收塔吸收剂的量和结晶区浆液的pH值。
根据烟气中SO2量的变化自动调节吸收剂的加入量和循环浆液的pH值,获得90%以上的脱硫效率。