毕业论文平板对接焊缝的超声波检测Word文件下载.docx
《毕业论文平板对接焊缝的超声波检测Word文件下载.docx》由会员分享,可在线阅读,更多相关《毕业论文平板对接焊缝的超声波检测Word文件下载.docx(22页珍藏版)》请在冰豆网上搜索。
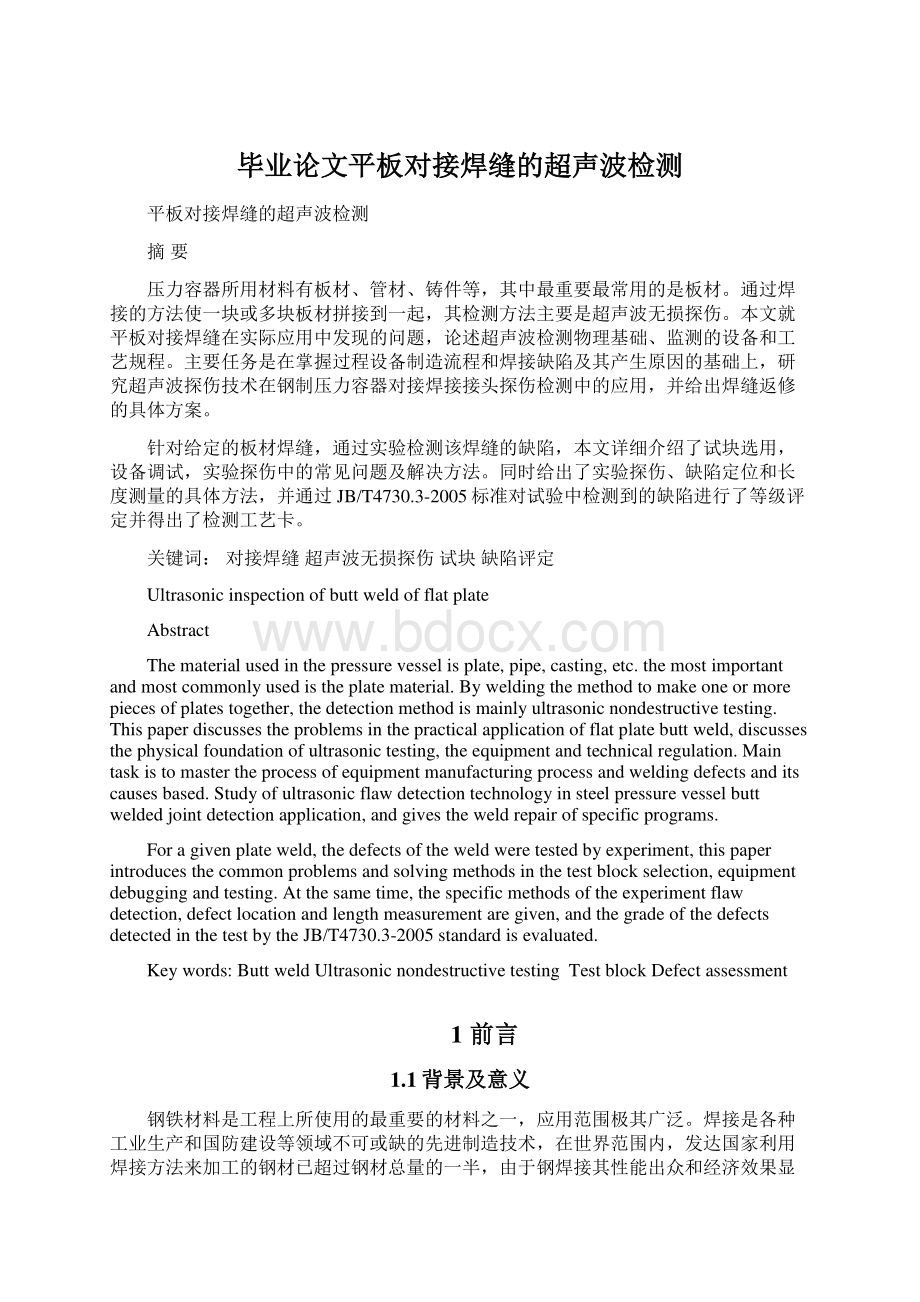
脉冲反射式超声波探伤仪就是根据这个原理设计的。
1.2超声波检测的发展与现状超声波检测的发展与现状无损探伤技术是检测压力容器焊缝内部缺陷的主要手段。
无损检测(non-destructiveexamination)是指在不损害或不影响被检测对象使用性能,不伤害被检测对象内部组织的前提下,利用材料内部结构异常或缺陷存在引起的热、声、光、电、磁等反应的变化,以物理或化学方法为手段,借助现代化的技术和设备器材,对试件内部及表面的结构、性质、状态及缺陷的类型、性质、数量、形状、位置、尺寸、分布及其变化进行检查和测试的方法。
工业上常用的无损检测方法有射线检验(RT)、超声检测(UT)、磁粉检测(MT)和液体渗透检测(PT)四种。
其中射线探伤和超声波探伤是检测压力容器焊缝内部缺陷的主要手段。
1.2.1国际超声波检测技术的发展历程与现状国际超声波检测技术的发展历程与现状超声无损检测技术(UT)是五大常规检测技术之一,是国内外应用最广泛、使用颇率最高且发展较快的一种无损检测技术,体现在改进产品质量、产品设计、加工制造、成品检验以及设备服役的各个阶段,体现在保证机器零件的可靠性和安全性上。
世界各国出版的无损检测书籍、资料、文献中,超声探伤所占的数量都是首屈一指的。
有关资料表明,国外每年大约发表3000篇涉及无损检测的文献资料,全部文献资料中有关超声无损检测的内容约占45%。
前几届世界无损检测会议论文集收录的论文中有关超声检测的论文数遥遥领先于其它检测方法,特别是2000年10月在罗马召开的第十五届世界无损检测会议(WCNDT)收录的663篇论文中,超声检测就占250篇(2000年WCNDT会议收录的论文分布情况)。
这些都说明超声无损检测的研究势头和其在无损检测中的重要地位。
20世纪70年代以来,超声检测的数字化、自动化、智能化和图像化成为超声无损检测技术研究的热点,标志着超声无损检测的现代化进程。
近年来,随着传感技术、电子技术、自动控俐技术、记算机技术的发展,现代无损检测技术已经进人到以计算机控制为主的信息加工时代。
20世纪80年代,新一代的超声检测仪器数字化、智能化超声仪问世,标志着超声检测仪器进入一个新时代。
超声无损检测仪器将向数字化、智能化、图像化、小型化和多功能化发展。
在第十三、十四世界无损检测会议仪器展览会、1996年中国国际质量控制技术与测试仪器展览会、1997年日本无损检测展览会等大型国际会议会展中,数字化、智能化、图像化超声仪最引人注目,显示了当今世界无损检测仪器的发展趋势。
其中以德国Krautraemer公司、美国Panametrics公司、丹麦ForceInstitutes公司与美国PAC公司的产品最具代表性。
从20世纪90年代以来,超声成像技术是一种令人瞩目的新技术。
超声图像可以提供直观和大量的信息,直接反映物体的声学和力学性质,有着非常广阔的发展前景。
现代超声成像技术都是计算机技术、信号采集技术和图像处理技术相结合的产物。
数据采集技术、图像重建技术、自动化和智能化技术以及超声成像系统的性能价格比等发展直接影响超声检测图像化的进程。
1.2.2国内超声波检测技术的发展现状国内超声波检测技术的发展现状近年来我国超声无损检测事业取得了巨大进步和发展。
超声无损检测已经应用到了几乎所有工业部门,其用途正日趋扩大。
超声无损检测的相关理论和方法及应用的基础性研究正在逐步深入,已经取得了许多具有国际先进水平的成果。
许多不同用途的微机控制自动超声检测系统已经应用于实际生产。
我国在这方面开展的主要研究有:
计算机化超声设备;
用户友好界面操作系统软件;
超声数字信号处理,包括人工智能、神经网络、模式识别、相位补偿等;
高频超声无损检测技术:
各种扫描成像技术:
多坐标、多通道的自动超声检查系统:
超声机器人检测系统:
复杂构件的自动扫描超声成像检测(如5维以上多维探头调节结构等辅助设备的开发研究)等。
这其中许多成果已经达到国际先进水平,这些研究为我国超声无损检测技术的持续发展提供了保证。
无损检测的标准化和规范化,检测仪器的数字化、智能化、图像化、小型化和系列化工作也都取得了很大发展。
我国已经制订了一系列国标、部标及行业标准,而且引进了ISO,ATSM、DIN、SS、BS、NF、JIS等一百多个国外标准。
无损检测人员的培训也逐渐与国际接轨。
但是,我国超声无损检测事业从整体水平而言,与发达国家之间存在很大差距,具体表现在:
检测专业队伍中高级技术人员和高级操作人员所占比例较小,极大阻碍了超声无损检测技术自动化、智能化、图像化的进展。
专业无损检测人员相对较少,现有无损检测设备利用率低。
对无损检测技术领域的信息技术应用重视度。
2超声波检测物理基础及设备超声波检测物理基础及设备2.1超声波原理及特点超声波原理及特点超声波探伤是利用材料及其缺陷的声学性能差异对超声波传播波形反射情况和穿透时间的能量衰减变化来检验材料内部缺陷的无损检测方法。
实验室中常用横波来进行超声波探伤实验,其探伤原理如图2-1所示。
1-工件2-焊缝3-缺陷4-超声波束5-斜探头图2-1横波探伤原理图超声波是一种频率高于20000Hz的声波,它的方向性好,穿透能力强,易于获得较集中的声能,在水中传播距离远,对人体无害可用于测距、测速、清洗、焊接、碎石、杀菌消毒等。
但是超声波探伤显示不太直观,易发生衰减和散射,对工作表面要求平滑,要求富有经验的检验人员才能辨别缺陷种类、适合于厚度较大的零件检验,这是超声波的局限性。
2.2超声波检测的设备超声波检测的设备2.2.1超声检测仪超声检测仪超声波检测仪是检测的主体设备,作用是产生电振荡作用于探头,使之发射超声波,同时将探头送回的电信号进行滤波、检波、放大等,并以一定的方式显示出来。
超声波检测仪按发射超声波的方式分为脉冲波检测仪、连续波检测仪和调频波检测仪。
其中使用最广的是脉冲波检测仪,它向工件周期性地发射频率固定的超声波。
超声波检测仪按显示方式可分为:
A型探伤仪:
是一种波型显示,在显示屏幕上以横坐标代表声波的传播时间(距离),纵坐标代表反射波的幅度。
B型探伤仪:
是一种图像显示,可显示工件纵截面的图像。
C型探伤仪:
也是一种图像显示,可显示工件平行截面的图像。
目前使用最广的是A型脉冲反射式检测仪图2-1图2-2A型脉冲反射式检测仪2.2.2探头探头超声波检测一般采用压电型探头,其作用是利用压电晶片,在高频电振荡激励下产生高频机械振动发射超声波(发射探头),或在超声波作用下产生机械变形,并因此产生电荷。
超声波探头按结构形式分为:
直探头:
用于交替地发射和接收纵波,波束垂直于工件表面。
斜探头:
利用楔块将声束倾斜于工件表面而射入工件。
一般用于横波探伤。
2.2.3耦合剂耦合剂超声耦合剂是指超声波在检测面上的声强透射率。
声强透射率高,超声耦合号。
为了改善探头与工件声能的传递,而加在探头和检测之间的液体薄层为耦合剂。
耦合剂可以填充探头与工件间空间距离,使超声波能够传入工件,这是耦合剂的主要目的。
此外耦合剂还可以减少摩擦力的作用。
常用的耦合剂有水、甘油、机油、变压油、化学糨糊等。
水的优点是来源方便,缺点是易流失,使工件生锈。
甘油优点是声阻抗大,耦合效果好,缺点是需要水稀释,容易使工件形成腐蚀坑,价格昂贵。
机油和变压油附着力粘度较合适,无腐蚀价格不贵,是最常用的耦合剂。
化学糨糊耦合剂效果较好,也是常用的耦合剂。
2.2.4试块试块试块按照用途设计制作的具有简单性状的人工反射体的式样,是超声探伤重要的工具。
其作用是:
A进行探伤灵敏度的调整和确定B调整和确定合适的扫描速度C测试探头的一些性能D测绘确定缺陷大小超声波探伤常用的标准试块有:
CSKIA试块,SH1型半圆试块,RB-2试块,IIW试块。
对比试块有:
WGT-3试块,DB-H2试,块阶梯试块。
专用试块有:
GTS-60试块,GTS-60加长测试轨。
3平板对接焊缝制造方法及缺陷平板对接焊缝制造方法及缺陷3.1平板对接焊缝主要制造方法平板对接焊缝主要制造方法在过程装备制造中,常用的焊接方法主要有手工电弧焊、埋弧自动焊、气体保护焊、电渣焊等。
对于小型的板材焊接常采用手工电弧焊和埋弧自动焊。
3.1.1手工电弧焊手工电弧焊手工电弧焊简称手弧焊,是以手工操作的焊条和被焊接的工件做为两个电极,利用焊条与焊件之间的电弧热量熔化金属进行焊接的方法。
由于其设备简单、操作方便、能够进行全方位焊接且适合焊接多种材料等特点,在装备制造中是一种应用十分广泛的焊接方法。
当然其不足之处是焊接速度慢、生产效率低劳动强度大、烟尘大对操作人员身体有损害等。
3.1.2埋弧自动焊埋弧自动焊埋弧自动焊简称埋弧焊,是电弧在焊剂层下燃烧,用机械自动引燃电弧并进行控制,自动完成焊丝的送进和电弧移动的一种电弧焊方法。
埋弧自动焊具有生产率高、机械化程度高、焊接质量好且稳定的优点。
在金属结构、桥梁、压力容器、石油化工、核容器、石油天然气管线、船舶制造等领域,埋弧自动焊获得了广泛的应用。
埋弧焊局限性是工作量非常大,所消耗的钢材、焊丝、焊剂的量也很大。
3.2平板对接焊缝常见缺陷平板对接焊缝常见缺陷3.2.1焊接过程中主要缺陷焊接过程中主要缺陷在焊接过程中焊接接头会产生金属不连续,不致密或者连续不良的现象称为焊接缺陷。
焊接过程中主要出现的缺陷分为两大类:
外观形状缺陷和内部缺陷。
外观形状缺陷主要有咬边、焊瘤、凹坑、未焊满、烧穿、错边、塌陷、成形不良、表面气孔、各种焊接变形和波浪变形等。
这些缺陷存在将对超声波探伤缺陷的判断产生影响。
因此,在对焊缝进行超声波探伤前必须对工件焊缝外观进行检查,发现有上述缺陷时尽量设法清除。
内部缺陷主要有气孔、夹渣、未焊透、未融合和裂纹等,这些缺陷是超声波探伤的检测对象,检测目的就是要发现这些缺陷。
相关人员必须了解其特点、分布规律和对超声波的反射特性。
气孔气孔是指焊接时,熔池中的气体未在金属凝固前逸出,残存于焊缝之中所形成的空穴。
其气体可能是熔池从外界吸收的,也可能是焊接冶金过程中反应生成的。
气孔的危害气孔减少了焊缝的有效截面积,使焊缝疏松,从而降低了接头的强度,降低塑性,还会引起泄漏。
气孔也是引起应力集中的因素。
氢气孔还可能促成冷裂纹。
夹渣夹渣是指焊后溶渣残存在焊缝中的现象。
夹渣的危害点状夹渣的危害与气孔相似,带有尖角的夹渣会产生尖端应力集中,尖端还会发展为裂纹源,危害较大。
未焊透未焊透是指母材金属未熔化,焊缝金属没有进入接头根部的现象。
未焊透的危害:
未焊透的危害之一是减少了焊缝的有效截面积,使接头强度下降。
其次,未焊透焊透引起的应力集中所造成的危害,比强度下降的危害大得多。
未焊透严重降低焊缝的疲劳强度。
未焊透可能成为裂纹源,是造成焊缝破坏的重要原因。
未融合未熔合是指焊缝金属与母材金属,或焊缝金属之间未熔化结合在一起的缺陷。
未熔合的危害:
未熔合是一种面积型缺陷,坡口未熔合和根部未熔合对承载截面积的减小都非常明显,应力集中也比较严重,其危害性仅次于裂纹。
裂纹焊缝中原子结合遭到破坏,形成新的界面而产生的缝隙称为裂纹。
根据裂纹尺寸大小,分为三类:
A宏观裂纹:
肉眼可见的裂纹。
B微观裂纹:
在显微镜下才能发现。
C超显微裂纹:
在高倍数显微镜下才能发现,一般指晶间裂纹和晶内裂纹。
3.2.2使用过程中出现的缺陷使用过程中出现的缺陷焊接结构使用过程缺陷甚至失效形式有:
脆性失效、塑性失效、疲劳失效、应力腐蚀失效等。
脆性断裂:
焊接结构的一种最为严重的断裂失效。
通过脆性断裂失效都在实际应力低于结构设计应力下发生,断裂时无显著的塑性变形,具有突发破坏的性质,往往造成重大损失。
其特点是裂纹扩展迅速,能量消耗远小于韧性断裂,断裂之前无明显的征兆。
脆性断裂断口表面发亮,呈颗粒状,属于平直类型。
塑性断裂:
金属断裂时伴随有明显的塑性变形并消耗大量能量。
由于塑性断裂是在大量塑性变形后发生的,结构断裂后在受力方向上会留下较大的残余变形,在断口附近有肉眼可见的挠曲、变粗、缩颈等。
在大多数材料中,拉伸塑性断口呈灰色纤维状,宏观上分为平直面和剪切面。
疲劳失效:
零件或试样在整个疲劳失效过程中,不发生肉眼可见的宏观塑性变形。
在多数情况下疲劳断裂是突然发生的,因而这种断裂方式给焊件失效前的预报和预防工作带来一定的困难。
一个典型的疲劳断口往往由裂纹源区、裂纹扩展区和瞬时断裂区三个部分组成。
这种独特的形貌是区别于其他断裂形式的极为重要的凭证。
应力腐蚀断裂:
它是一种远低于金属屈服点的拉应力与化学侵蚀共同作用的破坏过程。
纯金属对该类破坏的敏感性比不纯的金属低的多,而纯二元合金对该类破坏一般都是很敏感的。
裂纹常常产生大量的分叉,并在大致垂直于影响它们产生和扩展的拉应力方向连续扩展。
在这种情况下,细小的裂纹会深深地扩展进焊件之中而表面又呈现出模糊不清的腐蚀迹象。
4超声波无损探伤实验超声波无损探伤实验4.1超声波探伤实验器材及实验操作超声波探伤实验器材及实验操作实验中采用PXUT320C型数字式超声波探伤仪,见图4-1。
采用的试块为300X300X22mm的对焊平板,材料为铸铁,见图,4-2。
实验中用到的试品及基本参数详见表4-1。
图4-1PXUT-320C型数字式超声波探伤仪图4-2钢制平板对接焊缝仪器名称PXUT320C型数字超声波探伤仪探头型号2.5P13x13试件厚度22mm探头k值K2探头标准JB/T4730.3-2005标准试块CSK-IA检测面单侧双面耦合剂机油检验级别B级检测方法横波斜入射验收级别A级表面补偿3dBDAC点数3(10、20、30)评定线移量:
-9dB定量线移量:
-3dB判废线移量:
5dB表4-1实验用品及基本参数4.1.1检测面的修整检测面的修整试件表面情况的好坏对检测结果影响较大。
所以在检测前应对检测面的飞溅物、氧化皮及锈蚀等进行处理。
通常用砂轮、锉刀、磨石砂纸等对检测面进行处理,表面粗糙度Ra6.3um。
焊缝两侧检测面宽度不小于探头移动区域。
由试件的厚度、探头的K值与探头的尺寸A来确定跨距用P表示,则:
P=2KTK探头的K值T试件的厚度按照焊缝检测工艺卡中JB/T4730.3-2005中规定:
采用直射法检测,探头移动区域应不小于0.75P,采用一次反射法检测时,探头移动区域不小于1.25P。
本实验移动区域120mm。
4.1.2零点声速的测定零点声速的测定1)通道的初始化。
接通电源打开仪器。
按进入探伤界面,按“1当前通道”完成初始化。
2)按进入设置界面,输入探头的原始参数如表4-2所示,按键生效。
探头类型斜探头探头频率2.5MHz晶片尺寸13x13K值2工件声速3230m/s前沿长度12.5mm表4-2探头原始参数3)按按钮两次再按“1测零点声速”进入零点调校界面,输入参数如表4-3所示,按键进行测试。
预设工件声速3230m/s一次回波声程50mm二次回波声程100mm表4-3零点测试测定参数表将探头放置在CSK-IA试块上并移动,使R50回波处于门内(波高约80%),按键保持探头位置不变,当R100回波波高在波门内且稳定时再一次按键,屏幕出现“探头只一次反射体水平距离”。
用直尺测出探头到R50圆弧的水平距离为33mm,输入仪器并按键,按进行存储。
完成零点声速的测定如图4-3所示,波形图如图4-4所示。
图4-3零点声速测试示意图图4-4测零点声速波形图4.1.3折射角的测定折射角的测定按按钮两次,按“2测折射角”开始测折射角,屏幕提示“先测零点声速?
y|n”,按键,输入参数如表4-4所示。
目标反射体直径50mm标称k值2反射体中心深度30mm表4-4折射角测定的参数将探头放在CSK-IA试块上,移动探头使50孔的最高回波出现在波门之内,按键,按键,把仪器算出的K值和折射角值存储。
如图4-5所示,波形图如图4-6所示图4-5测折射角示意图图4-6折射角测定波形图4.1.4DAC曲线曲线按按钮两次,按“3制作DAC”按钮,屏幕提示“先测零点声速?
y|n”,按键,输入参数如表4-5所示。
最大深度50mm反射体长度40mm反射体直径3mm表4-5DAC曲线按键后将探头放在RB-2试块上移动,如图4-7,自动调节增益使10mm孔的最高回波在40%80%之间,当参数区有“DAC”提示时,按键将光标移至10mm孔的回波上,再按键确认此回波;
再次移动探头,找到深度为30mm孔的最高回波,按键将光标移至30mm孔的回波上,再按键确认此回波;
同样方法确认40mm深孔的波高,待各点采集完成经确认存储后,DAC曲线制作完成。
制作如图4-8(a)、4-8(b)、4-8(c)、4-8(d)所示。
图4-7RB-2制作DAC曲线(a)(b)(c)(d)图4-8DAC曲线波形图的制作4.1.5其他参数的输入其他参数的输入按键,将所测前沿的值输入,按键。
然后按键,依据表4-1进行其他数据的输入:
判废偏移输入5dB,定量偏移输入-3dB,评定偏移输入-9dB。
此时DAC如图4-9所示:
图4-9DAC曲线至此,实验准备阶段完成,开始进行超声波探伤。
4.2超声波探伤试验现象数据超声波探伤试验现象数据4.2.1探头扫查探头扫查1)缺陷I反射波形图如图4-10所示:
图4-10缺陷I反射波形图缺陷I定位:
由探伤仪可读取缺陷水平位置距探头发射点距离lf=42mm,由1过程装备制造与检测中公式3-4:
可求得缺陷深度为3.3mm。
2)缺陷II反射波形图如图4-11所示:
图4-11缺陷II反射波形图缺陷II定位:
由探伤仪可知有两处缺陷,读取缺陷1水平位置为35mm,缺陷深度为6.5mm;
缺陷2水平位置为45mm,缺陷深度为2.0mm。
4.2.2缺陷长度测定缺陷长度测定由三处缺陷反射波形图判断,三处缺陷均可以采用6dB法(即:
半波高度法),现以缺陷I为例进行计算,具体操作步骤如下:
1)移动探头找出最大反射波;
2)调节增