脱硝装置设计说明正式版Word格式.docx
《脱硝装置设计说明正式版Word格式.docx》由会员分享,可在线阅读,更多相关《脱硝装置设计说明正式版Word格式.docx(48页珍藏版)》请在冰豆网上搜索。
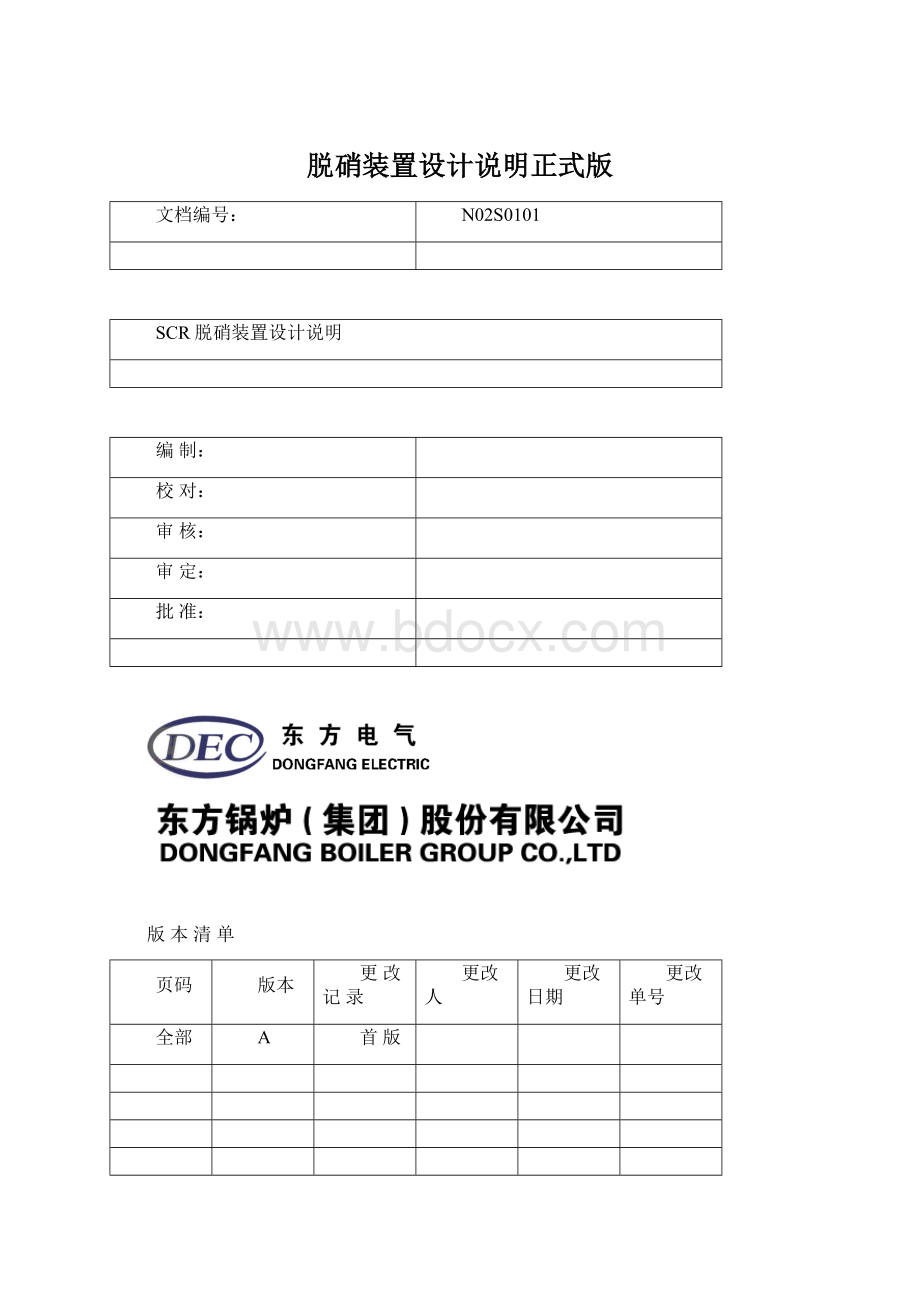
氨站区域1米外至SCR区域外1米的脱硝装置管线由业主规划,DBC供货。
DBC对除SCR钢支架基础、氨区设备基础外的系统和设备进行供货,另对暖通、消防系统DBC仅提供技术要求,不负责设计与供货。
供货范围至少包含以下部分:
1)氨的制备供应系统:
指从液氨罐车出口到氨气/空气混合器(含氨气/空气混合器)所包含所有设备和部件。
2)氨的喷射系统:
指从氨气/空气混合器出口到氨气喷嘴内所包含的所有设备和部件。
3)氮气吹扫系统:
应包含系统所必须所有设备部件、管道附件等(不含氮气瓶)。
4)烟道系统:
包括省煤器出口烟道到SCR反应器入口和SCR出口到空气预热器进口烟道包含的支吊架、膨胀节等所有部件。
5)SCR反应器:
包含反应器壳体、催化剂、壳体内部所包含的支撑结构、烟气整流装置、密封装置等。
6)催化剂装卸系统:
满足催化剂在安装和卸下时所需要的设备,包括催化剂运送器,升降装置、滑轨等。
7)吹灰系统:
包括吹灰系统所有必须的所有设备部件、吹灰器、相关阀门管路系统、控制设备等。
8)控制系统:
DBC负责脱硝范围内仪表控制系统的系统设计及安装设计,并负责设备、材料与备品备件的供货,配合完成设备安装和系统调试,负责对用户的培训,以及提供接口软、硬件相应的配合工作。
整套脱硝控制系统,包含但不限于下列设备:
a)脱硝DCS系统及全套附件(含DCS模件柜、端子柜,远程I/O模件柜、端子柜,通讯电缆,便携式工程师站等)。
b)程控柜、电源柜、配电箱、吹灰系统动力柜,包括柜内所有的继电器、电源开关等辅助设备和柜内接线等。
c)现场安装的控制箱、仪表柜和接线盒等,包括箱柜内外所有仪表设备和材料、接线等。
现场安装的控制箱、仪表柜和接线盒采用不锈钢材质。
d)脱硝系统内所有仪表及控制设备。
e)脱硝系统内所有仪表阀门及导管,仪表阀门及导管采用不锈钢。
f)气动阀们的气源所配的减压过滤器,流量控制阀和气源管路等附件。
g)预制电缆、就地设备至就地控制箱、就地接线盒的连接电缆以及所有配供设备之间的连接电缆。
h)软件:
操作系统软件、监控界面软件、编程软件等均由卖方提供。
i)卖方在合同附件中列出仪控设备的细化清单,包括型号、厂家、数量等。
9)SCR钢支架和平台、扶梯:
在柱底板及以上(含地脚螺栓)的所有钢结构部件(包含钢支架区域一次风机、送风机起吊和烟道的支吊所需要的钢结构),脱硝装置必须的平台和扶梯以及与锅炉之间的联络平台。
10)保温、油漆:
a)DBC提供保温设计和保温所需的金属构件和外护板,外护板采用1mm厚彩涂梯型钢板;
保温材料由业主自行采购。
所有管道的保温及保温用金属件不在DBC的设计和供货范围。
b)设备的油漆应在工厂完成,并提供必要的现场补漆。
c)钢结构支架和平台扶梯除最后一道面漆外的所有底漆和面漆应在工厂完成。
最后一道面漆由DBC提供并运送至现场,由业主施工。
1.5.2设计分包
为配合完成烟气脱硝装置技术工作,以下设计工作由其他有关单位完成:
•脱硝装置氨供应系统,由DBC委托四川晨光工程设计院负责完成。
•脱硝工程中SCR装置本体支撑钢架基础,脱硝氨站区域设备基础、建(构)筑物详细设计(施工图设计),脱硝项目中供水、供电、供气(汽)等至各设计分界,由业主委托主体发电工程设计单位湖南省电力勘测设计院负责完成。
1.5.3主要设计文件
设计文件包括设计资料和设备设计文件。
详见“设备及供外资料目录(N02S0100(GW))”。
2设计条件
2.1工程概况
2.1.1电厂厂址
电厂位于湖南省中部的望城县,距长沙市北面约35km的湘江下游。
2.1.2电厂规模
本期工程规模为2×
600MW的国产超临界参数燃煤汽轮发电机组。
2.1.3交通运输条件。
电厂进厂公路从长湘公路K23+900(戴公桥)接引,公路全长12.073km。
湘江是湖南省最大的河流,湘江常年可通航1000t级船舶,厂址东南方向有霞凝港,水路交通方便,可作为电厂部分地材和大件运输的备用方案。
2.1.4主厂房设备布置
本期装设两台600MW燃煤汽轮发电机组,锅炉由东方锅炉(集团)股份有限公司设计供货。
锅炉为超临界参数变压直流炉,单炉膛、一次再热、平衡通风、露天布置、固态排渣、全钢构架、全悬吊结构Π型锅炉。
本工程发电机组同步建设锅炉烟气脱硝装置,位于锅炉尾部,呈露天布置,由东方锅炉(集团)股份有限公司设计和成套供货。
2.2环境条件
2.2.1气象特征
多年平均大气压力1008.1hPa
多年平均大气温度16.9℃
多年平均相对湿度81%
多年最热月平均气温28.9℃
多年最冷月平均气温4.6℃
历年极端最高气温39.0℃
历年极端最低气温-12.0℃
多年平均降水量1400.6mm
最大一日降水量(24h)143.9mm
多年最大积雪深度0.27m
最大冻土深度0.05m
最冷季主导风向NNW风
最热季主导风向NW风
2.2.2厂区土质
湘江Ⅲ级阶地,第四系中更新统冲积地层,阶地已丘陵化,海拨高度35~52m。
2.2.7地震烈度
根据国家地震局2001版《中国地震动参数区划图》(GB18306—2001),测区地震动峰值加速度0.05g(相当于地震基本烈度Ⅵ度),地震动反应谱特征周期为0.35s,属于低烈度低频度的少震区。
2.3煤质、灰份和点火油资料
2.3.1煤质分析资料
表2-1煤质分析
项目
符号
单位
设计煤种
校核煤种
元
素
分
析
收到基碳
Car
%
60.09
55.4
收到基氢
Har
2.94
1.89
收到基氧
Oar
3.59
2.53
收到基氮
Nar
1.34
0.95
收到基全硫
St,ar
0.63
0.88
收到基铅
Pb
μg/g
7
收到基镍
Ni
10
收到基锌
Zn
3
收到基铬
Cr
16
收到基砷
As
6
收到基氯
CL
0.010
0.3355
收到基氟
F
0.0054
0.2558
工
业
收到基灰份
Aar
23.63
29.75
收到基水份
Mt
7.78
8.6
空气干燥基水份
Mad
1.37
1.65
干燥无灰基固定碳
Cdaf
干燥无灰基挥发份
Vdaf
15.00
11.0
收到基低位发热量
Qnet,ar
Kcal/kg
KJ/kg
22600
20240
可磨系数
HGI
—
61
KVT1
冲刷磨损指数
Ke
1.18
2.0
综合着火指数*反应指数
Rw/ri
煤粉气流着火温度
IT
℃
695
710
收到基原煤堆积比重
ρc,b
T/m3
0.9358
0.9568
灰
熔
点
变形温度
DT
1470
>1500
软化温度
ST
熔化温度
FT
成
二氧化硅
SiO2
51.62
45.55
三氧化二铝
Al2O3
33.75
35.41
三氧化二铁
Fe2O3
2.74
4.64
氧化钙
CaO
4.01
6.10
氧化镁
MgO
0.91
1.96
氧化钾
K2O
0.59
1.12
氧化钠
Na2O
0.38
0.44
三氧化硫
SO3
3.91
3.05
二氧化锰
MnO2
五氧化二磷
P2O5
0.16
五氧化二钒
V2O5
281
五氧化二砷
As2O3
<
1
二氧化钛
TiO2
1.03
0.21
比
电
阻
20℃500V
R20
Ω·
cm
12.5℃500V
R80
6.0×
1010
8.65×
100℃500V
R100
5.70×
1011
8.69×
120℃500V
R120
8.2×
5.6×
150℃500V
R150
3.05×
7.65×
180℃500V
R180
1.60×
7.11×
2.3.2燃油
本期锅炉点火及助燃油为0号轻柴油,油质的特性数据见下表2—2。
表2-2油质的特性数据表
平均
粘度
°
E
1.2~1.67
含硫量S
0.23
机械杂质
无
低位发热量
kJ/kg
41031~41870
水份
痕迹
闭口闪点
≥65
凝固点
比重
Kg/m
0.817
2.4脱硝系统入口参数
2.4.1脱硝系统入口烟气参数
表2-3脱硝系统入口烟气参数(BMCR工况)
单位
数据
湿基
干基
省煤器出口烟气成分(过量空气系数为1.15)
CO2
Vol%
15.35(设计煤种)
15.96(校核煤种)
16.56(设计煤种)
17.06(校核煤种)
O2
2.59(设计煤种)
2.59(校核煤种)
2.79(设计煤种)
2.77(校核煤种)
N2
74.77(设计煤种)
75.01(校核煤种)
80.65(设计煤种)
80.17(校核煤种)
SO2
0.06(设计煤种)
0.09(校核煤种)
0.07(设计煤种)
0.10(校核煤种)
H2O
7.36(设计煤种)
6.51(校核煤种)
锅炉不同负荷时的省煤器出口烟气量和温度(湿基)
BMCR
THA
75%THA
40%THA
30%THA
省煤器出口湿烟气量(设计煤种)Nm3/h
1717904
1572292
1210771
788542
683592
省煤器出口烟气温度(设计煤种)℃
388
377
352
324
306
省煤器出口湿烟气量(校核煤种)Nm3/h
1706236
1560537
1201553
794847
685053
省煤器出口烟气温度(校核煤种)℃
390
379
353
2.4.2脱硝系统入口烟气中污染物成分
表2-4脱硝系统入口烟气中污染物成分(BMCR工况,标准状态,干基,含氧量6%)
烟尘浓度
g/Nm3
25.96
36.81
NOX(以NO2计)
mg/Nm3
650
Cl(HCl)
F(HF)
1179
1856
17
26
2.5纯氨资料
脱硝系统用的反应剂为纯氨,其品质符合国家标准GB536—88《液体无水氨》技术指标的要求,如下表:
表2-5液氨品质参数
指标名称
合格品
备注
氨含量
99.0
残留物含量
0.4
重量法
水分
油含量
Mg/kg
红外光谱法
铁含量
密度
kg/L
25℃时
沸点
标准大气压
3脱硝装置性能
3.1NOX脱除率、氨的逃逸率、SO2/SO3转化率
在设计煤条件下,对NOX脱除率、氨的逃逸率、SO2/SO3转化率同时进行考核:
脱硝装置在性能考核试验时的NOX脱除率不小于52%,脱硝装置出口NOX含量不大于312(终期87%时84.5)mg/Nm3,氨的逃逸率不大于3ppm,SO2/SO3转化率小于0.9%。
(含氧量6%)
脱硝装置在保证的催化剂化学寿命期内,即备用层催化剂投运前,NOX脱除率不小于50%(终期85%),氨的逃逸率不大于3ppm,SO2/SO3转化率小于1%。
脱硝装置在备用层催化剂投运后,NOX脱除率不小于50%(终期85%),氨的逃逸率不大于3ppm,SO2/SO3转化率小于1%。
1)锅炉45%BMCR—100%BMCR负荷。
2)烟气中NOX含量:
450mg/Nm3至650mg/Nm3,(干基,含氧量6%)。
3)脱硝系统入口烟气含尘量不大于24.05g/Nm3(干基,含氧量6%)。
4)脱硝效率为50%时NH3/NOX摩尔比不超过保证值0.51(脱硝效率为85%时,不超过0.81)时。
3.2压力损失
1)从脱硝系统入口到出口之间的系统压力损失(省煤器出口至空预器进口)在性能考核试验并按脱硝效率50%时不大于710Pa;
按脱硝效率85%时不大于810Pa(设计煤种,100%BMCR工况,不考虑附加催化剂层投运后增加的阻力)。
2)从脱硝系统入口到出口之间的系统压力损失(省煤器出口至空预器进口)按脱硝效率50%时不大于835Pa;
按脱硝效率85%时不大于985Pa(设计煤种,100%BMCR工况,并考虑附加催化剂层投运后增加的阻力)。
3)化学寿命期内,对于SCR反应器内的每一层催化剂,由于粘污和堵塞等原因导致的压力损失应保证增幅不超过20%,初始的压力损失数据在试运行的时候确定。
3.3脱硝装置可用率
在质保期内,脱硝整套装置的可用率在最终验收前不低于98%,在燃用校核煤种时,保证脱硝装置安全运行。
3.4催化剂寿命
从脱硝装置投入商业运行开始到更换或加装新的催化剂之前,催化剂的运行小时数作为催化剂化学寿命(NOX脱除率不低于性能保证要求,氨的逃逸率不高于3ppm)。
DBC保证催化剂的化学寿命不少于24000小时。
DBC保证催化剂的机械寿命不少于50000小时。
3.5系统连续运行温度
在满足NOX脱除率、氨的逃逸率及SO2/SO3转化率的性能保证条件下,DBC保证SCR系统具有正常运行能力。
最低连续运行烟温310℃。
最高连续运行烟温430℃。
3.6氨耗量
在100%BMCR至45%BMCR负荷,且原烟气中NOX含量为650mg/Nm3时(干基,含氧量6%),DBC保证系统氨耗量。
BMCR工况,50%脱硝效率条件下,两台机组最大氨耗量不超过473kg/h。
此消耗值为性能考核期间48小时的平均值。
3.7其它消耗
DBC保证在100%BMCR工况,含尘量24.05g/Nm3(干基,含氧量6%)时,以下消耗品的值,此消耗值应为性能考核期间48小时的平均值。
1)吹扫的单位时间内的蒸汽耗量11.5t/h。
2)每次吹扫期间的蒸汽耗用总量23t。
3)吹扫频率1次/周。
注:
一台机组各1台吹灰器同时吹扫运行。
4工艺设计
4.1脱硝工艺原理
脱硝工艺采用选择性催化还原方法,该反应发生在装有催化剂的反应器里,烟气与喷入的氨在催化剂的作用下反应,实现脱出氮氧化合物。
自站区域来的氨气与稀释风机来的空气在氨/空气混合器内充分混合。
氨的爆炸极限(在空气中体积浓度)16~25%,为保证安全和分布均匀,稀释风机流量按稀释后的氨体积浓度不超过5%设计。
氨的注入量控制由SCR进出口NOX,出口O2监视分析仪测量值、烟气温度测量值、稀释风机流量、烟气流量(由燃煤流量和燃煤资料经换算求得)来控制。
通过氨/烟气混合器的混合气体进入位于烟道内的氨注入格栅,在注入格栅前设有手动调节和流量指示,在系统投运初期可根据烟道进出口检测NOX浓度来调节氨的分配量,调节结束后不再调整。
混合气体通过氨注射栅格注入到催化剂前的烟道中,与烟气充分混合后,进入SCR反应器,SCR反应器运行温度可在310℃~400℃范围内,SCR反应器的位置位于省煤器与空预器之间,SCR反应器进、出口均设置有温度测量点,出现310℃~400℃温度范围以外的情况时,控制系统将自动连锁报警和停止氨供给。
脱硝反应生成的水和氮气随烟气进入空气预热器。
在SCR进口设置NOX分析仪、温度监视,在SCR出口设置NOX,O2分析仪、温度监视。
SCR反应器设置吹灰器,吹扫介质为过热蒸汽,脱硝装置的吹灰器采用耙式吹灰器。
根据运行经验设定吹扫频率,一般3次/天或根据反应器里催化剂前后的压差变化情况进行控制。
脱硝装置采用液氨制备还原剂(气氨)。
氨供应系统包括液氨卸料压缩机、储氨罐、液氨泵,液氨蒸发槽、氨气吸收槽,废水池、废水泵等。
此套系统提供氨气供脱硝反应使用。
液氨的供应由液氨槽车运送,利用液氨卸料压缩机将液氨由槽车输入储氨罐内,通过重力或压力将储槽中的液氨输送到液氨蒸发槽内蒸发为氨气,经压力控制阀控制一定的压力并经脱硝自动控制系统控制其流量,然后与稀释空气在混合器中混合均匀,再送达脱硝装置中。
本工程脱硝装置的P
&
ID’S详见“SCR系统P&
I图(N02S0203(Ⅰ))”和“氨系统P&
I图(N02S0203(II))”。
4.2工艺设计原则
本项目脱硝工艺设计遵循以下原则:
1)脱硝工艺采用SCR法。
2)脱硝装置在燃用设计煤种、锅炉100%BMCR烟气条件下脱硝效率不小于50%,脱硝装置结构及相关系统按脱硝效率不小于85%规划设计,催化剂层设有一个备用层。
3)脱硝系统吹灰器采用蒸汽吹灰器。
4)脱硝反应器布置在锅炉省煤器和空预器之间。
5)吸收剂采用纯氨。
6)脱硝设备年利用小时不小于7000小时,年可用小时不小于8000小时。
7)脱硝装置可用率不小于98%。
8)脱硝装置服务寿命为30年。
9)本工程主要由两个系统组成,一个是SCR系统,另一个是还原剂供应系统,即氨供应系统,两个系统分区域布置。
SCR脱硝工艺设计考虑的主要因素包括:
烟气的温度、飞灰特性和颗粒尺寸、烟气流量、中毒反应、NOX的脱除率、烟气中SOX的浓度、压降、催化剂的结构类型和用量等。
脱硝反应一般在300~420℃范围内进行,此时催化剂活性最大,所以SCR反应器布置在锅炉省煤器与空预器之间。
在脱硝同时也有副反应发生,如SO2氧化生成SO3,在低温条件下SO3与氨反应生成NH4HSO4。
NH4HSO4会附着在催化剂或空预器冷段换热元件表面上,导致脱硝效率降低或空预器堵塞。
氨的过量和逃逸取决于NH3/NOX摩尔比、工况条件和催化剂的活性用量。
本工程氨逃逸不大于3ppm。
SO2氧化生成SO3的转化率不大于1%。
本项目设计采用蜂窝式催化剂,其特点为表面积大,体积小,机械强度大、阻力较大。
烟气的组成成分(如粉尘浓度、粉尘颗粒尺寸、碱性金属和重金属等)的含量是影响催化剂选型的主要参数。
针对长沙项目锅炉机组的实际情况,选用节距为8.2mm的蜂窝式催化剂,可以避免催化剂在运行中产生堵塞。
催化剂能够长期承受的温度不得高于430℃,短期承受的温度不得高于450℃,超过该限值,会导致催化剂烧结。
SCR脱硝系统采用的还原剂为氨(NH3),其爆炸极限(在空气中体积%)16%~25%,为保证氨(NH3)注入烟道的绝对安全以及均匀混合,需要引入稀释风,将氨浓度降低到爆炸极下限以下,本项目设计控制在5%(体积浓度)以内。
4.3主要工艺设计参数
脱硝装置主要工艺设计参数根据SCR工艺物料与能量平衡计算得出。
脱硝装置出口相关烟气参数见表4-1~4-4。
催化剂设计应满足NOX脱除率、氨的逃逸率、SO2/SO3转化率等性能保证要求。
SCR工艺还原剂耗量指标如下:
设计煤,初装50%脱硝效率时,每台机组设计最大气氨供应量为236.8k