澄清桶施工方案.docx
《澄清桶施工方案.docx》由会员分享,可在线阅读,更多相关《澄清桶施工方案.docx(25页珍藏版)》请在冰豆网上搜索。
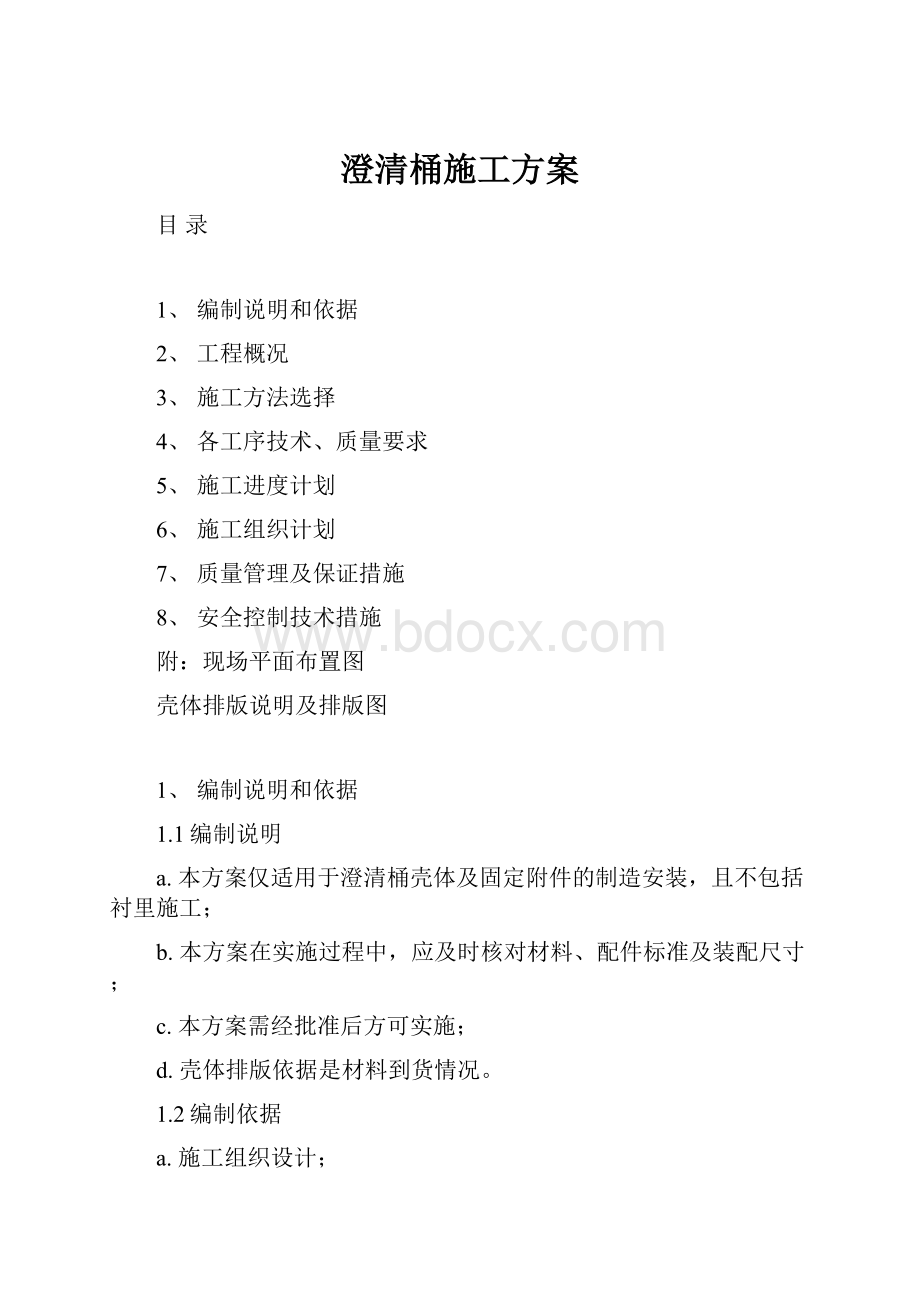
澄清桶施工方案
目录
1、编制说明和依据
2、工程概况
3、施工方法选择
4、各工序技术、质量要求
5、施工进度计划
6、施工组织计划
7、质量管理及保证措施
8、安全控制技术措施
附:
现场平面布置图
壳体排版说明及排版图
1、编制说明和依据
1.1编制说明
a.本方案仅适用于澄清桶壳体及固定附件的制造安装,且不包括衬里施工;
b.本方案在实施过程中,应及时核对材料、配件标准及装配尺寸;
c.本方案需经批准后方可实施;
d.壳体排版依据是材料到货情况。
1.2编制依据
a.施工组织设计;
b.施工图纸XN40-0726;
c.施工及验收标准JB/T4735-97,参考标准HGJ229-90;
d.我公司类似工程施工经验。
2、工程概况
2.1设备概况
该澄清桶布置在离子膜烧碱装置一次盐水区域,原有澄清桶旁边,凹锥基础上。
基础距地面高度约5.3米。
桶底为凹锥形,桶体为圆锥台形,桶盖为顶锥形,桶内装有搅拌装置。
主要内件有:
内桶体、搅拌桨、耙子、溢流箱、溢流管等。
桶体最大直径φ24.6米,总重量约153.3吨。
主体材料为Q235-A,设计压力为常压,设计温度为65℃。
工艺介质为粗盐水,容积2784m3,容器类别为类外。
桶底板厚δ=14,焊接接头形式为V型对接。
桶体板厚从下向上依次为δ=14一带;δ=12二带;δ=10三带。
桶体与底板焊接接头形式为斜型,桶体纵缝接头形式为V型对接,桶体环缝接头形式为偏V型对接。
桶底、桶体、坡口全为内坡口。
桶盖板厚δ=8,在其上面设36根[25纵向加强肋和5圈80×8的环向加强圈肋。
内桶体、溢流箱壁厚为δ=6。
设备内侧及内件表面均衬3mm厚的环氧玻璃磷片树脂。
2.2施工范围
壳体内部固定件、外部固定附件的制作安装,壳体外表面涂刷防锈漆。
2.3施工技术要求
该澄清桶的设计、制造、验收标准为JB/T4735-97;CD130A5-87。
桶壁部分对接焊缝X射线探伤率10%,合格级别TB4730-94Ⅲ级。
桶内表面焊缝高度≤3mm,且须修磨圆滑,贴角焊缝修磨圆角R≥10mm。
零件切割表面粗糙度50。
焊接材料T422焊条或相当级别的焊丝。
设备制造好后,须做充水试漏;合格后,方可进行衬里施工。
2.4工期进度要求
壳体及固定件安装施工要求在4月1日前完成。
3、施工方法的选择
根据现场条件和现有机具布置情况,拟采取在预制场制作成散件或部件,在现场基础上再进行散件或部件的组装焊接。
3.1总体施工程序及次序:
图纸会审技术交底
施工方案编制、审批
排版图的绘制审批
工装准备
技术准备
检验手段准备
班组技术交底
办理开工手续
划线切割
卷圆、加工
基础交接、复测
锥底铺设、调整
锥底焊接、
矫正
脚手架搭设
胎具安装
第一带桶壁组装
调整
第一带桶壁焊接、矫正脚手架、胎具调整
第二带桶壁组装,调整内桶体及支架就位
第二带桶壁焊接、矫正
其余桶壁组装、调整、焊接、矫正
内筒体支架找正,溢流箱、溢流管安装找正
锥顶分块预制,人孔安装
锥顶组装、调整
锥顶组合焊接、矫正
劳动保护及附件安装
外表面涂漆
内表面修磨
交付内防腐衬里及
搅拌器
充水实验
安装
带料试车
交工
3.2主要施工方法的确定:
a.下料及切割
采取逐带、逐张计算,逐张实物划线、切割,切割气—氧气。
曲线部分用手工切割,直线部分用半自动切割机切割,然后用角向磨光机磨去氧化层及疤瘤;
b.焊接
壳体焊接主要采用CO2气体保护半自动焊,单面焊双面成型,附件及零星焊缝采用手工电弧焊;
c.底板铺设
将底板分为5带,各分块下料、卷弧,在基础上散装拼接。
拼接前,靠基础一面进行手工机械除锈,手工涂漆防腐。
为保证焊接质量,在焊缝背面加垫焊接衬板—30×4扁钢;
d.底板焊接
将底板各带纵缝按一定次序焊接后,再焊接环缝。
在焊接过程中,采取留伸缩缝、刚性加固等反变形措施,确保底板的感观质量;
e.桶体壁板安装
各带壁板按排板图标注、编号,逐个放样、划线、切割、卷弧、对号组装。
第一带壁板安装前,在底板上用地规划线,焊上限位挡块;在底板外侧基础上面焊上胎具,并使之有足够的刚度和精度。
组对壁板纵缝时,用斜度样尺检查每块板的倾斜度,组成环形后,还应检查壁板与锥底中心孔的同心度。
纵缝焊完后,再组对环缝,根据组对检查数据,确定环缝的焊接次序。
第二带壁板安装时,在第一带壁板上焊接安装胎具,组对、调整,焊接次序同第一带板。
第三、四、五带壁板安装同第一、二带板壁板。
每一带壁板安装后均需检查其上口的平整度及各部位的曲率和倾斜度。
每一带壁板安装找正过程中,均采用微调装置,调整板的倾斜度;
f.桶体壁板的焊接
焊接全部采用CO2气体保护半自动焊,单面焊双面成型,壁板组对间隙最小4mm;
g.锥顶组件制作
将锥顶按径向分成16块预制,每块重量约2.5t。
在预制场制作一专用胎具。
将每块顶板放置在胎具上面,采用工装卡具,将板块周向压制成圆弧后,焊上纵环向加肋,以保持其圆弧形状及整体刚度;
h.每块锥顶板的组对
首先在平台上将δ=8板拼接成6000×11000规格,然后将其一分为二下料,即成二块顶板;
i.锥顶安装
将溢流箱安装、调整、加固处理后,方可进行锥顶分块的安装,安装时从一点开始,留一块作为调整板。
安装前,需测量桶体上口椭圆度,最好在包边角钢上划出“理想圆周线”,以便于锥顶板的调整;
j.包边角钢制作
采用钢板拼接。
角钢立面先圈弧点焊在桶体上口,平面割制成环弧,分段和立面先点焊在一起,将整个圆找好后再分段跳焊,然后将保温档圈扁钢焊在角钢外侧;
k.溢流箱口配件、槽钢环用槽钢在卷床上卷制成型;
l.吊装
根据所吊物体的轻重、远近分别租8t、16t、25t汽车吊装;
m.运输
做专用胎具放置桶体弧板,利用板车运输;
n.除锈、涂漆
用抛光轮手工机械除锈;
o.焊缝表面修磨
用角向磨光机修磨;
p.脚手架
整体采用钢管搭设,铺竹跳板。
局部脚手架采用临时挂架。
4、各工序技术、质量要求
4.1原材料
原材料必须有质量保证书,逐张检查外观,表面不得有裂纹、拉裂、折叠、夹杂、结疤、压入氧化皮、分层等缺陷。
在下料过程中,如发现以上缺陷视为不合格,须处理和更换。
钢材表面锈蚀减薄量、划痕深度与钢板实际负偏差之和应≤0.8mm。
在施工过程中须注意产品保护,以免对钢材表面造成损害,如有伤损,须进行补焊,并修磨平整。
4.2排版
根据来料之规格,放样、计算相结合,参照图纸开孔方位,绘制排版图。
在排版图上,标出0℃、90℃、180℃、270℃坐标轴线、开孔坐标位置、各张板的坐标位置及大端弧长、小端弧长、包角角度。
桶体各圈壁板(含内桶体)的纵向焊接接头宜向同一方向逐圈错开,其间距约为板长的1/3,且不得小于500mm。
底圈壁板的纵向接头与底板纵向接头之间的距离≥200mm;壁板开孔接管、补强板外缘与壁板纵向接头之间的距离≥200mm;包边角钢对接接头与壁板纵缝之间的距离≥200mm;壁板长度≥2m;底板任意相邻焊接接头之间的距离≥200mm;顶板任意拼接焊缝间距≥200mm。
具体排版情况见本方案附件—壳体排版说明及排版图。
4.3下料、切割
由于该澄清桶顶、底、体全为锥形或锥台形,所以每张板下料后均为扇形,尺寸较大,不可能采取样板下料,须逐张划线、切割,切割后的质量要求如下:
a.表面粗糙度50;
b.偏V形对接坡口、角度50±5°;
V形对接坡口角度30±2.5°;
c.坡口钝边b=0~3mm;
d.长度允差±2mm;
宽度允差±2mm;
对角线之差≤3mm;
直线度≤2mm;
曲线度≤2mm。
下料划线时,理论尺寸由计算得出,保留到0.5mm,划线后再进行复查,确保划线精度,切割用工具要求完好,操作人员要求技术水平高,对局部超差部位,可以修整的一定要修正。
底板、顶板下料时,各需一块调整板,壁板下料全部下成净料。
4.4制弧
底板、壁板卷制成弧形后,用样板检查,(扇形)射线方向用直线样板检查,其间隙不得大于1mm,曲面法线方向上用弧形样板检查,其间隙不得大于4mm(每圈板须在大端、小端各用不同样板检查)。
为保证底板、壁板瓦块的卷制精度,须在每一块板上多划出几条射线,在圈制过程中做好参照。
顶板制弧,是将单块(组焊平板)板放置在专用胎具上,用卡具压成弧形,用弧形样板检查,其间隙不得小于2mm,焊上定形板(加强肋)。
包边角钢,采用钢板割制、拼接,立面弧用滚床圈制,平面弧划线切割。
成弧后,用弧形样板检查,其间隙不得大于2mm。
槽钢圈圈制成弧后,其翘曲变形不得超过构件长度的0.1%,且不得大于4mm。
4.5组装
组装前须将构件的坡口部位清理干净,拆除组装用的卡具时,宜用角向磨光机磨削、拆除。
如对构件表面造成损伤,须按规定进行修补。
组装过程中,须采取措施,防止失稳破坏。
组装前必须对土建基础表面尺寸进行检查。
4.5.1底板铺设
底板铺设前,其下表面须涂刷防腐涂料。
每块底板边缘50mm范围内不刷。
组装时,按各块板编号对号放置。
底板采用带垫板的对接接头,垫板与对接的两块底板贴紧,其间隙不得大于1mm,对接接头间隙5~8mm。
错边量:
径向1.5mm;环向2.5mm。
为保证底板质量,各圈底板径向对接接头均应留一道作为收缩调节间隙接头。
焊接时,先焊径向焊缝,后焊环向焊缝。
在焊接过程中采取反变形措施。
4.5.2壁板组装
壁板组装前,须在底板上划出圆周线,并对该圆周线的水平度进行复查,调整至误差≤6mm。
对各块壁板进行尺寸外形复验。
需重新校正时,应防止出现锤痕。
底圈壁板,相邻两块壁板上口的水平允差不大于2mm;在整个圆周上任意两点的水平允许偏差不应大于6mm;壁板射线的向外倾斜度允许偏差不大于3mm;组装焊接以后,在底圈壁板1m高处内表面任意点半径的允许偏差为±19mm。
其它各圈壁板的射线向外倾斜度允许偏差不大于该圈壁板高度的0.3%。
壁板对接接头的间隙:
采用手工电弧焊时0~3mm;
采用CO2气体保护半自动焊时4~8mm。
壁板内表面应齐平,纵向接头的错边量为板厚的1/10;环向接头的错边量为板厚的1/5。
壁板焊接时,先焊纵缝,调整施放应力后再组焊环缝。
焊接后壁板接头处角变形用1m长的样板检查应小于10mm;壁板的局部凹凸变形≤13mm。
包边角钢组装后,用样板检查其弧度;用尺子检查任意一点的半径,允许偏差±19mm。
4.5.3顶板组装
顶板组装前,须将内件安装完毕,溢流箱经加固可靠,足以承受安装顶板的偏心载荷;在圆周上及溢流箱槽钢圈上,对应划出等分线。
安装时,从一点开始,块与块之间对接间隙4~8mm,对接接头下部放陶瓷衬垫,焊接采用CO2气体保护半自动焊。
4.5.4开孔
开孔接管的中心位置偏差不大于10mm;开孔补强板的曲率与桶体曲率一致;开孔接管法兰的密封面应平整,不得有焊瘤和划痕,法兰的螺栓孔应跨中安装。
4.6焊接
4.6.1焊接方法
主要对接焊缝、大面积贴角焊缝,采用CO2气体保护半自动焊,零星焊接采用手工电弧焊。
4.6.2焊接材料
CO2气体保护焊:
采用ER49-1φ1.2焊丝;CO2气体纯度99.5%以上。
手工电弧焊:
采用J422焊条φ3.2~φ4.0
4.6.3焊接工艺参数
焊接前下达焊接工艺卡。
4.6.4主要部位的焊接顺序
a.底板焊接:
先焊径向焊缝,后焊环向焊缝,径向收缩接头的第一层焊接,应采用分段退焊或跳焊法;
b.底板与壁板连接的角焊接头,应在底圈壁板纵焊接头焊完后施焊,并由数对焊工分别从内外两侧沿同一方向分段焊接,初层焊道应采用分段退焊或跳焊法;
c.壁板焊接:
先焊纵向接头,后焊环向接头,焊环缝时焊工应均匀分布,并沿同一方向施焊;
d.顶板焊接:
径向长焊道采用间隔焊对称施焊方法,并由中心向外分段退焊;
e.焊接顶板与包边角钢时,焊工应对称均匀分布,并沿同一方向分段退焊。
4.6.5焊接质量检验
a.焊接接头的表面及热影响区,不得有裂纹,气孔、夹渣和弧坑等缺陷,对接焊接接头的咬边深度,不得大于0.5mm,咬边的连续长度不得大于100mm,接头两侧咬边的总长度不得超过该接头长度的10%;
b.桶壁纵向对接接头不得有低于母材表面的凹陷,其余对接接头底于母材表面的凹陷深度不得大于0.5mm,凹陷的连续长度不得大于10mm,凹陷的总长度不得大于该接头的总长度的10%;
c.焊接接头宽度应按坡口宽度两侧各增加1~2mm确定;
d.对接接头的错边量:
纵向接头≤0.1δ,环向接头≤0.2δ;
e.桶壁对接接头作X射线探伤抽查,抽查率10%,合格级别JB/T4730Ⅲ级。
4.7总体形状和尺寸检查
4.7.1几何形状和尺寸,应符合下列规定:
a.桶壁高度允差,应不大于设计高度的0.5%;
b.桶壁向外倾斜度允许偏差不应大于壁高的0.4%;
c.桶壁的局部凹凸变形不应大于13mm;
d.底圈壁板内表面直径的允许偏差,不应大于±19mm;
e.桶底局部凹凸变形的深度不应大于变形长度的2%,且≤10mm。
4.7.2内表面处理
a.壳体上的工卡具焊迹应清除干净,焊疤应打磨平滑;
b.焊缝表面及其与母材交界边缘应打磨平滑;
c.内贴角焊缝修磨圆角R≥10mm;
d.内件焊接棱角修磨圆角R≥10mm。
4.8总体充水实验
4.8.1充水前的条件
a.各项检查合格,所有焊接工作结束;
b.各项准备工作就绪,水质清洁、无杂质。
4.8.2检查项目
a.桶体试漏;
b.基础沉降观测。
4.8.3试验步骤
a.桶底、桶壁上管口封闭,测量基础标高(设4个观测点);
b.拆充水阀门:
将水充至1/3设计高度处,停止充水,稳定2小时,测量基础标高,检查桶底、桶壁有无渗漏。
若有渗漏应立即放水,处理后,方可继续充水;
c.当充水至设计高度2/3时,停止充水,稳定2小时,检查合格后继续充水至设计高度,保持48小时,桶体无渗漏及异常变形即为合格。
5、施工进度计划
甲方要求最终交付下道工序施工日期为4月1日,且不得推迟。
为此,作出施工总体进度计划如下:
项目
2月
3月
1~7
8~14
15~21
22~29
1~7
8~14
15~21
22~31
进场准备
底板预制
壁板预制
桶盖预制
内件附件预制
现场布置
底板铺设焊接
外脚手架搭设
壁板组焊
内件安装
桶盖安装组焊
外附件安装
内表面修磨拆架子
充水试漏
交付下道工序
4月1日
6、施工资源组织计划
6.1管理人员计划及名单
项目负责施工员:
谭东海王晓晨
质检员:
孔金荣
工业卫生、安全、保卫:
李金方
后勤、材料、预算:
于丛福
焊接工程师:
朱新建
6.2施工操作人员计划
铆工:
8人
电焊:
8人
起重:
5人
气焊:
4人
油工:
2人
6.3主要械具动员计划
CO2气体保护半自动焊机4台
晶闸管整流焊机4台
交流焊机4台
半自动切割机2台
空气压缩机1台
汽车吊2台租赁
板车1辆租借
倒链5t2只
3t4只
千斤顶16t4只
30t2只
7、质量管理及保证措施
7.1质量管理
设置专职质检员,班组设兼职质检员,施工人员对自己负责的工序、工步均须进行自检。
施工前进行技术、质量交底,使人人都熟悉质量标准、技术要求,掌握操作要领。
时常对施工人员进行质量意识教育,贯彻“追求完美,为用户提供期望的工程和服务”这一质量方针。
执行质量否决制度,当发现施工质量不符合设计或规范要求时,须及时整改,否则不得进入下道工序。
施工员认真做好施工记录,操作人员认真做好标识记录,记录必须与施工同步,必须完整、准确、及时。
对各施工工序,根据工序性质不同,制定三级质量控制点,制订工序质量检查制度,建立工序质量检查台帐。
各工序质量控制表如下:
序号
工序名称
检查等级
1
施工方案、技术准备
B
2
材料交底、验收
B
3
基础交接
BR
4
基础复查
C
5
排版
B
6
划线
C
7
切割
C
8
制弧
C
9
底板铺设
B
10
底板焊接
BR
11
壁板组装
B
12
壁板焊接
BR
13
内部附件制安
C
14
盖板制作
C
15
盖板安装
C
16
内表面处理
B
17
最终尺寸、形状检查
BR
18
充水试漏
AR
19
外防涂漆
CR
20
交付下道工序
BR
注:
A级:
业主、监理、承包三方检查确认
B级:
承包方、监理方质量控制人员检查确认
C级:
施工单位自行检查
R:
提交检查记录
7.2质量保证措施
a.在人员组织方面,挑选技术过硬、经验丰富、质量意识强的骨干力量从事施工;同时强化质量教育,实行质量责任制,质量经济挂钩,以质量体现真正的进度,体现真正的劳动成果;
b.在使用工机具方面,配备性能优越、状态完好的施工机具,真正体现到“欲善其工,必利其器”。
在施工过程中,对机具设备进行维护保养,使之经常处于良好的状态;
c.对所用材料,求全责备,优中选优,杜绝使用低劣材料、可疑材料;
d.在施工方案、施工工艺上,选择易保证质量的方法和工艺,制定出完整的施工工序,对各工序均制定出质量要求,采取相应的检测手段。
在焊接方面,主要焊缝采用CO2气体保护半自动焊,确保焊接接头的内在质量;
e.创造保证工程质量的良好环境和气氛,为提高工程质量造就可靠的操作条件。
例如,脚手架、劳动保护、环境卫生等等;
f.开展质量竞赛活动,兑现质量奖惩制度。
对施工质量一向优良的班组和个人实行奖励,评选质量标兵,对质量较差的班组和个人,责令其限时整改,如确实不能胜任该工程施工的个人责令其下岗。
8、安全控制技术措施
8.1安全管理规定
a)认真执行国家和氯碱厂有关安全生产的规定和公司《安全生产手册》;
b)工程开工前,技术人员向全体施工人员进行安全技术交底,安全员向施工人员强化安全技术教育,并做好记录;
c)进入施工现场的所有人员都应穿戴工作服、安全帽,各专业工种应按规定佩戴劳保用品,登高作业佩戴安全带;不得从高处向下扔物;
d)起重、电工、焊工等特种作业人员必须持证上岗;
e)现场须与原装置生产设施加以隔离,施工人员不得进入原装置内;
f)施工用电须由维修电工巡视和维护,用电线路布置规范、整齐,对用电设备施行专机专控,并配备漏电保护装置;
g)施工脚手架搭设须保证足够的稳定性,并做到整齐、美观,脚手架搭设后,必须经安全部门检查合格方能投入使用;
h)现场动火必须办理动火证,做到“四不动火”;
i)在施工过程中,坚持班前安全例会制度,坚持安全周会制度。
安全员、施工员时刻监督,一经发现安全违规现象,立即制止。
8.2安全技术措施
a.施工用电设施、电动工器具,必须有可靠的接地或接零保护,并经常检查、维护,以确保用电设备的安全可靠;
b.吊装作业时,专人指挥,吊车打腿牢固可靠,吊臂下面严禁站人,使用绳索、卡具时常检查,一经发现不安全现象,立即作报废处理;
c.对使用的工具、小型机具如:
倒链、千斤顶等,要进行安全检查,确认可靠后,方可使用。
对临时制作的受力构件吊耳、挂钩等,均应进行安全确认;
d.在容器内施工时,使用12V安全照明,以防触电;在桶内进行焊接、打磨时,应装通风设施,实现强制通风;
e.风力大于五级以上时,严禁吊装作业;
f.现场配置灭火器材;
g.现场通道保持畅通,如需临时占据通道时,应报有关管理部门批准后,方可在规定的时间内占据,过时立即保持其畅通。
附:
澄清桶壳体排版说明
澄清桶壳体排版是根据来料规格,本着节约用料,尽可能地减少消耗,降低成本。
1、桶底排版
桶底形状为一凹圆锥形,设计板厚δ=14,排料尺寸按中径计算如图:
锥底直径φ16086,锥高3410,底角22.976°,小直径φ866。
展开形状为一环扇形,大端半径R=8736,
小端半径r=470,展开包角331.4423°,φ16086
展开射线宽度8266。
现来料规格
2000×8000板2张,其余均为22.976°
2000×9000以上,需按5带排3410
料,从大端向小端开始排。
为φ866
节约用料,保证单带板的有效
宽度,将整板在长度方向从中
斜着割开,作为两块使用。
1.1第一带:
11块,单块大端弧长4594,每块包角30.1311°,大端半径8736,大端弧长4541.4mm,弦高300.3mm,有效宽度1750;小端半径6986,小端弦长3632,弦高240。
使用板2000×9100以上板5.5张。
1.2第二带:
9块,其中8块包角38°,1块包角27.4423°,有效宽度1710。
1.2.1包角38°的8块,大端半径R6986,大端弦长4549,弧长4633,大端弦高381;小端半径5276,小端弦长3435.4,弧长3499,小端弦高287.4。
1.2.2包角27.4423°的1块,大端弦长3314,弧长3346,大端弦高199.4,小端弦长2503,弧长2527,小端弦高150.6。
1.2.3第二带共用2000×9100以上板4张,2000×3500板1张。
1.3第三带6块,每块包角55.24°,大端半径5276,小端半径3711,有效宽度1565;大端弦长4892,弧长5087,大端弦高601,小端弦长3411,弧长3578;小端弦高423。
第三带共需2000×9200以上板3张。
1.4第四带5块,每块包角66.288°。
大端半径3711,小端半径2061,有效宽度1650,大端弦长4058,弧长4293,大端弦高604;小端弦长2254,弧长2384.5,小端弦高335.3。
第四带板共需2000×8000板2张,另2000×