工艺学作业答案1Word格式文档下载.docx
《工艺学作业答案1Word格式文档下载.docx》由会员分享,可在线阅读,更多相关《工艺学作业答案1Word格式文档下载.docx(22页珍藏版)》请在冰豆网上搜索。
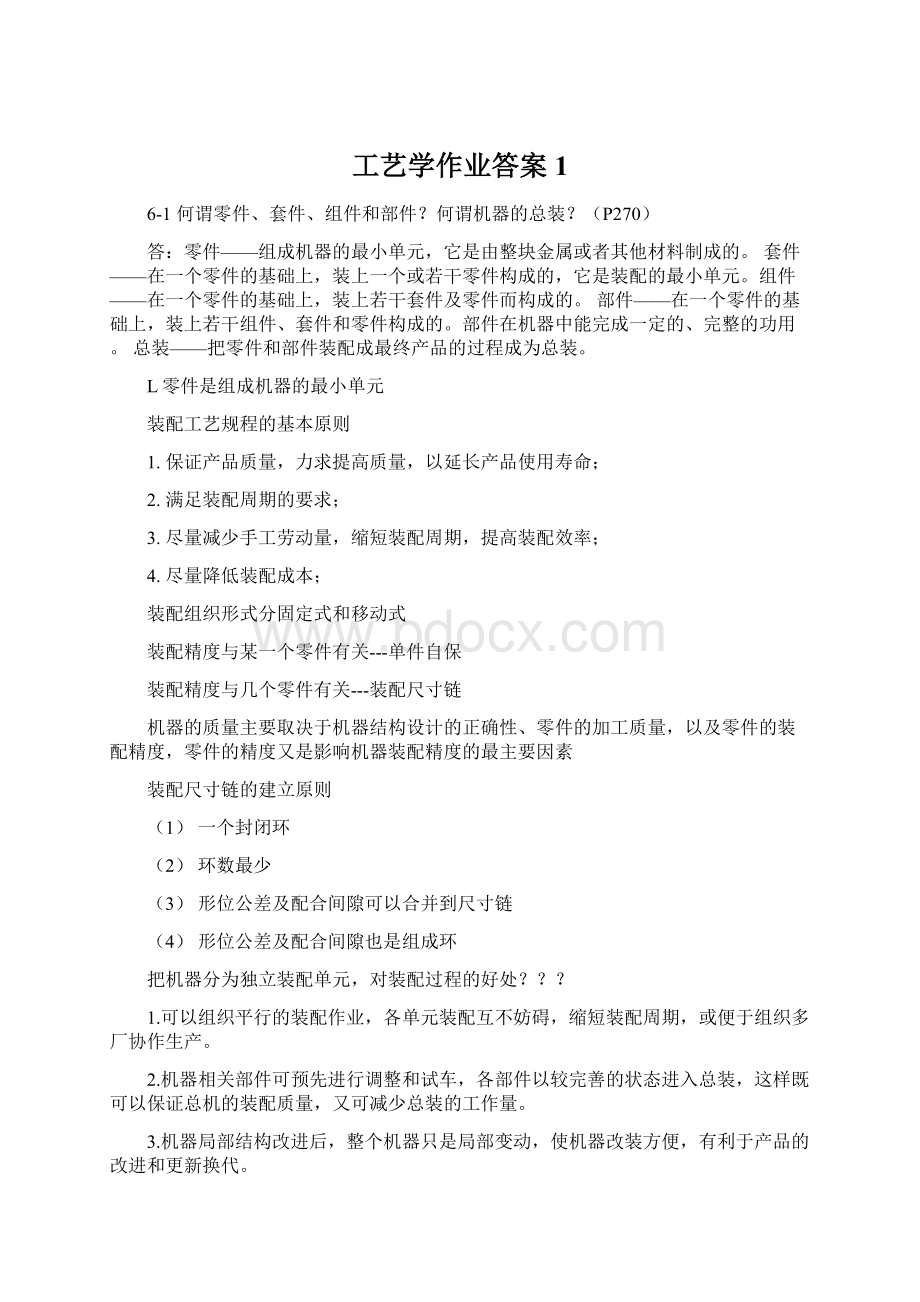
把机器分为独立装配单元,对装配过程的好处?
?
1.可以组织平行的装配作业,各单元装配互不妨碍,缩短装配周期,或便于组织多厂协作生产。
2.机器相关部件可预先进行调整和试车,各部件以较完善的状态进入总装,这样既可以保证总机的装配质量,又可减少总装的工作量。
3.机器局部结构改进后,整个机器只是局部变动,使机器改装方便,有利于产品的改进和更新换代。
4.有利于机器的维护检修,使重型机器的包装、运输带来便利
6-2装配工艺规程包括哪些主要内容?
经过哪些步骤制定的?
(P271-272)
装配工艺规程的主要内容:
1)分析产品图样,划分装配单元,确定装配方法;
2)拟定装配顺序,划分装配工序;
3)计算装配时间定额;
4)确定各工序装配技术要求、质量检查方法和检验工具;
5)确定装配时零、部件的输送方法及所需的设备和工具;
6)选择和设计装配过程中所需的工具、夹具和专用设备。
制定装配工艺规程的步骤:
(1)研究产品的装配图及验收技术条件;
(2)确定装配方法与组织形式;
(3)划分装配单元,确定装配顺序;
(4)划分装配工序;
(5)编制装配工艺文件。
6-6保证装配精度的方法有哪几种?
各适用于什么装配场合?
(P281-298)
保证产品装配精度的方法有:
互换装配法、选择装配法、修配装配法和调整装配法。
互换装配法——是在装配过程中,零件互换后仍能达到装配精度要求的装配方法。
根据互换程度不同,互换装配法又可分为完全互换法和大数互换法。
完全互换法常用于高精度的少环尺寸链或低精度多环尺寸链的大批大量生产装配中。
大数互换法适用于大批大量生产,组成环较多、装配精度要求又较高的场合。
选择装配法——是将尺寸链中组成环的公差放大到经济可行的程度,然后选择合适的零件进行装配,以保证装配精度的要求。
选择装配法装配方法常应用于装配精度要求高而组成环数又较少的成批或大批量生产中。
选择装配法有三种形式:
直接选配法不能用于生产节拍要求较严的大批大量流水作业中;
分组装配法应用于在大批大量生产中对于组成环数少而装配精度要求又高的部件;
复合选配法应用于配合件公差可以不等,装配速度较快、质量高、有一定生产节拍的要求的场合。
修配装配法——是将尺寸链中各组成环按经济加工精度制造,装配时,通过改变尺寸链中某一预先确定的组成环尺寸的方法来保证装配精度。
装配时进行修配的零件叫修配件,该组成环称为补偿环(或者修配环),该组成环的修配是为补偿其他组成环的累积误差以保证装配精度。
常见的修配方法为三种:
(1)单件修配法;
(2)合并加工修配法;
(3)自身加工修配法。
采用这种方法,补偿环满足要求
(1)便于装拆,零件形状比较简单,易于修配
(2)不应为公共环,选不进行表面处理的零件
调整装配法——在装配时,用改变产品中可调整零件的相对位置或选用合适的调整件以达到装配精度的方法称为调整装配法。
常见的调整方法有固定调整法、可动调整法、误差抵消调整法三种。
固定调整法多用于大批大量生产中;
可动调整法应用于由于磨损、热变形所引起的误差的场合,应用广泛,误差抵消调整法应用于装配精度要求很高的机械设备。
6-7说明装配尺寸链中的组成环、封闭环、协调环、补偿环和公共环的含
义,各有何特点?
在装配关系中,对装配精度有直接影响的零、部件的尺寸和位置关系,都是装配尺寸链的组成环。
装配尺寸链的封闭环就是装配所要保证的装配精度或技术要求。
装配精度(封闭环)是零部件装配后才最后形成的尺寸或位置关系。
显然,当各组成环都按上述原则确定其公差时,按式(5.2)计算公差累积值常不符合封闭环的要求。
因此,常选一个组成环,其公差与分布需经计算后最后确定,以便与其他组成环相协调,最后满足封闭环的精度要求。
这个事先选定的在尺寸链中起协调作用的组成环,称为协调环。
不能选取标准件或公共环为协调环,因为其公差和极限偏差已是确定值。
可选取易加工的零件为协调环,而将难加工零件的尺寸公差从宽选取;
也可选取难加工零件为协调环,而将易于加工的零件的尺寸公差从严选取。
修配法是将尺寸链中各组成环按经济加工精度制造。
装配时,通过改变尺寸链中某一预先确定的组成环尺寸的方法来保证装配精度。
装配时进行修配的零件叫修配件,该组成环称为修配环。
由于这一组成环的修配是为补偿其他组成环的累积误差以保证装配精度,故又称补偿环。
公共环是在并联尺寸链中出现的。
由于这个环(或几个环),使得两个以上尺寸链而相互联系起来形成并联尺寸链这些环属于不同尺寸链的共有环称为公共环、公共环可以是各个尺寸链的组成环,也可以在一个尺寸链中是封闭环,而在另一个尺寸链则是组成环。
6-10现有一轴、孔配合,配合间隙要求为0.04~0.26mm,已知轴的尺寸6-10现有一轴、孔配合,配合间隙要求为0.04~0.26mm,已知轴的尺寸为00.150mm,孔的尺寸为0.2050mm。
若用完全互换法进行装配,能否保证装配精度要求?
用大数互换法装配能否保证装配精度要求?
加工表面的几何形貌(表面结构)包括表面粗糙度、表面波纹度、纹理方向和表面缺陷等。
由于机械加工中力因素和热因素的综合作用,加工表面的物理力学性能的变化:
1表面层因塑性变形引起的加工硬化(冷作硬化);
2.表面层因力或热的作用产生的残余应力;
3.表面层因切削热或磨削热的作用引起的金相组织变化;
加工表面质量对零件使用性能的影响:
1,表面质量对耐磨性的影响
2,表面质量对耐疲劳性的影响
3.表面质量对耐蚀性的影响
4,表面质量对零件配合质量的影响
影响切削残留面积高度的因素主要包括刀尖圆角半径,主偏角,副偏角及进给量
较少磨削烧伤的途径:
正确选择砂轮合理选择磨削用量改善冷却条件选用开槽砂轮
表面层的残余应力的原因
冷态塑性变形在切削力的作用下,已加工面受后刀面的挤压,使晶格扭曲,表层金属比容积增大,体积膨胀,而内层金属又阻止其伸长。
故加工后表面层残余应力为压应力(-),里层为拉应力(+)。
热态塑性变形在切削热的作用下,已加工面产生热膨胀,此时表层产生热压应力。
加工后,表层已产生的热塑性变形收缩受到内层金属的阻碍。
故加工后表面层残余应力为拉应力(+),里层为压应力(-)。
局部金相组织变化不同的金相组织有不同的密度,如ρM=7.75g/cm3ρA=7.96g/cm3、ρP=7.78g/cm3、ρF=7.88g/cm3当金相组织变化时,由于密度不同,体积会发生变化。
如果表层金属膨胀则残余应力为压应力(-),反之,如果表层金属体积缩小则产生残余拉应力(+)。
5-2为什么机器零件一般总是从表面层开始破坏的?
加工表面质量对机器使用性能有哪些影响?
(P231)
(1)由于表面是零件材料的边界,常常承受工作负荷所引起的最大应力和外界介质的侵蚀,表面上有着引起应力集中而导致破坏的微小缺陷,所以这些表面直接与机器零件的使用性能有关。
(2)加工表面质量对机器的耐磨性、耐疲劳性、耐蚀性、零件配合质量都有影响。
5-3车削一铸铁零件的外圆表面,若进给量f=0.40mm/r,车刀刀尖圆弧半径re=3mm,试估算车削后的表面粗糙度。
5-6为什么提高砂轮速度能减小磨削表面的粗糙度数值,而提高工件速度却得到相反的结果?
(P224)砂轮速度越高,单位时间内通过被磨表面的磨粒数就越多,工件材料来不及变形,因而工件表面粗糙度值越小。
而工件速度增大,单位时间内通过被磨表面的磨粒数减少,塑性变形增加,表面粗糙度值将增大。
5-7为什么在切削加工中一般都会产生冷作硬化现象?
答:
(P240)机械加工过程中产生的塑性变形,使晶格扭曲、畸变,晶粒间产生滑移,晶粒被拉长,进一步变形受到阻碍,这些都会使表面层金属的硬度增加,统称为冷作硬化(或称为强化)。
磨削烧伤:
对于已淬火的钢件,很高的磨削温度往往会使表层金属的金相组织产生变化,使表层金属硬度下降,使工件表面呈现氧化膜颜色
磨削烧伤包括回火烧伤、淬火烧伤、退火
5-11什么是回火烧伤、淬火烧伤和退火烧伤?
(P243)磨削淬火钢时,在工件表面形成的瞬时高温将使表层金属产生以下三种金相组织变化:
1)如果磨削区的温度未超过淬火钢的相变温度(碳钢的相变温度为720℃,但已超过马氏体的转变温度(中碳钢为300℃,工件表面金属的马氏体将转化为硬度较低的回火组织(索氏体或托氏体),这称为回火烧伤。
2)如果磨削区温度超过了相变温度,再加上冷却液的急冷作用,表层金属会出现二次淬火马氏体织织,硬度比原来的回火马氏体高;
在它的下层,因冷却较慢,出现了硬度比原来的回火马氏体低的回火组织(索氏体或托氏体),这称为淬火烧伤。
3)如果磨削区温度超过了相变温度,而磨削过程又没有冷却液,组织,表层金属的硬度将急剧下降,这称为退火烧伤。
1-6什么是机械加工工艺过程?
什么是机械加工工艺系统?
机械加工工艺过程:
对零件采用各种加工方法,以改变生产对象的形状‘尺寸’表面粗糙度和力学性能,成为合格零件的生产过程。
机械加工工艺系统是零件进行机械加工时,必须具备一定的条件,即要有一个系统来支持。
通常,一个系统是由物质分系统、能量分系统和信息分系统所组成。
机械产品生产过程是指将原材料转变成机械产品的全部劳动过程
1-7什么是工序、安装、工位、工步和走刀?
1.工序:
一个(或一组)工人在一个工作地点对一个(或同时对JL个)工件连续完成的那一部分工艺过程。
2.安装:
如果在一个工序中需要对工件进行几次装夹,则每次装夹下完成的那部分工序内容称为一个安装。
3.工位:
在工件的一次安装中,通过分度(或移位)装置,使工件相对于机床床身变换加工置,则把每一个加工位置上的安装内容称为工位。
4.工步:
加工表面、切削刀具、切削速度和进给量都不变的情况下所完成的工位内容,称为一个工步。
5.走刀:
切削刀具在加工表面上切削一次所完成的工步内容,称为一次走刀。
计划期为一年的生产纲领称为年生产纲领。
生产类型可分为大量生产、成批成产和单件生产。
装夹为定位和夹紧。
定位是指确定工件在机床(工作台)上或夹具中占有正确位置的过程
夹紧是指工件在定位后将其固定,使其在加工过程中能承受重力、切削力等而保持定位位置不变的操作
夹具的装夹类型:
1:
夹具中装夹,易于保证加工精度要求,操作简单方便,效率高,应用于成批、大批和大量生产中
2:
直接找正装夹,找正效率低、精度高。
应用场合:
小批量或精度要求很高的生产。
3:
划线找正装夹,特点:
不用专门设备,通用性好,但生产率及精度低。
应用场合:
单件、中小批生产的复杂铸件或铸件精度低时
1-8某机床厂年产CA6140车床2000台,已知机床主轴的备品率为14%,机械加工废品率为4%,试计算机床主轴的年生产纲领并说明属于何种生产类型,工艺过程有何特点?
若一年工作日为282天,试计算每月(按26天计算)的生产批量。
(1)机床主轴的年生产纲领N=Qn(1+%+%)=20001(1+14%+4%)=2360ab´
´
台机床主轴属于中型机械,查表属于大批生产的生产类型。
(2)工艺过程特点a)采用模锻制造毛坯,毛坯精度高,加工余量小。
b)采用专用机械加工设备流水线生产c)采用专用工装d)采用详细的工艺规程,用工序卡、操作卡及调整卡管理生产。
(3)生产批量n¢
=NA/F=2360*26/282=217.589台
1-10何谓六点定位原理?
何谓完全定位和不完全定位?
何谓欠定位和过定位?
试举例说明之。
六点定位原理:
采用6个按一定规则布置的约束点来限制工件的6个自由度,实现完全定位,称之为六点定位原理。
完全定位:
限制了6个自由度。
不完全定位:
仅限制了1—5个自由度。
欠定位:
在加工时根据被加工面的尺寸、形状和位置要求,应限制的自由度未被限制,即约束点不足,这样的情况称为欠定位。
过定位:
工件定位时,一个自由度同时被两个或两个以上的约束点(夹具定位元件)所限制,称为过定位,或重复定位,也称之为定位干涉。
1-13何谓基准?
基准分哪几种?
各种基准之间有何关系?
基准是用来确定生产对象上几何要素之间的几何关系所依据的那些点,线或面。
基准的分类:
从设计和工艺两个方面看基准,可把基准分为两大类,即设计基准和工艺基准。
在设计图上标注尺寸的起始位置称为设计基准。
零件在加工工艺过程中所采用的基准称为工艺基准。
工艺基准又可进一步分为:
工序基准,定位基准,测量基准和装配基准。
基准之间的关系:
在设计工序基准时,应首先考虑用设计基准为工序基准;
工序基准应尽可能与定位基准和测量基准重合
机械加工工艺规程是规定产品或零部件机械加工工艺过程和操作方法等的工艺文件,是一切有关生产人员都应严格执行、认真贯彻的纪律性文件。
不得随意变更。
机械加工工艺规程的作用:
1,根据机械加工工艺规程进行生产准备
2,机械加工工艺规程是生产计划、调度,工人的操作、质量检查等的依据
3,新建或扩建车间依据为机械加工工艺规程
常用的毛坯种类有铸件、锻件、焊接件、冲压件、型材等。
设计机械工艺规程遵循的原则
1,可靠地保证零件图上所有的技术要求的实现
2,必须能满足生产纲领的要求
3在满足技术要求和生产纲领要求的前提下,一般要求工艺成本最低
4,尽量减轻工人的劳动强度,确保生产安全
选用毛面为基准称为粗基准,选已加工的面为定位基准,称为精基准
粗基准的选择原则:
1保证相互位置要求2,保证加工面加工余量合理分配
3,便于工件装夹4,粗基准一般不得重复使用
精基准的选择原则1,基准重合原则(尽可能选择被加工面的设计基准为精基准)
2,统一基准原则*(当工件以某一表面作精基准定位,可以方便地加工大多数(或全部)其余表面时,应尽早将这个基准面加工出来,并达到一定精度,以后大多数(或全部)工序均以它为精基准进行加工。
)
3,互为基准原则(某些位置精度要求很高的表面,常采用互为基准反复加工的方法来达到位置度要求。
)
4,自为基准原则(为减少表面粗糙度、减少加工余量和保持加工余量均匀的工序,常以加工面本身作为基准进行加工。
床身导轨面磨削加工)
5,便于装夹原则(所选择的精基准,应能保证工件定位准确、可靠,并尽可能使夹具结构简单、操作方便)
加工经济精度是指在正常加工条件下所能保证的加工精度和表面粗糙度
工艺顺序的安排原则:
1,先加个基准面,再加工其他面
2,一般情况下,先加工平面,后加工空
3,先加工主要表面,后加工次要表面
4,先安排粗加工工序,后安排精加工工序
工序集中:
是使每个工序中包括尽可能多的工步内容,因而使总的工序数目减少,夹具的数目和工件的安装次数也相应的减少。
有利于保证各加工面间的相互位置精度要求,有利于采用高生产率机床,节省装夹工件的时间,减少工件的搬动次数。
工序分散:
是将工艺路线中的工步内容分散在更多的工序中去完成,因此工序工步少,工艺路线长。
可使每个工序中使用的设备和夹具比较简单,调整、对刀比较容易,对操作工人的技术水平要求较低。
工艺过程分为粗加工阶段、半精加工阶段、精加工阶段、精密、光整加工阶段
加工余量为切除金属层厚度
加工余量使加工表面达到所需的精度和表面质量而应切除的金属层
机械加工精度是指零件加工后的实际几何参数与理想几何参数的符合程度
加工误差是指加工后零件的实际几何参数对理想几何参数的偏离程度
零件加工精度为尺寸精度、形状精度、位置精度
工艺系统是指在机械加工时,机床、夹具、刀具和工件就构成了一个完整的系统
对加工精度影响最大的方向(即通过切削刃的加工表面的法向)称为误差的敏感方向
主轴回转误差,指主轴实际回转轴线对其理想回转轴线的漂移
主轴回转轴线的运动误差分为径向圆跳动、轴向圆跳动和倾角摆动
短而粗的工件变形后为马鞍形
细长轴的变形为鼓形
误差复映:
工件上原有的形状误差,在加工上的零件上仍然会出现的误差,在数值上回减少。
在顺序加工一批工件中,其加工误差的大小和方向都保持不变为常值系统误差,按一定规律变化,称为变直系统误差
4-8设已知一工艺系统的误差赴映系数为0.25,工件在本工序前有圆度误差
0.45mm,若本工序形状精度规定允许差0.01,问至少进给几次方能使形状精度
合格?
△Q=∑△m∑=c/r为常数设需要进给N次
∑总=∑△m≤0.01n≥3