表面组装技术现状与展望0702班刘辉小组Word下载.docx
《表面组装技术现状与展望0702班刘辉小组Word下载.docx》由会员分享,可在线阅读,更多相关《表面组装技术现状与展望0702班刘辉小组Word下载.docx(23页珍藏版)》请在冰豆网上搜索。
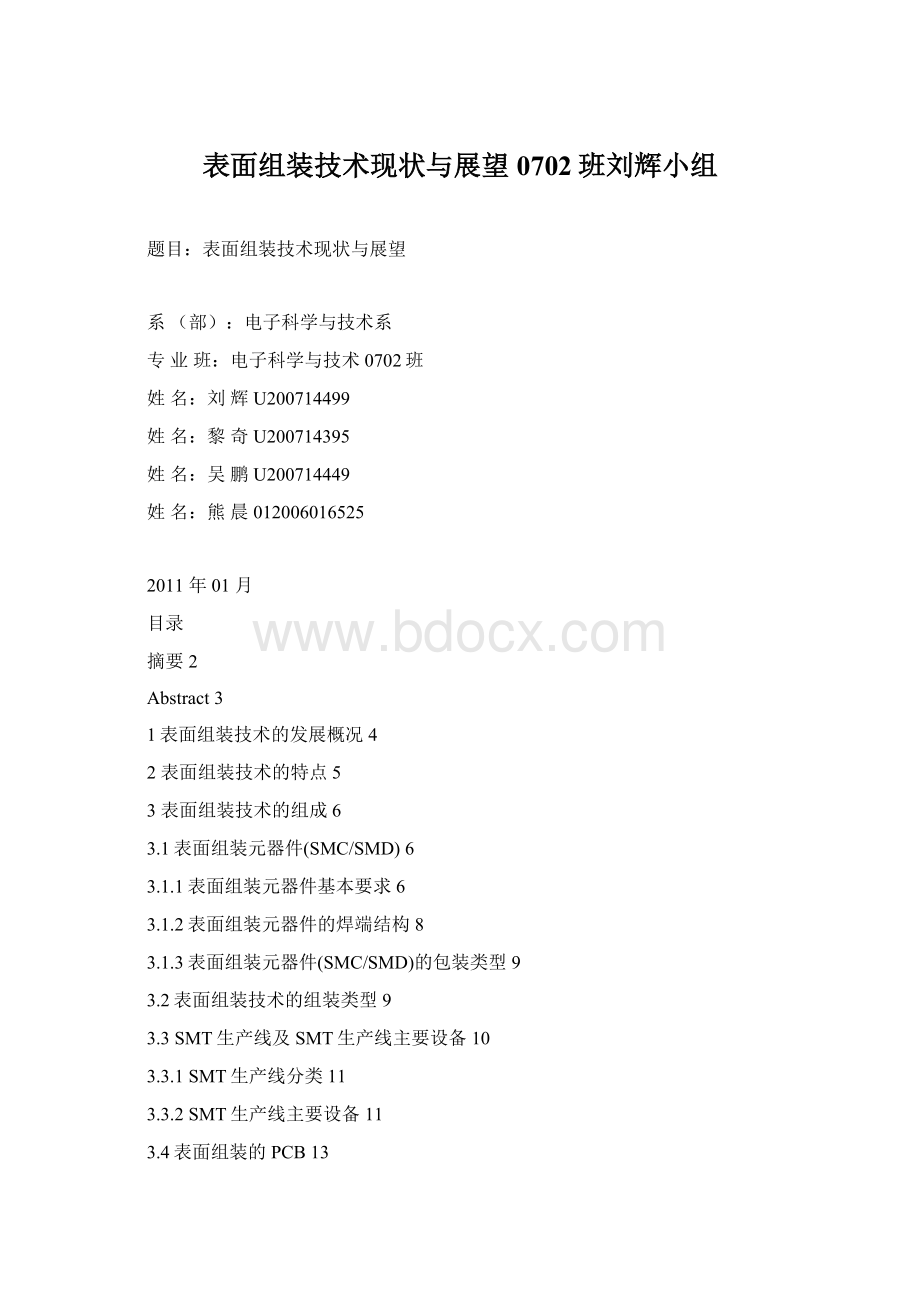
摘要
表面组装技术自20世纪80年代以来以在电子工业中得到了广泛应用和发展,本文主要对表面组装技术的特点、表面组装工艺和表面组装技术的现状及发展趋势进行了全面的介绍。
关键词:
表面组装技术;
印制电路板;
贴片机;
网板印刷机;
回流焊;
波峰焊
Abstract
SurfaceMountTechnologyhasbeendevelopedquicklyandgotwideapplicationinelectronicindustrysince1980,ThispaperintroducesthefeatureoftheSurfaceMountTechnology,theSurfaceMountProcessandthedevelopmentofSurfaceMountTechnology.
Keywords:
surfacemounttechnology;
printedcircuitboard;
chipshooter;
Screenprinter;
reflowsoldering;
wavesoldering
1表面组装技术的发展概况
表面组装技术是从厚、薄膜混合电路演变发展起来的。
美国是世界上SMD与SMT最早起源国家,并一直重视在此类电子产品的投资。
在军事装备领域,表面组装技术发挥了高组装密度和高可靠性能方面的优势。
组装技术经历了以下几个发展阶段:
手工阶段(20世纪50年代);
半自动插装浸焊(20世纪60年代);
全自动插装波峰焊(20世纪70年代);
全自动表面组装技术(SMT)(20世纪80年代);
窄间距SMT和超窄间距SMT(20世纪90年代)。
日本在70年代从美国引进SMD和SMT应用在消费类电子产品领域,并投入巨资大力加强基础材料、基础技术和推广应用方面的开发研究工作。
从80年代中后期起加速了SMT在电子设备领域中的全面推广应用,仅用了四年时间使SMT在计算机和通信设备中的应用数量增长了近30%,在传真机中增长40%,使日本很快超过了美国,在SMT方面处于世界领先地位。
欧洲各国SMT的起步较晚,但他们有较好的工业基础,发展速度十分迅速,其技术水平和整机中SMC/SMD的使用率仅次于日本和美国。
80年代以来,新加坡、韩国、香港和台湾省亚洲四小龙不惜投入巨资,纷纷引进先进技术,使SMT的中端产品获得较快的发展。
我国SMT的应用起步于80年代初期,最初从美、日等国成套引进了SMT生产线用于彩电调谐器生产。
随后应用于录像机、摄像机及袖珍式高档多波段收音机、随身听等产品生产中,近几年在计算机、通信设备、航空航天电子产品中也逐渐得到应用。
据2000年不完全统计,全国约有40多家企业从事SMC/SMD的生产,全国约有300多家引进了SMT生产线,上万个产品不同程度地采用了SMT。
到2000年全国引进4000~5000台贴装机。
随着改革开放的深入以及加入WTO,近两年一些美、日、新加坡、台商已经将SMT加工厂搬到了中国。
例如英国DEK公司和日本日立公司分别在深圳和南京生产印刷机;
美国HELLER、BTU公司在上海生产再流焊炉;
日本松下、美国环球公司分别在苏州和深圳蛇口生产贴装机等等。
目前我国SMT正处于快速发展阶段,2003年以来,每年进口贴装机5000台以上,2007年中国引进SMT主要设备贴片机10189台,约占全球当年贴片机产量的1/2。
中国贴片机的保有量约6万余台,居全球第一,是SMT应用大国。
我国已经成为SMT世界加工基地之一,我国SMT发展前景是非常广阔的。
目前,我国的SMT设备己经与国际接轨,但设计、制造、工艺、管理技术等方面与国际还有差距。
2表面组装技术的特点
表面组装技术(SMT)是无须对印制电路板钻插装孔,直接将表面贴装微型元器件贴焊到印制电路板(PCB)或其他基板表面规定位置上的电子装联技术,其与传统的通孔插装技术比较有以下特点:
(1)结构紧凑、组装密度高、体积小、重量轻
表面组装元器件(SMC/SMD)比传统通孔插装元件所占面积和质量都大为减少,而且贴装时不受引线间距、通孔间距的限制,从而可大大提高电子产品的组装密度。
如采用双面贴装时,元器件组装密度达到5~20个/cm2,为插装元器件组装密度的5倍以上,从而使印制电路板面积节约60~70%以上,重量减轻90%以上。
(2)高频特性好
表面组装元器件(SMC/SMD)无引线或短引线,从而可大大降低寄生电容和引线间的寄生电感,减少了电磁干扰和射频干扰;
偶合通道的缩短,改善了高频性能。
(3)抗振动冲击性能好
表面组装元器件比传统插装元器件质量大为减少,因而在受到振动冲击时,元器件对印制电路板(PCB)上焊盘的动反力较插装元器件大为减少,而且焊盘焊接面积相对较大,故改善了抗振动冲击性能。
(4)有利于提高可靠性
焊点为面接触,消除了元器件与印制电路板(PCB)之间的二次互连。
减少了焊接点的不可靠因素。
(5)工序简单,焊接缺陷极少
由于表面组装技术的生产设备自动化程度较高,人为干预少,工艺相对较为简单,所以工序简单,焊接缺陷少,容易保证电子产品的质量。
(6)适合自动化生产,生产效率高、劳动强度低。
(7)降低生产成本
用表面组装工艺的产品,双面贴装起到减少PCB层数的作用;
印制电路板使用面积减小,其面积为采用插装元器件技术面积的1/10,若采用CSP安装,则其面积还可大幅度下降;
印制电路板上钻孔数量减少,节约返修费用;
元件不需要成形;
工序简单,节省了厂房、人力、材料、设备的投资;
频率特性提高,减少了电路调试费用;
片式元器件作积小、重量轻,减少了包装、运输和储存费用;
而且目前表面组装元器件(SMC/SMD)的价格已经与插装元器件相当,甚至还要便宜,所以一般电子产品采用表面组装技术后可降低生产成本30%左右。
3表面组装技术的组成
表面组装技术(SMT)是电子制造业中技术密集、知识密集的高新技术。
表面组装技术涉及到元器件封装、电路基板技术、涂敷技术、自动控制技术、软钎焊技术、物理、化工、新型材料等多种专业和学科。
表面组装技术内容丰富,跨学科,它主要包含:
表面组装元器件(SMC/SMD)、表面组装电路板及图形设计(EAD设计)、表面组装专用辅料(焊锡膏及贴片胶)、表面组装设备、表面组装焊接技术(包括双波峰焊、再流焊、汽相焊、激光焊)、表面组装测试技术、清洗技术、防静电技术以及表面组装生产管理等多方面内容。
这些内容可以归纳为三个方面:
(1)设备方面,人们称之为表面组装技术(SMT)的硬件;
(2)装联工艺,人们称之为表面组装技术的软件;
(3)表面组装元器件(SMC/SMD),它既是表面组装技术的基础,又是表面组装技术发展的动力,它推动着表面组装技术专用设备和装联工艺不断更新和深化。
3.1表面组装元器件(SMC/SMD)
电子元件的小型化、制造与安装自动化是电子工业发展的需求和多年来追求的目标,表面组装元件(SMC)就是为满足这一需求而产生的。
表面组装元器件的主要特点是:
微型化、无引线(或扁平、短小引线),适合在印制电路板上进行表面组装。
当然,无论是无引线或短引线片式元件,其所有的焊点一般都应处于同一平面上。
常用表面组装器件(SMD)的外形封装、引脚参数及包装方式见表3-1。
常用表面组装元件(SMC)的外形封装、尺寸、主要参数及包装方式见表3-2。
3.1.1表面组装元器件基本要求
(1)元器件的外形适合自动化表面贴装;
(2)尺寸、形状标准化、并具有良好的尺寸精度;
(3)包装形式适合贴装机自动贴装要求;
(4)具有一定的机械强度;
(5)元器件焊端或引脚可焊性良好;
(6)可承受有机溶剂的洗涤。
表3-1表面组装元件(SMC)的外形封装、尺寸及包装方式
外形
元件名称
封装名称及外形尺寸
主要参数
包装方式
矩形片式元件
电阻
0201
0402
0805
1206
1210
1812
0Ω~10MΩ
0.5pf~1.5uf
0.1~100uf/4~35V
0.047uH~33uH
1.0kΩ~150Ω
22~270V
Z=7~125Ω
编带或散装
陶瓷电容
钽电容
电感
热敏电阻
压敏电阻
磁珠
圆柱形片式元件
2210
1.0~33000pf
陶瓷振子
2511
2~6MHz
复合片式元件
电阻网络
SOP8~20
47~l0KΩ
编带
电容网络
1pf~0.47uf
滤波器
4.5×
3.2和5.0×
5.0
低通、高通、带通等
异形片式元件
铝电解电容
3.0×
3.0
4.3×
4.3
4.5×
4.0
3.8
0.1~220uf/,4~50V
微调电容器
3—50pf
微调电位器
100Ω一2MΩ
绕线形电感器
10nH一2.2mH
变压器
8.2×
6.5
接触、旋转、扳钮
各种开关
尺寸不等
3.5—25MHz
振子
10.0×
0.8
规格不等
托盘
继电器
16×
10
连接器
表3-2表面组装元件(SMD)的外形封装、尺寸及包装方式
器件类型
封装名称和外形
引脚数和间距(mm)
包装
片式晶体管
圆柱形二极管
SOT23
三端
SOT89
四端
SOT143
集成电路
SOP(翼型小外形塑料封装)
TSOP(薄形SOP)
8~44引脚
引脚间距:
1.27、1.0、0.8、0.65、0.5
编带
管装
SOJ(J形小外形塑料封装)
20~40引脚
1.27
PLCC(塑料J形引脚芯片载体)
l6~84引脚
LCCC(无引线陶瓷芯片球体)
电极数:
18~156
QFP(四边扁平封装器件)
PQFP(带角耳的QFP)
20~34引脚
BGA(球形栅格阵列)
GSP(又称uBGA,外形与BGA相同,封装尺寸比BGA小)
焊球间距:
1.5、1.27、1.0、0.8、0.65、0.5、0.4、0.3
Fipchip(倒装芯片)
MCM(多芯片模块)
3.1.2表面组装元器件的焊端结构
(1)表面组装元件(SMC)的焊端结构
无引线片式元件焊接端头电极一般为三层金属电极(如图3-1所示),其内部电极一般为厚膜钯银电极。
由于钯银电极直接与铅锡焊料焊接时,在高温下熔融的铅锡焊料中的铅会将厚膜钯银电极中的银食蚀掉,这样会造成虚焊或脱焊,俗称“脱帽”现象。
因此在钯银电极外面镀一层镍,镍的耐焊性比较好,而且比较稳定,用镍作中间电极可起到阻挡层的作用。
但是镍的可焊性不好,因此还要在最外面镀一层铅锡合金,以提高可焊性。
图3-1无引线片式元件焊端结构
(2)表面组装器件(SMD)的焊端结构
表面组装器件的焊端结构可分为羽翼形、J形和球形(如图3-2所示)。
羽翼形的器件封装类型有:
SOT、SOP、QFP等。
J形的器件封装类型有:
SOJ、PLCC等。
球形的器件封装类型有:
BGA、CSP、FlipChip等。
图3-2表面组装器件(SMD)的焊端结构
3.1.3表面组装元器件(SMC/SMD)的包装类型
表面组装元器件包装形式直接影响组装生产的效率,必须结合贴装机送料器的类型和数目进行优化设计。
表面组装元器件的包装类型有编带、散装、管装和托盘。
(1)表面组装元器件包装编带
表面组装元器件包装编带有纸带和塑料带两种材料。
纸带主要用于包装片式电阻、电容的8mm编带。
塑料带用于包装各种片式无引线元件、复合元件、异形元件、SOT、SOP、小尺寸QFP等片式元件。
纸带和塑料带的孔距为4mm(1.0×
0.5mm以下的小元件为2mm)或元件间距4mm的倍数,根据元器件的长度而定。
(2)散装包装散装包装主要用于片式无引线无极性元件,例如电阻、电容。
(3)管状包装主要用于SOP、SOJ、PLCC以及异形元件等。
(4)托盘包装托盘包装用于QFP、窄间距SOP、PLCC等。
3.2表面组装技术的组装类型
(1)按焊接方式可分为再流焊和波峰焊两种类型
①再流焊工艺——先将微量的铅锡焊膏印刷或滴涂到印制电路板的焊盘上,再将片式元器件贴放在印制电路板表面规定的位置上,最后将贴装好元器件的印制电路板放在再流焊设备的传送带上,从再流焊炉入口到出口大约需要2~5分钟就完成了干燥、预热、熔化、冷却全部焊接过程。
②波峰焊工艺——先将微量的贴片胶(绝缘粘接胶)印刷或滴涂到印制电路板与被安置的元器件底部或边缘位置上(贴片胶不能污染印制电路板焊盘和元器件端头),再将片式元器件贴放在印制电路板表面规定的位置上,将贴装好元器件的印制电路板进行胶固化。
固化后的元器件被牢固地粘接在印制电路板上,然后插装分立元器件,最后与插装元器件同时进行波峰焊接。
(2)按组装方式分类可分为全表面组装、单面混装、双面混装,见表3-3。
表3-3按组装方式分类
序号
组装方式
电路基板
元器件
特征
1
单面混合
先贴法
单面印制电路板
表面组装元器件及通孔插装元器件
先贴后插、工艺简单、组装密度低
2
后贴法
同上
先插后贴、工艺复杂、组装密度高
3
双面混装
表面组装和通孔插装元器件都在A面
双面印制电路板
4
通孔插装元器件在A,A、B两面都有表面组装器件
THC和SMC/SMD组装在PCB同一侧
5
表面组装
单面表面组装
单面印制电路板和陶瓷基板
表面组装元器件
工艺简单,适用于小型、薄型化的电路组装
6
双面表面组装
双面印制电路板和陶瓷基板
同上
高密度组装,薄型化
3.3SMT生产线及SMT生产线主要设备
3.3.1SMT生产线分类
按照生产线的规模大小可分为大型、中型和小型生产线;
按照自动化程度可分为全自动生产线和半自动生产线;
全自动生产线是指整条生产线的设备都是全自动设备,通过自动上板机、缓冲连接线和卸板机将所有生产设备连成一条自动线;
半自动生产线是指主要生产设备没有连接起来或没有完全连接起来,如印刷机是半自动的,需要人工印刷或人工装卸印制电路板等。
3.3.2SMT生产线主要设备
SMT生产线主要生产设备包括印刷机、点胶机、贴装机、再流焊炉和波峰焊机。
辅助设备有检测设备、返修设备、清洗设备、干燥设备和物料存储设备等。
(1)印刷机
用来印刷焊膏或贴片胶的。
将焊膏(或贴片胶)正确地漏印到印制电路板相应的位置上。
①印刷机的基本结构(如图3-3所示)。
②印刷机的主要技术指标:
1)最大印刷面积:
根据最大的PCB尺寸确定。
2)印刷精度:
一般要求达到±
0.025mm。
3)印刷速度:
根据产量要求确定。
图3-3印刷机的基本结构
(2)贴装机
相当于机器人,把元器件从包装中取出,并贴放到印制电路板相应的位置上。
①贴装机的基本结构(如图3-4所示)。
图3-4贴装机的基本结构
②贴装机的主要技术指标。
1)贴装精度:
包括三个内容:
贴装精度、分辨率、重复精度;
贴装精度指元器件贴装后相对于印制电路板标准贴装位置的偏移量,一般来讲,贴装SMC元件要求达到±
0.1mm,贴装高密度窄间距的SMD至少要求达到±
0.6mm。
分辨率是贴装机运行时每个步进的最小增量。
重复精度是指贴装头重复返回标定点的能力。
2)贴片速度:
一般高速机为0.2s/Chip元件以内,多功能机度为0.3~0.6s/Chip元件左右。
3)对中方式:
有机械对中、激光对中、全视觉对中、激光/视觉混合对中。
4)贴装面积:
指贴装头的运动范围,可贴装的PCB尺寸,最大PCB尺寸应大于250×
300mm。
5)贴装功能:
是指贴装元器件的能力。
一般高速机只能贴装较小的元器件;
多功能机可贴装最小0.6×
0.3mm~最大60×
60mm器件,还可以贴装连接器等异形元器件。
6)供料器数量:
是指贴装机料站位置的多少(以能容纳8mm编带供料器的数量来衡量)。
7)编程功能:
是指在线和离线编程优化功能。
(3)再流焊炉
再流焊炉是焊接表面贴装元器件的设备。
再流焊炉主要有红外炉、热风炉、红外加热风炉、蒸汽焊炉等。
目前最流行的是全热风炉。
再流焊炉的主要技术指标:
①温度控制精度:
应达到±
0.1~0.2℃;
②传输带横向温差:
要求±
5℃以下;
③温度曲线测试功能:
如果设备无此配置,应外购温度曲线采集器;
④最高加热温度:
一般为300~350℃,如果考虑无铅焊料或金属基板,应选择350℃以上。
⑤加热区数量和长度:
加热区数量越多、加热区长度越长,越容易调整和控制温度曲线。
一般中小批量生产选择4~5温区,加热区长度1.8m左右即能满足要求。
⑥传送带宽度:
应根据最大PCB尺寸确定。
3.4表面组装的PCB
根据产品的功能、性能指标以及产品的档次选择PCB:
对于一般的电子产品采用环氧玻璃纤维基板;
对于使用环境温度较高或挠性电路板采用聚酰亚胺玻璃纤维基板;
对于散热要求高的高可靠电路板采用金属基板;
对于高频电路则需要采用聚四氟乙烯玻璃纤维基板。
3.5表面组装焊接材料
3.5.1焊膏
焊膏是再流焊工艺必须材料。
焊膏是由合金粉末、糊状助焊剂载体均匀混合成的膏状焊料。
(1)焊膏的分类
1)按合金粉末的适应性可分为:
高温、低温,有铅和无铅;
2)按合金粉末的颗粒度可分为:
用于一般间距和窄间距;
3)按焊剂的成分可分为:
免清洗、可以不清洗、溶剂清洗和水清洗;
4)按松香活性可分为:
非活性(R)、中等活性(RMA)、全活性(RA);
5)按黏度可分为:
印刷用和滴涂用。
(2)焊膏的组成
1)合金粉末
合金粉末是焊膏的主要成分,合金粉末的组分、颗粒形状和尺寸是决定焊膏特性以及焊点质量的关键因素。
目前最常用焊膏的金属组分为Sn63Pb37和Sn62Pb36Ag2。
2)焊剂
焊剂是净化金属表面、提高润湿性、防止焊料氧化和保证焊膏质量以及良好工艺性的关键材料。
目前普通焊膏还继续沿用。
随着环保要求,免清洗焊膏的应用越来越普及,对于清洁度要求高的产品可使用溶剂或水洗焊膏。
另外,为了防止铅对环境和人体的危害,无铅焊料也迅速地被提到议事日程上,日本已研制出无铅焊料并应用到实际生产中,美国和欧洲也在加紧研制和应用。
3.5.2贴片胶
贴片胶是表面贴装元器件在波峰焊工艺必须的粘接材料。
波峰焊前需要用贴片胶将贴装元器件固定在PCB相对应的位置上,以防波峰焊时元器件掉落到锡锅中。
贴片胶主要有两种:
环氧树脂和聚丙烯。
环氧树脂型贴片胶属于热固型,一般固化温度在140±
10℃/2min;
聚丙烯型贴片胶属于光固型,须先用紫外灯照射,打开化学键,然后再用140±
10℃/1—2min完成完全固化。
3.6表面组装工艺
表面组装工艺主要由涂敷工艺、贴装元器件工艺、焊接工艺和检测工艺等组成。
3.6.1涂敷工艺
涂敷工艺就是施加焊膏,工艺目的是把适量的Sn/Pb焊膏均匀地施加在PCB的焊盘上,以保证贴片元器件与PCB相对应的焊盘达到良好的电气连接。
3.6.2贴装元器件工艺
贴装元器件工艺是用贴装机或人工将片式元器件准确地贴放到印好焊膏或贴片胶的PCB表面的相应位置上。
贴装元器件是保证SMT组装质量和组装效率的关键工序。
(1)贴装元器件的工艺要求
1)各装配位号元器件的类型、型号、标称值和极性等特征标记要符合产品的装配图和明细表要求;
2)贴装好的元器件要完好无损;
3)贴装元器件焊端或引脚不小于1/2厚度,要浸入焊膏。
对于一般元器件贴片时的焊膏挤出量(长度)应小于0.2mm,对于窄间距元器件贴片时的焊膏挤出量(长度)应小于0.1mm;
4)元器件的端头或引脚均和焊盘图形对齐、居中。
由于再流焊时有自定位效应,因此元器件贴装位置允许有一定的偏差。
元器件贴装位置允许偏差范围:
①矩形元件允许偏差范围在元件宽度方向焊端宽度的1/2~3/4以上在焊盘上;
在元件长度方向元件焊端与焊盘交叠后,焊盘伸出部分要大于焊端高度的1/3;
有旋转偏差时,元件焊端宽度的3/4以上必须在焊盘上。
②小外形晶体管(SOT)和小外形集成电路(SOIC)允许偏差范围允许方向x、方向Y、旋转角度T有偏差(△X、△y、△T),但必须保证器件引脚宽度的
3/4(含趾部和根部)处于焊盘上。
③四边扁平封装器件和超小形封装器件(QFP和PLCC):
要保证引脚宽度的
3/4处于焊盘上,允许方向x、方向Y、旋转角度T有偏差(△X、△y、△T),允许引脚趾部少量伸出焊盘,但必须有3/4引脚长度在焊盘上、引脚的根部也必须在焊盘上。
(2)自动贴装机贴装原理
1)PCB基准校准原理
自动贴装机贴装时,元器件的贴装坐标是以PCB的某一个顶角(一般为左下角或右下角)为原点计算的。
而PCB加工时多少存在一定的加工误差,因此在高精度贴装时必须对PCB进行基准校准。
基准校准采用基准标志(Mark)和贴装机的光学对中系统进行。
基准标志(Mark)分为PCB基准标志(PCBMark)和局部基准标志(局部Mark)。
1PCBMark的作用和PCB基准校准原理
PCBMark是用来修正PCB加工误差的。
贴片前要给PCBMark照一个标准图像存人图像库中,并将PCBMark的坐标录入贴片程序中。
贴片时每运送上一块PCB,首先照PCBMark,与图像库中的标准图像比较:
一是比较每块PCBMark图像是否正确,如果图像不正确,贴装机则认为PCB的型号错误,会报警不工作;
二是比较每块PCBMark的中心坐标与标准图像的坐标是否一致,如果有偏移,贴片时贴装机会自动根据偏移量修正每个贴装元器件的贴装位置,以保证精确地贴装元器件。
②局部Mark的作用
多引脚窄间距的器件,贴装精度要求非常高,靠PCBMark不能满足定位要求,需要采用2—4个局部Mark单独定位,以保证单个器件