子午线轮胎设计制造技术汇总Word格式文档下载.docx
《子午线轮胎设计制造技术汇总Word格式文档下载.docx》由会员分享,可在线阅读,更多相关《子午线轮胎设计制造技术汇总Word格式文档下载.docx(25页珍藏版)》请在冰豆网上搜索。
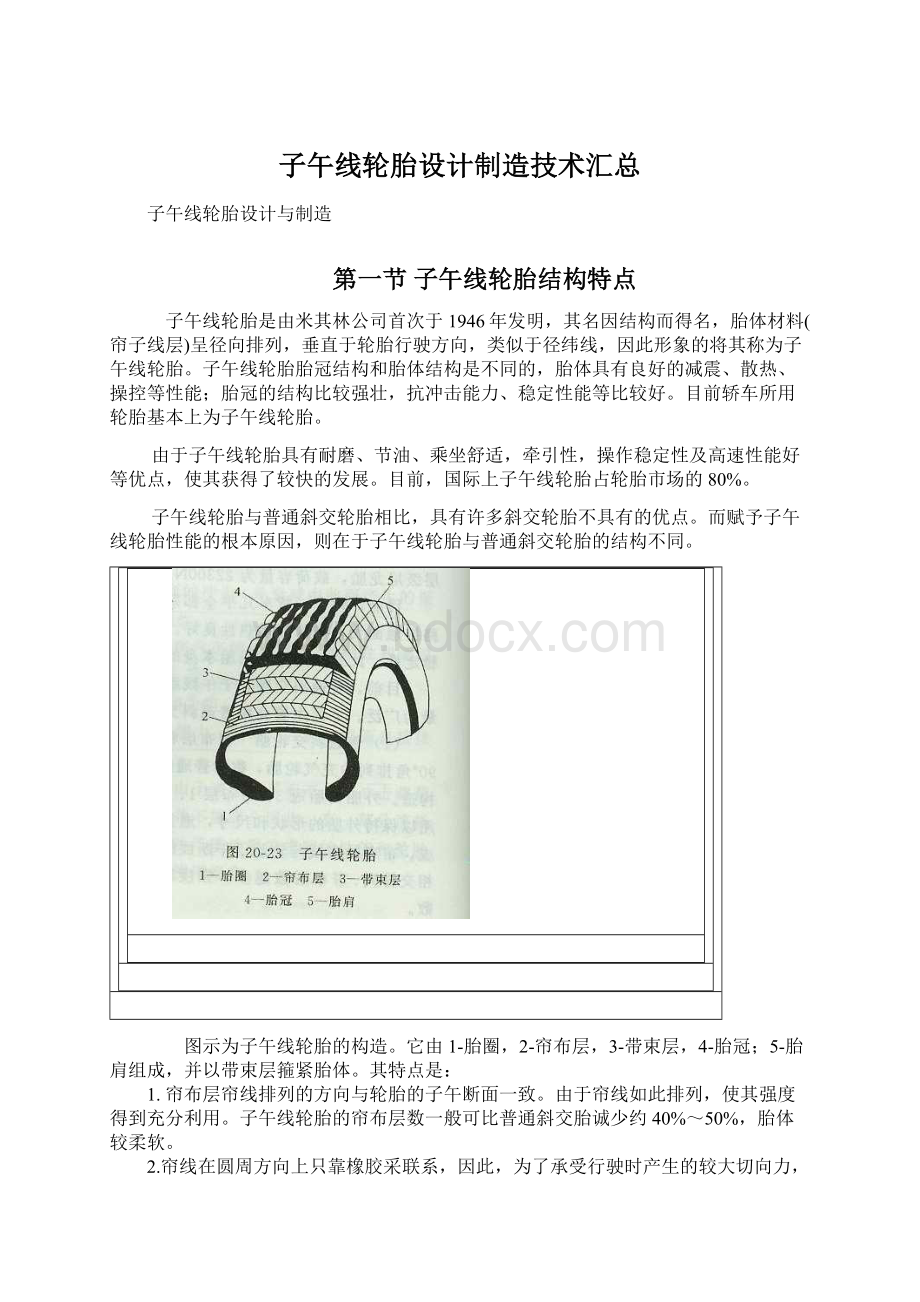
生胶塑、混炼,胎面、胎侧制造,胎体、带束层制造,各种型胶部件制造,胎圈制造,外胎成型,外胎硫化,外胎成品的生产检测等。
第二节塑炼和混炼
塑炼和混炼是橡胶加工的基本工艺过程。
塑炼是将天然橡胶分子链发生机械和氧化裂解,使天然橡胶失去部分弹性和增加塑性。
混炼是将各类配合剂均匀分散到已具有一定塑性的橡胶类高弹体中,从而制得供产品各胶料部件使用的混炼胶。
本节只对子午线轮胎的加工工艺的特殊要求和其相关设备及机械结构方面做简要的介绍。
一、橡胶的塑炼
1.橡胶塑炼准备
天然橡胶的原料、因橡胶树受自然界的气候、地理等各种客观复杂条件的限制,橡胶块品质存在着差异。
为此,天然橡胶块在塑炼前,先将同等级品质的橡胶块加以混合。
橡胶块混合的加工工艺流程是:
一块橡胶块经提开到一排辊道上后,滚向一台切胶机一次切割成4-6块小块橡胶,然后依次落入坐落在圆盘式转台上的4-6辆框式小车里。
小车经传动板依次运入橡胶烘房,烘胶的温度夏季为35-40º
C,冬季为65-70º
C;
烘胶的相应时间为8个小时和12个小时。
整个生产过程可以达到完全自动。
橡胶被切成小块并经恒温烘胶,使胶块温度比较一致,塑炼不仅可节省电能,主要可以改善塑炼橡胶的可塑度的批量均一程度。
2.橡胶塑炼设备
天然橡胶的塑炼方法有用开放式炼胶机、螺杆塑炼机、密炼机等三种设备进行。
开放式炼胶机塑炼,劳动生产率低,占地大,不适宜于用胶量大的轮胎工业。
用螺杆塑炼机塑炼,在五十年代比较盛行。
橡胶块先经切胶、破胶后喂入螺杆塑炼机,塑炼后的橡胶可根据需要呈颗粒状或片状,缺点是橡胶的可塑度变化范围受到一定的限制,现在建设新的轮胎工厂,几乎已不再采用这种塑炼工艺了。
现在使用最广的是密炼机的塑炼方式。
橡胶块经皮带称量后直接通过密炼机进料口进入混炼室内进行塑炼,达到给定的功率和时间就自动排胶,在开放式出片机或者辊筒机头螺杆挤出机连续出胶片,然后胶片被喷涂隔离剂、挂片风冷、成片折叠、定重切割、停放待用。
生胶从塑炼到胶片切割的全过程实现机械化、连续化、微机控制。
如密炼机转子速度为60r/min,天然橡胶塑炼容量为195-210公斤,排胶温度为165-170º
C,塑炼时间为4分钟左右。
二、胶料的混炼
子午线轮胎的胶料,为获得良好的分散性,不少配合剂在混炼之前,有的做成膏状、有的搅拌分散于微量的类如干燥的白炭黑、碳酸钙中、有的做成母胶等等。
轮胎胶料的生产工艺大部分是两端混炼,钢丝帘线胶料大多是三段混炼。
轮胎工业使用的混炼设备是密炼机系统。
1.混炼周期的控制方法
胶料混炼周期有时间、温度和能量消耗-功率积分等控制方法。
单一的时间因素的传统控制方法已属落后而将被淘汰。
一般使用的是以温度控制为主、辅以参考时间的方法。
现在已发展到以混炼能量为主、温度控制为辅的方法了。
混炼能量控制混炼过程方法的优点是可以缩小批量胶料之间的质量差异,提高混炼胶质量的均一性能。
2.胶料的分段混炼
轮胎胶料的第一段混炼通常制成含有软化剂的炭黑母胶。
第一段混炼方法有顺序混炼和逆法混炼两种。
顺序混炼工艺就是在密炼机混炼过程中先加生胶后加其它配合剂的加料顺序,通常是生胶+小料+1/2炭黑+软化剂+1/2炭黑——排胶。
逆法混炼工艺就是先加配合剂最后加生胶的加料顺序,如炭黑-软化剂-小料-生胶-排胶,也有把软化剂最后加入的。
制造母胶的第一段混炼采用270立升、60r/min的密炼机,混炼时间为2分钟,排胶温度在165º
C以下。
第二段混炼工艺是母胶+促进剂、硫磺-排胶。
终炼采用270立升、30r/min的密炼机,混炼时间为2.5分钟。
由于排胶温度可控制在100º
C以下,保证了胶料加工的安全性。
3.钢丝帘线胶料的混炼
钢丝帘线胶料的胶质硬、炭黑量多、粘合剂分散性差,一般采用三段混炼方法。
制造炭黑母胶如采用30r/min的密炼机,混炼时间为4.5分钟,排胶温度为145º
C左右。
终炼阶段如加促进剂和硫化剂时,如有不溶性硫磺配合时,则要特别注意混炼室内的胶料温度,其一般控制在90-95º
C之间,最高不得超过100º
C。
终炼采用的是低速密炼机,如270立升密炼机的转子转速,有的选用15r/min,有的选用20r/min,终炼周期为2.5-3分钟。
Banbury公司推荐用较高的38º
C等水温作密炼机的冷却循环水,能弥补季节性、冷设备开车等温度差异所引起的胶料品质的均一程度。
此外,还有缩短密炼时间、减少耗水量、节省能量等优点。
为了混炼类如钢丝帘线这类硬胶料,密炼机上顶栓对混炼室中胶料的单位压力,选用设备时不要低于550KPa。
在正常情况下,上顶栓应该能上下浮动,浮动距离以50mm左右为佳。
4.混炼胶料的质量检测
混炼胶料的质量检测项目主要有可塑度、硬度、比重和硫化仪曲线。
硫化曲线是硫化仪利用转矩量对温度下的胶料之间的变化绘制的曲线,每种胶料配方都有其特定的硫化曲线,用此标准曲线检验每批混炼料的质量情况。
三、密炼机组
密炼机是塑炼或混炼橡胶的加工装备。
上辅机组是指粉状、液状、颗粒状等原材料为储存、称量、输送后投入密炼机所需的装置。
下辅机组是指密炼机排出的胶料经出片直到叠片切割等一系列的装置。
现代化的轮胎工厂的炼胶系统,是以密炼机为中心,并与上辅机组和下辅机组联结成一条完整的炼胶生产线。
1.上辅机组
(1)炭黑系统炭黑经槽车或拆包后在密闭状态下用风压送到各个炭黑储罐或分格大储罐。
大储罐中炭黑分别被风送到各种品种的炭黑日料斗,风送炭黑有13-18m/s高压快速和4m/s低压低速两种方法。
现在发展低压低速方法,其优点是湿法颗粒炭黑在风送过道中的破碎率为10-20%,大大低于前者的20-30%.日料斗内的不同品种炭黑按照加料次序依次投入悬挂秤称量,然后投入密炼机混炼室。
(2)液体软化剂系统软化剂从加温储罐中经泵送入中间保温罐后备用。
液体软化剂以重量法或溶剂法用压力直接注射进密炼机混炼室中与胶料进行充分混炼,一般而言用重量法比较准确。
(3)小量原料配量系统。
各种原料分别存放在依次排列的储斗内,用低熔点聚乙烯包装袋包装、微处理机控制称量。
2.下辅机组
下辅机组的排列大致有以下三种形式:
(1)270立升密炼机后用两台Φ660x2100mm压片机串联排列出片。
(2)270立升密炼机后用一台Φ660x2100mm压片机连续出片。
(3)270立升密炼机后用一台辊筒机头螺杆挤出机连续出片。
3.密炼机
密炼机全称叫做“密闭式炼胶机”,是在开炼机的基础上发展起来的。
1820年发明开炼机以后,使橡胶工业发生了根本的转变,但由于开炼机存在许多缺点,比如劳动强度大,效率低,粉尘大等,严重影响人的身体健康,于是人们开始考虑能否把这一加工设备用一个罩子把它罩起来,就逐步发展成密炼机。
因为它在密炼室里面工作,所以称作密闭式。
由于开炼机工作是敞开的,故叫做开放式炼胶机。
一般介绍均认为密炼机是Banbury在1916年发明的,实际最早是由西德W&
P公司的一名商业工程师(英国人)根据该公司的原型机台设计的,由于其发展较快,产量也大应用较广,故人们一直认为Banbury密炼机是最早问世的。
自从出现密炼机后,在混炼过程中显示了比开炼机具有的一系列优点,如混炼时间短,生产效率高,操作容易,较好地克服粉尘飞扬,减少配合剂的损失,改善劳动条件,减轻劳动强度等。
由于它在很大程度上是凭经验发展起来的,因而在发展早期曾出现过认为塑炼效率低,不能用它来塑炼的说法,但已经为生产实践所否定。
因此,密炼机的出现是炼胶机械的一项重要成果,至今仍然成为塑炼和混炼中的典型设备,并处于不断发展完善中。
据国外资料统计,在橡胶工业中有88%的胶料是由密炼机制造的,塑料、树脂行业亦广泛应用密炼机。
现代密炼机发展的标志之一是高速、高压和高效能机台。
通常将转子转速为20rpm的称为低速密炼机,30~40rpm的称为中速密炼机,60rpm以上的称为高速密炼机。
近年来,出现了转速达80rpm甚至更高的密炼机,亦有对工艺和效能有广泛适应性和处理手段的双速、三速、变速密炼机,也有转子速比可调节的密炼机。
其操作时间大大缩短,从过去慢速机台的8~15min缩短至1.5~3.5min,甚至有的达1~1.5min(包括采用密炼法与补充混炼法配合的工艺过程等)。
密炼机的结构也在不断发展。
密炼机工作过程及整个机组的机械化、自动化水平也在不断提高,采用了程序控制,现在大型引进机台均采用计算机控制。
总之,此种发展是在大大强化混炼过程,提高机台效能,减轻体力劳动和改善工作环境等。
在这种剧烈的混炼过程中,当然会带来许多新问题,因此,对机械研究设计来说,从机台的捏炼系统、冷却系统、密封系统、加料及压料系统、卸料系统、传动系统、控制系统、主要零部件、材料到各种参数的技术决定以及理论,都需要相应的发展,以使机台性能优良,为生产过程提供可能的适应性和调节性。
我国密炼机发展状况是:
解放前是空白,解放后国产密炼机逐步发展起来了。
我国第一个制造密炼机的厂家是大连橡塑机厂,首先仿苏生产了PC-2140/20L密炼机,现在改为250L、75/40L密炼机。
然后上海等地逐步也生产这些机台,如250/20/40,75/30/60,75/35/70,以及50L密炼机。
近年来又仿照F系列密炼机生产F080,F160,F270,均已出口。
另外又给日本生产翻转式50L、70L密炼机。
益阳橡机厂又从西德引进GK系列技术生产GK系列密炼机。
F系列、GK系列是当前世界两大先进系列密炼机。
国内橡胶大厂均有引进。
我院一直在研究密炼机,销钉转子、销钉混炼室密炼机等。
密炼机发展方向:
“二大”、“二高”、“一低”,即大规格(大容量)、大功率,高速、高压,单位能耗低,主要问题:
端面密封。
1)用途
主要用于橡胶的塑炼和混炼,同时也用于塑料、沥青料、油毡料、合成树脂料的混炼。
它是橡胶工厂主要炼胶设备之一。
七十年代以来,国外在炼胶工艺和设备方面虽然发展较快,例如用螺杆挤出机代替密炼机和开炼机进行塑炼和混炼,但还是代替不了密炼机。
新的现代工厂中的炼胶设备仍以密炼机为主,混炼方法也仍采用两段混炼法。
2)分类
密炼机分类方法较多,主要有以下几种方法:
(1).按转子端面形状不同(RotorSectionForm)
本伯里型(Banbury)过去D型,现在F型(二棱、四棱)
椭圆型转子密炼机GKN非啮合切线型
GK型
GKE啮合型圆筒型(二棱、四棱)
过去叫做GK-UK型
圆筒型转子密炼机肖氏(Francisshaw)、K型
三角型转子密炼机
相切型,切线型
(2).按转子啮合与否(Intermeshing)
啮合型,联锁型
(3).按转子转速不同(RotorSpeed)
慢速以XM-250为例<
20rpm
中速以XM-250为例30~50rpm
高速以XM-250为例<
60rpm
转速与其它机械相比,纯属低速范围,但对炼胶作业来讲却是高速了,因炼胶要消耗大量能量,产生大量热量,这两点都限制转速范围。
单速
(4).按转子转速变化与否双速转子具有两个速度
变速
普通型四棱、两棱
(5).按转子外表面结构来分销钉型转子
特殊型螺旋型
普通型
(6).按混炼室结构来分特殊型销钉密炼室
翻转密炼室
大容量(规格)密炼机370L
(7).以密炼机的容量来分中容量80-270L
小容量10-50L
试验用密炼机在10L以下
(8).按转子速比异步转子
同步转子
3)生产厂家
(1)国外
目前世界各国生产密炼机的厂家较多,产量较大,但具有竞争能力的仍是以下三家:
a.美国FarrelBirminghanCo.法勒尔·
伯明翰公司D型和F型为其首创;
b.西德Werner&
PfleidererCo.(简称W&
P公司)维尔纳·
普弗莱德瑞尔公司,GK-UK和GKN/GKE系列为其首创;
c.英国FrancisShawCo.弗兰西斯·
肖公司,K型属于首创
此外还有日本的KobeSteel神户制钢所研制的BB型、D型、F型;
意大利伯米尼Pomini公司;
西班牙的GuixCo.魁克斯公司的挑担式GK和F结合;
苏联布尔什维克厂PC型、椭圆型;
意大利依·
科未里奥公司ComerioErcoleSPA,MA型密炼机为其独创,1936年生产并取得专利。
(2)国内
解放前我国不能自己生产密炼机,当时国内橡胶厂也没有使用密炼机的,橡胶作业完全靠开炼机。
解放后,五十年代我国从苏联、捷克等社会主义国家进口了一批中型密炼机(11#),此后我国橡机制造厂逐步走向自主设计制造阶段。
目前,国内不少厂家生产各类型密炼机,并有部分出口。
大连橡塑机械厂:
最早生产国产密炼机的厂家,引进苏联图纸。
目前国内橡胶厂大部分都是采用的该厂产品,1986年已仿制出F270L密炼机。
益阳橡机厂:
是60年代我国新建的大型橡机厂,也生产了不少密炼机。
最近从西德引进GK型密炼机制造技术,1987年已生产出GK270密炼机。
上海橡机厂(原茶陵机器厂):
是生产中型密炼机的工厂,其产品质量好。
上海橡机二厂:
生产中小型密炼机
西亚机器厂:
中小其特点是用行星减速机
天津机厂:
中小
天津电工机械厂:
桂林机厂:
此外还有不少塑料机械厂、轻工机械厂生产密炼机。
4)规格与技术特征
(1)规格:
过去采用混炼室的工作容量和主动转子转速表示。
现在采用混炼室的总容量/主动转子的转速表示。
国产密炼机的规格表示法:
XM-250/20
XM-75/35╳70
美Banbury密炼机,过去D型:
3D,9D,11D,27D
现在F型:
F40,F120,F270,F620
西德W&P密炼机,过去:
GK-UK,GK-50UK,GK-160UK
现在:
GK-N,GK-90N,GK-270N
GK-E,GK-90E,GK-270E
英FranisShaw密炼机:
K0K1K2K5K6K7K2AK4K8K10
1.85.318.813218935145.584475915
苏联布尔什维克250-20,250-30,250-40
(2)技术特征
混炼室总容量分容量,工作容量的区别
a.电机功率随转子转速不同而异转速提高一倍电机功率增加1~4倍
b.转速小规格转速高,大规格转速低,以便胶料能经受同样的剪切速率与剪切应力
c.冷却消耗量很大
5)基本结构
(1)整体结构组成:
密炼机的结构,一般是由六个部分五个系统组成的,六个部分指的是:
a.混炼部分mixingsection(包括转子rotor、混炼室mixingchamber、密封装置duststop、转子轴向调正装置、轴承bear)
b.加料部分Feedmodulesection
c.压料部分Pressureramsection不加压胶吃不进
d.卸料部分Dischargesection
e.传动装置部分Drivesection耗电1.7e-30KW相当100W灯泡300个传动比大电机上千转,转子几十转,转子20rpmI=75
五个系统:
f.加热冷却系统Heating&coolingsystem
g.气压系统Compressedairsestem
h.液压系统Hydrauliesystem
i.电控系统Elestriccontroller(system)
j.润滑系统Lubrication
每个部分组成及作用
a.混炼部分
混炼部分主要有转子、混炼室、密封装置等组成,从图上可以看出,主要有上、下机壳6、4,上、下混炼室7、5,转子8,密封装置(图上看不见)等组成,下机壳4用细栓固定在机座1上,上机壳6与下机壳4用细栓紧固在一起。
上、下机壳内分别固定有上下混炼室7和5,上、下混炼是带有夹套(新型密炼机采用钻孔冷雀,不必带有夹套)可通入冷却水(当用于炼胶时现在新型的迷恋机通入恒温水)或通入蒸汽(当用于炼塑料时)进行冷却或加热,转子两端用双列圆锥滚子轴承安装在上、下机壳中,两转子通过安装在其颈部的速比齿轮的带动,在环形的混炼室内做不同转速的相对回转,上、下密炼室内表面及转子工作部分的突棱及全部椭圆行外表面均堆焊硬质合金,提高硬度,以增加使用寿命。
为了防止炼胶时粉料及胶料向外溢出,转子两端设有反螺纹与端面接触式自动密封装置(或其它各种形式密封)。
密封装置的摩擦面用油泵强制诸如干油进行润滑(国内这一点较差)。
干油泵由前转子带动,调节油泵摇杆的长度和油泵活塞的细钉,可调节油泵的供油量。
这一部分是密炼机的核心部分,其主要作用是对胶料进行混合、剪切、捏炼。
b.加料部分
它主要右加料室和斗形的加料口以及翻板门(加料门)11组成,加料门(翻板门)的开关由风缸带动,安装在混炼是的上机壳6上面,在加料口上方安有吸尘罩,使用单位可在吸尘罩上安置管道和抽风机,以便达到良好的吸尘效果。
加料斗的后壁设有方形孔,根据操作需要可将方形孔盖板拿掉,安装辅助加料管道,一般安装碳黑管道,自动加入碳黑,在侧面右一小圆孔,以便安装自动注油管道。
这部分作用主要是用于加料和瞬间存料。
c.压料部分:
它主要由上顶栓9和推动上顶栓做上、下往复运动的气缸14组成,各种物料从加料口加入后,关闭翻板门(加料门)由气缸14操纵上顶栓将物料压入混炼室中,并在炼胶过程中给物料一定的压力来加速炼胶过程。
它的主要作用:
给胶料一定的压力,加速炼胶过程,提高炼胶效果。
如果不加压,胶料就吃不进去,等于开炼机一样,效率较低,加压后,使脚镣能较顺利进入转子之间进行混炼。
上顶栓与物料接触的表面,堆焊耐磨合金,增加耐磨性,上顶栓内腔通冷却水冷却,新型现在没有。
d.卸料装置部分:
主要由安装在混炼室下面的下顶栓3和下顶栓锁紧机构2所组成,下顶栓固定在旋转轴上,而旋转轴由安装在下机壳侧壁上的旋转油缸17带动,使下顶栓以摆动形式开闭。
下顶栓锁紧机构2主要由一旋转轴和锁紧栓所组成。
锁紧栓之摆动由往复式油缸16新驱动。
在下顶栓上装有热电偶,用于测量胶料在炼胶过程中的温度。
所以它的主要作用,就是在炼胶完毕后排除胶料,也就是卸料。
下顶栓内可通冷却水冷却,下顶栓与物料接触的‘
’形表面可堆焊耐磨合金,增加其耐磨性。
e.传动装置部分;
主要有电机22,弹性连轴节21,减速机20和齿形连轴节19等组成。
安装在传动底座上,其作用传递动力,使转子克服工作阻力而转动,从而完成炼胶作业。
f.底座
主要有机座而组成。
有的分为主机底座和传动底座。
其作用使供密炼机使用,在其上安装主机和传动系统的部件。
g.加热冷却系统
作用:
根据工艺要求,控制炼胶过程中胶料的温度
主要由管道和分配器等组成,以便将冷却水或蒸汽通人混炼室、转子和上、下顶柱等的空腔内循环流动,以控制胶料的温度。
从国外引进的密炼机加热冷却系统配有温控装置,采用恒温水加热冷却。
采用恒温水主要优点表现在
(1)消灭水露,减轻胶料打滑。
因为在炼胶作业中要有放出大量的热,同时要保证一定的温度。
当室温一高,混炼室中形成蒸汽,当室用冷却水冷却,就会形成水露,附在混炼室内壁上和转子表面上。
这样就会降低胶料与金属表面摩擦系数,形成打滑,降低了炼胶效果。
(2)保持恒定的橡胶的摩擦系数提高产品质量。
橡胶的摩擦系数是随着金属温度变化的,温度越低,摩擦系数越小。
在混炼作业中,突然加入冷却水,使橡胶接触的金属温度太低,就会在冷却的表面打滑。
要实现良好的混炼和获得分散度较均匀的质量,必须使剪切应变能施加到混合物上,而只有胶料被夹着,不打滑才能实现,所以片面采用冷却水或冷却水温度较低对密炼室却是不利的。
(3)采用恒温水,可以大大降低设备上的热应力,延长机体寿命。
采用恒温水循环冷却后,可以发现
(1)消灭“露水”,可缩短混炼周期50%
(2)峰值功率降低,能耗节省10—20%
(3)减少冷却水消耗可达80%
(4)大大降低设备的热应力,延长机体寿命
(5)改善混炼胶的分散度
(6)增大填充系数
(7)消除许多操作误差
(8)保持每批胶料之间的均匀性
(9)为配方人员提供控制参数的新方法
国外引进密炼机全部采用温水循环冷却,常温控系统。
国内正在研究,当前只有我院我们实验室研究,我们实验室已制造出十几,在全国各大橡胶厂使用,效果很好。
同学们回厂后,如想要,可与我们取得联系。
h.液压系统
主要由一个双联叶片油泵15,旋转油缸17,往复油缸16,管道和油箱等组成。
它是卸料机构动力供给部分。
用于控制下顶栓及下顶栓锁紧机构的开闭。
i.气压系统
主要有气缸14,活塞13,加料门的气缸,气阀,管道和压缩空气等组成。
它是加料,压料机构的动力供给部分。
用于控制上顶栓的升降,加压及翻板门的开闭。
j.电控系统
主要由控制箱,操作机台和各种电气仪表组成,它是整个机台的操作中心。
k.润滑系统
主要由油泵,分油器和管道组成,目的是为了使各个转动部分(如旋转轴、轴承、密封装置的密封环摩擦面等)减少摩擦。
增加使用寿命,向这些摩擦面注入润滑油。
向每个转动部位,注入润滑油,以致减少运动部件之间的摩擦,延长其使用寿命。