工艺编制规范Word文件下载.docx
《工艺编制规范Word文件下载.docx》由会员分享,可在线阅读,更多相关《工艺编制规范Word文件下载.docx(7页珍藏版)》请在冰豆网上搜索。
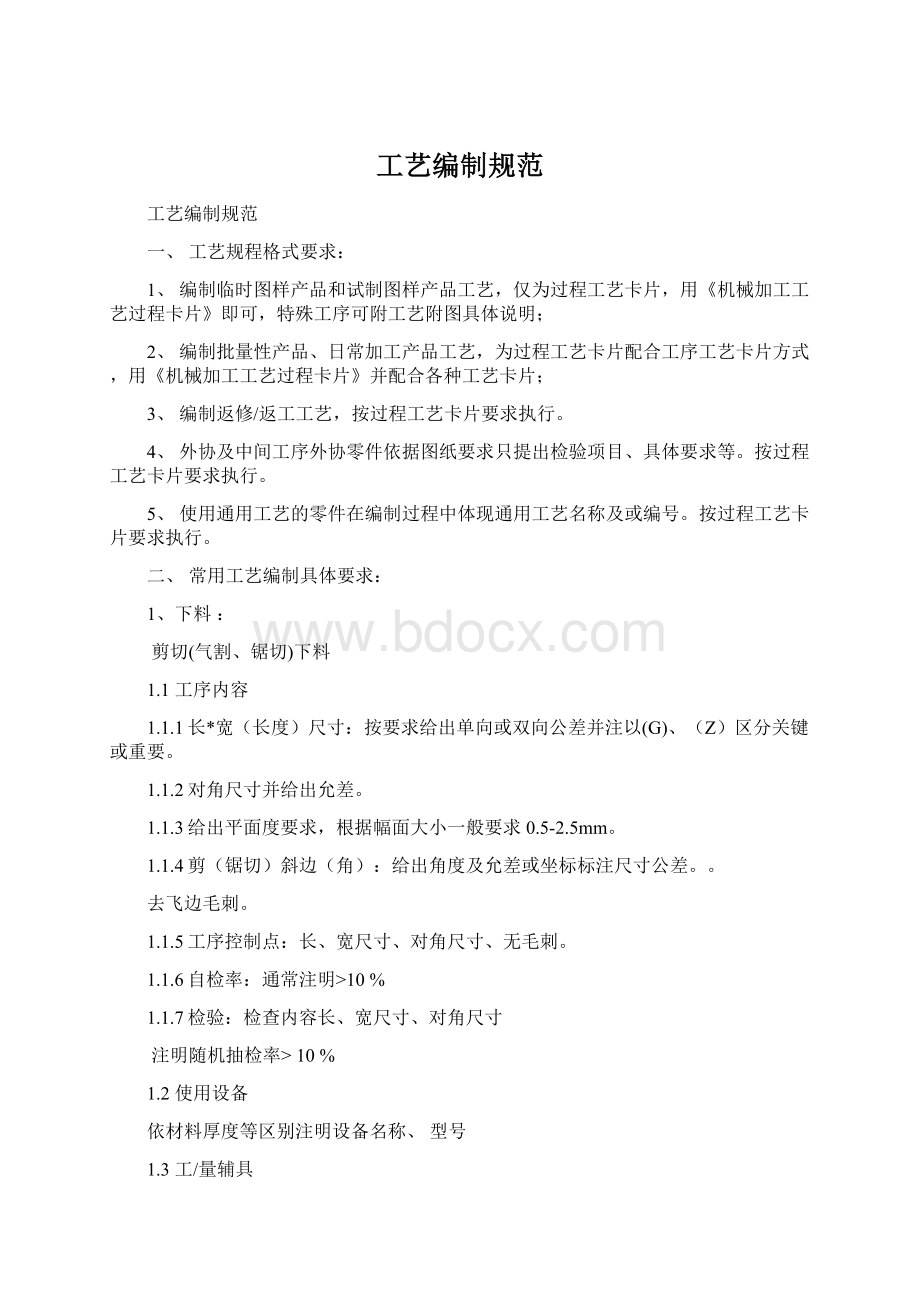
去飞边毛刺。
1.1.5工序控制点:
长、宽尺寸、对角尺寸、无毛刺。
1.1.6自检率:
通常注明>
10%
1.1.7检验:
检查内容长、宽尺寸、对角尺寸
注明随机抽检率>
10%
1.2使用设备
依材料厚度等区别注明设备名称、型号
1.3工/量辅具
1.3.1注明使用量具名称、规格
1.3.2注明去毛刺使用工具名称、规格
1.4注明同时加工件数、人员密度、单件工时
2、气割
2.1工序内容
2.1.1一般以工艺附图形式给出气割部位并注明允差。
2.1.2工序卡或必要时依据材料厚度注明割炬割嘴型号,氧气、乙炔气压力。
2.1.3注明划线或使用仿形样板。
2.1.4气割斜边(角):
给出角度或坐标标注尺寸及允差。
2.1.5去割渣毛刺。
2.1.6工序控制点:
尺寸、角度、无毛刺。
2.1.7自检率:
2.1.8检验:
检查尺寸、角度、无毛刺。
2.2使用设备
仿形切割机注明型号(如CG2-150A)或氧气、乙炔、割嘴号
2.3工/量辅具
2.3.1注明使用模板编号等。
2.3.2注明使用量具名称、规格
2.3.3注明去毛刺使用工具名称、规格
2.4注明同时加工件数、人员密度单件工时及准结工时
3、折弯
3.1工序内容
3.1.1一般以工艺附图形式给出折弯线尺寸,按要求给出单向或双向公差并注以(G)、(Z)区分关键或重要。
3.1.2按需要给出或经调形满足垂直度、平行度、平面度等形状和位置公差要求。
3.1.3折弯斜边(角)时按需要给出角度及公差。
3.1.4按需要注出调形、打磨压痕等。
3.1.5工序控制点:
折弯后尺寸、垂直度、平行度、平面度、无压痕等。
3.1.6自检率:
30%
3.1.7检验:
检查内容折弯后尺寸、无压痕等
3.2使用设备
依材料厚度、幅面、折弯半径等区别使用折弯机或油压机,注明设备名称、型号。
3.3工/量辅具
3.3.1注明使用压形模具图号或编号、规格等。
3.3.2注明使用量具名称、规格
3.3.3注明去除压痕使用工具名称、规格
3.4注明同时加工件数、人员密度单件工时等
4、钻孔(扩孔攻丝)
4.1工序内容
4.1.1注明划线钻孔或利用钻模钻孔并附以附图给出划线基准及钻孔定位基准。
4.1.2除原图给定公差外,其余均按自由公差给出孔径、孔位、孔距公差数值并按要求注以(G)、(Z)区分关键或重要。
4.1.3注明钻模检验频次。
4.1.4按需要给出需分次扩孔时各次钻孔直径。
4.1.5按需要给出需铰孔时底孔直径。
4.1.6按需要给出螺纹孔底孔直径。
4.1.7工序卡或需要时给出切削用量(主轴转速、进给量、切削速度等)。
4.1.8去孔口毛刺。
4.1.9工序控制点:
孔径、孔位、孔距
4.1.10自检率:
30%
4.1.11检验:
检查孔径、孔位、孔距
40%
4.2使用设备
依孔径、零件幅面尺寸等注明使用设备名称、规格。
4.3工/量辅具
4.3.1注明使用钻具图号或编号、规格等。
4.3.2按需要给出钻头(铰刀、丝锥)规格。
4.3.3按需要给出去孔口毛刺所需工具名称、规格。
4.4注明同时加工件数、人员密度、单件工时等。
5、焊接
5.1工序内容
5.1.1零件焊接按图纸要求焊接。
5.1.2总成图焊接需注明组成零件图号、名称、件数(材料)并注明零件组合顺序,需要时以附图注明基准、定位方式等,分别注明使用手工电弧焊或CO2保护焊并给定使用电压、电流、焊速等参数。
注明使用焊条或焊丝材质、直径、规格等。
5.1.3注明焊接要求(牢固可靠、无虚假焊等缺陷等)。
5.1.4注明去除焊渣、飞溅等
5.1.5需要时注明焊后调形并给出或平行度、平面度等要求。
5.1.6工序控制点:
焊缝高度符合要求。
焊缝平整、无缺陷、无焊渣、飞溅等。
5.1.7自检率:
5.1.8检验:
检查焊缝高度、平整度、无缺陷、无焊渣、飞溅
5.2使用设备
依需要注明使用设备名称、规格。
5.3工/量辅具
5.3.1注明使用焊具图号或编号、规格等。
5.3.2按需要给出焊条、焊丝型号、牌号、规格等
5.3.3按需要给出清渣所需工具名称、规格等。
5.4注明同时加工件数、人员密度、单件工时等。
6、抛丸
6.1工序内容
6.1.1注明均匀去除表面油污与氧化层,但不得出现由于抛丸时间过长或压力过大产生的表面凹坑与麻点。
6.1.2对易变形零件注明防变形措施,(上道序增加加固措施,抛丸前注意吊挂方式等),需要时注明抛丸最长时间。
6.1.3工序控制点:
表面光整、无变形
6.1.4自检率:
6.1.5检验:
检查焊缝平整、无缺陷、无焊渣、飞溅
6.1.6对于厚度小于4毫米的薄板件进行手工除锈,给出工具、工时。
6.2使用设备
依需要注明使用双钩式或辊道式抛丸机。
6.3工/量辅具
略
6.4注明同时加工件数、人员密度单件工时.。
7、涂装(电泳或喷漆)
7.1工序内容
7.1.1图纸对涂装有具体要求的依零件形状、体积等注明使用喷漆或电泳。
并提出按《表面处理工艺规程》进行并执行“油漆(电泳)通用工艺”且符合或TQ3(TQ4)SQB03005-2009要求.测量设备:
测厚仪。
并标注漆膜厚度(G)和(Z)。
7.2使用设备
略
7.3工/量辅具
7.4工时
8、零件标识
8.1工序内容
8.1.1有规定零件永久标识的附注标识内容和格式。
8.1.2需要打标牌的给出标牌位置和式样。
8.1.3纸质标签的给出粘贴位置。
8.2使用设备/工具
给出使用的设备、工具的名称、型号
机加工工艺
1车加工
1.1工序内容
1.1.1下料依据所加工零件的直径、长度及机床性能提出下料尺寸为单件或多件。
当下料尺寸为多件时应增加切刀量和两端平端面余量。
实际下料尺寸一般为“零件净长度*所制件数+(件数-1)*(4+3)+3”。
对直径大于60mm的轴类下料应提出垂直度要求。
1.1.2车制(轴类)
1.1.2.1对轴类零件依零件形状、加工部位及长径比等提出要否制出中心孔,(一般长径比>
6时应制出)。
并根据中心孔用途、零件质量等给出中心孔类型。
1.1.2.2依据零件形状、精度等要求提出工步顺序、夹持方法等。
依据毛坯类型、材料等区别使用刀具等。
1.1.2.3对需要分粗加工、半精加工、精加工的零件给出每道序预留余量及公差要求。
1.1.2.4对有中间工序热处理要求的零件给出粗加工预留余量、避免应力集中应制出的R圆角尺寸、热处理后经调形应满足的径向跳动等要求。
1.1.2.5对内螺纹提出底孔直径及公差要求。
1.1.2.6必要时对未注公差按SQB03016-2008给出具体公差数值。
1.1.3车制(盘类)略
1.2工/量辅具
1.2.1对轴类零件依据长度等必要时提出使用跟刀架、中心架等辅助工具要求。
1.2.2对盘类零件需要时提出二类工装,并提出辅具名称、规格、型号(编号)等
1.2.3依据零件尺寸、形状、精度等提出所需量具名称、规格。
1.2.4依据零件尺寸、体积(质量)提出人员密度、单件工时等。
1.2.5根据择优方案提出应转序流程。
2铣加工
2.1.1下料依零件图尺寸、形状提出下料方式(剪切、锯切、气割等),并对需加工面根据实际情况确定预留余量。
2.1.2铣削
2.1.2.1对需专用铣具的零件提出铣具名称、编号等。
2.1.2.2对通用件提出或采用平口虎钳等装夹方式。
2.1.2.3对有中间工序热处理要求的零件给出粗加工预留余量及热处理后经调形应满足的平面度要求等。
2.1.2.4依据材料、加工部位、形状、尺寸等给出所用刀具名称、规格。
2.1.2.5依据零件尺寸、形状、精度等提出所需量具名称、规格。
2.1.2.6依据零件尺寸、体积(质量)提出人员密度、单件工时等。
2.1.2.7根据择优方案提出应转序流程。
三、工时核定原则:
1、常规批量产品工时核定,以操作、辅助工时的实际工时为标准,结合生产加工实际情况,对常规产品进行工时核查。
2、临时产品工时核定,由工艺员根据经验确定,在工艺规程中给出。
3、试制产品工时核定,由工艺员根据经验确定,对于实际加工过程难度较大的产品,由车间班组长和主任核定,工艺员确认后可增加试制工时。
4、返修、返工工艺工时由工艺员根据实际情况提出并经技术领导签字确认。
5、外协及中间工序外协零件工时一般在工艺中不出现。
6、使用“通用工艺”零件的工时在工艺编制过程中不再体现。
编制:
审核:
批准: