焦化事故案例分析与处理文档格式.docx
《焦化事故案例分析与处理文档格式.docx》由会员分享,可在线阅读,更多相关《焦化事故案例分析与处理文档格式.docx(25页珍藏版)》请在冰豆网上搜索。
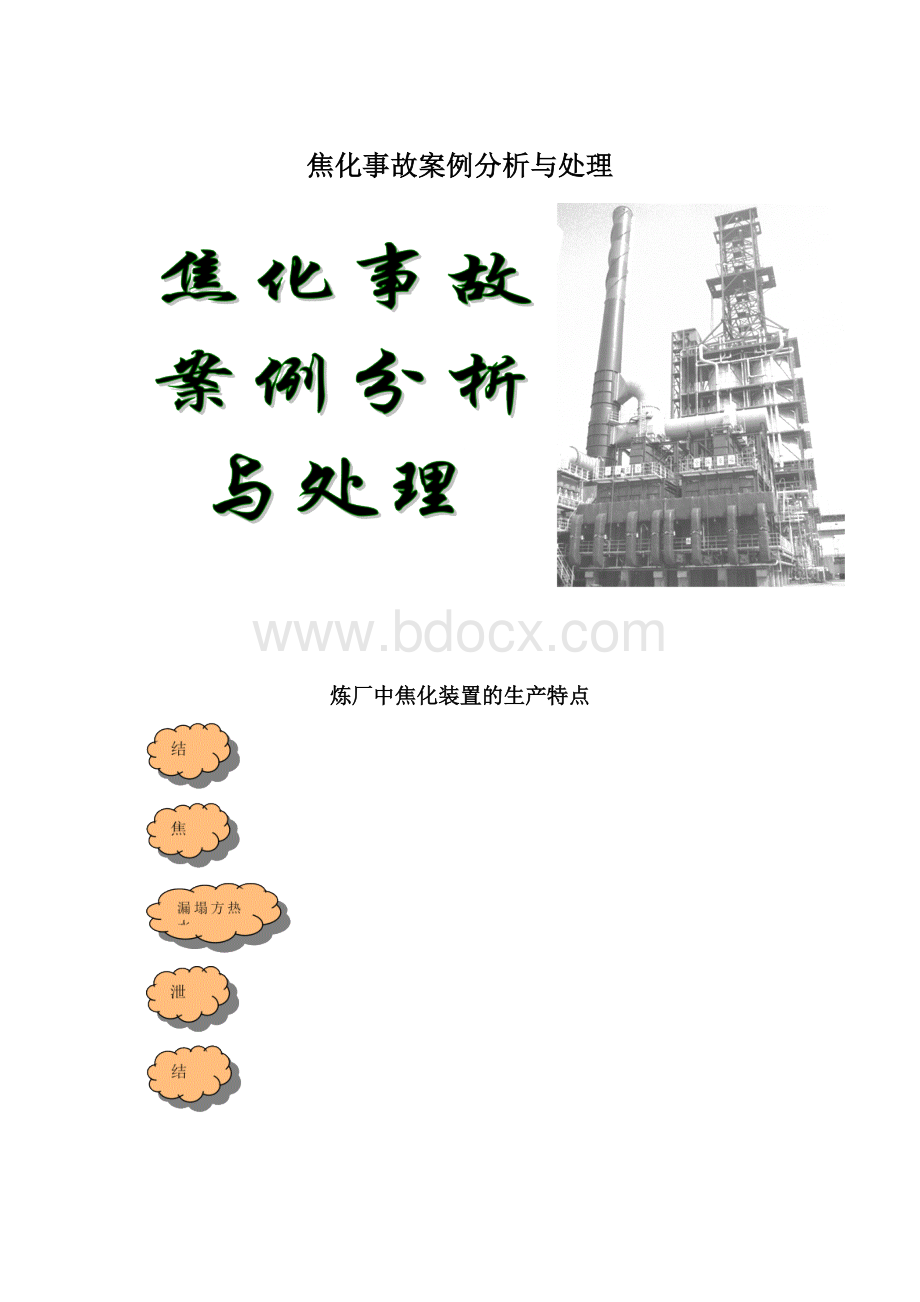
采取措施:
塔顶注水:
在分馏塔顶循泵抽空期间,由于采用冷回流控制塔顶温度,塔顶温度较高,一般在130~150℃之间,致使部分胺盐沉积在分馏塔顶空冷器管束中,将部分管束结死,分馏塔与气压机入口之间压降增大,于2004年7月份对分馏塔顶一组空冷器用高压水对其进行了清洗,并在入口增设了一条注水线。
采用提高塔顶温度的办法促使部分胺盐转移到塔顶空冷器,并将注水线定期投用冲洗,这样一方面减轻了分馏塔塔盘的结盐、一方面解决了分流塔顶空冷结盐问题。
在线水洗:
自2004年8月份起对焦化分馏塔进行了在线水洗,过程如下:
加热炉降处理量:
缓慢降低加热炉东、西分支进料量至28t/h,注水量随进料量调整。
根据分馏塔底液位相应调整循环油回炼量。
气压机、吸收稳定视加热炉、分馏岗位操作情况相应调整,分馏岗位加大冷回流流量逐渐将分馏塔顶温降到98℃。
注入流程:
新鲜水-粗汽油泵-顶循回流调节阀-顶循环油返塔线。
控制好分馏塔顶温在98℃以下,打开顶循环泵入口排凝见水后,加大分馏塔底循环油系统、蜡油、中段油循环取热负荷,同时避免水洗水落至柴油集油箱。
水洗过程中,分馏塔顶部较轻组份可能进入塔柴油组分中,应加强对柴油颜色、含水情况的监测。
顶循环泵入口排水中CL-及氨氮化验分析均≯300mg/L时,停注新鲜水。
水洗完毕,按步骤逐步提高处理量,恢复正常生产。
通过在线水洗,分馏塔操作恢复正常,较大程度的提高了产品质量、轻质油收率和装置处理量,避免了非计划停工。
水洗过后,分馏塔的平稳操作能维持一个月左右,顶循泵抽空严重时还要进行在线水洗。
在按照上述工艺过程添加结盐控制剂后,未出现顶循泵晃量的现象,分馏塔操作恢复正常,结盐控制剂作用效果明显。
1.2焦炭塔顶大油气线结焦
某焦化装置顶部短节处结焦后管线由原来的φ350缩径到不足φ150,且结焦情况呈均匀沿管径分布状。
在焦炭塔大油气线集合管处管线内壁表面集结有厚3-5cm致密焦层,隔断阀阀道内还附有厚10cm油泥状疏松焦粉,致使阀板失去弹性,无法正常密封。
由于焦的硬度很大,对大油气管线采用高压水力和爆破的方法进行除焦。
由于原料性质变差和焦炭塔的超负荷生产,导致焦化装置在焦炭塔顶出口线、大油气管线结焦的原因就是渣油在发生裂化反应的同时又产生一种副反应即缩合反应,小分子的烃类缩合成大分子的烃类即产生管线结焦。
生产中的结焦因素有:
∙大油气管线温度超过油品临界分解温度
∙原料性质变差
∙加热炉出口温度
∙加热炉炉管注汽(注水)量
∙吹汽量的影响
∙焦粉(或泡沫)的夹带
∙急冷油注入量和位置
焦炭塔顶出口线结焦主要和焦炭塔的操作有关,如果急冷油注入点距油气线出口较远,不能雾化直接将刚一出塔的油气温度降低到临界分解温度以下,这样在注
急冷油前的一段管线非常容易结焦,特别是油气刚出口的立管上。
采取措施
各炼厂焦化装置在长期的实践中总结了不少经验,提出了许多行之有效的方法。
●在油气管线上加法兰,当油气管线结焦时可以拆掉清焦。
●在油气出口管线上加过滤器。
●将急冷油注入油气刚出焦炭塔的根部,而且急冷油管线也增大到DN40。
●采用斜插式注入,有的采用内置环型喷雾管注入,均可有效的防止了油气线结焦。
见下图
通过进料量和消泡剂控制适宜的气速和泡沫层高度。
另外注入缓焦剂对减少系统结焦也非常有利。
1.3
分馏塔侧线带焦粉
由于分馏塔的空塔气速较大、塔的结构和塔板设计的不合理,使焦化富气、汽油、含硫污水、柴油和蜡油携带焦粉,影响产品质量。
分馏塔侧线带焦粉和焦炭塔与分馏塔的设计及操作有密切的关系。
●首先应使焦炭塔内的泡沫焦不被携带到分馏塔,必须控制适宜的气速和泡沫层高度,一旦被携带,应考虑降低温度,终止导致结焦的缩合反应,并在分馏塔控制气速使之沉降到塔底,
●另外要加强馏分油洗涤阻挡焦粉不被携带到蜡油集油箱以上,热态的焦粉类似絮状沥青质,个人认为洗涤比沉降更有效。
在分馏塔改造不便时,也可以通过自动反冲洗过滤器除去富气、汽油、含硫污水、柴油和蜡油携带的焦粉,目前采用此措施是非常有效的,在中石化九江分公司已经成功应用在蜡油中,如右图。
消泡剂注入位置、数量和消泡剂性质不合适会使消泡剂中的硅元素进入焦化产品,影响产品加氢精制等环节。
1.4
分馏塔底等部位的结焦事故
案例1描述:
2004年7月中旬某炼厂焦化装置发现焦炭塔大油气隔断阀靠总管处阀杆弯曲变形,有焦粉,油气隔断阀无法关严,经过多次处理后仍无法正常密封。
分馏塔塔底循环泵和重蜡油泵经常出现抽空情况,重蜡油换热器管程堵塞,分馏塔底循过滤器上游手阀关不严,重蜡油过滤器堵塞严重,过滤器无法进行正常的清理,影响到分馏塔的正常运行。
现象1:
分馏塔自下而上第1个人孔处已被结焦堵死;
现象2:
从第2人孔处观察塔内人字档板表面亦覆满油泥状焦粉,人字档板底部已结焦成三角形;
现象3:
蜡油集油箱处结焦情况亦很严重,集油箱底部油泥状焦粉堆积高度达0.3-0.5米;
现象4:
中段回流第11-17层塔盘处条形导向塔盘表面被焦粉淤积已无法自由升降;
17-24层塔盘处无明显结焦情况24-27层塔盘表面有细小焦粉沉积,浮阀粘连后无法自由升降。
同时塔底抽出线和重蜡油抽出线的过滤器也被焦粉堵死。
以上是造成分馏塔塔底循环泵经常抽空的原因。
案例2描述:
1997年,中石化荆门分公司焦化装置在加工南阳、江汉减压渣油及半沥青(脱油沥青)过程中,开工不到一年时间,由于原料密度原因,原料泵、辐射进料泵多次不上量,一度造成装置停工;
分馏塔、辐射进料泵出口、循环油线、加热炉管(结焦20mm)、焦炭塔顶油气线等部位结焦。
同时出现焦炭、焦粉量上升;
焦炭忽软忽硬,多次塌方,损害设备(2004年改为井架),1997年7月,被迫检修,分馏塔底及换热板严重结焦,用风镐、铁锤才能清除。
渣油是以沥青质和依附于它的胶质为分散相,以油分和部分胶质为分散介质的胶体分散体系,加热、溶剂稀释等都会引起分散相与分散介质之间的失衡,而导致沥青质的聚结和沉积。
高沥青质的渣油由于沥青质含量高,往往会造成渣油中的各组分失衡,渣油的稳定性变差,极易出现相分离现象,给渣油的正常储存、运输和加工带来困难。
渣油在转化到一定深度后,体系中沥青质的含量超过了能稳定地保持其胶体分散状态的限度,胶体分散状态开始被破坏,部分沥青质聚沉发生了相分离。
在分出的新相中,沥青质快速地进行缩聚反应生焦。
因此,要想控制渣油处于不生焦状态,就必须保证渣油胶体分散体系的稳定性,避免出现相分离和沥青质的聚沉。
高沥青质的渣油热稳定性差,极易出现相分离和沥青质的聚沉现象,在较低的温度下就会导致焦炭的生成,增加了加工难度。
加强原料跟踪管理:
渣油原料的混兑、兑加催化油浆;
做好操作条件的优化总结工作:
不同原料的不同操作条件;
采取蜡油下回流量可以有效控制分馏塔底的温度。
分馏塔底的温度≯365℃,要比常规原料焦化低10-20℃。
注入消泡剂;
监控焦层高度;
原料注缓焦剂、抑焦增收剂等方法。
1.5
焦炭塌方事故
加工高沥青质原料(荆门),弹丸焦从焦炭塔低的出焦口大量滚落,烫伤出焦工,球状焦炭堆积在焦炭塔底,影响正常生产。
重油在液相碳化过程中,其中的稠环芳烃逐渐经热解及缩聚并定向排列形成不溶于母液(油)的球状塑性物,即所谓的中间相小球体,小球体内部有层次地聚集着很多稠环芳烃的分子。
生成的小球体有一个成长、相遇和融并、增粘和老化,以及定向和固化的变化历程。
中间相小球体充分长大、融并、定向,最后固化为焦炭。
在处理纳波油等高沥青质渣油,可生成大量的直径为2~5mm弹丸焦炭,其中伴有排球大小的圆球焦,造成焦炭塔振动。
生产中主要有如下表现:
易造成加热炉炉管结焦。
易形成弹丸焦,焦炭塔的震动和出焦时的塌方威胁装置的安全生产。
在焦炭塔内形成的泡沫层高,更易造成焦粉携带,进而造成油气线、分馏塔底结焦;
堵塞加热炉辐射进料泵,加快加热炉炉管的结焦;
可造成液体产品中携带焦粉。
降低焦化原料的沥青质含量是抑制弹丸焦生成的有效措施。
采取加入富芳组分;
提高循环比;
降低焦化反应温度;
提高焦炭塔操作压力;
弹丸焦容易造成除焦时塌方事故,因此要增加除焦时拆卸底法兰的安全防范措施。
普通焦和弹丸焦的外形分别见下图。
图1普通焦图2弹丸焦
2
重油自燃案例
案例1
热油喷出烧伤仪表维修人员:
1995年4月8日,某炼厂的加氢裂化车间经检修后进行开工,期间仪表工处理一液面计,由于一次手阀没有完全关闭,在拆卸放空堵头的时候,高温热蜡油喷出并立即自燃。
扑救无效后,装置只能紧急停工,现场仪表工面部、手部2%被II°
烫伤。
案例2
1988年1月16日,某车间进行催化油浆的试验过程中,操作工人不清楚正确的采样口位置,而在泵出口处进行采样,由于天气冷,采样口被冻凝,无法采样。
当操作工开启采样阀门后,正准备用蒸汽吹扫时候,热油浆喷出自燃着火。
火势太大人员无法接近阀门,在上游进行切断源头才遏制火势,但是造成本装置和相邻装置的停工。
采样人员的脸部、手部烫伤。
教训:
采样部位选择错误;
没有安装采样器具;
采样人员对热油性能不了解,安全意识薄弱。
案例3
1984年10月3日,某焦化炉进料泵入口过滤器的隔离阀处管线腐蚀,厚度只剩0.2-1.0毫米时突然断裂,漏出的热油自燃,操作工果断关闭过滤器前后阀门,火势很快得到控制并被扑灭。
1984年8月16日,运行中的某常减压蒸馏装置的渣油与原油换热器的渣油入口处短管腐蚀形成一个Φ70mm的孔,370℃的热油突然喷出自燃。
3
经验知识不足,责任心不强案例
1995年11月24日,某炼厂焦化车间准备点火烧焦,由于炉用瓦斯内带液态烃,点火时造成回火,火从看火孔窜出,虽然及时发现并关闭了瓦斯,但是,一名实习的大学生求知心切,在打开看火孔看火时,脸部近距离正对看火孔,瞬间回火时回避不及,右侧脸部,颈后部被烧伤,头发被烧焦。
送医院诊断为II°
烧伤3%。
经验教训:
炉用瓦斯内存液态烃没有切尽;
实习人员安全知识缺乏,看火时间和看火方法不对;
炉子点火是一个危险的作业过程,非生产人员不得进入作业现场。
1980年10月3日,某催化裂化车间工人在采样过程中,因为油浆凝固,将阀门开大后仍无法排除液体油浆,经整齐吹扫后,油浆突然喷出,烫伤采用工人的下肢,治疗休息78天。
重视提高新工人的技术素质教育,加强安全知识教育;
新工人干活要多动脑筋;
高温油品不允许直接采样,要采取安全有效措施。
凭经验疏忽检查,污水罐浮油冒油:
1995年8月28日,冷焦水分离罐实际液面高,但液位指示失灵,操作工没有现场核实,未能发现隐患,致使冷焦水分离罐发生冒罐跑油事故。
操作工没有执行岗位巡回检查制度,对冷焦水罐液位高,指示失灵的情况没有及时发现,凭个人经验的错误工作方法导致了本次事故的发生。
案例4
操作不检查,炉管结焦:
1989年7月12日,某延迟焦化车间对流分支温度达到600摄氏度时候才被司炉工发现,尽管采取了多种措施,但是为时已晚,分支已经严重结焦,无法进料,加热炉被迫熄火。
焦化的操作条件是很严格的,如有变化不能即使进行调整,酒会酿成事故,这已是很多经验教训给我们的答案。
焦化加热炉分支进料流量偏低没有及时作出调整,形成炉管结焦;
司炉工专业技术不精,思想麻痹,工作马虎,没有按时认真巡回检查,缺乏岗位责任心而造成了这起重大责任事故。
案例5
气柜检修吹蒸汽,汽停冷凝柜抽瘪:
1991年4月6日,某炼厂管网车间瓦斯压缩站进行检修,为了防止气柜筒体壁上的硫化亚铁自燃,向气柜内通入蒸汽掩护,进罐检修前,停蒸汽卸人孔,刚卸了三个螺丝就发现空气从人孔向内倒吸,工人准备下来向车间汇报处理时,还没有离开罐顶,气柜顶紧接着就变形。
案例6
2006年5月31日,在另外一起事故之后,对焦化冷焦水沉降罐进行蒸汽保护,随后又装盲板隔离处理,蒸汽停用并在唯一的一个呼吸孔装好盲板后不足5分钟,沉降罐即发生严重变形倾斜,造成二次设备事故。
事故原因及教训:
蒸汽停用时,容器内蒸汽居然冷凝体积缩小,而空气又不能及时补充入罐,造成气柜内负压,罐壁变形。
在有关操作规程中要作必要的补充说明。
案例7
1982年6月11日,焦化外送抽出油后,通知半成品罐改线进行管线吹扫,开汽9分钟后,发现罐顶窜汽,并听到一阵闷响,随即停汽,发现罐顶出现两处裂口并变形。
原因:
焦化进行扫线工作的操作工是学徒工,缺乏操作经验,扫线时把蒸汽一开到头,蒸汽量太大,罐顶排空不及,造成柜内蹩压损坏。
今后措施:
装置操作工应该熟悉所用管线和油罐的运行情况。
扫线时,应把蒸汽中的存水排放干净,然后由小到大慢慢开启扫线阀门到一定的位置,并加强与罐区的联系,以保证扫线正常进行。
对学徒工应该加强教育,未经考试合格不能独立顶岗。
4
设备、人身事故案例
4.1修理抓斗时,坠落事故
夜间修行车坠落摔伤:
1978年10月4日,延迟焦化车间抓斗班长在操作抓斗行车时,进行抱闸调节工作。
当时由于焦炭出厂困难,焦场装焦高,抓斗无处存放。
当班长站在滚筒上进行抱闸调整时候,抓斗顺焦堆斜坡下滑,脚下滚筒转动,使该名班长站立不稳坠落在抓斗内。
右腿髋关节严重脱位,骨盆粉碎性骨折、肋骨折断。
调节抱闸时。
抓斗要停稳妥,钢丝绳要处于松弛状态,严禁站在滚筒上进行抱闸调整工作。
4.2夜间修设备,三人坠落身亡事故
1977年12月8日,某催化裂化车间在“三器”升温过程中,发现催化剂储罐顶部的蒸汽抽真空器出口堵塞,车间技术人员要求夜班工人处理。
当班三名工人在拆卸抽真空器的凹凸面法兰时,连接在真空器后边重达千斤的消音器因焊接不牢固而从平台坠落,三人也因一时失去平衡从平台摔下,全部死亡。
高空及较大作业尽可能不在夜间进行,在布置工作时要慎重,全面考虑,要使工作热情和科学态度相结合;
具体工作者要听从安排和布置,不能自行其事,不能冒险蛮干或存侥幸心理。
4.3水龙带突然断裂
案例
少上一块板,影响四塔焦:
1967年3月27日,某炼厂延迟焦化车间水力除焦的水龙带换了新的以后,为了便于检查有无泄漏现象,没有将水龙带绞车上的扇形板装好。
除焦中上提水龙带时,另外一块扇形板被水龙带挤出来,卡住底座后损害转盘对轮,并使得切割器和水龙带出位破损,影响正常生产。
水龙带在绞盘上频繁盘放长期使用疲劳断裂。
除焦切换时,预充时间不够。
塌方时焦炭抱住胶管,使胶管拉断。
高压水击穿。
发现水龙带突然爆裂,应立即紧急停泵,并迅速提起钻具。
如胶管被焦炭抱住,提不动,不得硬提,维修处理。
5
公用工程案例
●谐振过电压,导致全厂停电
1991年12月4日,某炼油厂电器车间110KV总变电所发生全厂停电事故。
事故前,2#主变压器停运检修后恢复供电操作中发现110KV的II段电压指示高达132KV,随即又发现母线电压分别为70KV、90KV和120KV,在准备检查IIP.T二次电压时,IIP.T发生爆燃,110KV两段母线短路失电,为了灭火,采取全厂停电。
事故原因:
经专家确认,这次事故是由于110KV开关断口电容、母线电容与PT电感形成串联谐振过电压造成的。
高压系统中,因为电容电感造成谐振,本身具有很大的随即性,即便是参数达到了谐振条件,也不是每次都会谐振。
因此,要让运行人员了解谐振产生的原因和有效的对付措施,以防止造成全厂停电的破坏性事故。
停工、防结焦、防着火、防设备事故。
●老鼠窜入母联柜,造成短路崩烧停电
1995年6月23日,老鼠窜入某电气车间,老鼠触电引发高压配电室母联柜短路,引起总降开关跳闸,生产南区和循环水厂停电。
加强配电室的现场管理。
6
腐蚀案例
6.1焦炭塔顶油气线腐蚀减薄穿孔
金陵:
大瓦斯管线于2001年元月更换,20#碳钢,厚度12mm,操作温度为420℃。
2004年3月15日、4月17日、5月17日三次出现腐蚀穿孔,检测时厚度最薄处只有2mm左右。
材质升级为Cr5Mo。
6.2
炉管腐蚀减薄泄漏火灾、爆炸事故
茂名:
2000年6月16日,焦化车间辐射进料线一个分支阀前大小头(DN200/DN150)破裂穿孔,高温热油喷出着火,烧死一名在现场干活的操作工。
大小头材质用错,本该用Cr5Mo材质而错用普通碳钢材质。
荆门:
1997年9月14日凌晨2:
40,焦化辐射集合管处发生爆裂,2.0Mpa、390℃高温循环油喷出自燃着火,烧坏桥式抓斗、部分仪表、管线等,装置被迫紧急停工。
停工后检查发现该泄露处破裂了一个鸡蛋大小的洞,管线最薄处仅1mm厚度。
管线材质用错,而此处应该采用Cr5Mo合金材质,但是施工时采用了20#碳钢。
2004年4月,发现五个热电偶套管冲刷减薄、辐射东分支转油线直角弯头冲刷减薄穿孔;
6月6日,停工抢修时发现加热炉急弯弯头减薄严重,最薄处只有2mm左右;
同时转油线90度弯头再次出现减薄现象。
2004年,在掺炼巴士拉减渣时,介质在高流速涡流状态下,冲刷硫化膜造成冲刷减薄。
高度重视高温重油部位工艺管线及管件的材质升级,对高温重油及240℃以上部位工艺管线及管件原设计采用碳钢的均要升级为Cr5Mo材质。
设计时,应特别注意高温部位的硫腐蚀问题,与主体管线相联结的诸如:
仪表引压管、排凝管、蒸汽吹扫线等小口径管线材质相应也要采用铬钼合金钢,以确保生产过程的安全性。
检修时,不可一味抢工期,而对重要部位的Cr5Mo管线焊口不进行理化探伤检测,这在焦化装置历次抢修中时有发生;
施工时,不能随意用奥氏体钢焊条(白钢焊条)替代热507焊条,这种低匹配焊接也给装置长周期生产埋下了不安全的隐患。
6.3
硫化亚铁自燃事故
在近期国外高硫原油采购比例不断增加的情形下,硫化亚铁在炼厂加工过程中越来越普遍地存在,自燃事故也多次发生。
1996年,某常减压蒸馏装置的减压塔在检修时开启人孔后,填料发生自燃。
类似事件已经多次发生。
2004年国内某烷基苯厂,检修期间的分馏塔在开启人孔后发生硫化亚铁自燃,在午夜时,塔中部过热烧红,塔体材料的强度下降而导致塔的倾倒。
在最近焦化装置中应用的冷焦水密闭处理系统中,用铁、镁、铝等金属氧化物来和硫化氢反应,减少冷焦水中恶臭气体对周边环境的影响,但是,饱和吸附后的铁、镁、铝等硫化物遇空气也会发生氧化放热反应,当空气流通速度达到一定程度,迅速释放的热量就会损坏固定床内构件,并引爆容器内的可燃气体。
2005年5月和2006年4月,国内两个焦化装置相继发生脱硫后硫化压铁催化剂自燃,并引起容器爆炸。
在炼油过程中,管线设备中的单质铁元素是普遍存在,使得原油加工过程中的各种活性硫与单质铁元素发生系列化学反应,最终以硫化亚铁的形式集存在大空间、低流速的塔、容器内。
在检修等停工过程中,这些硫化亚铁与空气中的氧气发生放热化学反应,放这些热量没有释放和传输途径就会产生高温而损坏设备。
尤其是在填料、塔盘等内构件多的塔、容器内,硫化亚铁的积存量大,极易发生硫化亚铁自然事故。
其化学原理如下:
H2S+FeO=FeS+H2O
2FeS+5O2=2SO2+2Fe2O3+Q
在干气脱硫生产过程,常用氧化锌、氧化铁等脱硫剂进行预处理,在卸剂过程中往往会发生硫化亚铁的自燃事故。
在检修过程中,吹扫后的塔、容器用硫化压铁钝化剂进行化学处理;
用高锰酸钾、双氧水等氧化剂进行预先安全的氧化;
用水喷淋,吸收反应热,阻止高温和燃烧;
改用铜系列氧化剂进行脱硫化氢处理,使得反应产物生成稳定的硫化铜,不在与空气中的氧气发生进一步氧化反应。
改用其它的化学、物理方法替代金属氧化物脱硫工艺。
7
设计、开工阶段事故案例
设计阶段的安全要点:
一是本质安全:
如管道或设备的设计压力远大于压力源的最大压力,该管道或设备不会超压;
二是安全防护:
如焦炭塔的设计压力不可能高于原料泵出口压力,应设置安全阀,当设备超压时以保护焦炭塔;
三是安全处理:
即如炉出口管线着火,火能够及时扑灭,人能安全撤离,减少损失。
消防通道的设计、消防措施的设计、梯子平台的设计应充分考虑焦化装置易发生火灾的特点,做到安全事故及时处理。
消除安全隐患应从本质安全和安全防护着手,首先应根据工艺条件检查所有设备、管道、阀门、法兰、垫片、螺栓、螺母、仪表等是否安全可靠,如超过使用寿命或不符合安全要求应更换;
其次应分析工艺过程,对超温、超压、泄漏、误操作等,是否有相应的安全措施,如安全阀,安全联锁等,
目前国内焦化装置中的联锁主要有加热炉的安全联锁、压缩机的安全联锁、四通阀系统的PLC、水力除焦系统的PLC,和国外焦化装置中的联锁相比要少的多,建议有条件的装置可适当增加安全联锁,以保障装置安全生产。
7.1
设计缺陷案例
●计算