铸造毕业设计离心铸造工艺流程设计Word格式.docx
《铸造毕业设计离心铸造工艺流程设计Word格式.docx》由会员分享,可在线阅读,更多相关《铸造毕业设计离心铸造工艺流程设计Word格式.docx(20页珍藏版)》请在冰豆网上搜索。
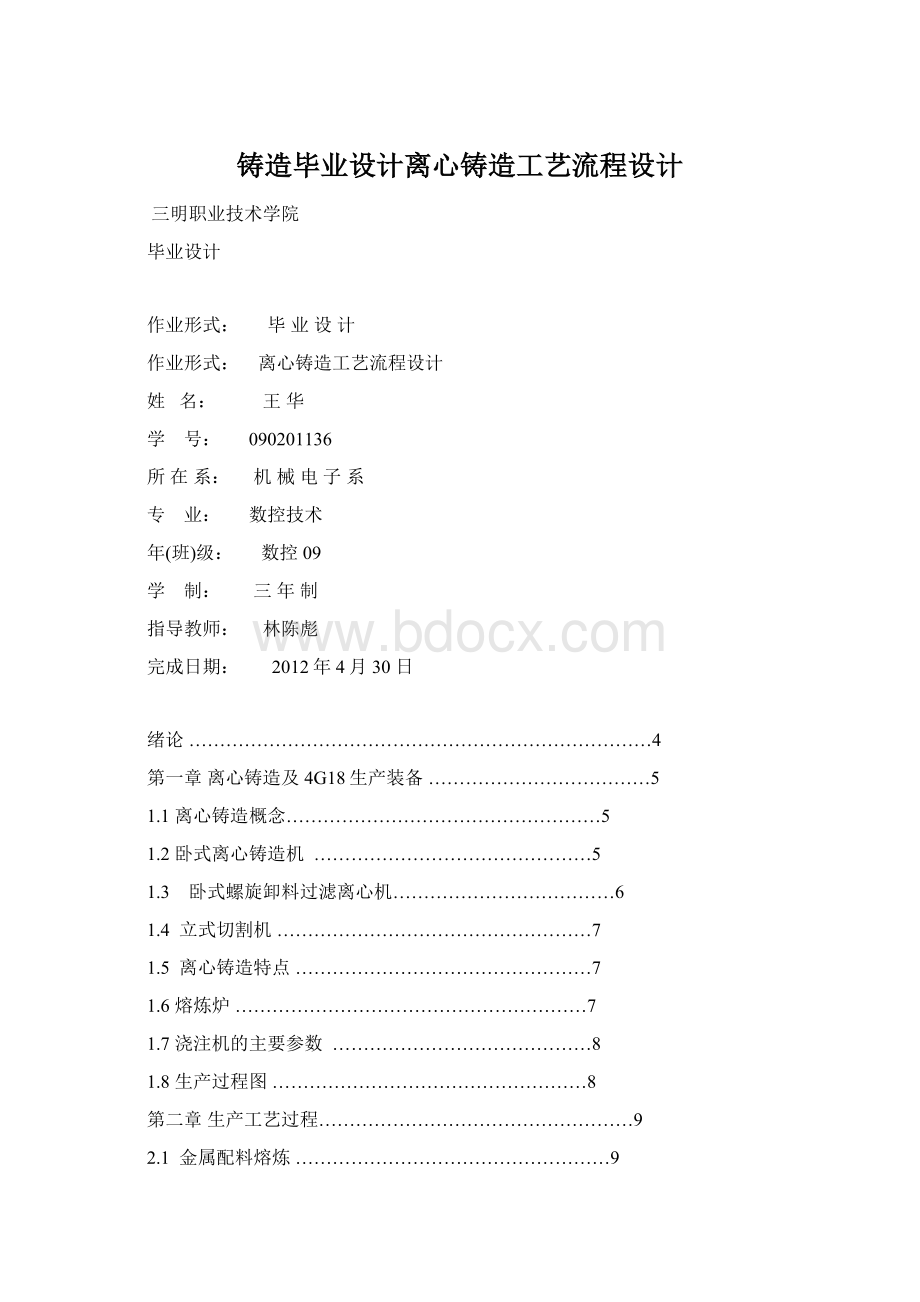
2.8主轴内上涂料……………………………………………13
2.9离心浇注…………………………………………………14
2.10冷却及取件……………………………………………14
2.11毛坯切断及检查…………………………………………15
第三章离心铸造原理及工艺……………………………………16
3.1离心力场…………………………………………………16
3.2离心力场液体自由表面的形状…………………………16
3.3离心铸型转速的选择……………………………………17
3.4离心铸造用铸型…………………………………………18
第四章影响材料性能的因素……………………………………19
4.1碳当量对材料性能的影响………………………………19
4.2合金元素对材料性能的影响……………………………19
4.3炉料配比对材料的影响…………………………………19
4.4微量元素对材料性能的影响……………………………20
第五章离心铸造汽车缸套常见缺陷分析………………………22
5.1硬度过高…………………………………………………22
5.2针孔………………………………………………………22
5.3应用效果…………………………………………………22
附录A熔炼工艺规程卡…………………………………24
附录B浇注工艺规程卡…………………………………25
附录C铸件后处理工艺…………………………………26
绪论
多年来,我国汽车缸套铸造生产工艺始终是传统的砂型铸造生产工艺,该工艺具有产品质量差,废品率较高,制造成本高,劳动强度大且劳动条件差,环境污染重,产品寿命低等致命弱点。
以充分的理论根据和丰富的实践经验较全面地分析了大胆采用国内外先进的离心铸造新工艺代替传统的砂型铸造工艺生产汽车缸套。
在二十世纪初期,国外开始研究并应用低压铸造工艺。
在第二次世界大战爆发后,北美的汽车工业和电机工业又广泛采用金属型低压铸造生产汽缸、电机转子等重要铸件。
而我国是从五十年代开始研究低压铸造,但发展一直比较缓慢。
随着汽车工业的发展,和大量新技术的采用,在上世纪末和本世纪初,低压铸造在我国得到快速发展,国产低压铸造机的功能和性能,及使用的稳定性和可靠性已经接近或达到国际先进水平,被大量用于汽车轮毂、汽车缸盖等铸件的生产。
本设计主要设计高新技术4G18系列的发动机内部的其中缸套,在福建汇华东南汽车缸套有限公司中把其缸套命名为4G18.主要体现缸套4G18的铸造装备,铸造流程,铸造工艺等特点,卧式离心铸造机。
第一章离心铸造及4G18生产装备
1.1离心铸造概念
将液态金属浇入高速旋转(通常为250~1500R/min)的铸型中,使其在离心力作用下充分填铸型和凝固而形成铸件的液态成形工艺称为离心铸造。
按照铸型的旋转轴方向不同,离心铸造机分为卧式立式和倾斜式3种。
卧式离心铸造机主要用于浇注各种管状铸件,立式离心铸造机则主要用以生产各种环形铸件和较小的非圆形铸件。
1.2卧式离心铸造机
合金液通过浇注槽落入镜型,随即从落点沿轴向流入。
图1.2.1内部机构图1.2.2外部机构
卧式离心铸造机由主机、浇注小车、取件机构、喷涂机构、电气控制系统、管模预热装置、水冷系统、安全防护罩等部分组成。
1、主机是离心铸造机的核心部分,完成管模的旋转动作。
主机由大底座、电机底座、调速电机、轴承座、轴、皮带传动、涨闸等部分组成。
2、喷涂机构完成管模的喷涂料动作,主要由气动元件、涂料罐、喷涂移动小车等组成。
3、电气控制系统由调速电机控制器、控制柜、低压电气元件、按钮、指示灯等组成,控制系统具有完善的动作互锁、过流、过载等安全保护措施。
4、安全防护罩、水冷却系统及浇注槽、支架等。
1.3卧式螺旋卸料过滤离心机
1.4立式切割机
1.5离心铸造特点
1)铸件在离心力作用下结晶,组织致密,无缩孔,缩松,气孔,夹渣等缺陷,力学性能好。
2)铸造圆形中空铸件时,可省去型芯和浇注系统。
简化了工艺,节约了金属。
3)便于制造双金属铸件,如刚套镶铸铜忖,其结合面牢固,耐磨,可节约铜合金。
4)离心铸造内表面粗糙,尺寸不易控制,需要增加加工余量来保证铸件质量,且不适宜生产易偏析的合金。
1.6熔炼炉
熔炼炉采用200~2500Hz中频电源进行感应加热,功率范围为20~2500KW。
其特点如下:
1、炉子周围温度低、烟尘少、作业环境好;
3、操作工艺简单、熔炼运行可靠;
4、加热温度均匀、烧损少、金属成分均匀;
5、铸件质量好、熔化升温快、炉温易控制、生产效高;
6、炉子利用率高、更换品种方便等;
1.7浇注机的主要参数
1.8生产过程图
A倒铁水B浇注C拔管
D清扫E喷涂 F样品
G去涂料H切割I成品
第二章生产工艺过程
2.1金属配料熔炼
1)材料的化学成分选择铸件的化学成分在很大程度上决定了铸件的金相组织,而铸件的金相组织又在很大程度上决定了铸件的力学性能,并且铸件的化学成分、铸件的金相组织和铸件的力学性能这三者均存在着十分紧密的内在联系,因此,铸件的化学成分在很大程度上决定了铸件的力学性能和其他性能。
4G18的化学成分:
化学成分
C
Si
Mn
P
Cr
S
Cu
B
2.9-3.5
2.0-2.7
0.6-1.2
0.4以下
0.1以下
0.035-0.08
2)金属炉料一般由新生铁,废铁,回炉料,铁合金组成,增加废钢加入里,可有效地降低铁水含碳量。
提高灰铸铁的力学性能,根据铁水成分要求,炉料情况,熔炼过程中元素的变化等确定炉料配比,且得让铸铁化学成分的首要环节。
4G18的原材料配料比表如图:
配合%
种类
生铁
(小焦)
4.18
1.08
0.37
0.06
0.03
(贵州)
3.98
1.39
0.76
0.21
0.037
25
废钢
0.2
0.35
轧辊屑
3.4
1.9
0.5
0.15
0.7
0.032
轴承钢
1.00
1.1
50
干屑
3.2
2.7
0.25
0.052
湿屑
0.3
回炉料
规格
品名
硬度(HRB)
C%
Si%
Mn%
P%
Cr%
S%
Cu%
B%
4G18
94—104
2.3-2.9
0.5-1.0
0.1-0.4
<
0.12
0.3-0.5
0.05-0.12
目标
3.5
1.8
0.04
0.045
3)过热熔炼:
为净化孕育处理等目的而将铁液加热到正常温度以上,都称为过热熔炼。
A.过热温度,铁液的过热温度通常为1500度,超过1550度则铸铁白口倾向大。
B.过热的作用;
1,过热可以去除杂质,净化铁液,主要是降低铁液中的溶氧量。
2,抗拉强度随铁液温度升高而增加,铁液温度小于1460度。
温度提高硬度HB增加,铁液温度大于1500度温度升高,硬度HB下降。
铁液过热温度与铸铁冶金质量指标的关系如下,过热温度升高,或热度RG提高,过热温度大于1460度。
相对硬度RH明显下降,品质系数Qi随过热温度升高而增加。
3,过热为孕育处理创造了必要条件。
4,过热可以提高铁液流动性,保证铸件健全,减少废品。
5,过热温度过高或保温时间过久,铸铁白口倾向增大,A型石墨减少,D型石墨增加,共晶团减少,故必须孕育处理,且孕育后不宜再长期保温。
2.2孕育技术
孕育处理目的在于促进石墨化,降低白口倾向,降低端面敏感性。
控制石墨形态,消除过冷石墨,适当增加共晶团数和促进细片状珠光体的形成,从而达到改善铸铁的强度和其它性能和其它性能的目的,在实际过程控制中,需要控制的参数如下:
孕育处理种类
粒度
加入里
孕育方式
孕育温度
孕育有效时间
75Si—Fe
3—5
0.3—0.6
二级孕育
1420—1480C
10分钟
液温度对孕育的影响及控制铁液温度对孕育的影响显著,在一定的范围内提高铁液的过热温度并保持一定时间,可以使铁液中残存着丰富的石墨质点,完全融入铁中,液中,以消除生铁的遗位影响,充分发挥孕育剂的孕育作用,提高铁水受孕育能力,过程控制中,对过热温度提高到1500—1520℃。
对孕育处理温度控制在1420—1450℃。
孕育剂的粒度是孕育剂状况的重要指标,对孕育效果有很大影响。
粒度过细易于分散或被氧化进入溶渣而失去作用。
粒度太大,孕育剂熔化成溶解不尽,不仅不能充分发挥孕育作用,仅而会造成偏拆,硬点,过冷石墨等缺陷。
因而对孕育剂的粒度应尽量控制在2—5MM。
保证孕育效果。
过程控制中孕育工艺主要在孕育槽孕育。
这样对一包浇注的铸件,基本可以在孕育衰退前浇注结束。
但对于比较大的件和双浇包浇注的件,不能满足要求,因而采用了晚期孕育方法。
即在浇注铸件之前,在浇包中进行浮硅孕育,这样减少了或不存在孕育衰退,提高了孕育效果。
2.3合金化处理
合金化处理向普通铸铁中加入少量的合金元素,提高灰铸铁的力学性能,在熔炼过程控制中,对合金的加入,主要是针对顾客要求
火的件和导轨比较厚的件,主要加入的合金元素及加入量。
:
常用合金元素及含量:
0.4—0.7%
0.05—0.08%
0.1—0.2%
这样在一定程度上保证了由于CE值的提高造成性能的下降,而且对火件来说提高了
火的
透性。
保证了
火深度。
2.4对熔炼过程的温度控制
图中,电炉熔炼过程曲线中O-A段是投料熔化过程,这个阶段重点控制的加料顺序,按废钢,机铁,生铁的先后顺序进行加料,为了减少含金元素的烧损。
铁合金应在最后加入,当冷料全部化清后升温至1450℃即A点,如果低于1450℃时,则有增加碳剂或铁合金不完全溶解的危险,在A-B段,应如下处理:
1)测温
2)扒渣
3)取样分析化学成分
4)利用热光谱仪对常规元素和微量元素进行分析
5)取三角试片测CW值
2.5三角试片的控制
根据各种检测结果对铁水进行调整后,继续送电10分钟后重新取样分析,确定所有数据正常后继续升温至1500℃左右。
即C点。
在C-D段让铁水静置5至10分钟后取三角试片测试CW值,测温后准备出铁。
2.6涂料配置
金属型内的涂料对铸件质量有较敏感的影响。
主要选用水基石英粉涂料;
其绝热性能较好,但涂料烘干后易出现翘壳,局部翘曲处铸件接触金属型,形成莱氏体,硬度高,使铸件局部切割困难,但其附着力强,效果较好。
故以此为基础,加入适量硅藻上。
合金种类
涂料配方%(重量)
备注
铸铁
石英粉陶土外加水
205
表面再涂石墨涂料总厚度2—3毫米
2.7主轴预热
主轴加热对铸件质量影响较大,且对主轴的使用寿命的长短影响也很大。
温度偏低,铸件外壁易出现气孔,温度偏高,铁水与主轴内部发生捏合,使得涂料失去了保护作用。
让铸件无法拔出。
使得主轴失去工作能力。
因此,主轴加热温度应控制适易。
控制主轴温度在230—290℃(主轴温度调整时间=冷却水时间调整+冷却水阀手柄位置)
2.8主轴内上涂料
为减少铸件的表面渣孔等废品及承口的安装尺寸,对管模的承口及内壁需要进行清理,以保证管子的安装和喷涂工序要求。
涂料在管模内壁起到保护管模和稳定铸件金相组织的作用,把配制好的涂料经过喷涂管喷到管模内壁,等到其靠管模本身温度烘干后再进行铁水浇注。
喷涂参数:
运行名称
目标值
喷涂泵进气压力
0.3—0.6MPa
空气压力
0.1—0.3MPa
10秒涂料喷出量
260—300/10S(双向)
喷涂转速
490—510
涂料粘度
45—55s
2.9离心浇注
将承口芯安装到离心机上,球化合格的铁水倒入定量包内,按照工艺规定要求,设定孕育剂加入量、管模粉加入量,离心机的旋转速度,铁水随着定量包的翻转浇注在旋转的管模内壁,并凝固成管子。
浇注参数:
名称
浇注转速
730—750
浇注旋转时间
130—150秒
小车行走速度
110
孕育量
180—220g
浇注重量
19.2—19.8kg
2.10冷却及取件
当管模内的铸件温度降到800℃左右时,按下取件按键,取件钳将铸件从管模内取出,并送至接料架上。
自然冷却扒管阶段
2.11毛坯切断及检查
送入螺旋卸料过滤离心机中进行铸件脱模,时效处理。
最后铸件清理,送入切割机中切割成长度为180mm的缸套。
切割成品
第三章离心铸造原理及工艺
3.1离心力场
重度:
r=pg
有效重度:
r’=pw~2r
重力系数:
G=w~2r/g
3.2离心力场液体自由表面的形状
卧式离心铸造时液态金属自内由表面的形状。
当不考虑重力场的影响时:
mw~2xdx+mw~2ydy=0
对此式积分得:
X~2+y~2=r~2
由此可推卧式离心铸造时,如果不考虑重力场的影响,液态金属的自由表面应为以旋转轴为轴线的圆柱面。
由于重力场的影响:
Va<
Vb
根据水力学的液态流动的连续性原理:
VaFa=VbFb
Fa和Fb为A,B两处的断面面积
因为Va<
Vb所以Fa>
Fb
从而出现圆柱形内表面向下偏移的现象。
3.3离心铸型转速的选择
选择离心铸造的转速时,主要应考虑两个问题:
1)离心铸型的转速应保证液体金属在进入铸型后立刻能形成圆筒形,绕轴线旋转;
2)充分利用离心力的作用,保证得到良好的铸件内部质量,避免铸件内部产生缩孔、缩松、夹杂和气孔。
卧式离心铸造时,为保证液体金属在型壁上的成形,应使液体金属自由表面上最高点处的金属质点所产生的离心力大于或等于重力,即:
Mw~2r>
=mg
若不能保证此条件,则在出注时会出现如下图所示雨淋现象。
铸件中将出现夹渣等缺陷。
3.4离心铸造用铸型
卧式悬臂离心铸造机上的金属铸型按其主体的结构特点可以分为单层金属型和双层金属型两种。
第四章影响材料性能的因素
4.1碳当量对材料性能的影响
决定灰铸铁性能的主要因素为石墨形态和金属基体的性能。
当碳当量(CE=C+1/3Si)较高时,石墨的数量增加,在孕育条件不好或有微量有害元素时,石墨形状恶化。
这样的石墨使金属基体能够承受负荷的有效面积减少,而且在承受负荷时产生应力集中现象,使金属基体的强度不能正常发挥,从而降低铸铁的强度。
在材料中珠光体具有好的强度、硬度,而铁素体则质底较软而且强度较低。
当随着C、Si的量提高,会使珠光体量减少,铁素体量增加。
因此,碳当量的提高将在石墨形状和基体组织两方面影响铸铁铸件的抗拉强度和铸件实体的硬度。
在熔炼过程控制中,碳当量的控制是解决材料性能的一个很重要的因素。
4.2合金元素对材料性能的影响
在灰铸铁中的合金元素主要是指Mn、Cr、Cu、Sn、Mo等促进珠光体生成元素,这些元素含量会直接影响珠光体的含量,同时由于合金元素的加入,在一定程度上细化了石墨,使基体中铁素体的量减少甚至消失,珠光体则在一定的程度上得到细化,而且其中的铁素体由于有一定量的合金元素而得到固溶强化,使铸铁总有较高的强度性能。
在熔炼过程控制中,对合金的控制同样是重要的手段。
4.3炉料配比对材料的影响
过去我们一直坚持只要化学成分符合规范要求就应该能够获得符合标准机械性能材料的观点,而实际上这种观点所看到的只是常规化学成分,而忽略了一些合金元素和有害元素在其中所起的作用。
如生铁是Ti的主要来源,因此生铁使用量的多少会直接影响材料中Ti的含量,对材料机械性能产生很大的影响。
同样废钢是许多合金元素的来源,因此废钢用量对铸铁的机械性能的影响是非常直接的。
在电炉投入使用的初期,我们一直沿用了冲天炉的炉料配比(生铁:
25~35%,废钢:
30~35%)结果材料的机械性能(抗拉强度)很低,当我们意识到废钢的使用量会对铸铁的性能有影响时及时调整了废钢的用量之后,问题很快得到了解决,因此废钢在熔化控制过程中是一项非常重要的控制数。
因此炉料的配比对铸铁材料的机械性能有着直接的影响,是熔炼控制的重点。
4.4微量元素对材料性能的影响
以往我们在熔炼过程中只注意常规五大元素对铸铁材质的影响,而对其它一些微量元素的作用仅仅只是一个定性的认识,却很少对他们进行定量的分析讨论,近年来,由于铸造技术的进步,熔炼设备也在不断的更新,冲天炉已逐渐被电炉所代替。
电炉熔炼固然有其冲天炉不可比拟的优点,但电炉熔炼也丧失了冲天炉熔炼的一些优点,这样一些微量元素对铸铁的影响也就反映出来。
由于冲天炉内的冶金反应非常强烈,炉料是处于氧化性很强的气氛中,绝大部分都被氧化,随炉渣一起排出,只有一少部分会残留在铁水中,因此一些对铸件有不利影响的微量元素通过冲天炉的冶金过程,一般不会对铸铁形成不利影响。
在冲天炉的熔炼过程中,焦炭中的氮和空气中的氮气(N2)在高温下,一部分分解会以原子的形式溶铁水中,使得铁水中的氮含量相对很高。
据统计自电炉投产以来,由于铅含量高造成的废品和因含铅量太高无法调整而报废的铁水不下百吨,而因含氮量不足造成的不合格品数量也相当高,给公司造成很大的经济损失。
第五章离心铸造汽车缸套常见缺陷分析
离心铸造汽车缸套,生产效率高,铸件质量好。
但是由于工艺参数或铸件化学成分控制不严格,操作部当,也易出现各种缺陷。
5.1硬度过高
硬度>
350HBS,使铸件外表面加工困难,是金属型离心铸造汽车缸套常见的缺陷。
这种缺陷常因材料选择不当,过多添加含合金元素或涂料层提起前崩溃所致。
为防止硬度过高,在适量合金元素和过冷度条件下,加强孕育处理,使之形核多,而且生长快,合理选择涂料并保证涂料层厚度完整性,铸件硬度可稳定在212—280HBS范围内。
5.2针孔
汽车缸套工件面经研磨,在镜面光面上如出现多量孔径大于0.3mm的孔洞,则为针孔缺陷。
缺陷的成因是由于离心铸造时,发生双面结晶,凝固被前沿自外向里推进的同时,表面凝固也自里向外延伸,后凝固层较薄,使得两个凝固被前汇合区产生疏松所致。
这一疏松区恰好位于加工后气缸套的内表面,通常在浇入端铸件后壁处较多。
研磨后用灯光照射,仔细观察方可发现。
防止这种缺陷的方法是调整浇注速度及化学成分,并在铸件壁厚处采用吹风的方法进行消除。
5.3应用效果
离心铸造比砂型铸造有显著地经济效果。
主要有一下几点:
1,控制了铸造缺陷,提高了产品质量。
采用离心铸造,铸件中的气孔,熔渣等夹杂物因密度小均集中在内表面,面金属的结晶则从外向内呈方向性结晶,因而铸件结晶细密、无缩孔、疏松、气孔、夹杂等缺陷,力学性能较高,铸造缺陷得到了控制。
力学性能优于砂型铸造,成品率由原来的砂型铸造的50%提高到85%以上。
2,减少了工作,节约了能耗和工时。
离心铸造不用型芯和浇注系统,减少了碾砂、造型、烘干及合箱的工序,使铸造工艺简化,并节省金属、人力及能耗,生产成本现在显著降低,提高了经济效益。
3,改善了劳动环境,减轻了劳动强度。
4,提高了汽车缸套组织的致密性。
气密性高、耐磨性强、节油和维修方便,使用寿命长,提高了发动机整体性能等,其力学性能随之大幅度提高。
抗弯强度在570MPa以上,扰度在1.2mm以上,且性能稳定。
使用寿命有明显的提高。
附录A熔炼工艺规程卡
材料
铜、铁
熔炼炉
牌号
2#
技术
参数
项目单位数据
额定容量t0.5
液态钢/铁水最大容量t0.55
液态钢/铁水工作温度℃1500
最高工作温度℃1700
炉衬厚度mm150
感应圈内经φmm1410
感应圈高度mm1620
每炉熔
铁量
500kg
每炉浇注
零件个数
炉料
配制
废钢100kg
干屑200kg
湿屑100kg
精炼剂
除渣
剂
细沙
变质
石墨/碳
涂料
205
附录B浇注工艺规程卡
喷涂工艺
频率
预热模具温度
正在喷涂的模具温度
6mine/次
230—290℃
270℃左右
涂料牌号
配比
喷涂方式
喷涂区域
1#
4:
1
双向
模具内表面
浇注工艺
烫模
利用铁棒烧红,放进模具内考,使其温度最低达到230℃
浇注时间
拔管时间
每小时产量
每班产量
2mine
30s
12根/台
144根/台
浇注温度
1480—1520℃
模具温度
270度左右
在浇注时,模具内表面温度不得低于230℃不得高于290