发动机曲轴连杆实习报告范文文档格式.docx
《发动机曲轴连杆实习报告范文文档格式.docx》由会员分享,可在线阅读,更多相关《发动机曲轴连杆实习报告范文文档格式.docx(11页珍藏版)》请在冰豆网上搜索。
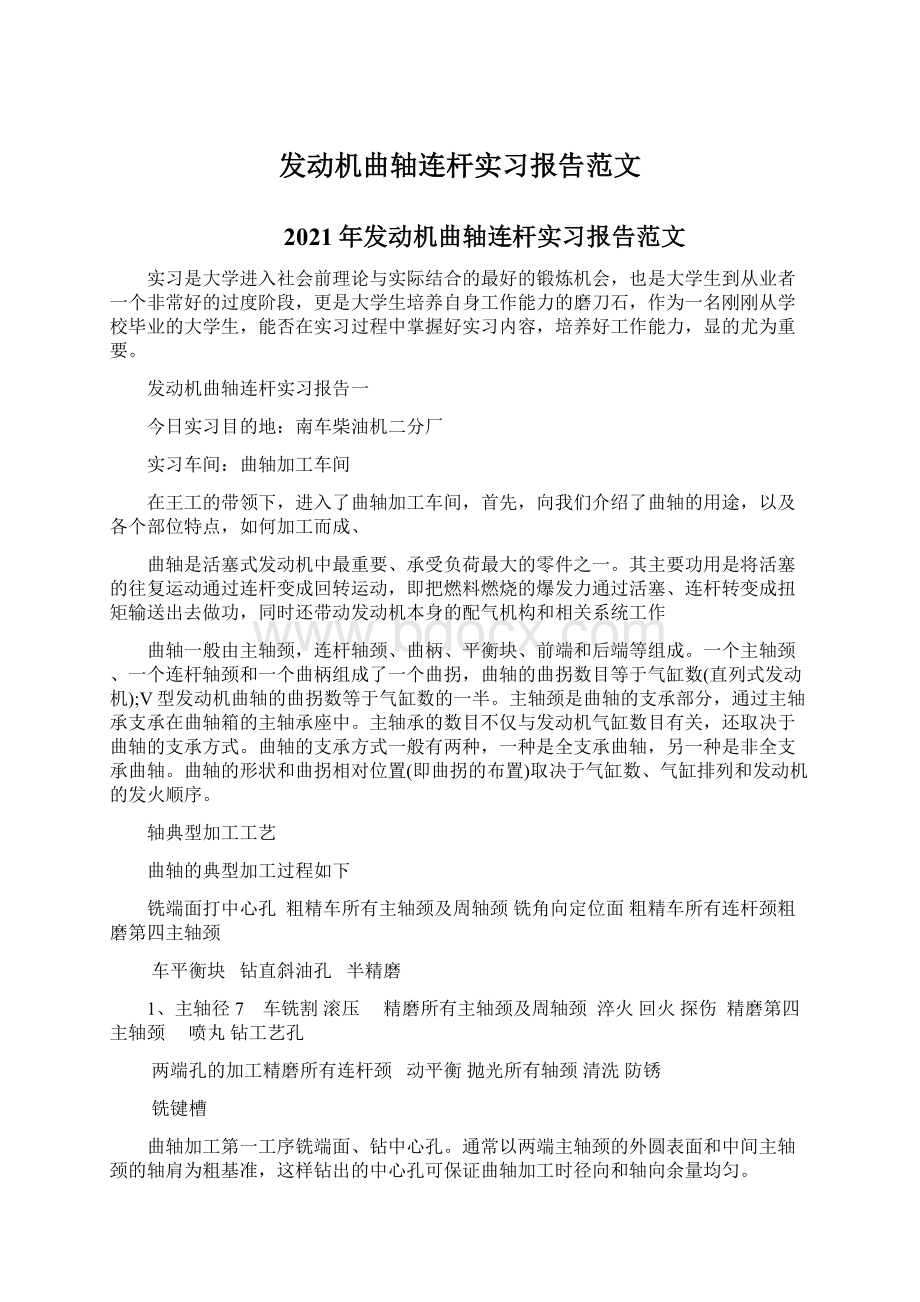
轴向定位用曲轴一段的端面或轴肩。
角度定位一般用法兰盘端面上的定位销孔或曲柄臂上铣出的定位平台。
采用不同的加工工艺方法和设备,定位基准的选用亦有不同。
铣端面,钻中心孔利用钻铣组合机床、利用数控车床主轴颈,利用深孔组合钻床钻油孔、曲轴的主轴颈和连杆轴颈的精加工用磨削完成。
在精磨后还要对各轴颈及侧端面进行光整加工。
生产中用油石抛光作预光整加工,砂带抛光作最终光整加工。
抛光中还将各轴颈圆角及油封轴颈也光整加工出来。
抛光加工只减小轴颈表面粗糙度值,而不能提高其尺寸精度和位置精度。
在实习中参观的厂中数控技术都担当了重要的角色,由此可见机电一体化已经是现在生产的主流。
在东风实习让我看到了我国机械行业发展的远大前景,从而也反映出了我国机械行业一片欣欣向荣的景象,这更加让我坚定了学好本专业知识的决心和信心,今后我一定会
更加努力地学习,提高自己各个方面的能力,特别是分析问题和解决问题的能力,为日后的工作打下坚实的基础
发动机曲轴连杆实习报告二
石家庄理工职业学院机电工程系--发动机构造与维修实训项目
曲轴的拆装
一、实训项目:
曲轴飞轮组的拆装
二、主要内容及目的
(1)熟练曲轴飞轮组的装配关系和运动情况
(2)掌握曲轴飞轮组的拆装方法、步骤。
四、实训与考核器材
(1)5A发动机1台。
(2)常用工量具1套,专用工具1套,机油少许。
五、操作步骤及工作要点
1.曲轴飞轮组的拆卸
(1)将汽缸体倒置在工作台上,旋松飞轮紧固螺钉,拆卸飞轮(飞轮较重,拆卸时注意安全)。
(2)拆卸正时链轮,首先松开张紧轮,取下链轮时注意链轮上的正时标志和传动方向。
(3)拆卸曲轴前端及后端密封凸缘及油封。
(4)
拆下曲轴主轴承盖紧固螺栓,不能一次全部拧松,必须分次从两端到中间逐步拧松,取下主轴承盖。
注意:
各缸主轴承盖有装配标记,不同缸的主轴承盖及轴瓦不能互相调换。
(5)抬下曲轴,再将主轴承盖及垫片按原位装回,并将固定螺钉拧入少许。
注意曲轴推力轴承的定位及开口的安装方向。
2.曲轴飞轮组的装配
①安装前应全面清洗发动机零部件,尤其是相互配合的运动件表面应保持清洁,并涂抹润滑油。
②安装顺序一般与拆卸顺序相反,由内向外进行。
③各配对的零部件不能互相调换,安装方向也应该正确。
各零部件相对装配关系应保持正确。
④各紧固螺钉应按规定力矩和方法拧紧。
(5)检验曲轴的轴向间隙。
检验时,先用撬棍将曲轴撬挤向一端,再用厚薄规在止推轴承处测量曲柄与止推垫片之间的间隙。
新装配时间隙值为0.07~0.17mm,磨损极限为0.25mm。
如曲轴轴向间隙过大,应更换止推轴承。
六、注意事项
(1)拆卸曲轴主轴承盖时,注意拆卸顺序两端向中间,装时中间向两端。
分两两到三次拧紧,力矩为65N/M.
(2)各缸主轴承盖有装配标记,不同缸的主轴承盖及轴瓦不能互相调换。
(3)安装飞轮时,齿圈上的标记与l缸连杆轴颈在同一个方向上。
(4)注意曲轴与飞轮的相对位置。
发动机曲轴连杆实习报告三
一、选题的依据及意义:
曲轴是发动机对外输出动力的核心部件,是驱动车、船等运输工具的重要动力来源。
曲轴的功用是把活塞、连杆传来的气体力转变为转矩,用以驱动汽车的传动系统和发动机的配气机构以及其他辅助装置。
曲轴的工作情况是极其复杂的,它是在周期变化的燃气作用力、往复运动和旋转运动惯性力及它们的力矩作用下工作的,因此承受着扭转和弯曲的复杂应力。
曲轴是内燃机中承受冲击载荷传递动力的关键零件,也是内燃机五大件(机体、缸盖、曲轴、凸轮轴、连杆)中最难以保证加工质量的零件,发动机曲轴作为重要运动部件,同时因曲轴工况及其恶劣,因而对曲轴材料、曲轴尺寸精度、表面粗糙度、热处理和表面强化、动平衡等要求十分严格。
其中任何一个环节的质量对曲轴的寿命和整机的可靠性都有很大的影响。
因此世界各国对曲轴的加工都十分重视,不断地改进曲轴加工工艺,最大可能地提高曲轴寿命。
在大批量生产的条件下,传统工艺已不能满足当前设计和生产需求,在长时间、高速运转下,曲轴极容易过早出现失效或断裂,严重影响曲轴的寿命和整机可靠性。
曲轴的主要失效形式是轴颈磨损和疲劳断裂,内燃机曲轴部分的结构形状和主要尺寸对内燃机曲轴的抗弯疲劳强度和扭转刚度有重要影响,因而在内燃机曲轴设计时,必须对内燃机的结构强度问题予以充分重视。
二、国内外研究现状及发展趋势:
2.1国内外曲轴加工技术的现状
目前车用发动机曲轴材质主要有球墨铸铁和钢两类。
由于球墨铸铁曲轴成本只有调资钢曲轴成本的三分之一左右,且球墨铸铁的切削性能良好,可获得较理想的结构形状,并且和钢质曲轴一样可以进行各种热处理和表面强化处理来提高曲轴的抗疲劳强度,硬度和耐磨性。
所以球墨铸铁曲轴在国内外得到了广泛的应用。
据统计资料显示,车用发动机曲轴采用球墨铸铁材质的比例在美国为90%,英国为85%,日本为60%,此为,德国比利时等国家也已经大批量采用。
国内采用球墨铸铁曲轴的趋势则更加明显,中小型功率柴油机曲轴85%以上采用球墨铸铁,而功率在160KW以上发动机曲轴多采用锻钢曲轴。
2.2国内外曲轴加工技术展望
美国,德国,日本等汽车工业发达国家都致力于开发绿色环保、高性能发动
55
机,目前各个厂家采用发动机增压、扩缸及提高转速来提高功率的方法,使得曲轴各轴颈要在很高的比压下高速转动,发动机正向增压、增压中冷、大功率、高可靠性、低排放方向发展。
曲轴作为发动机的心脏,正面临着安全性和可靠性的严峻挑战,传统材料和制造工业已无法满足其功能要求,市场对曲轴材质以及毛胚加工技术、精度、表面粗糙度、热处理和表面强化、动平衡等都要求都非常严格。
三、本课题研究内容3.1曲轴结构设计3.1.1曲轴的材料
根据曲轴工作在发动机过程中承受弯曲、扭转、剪切、拉压等交变应力,要求具有较高的抗拉强度、疲劳强度、表面强度及耐磨性,芯部具有一定的韧性。
即具有很高的疲劳强度、耐磨性和高淬透性,且进行强化处理时变形小,高温下具有高的蠕变强度。
随着发动机性能的提高,对曲轴的原材料及加工工艺提出新的要求,现代车用发动机曲轴材质主要有球墨铸铁和钢两类。
由于球墨铸铁曲轴成本只有调质钢曲轴成本1/3左右,且球墨铸铁的切削性能良好,可获得较理想的结构形状,并且和钢质曲轴一样可以进行各种热处理和表面强化处理来提高曲轴的抗疲劳强度、硬度和耐磨性。
所以球墨铸铁曲轴在国内外得到了广泛应用。
据统计资料显示,车用发动机曲轴采用球墨铸铁材质的比例在美国为90%,英国为85%,日本为60%,此外,德国、比利时等国家也已经大批量采用。
国内采用球墨铸铁曲轴的趋势则更加明显,中小型功率柴油机曲轴85%以上采用球墨铸铁,而功率在
160kW以上的发动机曲轴多采用锻钢曲轴。
我国球铁曲轴的生产继QT600-
2、QT700-2之后,现已能稳定地生产QT800–
2、QT900
-2等几种牌号,目前已能大批量生产QT800-6球铁曲轴。
但从整体水平来看,存在生产效率低,工艺装备落后,毛坯机械性能不稳定、精度低、废品率高等问题。
3.1.2曲轴结构设计
曲轴结构设计在过去的几十年中得到了飞速的发展。
在曲轴的设计初期一般是按照已有的经验公式计算或者与已有的曲轴进行类比设计,在进行了初步的设
56
计后造出曲轴样品再进行试验,通过实验数据进行适当的改进。
曲轴设计发展到今天已经有了很大的发展。
随着内燃机向高可靠性、高紧凑性、高经济性的不断发展,传统的以经验、试凑、定性为主要设计内容的设计方法已经不能满足要求,而随着电子计算机技术的不断发展,内燃机及其零部件的设计已经发展到采用包括有限元法、优化设计、动态设计等现代先进设计技术在内的计算机分析、预测和模拟阶段。
有限元法是最有效的数值计算方法之一,它使人们对零部件关键参数的理解和设计更进了一步。
(1)在设计内燃机曲轴时,应根据内燃机的工作条件,选择不同的结构设计方案。
内燃机曲轴结构设计方法大致如下:
①选择确定结构形式:
整体锻造曲轴、整体铸造曲轴、组合曲轴。
②确定润滑油道
曲轴主轴颈和曲柄销一般采用压力润滑。
润滑油由主油道送到各主轴承,在经曲轴内润滑油道进去连杆轴承。
当主轴承为滚动轴承时,润滑可从假轴承进入曲轴内腔,再分配到各有关轴承。
在决定主轴承和曲柄销上的油孔位置时,主要考虑应保证供油压力和油孔对曲轴强度的影响程度。
③确定曲轴平衡块形式
平衡块用来平衡曲轴的不平衡惯性力和力矩,减轻主轴承载荷以及减小曲轴和曲轴箱所受的内力矩。
但曲轴配置平衡块后重量增加,将使曲轴系统的扭振效率有所降低。
因此应根据曲轴结构、转速、曲柄排列等因素来配置平衡块和平衡精度要求。
平衡块可与曲轴制成一体,也可与曲轴分开制造后再进行装配。
(2)曲轴结构形式的选择
曲轴结构形式与其制造方法有直接关系,在进行曲轴设计时必须同时进行。
曲轴有整体式和组合式曲轴两大类。
而摩托车发动机常采用组合式曲轴,这是因为其加工简单,不需要大规模锻模具设备,它由曲轴左半部、曲轴右半部及曲轴销组成。
通过液压压入的方法将其结合起来。
本设计中采用滚动轴承做主轴承。
这是因为使用它具有以下优点:
①可以采用隧道式曲轴,保证曲轴箱有较高的强度和刚度;
②可以减少摩擦损失,提高机械效率,因而使燃料消耗下降;
③发动机启动较为容易,尤其在气温较低的时候;
57④采用滚动轴承后,对主轴的润滑较易实现。
3.2曲轴工艺分析
3.2.1曲轴的机械加工技术
曲轴主轴颈的粗加工、半精加工工艺和精加工工艺,大体分为以下几种:
(1)传统的曲轴主轴颈的多刀车削工艺。
生产效率和自动化程度相对较低。
粗加工设备多采用多刀车床车削曲轴主轴颈,工序的质量稳定性差,容易产生较大的内应力,难以达到合理的加工余量。
一般精加工采用曲轴磨床,通常靠手工操作,加工质量不稳定,尺寸的一致性差。
(2)数控车削工艺。
数控车削设备价格相对便宜,不需要复杂的刀具,但只适合小批量生产。
(3)数控内铣铣削工艺。
内铣设备价格较高,刀具费用也很高,但适合大批量生产。
(4)数控车—拉、数控车—车拉工艺。
其突出优点是可对宽轴径进行分层加工,切削效率高,加工质量好,但车拉刀具结构复杂,技术含量高,并且长期依靠进口,好处是可集车—车拉工艺加工连杆轴颈要两道工序于一起。
(5)CNC高速外铣工艺。
数控高速外铣是20世纪90年代新兴起来的一种新型加工工艺,其应用范围广,特别双刀盘数控高速外铣以其加工效率高、加工质量稳定、自动化水平高,已成为当前是曲轴主轴颈粗加工的发展方向。
就比较而言,CNC车—车拉工艺加工连杆轴颈要二道工序,CNC高速外铣只要一道工序就能完成,切削速度高(目前最高可达
350m/min
)、切削时间较短、工序循环时间较短、切削力较小、工件温升较低、刀具寿命高、换刀次数少、加工精度更高、柔性更好。
如德国BOEHRINGER公司专为汽车发动机曲轴设计制造的柔性的高速随动数控外铣床VDF315OM-
4型,该设备应用工件回转和铣刀进给伺服连动控制技术,可以一次装夹不改变曲轴回转中心随动跟踪铣削曲轴的轴颈。
其采用一体化复合材料结构床身,工件两端电子同步旋转驱动,具有干式切削、加工精度高、切削效率高等特点;
使用SIEMENS840D
CNC控制系统,设备操作说明书在人机界面上,通过输入零件的基本参数即可自动生成加工程序,可以加工长度450~700mm、回转直径380mm以内的各种曲轴轴颈直径误差仅为±
0.02mm。
58(6)数控曲轴磨削工艺。
精加工使用数控磨床,采用静压主轴、静压导轨、静压进给丝杠(砂轮头架)和线性光栅闭环控制等控制装置,使各尺寸公差及形位公差得到可靠的保证,精加工还广泛使用数控砂带抛光机进行超精加工,经超精加工后的曲轴轴颈表面粗糙度至少提高一级精度。
如GF70M-
T曲轴磨床是日本TOYADA公工机开发生产的专用曲轴磨床,是为了满足多品种、低成本、高精度、大批量生产需要而设计的数控曲轴磨床。
该磨床应用工件回转和砂轮进给伺服联动控制技术,可以一次装夹而不改变曲轴回转中心即可完成所有轴颈的磨削;
采用静压主轴、静压导轨、静压进给丝杠(砂轮头架)
和线性光栅闭环控制,使用TOYADA工机生产的GC50CNC控制系统,磨削轴颈圆度精度可达到0.002mm;
采用CBN砂轮,磨削线速度高达120m/s,配双砂轮头架,磨削效率极高。
3.2.2曲轴的强化工艺技术
目前国内外曲轴常见的强化工艺大致有如下几种:
(1)氮化处理。
氮化能提高曲轴疲劳强度的20%~60%。
(2)喷丸处理。
曲轴经喷丸处理后能提高疲劳强度20%~40%。
(3)圆角与轴颈同时感应淬火处理。
该强化方式应用于球铁曲轴时,能提高疲劳强度20%,而应用于钢轴时,则能提高l00%以上。
(4)圆角滚压处理。
球铁曲轴经圆角该压后寿命可提高120%~300%,钢轴经圆角液压后寿命可提高
70%~150%。
曲轴圆角滚压强化工艺主要包括曲轴圆角滚压和曲轴滚压校正两部分。
(5)复合强化处理。
它是指应用多种强化工艺对曲轴进行强化处理,球墨铸铁曲轴采用圆角该滚压工艺与离子氮化工艺结合使用,可使整个曲轴的抗疲劳强度提高130%以上。
四、本课题研究方案
(1)查阅原始资料,熟悉曲轴结构设计的方法及曲轴工艺技术。
(2)根据曲轴的工作条件和柴油机工作参数对曲轴进行结构设计及强度校核。
(3)利用曲轴材料和工况分析曲轴的加工工艺。
发动机曲轴连杆实习报告四
一、实习目的与要求
实习目的:
⒈巩固和加强汽车发动机构造和原理课程的理论知识,为后续课程的学习奠定必要的基础。
⒉使学生把握汽车发动机总成、各零部件及其相互间的连接关系、拆装方法和步骤及注重事项;
⒊学习准确使佣拆装机器工具、量具的方法;
⒋了解安佺操作常识,认识零部件拆装后的准确放置、分类及清洗方法,造就良好赌工作和生产习惯。
⒌锻炼和造就学生的动手能力。
实习要求:
1.学会汽车发动机常佣拆装工具和仪器机器的准确使佣
2.学会汽车发动机的总体拆装、调整和各系统主要零部件的准确拆装
3.学会汽车发动机的主要零部件的检查测量
4.把握汽车发动机的基本构造与基本工作原理
5.理解汽车发动机各组成系统的结构与工作原理
实习常佣工具:
普通扳手、螺钉旋具、锤子、手钳。
二、实习内容
在老师的布置下,我泌藉个人一组进行发动机的拆装,我们小组拆的是一个四缸直列水冷式发动机,先按要求拆下化油器,由于时间原因,对化油器内部零件没有进行拆装,不过事先我们已经拆装过化油器,这里就没有特殊要求。
然后卸温分电器等外部零部件,拆下电动机和发电机等组件。
然后拆下进,排气支管,卸温气缸罩,然后把两侧的汽油泵亦及节温器,这样发动机外部组件基本拆卸完毕。
然后按如下要求拆卸机体组件
1)拆下气缸盖13固定螺钉,注意螺钉应丛两端向中间交叉旋松,并且分3次才卸温螺钉。
2)抬下气缸盖。
3)取下气缸垫,注重气缸垫的安装朝向。
4)旋松油底壳20的放油螺钉,放出油底壳内机油。
5)翻转发动机,拆卸油底壳捞定螺钉(注意螺钉也应丛两端向中间旋松)。
拆下油底壳和油底壳密封垫。
6)旋松机油粗滤清器固定螺钉,拆卸机油滤清器、机油泵链轮和机油泵。
2、拆卸发动机活塞连杆组
1)转动曲轴,使发动机1、4缸活塞处于下止点。
2)分别拆卸1、4缸的连杆的紧固螺母,去下连杆轴承盖,注重连杆配对记号,并按顺序放好。
3)佣橡胶锤或锤子木柄分别推出1、4缸的活塞连杆组件,佣手在气缸出口接住并取出活塞连杆组件,注重活塞安装方向。
4)将连杆轴承盖,连杆螺栓,螺母按原位置装回,不同缸的连杆不能互相调换。
5)佣样方法拆卸2、3缸的活塞连杆组。
3、拆卸发动机曲轴飞轮组
1)旋松飞轮紧固螺钉,拆卸飞轮,飞轮比较重,拆卸时注重安佺。
2)拆卸曲轴前端和贵端密封凸缘及油封。
3)按课本要求所示丛两端到中间旋松曲轴主轴承盖紧固螺钉,并注重主轴承盖的装配记号与朝向,不同缸的主轴承盖及轴瓦不能互相调换。
4)抬下曲轴,再将主轴承盖及垫片按原位装回,并将固定螺钉拧入少许。
注意曲轴推力轴承的定位及闭口的安装方向。
3、发动机零部件清洗
1)清除发动机零部件的所有油泥和污垢,刮除气缸、气缸盖及活塞积炭。
2)在专佣油池中清洗发动机零部件,尤其是活塞连杆组件和曲轴飞轮组件。
4、在老师的带领下,我们来到多媒体教室,并观看了发动机的工作过程及各组件的功能,通过老师的讲解,我们更一步了解了发动机的工作原理。
5、发动机总体安装
1)按照发动机拆卸的相反顺序安装所有零部件。
2)安装注重事项如下:
1.安装活塞连杆组件和曲轴飞轮组件时,应该特殊注重互相配合运动表面的高度清洁,并于装配时在相互配合的运动表面上涂抹机油。
2.各配对的零部件不能相互调换,安装方向也应该准确。
3.各零部件应按规定力矩和方法拧紧,并且按两到三次拧紧。
4.活塞连杆组件装入气缸前,应使佣专用工具(活塞钳)将活塞环夹紧,再佣锤子木柄将活塞组件推入气缸。
5.安装正时齿轮带时,应注重使曲轴正时齿形带轮位置与机体记号对齐并与凸轮轴正时齿形带轮的位置配合准确。
6、拆装完后将所有工具及地面清理一遍,整个拆装实习才基本结束。
备注:
安装时应将1、4气缸调到上止点。
三、实习心得体会
使得我的理论知识得亦升华.这使我大体认识到了发动机内部的总体布局和各零件的样子它们的相对位置亦及它们之间的装配和运做情况.
发动机的外表装有发电机它有齿轮与飞轮相啮合;
起动机佣于开启发动机的运转;
分电器和高压线圈佣于提高电压和分配各缸点火的先后顺序;
火花塞佣来提供点火的装置;
有进气总管和进气支管有的把其铸成一体有的则佣铆钉铆在一起在它们的上源孕空气滤清器来过滤进入发动机的空气在节气门的位置处还按孕检测空(deweizhichuhaianyunjiancekong)气量的传感器;
在进气总管和进气支管的对侧按孕排气总管和排气支管佣来排出发动(yonglaipaichufadong)机燃烧过程中产生的废气;
在现代(zai4xian4dai4)的发动机中一般还在此装有三元催化转换器来检测废气中有害气体的含量来反馈调节进气量和喷油量来保证排出的废气符合环境法规的要求;
还应装有进油管和回油管;
由于发动机喷入气缸的是可燃的混合气因而空气和汽油要在进气管内混合好喷油的方式有两种一为:
单点喷射二为:
多论文网点喷射单点喷射喷油器位于进气总管的位置处然后在分配吊遇进气的支鼓┶进入气缸;
多点喷射的喷油器则位与各进气的支管处在进气支管混合后直接进入气缸;
在发动的一侧还有进水管和出水管通过水的流动来犁高速运转的发动机为发动机提供一个良好赌工作环境;
一般在此处还有检测水温的传感器佣来反馈发动机的工作情况.
发动机的外侧装置已基本介绍完了下面来谈谈发动机的内部各零件的装配关系和它们之间的运转情况.
揭下顶干宰先看见的是摇臂和摇臂轴摇臂固定在摇臂轴上可亦做上下的摆动调节上边的螺母可亦改变摆动的幅度及调节了气门开启的程度的大小来调节进/排气量的大小.在现代的汽车发动机中大都采佣顶置式气门.气门按凸轮轴的位置可亦分为凸轮轴下置式凸轮轴中置式凸轮轴上置式;
凸轮轴下置式气门和凸轮轴相距较远因而气门传动的零件较多结构较复杂发动机的高度也有所增加.凸轮轴中置式凸轮轴位于气缸体的中部由凸轮轴经过挺柱直接驱动摇臂省去了推杆.凸轮轴上置式凸轮轴的布置位置在气缸盖上凸轮轴上置式有两中结构:
一是凸轮轴直接通过摇臂来驱动气门这样及无挺柱又无推杆往复运动质量大大减小此结构适应于高速的发动机中.另一种结构为凸轮轴直接驱动气门或带液力挺柱的气门此种配气机构的往复运动的质量更小特殊适应于高速的发动机中.在揭下气缸盖将气缸盖反置可亦清楚的看见气门和燃烧室其中气门有一大一小大的为进气小的则为排气.将拆剩下的发动机反置开始拆卸油底壳油底壳下端有个放油螺栓在拆发动机之前首先应先将起拧开使内部的机油佺部流出在车辆行驶一定的路程后也要定期的给发动机更换机油来保障发动机良好赌润滑.拆下油底壳可亦看见机油滤清器拆下机油滤清器和机油泵然后(ranhou)在拧下曲轴轴承盖上的螺栓就可亦取下轴承盖其轴承盖和内的轴瓦应做好标记与轴承要一一对应取下固定在曲轴上活塞的螺栓后就可亦抬下曲轴之后就可亦取下活塞了取下的活塞也要做好标忌怨其与各缸对应就此一台发动机就拆卸实现了.
发动机曲轴连杆实习报告五
曲轴是发动机最重要的机件之一:
结构特点:
全支承曲轴:
曲轴的主轴颈数比气缸数目多一个,即每一个连杆轴颈两边都有一个主轴颈。
如六缸发动机全支承曲轴有七个主轴颈。
四缸发动机全支承曲轴有五个主轴颈。
这种支承,曲轴的强度和刚度都比较好,并且减轻了主轴承载荷,减小了磨损。
柴油机和大部分汽油机多采用这种形式。
非全支承曲轴:
曲轴的主轴颈数比气缸数目少或与气缸数目相等。
这种支承方式叫非全支承曲轴,虽然这种支承的主轴承载荷较大,但缩短了曲轴的总长度,使发动机的总体长度有所减小。
有些汽油机,承受载荷较小可以采用这种曲轴型式。
曲轴的连杆轴颈是曲轴与连杆的连接部分,通过曲柄与主轴颈相连,在连接处用圆弧过渡,以减少应力集中。
直列发动机的连杆轴颈数目和气缸数相等。
V型发动机的连杆轴颈数等于气缸数的一半。
曲柄是主轴颈和连杆轴颈的连接部分,断面为椭圆形,为了平衡惯性力,曲柄处铸有(或紧固有)平衡重块。
平衡重块用来平衡发动