压下量对冷轧板材变形力和金属机械性能的影响Word文档格式.docx
《压下量对冷轧板材变形力和金属机械性能的影响Word文档格式.docx》由会员分享,可在线阅读,更多相关《压下量对冷轧板材变形力和金属机械性能的影响Word文档格式.docx(16页珍藏版)》请在冰豆网上搜索。
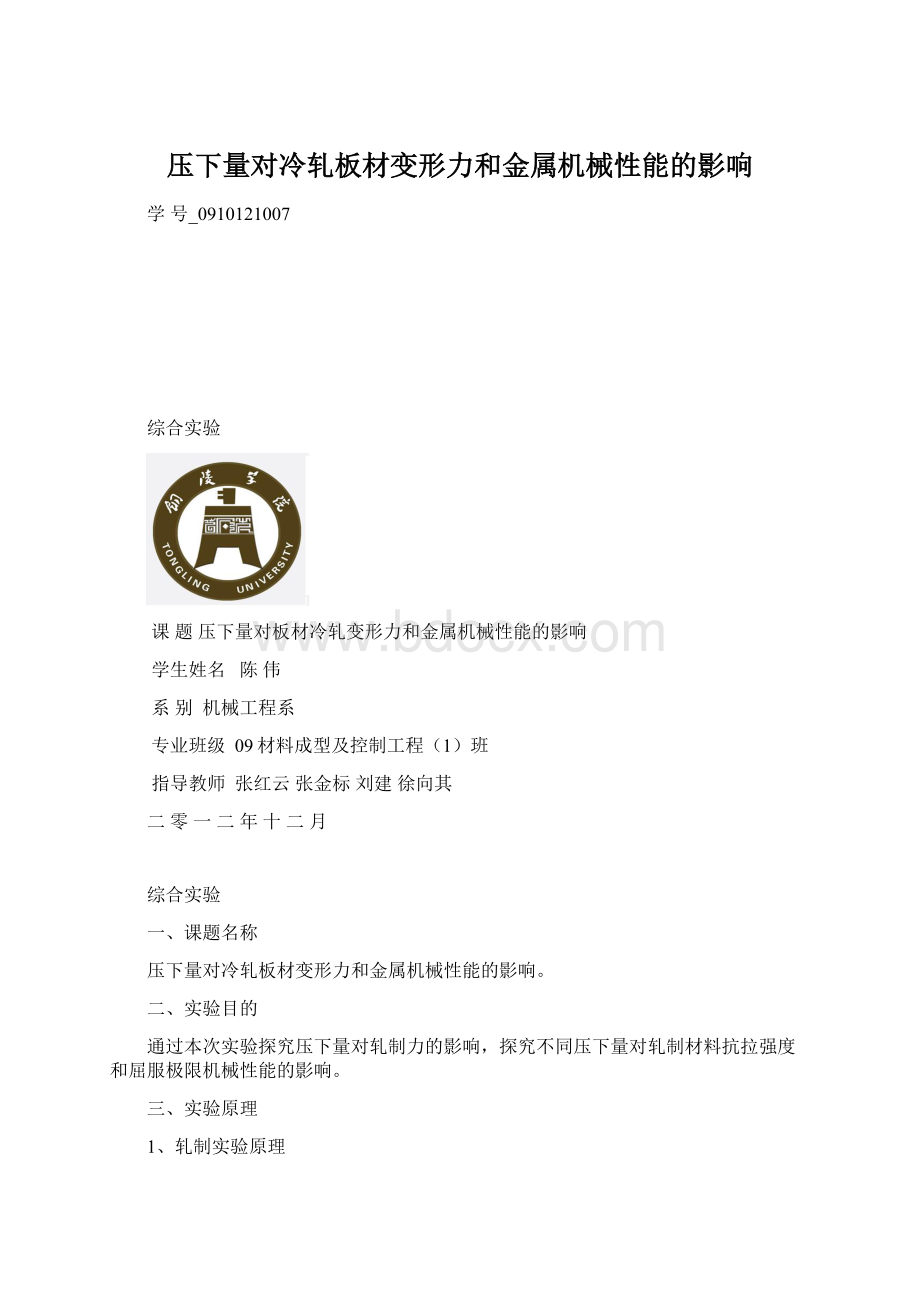
(2)拉伸实验
拉伸试样(轧制后加工设计的拉伸试样)、液压万能实验机、游标卡尺、划线机、錾子、锯子、锤子、砂纸、圆锉和平锉等。
2、条件参数
(1)轧制相关参数:
最大轧制力150KN,轧机辊径为130mm,最大轧薄能力0.4mm,轧材相关数据:
铝板5块,尺寸2.86×
150mm。
(2)拉伸试样相关参数:
轧后铝板5块。
3、设计实验参数
考虑到板冷轧过程中的加工硬化,设计本次实验的轧制道次为1,轧制材料选用铝板,板材厚度H=2.86mm,考虑到轧机的能力和咬入条件,压下量分别取
0.24mm,0.29mm,0.29mm,0.29mm,0.29mm。
利用上次轧制实验得到的轧件,在钳工实验室加工成长宽为50×
145mm,厚度不变的5组试样。
根据体积不变定律和
公式,把5组试样打磨成设计拉伸试样的尺寸,如图1示。
其中
—拉伸试样的截面积;
—拉伸试样的有效长度;
—拉伸试样的厚度;
—拉伸试样的宽度。
4、加工步骤
(1)首先按照设计好的尺寸图1对试样进行划线,将轧制后的铝板打磨出两个基准面;
(2)先对各试样用锯子把四个斜度锯好,再用錾子将多余的部分錾掉,然后用平锉和圆锉按照图示尺寸对各试样进行加工;
(3)最后用砂纸进行打磨,得到所需的拉伸试样。
五、实验方法与步骤
1、试验方法
(1)轧制试验方法
金属在轧制过程中作用在轧辊上的压力即轧制压力,它是轧机的基本负荷参数之一。
准确的测量轧制压力,对合理安排轧制工艺,合理使用和控制现有轧机以及设计新轧机,都具重要意义。
压下量轧制实验是模拟实验方法,目前广泛采用两种测量轧制压力的方法。
第一种是通过测量机架立柱的拉伸应变测量轧制压力,又称应力测量法;
第二种是用专门设计的测力传感器直接测量轧制压力。
应力测量法在测力过程中容易引起较大误差,所以该实验不选此方法。
测力传感器传感器分为电阻应变式、压磁式、电容式及电感式等。
当前应用最广的主要是前两种。
压磁式所需仪器设备较复杂,需要在特定条件下使用,故不使用;
电阻应变式传感器适合于现场条件下的短期测量,符合本实验条件要求。
故本实验主要用电阻应变式传感器。
(2)拉伸试验方法
将试样安装在试验机的夹头中,然后开动试验机,使试样受到缓慢增加的拉力(应根据材料性能和试验目的确定拉伸速度),直到拉断为止,并利用试验机的自动绘图装置绘出材料的拉伸图如图2所示。
材料在拉伸过程中分为三个阶段:
①弹性变形阶段。
随着拉力的增加,材料开始伸长,此时因为应力与应变是一条直线,即两者成比例关系,称之为弹性阶段。
②塑性变形阶段。
随着拉力的继续加大,材料开始急剧变形,继续拉伸时会出现颈缩,应力会继续增加,但变形会急剧增大,材料产生宏观变形时的应力称之为屈服强度,又称之为屈服极限。
③破坏阶段。
当拉力继续增大,材料的应力达到极限,会突然断裂,此时的应力最大,称之为强度极限或抗拉强度。
对于无明显屈服点的材料,在静力拉伸时,常把σ0.2作为变形抗力指标。
σ0.2为试样标长部分产生20%的塑性变形时的负荷P0.2除以试样的原始横截面积F0。
本实验依据图2,采用图解法来测定σ0.2。
(3)实验计算公式
①伸长率:
;
②断面收缩率:
;
③强度极限:
④抗拉极限:
。
通过计算试件的拉伸过程中的屈服强度和抗拉强度可度量试件拉伸后的强度指标;
计算公式为
中横截面积
,拉伸载荷P可从仪器上读出,然后做出
曲线图,求出屈服强度和抗拉强度。
2、数据采集方法
轧制实验是按照实验要求先制作出测力传感器,然后将测力传感器应安装在工作机座两侧轧辊轴承垂直载荷的传力线上,通过测量两侧的轧制力分力即可得到总轧制力。
利用Excel可以将轧制力和异速比的关系曲线描绘出,实验过程流程图如图3示。
3、数据分析处理方法
回归分析法是利用数据统计原理,对大量统计的数据进行处理并通过变量和某些自变量的之间的相关关系,建立一个相关方程。
通过实验采集的数据,利用Excel中的“数据分析”选项下的“回归”功能,分别选定X、Y值输入区域,并勾选“残差”中的各个选项,点击“确定”,得到相关值,通过分析得到函数方程。
4、实验步骤
(一)轧制实验步骤
本实验利用电阻式传感器测定轧制力,需进行如下操作:
轧制试样的制作—设备准备—传感器的制作(贴片、组桥连线与防潮)—传感器的标定—传感器的安装—轧机实验参数综合测试仪的使用—数据采集记录—轧制并采集数据—数据分析。
具体操作如下:
(1)将板材打磨去除表面的铝锈污迹,保证板材表面的光洁,通过剪切机将样板制作成5块2.8×
140mm的试样。
(2)取出要轧制的5块试样铝板,分别用游标卡尺测量其原始厚度H、宽度B、长度L,并编号为1、2、3、4、5,作好记录。
(3)将压力传感器安装在轧机上,并将各设备连接好。
(4)先将轧辊辊缝调为0,根据压下量和试样原始厚度,转动压下螺丝,调整辊缝。
(5)开启计算机和压力测试仪的电源,之后在计算机上打开测试软件,通过点击“采样”开始采集并有图形输出即表明各设备或各一起之间已连接好,否则要重新检查连接线路排除故障。
(6)检查好各通道,打开轧制仪器电源的电源开关,电源灯亮。
(7)调节轧制综合参数测试仪至平衡状态。
(8)采用同步方式轧制,将两工作辊速度调节至某一相同速度,让试样1以缓慢的速度水平垂直进入轧机。
测量轧制后试样的厚度
,并通过传入电脑的数据,读出这次的轧制压力,记入表1中。
(9)保持轧辊速度不变,调节压下螺丝,使压下量分别增加0.24mm,0.29mm,0.29mm,0.29mm,对其余4块试样分别进行轧制,并将轧制后所测量的数据记入表1中。
(10)实验结束时停止采样。
(11)把实验器材整理并放回原处。
轧制实验中由于轧辊的磨损、弹性弯曲等因素,使轧辊呈凹形,从而影响辊缝,使轧板在轧制后出现不平直的板形,所以当发现板形弯曲时,采用辊缝不变的反轧使轧件保试样,平板下压保证板的平直。
对异步轧机进行调速时,注意轧辊的加速或减速期,应当在轧辊速度稳定之后喂入试样。
(二)、拉伸实验步骤
(1)在钳工工作室利用相关工具进行试件准备与尺寸测量并对5块试件进行编号,分别为1、2、3、4、5,计算试件的横截面面积A0,并绘制两条平行线为试件的有效长度,取线间的距离作为标距长度记录到表2中,以便观察标距范围内沿轴向的变形情况。
(2)调整测力指针指零
①开机进油,使活动平台上升一段距离;
②摆锤对中,是摆锤垂直;
③调整测力指针对准零点,使测力指针与随动指针重合。
(3)
装夹试件如图4示,保证试件与水平方向垂直。
(4)进行实验
①开始试验机,缓慢匀速加载;
②冷拉试件,取多组测力盘上的轧制力,并记录相对应的标尺读数,整理到表2中;
③观察颈缩现象。
当万能试验机上的表盘出现回转时,记录下开始回转时的指针读数为
,当侧力指针再次出现停滞不前、倒退现象时,记录刻度尺的示数为
,可以观察到试件产生局部变形的颈缩现象;
继续缓慢加载,直至试样断裂,记下断裂时表盘指针的读数为,此时记录刻度尺的示数为
⑤试件断裂后,关闭机器电源;
取下试件,测量拉断后标距长度记入表中;
重复上述步骤,分别对试样2、3、4、5进行拉伸,记录相关数据并整理到表3中,停机后,送油阀一定要置于关闭位置。
六、数据分析
1、轧制实验
表1各试样轧制实验参数
试样编号
轧前
厚度H/mm
轧后
厚度h/mm
理论压下量
/mm
相对压下量
轧制P1
/kN
轧制力P2
总轧制力P总
1
2.86
2.68
0.24
0.063
15.37
13.72
29.09
2
2.5
0.29
0.126
25.91
25.15
51.06
3
2.24
0.217
34.64
33.44
68.08
4
0.301
44.92
43.26
88.18
5
1.82
0.364
54.04
53.17
107.21
表2拉伸试样参数表
拉前厚度h/mm
标距/mm
测力盘读数F/N
标尺读数/mm
位移变化/mm
拉伸后宽度/mm
断后标距/mm
断面厚度/mm
80
30.66
85.18
0.98
2000
5.2
1.2
4000
6.5
6000
7.4
3.4
8000
9
8800
10
6
9000
12
8
28.70
84.98
0.84
7.6
3.6
9.5
5.5
8200
13
4.5
28.46
83.80
0.8
3000
6.2
1.7
7
6500
8.5
7200
11
7500
12.5
3.5
28.30
83.40
0.74
5000
20
16.5
续上表
1.86
27.42
83.02
0.66
4.7
5.4
1.9
6300
7.2
3.7
根据表1压下量对轧制力影响的数据可知,相同式样的铝板进行轧制时,随着压下量的增加,轧机对轧件的轧制力也相应的增加。
这是由于冷轧时,金属的变形温度低于再结晶温度,因此金属只产生加工硬化现象,变形抗力提高。
所以试样在轧制过
程中轧制力的增加总体原因是金属的加工硬化现象。
以处理相对压下量和轧制力的回归关系为例,在Excel中选中数据分析
回归,对表1相对压下量和轧制力进行回归分析,令
轴为相对压下量,
轴为轧制力,可得到方程
图5相对压下量-轧制力曲线图
通过方程绘制出回归曲线图如图5所示,可知相对压下量与轧制力成简单的线性关系,随着相对压下量的增加,轧制力也相应的增加。
2、拉伸试验
对表2数据进行处理和结合实验的过程,试样4存在明显的实验误差,没有明显的抗拉极限,试样4在拉伸过程中没有产生明显的断裂现象,而是缓慢的撕裂过程。
所以试样4数据不准确,在这里不做具体分析。
现对其余四组数据进行处理得到表3。
表3试样1分析数据
试样1数据
读数次数i
横截面积A0/mm2
拉伸后横截面积A/mm2
断面收缩率
伸长率
应变ε
应力σ/MPa
86.1352
30.0468
65.12%
6.48%
0.00
0.150
23.22
0.313
46.44
0.425
69.66
0.625
92.88
0.750
102.16
1.000
104.49
根据表中数据应变应力的数据可以通过Excle中的图表制作出试样1的应变应力图,如图5所示。
有图可知试样在刚开始拉伸过程中为弹性变形阶段。
随着拉力的增加,试样开始拉长,此时因为应力与应变是一条直线,即两者成比例关系,如图系列1所示。
当随着拉力的继续加大,材料开始急剧变形,继续拉伸时会出现颈缩,铝板中间地带出现线性凹陷,应力继续增加,变形也会急剧增大,材料产生宏观变形时的应力称之为屈服强度,如图系列1和系列2的交点处。
当拉力继续增大,铝板的应力达到极限,会突然断裂,此时的应力最大,称之为强度极限或抗拉强度,应力与与应变关系为对数关系,如图系列2示。
从图6中可以看出试样1的屈服强度为83MPa。
图6试样1应力应变图
同理对得到试样2,3,5的应力应变图进行分析,并得到相应的屈服强度分别为90MPa,96MPa,102MPa。
对上述的数据进行处理整合可得到试样拉断时的延伸率,断面收缩率屈服强度以及抗拉强度见表4。
表4各试样分析数据
编号编号
材料伸长率δ
断面收缩率ψ
屈服强度σ0.2/MPa
抗拉强度σb/MPa
83
104
6.23%
67.92%
90
109
4.75%
65.98%
96
112
\
3.78%
65.52%
102
120
对表4数据中相对压下量和轧制力进行回归分析,令
轴为相对压下量,令
轴为轧制力,可假设它们之间呈二次多项式关系,即
。
可以通过Excel中的回归分析得到它们之间的关系式。
设
,
,得方程:
回归曲线如图7示,可知相对压下量与屈服强度成二次函数关系关系,由图示和函数可知:
当压下量小于0.413时,屈服强度随着相对压下量的增加也相应的增加。
图7相对压下量-屈服应力曲线图
同理对相对压下量和抗拉强度进行回归分析,令
(1)
或者
(2)
因为回归方程
(2)的标准误差0.9小于方程
(1)的标准误差1.3,所以采用回归方程
(2),回归方程曲线如图8示,可知抗拉强度和相对压下量存在线性关系,从图中可以看出随着压下量的增加,抗拉强度也相应的增加。
图8相对压下量-抗拉强度曲线图
综合以上曲线和表格数据可知,随着相对压下量的增大,轧制力、屈服应力、抗拉强度也增大,伸长率减少,断面收缩率变化不大。
在这次实验中,研究的是不同压下量对试样轧制力和材料性能的影响,材料性能主要体现在屈服强度和抗拉强度上。
随着相对压下量的增大,轧制力也增大。
这是因为随着压下量的增加,轧制时所需的轧制力是呈增大的;
按照斯通公式:
可得单位轧制力是增大的,又因为轧制力为
,且
,接触面积S也是增大的;
所以轧制力是增大的。
由于试样的压下量的不同,导致试样的变形程度的变化,由图7及8可知在冷轧过程中,随着压下量增加,变形程度相应增加,金属出现加工硬化现象,导致轧制力、屈服强度和抗拉强度的增加。
加工硬化是指金属在变形过程中,随着变形程度的增加,强度和硬度明显增高,而塑性迅速下降的现象。
第一阶段是在界面上进行线性滑移方式,第二阶段发生了位错和交割,产生位错的塞积和缠结。
变形量增加,位错密度迅速增高,使变形抗力显著增加。
第三阶段变形抗力增加到一定程度后,滑移面上的位错可以通过交滑移,使位错密度降低,强度降低。
7、总结
这次综合实验主要研究的是相对压下量对板材同步轧制变形力和金属机械性能的影响,实验主要分为轧制实验和拉伸实验。
实验中最为困能的是设计方案阶段,在设计方案前要掌握轧制的相关理论与工艺,金属材料的机械性能,金属加工相关知识,了解实验原理后,经过指导老师的多番指导制定出实验方案。
轧制实验是通过对相同试样采用不同压下量时轧制力的变化,实验中对轧件厚度的测量精度要求较高,以实现较小的测量误差。
在制取拉伸试样时,主要是对轧后轧件设计,在钳工制做过程中一定要保证试样拉伸件光滑,防止在拉伸过程中因裂纹直接出现撕裂。
拉伸实验中,对不同压下量的轧件进行拉伸,探究其与金属铝板机械性能关系。
因为在实验中没有夹紧试样直接到导致试样4拉伸失败。
所以在试样中因注意要夹紧试样,防止打滑。
实验结束后,通过的数据的处理,进步加深了相对压下量对轧制力和金属机械性能关系的了解。
其中掌握了以前实验中没有学过的回归分析。
在对各组数据回归分析时,加深了对Excle数据分析功能的运用。
下届学生记得要将拉伸试样夹头部分设计到30mm,以便夹紧,因为实验中试样容易打滑。