龙兴钛渣沸腾氯化制取TiCl4工业试验Word文档格式.docx
《龙兴钛渣沸腾氯化制取TiCl4工业试验Word文档格式.docx》由会员分享,可在线阅读,更多相关《龙兴钛渣沸腾氯化制取TiCl4工业试验Word文档格式.docx(27页珍藏版)》请在冰豆网上搜索。
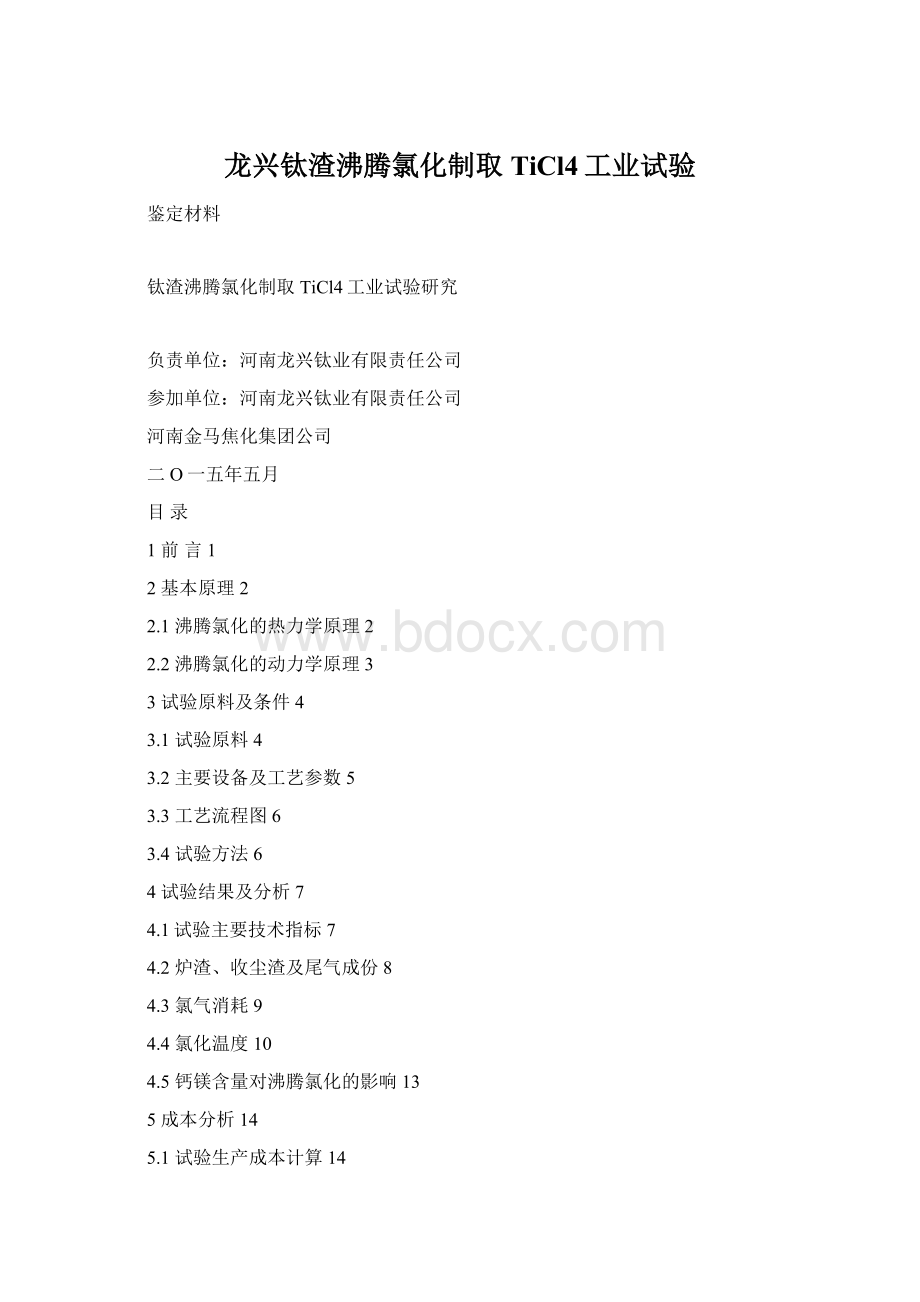
(2-1)
CaO+C+Cl2=CaCl2+CO
(2-1′)
2MnO+C+2Cl2=2MnCl2+CO2
(2-2)
MnO+C+Cl2=MnCl2+CO
(2-2′)
2MgO+C+2Cl2=2MgCl2+CO2
(2-3)
MgO+C+Cl2=MgCl2+CO
(2-3′)
2Fe2O3+3C+6Cl2=4FeCl3+3CO2
(2-4)
Fe2O3+3C+3Cl2=2FeCl3+3CO
(2-4′)
2FeO+C+3Cl2=2FeCl3+CO2
(2-5)
2FeO+2C+3Cl2=2FeCl3+2CO
(2-5′)
TiO2+C+2Cl2=TiCl4+CO2
(2-6)
TiO2+2C+2Cl2=TiCl4+2CO
(2-6′)
2Al2O3+3C+6Cl2=4AlCl3+3CO2
(2-7)
Al2O3+3C+3Cl2=2AlCl3+3CO
(2-7′)
SiO2+C+2Cl2=SiCl4+CO2
(2-8)
SiO2+2C+2Cl2=SiCl4+2CO
(2-8′)
2V2O5+3C+6Cl2=4VOCl3+3CO2
(2-9)
O2+2C=2CO
(2-10)
根据反应热力学数据可以计算出在700℃~1000℃温度范围内上述(2-1)~(2-10)式及(2-1′)~(2-8′)式反应的标准自由能ΔG°
值均为负值,表明在标准状态下,这些反应均能自发地正向进行,ΔG°
变化与温度的关系[4],见图2-1(图中的编号与上述反应式对应)。
图2-1表明:
钛渣中各种氧化物在1000℃左右的加碳氯化顺序为:
CaO>
MnO>
MgO>
Fe2O3>
FeO>
TiO2>
Al2O3>
SiO2,这在一定程度上反映了各种氧化物氯化率的高低,其中CaO、MnO、MgO、Fe2O3和FeO优先于TiO2被氯化,因此为了提高Cl2的有效利用率,必须尽量降低原料中的CaO、MnO、MgO、Fe2O3和FeO的含量,特别是要减少CaO、MgO含量,因为CaO、MgO被优先氯化生成的CaCl2、MgCl2
属于低熔点、高沸点的物质,在沸腾氯化炉中成粘度较强的液相存在,很容易粘结造成对床层的破坏。
2.2沸腾氯化的动力学原理
钛渣沸腾氯化是气、固两相反应,反应符合未反应核缩减模型。
首先,氯气包围参与反应的固体钛渣并与其表面发生反应,反应生成的化合物由表面脱落,气体产物由炉顶逸出,液态产物粘附在不参与反应的固体(焦粒等)上;
其次,未参与反应的固体由于内部可反应的物质已反应并脱离,形成多孔的固体骨架,氯气继续通过孔道渗入钛渣内部与可反应的化合物发生反应,直至反应完成。
整个反应过程由于不断有可反应化合物参与反应并脱离,钛渣是逐渐缩小的,由于其质量变小,在气速不变的条件下,将不能保持沸腾状态,而被气流带出。
为了使固体反应物尽可能保持沸腾状态而不被带走,沸腾氯化炉内必须满足气速可变的条件,其结构由气室、气体分布器、反应段、过渡段、扩大段、顶盖以及加料、排渣、气体收集系统等组成。
氯气经炉底部进入反应段,气流控制速度一般介于钛原料颗粒的起始流化速度和带出速度之间,使氯化炉中的固体物料形成沸腾状态,强化气、固间的传热、传质效果。
反应段一般为圆柱形,也有采用锥形,具有沿床高气流线速度逐渐降低的特性,即反应段底部气流高,上部气流低,这与反应段内物料粒度沿床高逐渐变细的特性相适应,扩大段与反应段截面积保持一定比例(通常为2~4倍),可减轻微小颗粒在生产过程中的夹带现象,过渡段的物料滑动角不易过小,不然,易堆积物料,产生搭桥现象。
国外的氯化炉型为直桶型,无扩大段,这种炉型对钛原料的粒度要求非常严格。
3试验原料及条件
3.1试验原料
(1)钛渣
试验用钛渣包括龙兴钛渣和天泰公司外购钛渣,其主要成份和粒度分布见分别见表3-1和表3-2。
表3-1试验用钛渣成份分析/%
化学成份
TiO2
TFe
MnO
SiO2
Al2O3
CaO
MgO
V2O5
龙兴钛渣
84.8
2.13
0.6
2.92
2.96
1.73
5.47
0.11
天泰钛渣
92.3
5.99
0.78
1.13
0.54
0.80
0.77
0.17
表3-2试验用钛渣粒度分布/%
筛网/mm
>
0.425
0.25
~0.425
0.18
~0.25
0.15
~0.18
0.125
~0.15
0.106
~0.125
0.1
~0.106
0.09
~0.1
<
6.5
11.3
11.5
12.8
12.3
7.0
15.1
5.8
17.7
15.8
15.3
13.5
10.9
5.7
8.5
3.8
15.0
(2)石油焦
试验用石油焦为1#焦和3#焦按一定配比混合制成,其成份和粒度分布见表3-3和3-4。
表3-3试验用石油焦分析结果/%
名称
固定碳含量
挥发份
灰份
水份
1#焦
97.33
2.27
0.66
0.40
3#焦
84.30
12.44
0.86
2.50
表3-4试验用石油焦粒度分布/%
0.85
0.425~0.85
0.25~0.425
0.18~0.25
0.15~0.18
3.5
38.9
18.0
12.4
8.8
18.4
33.0
23.5
10.0
7.5
10.50
15.5
(3)氯气
试验所用气均为天津化工厂的管道氯气,试验期间体积百分比波动范围为92%~96%。
3.2主要设备及工艺参数
试验所用的主要试验设备有沸腾氯化炉、隔板收尘器和淋洗塔,公司独有的Φ1000无筛板沸腾氯化炉结构示意图见图3-1。
图3-1公司沸腾氯化炉结构示意图
试验主要运行参数见表3-5。
表3-5试验主要工艺参数
编号
项目
工艺参数
1
龙兴钛渣钛渣配比/%
天泰
40
60
80
100
2
试验运行时间/h
—
27
45
25.5
50.3
9.95
3
反应温度/℃
967
963
942
933
928
/
4
炉顶平均温度/℃
741.5
731
716.5
718
688
696
5
配碳比/kg:
kg
100:
30
100:
33
6
钛原料加料速度/kg·
h-1
355.6
393.3
376.5
363.8
351.8
7
氯气平均质量流量/kg·
789
841
951
919
905
3.3工艺流程图
龙兴钛渣钛渣沸腾氯化工业试验的工艺流程图见图3-2。
图3-2龙兴钛渣钛渣沸腾氯化工业试验工艺流程图
3.4试验方法
原料配比:
根据攀渣钛渣原料的特点,为使试验顺利进行,实施与天泰钛渣混合并逐渐增加龙兴钛渣配比的方式进行,配比量分别40%、60%、80%。
在炉况正常及条件允许的情况下,进行100%龙兴钛渣沸腾氯化试验,试验原料成份见表3-6。
表3-6攀渣钛渣与天泰钛渣不同配比成份
配矿比
40%
60%
80%
100%
TiO2/%
89.3
87.8
86.3
∑(CaO+MgO)/%
1.57
3.822
4.948
6.074
7.2
配碳量:
龙兴钛渣由于钙镁含量较高,在氯化过程中床层内钙镁氯化物会不断的增加富积,适当的增加混合料中配碳比,是有效稀释床层中CaCl2和MgCl2浓度的方法之一,反应过剩的碳除了起到稀释的CaCl2和MgCl2浓度之外,还起到包裹、隔离钙镁氯化物的颗粒,阻止颗粒相互粘结、合并以至长大成团。
此次龙兴钛渣沸腾氯化试验采用配碳比为100:
45,并根据试验情况进行适当调整。
排渣:
试验过程中为了防止CaCl2和MgCl2在床层内富积过多有可能造成炉内沸腾状态恶化,炉渣施行每班排一次,并尽可能做到将炉渣排尽。
4试验结果及分析
本次试验是在将氯化炉原有入炉料氯化完全、不停炉的条件下直接加入试验钛原料,采用体积百分比大于92%的Cl2入炉氯化,启炉温度为968℃。
试验过程中,视沸腾炉运行情况,开展了龙兴钛渣配比为40%、60%、80%、100%的沸腾氯化条件试验,在此期间进行了氯化炉温度调整试验和配碳比条件试验,试验在进行到使用100%龙兴钛渣钛渣、配碳比为100:
33条件试验时,因炉壁耐火材料脱落,氯化炉无法继续进行,试验被迫终止。
试验共运行161h,制取粗TiCl4108.3t(产品成份见表4-1),试验结果及试验过程分析如下。
表4-1粗TiCl4产品成份/%
元素
V
TiCl4
FeCl3
AlCl3
SiCl4
固含量
百分含量
0.059
98
0.0055
0.30
0.12
0.50
4.1试验主要技术指标
试验主要技术指标见表4-2。
表4-2试验生产主要技术指标
天泰指标
试验结果
龙兴钛渣高钛渣配比/%
——
配碳比/kg:
运行时间/h
48
50
9
粗TiCl4产品/t
18.89
33.96
18.29
31.44
5.72
钛原料单耗/kg·
t-1粗TiCl4
500.0
508.14
521.20
524.79
543.2
612.38
石油焦单耗/kg·
192.0
228.66
234.69
236.16
236.79
202.96
管道氯单耗/kg·
1004.0
1064.98
1040.24
1095.72
1106.0
1493.52
8
TiO2氯化率/%
94.74
93.10
93.78
94.00
93.81
82.03
Ti总收率/%
92.2
91.8
91.02
91.96
91.24
81.09
10
氯化炉产能/t粗TiCl4·
m-2·
d-1
22.29
21.39
23.07
21.93
21.15
17.56
需要说明的是,在本次试验中,由于天泰公司计量条件有限,还存在以下问题影响试验数据的收集:
①粗四氯化钛,由于天泰公司一个氯化车间是由两台氯化炉组成的,共用一个粗四氯化钛计量槽,试验时另外一台氯化炉仍在在正常生产,导致两台炉子生产的粗四氯化钛混在一起无法精确计量,试验产生的TiCl4的量只能通过系统的总量减去另一台氯化炉的产量估算;
②原料加料速度,试验中采用螺旋加料机进行加料,螺旋的转速与加料速度没有一个比较准确的对应关系,只有依靠用完一批料后除以所用的时间来得出平均数;
③炉渣和收尘渣,每次排放的炉渣和收尘渣未按试验的要求单独称量计重,只能通过堆比重和体积估算。
从表4-1可以看出,配比为40%、60%、80%和100%的龙兴钛渣钛渣沸腾氯化试验的高钛渣单耗分别为508kg.t-1粗TiCl4、521kg.t-1粗TiCl4、525kg.t-1粗TiCl4和543.2kg.t-1粗TiCl4。
,氯化炉产能分别为21.39t粗TiCl4/(m-2·
d-1)、23.07t粗TiCl4/(m-2·
d-1)、21.93t粗TiCl4/(m-2·
d-1)、和21.15t粗TiCl4/(m-2·
d-1),从TiO2的氯化率看,氯化率都在93%以上,Ti收率在90%以上。
4.2炉渣、收尘渣及尾气成份
试验所得炉渣化学成份、收尘渣化学成份、尾气成份结果分别见表4-3、4-4、4-5。
表4-3试验炉渣的化学成份/%
天泰正常生产
5.65
2.07
0.79
0.32
14.97
0.71
40%配比
9.27
1.11
3.33
2.91
1.36
17.67
60%配比
6.43
2.01
3.18
4.44
1.23
17.17
0.34
80%配比
6.50
2.03
3.58
4.65
0.83
15.64
0.5
100%配比
6.40
3.90
5.51
0.81
10.84
0.46
表4-4试验收尘渣的化学成份/%
14.91
2.55
1.27
3.26
13.95
2.3
14.86
12.82
5.16
1.095
5.94
8.323
7.60
22.187
19.25
2.84
1.12
14.14
6.62
17.08
7.57
5.58
0.729
6.82
8.13
11.69
21.49
100%龙兴钛渣
9.597
6.36
0.891
15.517
4.857
13.47
14.073
表4-5尾气成份/V%
项目
Cl2
HCl
CO2
O2
CO
N2
微量
12.25
22.75
8.25
13.75
43
11.75
24
7.75
14
42.5
20.5
16
43.5
21.7
7.3
12.7
47
21.5
43.9
由表4-3炉渣的化学成份可以看出,在本次试验中以龙兴钛渣为原料正常生产的炉渣TiO2的含量为10.84%~17.67%之间,与天泰中TiO2相当,说明此次试验的氯化效果较好。
由表4-4收尘渣的化学成份可以看出,采用龙兴钛渣氯化的收尘渣中TiO2的含量为6.62%~13.47%,较天泰生产时的偏高,对比龙兴钛渣钛渣和天泰钛渣的粒度分布(见表3-2)可以看出,龙兴钛渣钛渣粒度较细,部分细粒级的龙兴钛渣钛渣未氯化就被气体带出氯化炉进入收尘器中,使收尘渣中的TiO2含量偏高。
从表4-5中尾气成份可以看出,尾气中的Cl2均为微量,完全可以达到环保的要求,同时也说明氯化反应进行得较完全,没有过剩的氯气进入尾气系统。
4.3氯气消耗
从表4-1可以看出,配比为40%、60%、80%和100%的龙兴钛渣钛渣沸腾氯化的氯气单耗分别为1.06t/t粗TiCl4、1.04.t/t粗TiCl4、1.095t/t粗TiCl4和1.106t/t粗TiCl4,其氯气单耗均高于天泰公司正常氯化指标1.004t/t粗TiCl4。
经分析,引起氯气消耗过大的主要原因是:
(1)龙兴钛渣钛渣杂质含量
表4-6天泰钛渣和龙兴钛渣钛渣理论氯气消耗量
成份
龙兴钛渣钛渣
含量/%
吨TiCl4理论氯气消耗/kg
747.37
4.19
32.83
2.74
23.37
0.87
3.97
2.98
12.20
34.31
1.83
17.43
30.69
0.35
2.02
10.89
1.74
14.09
48.21
0.61
合计
830.78
898.43
表4-6计算了天泰钛渣和龙兴钛渣钛渣的生产1吨TiCl4理论Cl2消耗量。
从表4-6可以看出,天泰钛渣生产吨TiCl4的理论氯气消耗量为830.78kg,龙兴钛渣钛渣生产吨TiCl4的理论氯气消耗量为898.43kg,因龙兴钛渣钛渣杂质含量增加,龙兴钛渣生产吨TiCl4的理论氯气消耗量比天泰钛渣多898.43-830.78=67.65kg/tTiCl4。
(2)淋洗温度偏高,系统收率偏低
表4-7统计了天泰正常生产时和不同配比龙兴钛渣钛渣沸腾氯化试验时3#淋洗塔出口温度。
从表4-7可以看出,在使用龙兴钛渣钛渣试验时,3#淋洗塔出口温度较天泰钛渣时高。
淋洗温度偏高势必使未被收集的TiCl4气体进入尾气淋洗系统,从试验现象也可以看出,在使用龙兴钛渣钛渣试验时,淋洗系统的的碱消耗量明显增加,且碱洗液中含有大量的白色物质,这也是造成此次100%龙兴钛渣钛渣试验时的系统收率偏低、氯耗偏高的主要原因。
表4-73#淋洗塔出口温度对比
3#淋洗塔出口温度/℃
20~25
22.17
21~25
23.13
21~39
25.91
22~40
25.39
22~34
26.27
(3)配碳量增加
此次试验采用的配碳比为100:
45,配碳量的增加相应增加了3#的加料,3#焦中含有约15%的挥发份,合肥工业大学胡乾定等研究表明,1mol挥发份约与6mol的Cl2发生反应。
由此可以看出,配碳量增加也是造成Cl2消耗量增加的原因之一。
4.4氯化温度
氯化炉内温度不仅是反映氯化炉炉况的关键因素,也是反映氯化效果的重要工艺参数,温度太低会使床层物料结块,炉况恶化,降低钛渣的氯化反应速率和氯化率。
保持炉内温度在一定范围之内为是维持正常生产的基础。
图4-1表示了天泰正常生产时(加料量355.6kg/h,配碳量为100:
30,氯气流量为789kg/h,纯氯)温度波动情况。
由图4-1可以看出,炉顶平均温度为741.5℃,炉中温度基本维持在