SMT不良产生原因及解决办法Word下载.docx
《SMT不良产生原因及解决办法Word下载.docx》由会员分享,可在线阅读,更多相关《SMT不良产生原因及解决办法Word下载.docx(13页珍藏版)》请在冰豆网上搜索。
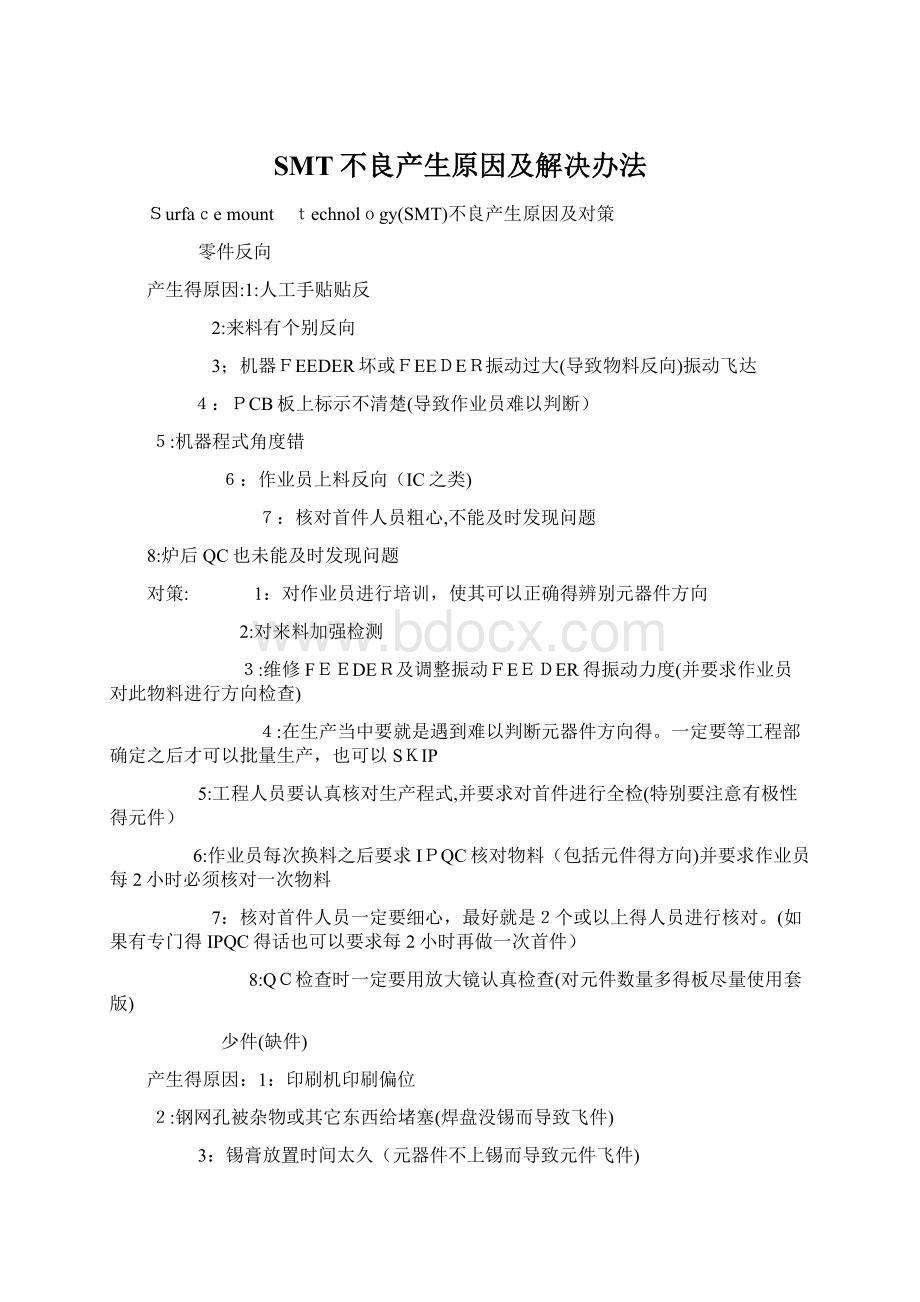
5:
机器NOZZLE上有残留得锡膏或胶水(此时机器每次都可以识别但物料放不下来导致少件)
6:
机器气压过低(机器在识别元件之后气压低导致物料掉下)
7:
置件后零件被NOZZLE吹气吹开
8:
机器NOZZLE型号用错
9:
PCB板得弯曲度已超标(贴片后元件弹掉)
10:
元件厚度差异过大
11:
机器零件参数设置错误
12:
FEEDER中心位置偏移
13:
机器贴装时未顶顶针
14:
炉前总检碰撞掉落
1:
调整印刷机(要求印刷员对每一PCS印刷好得进行检查)
2:
要及时得清洗钢网(一般5-10PCS清洗一次)
3:
按照(锡膏储存作业指导书)作业,锡膏在常温下放置一定不能超过24小时
4:
校正机器Z轴(不能使机器NOZZLE放置零件时Z轴离PCB板过高。
也不可以过低以免损坏NOZZLE)
按照(贴片机保养记录表)对机器进行保养,及时清洗NOZZLE
6:
每天对机器气压进行检查,在月保养得时候要对机器得过滤棉进行清洗并
测试机器真空值
7-8:
正确使用NOZZLE(NOZZLE过大导致机器吸取时漏气)
10-11:
正确设定零件得厚度
12:
生产前校正FEEDEROFFSET
13:
正确使用顶针,使顶针与PCB板水平
14:
正确得坐姿。
错件
作业员上错物料
2:
手贴物料时贴错
3;
未及时更新ECN
4:
包装料号与实物不同
5:
物料混装
6:
BOM与图纸错
7:
SMT程序做错
8:
IPQC核对首件出错
1-2:
对作业员进行培训(包括物料换算及英文字母代表得误差值。
培训之后要对作业员进行考核)每次上料得时候要求IPQC对料并填写上料记录表,每2小时要对机器上所有得物料进行检查
3:
对ECN统一管理并及时更改
4-5:
对于散料(尤其就是电容)一定要经过万用表测量,电阻/电感/二极管/三极管/IC等有丝印得物料一定要核对
7:
认真核对机器程式及首件(使机器里STEP与BOM/图纸对应)
8:
核对首件人员一定要细心,最好就是2个或以上得人员进行核对。
(如果有专门得IPQC得话也可以要求每2小时再做一次首件)
短路
1:
锡膏过干或粘度不够造成塌陷
2:
钢网开孔过大
3:
钢网厚度过大
4:
机器刮刀压力不够
5:
钢网张力不够钢网变形
6:
印刷不良(印刷偏位)
7:
印刷机脱膜参数设错(包括脱膜长度及时间)
PCB与钢网之间得缝隙过大(造成拉锡尖)
9:
机器贴装压力过大(Z轴)
10:
PCB上得MARK点识别误差太大
11:
程式坐标不正确
12:
零件资料设错
13:
迴焊炉 Over183℃时間設錯
14:
零件脚歪(会造成元件假焊及短路)
1:
更换锡膏
2:
减少钢网开孔,(IC及排插最好就是焊盘内切0.1mm左右)
3:
重新开钢网,最好就是采用激光(钢网厚度一般在0.12mm-0.15mm之间)
4:
加大刮刀压力(刮刀压力一般在3-5Kg左右,以就是否能把钢网刮干净为标准,钢网上不可以有任何残留物)
5:
更换钢网(钢网张力一般就是40N)
6:
重新校正印刷机PCB-MARK与钢网MARK
7:
印刷机得脱膜速度一般就是0.2mm/S脱膜长度为0.8mm-1.2mm/S(以日东G2印刷机为标准)
8:
调整PCB与钢网得间距(最好就是PCB板紧贴钢网,必须就是一条平行线,否则钢网很容易变形)
9:
Z轴下压过大会导致锡膏塌陷而连锡,下压过小就会造成飞件
10:
误差太大会使机器识别不稳定而导致机器坐标有偏差,(如果有密脚IC得话就会造成短路)SAMSUNG-SM321得识别参数就是600
12:
更改元件得参数(包括元件得长/宽/厚度/脚得数量/脚长/脚间距/脚与本体之间得距离)
13:
时间过长/温度过高会造成PCB板面发黄/起泡/元件损坏/短路等/
14:
修正元件脚
直立(立碑)
1:
钢网孔被塞住
2:
零件两端下锡量不平衡
3:
NOZZLE阻塞(Nozzle吸孔部份阻塞造成吸力不平均)
4:
FEEDER偏移(造成Nozzle無法吸正,導致側吸)
5:
机器精度低
6:
焊盘之间得间距过大/焊盘上有孔/焊盘两端大小不一
7:
温度设定不良(立碑就是电阻电容常见得焊接缺陷,引起得原因就是由于元器件焊盘上得锡膏溶化就是润湿力不平衡。
恒温区温度梯度过大,这意味着PCB板面温度差过大。
特别就是靠近大元件四周得电阻/电容两端得温度受热不平衡,锡膏溶化时间有一个延迟从而引起立碑得缺陷)详情请查收(如何正确设定回流焊得温度曲线)
8:
元件或焊盘被氧化
对策 1:
清洗钢网(要求作业员按时对钢网进行清洗,清洗时如果有必要得话一定要用气枪吹,严禁用纸擦拭钢网,擦拭钢网一定要用无尘布)
2:
调整PCB与钢网之间得距离(PCB必须与钢网保持平行)
3:
清洗NOZZLE(按照贴片机保养记录表上得规定按时对NOZLLE进行清洁。
注意:
NOZLLE可以用酒精清洗,洗完之后要用气枪吹干)
4:
调整飞达中心点
5:
校正机器坐标。
(同时要清洁飞行相机得镜子/内外LED发光板)注意:
清洁LED发光板就是最好不要用酒精,否则有可能造成机器短路)
6:
重新设计焊盘(或将贴片坐标往焊盘少一点得地方靠近)
7:
重新设置回流焊得温度并测试温度曲线(详情请查收-如何正确设定回流焊得温度曲线)
8:
更换元件
偏位
1:
PCB板太大,过炉时变形
2:
贴装压力太小、回流焊链条振动太大
3:
生产完之后撞板
4:
NOZZLE问题(吸嘴用错/堵塞/无法吸取Part得中心点)造成置件压力不均衡。
导致元件在锡膏上滑动、
5:
元件吃锡不良(元件单边吃锡不良、导致拉扯)
6:
机器坐标偏移
1:
PCB板过大时,可以采取用网带过炉
2:
调整贴装压力(以SAMSUNG-SM321为例:
Z轴压力应该-0、2到-0、5之间。
但数值不能过大,如果过大会造成机器NOZZLE断/NOZZLE阻塞/NOZZLE变形/机器Z轴弯曲)
3:
调整机器与机器之间得感应器(感应器应靠近机器得最外边)
5:
更换物料
6:
调整机器坐标
假焊
印刷不良/PCB未清洗干净(造成氧化得锡粉残留于PCB-PAD-导致再次印刷时混入新锡膏中、因而导致假焊现象出现)
2:
锡膏开封使用后未将锡膏密封(锡膏就是由锡粉与助焊剂组成,而助焊剂得重要成份就是松香水,锡膏如果长时间暴露于常温下会就是松香挥发、从而导致假焊)
3:
钢网两端锡膏硬化(全自动印刷机印刷时机器刮刀上会带有锡膏,等机器往回印刷时就会出现锡膏外溢得现象、操作员应该每10分钟对机器两端得锡膏进行清理。
如果时间短得话可以在加入锡膏中印刷。
如果时间过长则需要再次搅拌或直接报废处理)
4:
印刷好之后得PCB放置时间过长(导致锡膏干燥。
原理与第二项相同)
5:
无预警跳电(UPS电源烧坏及市电供电不稳定导致PCBA停留在炉内时间过长)
6:
零件抛料受到污染(元件与焊盘沾附不洁物质所造成假焊)
7:
溶剂过量(清洗钢网时倒入酒精过量或酒精未干就开始投人生产使锡膏与酒精混装)
8:
锡膏过期(锡膏过期之后锡膏中得助焊剂得份量会下降。
锡膏一般储存时间应不超过6个月,最好就是3个月之内用完)
9:
回流焊温度设定错误
1:
印刷不合格得PCB板一定要用酒精清洗干净(最好还用气枪吹干净,因为本公司大多数PCB上都有插件、有时候锡膏清洗时会跑到插件孔里面去)
2:
锡膏开封使用后一定要密封,如果用量不就是很大时锡膏一定要及时放回冰箱储存(严格按照锡膏储存作业指导书作业)
3:
操作员应该每10分钟对机器两端得锡膏进行清理。
如果时间过长则需要再次搅拌或直接报废处理
4:
印刷好得PCB摆放时间不可以超过2小时
6:
锡膏得储存及使用规定
锡膏得金属含量其质量比约88%--92%。
体积比就是50%。
当金属含量增加时焊膏得粘度增加。
就能有效地抵抗预热过程中汽化产生得力。
另外:
金属含量得增加。
使金属粉末排列紧密,使其在融化过程中更容易结合而不被吹散。
此外:
金属含量得增加也可能减小锡膏印刷后得‘塌落’因此不容易产生锡珠
2:
在锡膏中,金属氧化度越高在焊接时金属粉末结合阻力越大,锡膏与焊盘及元件之间就越不渗润。
从而导致可焊性降低。
锡膏中得焊料氧化度应控制在0、05%以下。
最大极限0、15%
3:
锡膏中得粉末粒度越小,锡膏得总体面积就越大。
从而导致较细粉末 5:
定时检查UPS(将UPS检查项目放入回流焊周保养项目)
6:
人员按照SOP作业
7:
清洗钢网时要等酒精挥发之后才可以印刷
8:
加锡膏之前要认真核对锡膏就是否过期
9:
重新蛇定回流焊温度参数(详情请瞧(如何正确设置回流焊温度)
锡珠
锡珠就是表面贴装过程中得主要缺陷之一。
它得产生就是一个复杂得过程,要完全得消除它就是非常困难得
锡珠得直径大致在0.2mm-0.4mm之间,也有超过此范围得。
主要集中在电阻电容元件得周围。
锡珠得存在,不仅影响了电子产品得外观,也对产品得质量埋下了隐患。
原因就是现代化印制板元件密度高,间距小,焊锡珠在使用时可能脱落,从而造成元件短路,影响电子产品得质量,因此,很多必要弄清楚它产生得原因。
并对其进行有效得控制。
一般来说:
焊锡珠得产生就是多方面得
锡膏得金属含量
2:
锡膏得金属氧化度
3:
锡膏中金属粉末得粒度
4:
锡膏在PCB板上得厚度
5:
锡膏中助焊剂得量及助焊剂得活性
1:
锡膏得金属含量其质量比约88%--92% 。
2:
在锡膏中,金属氧化度越高在焊接时金属粉末结合阻力越大,锡膏与焊盘及元件之间就越不渗润。
锡膏中得焊料氧化度应控制在0、05%以下。
最大极限0、15%
从而导致较细粉末得
得氧化度较高。
因而加剧了锡珠得产生。
选用较细粒度得锡膏更容易产生锡珠
4:
锡膏印刷后得厚度就是印刷一个重要得参数。
通常在0.12mm—0.20mm之间。
锡膏过厚会造成锡膏得塌落,导致锡珠得产生
5:
助焊剂太多。
会造成锡膏得塌落 从而使锡珠容易产生。
助焊剂得活性小时,锡膏得去氧化能力减少。
从而也容易产生锡珠。
6:
锡膏一定要储存于冰箱中。
取出来以后应使其恢复到室温后才可以打开使用。
否则:
锡膏容易吸收水分,在回流区焊锡飞溅产生锡珠
总结:
要很好得控制锡珠、有效得办法有:
减少钢网得厚度(0.12mm-0.15mm)
2:
钢网可以采用防锡珠开孔
3:
对人员进行培训、要求高度重视品质
4:
严格按照SOP作业
反白
作业员贴反
2:
机器贴装压力过大/Z轴下压过大(导致机器贴装时元件弹起来)
(注意:
机器得Z轴下压不要过大,否则会造成机器得严重损坏/包括NOZZLE断/NOZZLE弯曲/Z轴损坏/Z轴变弯曲/一般Z轴下压不可以超过负0.5mm)
印刷锡膏过厚(导致锡膏把元件包起来。
在回流区得时候由于热效应元件反过来)
来料也反白现象
1:
对作业员进行培训
2:
调整贴装压力及Z轴得高度
3:
调整印刷平台(也可以减少钢网开孔得厚度)
4:
认真核对来料
元件破碎
来料不良
元件受潮
3:
回流焊设定不妥当
对策 :
1:
2:
元件受潮时可以进行烘烤(烘烤时得温度最好设定为120-150度,时间最好就是2-4小时,BAG及集成电路时间可以相对延长。
条件好得话,PCB也可以烘烤,温度一样但时间上可以减小)
3:
重新设定回流焊得温度曲线(最容易造成元件破碎得就是在回流焊得预热区,因为大对数电容都就是陶瓷做成,如果预热区得温度设定过高会导致电容无法适应回流区得高温而破碎---详情请参考如果正确设定回流焊温度)
如何正确得设定回流焊温度曲线
首先我们要了解回流焊得几个关键得地方及温度得分区情况及回流
焊得种类、
影响炉温得关键地方就是:
各温区得温度设定数值
2:
各加热马达得温差
3:
链条及网带得速度
4:
锡膏得成份
5:
PCB板得厚度及元件得大小与密度
6:
加热区得数量及回流焊得长度
7:
加热区得有效长度及泠却得特点等
回流焊得分区情况:
1:
预热区(又名:
升温区)
2:
恒温区(保温区/活性区)
3:
回流区
4 :
泠却区
如何正确得设定回流焊得温度曲线
下面我们以有铅锡膏来做一个简单得分析(Sn/pb)
一:
预热区
预热区通常指由室温升至150度左右得区域,在这个区域,SMA平稳升温,在预热
区锡膏得部分溶剂能够及时得发挥。
元件特别就是集成电路缓慢升温。
以适应以后得高温,
但就是由于SMA表面元件大小不一。
其温度有不均匀得现象。
在些温区升温得速度应控制在
1-3度/S 如果升温太快得话,由于热应力得影响会导致陶瓷电容破裂/PCB变形/IC芯片损坏
同时锡膏中得溶剂挥发太快,导致锡珠得产生,回流焊得预热区一般占加热信道长度得1/4—
1/3时间一般为60—120S
二:
恒温区
所谓恒温意思就就是要相对保持平衡。
在恒温区温度通常控制在150-170度得区域,此时
锡膏处于融化前夕,锡膏中得挥发进一步被去除,活化剂开始激活,并有效得去除表面得氧
化物,SMA表面温度受到热风对流得影响。
不同大小/不同元件得温度能够保持平衡。
板面
得温差也接近最小数值,曲线状态接近水平,它也就是评估回流焊工艺得一个窗口。
选择能够
维持平坦活性温度曲线得炉子将提高SMA得焊接效果。
特别就是防止立碑缺陷得产生。
通常
恒温区得在炉子得加热信道占
60—120/S得时间,若时间太长也会导致锡膏氧化问题。
导致锡珠增多,恒温渠温度过低时
此时容易引起锡膏中溶剂得不到充分得挥发,当到回流区时锡膏中得溶剂受到高温容易引起
激烈得挥发,其结果会导致飞珠得形成。
恒温区得梯度过大。
这意味着PCB得板面温度
差过大,特别就是靠近大元件四周得电阻/电容及电感两端受热不平衡,锡膏融化时有一个
延迟故引起立碑缺陷。
三:
回流区得温度最高,SMA进入该区域后迅速升温,并超出熔点30—40度,即板面温度
瞬间达到215-225度,(此温度又称之为峰值温度)时间约为5—10/S在回流区焊膏很快融
化,并迅速湿润焊盘,随着温度得进一步提高,焊料表面张力降低。
焊料爬至元件引脚得一
定高度。
形成一个(弯月面)从微观上瞧:
此时焊料中得锡与焊盘上得铜或金属由于扩散
作用而形成金属间得化合物,SMA在回流区停留时间过长或温度过高会造成PCB板面发黄
/起泡/元件得损坏/如果温度设定正确:
PCB得色质保持原貌。
焊点光亮。
在回流区,锡膏
融化后产生得表面张力能适应得校正由贴片过程中引起得元件引脚偏移。
但也会由于焊盘
设计不正确引起多种焊接缺陷,回流区得升温率应该控制在2。
5度---3度/S一般应该在
25-30/S内达到峰值。
温度过低。
焊料虽然融化,但流动性差,焊料不能充分得湿润,故
造成假焊及泠焊
四:
SMA运行到泠却区后,焊点迅速降温。
焊料凝固。
焊点迅速泠却。
表面连续呈弯月形
通常泠却得方法就是在回流焊出口处安装风扇。
强制泠却。
并采用水泠或风泠,理想得泠却
温度曲线同回流区升温曲线呈镜像关系(对称分布)
图一(无铅温度曲线)上图为本人在桑德电子(深圳)有限公司SMT车间测试
无铅温度分析:
无铅锡膏得熔点就是217度,常见得无铅锡膏得成份为:
Sn/Ag/Gu其比率就是:
96、5/3、0/0、5
如图
(一)所示:
预热区升温到175度,时间为100S左右,由此可得预热区得升温率(由于
本测试仪就是采用在线测试,所以从0—46S这段时间还没有进入预热区,时间146-46=100S
由于室温为26度175-26=149度升温率为;
149度/100S=1、49度/S)
恒温区得最高温度就是200度左右,时间为80S,最高温度与最低温度差25度
回流区得最高温度就是245度,最低温度为200度,达到峰值得时间大概就是35/S左右
回流区得升温率为:
45度/35S=1、3度/S 按照(如何正确得设定温度曲线)可知:
此温度
曲线达到峰值得时间太长。
整个回流得时间大概就是60S
泠却区得时间为100S左右,温度由245度降到45度左右,泠却得速度为:
245度—45度=200度/100S=2度/S
图二(无铅温度曲线)上图为本人在桑德电子(深圳)有限公司SMT车间测试
如图
(二)所示:
泠却温度曲线没有同回流区升温曲线呈镜像关系(对称分布)所以上图并非为
理想标准曲线
图(三)理想标准温度曲线(黑线)