长形堆取料机中文说明书0MWord格式.docx
《长形堆取料机中文说明书0MWord格式.docx》由会员分享,可在线阅读,更多相关《长形堆取料机中文说明书0MWord格式.docx(25页珍藏版)》请在冰豆网上搜索。
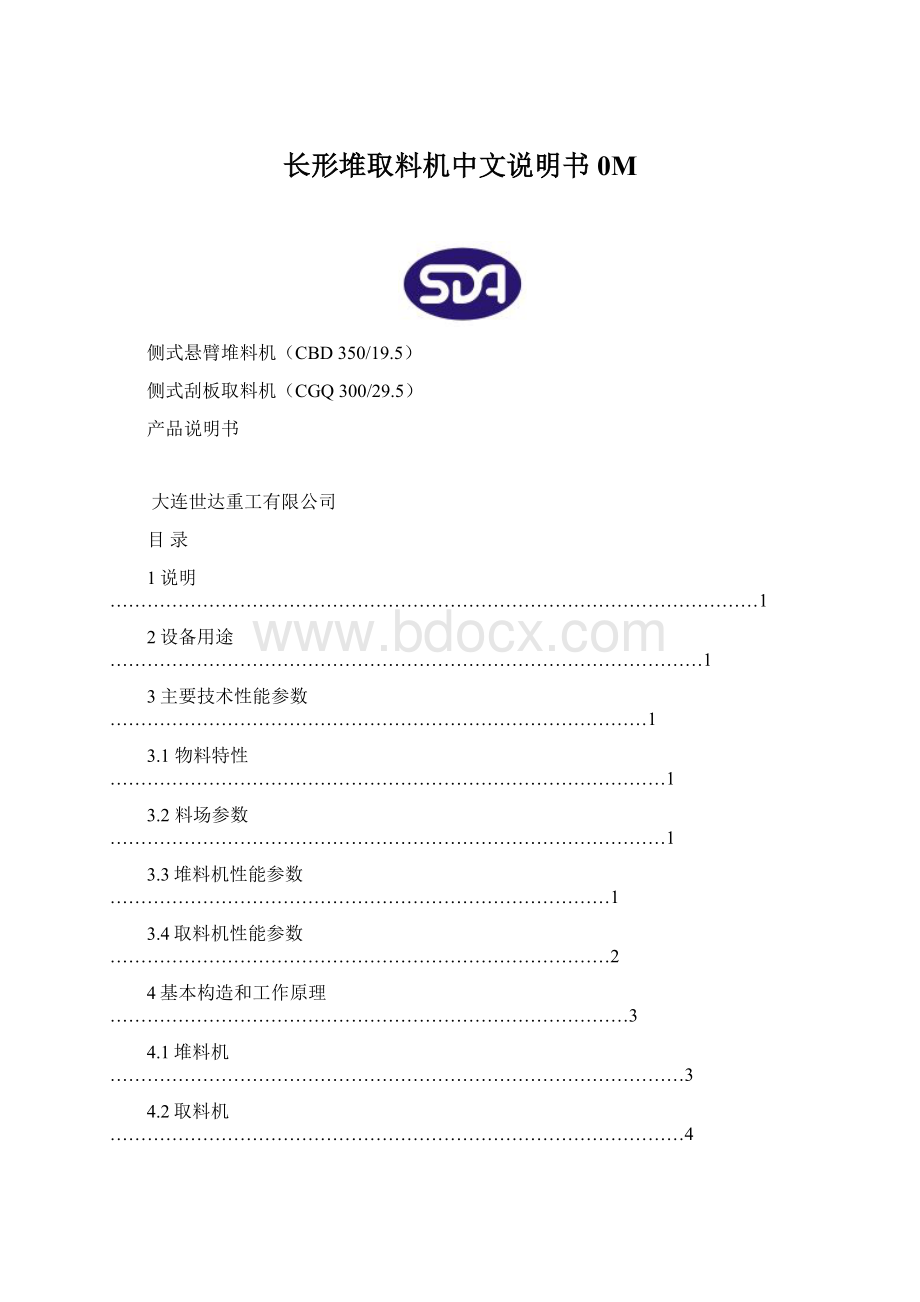
1.0t/m3
物料粒度:
0-50mm
休止角:
38°
3.2料场参数
料场长度:
379m
料堆宽度:
30m
料堆高度:
12.89m
3.3堆料机性能参数
规格型号:
CBD350/19.5
图号:
CBD197.00
堆料能力:
350t/h
堆料方式:
人字形堆料法
行走驱动装置:
轨道中心距:
4000mm
钢轨型号:
50kg/m
行走速度:
19m/min
车轮直径:
Φ630mm
车轮轮压:
28T
电机型号:
YEJ132M2-6
功率:
5.5KW
转速:
960r/min
减速器速比:
100
驱动装置数量:
2
悬臂部分:
悬臂长度:
19.5m
悬臂胶带机:
胶带机带宽:
1000mm
胶带机带速:
1.6m/s
头尾轮中心距:
21.73m
电动滚筒型号:
JWDⅡ22-1.6-1000-630
驱动电机功率:
22KW
驱动电机型号:
Yga180L-4
驱动电机速度:
1480r/min
传动滚筒直径:
φ630mm
变幅机构:
变幅角度:
-14°
~+16°
驱动方式:
液压
变幅液压站功率:
5.5KW
变幅油缸行程:
1400mm
变幅油缸速度:
0.3~0.6m/min
油缸直径:
φ140mm
来料车:
倾角:
16°
动力电缆卷盘:
JDO-650(D)-T
卷盘外径:
φ3600mm
电缆规格:
YCW3×
35+1×
10
电机功率:
3KW
控制电缆卷盘:
JDO-650(D)-KT37
CEFR30×
2.5
1.5KW
来料胶带机:
1.6m/s
控制方式:
PC程控、手控
动力电压:
380V
控制电压:
220V
总装机功率:
60KW
3.4取料机性能参数
CGQ300/29.5
图号:
CGQ108.00
取料能力:
300t/h
钢轨:
QU80
刮板链节距:
500mm
刮板尺寸:
1400×
300(mm)
Φ710
最大轮压:
50t
端梁取料运行速度:
0.2~2m/min
端梁取料时驱动功率:
2×
1.5KW
端梁调车时运行速度:
10.4m/min
端梁调车时驱动功率:
5.5KW
钢丝绳速度:
24/2.4m/min
卷扬提升功率:
13/2kw
刮板链速:
0.5m/s
刮板驱动功率:
75KW
JDO-1250-T
Φ4200mm
驱动功率:
3KW
YCW3×
70+1×
25
JDO-650-KT37
1.5KW
Φ3600mm
CEFR(37×
1.5)
380V50HZ
220V50HZ
135KW
4.基本构造和工作原理
4.1堆料机
堆料机主要由悬臂部分、行走机构、液压系统、来料车、轨道部分、电缆坑、动力电缆卷盘、控制电缆卷盘、限位开关装置等组成。
4.1.1悬臂部分
悬臂架由两个变截面的工字型梁构成,横向用钢板连接成整体,工字型梁采用钢板焊接成型。
因运输限制,臂架厂内分段制造,现场焊接成整体。
悬臂架上面安装有胶带输送机,胶带机可随臂架上仰16°
、下俯14°
,胶带机的传动采用电动滚筒。
张紧装置设在头部卸料点处,使胶带保持足够的张力。
张紧装置采用螺旋张紧。
胶带机上设有料流检测装置,当胶带机上无料时发出信号,堆料机停机,同时还设有打滑检测器、防跑偏等保护装置。
胶带机头、尾部设有清扫器。
头部卸料改向滚筒处设有可调挡板,现场可以根据实际落料情况调整挡板角度、位置来调整落料点。
悬臂前端垂吊两个料位探测仪。
随着堆料机一边往复运动,一边堆积物料,料堆逐渐升高,当料堆与探测仪接触时,探测仪发出信号,传回控制室,控制室启动变幅液压系统,通过油缸推动悬臂提升一个预先给定的高度。
两个探测仪,一个正常工作时使用,另一个用作极限保护。
悬臂尾部设有配重箱,箱内装有铸铁及混凝土配重块。
悬臂两侧设有走台,一直通到悬臂的前端,以备检修、巡视胶带机之用。
悬臂下部设有两处支撑铰点,一处是与行走机构的门架上部铰接,使臂架可绕铰点在垂直面内俯仰;
另一处是通过关节轴承与液压缸的活塞杆端铰接,随着活塞杆在油缸中伸缩,实现臂架变幅运动。
液压缸尾部通过球铰铰接在门架的下部。
在悬臂与三角形门架铰点处,设有角度限位开关,正常运行时,悬臂在-14°
之间运行;
当换堆时,悬臂上升到最大角度16°
。
4.1.2行走机构
行走机构由门架和行走驱动装置组成。
门架通过球铰与上部悬臂铰接,堆料臂的全部重量压在门架上。
门架下端两侧分别与一套驱动装置铰接(驱动装置共2套)。
每套驱动装置由一台4kw的电机驱动。
驱动装置实现软启动、延时制动。
门架下部设有平台,用来安装变幅机构的液压站。
行走驱动装置采用电机—制动器—减速器—车轮系统的传动形式,驱动系统的同步运行是靠结构刚性实现的。
车轮架的两端设置缓冲器和轨道清扫器。
在门架的横梁上吊装一套行走限位装置,所有行走限位开关均安装在吊杆上,随堆料机同步行走,以实现堆料机的限位。
(关于限位开关功能的详细说明参见图纸和电气说明书。
)
4.1.3来料车
堆料胶带机从来料车通过,将堆料胶带机运来的物料通过来料车卸到悬臂的胶带机上。
来料车由卸料斗、斜梁、小立柱、斜梁拉杆等组成。
卸料斗悬挂在斜梁前端,使物料通过卸料斗卸到悬臂的胶带面上。
斜梁由两根焊接工字型梁组成,斜梁上设有胶带机托辊,前端设有卸料改向滚筒,尾部设有防止空车时飘带的压辊。
小立柱下端装有两组车轮。
卸料改向滚筒处设有可调挡板,现场可以根据实际落料情况调整挡板角度、位置来调整落料点。
来料车的前端斜梁拉杆与行走机构的门架通过铰轴联接,使来料车能够随行走机构同步运行。
4.1.4液压系统
液压系统实现悬臂的变幅运动。
液压系统由液压站、油缸组成,液压站安装在三角形门架下部的平台上,而油缸支撑在门架和悬臂之间。
4.1.5电缆卷盘
动力电缆卷盘由单排大直径卷盘、集电滑环、减速器及力矩堵转电机组成。
外界电源通过料场中部电缆坑由电缆通到卷盘上,再由卷盘通到堆料机配电柜。
控制电缆卷盘由单排大直径卷盘、集电滑环、减速器及力矩堵转电机组成。
主要功能是把堆料机的各种联系反映信号通过多芯电缆与中控室联系起来。
4.2取料机
侧式刮板取料机由刮板取料系统、卷扬提升系统、机架部分、固定端梁、摆动端梁、轨道系统、导料槽、动力电缆卷盘、控制电缆卷盘等部分组成。
4.2.1刮板取料系统
刮板取料系统是本机实现取料功能的主要部件。
驱动装置通过锁紧盘联接在驱动轴上,驱动轴上的链轮带动链条及固定在链条上的刮板在悬臂架的支承下循环运转,将物料刮取到料仓一侧。
驱动装置由电机、偶合器和减速器组成,减速器为直角轴全硬齿面空心轴减速器。
臂架为两个工字形板梁中间加交错连杆的结构,梁的上、下分别布置有支承链条的轨道导槽。
在改向链轮一端设有带塔形的张紧装置,可调节链条的松紧。
链条采用套筒滚子链。
4.2.2机架及行走端梁
机架和行走端梁的作用是支承整机重量并驱动取料机在料场内的轨道上往复运行,机架采用了箱形结构的刚性平台,行走端梁由车轮组、驱动装置和支承结构梁组成,其下部可在轨道上行走,上部与机架平台一侧用螺栓刚性连接(固定端梁),另一侧铰接(摆动端梁)。
两套驱动装置均设在固定端梁上,构成单侧双驱动形式。
驱动装置由电机和行星摆线减速器、电磁离合器、调车电机和直交轴减速器、制动器等组成。
在取料机进行取料工作行走时,取料电机驱动车轮组,此时电磁离合器处于通电状态,即合的位置。
当调车时,由调车电机驱动车轮组,此时电磁离合器处于断电状态,即脱开状态。
注意:
二个电机不能同时处于工作状态,启动其中一台电机,另一个电机必须首先停止运行,当设备调试好后取料量的调整依靠改变行走电机的频率来实现。
4.2.3卷扬提升系统
该系统是完成刮板取料系统变幅的机构,由支承架和电动葫芦、滑轮组等组成,并带有过载保护装置。
4.2.4链条润滑系统
本机在机架的一侧设有稀油润滑站,通过油管和给油指示器将润滑油滴在链条上保证两条道路正常工作。
在正常工作情况下,要求链条每工作三小时就需润滑一次,每次润滑5分钟,每次总油量为1.25升。
4.2.5导料槽
导料槽设计有可调溜板,可跟据实际落料情况调节合适的角度,保证物料准确落在出料胶带机上。
导料槽内设有耐磨衬板。
4.2.6电缆卷盘
a.动力电缆卷盘由单排大直径卷盘、集电滑环、减速器及力矩堵转电机组成。
外界电源通过料场中部电缆坑由电缆通到卷盘上,再由卷盘通到取料机配电柜。
b.控制电缆卷盘由单排大直径卷盘、集电滑环、减速器及力矩堵转电机组成。
5.操作
本套设备采用三种操作方式,即:
集中程控、手控和机旁(维修)控制。
每种操作是通过工况转换开关实现的。
5.1手工操作
手工操作(机上人工控制)适用于调试过程中所需要的工况和自动控制出现故障,要求取料机继续工作,允许按非规定的取料方式取料。
操作人员在机上控制室内,控制操作盘上相应按钮进行人工取料作业。
只能在操作台上进行,通过操作台上的控制按钮对各部进行单独操作。
当工况开关至于手动位置时,自动、机旁(维修)工况均不能切入,手动控制可使各系统之间失去相互联锁(电缆卷盘与行走机构的联锁保留),但各系统的各项保护仍起作用。
5.2自动操作
自动控制方式下的堆、取料作业由中控室和机上控制室均可实施。
当需要中控室对堆取料机自动控制时,操作人员只要把操作台上的自动操作按钮按下,然后按下启动按钮,堆、取料机上所有的用电设备将按照预定的程序启动,整机操作投入正常自动运行作业状态。
在中控室的操作台上,通过按动按钮可以对堆取料机实现整机系统的启动或停车。
在自动控制状态下堆料机起机前首先响铃,启动顺序是:
a.启动悬臂上的卸料皮带机
b.启动液压系统
c.启动堆料皮带机(连锁信号)
d.启动电缆卷盘
e.启动行走机构
正常停车顺序:
a.停止堆料皮带机(连锁信号)
b.停止悬臂上的卸料皮带机
c.停止行走机构
d.停止电缆卷盘
在自动控制状态下取料机起机前首先响铃,启动顺序是:
a.启动取料皮带机(连锁信号)
b.启动电缆卷盘
c.启动刮板输送系统
d.启动耙车
e.启动行走端梁
a.停止刮板取料系统。
b.停止行走机构
c.卷扬提升系统将刮板臂提升至45度位置,停止卷扬提升系统。
d.停止电缆卷盘。
e.通知出料胶带机停止运行。
5.3机旁(维修)操作
只能在现场机旁进行操作。
当工况开关至于机旁(维修)位置时自动工况及手动工况不能切入,手动工况的功能,机旁工况也具备。
但操作按钮只装在有利于维修操作的位置上。
机旁工况不装行走操作按钮。
5.4调车
无论是调车工况还是堆料机与取料机交错工况,取料机的刮板臂必须抬升到最高极限位置即45度,然后原地不动等待堆料机错车或运行到指定取料区域。
5.5事故停车
凡在本系统任何地方出现事故,必须停车时,按动紧急开关,使取料机马上停止工作。
6.检查、维修
设备能够无故障地运行并且有较长时间的使用寿命,在很大程度上取决于经常的检查和良好的使用、维护、保养。
为保证设备正常工作,要求工作现场建立严格的交接班和操作人员定时巡视制度。
要求操作和维修人员在现场经常进行巡视,在出现故障时能及时发现并得到处理。
为保证设备正常工作并在出现故障时能及时发现并得到处理,本套设备设有报警装置,当某部位发生故障,就会通过电控系统在现场和中控室发出声光报警信号,提醒操作人员查明原因,及时检修,排除故障。
在平时,操作人员应经常检查联接处、铰接处的螺栓是否松动、卡死现象,驱动装置是否有异常声音,如发现问题应查明原因,及时解决,同时根据润滑项目表中的规定结合运转情况进行必要的润滑。
设备的检查,用户应制订定期检查制度,日常检查项目和要求见表1。
表1设备的检查项目和要求
序号
检查项目
技术要求
1
轨道
检查轨道无下沉、变形,压板螺栓无松动现象,应及时校正轨道,拧紧螺栓。
2
电缆
检查动力及控制电缆有无破损老化及触点接触不良、烧焦等现象,应及时修复。
3
减速器及液压站油箱的油位
油位若低于规定的标准,应及时补充并按规定换油周期更换新油。
4
制动器
制动瓦与制动轮间隙正常、制动可靠。
若制动瓦磨损应及时更换,及时清除制动轮上的污物。
5
轴承座
固定螺栓无松动,润滑良好。
6
胶带机
胶带无断裂、撕裂,张紧适度,托辊滚筒运转灵活,各种保护装置良好。
7
电气元件及
限位开关
在机器开动时,观察各元件动作是否灵敏,发现接触点不正常时,及时修复。
各限位开关动作应准确、可靠。
6.1检修
要建立大修、中修和日常的维护制度,大修时全部零件都应拆下检查并更换磨损零件和密封件。
检修的主要内容有:
液压系统中齿轮泵、电磁阀及各种阀件;
液压缸的磨损件;
各种保护装置及料位开关;
行走机构中的减速机、制动器及车轮的磨损;
各个转动部位的轴承是否良好,并根据磨损件的使用年限及使用情况来决定是否修复或更换。
6.2设备故障的诊断及处理(见表2)
表2设备故障的诊断及处理
故障形式
故障原因
消除故障措施
悬臂胶带机打滑
1.物料过载
2.滚筒有油污
3.张紧力不够
减少物料
清除油污
加大张紧力
悬臂胶带机胶带边
缘损伤
1.与漏斗、溜槽、机架碰撞
调整胶带与相关件距离,使其脱离接触
悬臂胶带机跑偏
1.头、尾滚筒中心线与输送机中心线不垂直
2.头、尾滚筒与托辊安装不对中
3.胶带接头不直
4.受料偏载
调整滚筒轴承座,重新安装、找正
重新连接
调节卸料挡板,使受料居中
滚筒转动不灵活
1.轴承损坏
2.密封碰撞
3.两侧轴承座中心线不同轴
更换轴承
修理密封,加大间隙
重新安装、找正,拧紧固定螺栓
堆料机制动不灵
1.制动器制动瓦与制动轮间隙过大
调整间隙使其符合制动器说明书的要求
6.3报警信号
本取料机设有报警装置,当某部位发生故障,就会通过电控系统在现场和中控室发出声光报警信号,提醒操作人员查明原因,及时检修,排除故障。
6.4润滑
根据下表3结合运转情况进行必要的润滑。
表3
润滑点
润滑
方式
润滑剂
一次加油量
(L)
换油周期
备注
名称
标准代号
行
走
装
置
减速器
换油
按产品说明书
车轮组滚子
轴承
油枪
ZG-3钙基
润滑脂
GB491-65
加满
每板一次
每年清洗一次
挡轮滚子
动力电缆卷盘
按产品说明书
控制电缆卷盘
刮
板
取
料
系
统
头部链轮组
滚子轴承
滑动轴承
尾部链轮组
张紧装置导轨
涂抹
视具体情况定
链条
泵站
滴油
N320中负荷
工业齿轮油
GB5903-66
1.25
三小时一次
油箱容
量40L
液力偶合器
卷
筒
电动葫芦
钢丝绳
ZJ-S石墨烃
基润滑脂
SY1507-65
视需要加脂
滑轮组
吊杆滑动
6.5取料机的检查项目和要求
6.5.1取料系统链条是本机重要部件之一,操作人员要检查润滑系统的调油嘴应对准内外链板的间隙。
6.5.2刮板链条由于某种事故造成局部损坏,可单独更换坏的链条,但需要两条链子对应部位同时更换,以保证两条链条啮合正确。
6.5.3当输送链磨损后伸长程度达到2%时,必须全部更换新链条。
6.5.4为使两条链板得到同样的张紧力,可通过张紧装置的螺母来调整。
6.5.5刮板上的刮齿磨损后,可将其调头使用或更换。
6.5.6刮板表面固定的耐磨衬板,当其磨损危机刮板体时,应及时予以更换。
6.5.7刮板取料系统的驱动链轮和尾部链轮是分体组装结构,轮缘由4片扇形齿块用螺栓与轮毂紧固在一起,应定期检查齿圈磨损情况,更换时不需拆卸链条即可更换齿块。
6.5.8卷扬部分中电动葫芦钢丝绳磨损或断丝达到报废标准中规定的数值时,应及时更换。
6.5.9每隔2000小时,要进行一次钢轨垫板检查,如有松动应及时紧固。
平时,操作人员应经常检查连接处、铰接处螺栓是否松动、卡死现象,驱动装置是否有异常声音,如有应查明原因,及时解决,同时结合运转情况进行必要的润滑。
用户应制订定期检查制度。
建立大、中修和日常维护制度。
7.安装
详细阅读、熟悉本说明书及随机所带图纸,了解本机的主要构造、组成及性能,掌握安装要领,按照下列步骤和要求安装。
7.1.安装前准备
a.安装前必须将取料机的全部机件查点清楚,保证完好无损。
并准备好清洗油、垫木、安装工具及吊运设备
b.在工地附近准备50X30m的水平场地,用于放置即将安装的部件。
现场应有适宜的水、电、通讯和交通条件,供现场技术人员使用的工作房间,现场工作人员使用的休息房间和储存不宜露天放置的工具、仪器及重要设备零件的存放房间。
c.检测轨道基础在长度方向上任意10m内水平高度误差不得大于±
5mm,地脚孔距的偏差不得大于±
5mm,10个地脚孔的间距累积偏差不得大于±
20mm.
7.2安装顺序
7.2.1堆料机
a.安装轨道系统
b.安装行走机构
c.安装堆料臂架
d.安装来料车
e.安装液压变幅系统
f.安装配重块
g.安装其它零部件
7.2.2取料机
a.安装轨道系统
b.安装行走端梁及机架平台
c.安装刮板取料系统
d.安装卷扬提升系统
e.安装配重块
f.安装其他零部件
7.3轨道系统的安装
轨道系统安装前必须对钢轨进行检查,如有因运输、装卸造成弯曲、变形损坏现象,需经重新校正调直后方可按轨道系统图安装。
在铺设轨道前,根据轨道系统图纸预埋轨道地脚螺栓;
用枕板将轨道垫高,将垫板,压板,地脚螺栓安放整齐,安装固定部件(如螺母,垫圈,压板等,预留调整空间),铺好轨道,检查是否与图纸的要求一致,如有不符,则进行调整,之后固定地脚螺栓,并进行第一次灌浆,灌浆后,使之达到使用要求。
压板