无侧隙双滚柱包络环面蜗杆传动的研究论文Word下载.docx
《无侧隙双滚柱包络环面蜗杆传动的研究论文Word下载.docx》由会员分享,可在线阅读,更多相关《无侧隙双滚柱包络环面蜗杆传动的研究论文Word下载.docx(26页珍藏版)》请在冰豆网上搜索。
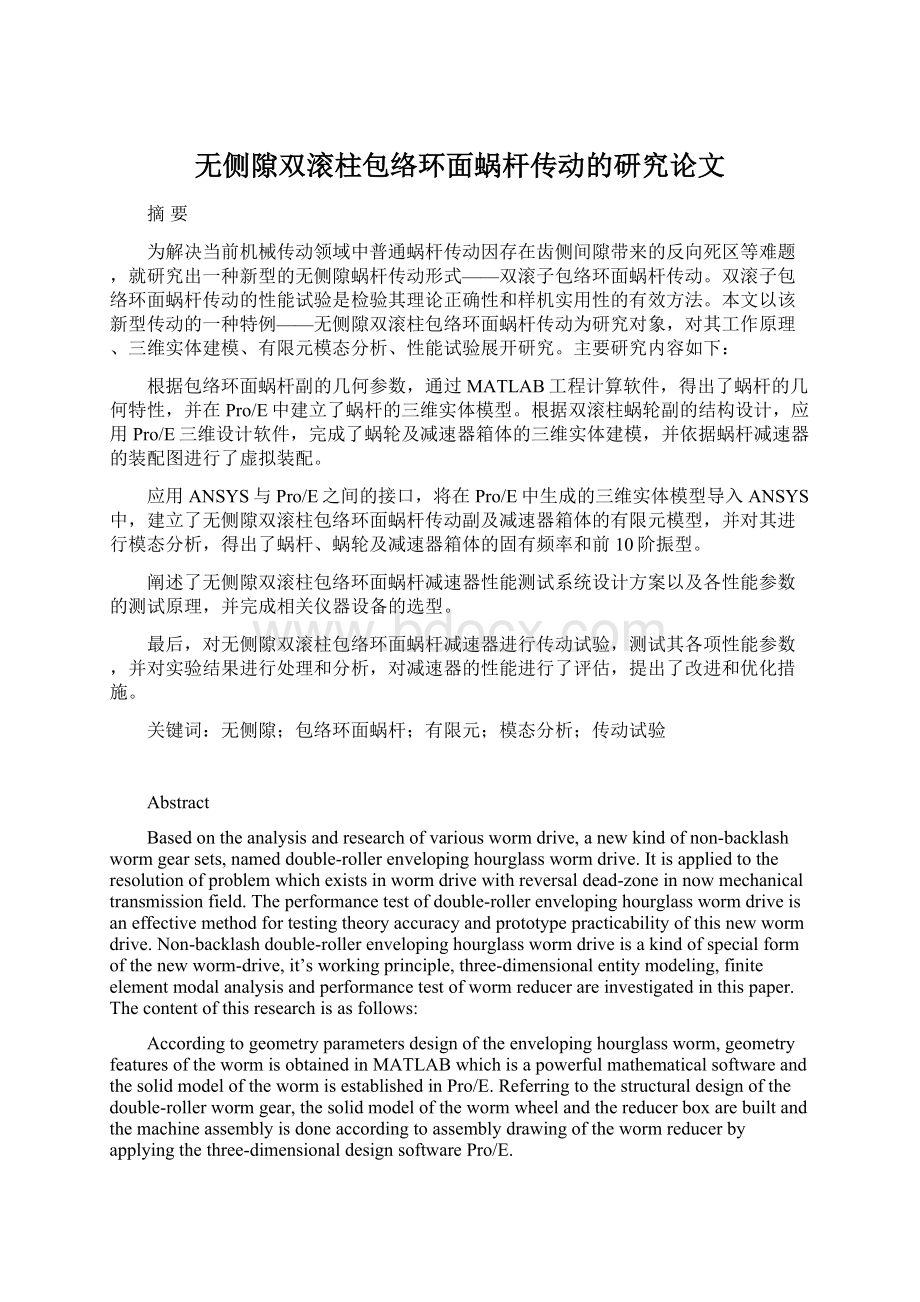
EnvelopingHourglassWorm;
FiniteElement;
ModalAnalysis;
TransmissionTest
目录
摘要1
Abstract2
1绪论4
1.1课题研究背景及意义5
1.2蜗杆传动的研究历史及发展趋势5
2无侧隙双滚柱包络环面蜗杆减速器三维实体模型的建立7
2.1蜗杆副的工作原理及蜗轮的组成结构7
2.2包络环面蜗杆三维实体模型的建立9
2.4无侧隙双滚柱包络环面蜗杆减速器整机三维实体模型的建立11
3无侧隙双滚柱包络环面蜗杆减速器性能测试系统方案设计13
3.1减速器性能测试系统的组成14
3.2主要测试内容及测试原理15
3.2.1传动效率测试15
3.2.2温度测试16
3.2.3振动测试17
3.2.4噪声测试19
4.各种实验仪器设备及其技术参数19
4.1试验台转速控制设备19
4.2传动效率测试设备19
5无侧隙双滚柱包络环面蜗杆减速器的传动试验22
5.1传动试验台的建立22
5.1.1设备仪器的检验23
5.1.2蜗杆减速器性能测试试验台的搭建23
5.2实验数据的采集44
5.2.1减速器传动试验内容及要求24
5.2.2减速器性能测试项目及结24
参考文献29
1.绪论
1.1课题研究背景及意义
本课题为国家自然科学基金项目“无侧隙双滚子包络环面蜗杆传动的研究”(编号:
50775190)的一部分。
蜗杆传动是在空间交错的两轴间传递运动和动力的一种传动形式[1],属于齿轮传动的范畴,它具有传动比大,冲击载荷小,传动平稳,结构紧凑等特点,广泛应用于冶金、化工、矿山、建筑、运输等行业的机械设备中。
随着生产力和工业技术的不断发展,各种机械设备对蜗杆传动的精度和稳定性提出了越来越高的要求,这将促使人们对蜗杆传动做更深入的研究。
在普通蜗杆传动中,适当的侧隙是蜗杆传动正常工作的必要条件之一[2].该侧隙可以避免因齿面摩擦生热而膨胀和受力变形所导致的挤压或卡死现象;
可以在一定程度上补偿制造和装配过程中产生的误差;
可以提供储藏润滑油的空间,减少齿面磨损等。
然而,由于侧隙的存在,给一些机电系统带来一定的冲击、振动和噪声,降低了系统的控制精度和稳定性。
因此,一方面为了提高蜗杆传动的精度,齿侧间隙越小越好,最好为零;
另一方面为了提高蜗杆传动的承载能力,齿侧间隙又宜大。
那么,在既要求传动精度高,又要求承载能力大的场合,这对矛盾更加突出。
因此,研究开发一种能同时满足高精度、重载荷要求的无侧隙蜗杆传动机构具有重要的工程意义。
1.2蜗杆传动的研究历史及发展趋势加
人们对蜗杆传动的研究有着很长的历史,早在两千多年前,阿基米德(Archimedes)就提出了利用螺旋线推动齿轮旋转的方法。
后来意大利的达·
芬奇(DaVinici)又提出了环面蜗杆传动的概念。
1765年,英国人Hindley首次提出并成功制造出第一对环面蜗杆传动副。
然而,蜗杆传动得以快速发展是开始于上世纪的二十年代。
1922年,美国人Wildharber研究成功一种直平面单包络环面蜗杆传动,主要用于精密分度装置,并且该传动只适用于大传动比的场合。
五十年代初,日本人佐藤申一和日本植田公司合作发明了一种斜齿平面单包络蜗杆传动[3],该传动主要用于重载传动装置,并且它使传动装置由大传动比扩展到中、小传动比。
二十世纪六十年代初,我国开始对平面蜗轮做深入的研究。
1971年,首钢机械厂在重庆大学的协助下制造出我国第一台直齿平面二次包络环面蜗杆减速器[4]。
随着人们对蜗杆传动的不断深入研究,截止目前,世界各国已提出了多种蜗杆传动形式。
但就无侧隙或齿侧间隙可补偿的蜗杆传动而言,国内外至今主要有三种传动形式:
(1)正平面一次包络环面蜗杆传动[5],又称直齿平面包络环面蜗杆传动。
这种传动的蜗轮是一个以直线为齿廓的正齿轮,齿面是与蜗轮轴线平行的正平面,蜗杆则是一包围着蜗轮的环面蜗杆,其齿面是以上述蜗轮齿平面作为母面,按蜗轮与蜗杆的啮合关系作展成运动所形成的包络面,属于平面包络环面蜗杆。
蜗轮齿两侧面的接触区域成反对称分布,故当将其沿齿面宽中央平面剖分制造时,通过相对转动两半个蜗轮,便可以达到调整齿侧间隙的目的,适用于精密分度蜗轮传动。
我国于二十世纪六十年代开始研究正平面一次包络环面蜗杆传动,并先后应用于河南豫西机床厂滚齿机分度蜗轮,首钢炼钢转炉倾翻机构和南京天文台望远镜等。
正平面一次包络环面蜗杆传动的优点是蜗杆与蜗轮同时啮合的齿数多,蜗杆齿面可以淬火和精确磨削;
蜗轮齿面为平面,齿廓为直线,容易加工制造。
该传动的缺点是:
当传动比小于30时,蜗杆入口端的齿面将产生根切,因而适用于传动比大于30的场合。
由于采用错齿消隙的结构,蜗轮齿分别与蜗杆左右齿面同时接触,而且相啮合齿面处于滑动摩擦状态,故齿面磨损严重,传动效率低。
由于蜗轮是通过轮毂上的键槽与轴上的键相联接的,为确保其中半个蜗轮相对另半个蜗轮错位转动,只能通过将蜗轮的键槽随错位加宽来实现,这不便于齿侧间隙的调整。
因此,该传动一直没有得到广泛应用。
(2)双导程蜗杆传动[6],又称“复合模数蜗杆传动”。
双导程蜗杆的成形原理与普通圆柱蜗杆相同,但蜗杆两侧齿面的模数不相等,相应两侧螺旋面的导程也不相等,从而产生导程差,这使蜗杆的齿厚沿其轴线方向发生变化;
然而,同一侧面的齿距是相等的,仍然满足啮合条件。
蜗轮是由相对应的复合模数蜗轮滚刀加工而成的。
通过调整蜗杆的轴向位置来调整齿侧间隙。
该传动已被应用于滚齿机等的精密分度机构中。
双导程蜗杆可以比较精确的调整齿侧间隙,根据以往试验,侧隙可调整至0.01~0.015mm,再小则容易发生卡死现象。
由于能满足正确的啮合条件,双导程蜗杆传动精度保持性好,传动比较稳定。
这种传动的缺点是:
变齿厚蜗杆的加工比较困难,而且,由于蜗轮是由复合模数蜗轮滚刀加工而成的,无法使用标准刀具,需要根据双导程蜗杆的参数来设计制造专用刀具,通用性差,成本高。
蜗杆蜗轮啮合同时接触的齿数少,且同时接触的各对齿的齿侧间隙不相等,只能保证一对齿的侧隙符合精度要求。
承载能力低,当载荷大、转速高时容易磨损。
精度低、寿命短,难以满足高速精密传动和重载精密传动的要求。
(3)侧隙可调式变齿厚平面包络环面蜗杆传动[7],亦称:
变齿厚平面蜗轮传动。
该传动是由重庆大学张光辉教授提出的,属于斜平面一次包络环面蜗杆传动。
在该传动中,蜗轮的啮合区域随齿平面的倾角改变而变化,当其它参数为已知,齿平面倾角小于一定值时,其瞬时接触线和相应的啮合区域假如落在轮齿齿面的左半部分的话,此时,当齿平面倾角大于一定值时,其瞬时的接触线及啮合区就落在轮齿齿面的右半部分。
现把一个轮齿两侧的平面倾角分别取为
和
,两侧的接触区都同时位于蜗轮齿的半边。
由于两个齿平面倾角不相等,使得轮齿成为一倾斜的楔形,即蜗轮齿在同一半径上的各端面齿厚都不相等,可将蜗轮副设计成首先接触于齿厚薄的半边,就可以通过调整蜗轮的轴向位置来获得合适的齿侧间隙。
除此之外,一些科技工作者还提出了许多采用辅助机构或装置来实现无侧隙传动的方法[8],并申请了一些无侧隙和齿侧间隙可调的齿轮传动机构的专利[9],例如“双蜗杆传动”、“双斜齿轮结构”和“直齿轮轮系结构”等,但这些传动装置都有传动元件多、体积大、结构复杂的缺点,很难适用于传动精度高、承载能力大、结构紧凑的伺服驱动系统的传动装置。
2无侧隙双滚柱包络环面蜗杆减速器三维实体模型的建立
双滚柱包络环面蜗杆传动是一种新型的无侧隙蜗杆传动形式,该传动副中蜗轮轮齿为两个能绕自身轴线转动的滚柱,并且沿蜗轮体轴线方向错开一定角度,使得滚柱与蜗杆齿面啮合时可以相对滚动。
而蜗杆则是以这两个滚柱面为原始母面包络形成的环面蜗杆,通过合理设置错开角度的大小,使滚柱与蜗杆齿面始终保持接触,从而实现无侧隙传动。
因此,无侧隙双滚柱包络环面蜗杆传动具有齿面磨损少,振动冲击小,传动效率高等优点[10][11]。
2.1蜗杆副的工作原理及蜗轮的组成结构
无侧隙双滚柱包络环面蜗杆副的工作原理如图2.1所示。
其中,蜗杆右侧齿面是由位于中间平面下方,偏距为
的滚柱侧面为工具母面包络而成,蜗杆左侧齿面是由位于中间平面上方,偏距为
的滚柱侧面为工具母面包络而成[12][13]。
双滚柱蜗轮的组成结构如图2.2所示。
该结构由两半个蜗轮组成,蜗轮轮齿为两个能绕自身轴线转动的滚柱,并且滚柱均匀分布在每半个蜗轮的圆周方向。
蜗轮轮齿采用双排滚柱错位布置,通过调节两半个蜗轮轮体的相对错位角度β,使得两排滚柱分别与蜗杆左右齿面同时并且始终保持接触,从而实现无侧隙传动。
就单排滚柱齿而言,工作过程中存在侧隙,保证了啮合运动的正常进行和良好润滑;
但对蜗轮整体而言,双排滚柱均与蜗杆齿面接触,消除了正反转运动的回程误差,使传动更加平稳,提高了传动精度[14]。
图2.1工作原理
图2.2蜗轮结构示意图
2.2包络环面蜗杆三维实体模型的建立
目前,构造实体模型的方法有网格分解法、实体实例法、构造实体几何法、扫描法和边界表示法。
其中,边界表示法是在表面模型的基础上通过定义形体的边界来描述实体,这为构建不规则复杂实体提供了可能。
本文采用边界表示法来生成蜗杆齿槽特征,在Pro/E中利用齿面上的变径螺旋线来生成齿根圆环面和左右两侧齿面[15][16]。
本文中双滚柱包络环面蜗杆传动的基本参数如表2.1所示:
表2.1蜗杆基本设计参数
参数
名称
滚柱
半径
中心距
滚子
偏距
蜗杆齿根
圆弧半径
蜗杆
头数
蜗轮
齿数
蜗杆齿顶
符号
R
A
类型
实数
初值
6.5mm
125mm
mm
106.8mm
1
32
94.2mm
(1)齿面的形成
要生成齿面特征,需要先将齿面上的变径螺旋线(基准曲线)绘制出来,然后通过边界混合命令,将线连成面。
在Pro/E中生成基准曲线有四种方法:
通过点、自文件、使用X截面和从方程[17]。
本文采用“自文件”生成基准曲线的方法来构建蜗杆齿面上的变径螺旋线。
根据包络环面蜗杆的齿面方程[11],应用Matlab软件编写程序,来得到蜗杆齿面上变径螺旋线的数据点坐标值,并将所得数据写成*.ibl文件[18]。
通过自文件命令将生成的数据文件导入Pro/E中,便可得到蜗杆齿面的螺旋线如图2.3所示[19][20]。
图2.3蜗杆齿面螺旋线
然后,通过边界混合命令即可得到蜗杆齿面,采用同样的方法,生成蜗杆的另一齿面,再利用两齿面根部的两条螺旋线生成蜗杆齿根圆环,最后使用“合并”命令即可得到蜗杆齿槽特征[21],如图2.4所示。
图2.4蜗杆齿槽特征
(2)蜗杆三维实体模型的建立
按以上步骤建立了蜗杆的齿槽特征后,就可以根据蜗杆的零件图建立蜗杆的齿坯模型,再通过实体化命令切出齿槽,最后建立好的蜗杆三维实体模型如图2.5所示。
图2.5蜗杆三维实体模型
2.3无侧隙双滚柱包络环面蜗杆减速器整机三维实体模型的建立
在Pro/E中建立好蜗杆减速器箱体、轴承端盖等相关零件的三维实体模型,根据蜗杆减速器的装配图选择合适的标准件,然后将所有零部件进行装配,装配过程中以蜗杆、蜗轮轴承端盖端面作为装配基准[22]。
所用到的标准件规格如表2.2所示,装配后的蜗杆减速器三维实体模型如图2.6所示。
表2.2减速器整机装配所用标准件
规格
数量
蜗杆轴承
7512E
2
螺栓
M18×
90-GB5786
4
蜗轮轴承
7310E
3
螺母
M18-GB6174
螺钉
60-GB5786
M12×
50-GB5783
垫圈
D18-GB955
M12-GB6174
D18-GB859
8
D12-GB859
M4×
16-GB29-2
M10×
30-GB5786
16
D10-GB859
M14×
50-GB5786
D14-GB955
D14-GB859
图2.6蜗杆减速器三维实体模型
3无侧隙双滚柱包络环面蜗杆减速器性能测试系统方案设计
无侧隙双滚柱包络环面蜗杆传动的性能试验是通过将蜗杆减速器置于机械传动试验台中进行传动试验,来测试蜗杆减速器的机械性能参数,主要参数为:
传动效率、温度、振动和噪声。
通过数据采集卡将各种采集信号进行A/D转换并传入计算机,由计算机软件对数据进行分析处理和结果显示,同时根据需要将测试结果进行存储和打印[23]。
因此,该传动试验主要包括传动效率测试、温度测试、振动测试和噪声测试。
该传动试验台为多功能数控试验台,主要包括:
电动机转速控制模块、磁粉加载器载荷控制模块、数据采集和分析模块。
其中,磁粉加载器加载,实验数据采集与分析均由一台计算机来实现集成控制[24][25]。
3.1减速器性能测试系统的组成
减速器性能测试系统的组成包括硬件系统和软件系统两大部分。
硬件系统主要包括电动机、机械传动装置、加载系统、检测装置和工作台,软件系统包括仪器驱动程序和数据处理软件[26]。
根据现有实验设备并结合实验要求和实验原理,制定的减速器性能测试系统技术方案如图3.1所示。
图3.1蜗杆减速器性能测试系统
机械传动装置包括待测减速器、陪试减速器及联轴器;
电动机是机械传动装置的动力源,为传动系统输入机械能;
联轴器连接电动机、待测减速器、转矩转速传感器和加载系统。
检测装置完成被测信号的采集、传输和测量结果的显示,主要包括各种传感器、信号调理装置、数据采集设备和计算机。
传感器是测量仪器与被测装置之间的接口,处于测量装置的输入端,它将被测量的温度、压力、位移等各种物理量转换成电量;
信号调理装置对电信号进行放大、滤波、隔离等预处理;
数据采集设备主要功能是将模拟信号转换成数字信号,此外一般还有放大、采样保持、多路复用等功能;
数据采集设备将数据传入计算机以后,由计算机软件对数据进行分析处理,并显示和存储实验结果[27]。
工作台是用来对机械传动装置和硬件测试系统进行定位和固定的,它应满足安全、合理、操作方便等要求。
软件测试系统是减速器性能测试系统的重要组成部分,它主要完成数据采集设备的驱动、数据分析处理以及显示、存储等功能[28]。
本文采用与效率仪、振动测量分析仪相配套的专用测试软件。
3.2主要测试内容及测试原理
3.2.1传动效率测试
轴传递的功率可按轴的角速度和作用于轴上的力矩求得,其公式如下:
P=Mω=
M=
M(3.1)
式(3.1)中,P为传动轴传递的功率,单位为KW;
M为作用于传动轴上的力矩,单位为N.m;
ω为轴的角速度,单位为rad/s;
n为轴的转速,单位为r/min。
传动效率η可表示为:
(3.2)
式(3.2)中,P0、Pi分别为传动轴上的输出和输入功率,M0、n0为输出转矩与转速,Mi、ni为输入转矩与转速,利用仪器测出减速器的输入转矩和输入转速以及输出转矩和输出转速,由式(3.2)可计算出减速器的传动效率η。
根据图3.1所示的蜗杆减速器性能测试系统技术方案,测出的传动效率为蜗杆减速器加两端联轴器的总效率,总效率可通过(3.3)式计算
(3.3)
式(3.3)中η2、η3为联轴器的传动效率,η被测为被测减速器的传动效率。
查机械设计手册得:
η2=η3=0.97[45]。
则被测减速器的传动效率为:
(3.4)
3.2.2温度测试
目前,测温系统主要分为两大类:
接触式测温系统和非接触式测温系统。
接触式测温系统要求传感器和被测对象充分接触,常见的有热电偶测温系统、热电阻测温系统、数字式测温系统以及膨胀式测温系统。
非接触式测温系统主要是指红外测温系统。
红外测温系统有其独特的优点:
通过接收被测物体辐射的红外线进行测温,可对那些难以接触到的或运动着的物体进行温度测量;
响应时间短,能快速地实现对回路的有效调节;
没有磨损的部件,不存在如使用温度计所存在的连续费用;
对于很小的被测物体,及腐蚀性的化学物或敏感表层的温度测试,使用红外测温系统可避免由于物体的导热性产生的测量误差;
通过远距离的遥控测量,可远离危险区域,保护操作人员[29]。
本文选用香港希玛SMARSENSOR公司生产的AR852B红外测温仪。
它由光学系统、探测单元、信号处理和数据显示四部分组成,其主要组成框图如图3.2所示。
图3.2红外测温系统主要组成框图
其中,光学系统主要包括瞄准系统、透镜和滤光片等,主要作用是收集被测目标的辐射功率,并使其会聚到探测器上。
探测器为红外探测器,作用是将接收到的红外辐射转换为电信号输出。
电信号处理部分的作用主要是对探测的微弱信号进行放大,以达到显示或记