大型塔类设备的制作安装.docx
《大型塔类设备的制作安装.docx》由会员分享,可在线阅读,更多相关《大型塔类设备的制作安装.docx(7页珍藏版)》请在冰豆网上搜索。
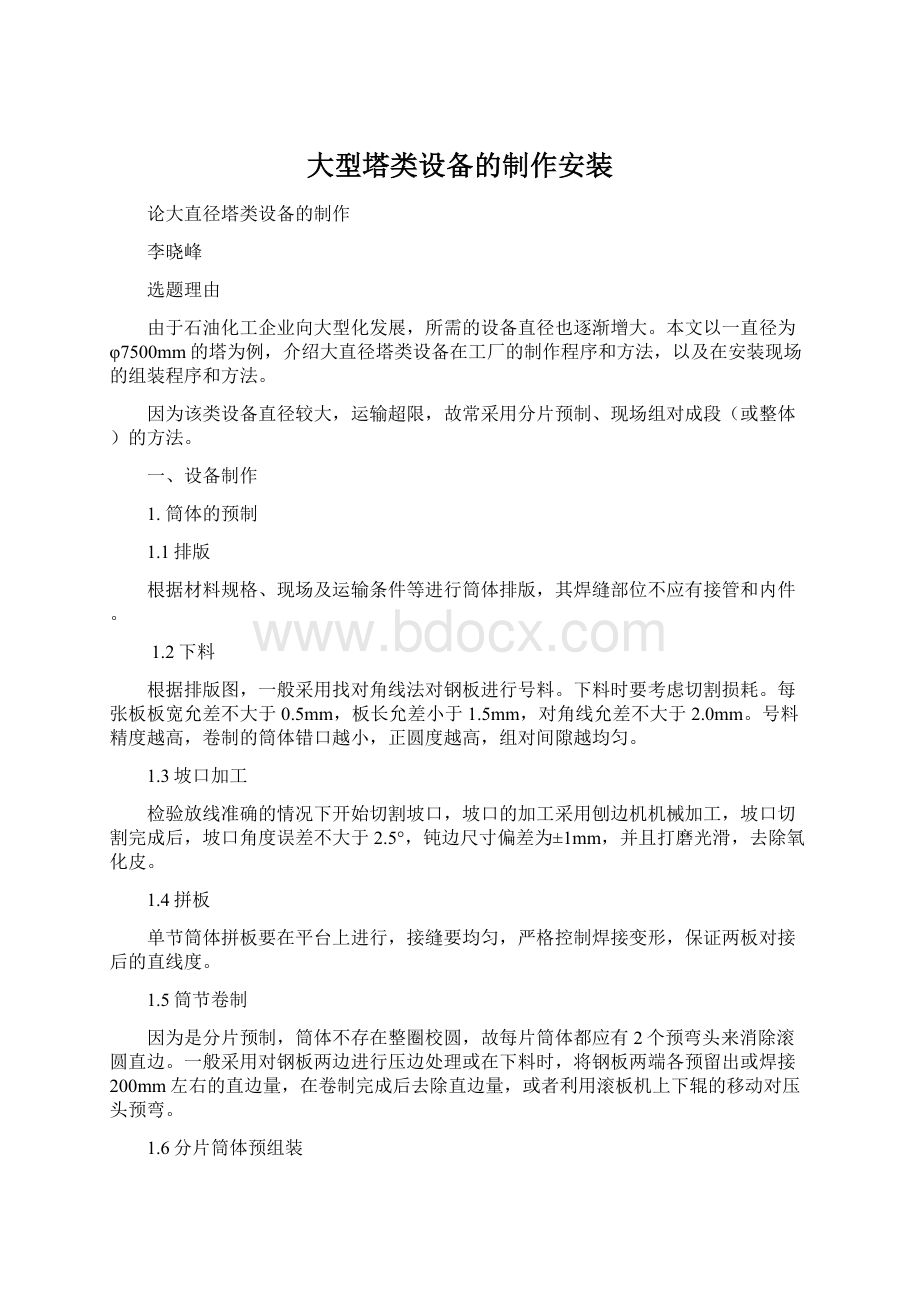
大型塔类设备的制作安装
论大直径塔类设备的制作
李晓峰
选题理由
由于石油化工企业向大型化发展,所需的设备直径也逐渐增大。
本文以一直径为φ7500mm的塔为例,介绍大直径塔类设备在工厂的制作程序和方法,以及在安装现场的组装程序和方法。
因为该类设备直径较大,运输超限,故常采用分片预制、现场组对成段(或整体)的方法。
一、设备制作
1.筒体的预制
1.1排版
根据材料规格、现场及运输条件等进行筒体排版,其焊缝部位不应有接管和内件。
1.2下料
根据排版图,一般采用找对角线法对钢板进行号料。
下料时要考虑切割损耗。
每张板板宽允差不大于0.5mm,板长允差小于1.5mm,对角线允差不大于2.0mm。
号料精度越高,卷制的筒体错口越小,正圆度越高,组对间隙越均匀。
1.3坡口加工
检验放线准确的情况下开始切割坡口,坡口的加工采用刨边机机械加工,坡口切割完成后,坡口角度误差不大于2.5°,钝边尺寸偏差为±1mm,并且打磨光滑,去除氧化皮。
1.4拼板
单节筒体拼板要在平台上进行,接缝要均匀,严格控制焊接变形,保证两板对接后的直线度。
1.5筒节卷制
因为是分片预制,筒体不存在整圈校圆,故每片筒体都应有2个预弯头来消除滚圆直边。
一般采用对钢板两边进行压边处理或在下料时,将钢板两端各预留出或焊接200mm左右的直边量,在卷制完成后去除直边量,或者利用滚板机上下辊的移动对压头预弯。
1.6分片筒体预组装
如分片筒体的下料、刨边全过程的质量控制能得到保证,可不用做预组装。
对于用户或图样有要求、或对上道工序有怀疑的,应进行筒体预组装。
2.封头和翻边过渡的预制
2.1分片数量的确定
根据压力机操作空间矫形的难易,及制作胎具的成本来确定,等分越多,越易成形,但焊缝越多。
2.2分片封头的冲压
将封头分片冲压上下胎具安装在压力机上,将加热的分片封头板放入上下胎具中间进行冲压。
2.3分片封头的切割和预组装
对压制好的瓜瓣进行检查,间隙应小于2mm,不合格的瓜瓣应重新矫形。
将切割好的每个瓜瓣按图样进行预组装,将预组装好的每个瓜瓣按顺时针方向连续编号序号,并在排版图上做好标记。
二、大型塔类设备现场组装工艺流程示意图
1.裙座组焊
裙座基础环预制时,按照图纸尺寸,在组对平台上划出基准圆,基准圆直径D=L+n·G/π
其中:
L到货基础环累加周长
n为等分数
G为对口间隙,一般取2mm。
在基准圆内外侧,点焊定位板,然后进行组焊。
待裙座基础环焊接完毕后,将裙座筒体板采用25t吊车吊运至基础环上部组对成型,裙座筒体板焊接成型后再与基础环板进行组焊,然后安装裙座立筋板与盖板。
裙座具体组焊流程如下:
图4.4裙座组焊流程示意图
裙座组对时应注意以下几点:
1)分片到货的基础环组焊后平面度不允许超过为3mm;接口处地脚螺栓孔中心距允许偏差为±2mm;地脚螺栓孔中心圆直径允许偏差为±2mm。
2)基础环、裙座与设备本体轴线允许偏差为5mm。
3)裙座与设备本体相接处,如遇到拼接焊缝时,应在裙座上开出豁口。
1.1锥形封头组焊
封头瓜片板到货后,认真进行验板工作,在符合标准要求的平台上放样划基准圆,在基准圆内,设置组装胎具,用吊车配合将封头瓜片板按排版图顺序安装。
封头组装在钢平台上按下述程序组装:
在钢平台上划出组装基准圆,封头基准圆直径DB可按下式确定:
DB=L+n·G/π
其中:
L为到货基础环累加周长
n为等分数
G为对口间隙,一般取2mm。
将基准圆按照封头的分瓣数n等分,在距等分线约200mm处点焊定位板,每个瓣片的定位板不少于二块。
如下图:
图4.5封头定位板位置示意图
以定位板和组装胎具为基准,用工卡具使瓣片紧靠定位板和胎具,并调整对口间隙和错边量。
封头瓣片在钢平台上组对焊接成封头后,应对每道缝按照附表1中的要求进行检测,并做好记录,最终检测结果应符合规范要求。
封头全部组对完毕,经检验符合要求并做好记录后,可根据封头对缝的长度和板厚情况,每条纵缝上可适当加2~3个防变形弧板(详见附图2)以减小焊接变形。
组焊合格后,按排板图定出0°、90°、180°、270°四条方位母线并做上标记。
2.筒体组装
2.1单节筒体组对
1)单节筒体组对前,根据每圈板片数、封头端部实际周长及焊接收缩量在钢平台上划出筒体基准圆,在基准圆内侧每隔1000~1500mm焊一块定位板。
2)按照排版图编号将同一圈的板片吊至基准圆处,利用工装卡具组对成整圈筒体,并进行检查。
检查结果应符合下列要求:
①对口错边量不大于3mm。
②纵缝棱角E用弦长等于1/6设计直径且不小于300mm的样板检查,其间隙值应不大于δs/10+2mm且不大于5mm。
③圆度e应小于等于25mm(直径为7500mm)、22mm(直径为4250mm)
④相邻两筒节外圆周长允许偏差值为±18mm(直径为4200mm~6000mm)、±24mm(直径为大于7600mm)。
⑤筒体直线度应满足表4.2的要求。
表4.2筒体直线度允许偏差值(单位:
mm)
检查项目
允许偏差值
任意3000
3
全长
H≤15000
H/1000
H>15000
0.5H/1000+8
3)检查合格后,在纵缝的内侧点焊防变形弧板。
4)筒节纵缝焊接后几何尺寸应满足2.4.1条中第二条要求。
5)单节筒体焊接后,标出方位线(0°、90°、180°、270°),进行号孔划线。
筒节内用“米”字型支撑固定。
图4.6筒节“米”字形加固图
2.2筒体组焊
1)采用正装法进行筒体组对,在组对口下方1.5m处搭设临时操作平台,以满足组对及焊接需要。
2)组对时,在上口外侧每隔约1000mm焊一块定位板,再将上面一圈筒节吊放上去,上、下两圈筒节的四条方位母线必须对正,其偏差不得大于5mm。
3)用卡具调整间隙、错边量,组对完成后应满足下列要求:
①筒体环缝对口错边量应符合以下规定:
表4.3环缝对口错边量(单位:
mm)
对口处钢材厚度δ
B类焊缝对口错边量b
δ=20~40
≤5
②组对后形成的棱角度E,用长度不小于300mm的直尺检查,其间隙值应不大于δs/10+2mm且不大于5mm。
③相邻筒节A类接头焊缝应相互错开,距离应大于钢板厚度的3倍,且不小于100mm。
④筒体分段组焊后,应按照排版图上的方位在各段内外壁校准相隔90°的四条方位母线。
4)分段组焊后,应满足下列要求:
吊装段形成后,检查对应筒节的周长及圆度且在误差范围内。
2.3接管安装
2.3.1人孔、接管应按设计文件规定,以壳体上的四条方位线和基准圆为基准划线开孔并进行组焊。
2.3.2接管与设备壳体相对位置见图4.7。
图中各种相交或交叉形式的接管均应先放样并做出样板;其安装角度也应做出样板,且样板靠接管一边的长度应不小于100mm。
a)接管中心线与设备轴线垂直相交b)接管中心线与设备轴线不垂直相交
c)接管中心线与设备轴线垂直交叉d)接管中心线与设备轴线不垂直交叉
图4.7接管与设备壳体相对示意图(1——接管;2——壳体)
2.3.3接管的法兰面应垂直于接管中心线,其允许偏差见下表。
序号
检验项目
允许偏差值
1
接管法兰面至设备外壁距离
±2.5
2
设备开口中心标高及周向位置
接管
±5
人孔
±10
液位计接口
±3
3
与设备不垂直的开孔接管的安装角度
安装角度样板长度的1/100
4
与外部管道连接的法兰面垂直度或平行度
法兰DN≤200
1.5
法兰DN>200
2.5
5
液位计对应接口之间的距离
±1.5
6
液位计对应接口周向位置
1.5
7
液位计对应接管外伸长度差
1.5
8
液位计法兰面垂直度
0.5D0%
注:
检查与设备不垂直的开孔接管安装角度的偏差是测量接管与安装角度样板之间间隙,D0为法兰外径
表4.4设备接管等允许偏差值(单位:
mm)
2.3.4直接焊接于筒体上的法兰应垂直于筒体中心轴线,其允许偏差为法兰外径的1%,且不大于3mm。
2.3.5接管法兰螺栓孔应与壳体中心轴线跨中布置,见下图4.8。
图4.8法兰跨中示意图
2.3.6人孔和接管组合件与壳体组装时,应先将补强圈套入接管,接管与壳体焊接后再组装补强圈;补强圈应紧贴于壳体上;补强圈影响接管焊接时,可将补强圈预制成2~3片,在接管焊接检查合格后组对焊接补强圈;开孔补强圈与壳体变截面交界处的焊接接头相碰时,可割除部分补强圈,保留补强圈的宽度应不小于设计文件规定宽度的2/3。
2.3.7补强圈、支座、垫板等覆盖的焊接接头余高应磨平。
2.3.8补强圈应设信号孔,信号孔宜位于补强圈下部,且为M10螺孔;多片组成的补强圈,每片上均应设信号孔。
2.3.9补强圈焊接后应经0.4MPa~0.5MPa气压试验,并涂刷中性发泡剂进行焊接接头质量检查,无渗漏为合格。
2.4内构件的安装
塔内固定件组焊一般分为划线及固定件组焊两个步骤。
固定件安装划线以基准圆为依据,在塔壁上划出每层塔盘固定件的位置。
塔内其他固定件按图所示的位置进行划线。
塔内除塔盘支撑以外的固定件在对划线进行检查核对正确后,按图样进行组装。
塔盘支撑固定件在对其划线的准确性进行检查后,按照受液盘——支持圈——降液板的顺序进行组装和焊接。
焊接过程应采取措施防止焊接变形。
焊接前要检查安装尺寸位置正确。
三、设备压力试验
设备安装完成后,根据技术要求,采用水压、气压试验,检验是否渗漏。