3D打印耗材总体分为几类Word格式文档下载.docx
《3D打印耗材总体分为几类Word格式文档下载.docx》由会员分享,可在线阅读,更多相关《3D打印耗材总体分为几类Word格式文档下载.docx(15页珍藏版)》请在冰豆网上搜索。
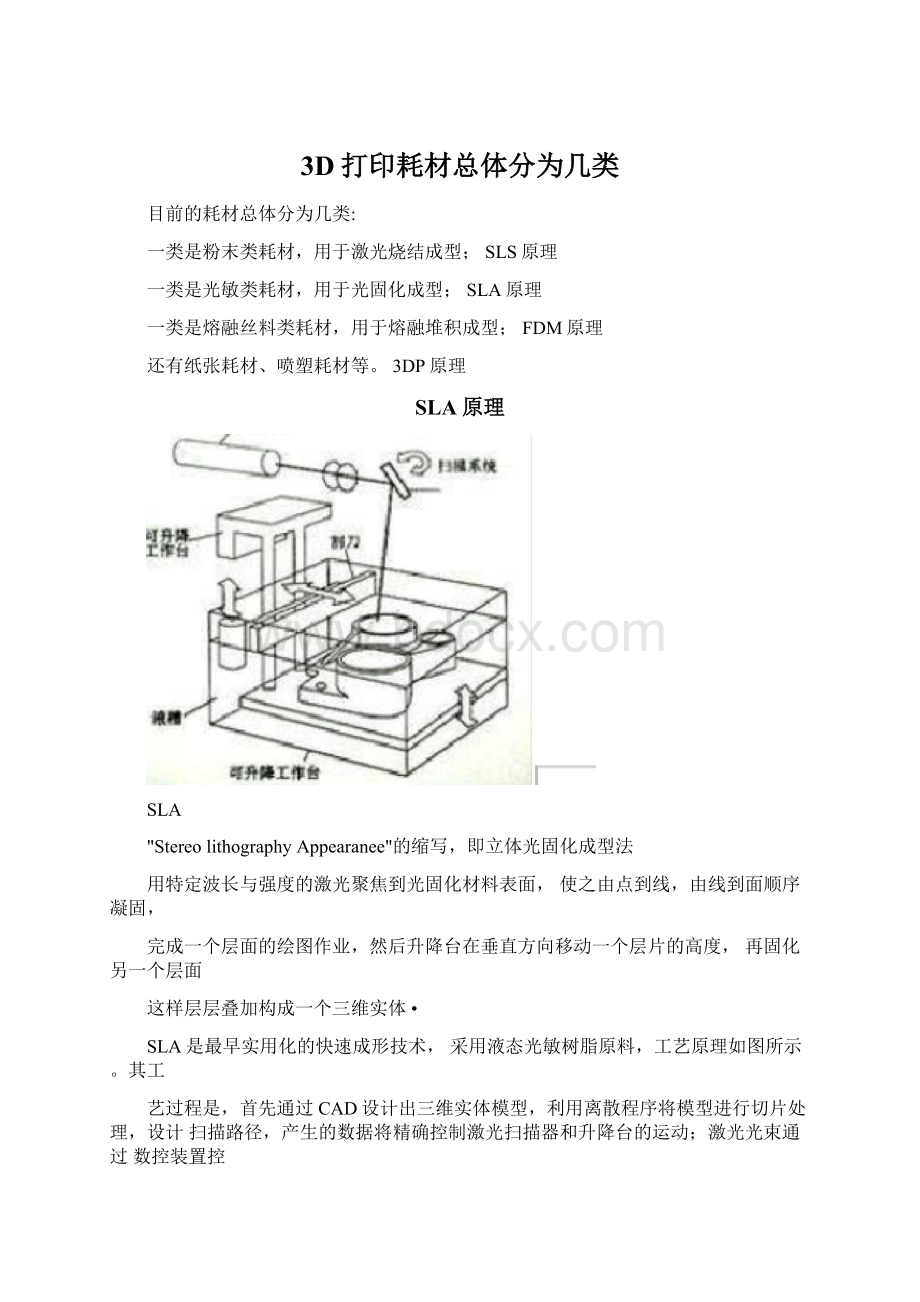
程中产生收缩,不可避免地会产生应力或引起形变。
因此开发收缩小、固化快、强度高的光
敏材料是其发展趋势。
3DSystems推出的ViperProSLAsystem
SLA的优势
1.光固化成型法是最早出现的快速原型制造工艺,成熟度高,经过时间的检验•
2.由CAD数字模型直接制成原型,加工速度快,产品生产周期短,无需切削工具与模具
/、■
3•可以加工结构外形复杂或使用传统手段难于成型的原型和模具
4.使CAD数字模型直观化,降低错误修复的成本•
5.为实验提供试样,可以对计算机仿真计算的结果进行验证与校核
6.可联机操作,可远程控制,利于生产的自动化•
SLA的缺憾
1SLA系统造价高昂,使用和维护成本过高•
2SLA系统是要对液体进行操作的精密设备,对工作环境要求苛刻.
3成型件多为树脂类,强度,刚度,耐热性有限,不利于长时间保存
4预处理软件与驱动软件运算量大,与加工效果关联性太高
5软件系统操作复杂,入门困难;
使用的文件格式不为广大设计人员熟悉
6立体光固化成型技术被单一公司所垄断•
SLA的发展趋势与前景
立体光固化成型法的的发展趋势是高速化,节能环保与微型化•
不断提高的加工精度使之有最先可能在生物,医药,微电子等领域大有作为
SLS原理
选择性激光烧结(以下简称SLS技术最初是由美国德克萨斯大学奥斯汀分校的Carl
ckard于1989年在其硕士论文中提出的。
后美国DTM公司于1992年推出了该工艺的商业化生产设备SinterSation。
几十年来,奥斯汀分校和DTM公司在SLS领域做了大量的研究工作,在设备研制和工艺、材料开发上取得了丰硕成果。
德国的EOS公司在这一领域也做了很多
研究工作,并开发了相应的系列成型设备。
国内也有多家单位进行SLS的相关研究工作,如西安交通大学机械学院,快速成型国
家工程研究中心,教育部快速成型工程研究中心,华中科技大学、南京航空航天大学、西北
工业大学、中北大学和北京隆源自动成型有限公司等,也取得了许多重大成果,如南京航空
航天大学研制的RAP-1型激光烧结快速成型系统、北京隆源自动成型有限公司开发的AFS—300激光快速成型的商品化设备。
选择性激光烧结是采用激光有选择地分层烧结固体粉末,并使烧结成型的固化层层层叠加生成所需形状的零件。
其整个工艺过程包括CAD模型的建立及数据处理、铺粉、烧结
以及后处理等。
SLS技术的快速成型系统工作原理见图1。
整个工艺装置由粉末缸和成型缸组成,工作时粉末缸活塞(送粉活塞)上升,由铺粉
辊将粉末在成型缸活塞(工作活塞)上均匀铺上一层,计算机根据原型的切片模型控制激光束的二维扫描轨迹,有选择地烧结固体粉末材料以形成零件的一个层面。
粉末完成一层后,工作活塞下降一个层厚,铺粉系统铺上新粉•控制激光束再扫描烧结新层。
如此循环往复,
层层叠加,直到三维零件成型。
最后,将未烧结的粉末回收到粉末缸中,并取出成型件。
对于金属粉末激光烧结,在烧结之前,整个工作台被加热至一定温度,可减少成型中的热变形,并利于层与层之间的结合。
与其它快速成型(RP)方法相比,SLS最突出的优点在于它所使用的成型材料十分广泛。
从理论上说,任何加热后能够形成原子间粘结的粉末材料都可以作为SLS的成型材料。
可成
功进行SLS成型加工的材料有石蜡、高分子、金属、陶瓷粉末和它们的复合粉末材料。
由于SLS成型材料品种多、用料节省、成型件性能分布广泛、适合多种用途以及SLS无需设计和
制造复杂的支撑系统,所以SLS的应用越来越广泛。
SLS技术的金属粉末烧结方法
3.1金属粉末和粘结剂混合烧结
首先将金属粉末和某种粘结剂按一定比例混合均匀,用激光束对混合粉末进行选择性
扫描,激光的作用使混合粉末中的粘结剂熔化并将金属粉末粘结在一起,形成金属零件的坯
体。
再将金属零件坯体进行适当的后处理,如进行二次烧结来进一步提高金属零件的强度和
其它力学性能。
这种工艺方法较为成熟,已经能够制造出金属零件,并在实际中得到使用。
南京航空航天大学用金属粉末作基体材料(铁粉),加人适量的枯结剂,烧结成形得到原型
件,然后进行后续处理,包括烧失粘结剂、高温焙烧、金属熔渗(如渗铜)等工序,最终制造出电火花加工电极(见图2)。
并用此电极在电火花机床上加工出三维模具型腔(见图3)。
3.2金属粉末激光烧结
激光直接烧结金属粉末制造零件工艺还不十分成熟,研究较多的是两种金属粉末混合烧结,其中一种熔点较低,另一种较高。
激光烧结将低熔点的粉末熔化,熔化的金属将高熔
点金属粉末粘结在一起。
由于烧结好的零件强度较低,需要经过后处理才能达到较高的强度。
美国Texas大学Austin分校进行了没有聚合物粘结剂的金属粉末如CuSnNiSn青铜镍粉复合
粉末的SLS成形研究,并成功地制造出金属零件。
他们对单一金属粉末激光烧结成形进行了研究,成功地制造了用于F1战斗机和AIM9导弹的工NCONEL625超合金和Ti6A14合金的金属零件。
美国航空材料公司已成功研究开发了先进的钦合金构件的激光快速成形技术。
中
国科学院金属所和西安交通大学等单位正致力于高熔点金属的激光快速成形研究,南京航空
航天大学也在这方面进行了研究,用Ni基合金混铜粉进行烧结成形的试验,成功地制造出
具有较大角度的倒锥形状的金属零件(见图4)。
3.3金属粉末压坯烧结
金属粉末压坯烧结是将高低熔点的两种金属粉末预压成薄片坯料,用适当的工艺参数
进行激光烧结,低熔点的金属熔化,流人到高熔点的颗粒孔隙之间,
重新排列,得到致密度很高的试样。
吉林大学郭作兴等用此方法对
验研究,发现压坯激光烧结具有与常规烧结完全不同的致密化现象,却方式而异,空冷得到细珠光体,淬火后得到马氏体和粒状。
4SLS技术金属粉末成型存在的问题
SLS技术是非常年轻的一个制造领域,在许多方面还不够完善,如制造的三维零件普遍
存在强度不高、精度较低及表面质量较差等问题。
SLS工艺过程中涉及到很多参数(如材料
的物理与化学性质、激光参数和烧结工艺参数等),这些参数影响着烧结过程、成型精度和
质量。
零件在成型过程中,由于各种材料因素、工艺因素等的影响,会使烧结件产生各种冶金缺陷(如裂纹、变形、气孔、组织不均匀等)。
4.1粉末材料的影响
粉末材料的物理特性,如粉末粒度、密度、热膨胀系数以及流动性等对零件中缺陷形
成具有重要的影响。
粉末粒度和密度不仅影响成型件中缺陷的形成,还对成型件的精度和粗
糙度有着显著的影响。
粉末的膨胀和凝固机制对烧结过程的影响可导致成型件孔隙增加和抗拉强度降低。
4.2工艺参数的影响
激光和烧结工艺参数,如激光功率、扫描速度和方向及间距、烧结温度、烧结时间以
及层厚度等对层与层之间的粘接、烧结体的收缩变形、翘曲变形甚至开裂都会产生影响。
上
述各种参数在成型过程中往往是相互影响的,如YongAkSong等研究表明降低扫描速度和扫
描间距或增大激光功率可减小表面粗糙度,但扫描间距的减小会导致翘曲趋向增大。
因此,在进行最优化设计时就需要从总体上考虑各参数的优化,以得到对成型件质量的改善最为有效的参数组。
制造出来的零件普遍存在着致密度、强度及精度较低、机械性能
和热学性能不能满足使用要求等一些问题。
这些成型件不能作为功能性零件直接使用,需要
进行后处理(如热等静压HIP、液相烧结LPS高温烧结及熔浸)后才能投人实际使用。
此外,还需注意的是,由于金属粉末的SLS温度较高,为了防止金属粉末氧化,烧结时必须将
金属粉末封闭在充有保护气体的容器中。
5总结与展望
快速成型技术中,金属粉末SLS技术是人们研究的一个热点。
实现使用高熔点金属直接烧结成型零件,对用传统切削加工方法难以制造出高强度零件,对快速成型技术更广泛的
应用具有特别重要的意义。
展望未来,SLS形技术在金属材料领域中研究方向应该是单元体
系金属零件烧结成型,多元合金材料零件的烧结成型,先进金属材料如金属纳米材料,非晶
态金属合金等的激光烧结成型等,尤其适合于硬质合金材料微型元件的成型。
此外,根据零
件的具体功能及经济要求来烧结形成具有功能梯度和结构梯度的零件。
我们相信,随着人们
对激光烧结金属粉末成型机理的掌握,对各种金属材料最佳烧结参数的获得,以及专用的快
速成型材料的出现,SLS技术的研究和引用必将进入一个新的境界。
LOM原理
LOM
分层实体制造(LOMLaminatedObjectManufacturing)法,LOM又称层叠法成形,
它以片材(如纸片、塑料薄膜或复合材料)为原材料,其成形原理如图所示,激光切割系统按照计算机提取的横截面轮廓线数据,将背面涂有热熔胶的纸用激光切割出工件的内外轮廓。
切割完一层后,送料机构将新的一层纸叠加上去,利用热粘压装置将已切割层粘合在一起,然后再进行切割,这样一层层地切割、粘合,最终成为三维工件。
LOM常用材料是纸、金
属箔、塑料膜、陶瓷膜等,此方法除了可以制造模具、模型外,还可以直接制造结构件或功能件。
该方法的特点是原材料价格便宜、成本低。
成形材料:
涂敷有热敏胶的纤维纸;
制件性能:
相当于高级木材;
主要用途:
快速制造新产品样件、模型或铸造用木模。
FDM原理
FDM
熔积成型(FDMFusedDepositionModeling)法,该方法使用丝状材料(石蜡、金
属、塑料、低熔点合金丝)为原料,利用电加热方式将丝材加热至略高于熔化温度(约比熔点高1C),在计算机的控制下,喷头作x-y平面运动,将熔融的材料涂覆在工作台上,冷却后形成工件的一层截面,一层成形后,喷头上移一层高度,进行下一层涂覆,这样逐层堆
积形成三维工件。
该方法污染小,材料可以回收,用于中、小型工件的成形。
下图为FDM
成形原理图。
固体丝状工程塑料;
制件性能:
相当于工程塑料或蜡模;
主要用途:
塑料件、铸造用蜡模、样件或模型。
特点:
1、优点:
(1)操作环境干净,安全,在办公室课进行;
(2)工艺干净、简单、
易于操作且不产生垃圾;
(3)尺寸精度高,表面质量好,易于装配,可快速构建瓶状或中空零件;
(4)原材料以卷轴丝的形式提供,易于搬运和金额快速更换;
(5)原料价格便宜;
(6)
材料利用率高;
(7)可选用的材料较多,如染色的ABS和医用ABD、PC、PPSF人造橡胶、
铸造用蜡。
2、缺点:
(1)精度较低,难以构建结构复杂的零件;
(2)与截面垂直方向的强度小;
(3)成型速度相对较慢,不适合构建大型零。
3意义方向
意义
大大缩短新产品研制周期,确保新产品上市时间;
------使模型或模具的制造时间缩短数倍甚至数十倍;
提高了制造复杂零件的能力;
------使复杂模型的直接制造成为可能;
显著提高新产品投产的一次成功率;
------可以及时发现产品设计的错误,做到早找错、早更改,避免更改后续工序所造成的大量损失;
支持同步(并行)工程的实施;
------使设计、交流和评估更加形象化,使新产品设计、样品制造、市场定货、生产准备、等工作能并行进行;
支持技术创新、改进产品外观设计;
------有利于优化产品设计,这对工业外观设计尤为重要。
成倍降低新产品研发成本;
------节省了大量的开模费用
快速模具制造可迅速实现单件及小批量生产。
使新产品上市时间大大提前,迅速占领市场。
总而言之,RP技术是九十年代世界先进制造技术和新产品研发手段。
在工业发达国家,企业在新产品研发过程中采用RP技术确保研发周期、提高设计质量已成为一项重要的策略。
当前,市场竞争愈演愈烈,产品更新换代加速。
要保持我市产品在国内外市场的竞争力,迫切需要在加大新产品开发投入力度、增强创新意识的同时,积极采用先进的创新手段。
RP
技术在不需要任何刀具、模具及工装卡具的情况下,可实现任意复杂形状的新产品样件的快速制造。
用RP技术快速制造出的的模型或样件可直接用于新产品设计验证、功能验证、外观验证、工程分析、市场订货等,非常有利于优化产品设计,从而大大提高新产品开发的一
次成功率,提高产品的市场竞争力,缩短研发周期,降低研发成本。
快速原型制造技术生产
力促进中心的成立为本市企业应用RP技术开展产品创新活动提供了很好的前提条件。
发展方向
RP技术已经在许多领域里得到了应用,其应用范围主要在设计检验、市场预测、工程测试(应力分析、风道等)、装配测试、模具制造、医学、美学等方面。
RP技术在制造工业
中应用最多(达到67%),说明RP技术对改善产品的设计和制造水平具有巨大的作用。
快速成形技术还存在许多不足,下一步研究开发工作主要在以下几方面:
⑴改善快速成形系统的可靠性、生产率和制作大件能力,尤其是提高快速成形系统的制作精度;
⑵开发经济型的快速成形系统;
⑶快速成形方法和工艺的改进和创新;
⑷快速模具制造的应用;
⑸开发性能良好的快速成形材料;
⑹开发快速成形的高性能软件等。
技术特点
1制造快速
RP技术是并行工程中进行复杂原型或者零件制造的有效手段,能使产品设计和模具生
产同步进行,从而提高企业研发效率,缩短产品设计周期,极大的降低了新品开发的成本及
风险,对于外形尺寸较小,异形的产品尤其适用。
2CAD/CAM技术的集成
设计制造一体化一直来说是一个难点,计算机辅助工艺(CAPP在现阶段由于还无法
与CADCAM完全的无缝对接,这也是制约制造业信息化一直以来的难点之一,而快速成型技术集成CAD、CAM、激光技术、数控技术、化工、材料工程等多项技术,使得设计制造一体化的概念完美实现。
3完全再现三维数据
经过快速成型制造完成的零部件,完全真实的再现三维造型,无论外表面的异形曲面还是内腔的异形孔,都可以真实准确的完成造型,基本上不再需要再借助外部设备进行修复。
4成型材料种类繁多
各类RP设备上所使用的材料种类有很多,树脂、尼龙、塑料、石蜡、纸以及金属或陶瓷的粉末,基本上满足了绝大多数产品对材料的机械性能需求。
5创造显著的经济效益
与传统机械加工方式比较,开发成本上节约10倍以上,同样,快速成型技术缩短了企
业的产品开发周期,使的在新品开发过程中出现反复修改设计方案的问题大大减少,也基本
上消除了修改模具的问题,创造的经济效益是显而易见的。
6应用行业领域广
RP技术经过这些年的发展,技术上已基本上形成了一套体系,同样,可应用的行业也逐渐扩大,从产品设计到模具设计与制造,材料工程、医学研究、文化艺术、建筑工程等等都逐渐的使用RP技术,使得RP技术有着广阔的前景。
发展动力
在现代化工业生产中,60%〜90%的工业产品需要使用模具加工,模具工业已经成为制造业中的一项基础工业,是技术成果转化的手段,同时又是高新技术产业的重要领域,在欧
美等工业发达国家被成为点铁成金”的磁力工业”。
可见,模具工业在世界各国经济发展中具有重要的显著地位。
西安交通大学机械学院,快速制造国家工程研究中心,教育部快速制造工程研究中心,
总结当前制造业呈现如下发展趋势:
1、生产、经营及市场全球化;
2、用户需求个性化、多样化;
3、产品生命周期短,更新换代加速;
4、产品技术高科技化;
5、市场竞争激烈化。
数据统计
据统计,我国新产品的平均开发周期为18个月,产品的生命周期为10.5年。
而美国
1990年已实现“个3”,即产品的生命周期为3年,产品的试制周期为3个月,产品的设计周期为3周。
因此,制造企业要想在21世纪求得生存和发展,就必须面对这一新的形势,不断研究或引进新的技术。
过去,传统的零件成型方法是采用多种机械加工机床,以及刀具和模具,还要有高水
平的技工,成本高,制造周期往往长达几星期,甚至几个月,不能适应新产品的更新。
为克服上述问题,近几年来开发成功了快速成型制造技术和相应的快速成型机。
它是利用激光等
物理方法,向用户提供物理模型和快速修改设计方案,从而大大减少了新产品开发前期的时
间和费用。
快速成型技术广泛应用于航空航天、汽车、电子、通讯、医疗、建筑、家电、玩具、家具、日用五金及工艺品制作等众多领域。
快速成型技术使之在以下四方面受益:
设计者
在设计产品时,通常分为概念设计及详细设计。
由于设计者的能力有限,不可能在短
时间内,仅凭图纸上的思维,就把结构、形状及尺寸等问题考虑得很周全并使结果优化,不
但费时费力,往往难免有所疏漏,从而造成返工。
为解决上述问题,在现代制造技术领域中,提出了并行工程的方法,它以小组协同工作为基础,通过网络共享数据等信息资源,来同步
考虑产品设计、制造的有关技术问题,从而实现并行设计的思想。
然而,仅仅依靠计算机及
数字模拟,没有必要的物理模拟手段,也难于完美地进行并行设计。
快速模型采用快速成型技术之后,设计者在设计的最初阶段,就能拿到实在的产品样
品,并可在不同阶段快速地修改、重做样品,甚至做出试制用工模具及少量的产品,据此判
断有关的各种问题。
这给设计者创造了一个优良的设计环境,无需多次反复思考、修改,即
可尽快得到优化结果。
因此,快速成型技术是真正实现并行设计的强有力手段。
制造者
制造者在产品设计的最初阶段,也能拿到实在的产品样品、甚至试制用的工模具及少
量产品,这使得他们能及早地对产品设计提出意见,做好原材料、标准件、外协加工件、加
工工艺和批量生产用工模具等准备,最大限度地减少失误和返工,大大节省工时、降低加工
成本和提高产品质量。
推销者
推销者在产品设计的最初阶段,也可拿到产品样品、甚至少量产品,这使得他们能据
此及早、实在地向用户宣传,征求意见,并进行比较准确的市场需求预测,而不是仅凭抽象
的产品描述或一张图纸、一份样本来推销。
所以,快速成型技术的应用可以显著地降低新产品的销售风险和成本,大大缩短其投放市场的时间和提高竞争能力。
用户
用户在产品设计的最初阶段,也能见到产品样品,甚至少量产品,这使得他们及早、深刻地认识产品,进行必要的测试,并且提出有关的意见,从而可以在尽可能短的时间内,以合理的价格得到性能最符合要求的产品。
综上所述,快速成型技术必将能承担起21世纪制造业持续高速发展的重任,为现代制造业提供源源不断的超动力。
3DP工艺
3DP工艺与SLS工艺类似,米用粉末材料成形,如陶瓷粉末,金属粉末。
所不同的是
材料粉末不是通过烧结连接起来的,而是通过喷头用粘接剂(如硅胶)将零件的截面印刷.
在材料粉末上面。
用粘接剂粘接的零件强度较低,还须后处理。
具体工艺过程如下:
上一层
粘结完毕后,成型缸下降一个距离(等于层厚:
0.013〜0.1mm),供粉缸上升一高度,推出若干粉末,并被铺粉辊推到成型缸,铺平并被压实。
喷头在计算机控制下,按下一建造截面
的成形数据有选择地喷射粘结剂建造层面。
铺粉辊铺粉时多余的粉末被集粉装置收集。
如此
周而复始地送粉、铺粉和喷射粘结剂,最终完成一个三维粉体的粘结。
未被喷射粘结剂的地方为干粉,在成形过程中起支撑作用,且成形结束后,比较容易去除[1]。