34库存管理doc文档格式.docx
《34库存管理doc文档格式.docx》由会员分享,可在线阅读,更多相关《34库存管理doc文档格式.docx(10页珍藏版)》请在冰豆网上搜索。
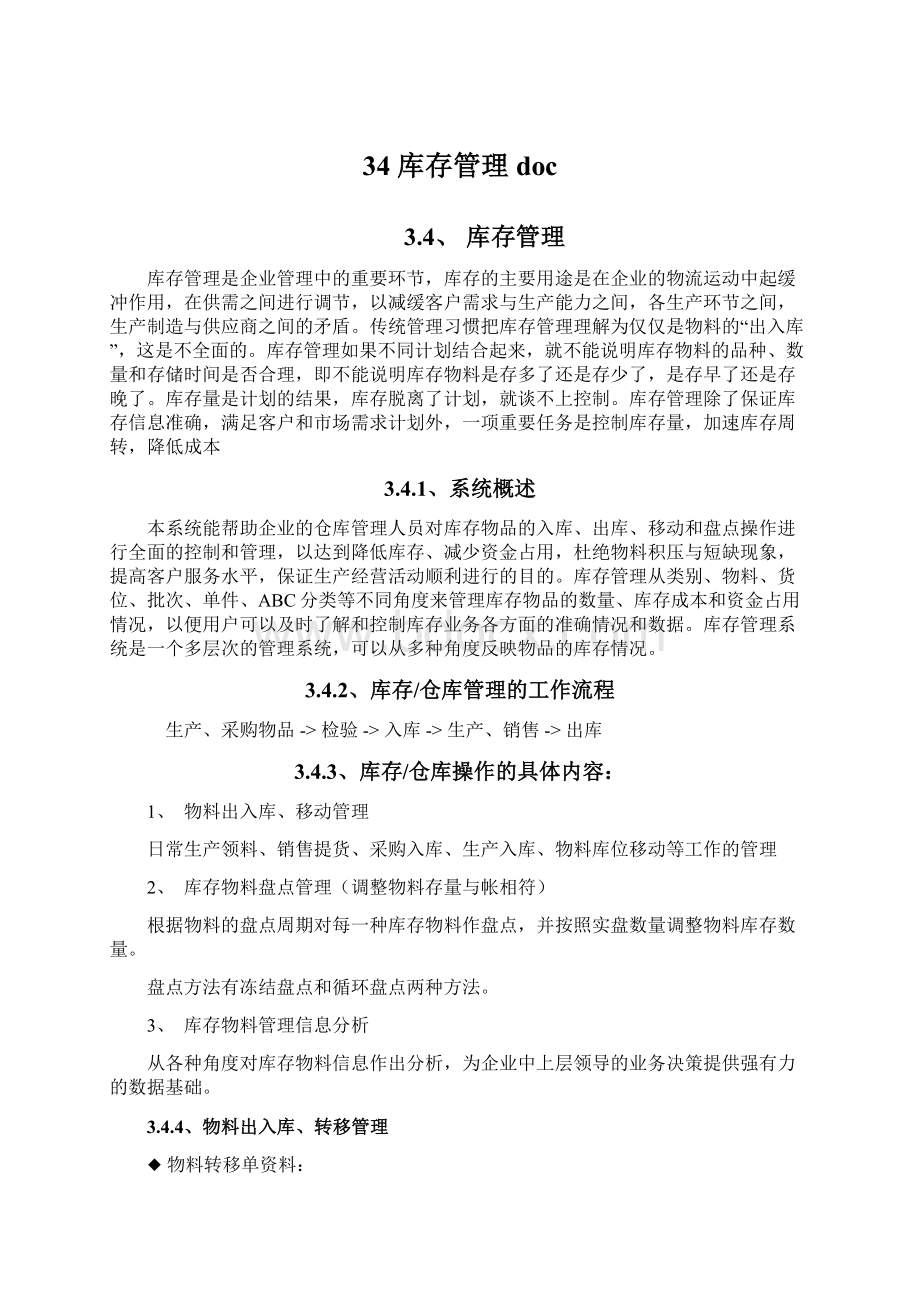
2、库存物料盘点管理(调整物料存量与帐相符)
根据物料的盘点周期对每一种库存物料作盘点,并按照实盘数量调整物料库存数量。
盘点方法有冻结盘点和循环盘点两种方法。
3、库存物料管理信息分析
从各种角度对库存物料信息作出分析,为企业中上层领导的业务决策提供强有力的数据基础。
3.4.4、物料出入库、转移管理
◆物料转移单资料:
《上马ERP!
》中,从物料转移单中更能体现其灵活,全面的特点。
由于本系统考虑到有些企业有异地仓库的可能,并充分考虑了我国现有企业的特点,将物料转移单分为四种状态,分别是:
“起草”,“确认”,“发送”,“接收”。
也就是说一张物料转移单分四步完成,当然,也可以根据用户的设置,将其分三步执行。
这样,既体现了本系统灵活的特点,又方便以后的权限控制。
◆1、如何新建一张物料转移单?
具体的操作:
1、单击起始界面中【G、库存和物料转移】下的【物料转移单资料】进入物料转移单资料窗口,如下图3-4-1所示:
3-4-1
2、在原因类别中选择一种原因类别,具体原因类别的定义请参考【库存操作定义】模块。
3、输入单据的起草日期后保存,如果不是系统自动生成编号,先要输入物料转移单编号,如果选择了系统自动生成编号,保存后系统自动生成编号。
4、在下面的明细窗口中输入要转移的物料(可以有一项或多项)及其数量。
◆如何确认一张起草的物料转移单?
1、在目录窗口中根据不同的条件组合找到要确认的物料转移单。
2、填写确认时间。
3、检查一下物料转移单的明细项有没有填写,如果没有,给出提示,不允许确认。
4、根据用户在【库存操作定义】中设置的选项【物料转移单确认时控制计划数量必须小于等于相关业务单据数量】,判断以下几种单据的计划数量是否大于相关业务单据的数量,如果大于就弹出窗口显示具体的差异情况。
如下图3-4-2所示:
3-4-2
几种物料转移单的原因类别分别是:
生产领料和生产入库,采购入库和采购退货,销售出库和销售退货。
5、如果发方或收方类别是库存,检查仓库的货位有没有填写,如果没有,给出提示。
以上几项如果均通过,系统将允许用户将此单据确认,确认时系统会给出提示,确认以后单据上列出的物料等待发送,下一步要进行的操作将是发送,所以确认以后除发送时间和发方经手人,以及发送数量和发送仓库的货位外,其余的将都不允许再进行修改。
◆如何发送一张确认的物料转移单?
处于“确认”状态的物料转移单才允许进行发送操作,表明用户已经确认单据上的数据均正确。
发送操作时系统做以下检查:
1.发送的时间是否填写,如果没有,将给出提示。
2.如果发方是仓库,判断仓库货位有没有填写,如果没有将给出提示。
3.根据用户在【库存操作定义】中设置的选项【物料转移单执行时控制发送数量必须小于等于计划数量】,判断发送数量是否大于计划数量,如果是,系统给出提示,并且不允许发送操作。
4.根据用户在【库存操作定义】中设置的选项【上述情况,如果实际发送数量不足,自动生成相关的补料单据】,如果发送数量不足,提示用户,是否自动生成相关的补料单据。
5.根据用户在【库存操作】中设置的选项【流程状态控制】,如果用户有异地仓库,进行异地的物料转移,则必须选择[必须分别通过发送,接收操作]同时用户可以根据本企业的实际情况选择是否物料转移单[只须发送],或者[只须接收]
以上几项,执行完之后,如果物料转移单的发方是仓库的话,系统将自动调整仓库的库存结存的值,并将单据的状态设为“发送”
◆如何接收一张发送的物料转移单?
并不是每条物料转移单都需要进行此项操作,只有那些在【库存操作定义】中选项【流程状态控制】,设为[必须分别通过发送和接收操作]的单据才进行此项操作。
并且满足物料转移单的状态是“发送”,进行接收操作时,系统做以下操作:
1.接收的时间是否填写,如果没有,将给出提示。
2.如果接收方是仓库,检查仓库货位有没有填写,如果没有,将给出提示。
3.根据用户在库存操作中设置的选项“物料转移单执行时控制接收数量必须小于等于发送数量”,判断接收数量是否大于发送数量,如果是,系统给出提示,并且不允许接收操作。
4.根据用户在库存操作中设置的选项“上述情况,如果实际接收数量不足,自动生成相关的补料单据”,如果接收数量不足,提示用户,是否自动生成相关的补料单据。
以上几项,执行完之后,如果物料转移单的收方是仓库的话,系统将自动调整仓库的库存结存的值,并将单据的状态设为“接收”。
3.4.5、库存盘点管理
◆如何自动生成盘点计划?
对于那些规定了盘点类型和盘点周期的物料或仓库,可以自动生成盘点计划。
具体的操作:
1、单击起始界面中【G、库存和物料转移】下的【06.库存盘点计划】进入盘点计划目录窗口,如下图3-4-3所示:
3-4-3
2、在目录窗口中,可以根据不同的条件组合,列出符合条件的盘点计划,同时也可以自动生成盘点计划。
3、单击【自动生成盘点计划】按钮,进入自动生成盘点计划资料窗口,如下图3-4-4所示:
3-4-4
4、自动生成盘点计划有两种类型,按物料和按仓库:
A、按物料:
1、窗口中的第一页是按物料来生成盘点计划,窗口上左边窗口中列出的是系统中所有的盘点周期大于0的物料,选中需要生成盘点计划的物料,单击
移至右边窗口中,也可以单击
将所有的物料全部移至右边的窗口中。
同时可以单击
将不需要的物料移至左边的窗口,也可以单击
将所有的物料都移到左边的窗口。
2、填写开始和截止的日期。
3、单击【确定】按钮,系统将根据物料的盘点周期自动生成右边窗口中所有物料在填写的日期段内的盘点计划。
A、按仓库:
1、窗口中的第一页是按仓库来生成盘点计划,窗口上左边窗口中列出的是系统中所有的盘点周期大于0的仓库,选中需要生成盘点计划的仓库,单击
将所有的仓库全部移至右边的窗口中。
同时也可以单击
将不需要的仓库移至左边的窗口,也可以单击
将所有的仓库都移到左边的窗口。
2、填写开始和截止的日期。
3、单击【确定】按钮,系统将根据仓库的盘点周期自动生成右边窗口中所有仓库
在填写的日期段内的盘点计划。
5、新生成的盘点计划可以同时在目录窗口中,按照物料或仓库(或别的查询条件)进行查看。
◆库存盘点资料:
如何新建一张盘点资料单据?
新建盘点资料有两种方法:
一种是用上面介绍的自动生成盘点计划,这里就不再详细介绍了,另外一种方法就是在盘点2资料窗口中直接新建。
具体的操作步骤:
1、从起始界面中单击【G、库存和物料转移】下的【07.库存盘点资料】进入库存盘点资料窗口。
如下图3-4-5所示:
3-4-5
2、在左边的窗口中填入详细资料,具体包括盘点类别,盘点对象,盘点方式,开始和结束时间,以及负责人等。
3、库存盘点有两种盘点类别,一种是按物料盘点,一种是按仓库盘点。
4、根据选择的盘点类别,填入盘点对象。
如果盘点类别是物料,则在盘点对象中输入要盘点的物料的编号,也可以从向导中选择,如果盘点类别是仓库,则在盘点对象中输入要盘点的仓库的编号,同样可以从向导中选择。
5、填写盘点开始和结束的时间,以及负责人后保存即可生成一张盘点单据。
备注:
如果用户不需要编号自动生成,那么还需要输入盘点单据的编号。
3.4.6、物料批次管理
◆如何进行物料的批次/单件追踪?
如果物料列入了批次或单件管理,就可以根据批次号对物料进行追踪。
如果依照本系统进行严格的批次管理,即在采购,生产,和库存部门对进行批次管理,那么系统就可以实现对物料的实时跟踪。
1、从起始界面中单击【G、库存和物料转移】下的【10.物料批次/单件追踪】进入物料批次追踪窗口,如下图所示:
2、单击工具栏中的打开
,如下图所示:
3、输入物料编号,或从向导中选择。
4、选择日期,共有五种日期可供选择:
A、采购到货日期:
列出的是在指定的日期范围内,物料的批次号及对应的采购收货单据。
B、生产完工日期:
列出的是在指定的日期范围内,物料的批次号及对应的生产指令。
C、销售发货日期:
列出的是在指定的日期范围内,物料的批次号及对应的销售发货单据
D、物料转移日期:
列出的是在指定的日期范围内,物料的批次号及对应的物料转移单。
E、全部日期:
列出的是在全部日期范围内,物料的批次号及对应的以上四种类型的单据。
3.4.7、定货批量
加工或采购的定货批量是运行ERP不可少的参数,确定批量是物料管理的一项重要工作,对加工周期的长短有很大影响。
合理制定定货策略也是控制库存量的一个重要内容。
3.4.7.1、批量规则
批量规则对MRP分解很重要,在计算出净需求量后,用来计算计划量。
最常用的批量规则有4种,其中固定批量法和经济批量法属于常用的静态方法,因需定量法和定期用量法属于常用的动态方法。
现有系统中的批量规则和处理方法简要说明如下:
MAX—最大:
如果净需求数量小于最大库存数量则把库存量补充到最大库存量来计算计划量。
反之则净需求量就是计划量。
在使用MAX时,仅考虑供货能力是否可以满足任务量,当任务量小于最大批量时,不考虑任务量的经济性。
MIN—最小:
如果净需求数量小于安全库存数量,则取安全库存数量作为计划量。
反之则净需求数量就是计划量。
使用最小批量时,仅考虑任务量的经济性,当任务量大于最小批量时,不考虑采购的供货能力是否可以满足任务。
FIX—固定:
当净需求量小于标准批量时,计划量等于标准批量;
当净需求量大于标准批量时,计划量等于净需求量。
使用FIX时,既考虑供货能力,又考虑任务量的经济性。
DIR—直接:
严格按照订单的净需求订货。
使用DIR时,仅考虑满足需求,不考虑供货能力和经济性。
CIR—周期:
将物品净需求量不为零的记录按批量周期定义的次数合并其净需求量,作为计划下达量。
使用DIR时,仅考虑控制采购的次数,同时可以保证满足需求,但不考虑供货能力,不考虑任务量的经济性。
FIR—固定周期:
不考虑净需求量是否为零,按批量周期中定义的天数合并净需求,作为计划下达量。
使用FIR时,仅考虑控制采购的间隔期,同时可以保证满足需求,但不考虑供货能力,不考虑任务量的经济性。
注:
现在还没有提供这种处理,把它和周期一样处理
DOB—倍数:
如果物品按一定数量X包装,计划量除标准批量不为整数(假定为N,余数为Y),则计划下达量取(N+1)*X,即取标准批量的整倍数作为下达量。
常见批量规则的解释
我们系统中有些批量规则是常见批量的变种
1、固定订货批量法(FixedOrderQuanlity)
这种订货方法可用于MRP控制下的所有物料,但在实践中,通常只限于订货费用比较大的部分物料。
对这些物料,根据净需求量的大小变化而不断发出订货是不合算的。
订货的数量可以根据经验来决定。
具体处理方法是:
有净需求,就产生一个批量的定单。
2、经济订货批量法(EconomicOrderQuantity------EOQ)
是指某种物料的订购费用和保管费用之和为最低时的最佳批量法。
一般用于需求是常量和已知的,成本和提前期是常量和已知的,库存能立即补充的情况下,即它是用于连续需求的,库存消耗是稳定的场合。
EOQ方法用于中等偏低成本水平的物料较好,这些物料比较多而且在使用量上也比较稳定。
一般不主张把经济批量法引入ERP系统。
计算公式:
EOQ=SQRT(2R*S/(I*C))
其中,R为年需求量,S为一次订货费用,I为年保管费用占平均库存值的百分比,C为物料单价。
有净需求,就产生一个批量的定单
3、直接批量法(Lotforlot)
根据净需求量来决定定货量,需要多少订多少。
采用这种方法可以降低物料存储费用,常用于价值较高和需求极不连续的外购件及制造件。
对通用组装部件是不适用的,这是因为将会使得对通用件的需求变化的响应带有动态的特性,从而大大增加了对通用部件的紧张度。
有净需求,就产生一个净需求量的定单
4、固定周期法(FixedPeriodRequirements)
它生成计划定单使之等于固定时间段内的几个周期的净需求之和。
主要优点是当计划覆盖未来的需求时可以控制未来需求的计划定单的数量。
多用于那些相对便宜些的物料。
具体的处理方法是:
把从上一个订货周期末开始,一个固定周期内的所有净需求量的总和生成一个定单。
?
5、周期订货批量法(PeriodOrderQuantity-----POQ)
这种方法是适应间断性需求环境而在EOQ基础上修改而的方法。
这种方法首先根据全年的需求量,用标准的EOQ批量去除算出每年的订货次数,然后用一年的总时区数除以订货次数,即得到订货的时间间隔。
主要优点是在它所覆盖的期间内,它要考虑单件成本和数量。
缺点是,它需要达到一定的准确程度,也可能在下次运行MRP时随着需求的改变而改变,另外,由于使用EOQ的计算公式(用假定的成本和用量水平),POQ方法对计划期间内不规律或波动需求的情况不是很有用。
每次定货覆盖此期间内的所有需求。
3.4.8、库存数据分析
系统提供多种库存数据分析报表,可使各级管理人员及时、准确地掌握库存信息反馈。
主要有:
1、仓库收发存报表、物料收发存报表、物料资金占用表、仓库资金占用表、超储报表、短储报表、呆滞物料报表、保质期物料到期情况汇总等结存报告表;
2、毛坯出库单、仓库收发报表、物料收发报表、盘点报表等变动报告;
3、物料齐套表、物料库存趋势、预计库存表、已收货未验收物料报表、已验收未入库物料报表等综合分析报表。