重质油催化裂化进展Word文件下载.docx
《重质油催化裂化进展Word文件下载.docx》由会员分享,可在线阅读,更多相关《重质油催化裂化进展Word文件下载.docx(5页珍藏版)》请在冰豆网上搜索。
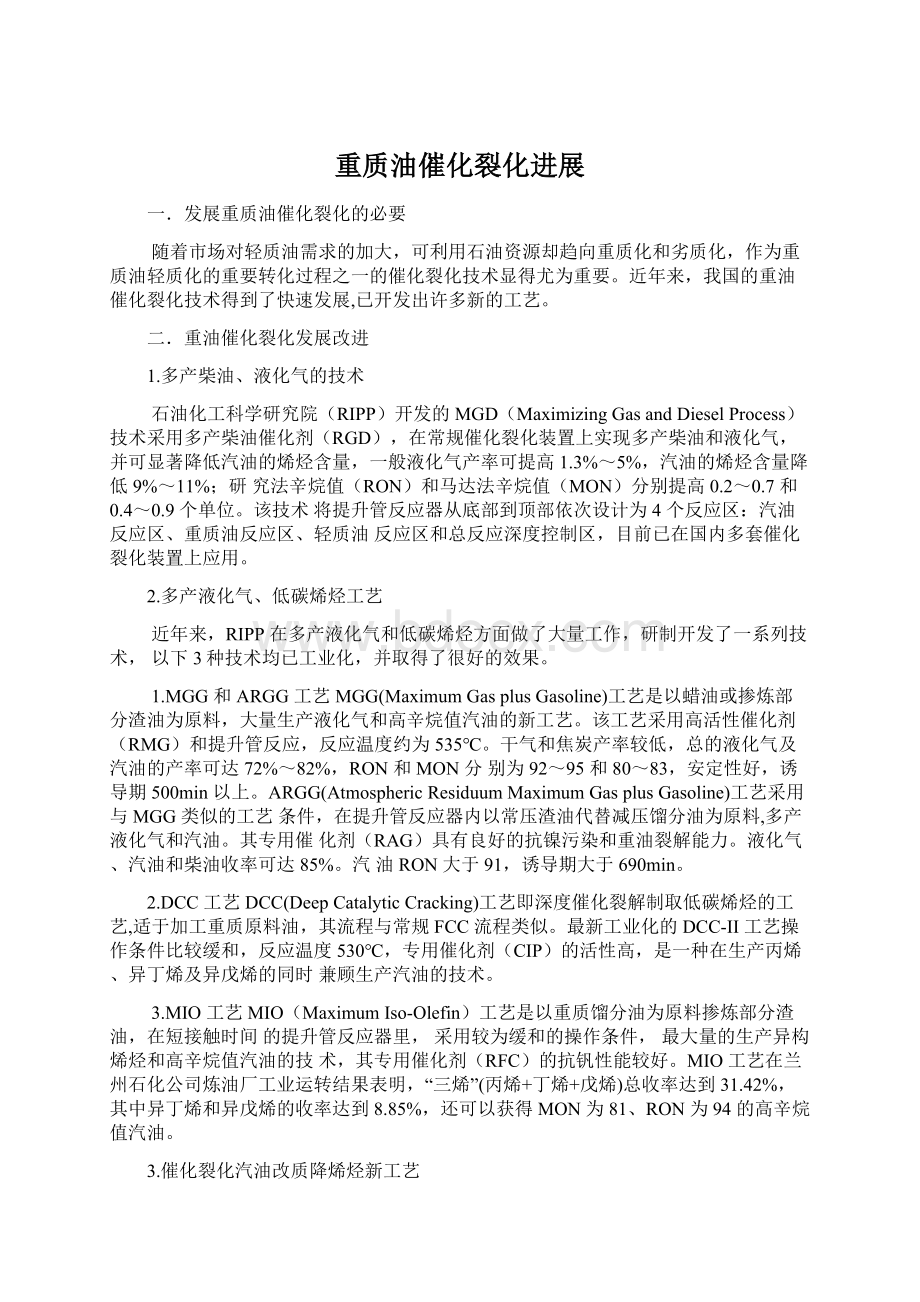
汽油反应区、重质油反应区、轻质油反应区和总反应深度控制区,目前已在国内多套催化裂化装置上应用。
2.多产液化气、低碳烯烃工艺
近年来,RIPP在多产液化气和低碳烯烃方面做了大量工作,研制开发了一系列技术,以下3种技术均已工业化,并取得了很好的效果。
1.MGG和ARGG工艺MGG(MaximumGasplusGasoline)工艺是以蜡油或掺炼部分渣油为原料,大量生产液化气和高辛烷值汽油的新工艺。
该工艺采用高活性催化剂(RMG)和提升管反应,反应温度约为535℃。
干气和焦炭产率较低,总的液化气及汽油的产率可达72%~82%,RON和MON分别为92~95和80~83,安定性好,诱导期500min以上。
ARGG(AtmosphericResiduumMaximumGasplusGasoline)工艺采用与MGG类似的工艺条件,在提升管反应器内以常压渣油代替减压馏分油为原料,多产液化气和汽油。
其专用催化剂(RAG)具有良好的抗镍污染和重油裂解能力。
液化气、汽油和柴油收率可达85%。
汽油RON大于91,诱导期大于690min。
2.DCC工艺DCC(DeepCatalyticCracking)工艺即深度催化裂解制取低碳烯烃的工艺,适于加工重质原料油,其流程与常规FCC流程类似。
最新工业化的DCC-II工艺操作条件比较缓和,反应温度530℃,专用催化剂(CIP)的活性高,是一种在生产丙烯、异丁烯及异戊烯的同时兼顾生产汽油的技术。
3.MIO工艺MIO(MaximumIso-Olefin)工艺是以重质馏分油为原料掺炼部分渣油,在短接触时间的提升管反应器里,采用较为缓和的操作条件,最大量的生产异构烯烃和高辛烷值汽油的技术,其专用催化剂(RFC)的抗钒性能较好。
MIO工艺在兰州石化公司炼油厂工业运转结果表明,“三烯”(丙烯+丁烯+戊烯)总收率达到31.42%,其中异丁烯和异戊烯的收率达到8.85%,还可以获得MON为81、RON为94的高辛烷值汽油。
3.催化裂化汽油改质降烯烃新工艺
1.FDFCC工艺洛阳石化工程公司开发了一种灵活多效催化裂化工艺(FDFCC)。
该工艺以常规FCC装置为基础,增设了一根与重油提升管反应器(第一反应器)并联的汽油改质提升管反应器(第二反应器)。
重油提升管反应器采用高温、短接触、大剂油比等常规催化裂化操作条件,反应产物经分馏塔分离后得到的高烯烃含量的粗汽油进入汽油改质提升管反应器,在那里采用低温、长反应时间、高催化剂活性的操作条件对汽油进行改质。
反应所需热量由重油提升管反应器生成的焦炭燃烧热提供,避免了汽油改质与重油裂化的相互影响。
工业试验表明,汽油改质提升管对催化汽油的改质效果十分显著,在不同的操作条件下,汽油的烯烃含量可降低30个体积百分点以上,RON可提高0.5~2个单位;
随着汽油改质反应器操作强度和汽油改质比例的提高,柴汽比一般可提高0.2~0.7,丙烯收率也可提高3~6个百分点。
2.MIP工艺由RIPP开发的多产异构烷烃的催化裂化工艺(MIP)突破了现有催化裂化技术对二次反应的限制,实现可控性和选择性裂化反应、氢转移反应和异构化反应,可明显降低汽油烯烃含量和增加汽油异构烷烃含量。
该工艺目前已在多家炼厂进行了工业应用,结果表明,工艺使产品分布得到了优化,MIP干气和油浆产率分别下降了0.41和0.99个百分点,液体收率增加了1.17个百分点,汽油的性质得到改善,汽油烯烃下降14.1个百分点,饱和烃含量增加了12.9个百分点,异构烷烃含量大于70%。
3.两段提升管工艺石油大学(华东)提出的两段提升管催化裂化(TSRFCC)技术将长提升管改为两个短提升管,分别与再生器构成两路循环。
一段反应生成的油气,分离产物后,进入二段提升管反应器,与再生剂接触继续进行反应。
其主要工艺技术特点是反应时间短,实现了催化剂接力、高剂油比和分段进料。
该工艺可大幅度提高原料转化深度,处理量增加20%以上。
轻质产品收率提高约3%,干气和焦炭降低。
产品质量提高,汽油烯烃含量下降近12%,当汽油回炼时其烯烃可降到35%以下,硫和十六烷值含量略有下降。
4.辅助反应器改质降烯烃技术中国石油大学(北京)研究开发了“催化裂化汽油辅助反应器改质降烯烃技术”,即在常规的FCC装置上,增设了一个辅助反应器,对裂化汽油进行改质处理,使其发生定向催化转化,裂化汽油中的烯烃在辅助反应器中进行氢转移、芳构化、异构化或者裂化等反应,使烯烃含量显著降低,而辛烷值基本不变。
工业运行表明,“辅助降烯烃技术”可使裂化汽油的烯烃含量降到35%(体积分数,下同)甚至20%以下,以满足越来越严格的汽油质量标准;
操作与调变灵活,通过调整改质反应器操作,可提高丙烯产率3~4个百分点。
5.灵活下行床反应器催化裂化工艺清华大学化工系流态化研究室于1994年提出的渣油催化裂化工艺,主要包括下行床反应器和两段提升管再生技术。
其下行床反应器的工艺特点是:
反应器总压降小;
气固接触时间短,反应油气停留时间维持在0.2~1.0s;
气固分离效率高;
气固轴向返混明显减少;
可以在较高的剂油比下操作等。
但该工艺对下行床反应器的入口和出口结构要求很高,由于气体和颗粒在下行床内的反应时间控制在1s以内,因此如何实现气固的快速混合和分离是至关重要的。
下行式柔性反应器渣油催化裂化工业试验表现出良好的产品分布,与原有提升管催化裂化相比,总液收增加了1.5%,丙烯收率提高了5%以上,汽油保持了较高的辛烷值,并显著降低了汽油中烯烃含量。
由于下行床催化裂化工艺的这些特征,其必将成为21世纪取代上行式提升管催化裂化的新技术之一。
三、重油加工利用技术的新进展
重油催化裂解技术——新开发的重油催化裂解技术,是以生产乙烯为主要目的产品的重油加工技术。
它是最近十多年里,在催化裂化工艺技术基础上,为调整产品结构多产液化气、多产丙烯,而逐步发展起来的重油加工技术。
1.重油催化裂解制烯烃技术综合评介
1、技术开发背景
发展石化工业需要发展乙烯——乙烯生产,在一定程度上已经成为衡量一个国家石油化工工业发展的重要标志,而传统的管式裂解炉制乙烯技术,原料需要使用轻烃(乙烷、石脑油、轻柴油),中国的轻烃资源不足,也成为制约中国乙烯—石化工业发展的重要因素之一。
发展重油深加工利用也是国情的需要——中国原油资源不足,而且多数原油较重,重油组份比例高,有较多的裂解重油原料资源。
因此,从利用好重油和增加乙烯原料两个方面来看,催化裂解制烯烃技术的开发,都是客观形势的要求。
CPP和HCC技术正是适应中国急需发展乙烯而原料又短缺的情况,从国内重油相对较多的实际出发,利用国内催化裂化技术较为成熟的基础条件来开发一项创新技术。
2、技术特点
(1)CPP技术
制取乙烯为主的重油催化热裂解新技术——(CPP)(CatalyticPyrolysisProcess,简称CPP)
工艺过程——CPP是以重油为原料,选用专门研制的分子筛催化剂,采用提升管反应器,催化剂以流态化连续反应-再生循环方式,在比管式炉蒸汽裂解制乙烯更为缓和的操作条件下,来生产乙烯和丙烯的催化裂解制烯烃技术。
反应机理——催化裂解技术的实质,是一个以催化裂解和热裂解同时存在的化学反应过程。
CPP催化剂具有正碳离子反应和自由基反应双重的催化活性,因此,新催化剂可以更多地生产乙烯和丙烯。
催化剂性能——CPP技术的核心在于CEP催化剂,CEP催化剂是一种酸性沸石催化剂,存在两种具有催化反应活性的酸性中心,一种为质子酸中心(即B酸中心);
另一种为非质子酸中心,(即L酸中心)。
石油烃类在催化剂的B酸中心催化活性作用下,较容易发生正碳离子反应,产生丙烯和丁烯;
而在催化剂的L酸中心催化活性作用下,除发生正碳离子反应外,还能进行自由基反应,因此,能较多地裂解产生乙烯。
一般的裂化催化剂反应活性中心以B酸为主,石油烃类在催化剂的B酸中心催化活性作用下,仅能发生正碳离子反应,因此生成的气体烯烃以丙烯和丁烯为主。
由于CEP催化剂中增添了较多的L酸中心活性组分,能够有利于增加自由基反应,从而可以生产大量的乙烯。
因此,CPP使用的CEP催化剂活性组分,应具有较高的L酸与B酸比值,以及较低的氢转移活性和较高的水热稳定性。
为此,采用专门研制的活性组分,并对基质、粘结剂以及CEP催化剂制备工艺等进行了改进。
CEP催化剂已由中国石化齐鲁石化公司催化剂厂实现了工业生产,工业产品CEP催化剂的物理性质与常规催化裂化催化剂相近,磨损指数还优于常规裂化催化剂,表明CEP催化剂具有良好的抗磨性能。
CPP催化热裂解工艺的主要特点——
适应重质原料(包括AGO、VGO、渣油、焦化蜡油、脱沥青油,以及常压渣油等),有利于拓宽乙烯原料降低成本;
催化剂综合性能好—催化剂是一种专门研制的改性新型择形沸石,具有正碳离子反应和自由基反应双重催化活性和对乙烯、丙烯的选择性,以及水热稳定性;
裂解反应温度低、能耗低投资省——催化剂的引入可降低裂解反应的活化能,使裂解乙烯温度较管式炉蒸汽裂解大幅度降低(由800℃以上,降至600~650℃),从而降低了生产能耗;
由于裂解反应温度低(650℃),再生温度也不很高(760℃),因此,反应再生系统可选用常规催化裂化装置使用的材料,无需选用昂贵的合金钢材料,节省了设备投资;
可利用催化裂化装置改造—CPP技术采用提升管反应器和催化剂流态化连续反应-再生循环操作工艺,总体上与催化裂化工艺完全相同,因此,工艺成熟、操作灵活,也可利用现有FCC装置来改造;
,
操作灵活性大有利于调整生产—可根据需要通过调整工艺参数来灵活调整产品结构,例如可实现最大量生产乙烯、或最大量生产丙烯,以及乙烯和丙烯兼顾等多方案操作;
(2)HCC技术
重油直接接触裂解制乙烯工艺——Heavy-OilContactCracking),一种以重油为原料,采用专用催化剂重油裂解制乙烯、丙烯等低碳烯烃及高芳烃液体产品的新工艺。
反应机理——HCC技术是在重油催化裂化工艺技术基础上,采用了一种专门研制的催化剂,烃类在催化剂上的裂解反应机理,以自由基热反应为主,催化反应(正碳离子反应)为辅。
技术特点——
催化剂特性—HCC专用催化剂的组成,以SiO2/Al2O3为基质,主要调控催化活性和选择性的主要影响组分,少量添加沸石分子筛作为调节组分,保证催化剂的基本物化性能,以及其对重油催化裂解活性和选择性,能以自由基热反应为主,催化反应为辅。
反应、再生温度高、剂油比高—HCC裂解反应温度670℃—700℃(最高730℃);
再生温度800℃—850℃;
剂油比高(18)、水油比高(>0.3)。
产品结构好—在重油深加工技术中HCC技术是碳氢利用比较好的工艺,其原料中所含的氢能较为理想地转移向气体、液化气和轻油,因此,HCC产品干气中乙烯含量高、液化气中丙烯含量高、液体产品中的芳烃含量高。
例如,用常压渣油原料的试验,产品中有约50%的低碳烯烃(其中乙烯为24-28%);
约25-27%的富含芳烃的液体产品。
HCC技术有利于实现单套乙烯装置规模大型化—由于HCC技术的工程化,可立足于成熟的重油催化裂化(RFCC)技术和管式炉蒸汽裂解乙烯技术来组合实现,因此,按300—350万吨/年规模的重油催化裂解装置计算,单套装置的乙烯生产能力可以达到65—80万吨/年。
2.CPP、HCC工艺的工业运用前景
由于乙烯裂解原料的质量,对乙烯裂解生产能耗的影响较大(例如,轻柴油原料的单位能耗要比石脑油高20%左右),因此,国内已经采取了一系列技术进步措施来增加乙烯轻原料比例,例如中国石化的乙烯原料中轻柴油所占比例1999年为17.99%,但从全国看,乙烯裂解原料中轻柴油所占的比例在20%以上(20-30%)。
根本原因在于国内原油偏重,直馏石脑油资源少;
同时中国炼油企业生产石脑油馏分的加氢裂化装置少,短时期又增加不了。
而且,国内汽油、煤油、重整装置原料等需求还在增长,乙烯裂解原料石脑油资源增长前景不容乐观,因此,轻柴油在乙烯裂解原料中仍会保持相当比例。
我国是柴油消费量比较大的国家(柴汽比一般大于2.0),市场上的柴油经常紧缺难以满足需要,因此,不与市场争柴油解决乙烯裂解原料短缺的矛盾,是摆在炼油化工工作者面前的一个重要课题,而重油催化裂解优点,正好有利于减缓我国化工资源不足的矛盾。
以HCC工艺为例,重油裂解的乙烯单程产率一般为23-25%,加上碳二、碳三、碳四烷烃的回炼,乙烯总产率可以达到26-28%,如果乙烯产率平均按25%计,相当于400万吨/年规模的HCC的装置,可生产100万吨乙烯。
按管式炉裂解乙烯原料单耗3.32计,相当于322万吨化工轻油(其中石脑油为156万吨,轻柴油为110万吨)。
因此,可以说重油催化裂解工艺是一个适合国情的炼油-化工一体化新工艺,对于发展中国乙烯工业有着良好的市场应用前景.