外文翻译纯中文版人工神经网络来优化铝合金挤压过程文档格式.docx
《外文翻译纯中文版人工神经网络来优化铝合金挤压过程文档格式.docx》由会员分享,可在线阅读,更多相关《外文翻译纯中文版人工神经网络来优化铝合金挤压过程文档格式.docx(11页珍藏版)》请在冰豆网上搜索。
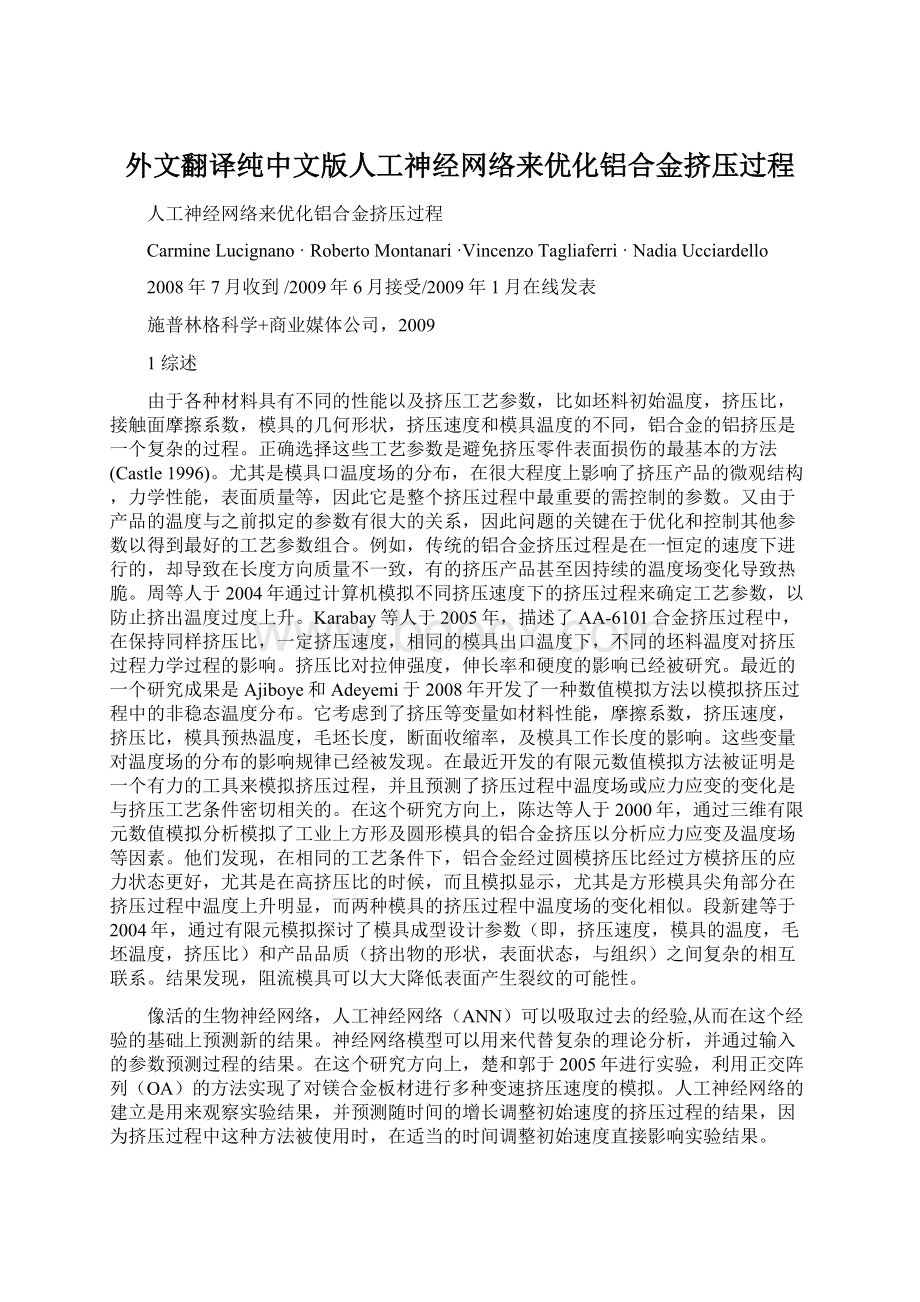
他们发现,在相同的工艺条件下,铝合金经过圆模挤压比经过方模挤压的应力状态更好,尤其是在高挤压比的时候,而且模拟显示,尤其是方形模具尖角部分在挤压过程中温度上升明显,而两种模具的挤压过程中温度场的变化相似。
段新建等于2004年,通过有限元模拟探讨了模具成型设计参数(即,挤压速度,模具的温度,毛坯温度,挤压比)和产品品质(挤出物的形状,表面状态,与组织)之间复杂的相互联系。
结果发现,阻流模具可以大大降低表面产生裂纹的可能性。
像活的生物神经网络,人工神经网络(ANN)可以吸取过去的经验,从而在这个经验的基础上预测新的结果。
神经网络模型可以用来代替复杂的理论分析,并通过输入的参数预测过程的结果。
在这个研究方向上,楚和郭于2005年进行实验,利用正交阵列(OA)的方法实现了对镁合金板材进行多种变速挤压速度的模拟。
人工神经网络的建立是用来观察实验结果,并预测随时间的增长调整初始速度的挤压过程的结果,因为挤压过程中这种方法被使用时,在适当的时间调整初始速度直接影响实验结果。
2006年,上述作者探索了镁合金热挤压过程中毛坯温度和拉伸强度之间的关系,并通过神经网络分析获得最佳温度范围。
在本文中,两种神经网络划分被应用在铝合金挤压工艺来优化工艺条件,确定了6060铝合金出口的感应加热器(ANN1)和在模具出口(ANN2)的温度场分布。
三层神经网络算法已从工业过程的实验数据中得出。
2热挤压工艺中的人工神经网络的模型建
在这项研究中,两种人工神经网络已经被应用于Matlab中以实现预测最佳铝合金挤压工艺条件。
由工业过程提取的两组数据已被用来验证神经网络模型,以此来确定模具出口的温度场分布。
实验数据是从五种不同的6060铝合金型材通过特定的挤压比挤压得到的。
直径为200毫米的6060铝合金坯料,放入感应加热器中加热,加热温度范围为400−470℃,保温时间在30秒到90秒区间。
温度由放在感应加热器内的四个热电偶测得(如图1所示)然后它们被送进温度约为550℃的环境下开始挤压。
在这一步中,铝型材成型,它们被挤成五个不同的部分。
感应加热器的温度以及模具出口的瞬时温度由不同频率的光学高温计测量(图1)以往的工艺参数都是从工业过程中获得并被优化,特别是6060铝合金。
图1
a示意图表示坯料在感应加热器出口位置。
b示意图表示棒料在模具出口位置。
第一个神经网络(ANN1)是用来实现预测毛坯出口的感应加热器的温度场分布的。
以下过程参数作为输入元素:
毛坯在感应加热器中的停留时间,由四个热电偶在感应加热器中测得的温度以及温度观测频率。
表1显示了16组热电偶测得的温度记录。
每个组合的保温时间变化范围为30–90S。
ANN1被用来研究包括层数,激活函数,复制率,随机权重在内的不同的拓扑结构。
每个网络用来实验不同次数的迭代。
ANN1的最后架构是6:
14:
1,如图2所示。
前馈ANN1算法由在实验中得出。
通常情况下,与到传递相比,这种算法的应用会导致在一些迭代实验次数数量级的减少。
S型传输功能是用来隐藏层的。
以数据库中的30组实验数据进行实验,其余的12组用来测试网格。
所有的变量增量均是在正常范围的0–1内进行,以确保认为输入比较的相对重要性。
增长率定为0.1,在ANN1的实验中最大值定为1500。
该网络的验证直到实际值与预测值的均方误差之间的差距减少到10−5。
这些数值被由预备实验得出。
图2
第二个人工神经网络(ANN2)是用来预测挤压截面在模具出口的温度分布的。
输入层三个方面:
挤压比,坯料在出口的感应加热器加热后温度分布(ANN1输出),不同频率的光学高温计所观测的温度。
坯料截面积被视为常数,而挤压比(坯料截面积与模具截面积之比)是根据不同的模具截面积(41.31,43.12,44.55,45.80,和47.75)而定的。
在研究阶段,该文应用Levenberg–Marquardt算法。
实验结果由两套数据组成,21组的用于实验和9组用来验证神经网络。
每个用于训练或验证神经网络的数据都是由24个实验结果组成的;
分别有720和504个实验点对网络进行验证。
为了确定最优结构的ANN2,对不同数量的神经元隐层和不同的传递函数。
一的些神经网络进行了验证。
最后的结构是:
三个输入,一个隐层和一个显层,如图3所示。
隐层应用S型传输功能,网络可以进行3500个数量级的验证。
输入变量是为了研究感应加热温度,加热时间和挤压比等参数对两种人工神经网络的影响,因为挤压速度和摩擦系数被定为是常数。
图3
表1四个热电偶在感应加热器记录的温度
T1(℃)T2(℃)T3(℃)T4(℃)
470440420400
450440420400
470460420400
450460420400
470440440400
450460440400
470460440400
450440440400
470460420430
450460420430
470440420430
470460440430
450440440430
450460440430
3结果与讨论
第一个神经网络是使用Levenberg–Marquardt算法的,并使用30组数据,计算期间并未导致过度的计算量,而且使用了12组数据进行验证。
表格4,5显示了验证结果,即,测量温度分布和神经网络预测感应加热器出口的温度,由温度观测频率决定的温度。
所有的数据均在正常范围在0–1。
图4,5之间的曲线图偏差是非常小的,但数值曲线似乎与实验曲线不同,它们不遵循实验波动。
图4
图5
非正规验证结果如图6所示,神经网络预测加热器出口温度与保温时间为80秒的实验温度对应。
倾斜45水平绘制在图中,一个完美的预测;
所有的点都在这。
神经网络预测的最佳温度是通过表2验证的,图6用来说明预测值与实验值的。
神经网络的预测误差的减小与感应加热器的保温时间有关。
四个热电偶在感应加热器测的温度为固定值,增加坯料在加热器的停留时间引起了加热器出口最大值的增加和最低温度的减少。
最大和最小值与热电偶温度T1和T4相当接近,因此通过增加保温时间,预测的加热器出口温度分布与实际更接近。
表2时间为80秒时在感应加热器出口温度场分布的实验值和神经网络预测值
Texp.[℃]TANN[℃]
420421.081
419419.632
421422.93
422421.88
421421.243
420421.417
423424.072
426429.587
429430.682
430428.104
431433.252
432436.067
434437.458
437439.355
441443.355
438439.78
437438.928
438439.778
445448.446
449451.139
450452.499
454457.583
457454.956
453453.418
图6
第二组人工神经网络依然采用Levenberg–Marquardt算法,但使用21组数据集,并没有造成计算过度,并使用9套数据进行验证。
图7–9显示实验结果;
我们绘制三个不同挤压比(41.31,43.12,和47.75)下实验温度场分布和神经网络预测的温度场在口模具出口的对比,而温度点依赖于温度观测频率。
所有的数据在0–1正常范围内,如图4,5所示。
图7–9两条曲线之间的偏差很小,尤其是数值曲线与实验值的叠加,由它的波动引起。
图7
图8
图9
非规范验证结果如图10所示,神经网络预测的模具出口温度是绘制在挤压比为47.75的实验的温度场基础上的;
所有的点都在一条倾斜的45°
线附近。
表3显示预测和实验温度值这一结果。
两组数值之间的差距值很小,尽管第二个神经网络的一个输入神经元的是坯料感应加热器出口的温度分布(ANN1输出)。
神经网络预测的误差随着挤压比的增大而增大。
最大的错误发生在挤压比为47.75的情况下。
温度在模具出口的分布随挤压比增加而增加,在一般情况下温度在出口迅速增加,少时就达到了最高值约570℃
表3挤压比为47.75时在感应加热器出口温度场分布的实验值和神经网络预测值
533529.773
550549.261
561557.144
564558.909
563560.004
565561.756
567562.413
568563.288
569564.383
570564.821
571565.916
571566.135
572566.573
572566.792
572567.011
572567.449
572567.668
572568.544
572568.106
572568.325
572567.23
图10
利用神经网络可以实现预测和控制坯料在感应加热器出口的温度,挤压温度曲线无疑是最重要的控制参数,在很大程度上影响该挤压过程的结果。
对于一个固定速度的挤压过程,优化的挤压过程只有通过监测和改变时间和感应加热器温度以及挤压比来控制。
显然,如果其他主要变量参与的过程中,它们可以同时由人工神经网络考虑和实施。
4结论
两种人工神经网络的实施是预测铝合金挤压工艺的最佳条件。
从工业过程提取的两组数据通过确定的温度在模具出口的分布来验证的神经网络模型。
实验数据五种不同型材的6060铝合金通过特定的挤压比获得的。
第一个神经网络(ANN1)可以预测钢坯在感应加热器出口的温度分布。
输入的因素有:
坯料在感应加热器的停留时间,四个热电偶在感应加热器记录的温度和温度观测频率。
第二个人工神经网络(ANN2)预测的是坯料截面杆在模具出口的温度分布。
输入层由三个神经元对应:
挤压比,钢坯在感应加热器出口的温度分布(ANN1输出),和由光学高温计所观测频率的温度。
两种神经网络都由三层构成,并都是采用Levenberg–Marquardt算法。
对型材预测的感应加热器和模具出口的剖面温度场分布,密切与实验值一致。
因此,神经网络方法可以有效地应用于预测和控制铝合金挤压过程。
参考文献
[1]Ajiboye,J.S.,&
Adeyemi,M.B.(2008).Effectsofextrusionvariablesontemperaturedistributioninaxisymmetricextrusionprocess.International
[2]JournalofMechanicalSciences,50,522–537.doi:
10.1016/j.ijmecsci.2007.08.006.
[3]Castle,A.F.(1996).Temperaturecontrolinaluminiumextrusion.ProceedingsoftheSixthInternationalAluminiumExtrusionTechnology
[4]Seminar(Vol.1,pp.181–184).Chicago:
AluminiumAssociationandExtrudersCouncil.
[5]Chanda,T.,Zhou,J.,&
Duszczyk,J.(2000).FEManalysisofaluminiumextrusionthroughsquareandrounddies.Materials&
Design,21,322–335.doi:
10.1016/S0261-3069(99)00073-4.
[6]Duan,X.,Velay,X.,&
Sheppard,T.(2004).Applicationoffiniteelementmethodinthehotextrusionofaluminiumalloys.MaterialsScienceandEngineeringA,369,66–75.doi:
10.1016/j.msea.2003.10.275.
[7]Fausett,L.V.(1994).Fundamentalsofneuralnetworks:
Architectures,algorithmsandapplications.EnglewoodCliffs,NJ:
PrenticeHall.
[8]Hsiang,S.,&
Kuo,J.(2005).ApplicationofANNtothehotextrusionofmagnesiumalloysheets.InternationalJournalofAdvancedManufacturingTechnology,25,292–300.doi:
10.1007/s00170-003-1828-2.
[9]Hsiang,S.,Kuo,J.,&
Yang,F.(2006).UsingartificialneuralnetworkstoinvestigatetheinfluenceoftemperatureonhotextrusionofAZ61magnesiumalloy.JournalofIntelligentManufacturing,17,191–201.doi:
10.1007/s10845-005-6636-0.
[10]Karabay,S.,Yilmaz,M.,&
Zeren,M.(2005).InvestigationofextrusionratioeffectonmechanicalbehaviourofextrudedalloyAA-6101fromthebilletshomogenised-rapidquenchedandas-castconditions.JournalofMaterialsProcessingTechnology,160,138–147.doi:
10.1016/j.jmatprotec.2004.05.025.
[11]Levenberg,K.(1944).Amethodforthesolutionofcertainnonlinearproblemsinleastsquares.QuarterlyofAppliedMathematics,2,164–168.
[12]Marquardt,D.(1963).Analgorithmforleastsquaresestimationofnonlinearparameters.JournaloftheSocietyforIndustrialandAppliedMathematics,11,431–441.
[13]Zhou,J.,Li,L.,&
Duszczyk,J.(2004).Computersimulatedandexperimentallyverifiedisothermalextrusionof7075aluminiumthroughcontinuousramspeedvariation.JournalofMaterialsProcessingTechnology,146,203–212.doi:
10.1016/j.jmatprotec.2003.10.018.